Fabricación digital como catalizador de la innovación
‘Smart Industry’ es un concepto usado con frecuencia para designar a los dispositivos completamente digitalizados e integrados, ya sean máquinas de producción o procesos empresariales en toda la cadena de suministro. Esto permite a las compañías ofrecer productos personalizados y servicios al menor coste posible, gracias a una capacidad de producción extremadamente flexible. Esta revolución industrial recibe múltiples nombres, en algunos mercados la denominan Industria 4.0 o industria del futuro y, en otros, es más conocido el concepto de transformación digital.
Este último término refleja muy bien el reto de implementar el concepto de Smart Industry: digitalizar todo lo manual y eliminar los procesos basados en el papel. La mayoría de las compañías industriales todavía está comenzando su transformación. En otras empresas sólo algunos de sus departamentos como los de diseños o ingeniería trabajan (completamente) de forma digital. En los próximos años estas compañías tendrán que digitalizar e integrar también los procesos de pruebas y de producción, algo que sin duda será una labor difícil.
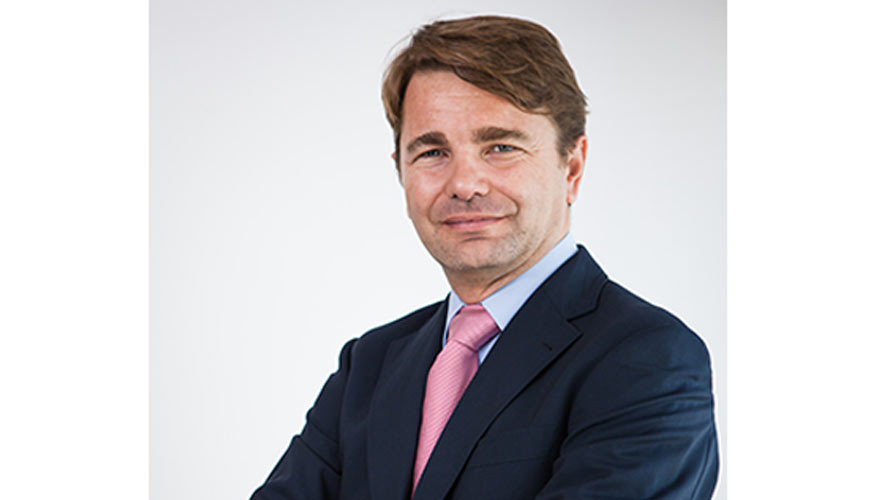
Una innovación más rápida
Otra ventaja de la Industria 4.0 es la oportunidad de lanzar nuevos productos y servicios al mercado de forma mucho más rápida. Cuando los empleados de ventas, diseñadores, ingenieros, trabajadores de producción y proveedores pueden trabajar juntos y de forma simultánea usando la misma información en tiempo real, pueden crear y aprovechar sinergias. Esto aumenta la innovación y reduce los ciclos de desarrollo, de producción y el tiempo de llegada al mercado.
Además, en este entorno los fabricantes están constantemente recopilando datos, no solo durante la producción, también durante otros procesos relacionados con el producto. Por ejemplo, reciben feedback desde todo tipo de sensores y gracias a este feedback se adaptan a las cambiantes necesidades del mercado y es más sencillo para ellos optimizar los procesos operacionales. Tan pronto como el conjunto de información es procesada y analizada, los clientes y proveedores operan en una cadena con valor optimizada.
Las pruebas digitales
Cuando ya se han completado las fases de diseño y desarrollo, el nuevo producto o sistema todavía tiene que ser probado. Esto es a menudo un proceso largo y caro como, por ejemplo, vemos en la simulación de accidentes en la industria de automoción. No obstante, el software de simulación 3D es ya tan preciso y fiable que incluso las pruebas de accidentes se están realizando digitalmente, reduciendo al máximo la necesidad realizar pruebas físicas.
Con la digitalización de productos y sistemas se puede ahorrar notablemente en costes y tiempos. Cuando estas pruebas son dirigidas en un entorno de simulación 3D, se ofrece a todos los implicados del proceso de desarrollo una experiencia realista. Esto ayuda a las compañías a tener una mejor percepción de la operación y ganar facilidad de uso en unos productos y sistemas que cada vez son más complejos.
