La farmacéutica Upsa amortiza en un año su inversión en impresión 3D
Upsa, una importante empresa farmacéutica francesa, está aumentando la capacidad de su planta de fabricación y reduciendo hasta en un 95% los costes de algunos procesos gracias a la adopción de la fabricación aditiva de Stratasys. El efecto positivo e inmediato en las operaciones de Upsa ha sido tal que la empresa ha amortizado el coste de la inversión en tan solo un año desde la adquisición de la impresora.
La empresa, propiedad de Bristol-Myers Squibb, se ha dado cuenta de que la fabricación aditiva es una forma de revitalizar su taller y de atraer a la siguiente generación de técnicos. Upsa también considera que la tecnología es esencial para superar los retos de la línea de producción que hasta ahora habían limitado el número de piezas que podían fabricar con los métodos tradicionales.
“Determinamos que la impresión 3D podía dar respuesta a nuestras necesidades e hicimos un cálculo aproximado de todas las piezas que podríamos imprimir en 3D. Nuestro objetivo era ver si podíamos ahorrar en costes de fabricación y reducir nuestro inventario de piezas”, explica Mathieu Dumora, jefe de Proyecto del departamento Técnico y de Infraestructura de Upsa. “Nos dimos cuenta rápidamente de que el peso de las piezas impresas en 3D era un 70% menor, lo que redundaba en un menor desgaste de la máquina y también tenía un importante efecto positivo en la productividad y duración de la misma”.
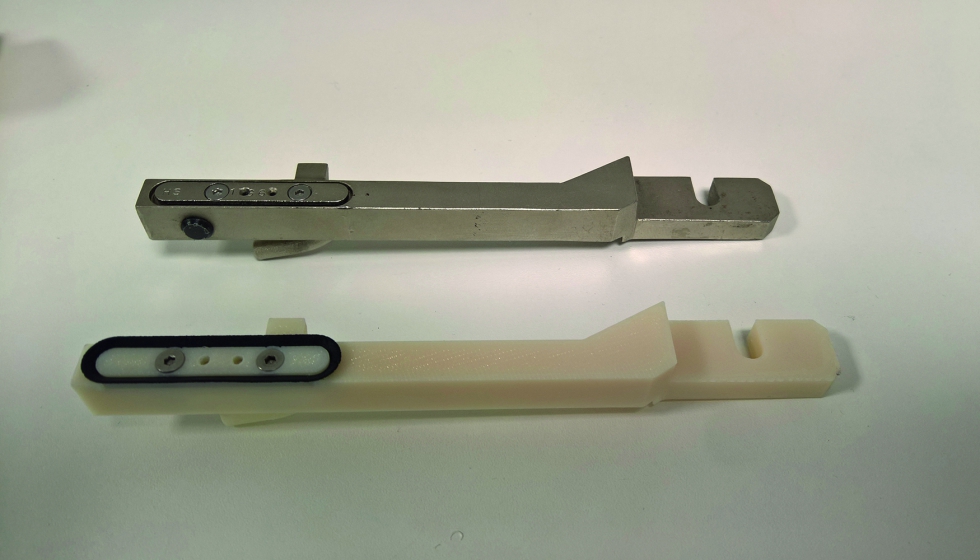
º
Un 95% de reducción de costes en tan solo una pieza
Con esta valoración tan positiva, Upsa se decidió a invertir en una impresora 3D Stratasys Fortus 450mc Production, una medida que demostró ser todo un éxito y que permitió a la empresa reducir considerablemente los costes, sobre todo en lo que respecta a la sustitución de piezas que, como indica Dumora, era un tema prioritario para Upsa.
“Una de las máquinas de nuestra línea de fabricación y envasado es un pesado brazo de acero moldeado que se emplea como parte del proceso para sujetar y abrir por succión un cartón plegable y así poder introducir los envases blíster”, explica.
“Son brazos pesados que pueden deformarse y, en ocasiones, fallar y causar averías en la máquina. Es más seguro utilizar un brazo impreso en 3D. El material de impresión 3D biocompatible ABS-M30i puede reajustarse si se deforma y, si se rompe, el coste de sustitución es mínimo y el tiempo de impresión también es muy breve. Hablamos de una mejora enorme con respecto a los costosos brazos de acero. En solo un año, hemos fabricado 55 brazos con una reducción del coste del 95% en cada uno de ellos”.
