Indaero consigue nuevos negocios con proveedores de Airbus gracias a la impresión 3D
Indaero, empresa española de ingeniería aeroespacial, se ha asegurado nuevos negocios con varios proveedores de primer y segundo nivel (Tier 1 y Tier 2) de Airbus gracias al uso de la impresión 3D FMD de Stratasys para la producción de útiles complejos.
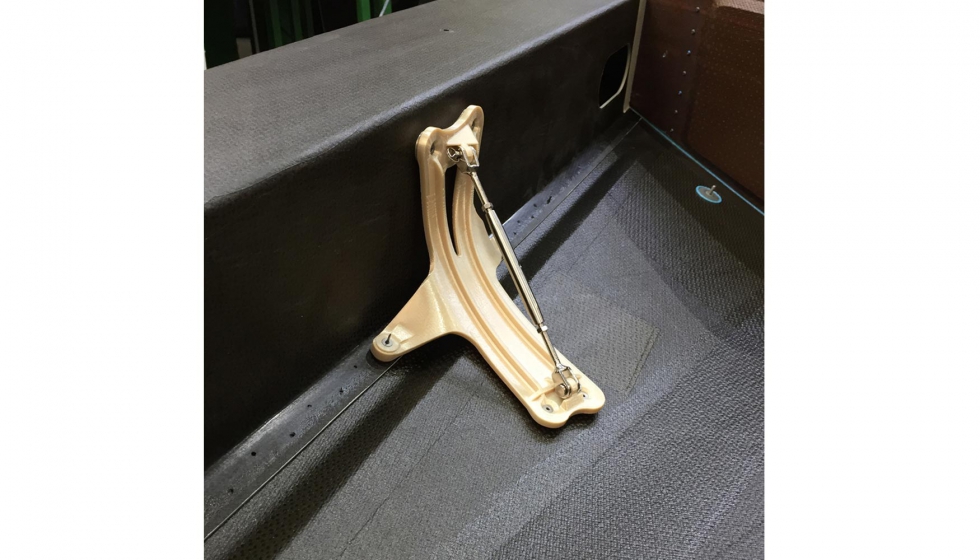
“El sector aeroespacial, a diferencia de otros sectores, produce grandes volúmenes de útiles", explica Darío González Fernández, director general de Indaero. “En la fabricación tradicional de útiles de producción, utilizaríamos mecanizado por CNC, proceso que supone un gran gasto de tiempo y dinero. Con nuestra impresora 3D Fortus 450mc, podemos ocuparnos de la producción de bajo volumen de forma rápida y económica, realizando muchos útiles diferentes a petición para acelerar el proceso de fabricación y garantizar el cumplimiento de los plazos de entrega del cliente.
“Tampoco se puede subestimar la importancia del material Ultem 9085”, prosigue. “Se ha convertido en un componente esencial de nuestro proceso de producción ya que cuenta con certificación para el sector aeroespacial; además, nuestro cliente Airbus conoce bien sus prestaciones para una serie de aplicaciones de aviones. Gracias a su exclusiva combinación de alto ratio resistencia/peso y certificación FST (llama, humo y toxicidad), podemos imprimir en 3D útiles resistentes y ligeros, y producir tiradas cortas de piezas de avión si es preciso, lo que nos proporciona una ventaja competitiva decisiva”.
Útiles ‘curvos’ y complejos impresos en 3D que contribuyen a aumentar el volumen de negocio
“La impresora 3D ha supuesto toda una revolución para nosotros”, comenta González. “La posibilidad de imprimir en 3D útiles de producción curvos en materiales resistentes nos ha hecho darnos cuenta de lo importante que es contar con útiles que se adapten perfectamente a los paneles. Esto no solo facilita el trabajo de nuestros operarios, sino que también libera recursos y mejora nuestra productividad general. Algunos de los principales proveedores de Airbus han reconocido inmediatamente esta mejora. Es el caso de Aernnova, que antes trabajaba con la competencia y cuyo negocio nos hemos asegurado”.
