Nuevas tecnologías de medida de la microgeometría de la herramienta han abierto las puertas a poder diseñar ‘ad-hoc’ la geometría del filo
Herramientas de corte: la clave está en el filo
El proceso de mecanizado es una de las aplicaciones más extremas a las que se enfrentan la ingeniería mecánica: altas temperaturas (300-1.200 °C), presiones extremas en la zona de contacto entre la herramienta y la pieza (100-1.000 N/mm²) y altas velocidades (1-30 m/s) [1]. Los mecanizadores son conscientes de la importancia que posee controlar la geometría del filo para conseguir un buen rendimiento de la herramienta.
Independientemente de la operación de mecanizado, la geometría de la arista de corte determina en gran medida los esfuerzos termo-mecánicos sufridos por la herramienta. De hecho, una pequeña variación en la microgeometría puede dar lugar a notables mejoras en la vida de la herramienta. La preparación del filo es, por lo tanto, una de las etapas más importantes en el proceso de fabricación de herramientas. Hasta hace algún tiempo, la tarea de preparación de los radios de filo era manual y dependía, en gran medida, de la experiencia del operario. Sin embargo, el desarrollo de nuevos procesos de fabricación y la aparición de tecnologías de medida de la microgeometría de la herramienta han abierto las puertas a poder diseñar ‘ad-hoc’ la geometría del filo.
1. Introducción
Este trabajo tiene como propósito ofrecer al lector una visión global del proceso completo de preparación, medición y análisis de la geometría del filo de corte. En primer lugar, se mostrarán las diferentes tecnologías de producción que permiten dar la forma deseada a la herramienta. A continuación, se presentarán las técnicas empleadas en varios trabajos de investigación para obtener la geometría 2D de la arista de corte. Por último, se describirán las diferentes metodologías que se han propuesto para analizar los datos obtenidos y obtener parámetros que permitan representar el aspecto del filo de corte.
2. Tecnologías preparación del filo
Para que el diseño a medida del filo de corte sea económicamente viable, es necesario disponer de una tecnología de fabricación que asegure la repetitividad del proceso. Entre los más comunes se encuentran el rectificado [2], el microchorreado abrasivo, el cepillado y el ‘drag-finishing’. Así mismo, varios estudios han investigado la posibilidad de emplear nuevas alternativas como el mecanizado magneto-abrasivo [3], el mecanizado en fluido abrasivo [4], el mecanizado laser [5] o la electroerosión [6]. La
La figura 1 muestra de forma esquemática cada uno de ellos.
![Figura 1. Alternativas para la preparación del filo de la herramienta. Adaptado de [7] Figura 1. Alternativas para la preparación del filo de la herramienta. Adaptado de [7]](https://img.interempresas.net/fotos/1617054.jpeg)
2.1. Rectificado
El rectificado es empleado para generar geometrías achaflanadas simples o dobles en sustratos cerámicos o de metal duro. El propósito de estos chaflanes es reducir el riesgo de astillamiento y aumentar la estabilidad del filo. Independientemente del material de herramienta utilizado, las deformaciones locales producidas por los granos abrasivos dan lugar a la aparición de varios defectos como rebabas, un acabado superficial pobre o el astillamiento del filo (ver figura 2). Además, el estado de tensiones residuales resultante del proceso de rectificado puede ser perjudicial para el rendimiento de la herramienta recubierta.
![Figura 2. Defectos ocasionados por la preparación del filo mediante rectificado. Adaptado de [8] Figura 2. Defectos ocasionados por la preparación del filo mediante rectificado. Adaptado de [8]](https://img.interempresas.net/fotos/1617055.jpeg)
Figura 2. Defectos ocasionados por la preparación del filo mediante rectificado. Adaptado de [8].
Se ha de tener en cuenta que antes de llevar a cabo la preparación del filo, la geometría global de la herramienta es ‘tallada’ mediante rectificado. La principal ventaja de preparar el filo rectificando es que se reducen los tiempos de fabricación de la herramienta. No obstante, si se desea obtener microgeometrías de filo complejas o conseguir un determinado radio de filo, el rectificado no es un proceso de preparación adecuado.
