Empire Cycles confía en las herramientas WNT para un nuevo modelo de competición de descenso
Después de haber recibido varios productos y el apoyo técnico de WNT UK en el desarrollo de sus grandes proyectos de bicicletas de carretera, incluyendo la primera bicicleta impresa en 3D del mundo, Empire Cycles cuanta una vez más con el especialista en herramientas ubicado en Sheffield en la preparación de su último modelo VX8.
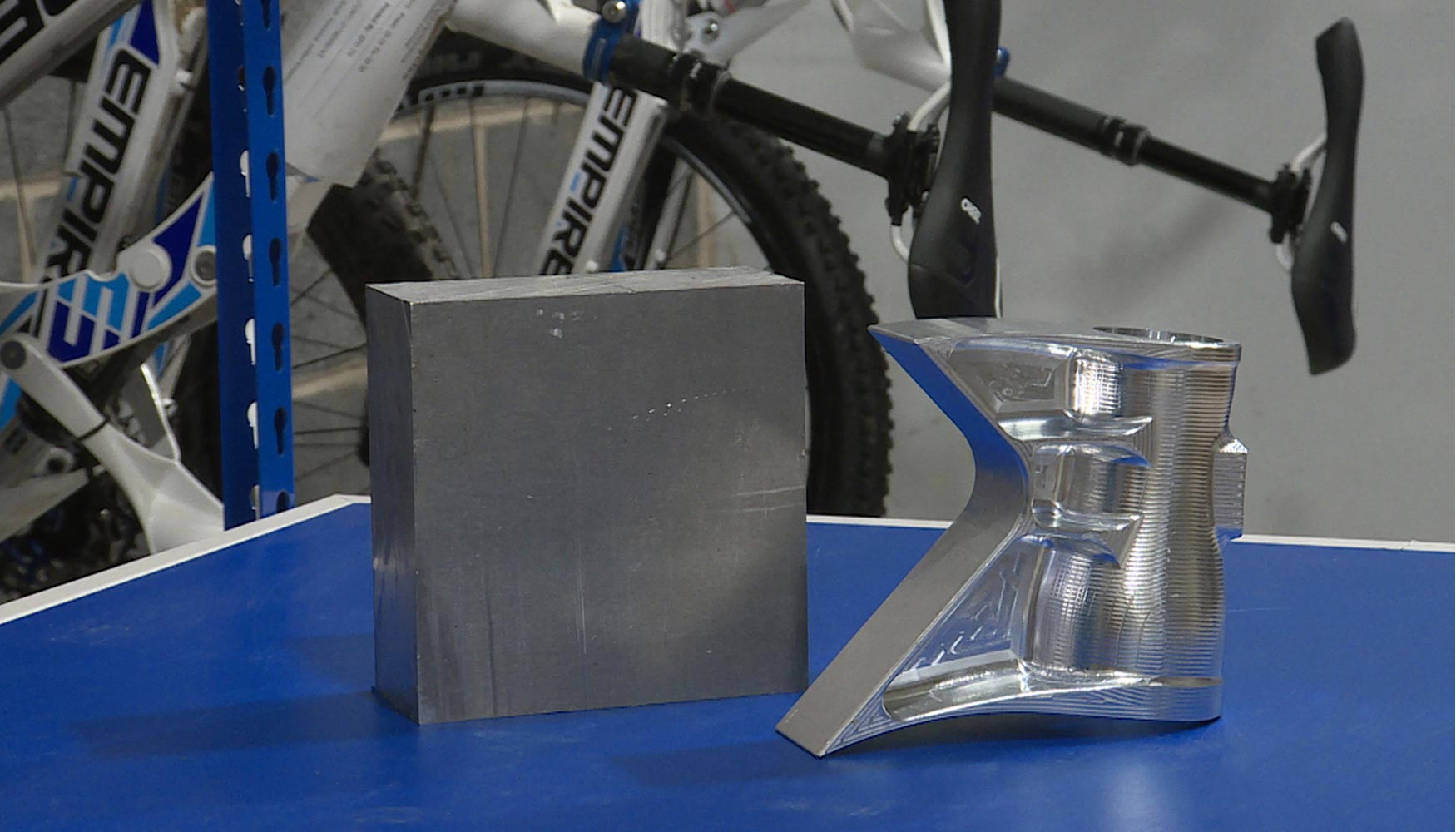
El modelo de bicicleta VX8 diseñado por Empire Cycles para la competición de descenso, hará uso de algunos componentes del modelo MX6 anterior pero también cuenta con varios elementos clave que se han diseñado específicamente para él, incluyendo un tubo de dirección totalmente nuevo y mecanizado que conecta las horquillas delanteras con el resto del cuadro. El tubo de dirección está mecanizado para reducir el peso y mejorar el rendimiento, pero el complejo resultado trajo consigo problemas de fabricación. El punto clave de venta de la gama de Empire es que está diseñada, mecanizada, y fabricada en el Reino Unido, en las instalaciones de Empire en Bolton. Esto es vital para mantener el control de los costes laborales y los prototipos iniciales de los tubos de la horquilla que tardaban en mecanizarse 1 hora y 50 minutos, que no daba un resultado final rentable.
