Istobal perfecciona sus procesos con el uso de NX y Teamcenter
Istobal es una empresa española especializada en el diseño, fabricación y comercialización de soluciones de lavado para la automoción, que exporta sus productos a más de 75 países. Cuenta con una amplia red de distribuidores por todo el mundo, nueve filiales y cuatro plantas de fabricación, dos en Europa y otras dos en EE UU y Brasil. Su sede principal está en L’Alcúdia (Valencia), donde trabajan unos 370 de sus más de 700 empleados.
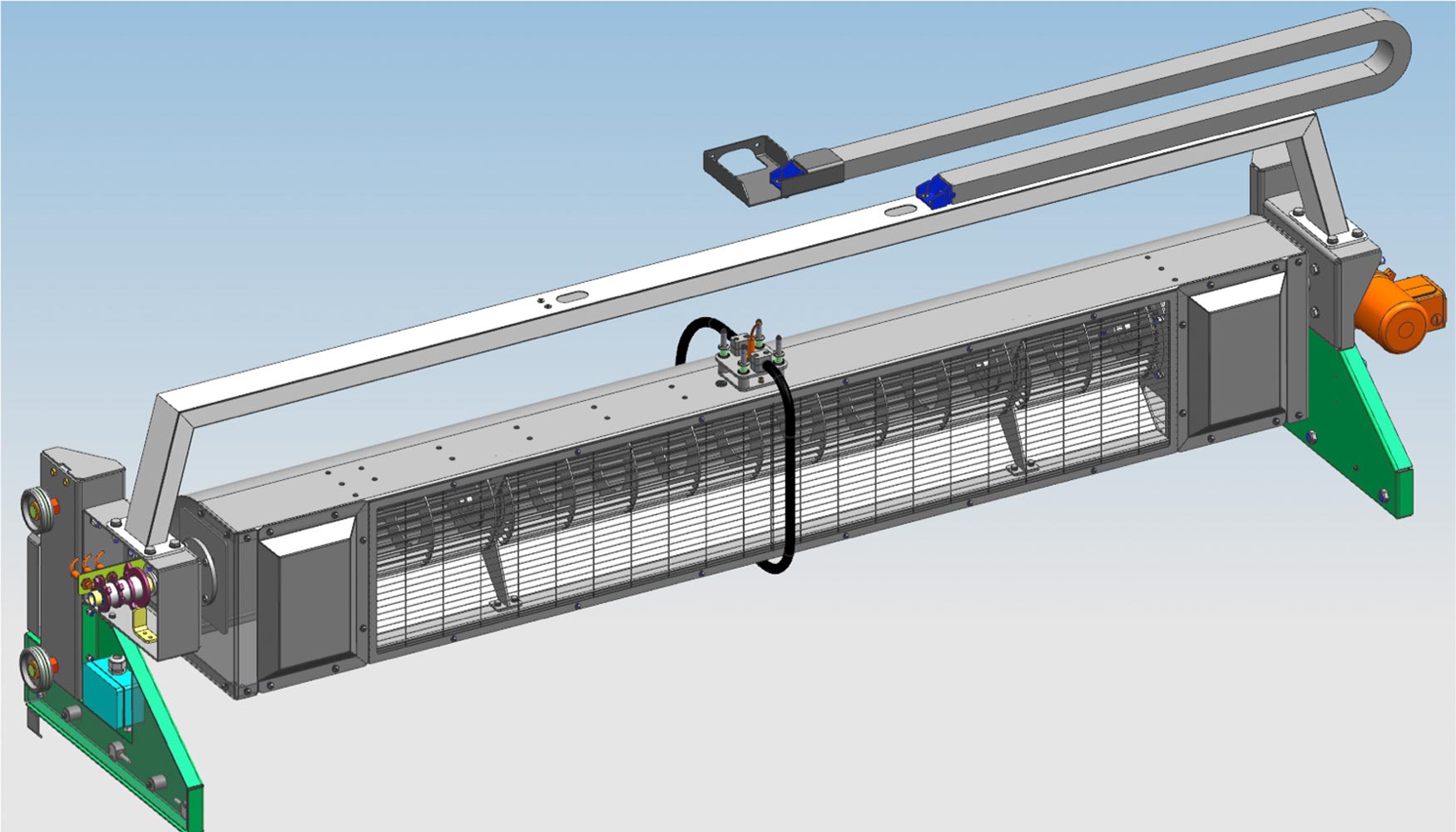
Fundada
en 1950, Istobal ha evolucionado su gama de productos desde una inicial máquina de engrase y elevadores para talleres a sofisticados sistemas de lavado que le han permitido convertirse en una multinacional con una facturación de 100 millones de euros consolidados en 2014. Su posición privilegiada en el mercado se
debe a una continua revisión de sus procedimientos de trabajo para poder responder a las cambiantes y exigentes demandas de sus aproximadamente 9.000 clientes en todo el mundo. Istobal siempre ha apostado por la innovación como herramienta para seguir creciendo, impulsando la calidad y la competitividad de sus productos.