2.2. Microchorreado abrasivo
El microchorreado es una alternativa al rectificado que permite realizar la preparación del filo y mejorar las propiedades superficiales de la herramienta. En este proceso, los granos abrasivos son proyectados hacia la superficie de la pieza bien en un medio seco (únicamente con aire a presión) o bien mediante el empleo de agua. De esta forma, la deformación y eliminación del material de la herramienta se produce tras el impacto de cada grano abrasivo.
El microchorreado abrasivo tiene varios resultados positivos para la vida de la herramienta. Por un lado, se genera una morfología sobre la superficie que permite mejorar la adhesión del recubrimiento. En concreto, se elimina el cobalto aglutinante dejando a la vista más superficie de los granos de metal duro (ver figura 3). Además, se reduce la rugosidad superficial y se introducen tensiones residuales de compresión en la herramienta. No obstante, el elevado número de parámetros a controlar hacen que sea difícil conseguir resultados repetitivos.
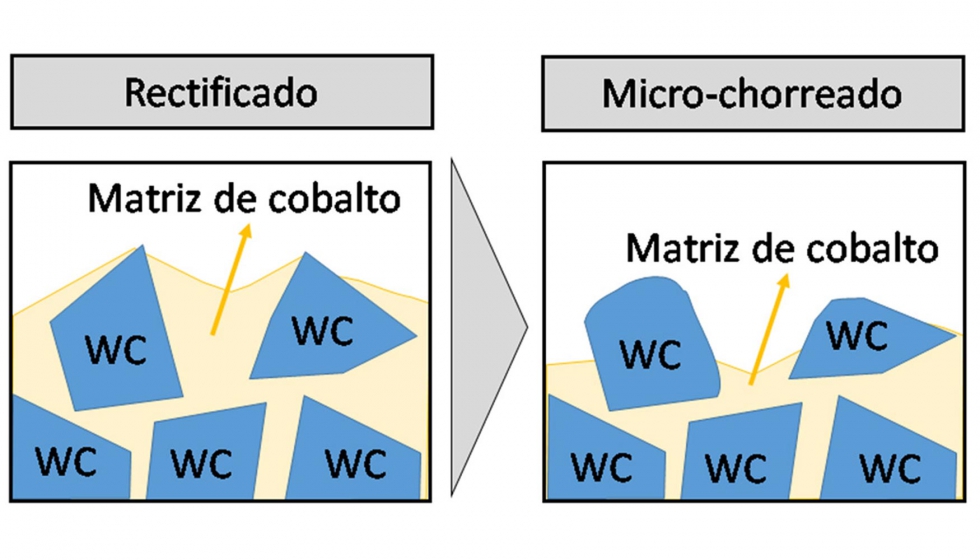
Figura 3. Efecto del microchorreado abrasivo sobre la estructura del metal duro.
2.3. Cepillado
El mecanizado de la geometría del filo puede realizarse también mediante el empleo de cepillos de filamentos metálicos o poliméricos que contienen un abrasivo en su extremo. Mediante este proceso, se consigue un redondeamiento del filo asimétrico que depende de si el cepillado se efectúa desde la cara de incidencia a la de desprendimiento o viceversa. El tamaño del redondeamiento dependerá de parámetros como el tamaño de grano abrasivo, la velocidad de corte o el tiempo de cepillado (entre otros).
El desarrollo de máquinas de 5 ejes junto con la variabilidad de geometrías de cepillos y abrasivos (Al203, SiC, CBN o PCD) han abierto las puertas a la posibilidad de generar un amplio espectro de geometrías y mecanizar gran variedad de materiales de herramienta. Sin embargo, el cepillado es un proceso que también requiere de prueba y error para conseguir la geometría de filo deseada.
2.4. ‘Drag-finishing’
El ‘drag-finishing’ es un proceso en el que la herramienta a mecanizar se sumerge en un medio abrasivo con partículas que pueden moverse libremente. Una vez sumergida, un mecanismo orbital mueve las herramientas de tal forma que el abrasivo choca aleatoriamente con éstas generando un perfil redondeado aproximadamente simétrico en el filo de corte. La magnitud del radio de filo depende, entre otros aspectos, del tipo de abrasivo, de la velocidad de movimiento del sistema planetario y del tiempo de mecanizado. Una de las grandes ventajas de este proceso es que facilita la preparación de herramientas con filos complejos como fresas o brocas enterizas.