“Idealmente, una parte de esta complejidad se mecaniza, en una sola operación, en un centro de mecanizado de cinco ejes, pero Empire solo dispone de un centro de mecanizado de tres ejes. Si bien esto era correcto para los prototipos iniciales, el ciclo de cerca de dos horas y la ineficiente manipulación de piezas, no eran comercialmente viables una vez se puso la producción en marcha", dice Tony Gale, técnico de aplicaciones. Como la inversión en la capacidad de la máquina de cinco ejes no era una opción, se contactó con WNT para revisar el proyecto y proporcionar un proceso viable dentro de los límites de capacidad de la máquina de tres ejes, añadiendo el reto de disminuir el tiempo de producción en menos de una hora.
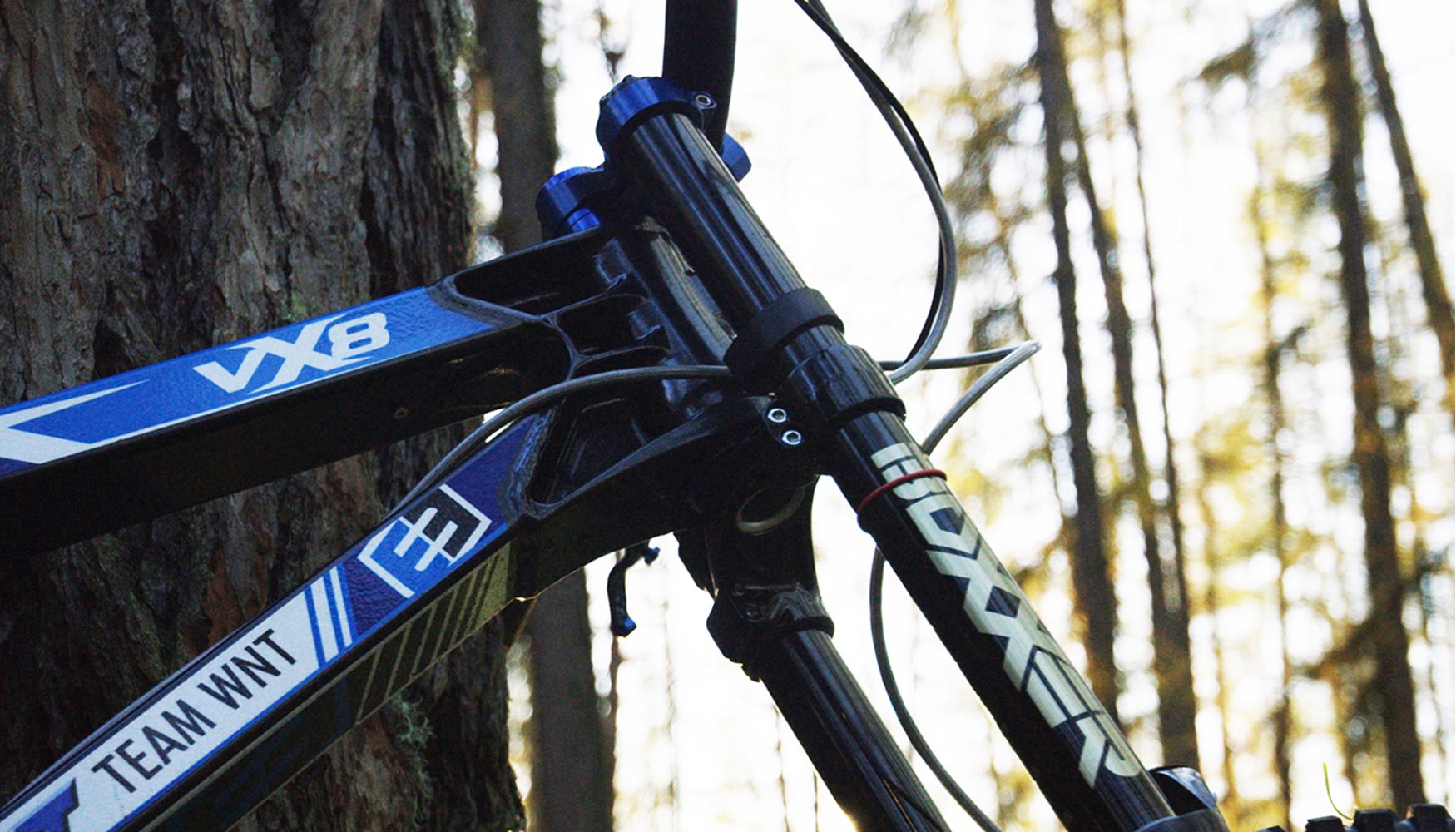
El primer paso era llevar los componentes al centro técnico de WNT en Sheffield, dónde Tony Gale y Billy Poore, también técnico de aplicaciones, podían trabajar en un proceso más eficiente, y que fuera fácilmente transferido de nuevo a Empire una vez finalizado. Resultó una