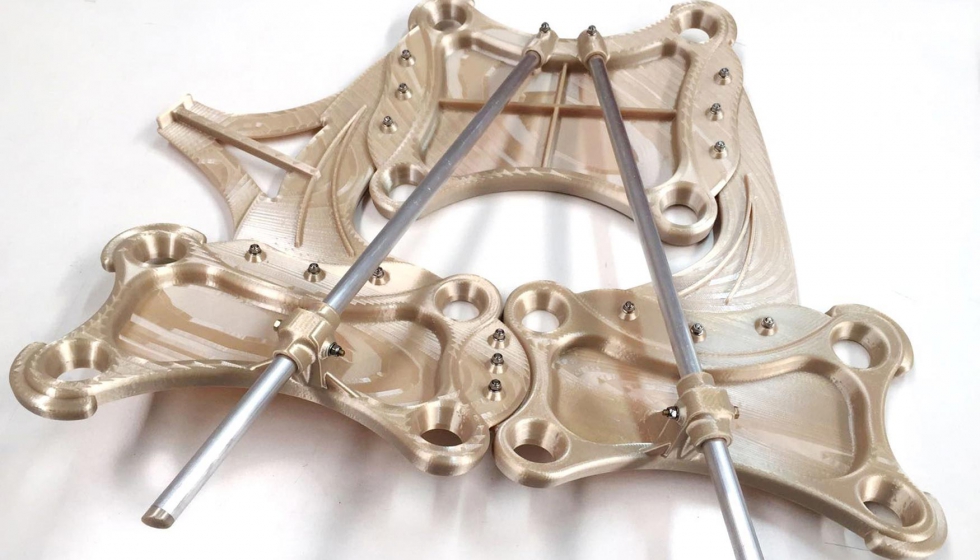
“La integración de la impresión 3D FDM en el proceso de fabricación de útiles de producción para este proyecto ofrece varias ventajas claras", explica González. “En primer lugar, desde la perspectiva de los recursos humanos, ya no se necesitan dos operarios porque el útil se acopla al panel de forma independiente, con lo que solo se necesita un operario que tiene las dos manos libres para colocar la caja flexible. En segundo lugar, podemos producir un útil resistente y ligero un 66 % más rápido que con el mecanizado por CNC. En consecuencia, esta parte del proyecto se completa con antelación, lo que conlleva una reducción del coste de fabricación de más del 50 %. Como es natural, el cliente está encantado”.
Andy Middleton, presidente de Stratasys para EMEA, concluye: “FDM es desde hace tiempo la tecnología aditiva preferida del sector aeroespacial, especialmente para aplicaciones de útiles personalizados. Las empresas como Indaero están aprovechando materiales de alto rendimiento, como Ultem 9085, para producir útiles más ligeros y con mejor rendimiento en menos tiempo y de forma más económica. No es ninguna sorpresa que estas empresas, que tienen visión de futuro, mejoren su rendimiento como resultado”.
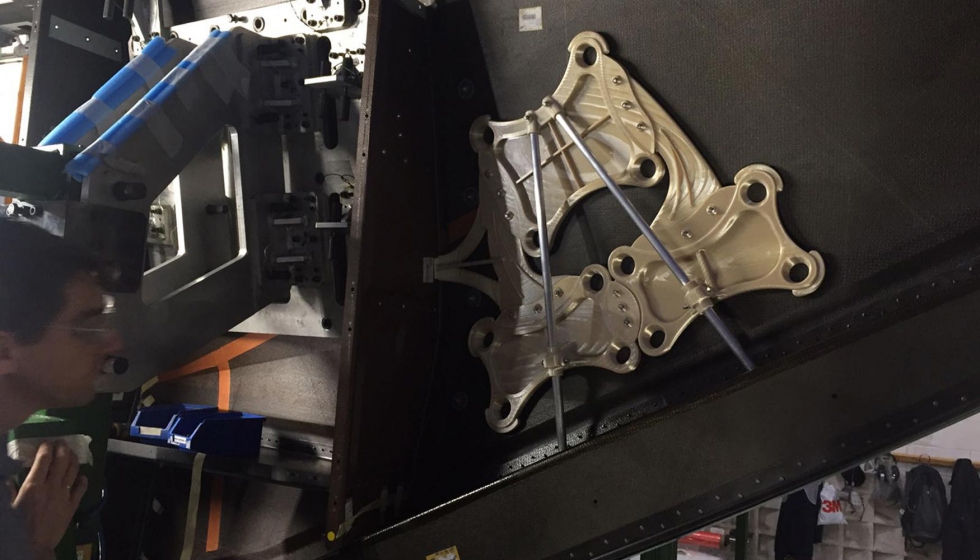