3. Tecnologías de medida de la geometría del filo
El análisis de la microgeometría del filo de corte es realizado habitualmente mediante la obtención de perfiles perpendiculares a la dirección de la arista de corte (ver figura 4). Este tipo de medidas pueden llevarse a cabo empleando técnicas de contacto u ópticas. Las primeras emplean sondas que palpan la superficie de la herramienta siguiendo una estrategia de barrido para obtener un perfil 2D [9]. En caso de desear obtener perfiles adicionales, es necesario repetir el proceso.
Esta forma de funcionar es, precisamente, su mayor desventaja frente a los métodos ópticos cuyo resultado es un modelo 3D del filo que pueden obtenerse tantos perfiles 2D como se desee. Entre las tecnologías ópticas, las basadas en la proyección de microbandas han demostrado ser mejores [8], pero también se ha propuesto el empleo de otras técnicas como la microscopía confocal, la autofocalizacion o la interferometría.
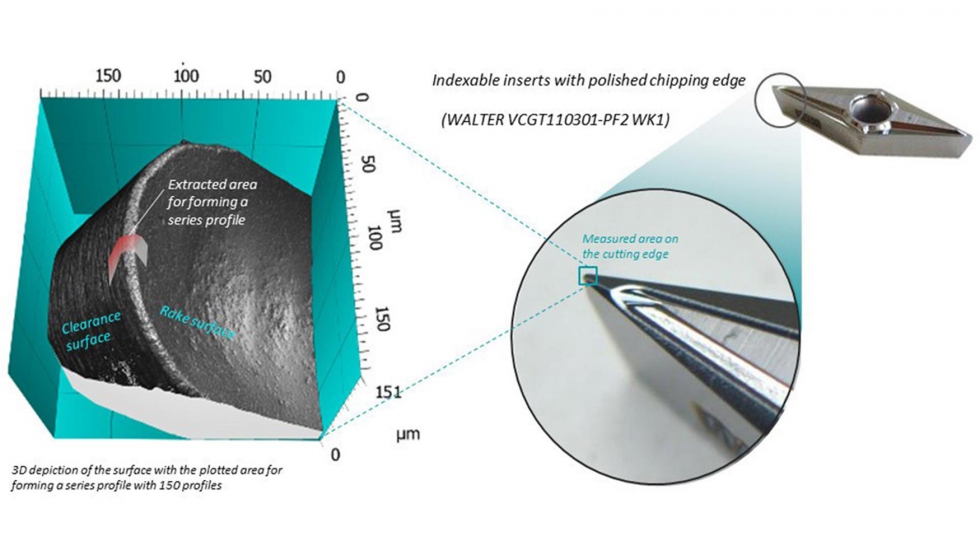
Figura 4. Medición 3D de la microgeometria de un filo de cort. Fuente: Confovis.
Un estudio realizado por varios centros de investigación tuvo como propósito comparar cinco técnicas de medida de la microgeometría del filo: la proyección de microbandas, la microscopia confocal, la inteferometría de luz blanca y dos técnicas de contacto [10]. Sorprendentemente, se observaron diferencias en los valores de radio de punta de la herramienta de hasta un 48% y, a día de hoy, no existe una metodología empleada mayoritariamente por la comunidad científica para medir la microgeometría de los filos de corte.
4. Metodologías para el tratamiento de los perfiles y la caracterización de la microgeometría del filo
Una vez obtenidos los perfiles con alguna de las tecnologías descritas en el apartado anterior, es necesario definir un procedimiento para tratar los datos obtenidos. El objetivo es obtener los valores de varios parámetros geométricos que nos permitan describir cómo es la forma del filo.
Para poder abordar este estudio es preciso distinguir entre los conceptos de macro-geometría y microgeometría. En pocas palabras, podríamos decir que la macrogeometría es la que hace referencia a la forma global de la zona de corte y estaría determinada por las superficies de incidencia y de desprendimiento (ver figura 5). Su forma la darían las tareas de tallado de la herramienta en las etapas anteriores a las de preparación del filo.