buena oportunidad para los dos para pensar libremente y ser creativos con la gama de los sistemas de sujeción de piezas y herramientas de WNT. Tras la debida consideración, la solución era romper el proceso en cuatro operaciones obteniendo, al final de cada ciclo, dos componentes mecanizados. Toda la sujeción de piezas sería colocada en un soporte WNT Zero Point. La primera operación deja ver las molduras de aluminio sujetas en un par de tornillos WNT ZSG céntricos, de modo que los puntos de ubicación del tapón de ajuste de Zero Point podrían ser mecanizados para la segunda operación. Una vez finalizadas las partes, éstas se transfieren a un soporte WNT Zero Point para la segunda operación. Aquí es dónde el perfil exterior y el hueco son desbastados y acabados de mecanizar usando las fresas de metal duro Type W de WNT. Después de esta secuencia de mecanizado, las piezas se giran 90 grados para perforar y terminar el agujero principal del componente y con la operación final se consigue el desbaste y acabado del segundo lado de la pieza.
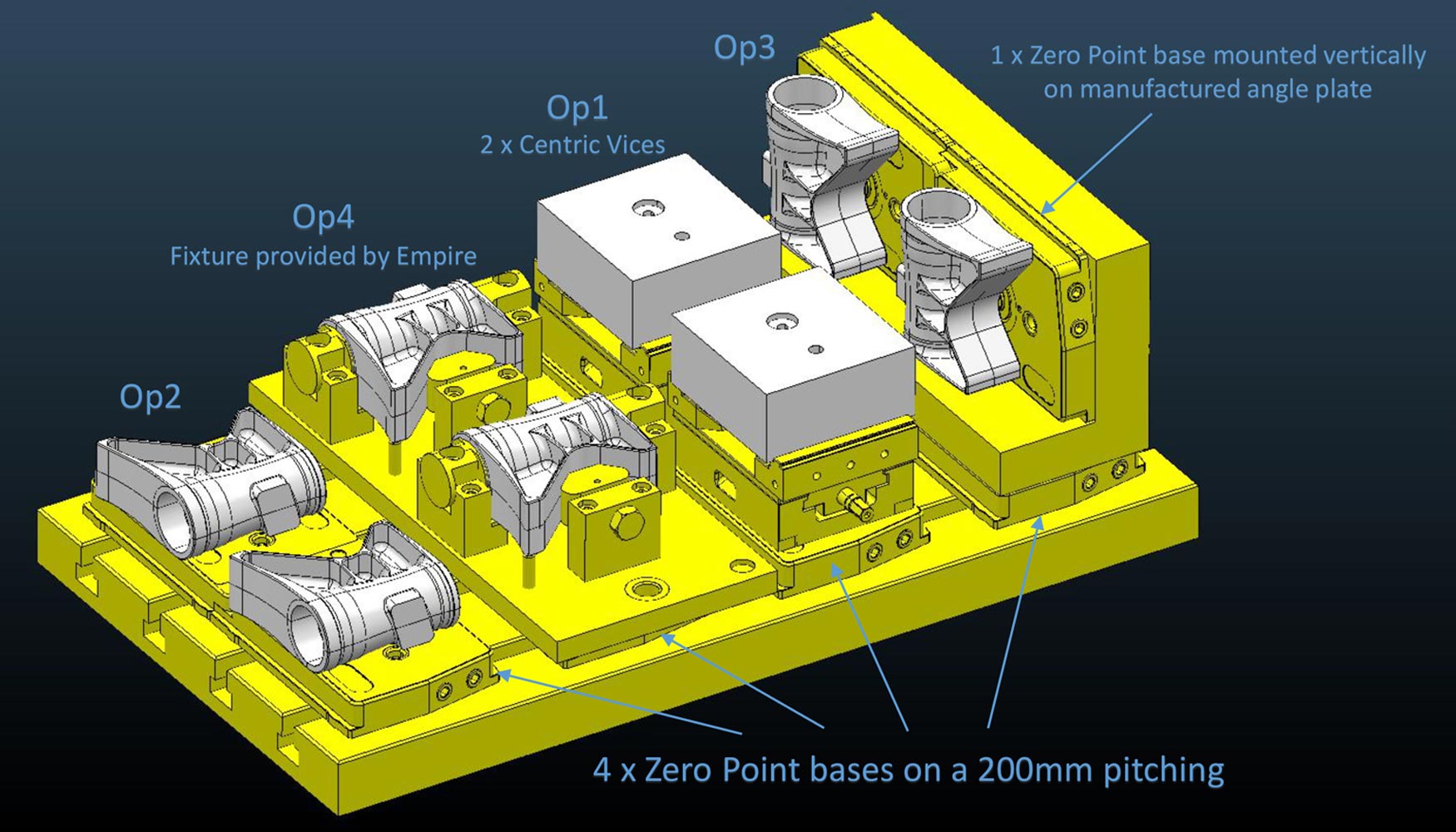
Las innovadoras fresas Type W cuentan con un acorde perfil redondo y un trabajo especial que genera pequeñas virutas que pueden ser fácilmente evacuadas de la zona de corte con la ayuda de un suministro estándar de refrigerante a través de la herramienta y con un final geométrico de los cortadores. Esto permitió las operaciones de desbaste en este proyecto, utilizando una fresa toroidal, para llevar a cabo velocidades de husillo de 11.000 rev/min y un avance de 2.500 mm/min. Las fases de acabado utilizan una variante de punta esférica de la fresa Type W con una velocidad de 10.000 rev/min. y una avance de 2.000 mm/min. Estos datos de corte y proceso significaban que dos piezas acabadas se crean a partir de una moldura sólida en solo una hora y diez minutos, o 35 minutos por cabezal o tubo de dirección. Esto supone una reducción del tiempo en un 68% comparado con el proceso original y casi el 50% del tiempo final establecido por Empire para que el proyecto sea comercialmente aceptable.