La fabricación aditiva ayuda a sustituir las largas y costosas inspecciones visuales
Upsa también utiliza su impresora 3D Fortus 450mc Production para fabricar un dispositivo que mejora la seguridad de los tapones de cierre del Efferalgan (paracetamol) pediátrico, después de detectar que algunos de los tapones del proveedor tenían partículas que podrían haber supuesto un riesgo de contaminación para el medicamento. Este dispositivo es tan eficaz que Upsa ya no tiene que realizar las costosas y largas inspecciones visuales que se realizaban antes.
“Hemos desarrollado un sistema que aspira y sopla aire para eliminar cualquier partícula”, comenta Dumora. “Comprobamos el aire aspirado y, algunas veces, incluso introducimos partículas en los tapones para comprobar la eficacia del sistema. Con la fabricación aditiva, podemos realizar esta solución nosotros mismos y mejorarla mediante iteraciones de desarrollo de manera rápida y económica”.
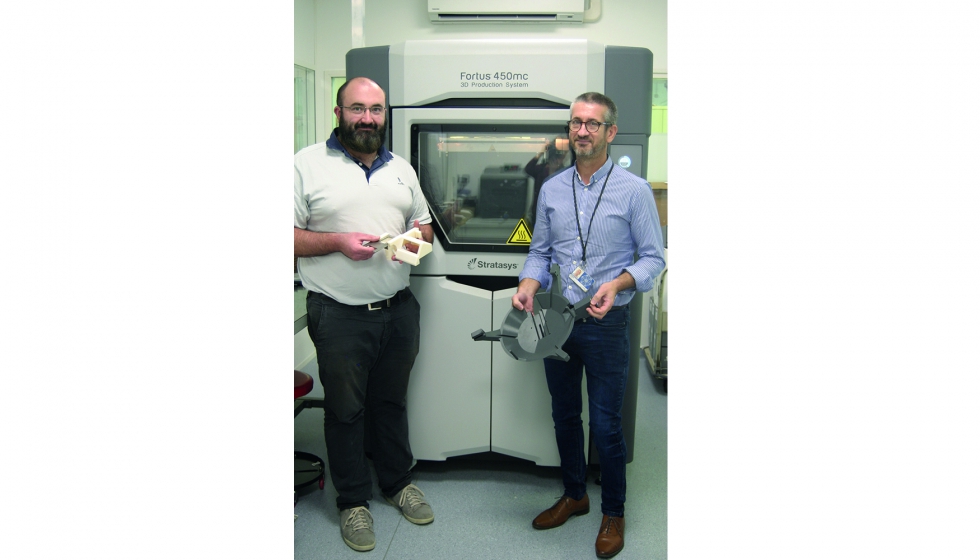
La consolidación de piezas contribuye al enorme ahorro conseguido en el primer año
“Aplicamos a nuestros envases codificación de seguimiento y localización y, para asegurarnos de que la impresión se realiza correctamente, se monta una cámara encima de cada uno de ellos”, explica Dumora. “Uno de nuestros ingenieros utilizó la Fortus 450mc para crear la forma que necesitaba, antes de utilizarla para realizar 22 unidades, una para cada máquina. Antes de esta innovación, se necesitaba un conjunto de 27 piezas; el nuevo diseño solo tiene dos piezas, lo que ha supuesto para nosotros un considerable ahorro de costes y tiempo de producción”.
“No hace falta decir que, para aquellos de nosotros que la utilizamos, la Fortus 450mc es una herramienta de trabajo incansable, pero su efecto positivo e inmediato se ve definitivamente confirmado por el hecho de que hemos amortizado completamente la inversión en el primer año de funcionamiento de la impresora”, concluye Dumora.
“Seguimos observando un aumento de la demanda de herramientas, piezas de producción y piezas de repuesto impresas en 3D para la maquinaria industrial”, comenta Andy Middleton, Presidente de Stratasys, Emea. “La rapidez con la que Upsa ha integrado con éxito nuestra impresora 3D en su proceso de producción y ha conseguido un enorme y cuantificable rendimiento de la inversión demuestra que esta tecnología puede ayudar a superar rápida y económicamente los retos de la línea de producción a que se enfrentan los fabricantes de casi todo los sectores industriales”.