La microgeometría, por su parte, haría referencia a la zona de transición entre la superficie de incidencia y de desprendimiento. Para describir el límite de ambas zonas de forma más científica, podemos fijarnos en la evolución del ángulo de desprendimiento (γ). En la zona más alejada de la punta de la herramienta, podemos considerar que tenemos una superficie plana en la que el ángulo γ es constante. Si recorremos la superficie de desprendimiento aproximándonos a la zona de generación de la viruta, llegará un momento en el que este ángulo comience a variar (punto A en la figura 5). Este sería el límite entre ambas zonas.
![Figura 5. Sección transversal al filo de corte y distinción entre la macro-geometría y la microgeometría. Adaptado de [7]... Figura 5. Sección transversal al filo de corte y distinción entre la macro-geometría y la microgeometría. Adaptado de [7]...](https://img.interempresas.net/fotos/1617058.jpeg)
Figura 5. Sección transversal al filo de corte y distinción entre la macro-geometría y la microgeometría. Adaptado de [7].
La figura 6 muestra los tres tipos de microgeometría entre los que distingue la norma ISO 3002-1. La primera forma fundamental sería aquella en la que tenemos un borde perfectamente afilado (figura 6). En la práctica, fabricar este tipo de geometría sería inviable y, además, un filo extremadamente afilado sería muy poco tenaz. Es por ello por lo que se prefiere la geometría achaflanada o la redondeada (o una combinación de ambas). En el caso de la geometría achaflanada pueden encontrarse variantes con un único chaflán (figura 6) o con dos chaflanes. En ambos casos, la caracterización de la microgeometría es sumamente sencilla y basta con medir la longitud (lß) y el ángulo del chaflán (γß). El diseño achaflanado resulta apropiado, por ejemplo, en herramientas cerámicas para operaciones de corte interrumpido y con una elevada tasa de arranque.
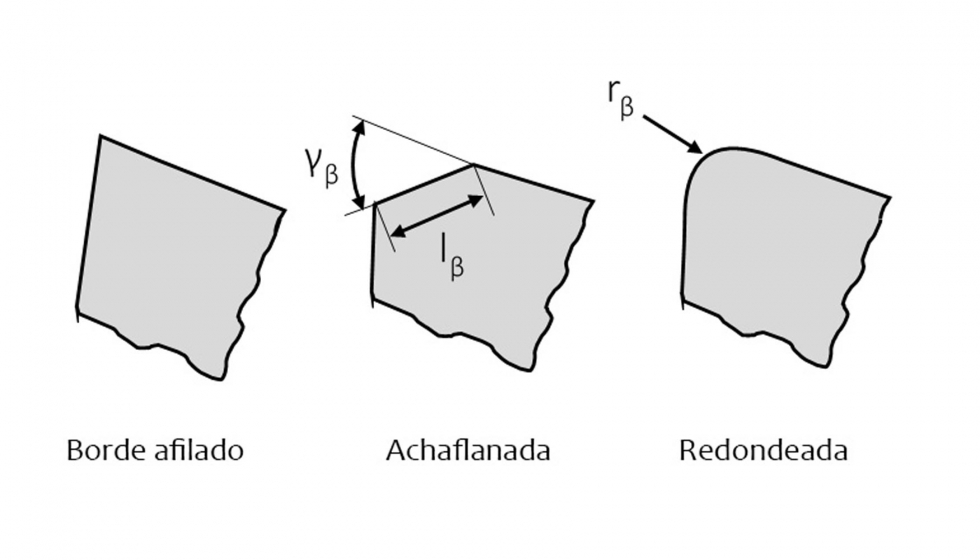
Figura 6. Formas fundamentales de la microgeometría del filo de corte.
Las herramientas con geometría redondeada son más complejas y su estudio requiere del uso de otros parámetros. Uno de los procedimientos más habituales consiste en representar la zona de la punta de la herramienta con un circulo y determinar el valor de su radio (rß). Sin embargo, el resultado es fuertemente dependiente de los puntos seleccionados para realizar el ajuste del círculo (ver figura figura 7). Además, no es adecuado para representar perfiles que poseen geometrías asimétricas que se alejan de la circular.