Dentro de esa filosofía empresarial, el departamento de I+D+i juega un papel fundamental ya que es el responsable de la optimización del catálogo de modelos existente y de la creación de novedades. Istobal realizó un análisis en profundidad de los procesos de fábrica y, entre estos, los que afectaban a ingeniería cuando la compañía actualizó su ERP en 2007. “Se repetían muchos procedimientos y diseños, lo que repercutía en la productividad”, apunta Salvador Cardona, responsable TIC de Istobal, “Se planteó trasladar al entorno de ingeniería las ventajas y procesos de las herramientas informáticas en otras áreas, pudiendo reutilizar los elementos realizados en los trabajos y compartirlos en un ambiente colaborativo. Esto suponía afrontar un cambio de estructura a todos los niveles”.
Objetivo del proyecto
- Máxima reutilización de componentes
- Reducción de los tiempos de diseño
- Ahorro en costes
- Control, estabilidad e integración de la información
- Producción de variantes en el diseño
Resultados
- Reducción del 50% en el tiempo del diseño
- Optimización de la gestión de cambio
- Reducción en pruebas, prototipos y costes
- Mejora de la capacidad de innovación (más patentes)
- Lanzamiento de Smartflow, reduciendo el consumo eléctrico en un 60% y el nivel de sonido en más de siete decibelios comparado con otros sistemas de secado
- La rotación de productos en el catálogo ha pasado del 15 al 60%
- Reducción de piezas y referencias en torno a un 60%- 70%
Claves del éxito
- Diseño en 3D con funciones avanzadas
- Centralización y automatización de la información en Teamcenter
- Capacidades CAE-Simulación Reestructuración de procesos
- Integración de Teamcenter con distintos sistemas
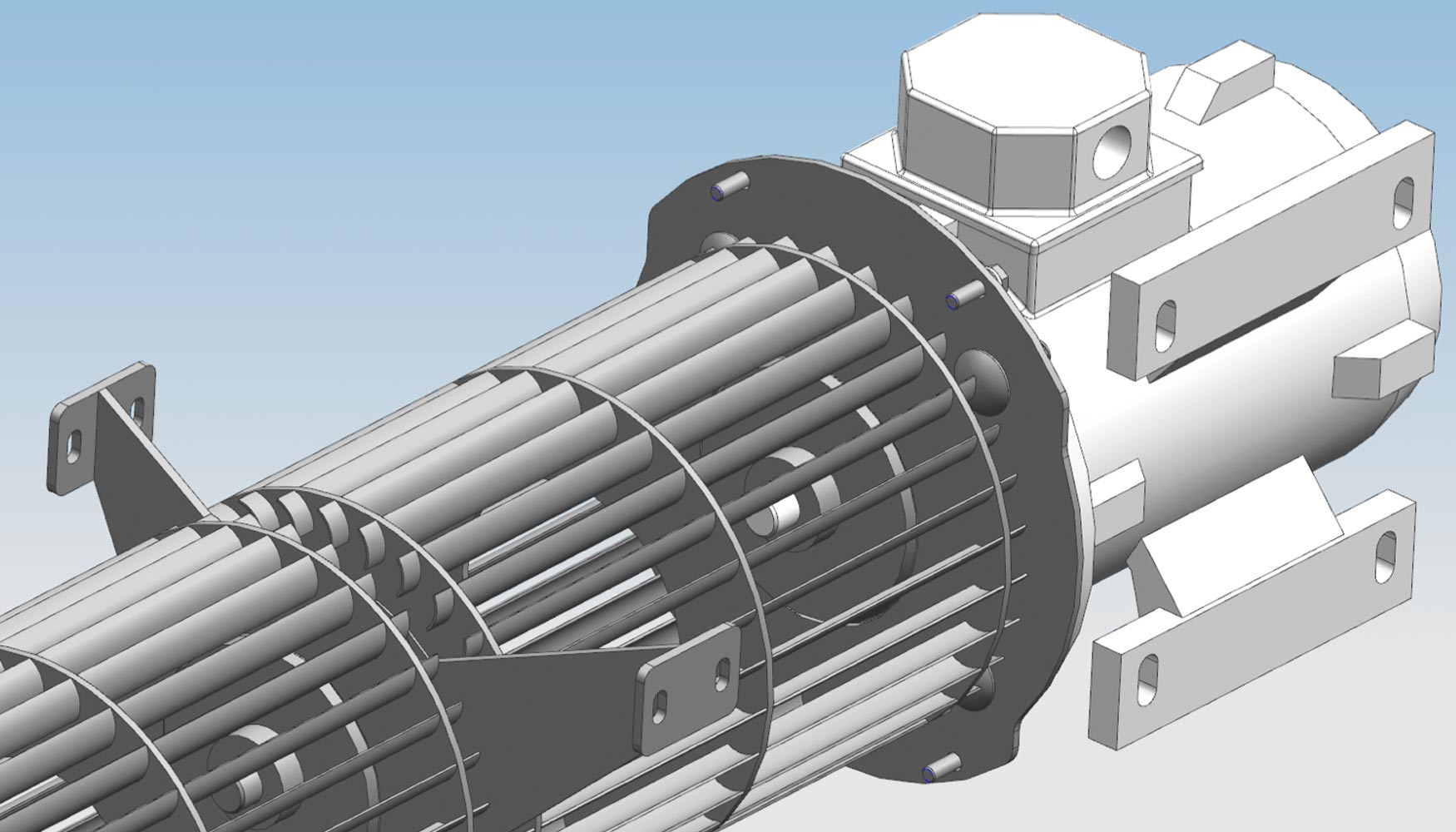