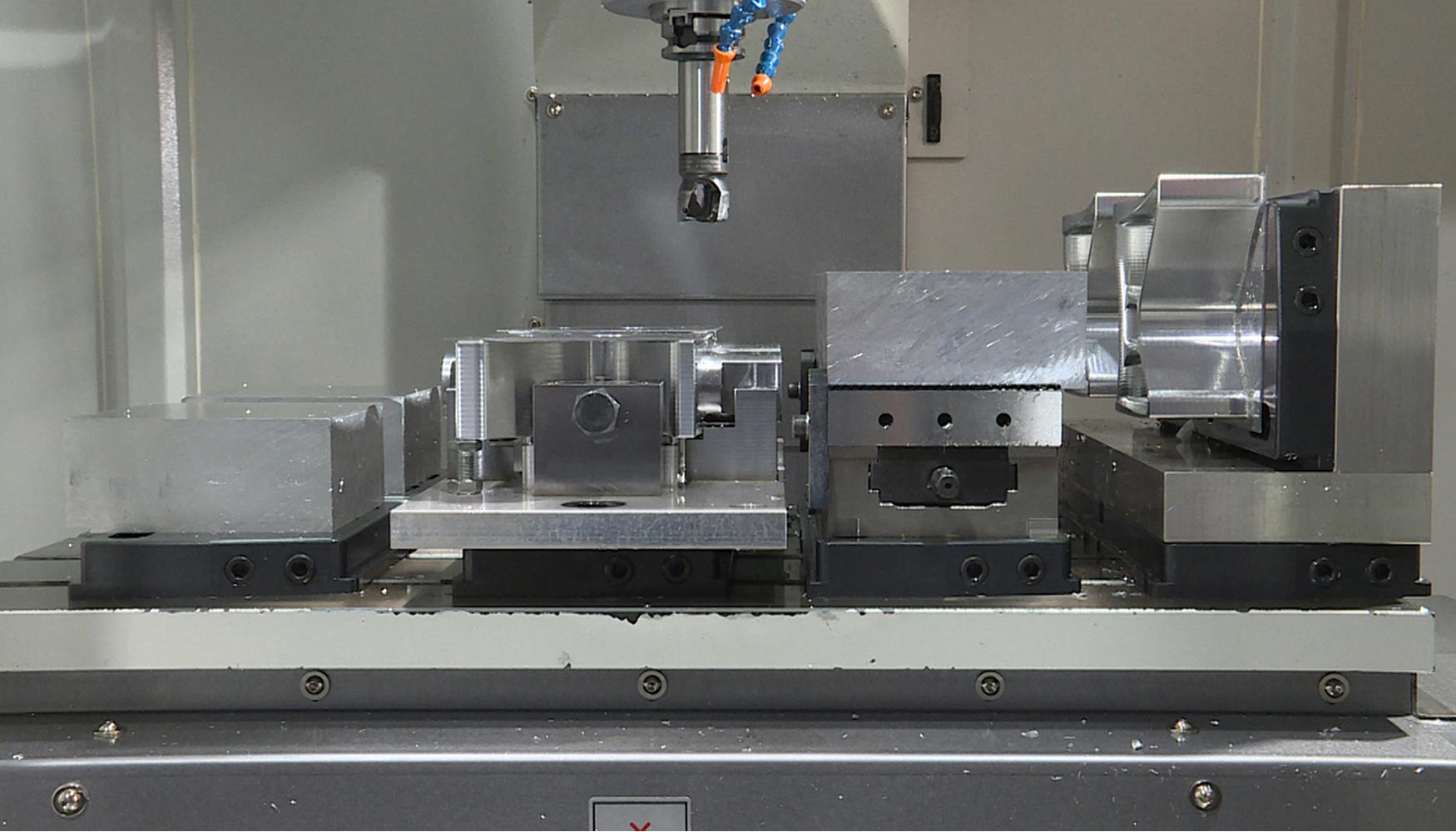
“Esto fue un reto fascinante para nosotros, para asumir que no todos pueden, o tienen la necesidad, de permitirse el lujo de invertir en centros de mecanizado de cinco ejes, pero al no tenerlos pueden tener que rechazar algunos tipos de trabajo. Mediante el uso de productos existentes en la gama de WNT y algunas ideas creativas, hemos proporcionado una alternativa que dará a Empire, y a otros clientes, la oportunidad de maximizar la capacidad existente con sus máquinas de tres ejes. Ya hemos invertido significativamente en nuestro equipo de soporte de aplicaciones, área que verá mayor desarrollo. Estamos viendo un gran interés por parte de los clientes que quieren hacer uso de nuestra experiencia interna, y como una gran ventaja para ellos es que podemos desarrollar estas nuevas estrategias de mecanizado y procesos en su nombre y lejos de sus máquinas, lo que significa que no pierden tiempo de producción. Todo el proceso es, en efecto, sin ningún riesgo para ellos”, en palabras de Tony Pennington, director general de WNT (Reino Unido).