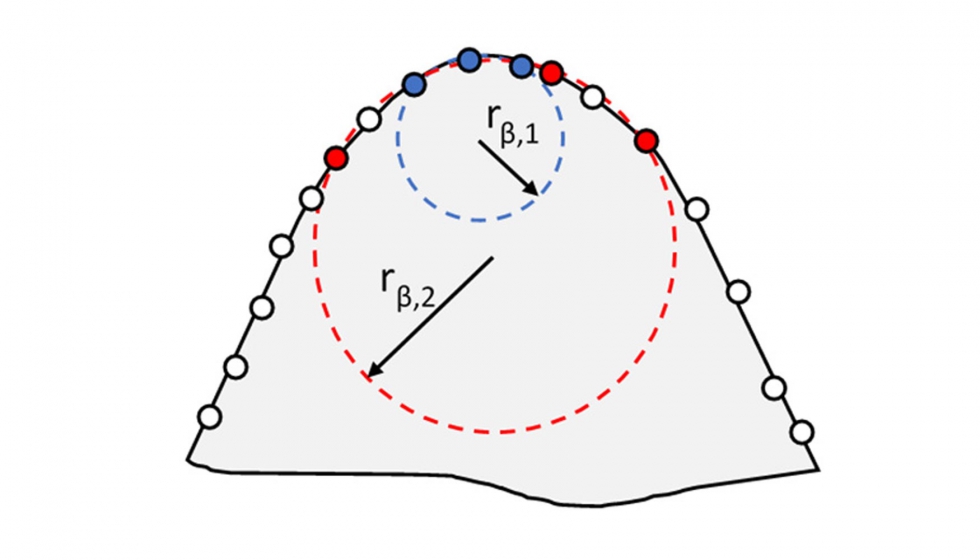
Figura 7. Caracterización de una microgeometría circular mediante el radio de punta.
En el caso de perfiles con una fuerte asimetría, la metodología más empleada es la propuesta por Denkena et al. [12] y que conocida habitualmente como el método del factor-K. En este caso, se emplean los segmentos Sα y Sß que representan la distancia desde la punta hipotética de una herramienta perfectamente afilada a las superficies de incidencia y de desprendimiento respectivamente (ver figura 8). El valor promedio de estos dos segmentos representará la magnitud del redondeamiento del filo y su cociente (K= Sß/Sα) la asimetría de éste. Adicionalmente el parámetro Δr es empleado para representar el achatamiento del filo. Sin embargo, los programas informáticos que tienen implementado el método del factor-K piden al usuario que defina manualmente los puntos que representan los límites de la microgeometría. Este hecho hace que el resultado dependa fuertemente de las decisiones tomadas por el operario.
Para hacer frente a este problema Wyen et al. [12] proponen una metodología que, mediante un proceso iterativo, define los límites de la microgeometría. En este caso se propone caracterizar el perfil a partir del radio de punta de un parámetro adicional que describe la desviación del circulo ajustado respecto de la posición simétrica. En cualquier caso, se ha de tener en cuenta que la representación del perfil asimétrico mediante un único circulo puede llegar a ser una simplificación excesiva. Una posible solución de compromiso podría pasar por aplicar el algoritmo iterativo de Wyen para detectar los límites de la zona a estudiar y emplear el método del factor-K para representar la microgeometría de la zona de corte.
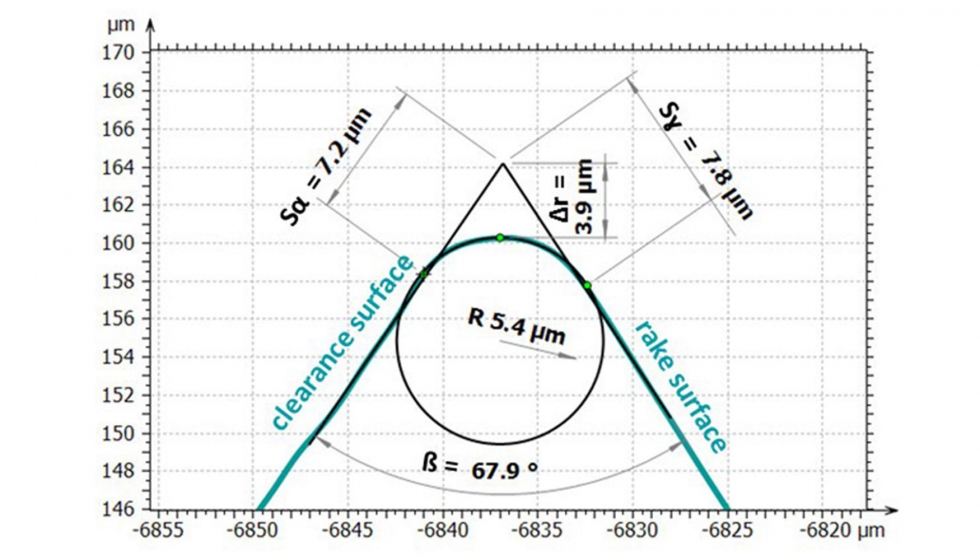
Las empresas nacionales también se encuentran en rápida evolución para dotar a los filos de corte de geometría más definida, mejor acabado y precisión. La posibilidad de controlar el filo permite una repetitividad y vida de herramientas elevadas. En este sentido, por ejemplo, la empresa Wolco está trabajando en estudiar el efecto para el mecanizado de superaleaciones. Las aleaciones de níquel son un campo donde el efecto del radio de filo y la eliminación de marcas de rectificado se ha visto más crítico.