ha logrado racionalizar cada uno de los procesos que requiere el diseño y la fabricación de nuestras máquinas y reasignar las tareas de cada departamento, permitiendo que cada profesional haga el trabajo que mejor sabe hacer”, explica Salvador Cardona Responsable TIC en Istobal
Ingeniería ya utilizaba el software NX de Siemens PLM Software para la gestión de la vida del producto como solución de diseño CAD y CAE, pero necesitaban
una herramienta complementaria para gestionar y controlar sus procesos y datos. “La nueva solución debía estar totalmente integrada con NX” destaca Salvador Cardona. “Nos tenía que permitir la máxima reutilización de componentes, la utilización de variantes para recortar los tiempos de diseño, ahorros en costes. Además, teníamos que mejorar la estabilidad e integridad de la información y garantizar la incorporación de proveedores y subcontratistas. Y lo más importante: que aportara valor a nuestro producto”.
Istobal trasladó todos sus requerimientos a Siemens PLM Software para determinar si sería factible implantarlos en el departamento de ingeniería. Los profesionales de Siemens PLM Software recomendaron la incorporación de Teamcenter de Siemens PLM Software como herramienta de gestión del ciclo de vida del producto. Tras demostrar su eficacia durante distintas pruebas, NX y Teamcenter se convirtieron en la piedra angular de su nueva filosofía de trabajo.
“La solución de Siemens PLM Software
nos dio gran confianza” comenta Cardona. “Para nosotros es vital utilizar la tecnología más novedosa del mercado y eso sólo te lo garantizan fabricantes de alto nivel”.
En la actualización y evolución continua de estas soluciones, Istobal cuenta con el apoyo de su socio tecnológico Navarro y Soler, Solution Partner de Siemens PLM Software, que ha participado también en la integración de NX y Teamcenter en las filiales de EE UU y Brasil.
