Danobat desarrolla en Australia el taller de reparación de trenes automatizado más avanzado del mundo
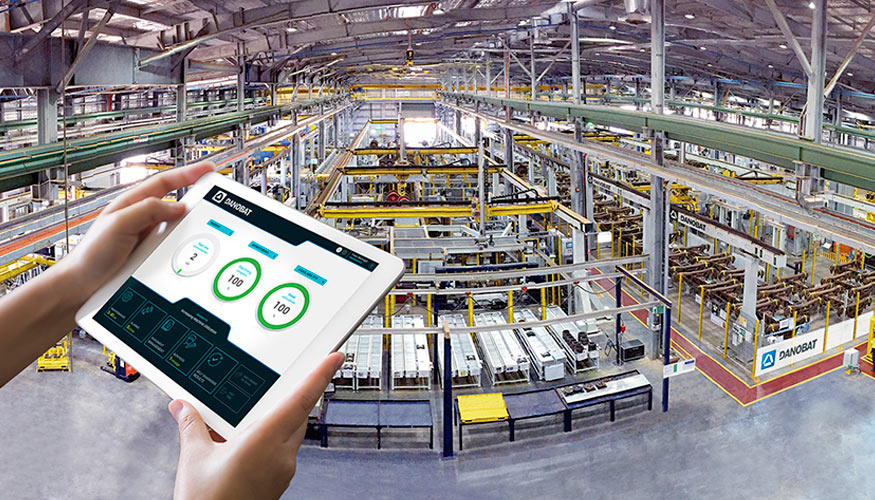
En el desierto de la región australiana de Pilbara son habituales las temperaturas superiores a los 45 grados. La zona es conocida por haber rebasado los 38 grados durante más de 160 días consecutivos. En este inhóspito rincón del planeta, de extremas condiciones climáticas y abundante en recursos minerales, es donde la empresa vasca Danobat se ha enfrentado al reto tecnológico de desarrollar un taller digital completamente automático destinado al mantenimiento de vagones de mercancías.
La instalación, con capacidad para reparar un vagón cada 28 minutos, es la solución de mantenimiento de trenes totalmente automatizada más avanzada del mundo y ha sido diseñada para la multinacional BHP Billiton, líder mundial en el sector minero.
El taller, que ha supuesto el salto tecnológico definitivo de la cooperativa vasca al nuevo paradigma de la fabricación digital, ya se encuentra operativo y ha sido presentado esta mañana en un acto celebrado en la sede del fabricante de máquina herramienta y sistemas de producción, que ha contado con la presencia de la consejera de Desarrollo Económico e Infraestructuras del Gobierno Vasco, Arantxa Tapia.
El proyecto, que ya ha entrado en operación, está ubicado en un área aislada y localizada a 1700 kilómetros de la ciudad más próxima. El emplazamiento responde a la necesidad de instalar el taller en una zona próxima al lugar por el que los trenes realizan su recorrido, un área en la que, además del desgaste habitual que sufren los trenes a lo largo de su vida útil, están sometidos al rigor climatológico.
La solución ha sido diseñada con el objetivo de realizar la reparación de los trenes destinados al transporte de minerales desde las áreas de extracción hasta las terminales portuarias, sin necesidad de intervención humana, salvo para las operaciones de programación, mantenimiento e inspección.
Uno de los principales desafíos a los que se han enfrentado los ingenieros y expertos de Danobat ha sido la necesidad de desarrollar una solución integral en la que los vagones pudieran entrar, ser desmontados en piezas, reparados y posteriormente reensamblados de forma completamente automatizada en un tiempo de 28 minutos.
“El taller de mantenimiento ferroviario de Danobat en Australia es la instalación para la reparación de vagones más avanzada del mundo y, aunque no ha sido nuestro primer proyecto ferroviario con sistemas de control inteligentes, sí ha supuesto para nosotros la transición definitiva al nuevo escenario de la fabricación digital. El desarrollo de este proyecto ha conllevado el impulso de perfiles profesionales altamente cualificados y la generación de una red de proveedores de elevada capacitación en Euskadi”, ha asegurado Xabier Alzaga, director gerente de Danobat.
El contrato entre Danobat y BHP, que ha sufrido diversas ampliaciones desde el inicio del proyecto en 2013, ha alcanzado una cifra total superior a los 100 millones de euros.
BHP Billiton, quinta empresa mundial por capitalización bursátil y fruto de la fusión de la australiana Broken Hill Proprietary y la británica Billiton, se dedica a la producción de materias primas como cobre, mineral de hierro, níquel y plata.
La compañía, que apuesta por la diversificación en producto, geografía y mercado, también trabaja en la industria del petróleo y gas.
El taller está dividido en cuatro áreas diferenciadas dotadas con su propio equipamiento y sistemas de manipulación automática para llevar a cabo los trabajos de mantenimiento de los vagones, de los bogies y de los ejes montados.
El conjunto es una solución integral de fabricación compuesta por una línea principal para la inspección y desmontaje, un taller de reparación de bogies, un espacio para el mantenimiento de las ruedas y un taller de estructuras. La instalación también lleva a cabo la inspección final de todos los componentes y reporta información relativa al proceso de fabricación de cada componente.
Con la misión de ejecutar con éxito todos los trabajos, el taller está equipado con soluciones digitales completamente inteligentes desarrolladas por el fabricante vasco como el Danobat Control System, un desarrollo que permite la monitorización, supervisión, control y gestión integral de la totalidad del proceso de mantenimiento y de las operaciones que se llevan a cabo en el taller.
Los trabajos de desmontaje, reparación y ensamblaje automático de las piezas requieren de una coordinación absoluta de todos los equipos. El flujo de los vagones, los bogies o los ejes montados puede variar en función de los resultados detectados durante las etapas de inspección y medición. Por este motivo, es clave disponer de un centro de control integral que coordine todas las operaciones y que garantice la reparación completa de los vagones cada 28 minutos, intervalo en el que se repara un vagón, 2 bogies y 4 ejes montados.
Asimismo, los equipos integrados en el taller disponen del SMART HMI, una interfaz inteligente, desarrollada también por la firma guipuzcoana, que aporta ayudas al operario para el manejo de las máquinas, permite optimizar sus operaciones y hace posible la mejora de la disponibilidad y fiabilidad de los equipos.
Además, los equipos de este taller disponen del Intelligent Data System, una solución que permite el control inteligente de la propia máquina y mejora la toma de decisiones. Las máquinas del taller están equipadas con sensores que captan datos sobre su funcionamiento y sobre el estado de las piezas. Toda esta información queda almacenada para poder analizar tendencias de uso y realizar una programación inteligente de los trabajos futuros. El Intelligent Data System permite emitir notificaciones automáticas de las labores de mantenimiento y realizar operaciones de autodiagnóstico.
“Este taller destaca por su elevada productividad y por una automatización completa de las operaciones con los más estrictos estándares de calidad y seguridad. Además está dotado de equipamientos en línea con el paradigma de las fábricas inteligentes y cumple con los requisitos de la fabricación cero defectos”, agrega Alzaga.
El desarrollo de esta solución se enmarca en la apuesta del grupo industrial Danobat Group, al que pertenece la cooperativa Danobat, por el desarrollo de sistemas de alto valor añadido basados en la aplicación de las tecnologías de la información y la comunicación a las plantas productivas y a los entornos de fabricación. La digitalización de los procesos industriales constituye una de las líneas prioritarias de investigación de Danobat Group.