5. Conclusión
El control de la geometría y el estado del filo de la herramienta es de vital importancia en las operaciones de mecanizado afectando a las fuerzas de corte, a las temperaturas y a otros muchos aspectos como el acabado superficial de la pieza. En este trabajo se han presentado diferentes alternativas para la preparación de la microgeometría de la arista de corte; parte del éxito del diseño de la herramienta dependerá de la selección de la más adecuada para cada aplicación. La verificación de la geometría del filo es fundamental, pero no existe una metodología ampliamente aceptada que sea independiente de las decisiones del operario. Se recomienda el usuario el empleo del método del factor-K, aunque es probable que veamos nuevos desarrollos en esta línea en un futuro no muy lejano.
Referencias
[1] E.M. Trent (1991), “Metal Cutting”, Butterworth Heinemann, ISBN 0-7506-1068-9.
[2] Biermann D, Terwey I (2008) Cutting Edge Preparation to Improve Drilling Tools for HPC Processes. CIRP Journal of Manufacturing Science and Technology 1:76–80.
[3] Byelyayev O (2008) Erhöhung der Leistungsfähigkeit von HSS-Spiralbohrern durch Einsatz der magnetabrasiven Bearbeitung, (Tesis doctoral) Otto von Guericke Universität, Magdeburg.
[4] Rech J, Yen Y-C, Schaff MJ, Hamdi H, Altan T, Bouzakis KD (2005) Influence of Cutting Edge Radius on the Wear Resistance of PM-HSS Milling Inserts. Wear 259(7–12):1168–1178.
[5] Aurich JC, Zimmermann M, Leitz L (2011) The Preparation of Cutting Edges Using a Marking Laser. Production Engineering 5:17–24.
[6] Ho KH, Newman ST (2003) State of the Art Electrical Discharge Machining (EDM). International Journal of Machine Tools and Manufacture 43(13):1287– 1300.
[7] Denkena B, Biermann D (2014) Cutting-edge geometries. CIRP Ann. Manuf Technol 63:631–653.
[8] Bassett E, Köhler J, Denkena B (2012) On the Honed Cutting Edge and its Side Effects During Orthogonal Turning Operations of AISI1045 with Coated WC-Co Inserts. CIRP Journal of Manufacturing Science and Technology 5:108–126.
[9] Thiele J-D, Melkote S-N (1999) Effect of Cutting Edge Geometry and Work-piece Hardness on Surface Generation in the Finish Hard Turning of AISI 52100 Steel. Journal of Materials Processing Technology 94:216–226.
[10] Davies MA (2008) CIRP General Assembly. Minutes STC ‘‘C’’, Manchester, 29th August.
[11] V.P. Astakhov (2006), “Tribology of metal cutting”, Tribology and interface engineering series, Nº 52 London: B. J. Briscoe. Elsevier.