Producción digital
Cuando un nuevo producto o sistema ha sido probado a fondo, se pasa a la producción. La simulación 3D proporciona beneficios en esta fase ya que permite a las compañías planificar al detalle todos los procesos de la planta y la cadena de suministro. Administrar materias primas, piezas, máquinas y otros recursos es más eficiente cuando cada acción es validada en un entorno 3D.
Este método también reduce el riesgo de errores y defectos. Tener toda la información del producto disponible en el lugar y de forma transparente tiene otra ventaja importante: se puede evaluar la aplicabilidad de las técnicas de producción, como la impresión 3D, y el uso de robots avanzados y, tras la validación, implementarla en los existentes procesos de producción.
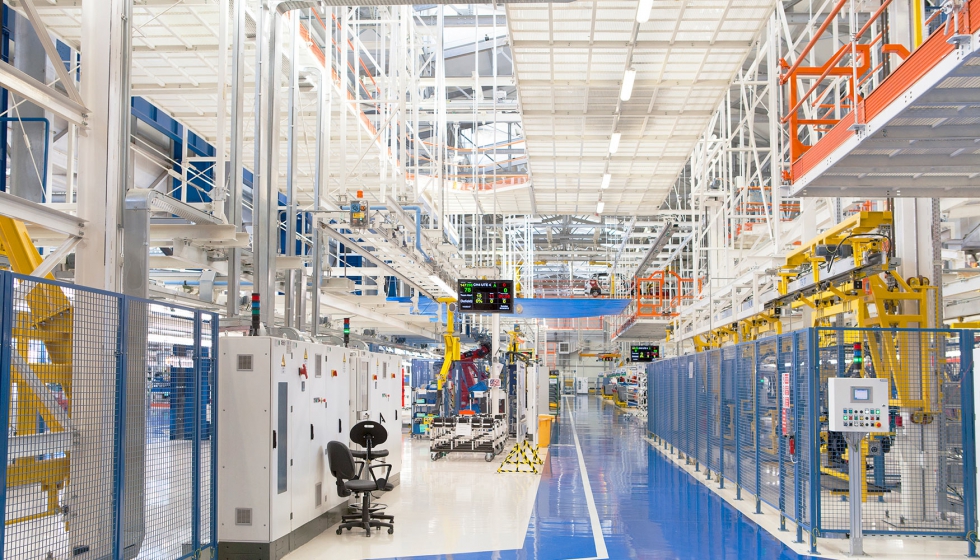
El resultado: máquinas inteligentes
En la feria Hannover Messe 2016, Claas, el fabricante alemán de maquinaria agrícola mostró cómo utiliza la plataforma 3DExperience y la industry solution experience de Dassault Systèmes, ‘Single Source for Speed’, para el desarrollo y la producción de sus máquinas inteligentes. Claas trabajaba con diferentes sistemas e interfaces que necesitaban actualizaciones regulares. Esto ha sido reemplazado por una plataforma unificada de innovación que es fácilmente accesible para todas las partes implicadas, en cualquier momento y en cualquier lugar del mundo.
La plataforma permite a Claas intensificar la experiencia del usuario y responder a las necesidades del cliente de forma más rápida. En el negocio de la fabricación de maquinaria, es esencial que todas las partes implicadas puedan colaborar y compartir información desde la fase de desarrollo. Además, esta tecnología permite a Claas conducir las pruebas y la producción de las simulaciones en 3D. Como resultado, los gastos y el número de errores son reducidos de forma significativa.
Para el futuro: programas de innovación industrial
Cada vez más gobiernos están mostrando su apoyo a los programas de innovación industrial para llevar a cabo la transformación digital de la industria de fabricación, colaborando estrechamente con empresas claves del sector. Por ejemplo, China lanzó la iniciativa ´Made in China 2025´ para acelerar la transformación industrial poniendo gran atención en el uso de plataformas digitales. Países Bajos impulsó un programa similar con el nombre de ‘Smart Industry’ y en Francia una iniciativa ligeramente distinta es denominada ‘Industry of the Future’. La necesidad de transformar ha sido reconocida a escala mundial, aunque solo el tiempo pueda decir qué países emergerán como líderes en la época de la producción digital.