[12] Wyen CF, Knapp W, Wegener K (2012) A new method for the characterisation of rounded cutting edges. Int J Adv Manuf Technol 59:899–914. doi: 10.1007/s00170-011-3555-4
[13] Fischer H (1897) Die Größe der Widerstände gegen das Abheben von Metall-spänen. VDI-Z 41(18):504–508
Recubrimientos avanzados: garantía de vida de la herramienta
El mecanizado de la herramienta con materiales cerámicos es, sin duda, la mejor alternativa para proteger al sustrato frente al desgaste. Tal es así que el 50% de las herramientas de acero rápido y el 85% de las herramientas de metal duro usadas en la industria se recubren [11] dando lugar a un ahorro que se estima en miles de millones de euros.
El sector aeronáutico es uno de los máximos beneficiarios de las herramientas recubiertas debido al empleo de materiales de baja maquinabilidad, condiciones de trabajo exigentes y a la demanda de una mejor calidad de las superficies mecanizadas. En este contexto, el poder contar con recubrimientos diseñados a medida para cada aplicación es, sin duda, una gran ventaja competitiva. La agrupación empresarial del Centro de Fabricación Avanzada Aeronáutica (CFAA) cuenta entre sus miembros con Metal Estalki con dilatada experiencia en el diseño de nuevos procesos de deposición de recubrimientos PVD. Por ejemplo, el recubrimiento de brocas para el taladrado de Inconel 718 (ver figura 9) permitió reducir la adhesión del material al filo y aumentar la vida de la herramienta en más de un 50%. Metal Estalki colabora estrechamente con el fabricante Platit que destaca por su éxito en la reducción de los ‘droplets’. Este defecto supone un verdadero problema en esta tecnología pues aumenta la rugosidad en la superficie de la herramienta.
El taladrado de aeroestructuras de compuesto es otra de las aplicaciones más exigentes del sector ya que las fibras de carbono presentan una dureza extrema y un comportamiento abrasivo. En este caso, el empleo de recubrimientos de diamante se ha comprobado que es una muy buena solución, aunque únicamente es posible en calidades de metal duro con un contenido en cobalto por debajo del 10%. Un ejemplo de este tipo de recubrimientos es el K-Fiber de Kendu que presenta una estructura multicapa con una dureza de en torno a 10.000 HV. Esta empresa, colaboradora también con el CFAA, se caracteriza por su intensa actividad de I+D y entre sus novedades más recientes cuenta con un nuevo recubrimiento K-CROM+, de estructura nano-composite y base AlCrN yque es aplicable en aceros hasta 55HRc, en inoxidables o en aleaciones de base Níquel. Sin dunda, la relación entre el usuario final, el fabricante de herramientas y el recubridor será una de las claves del éxito para hacer frente a los nuevos retos de la industria aeronáutica.
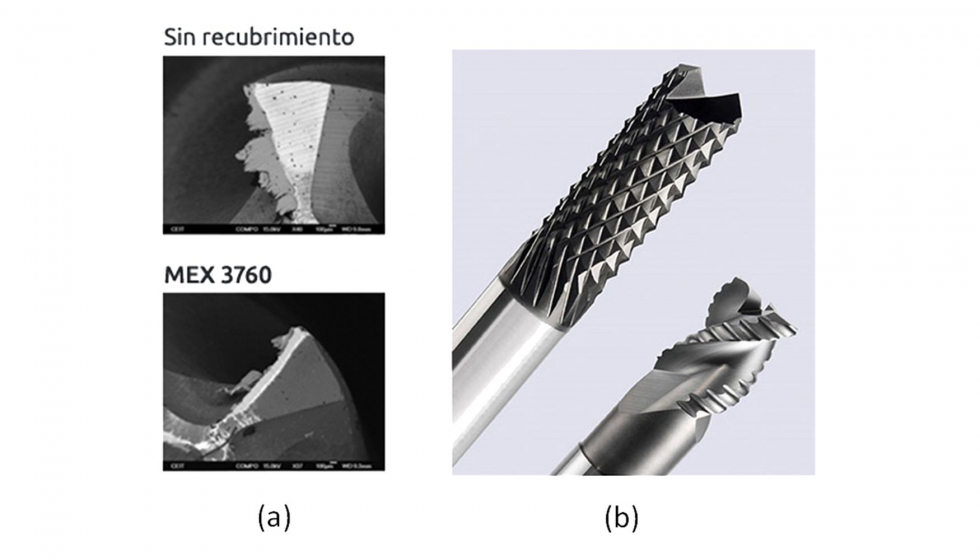