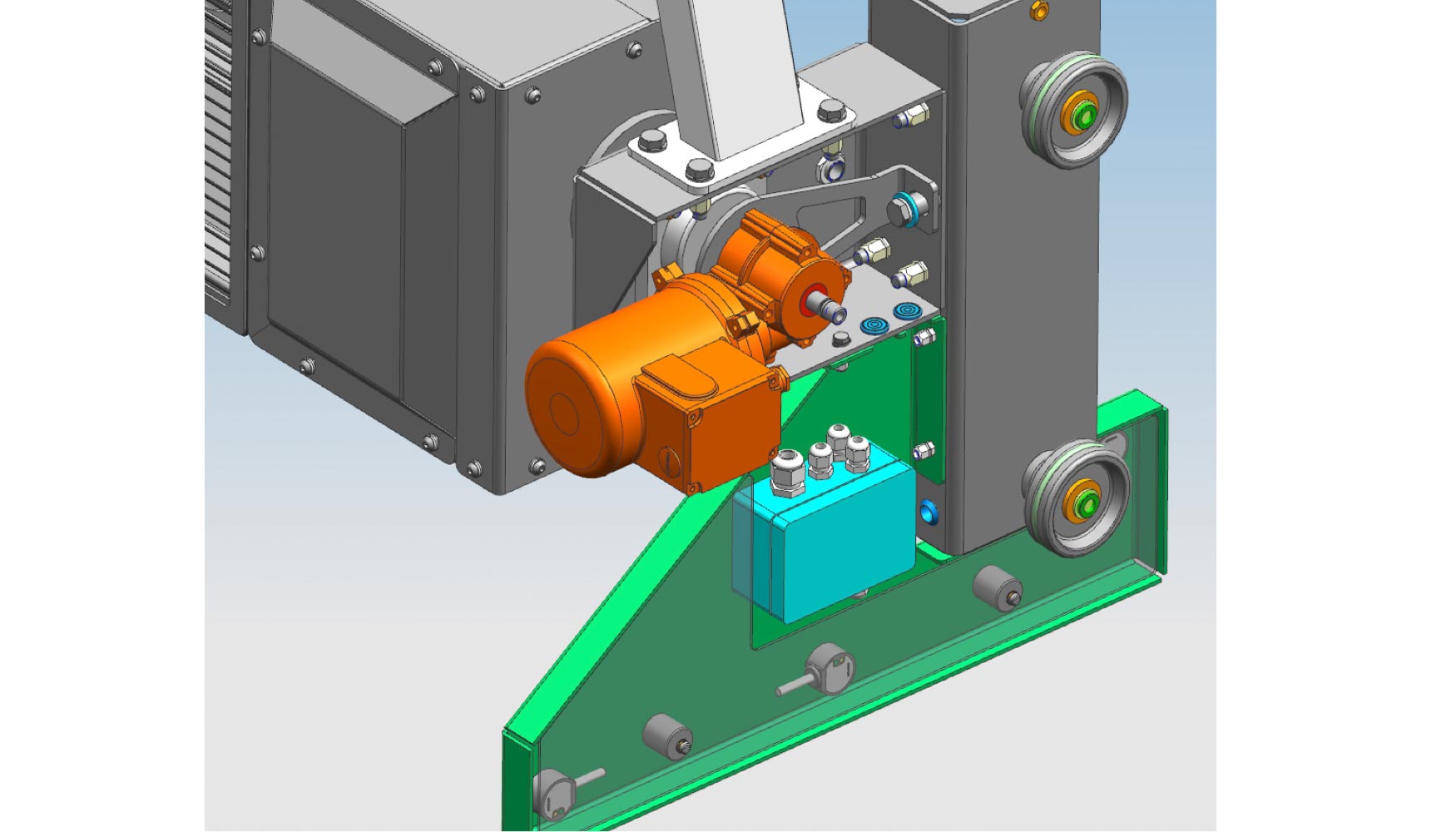
“Sin NX tardaríamos unos 6-9 meses en lanzarla al mercado, y tenemos previsto hacerlo en 2-3 meses”, afirma Marisol G. Castillo, jefe de I+D+i en Istobal.
Mejora en los procesos de diseño
La combinación NX-Teamcenter ha proporcionado a la compañía una solución PLM con la que han podido desplegar una nueva estructura de trabajo y organizativa definida por la singularidad de su negocio con la que cubrir el ciclo de vida de sus productos.
Istobal se dirige a clientes con distintas necesidades tanto por las características de sus negocios (desde grandes empresas a Pymes) como por su ubicación geográfica, lo que supone enfrentarse a diversos mercados y, por tanto, a diferentes especificaciones técnicas y normativas. Eso supone que sus productos, principalmente las líneas de puentes y túneles de lavado que incluyen miles de piezas, tienen que responder a múltiples especificaciones de alturas, ancho, longitud de pista, voltajes
y otros parámetros que son analizadas, según demandas de mercado, y definidas por el departamento de producto junto con el de I+D+i.
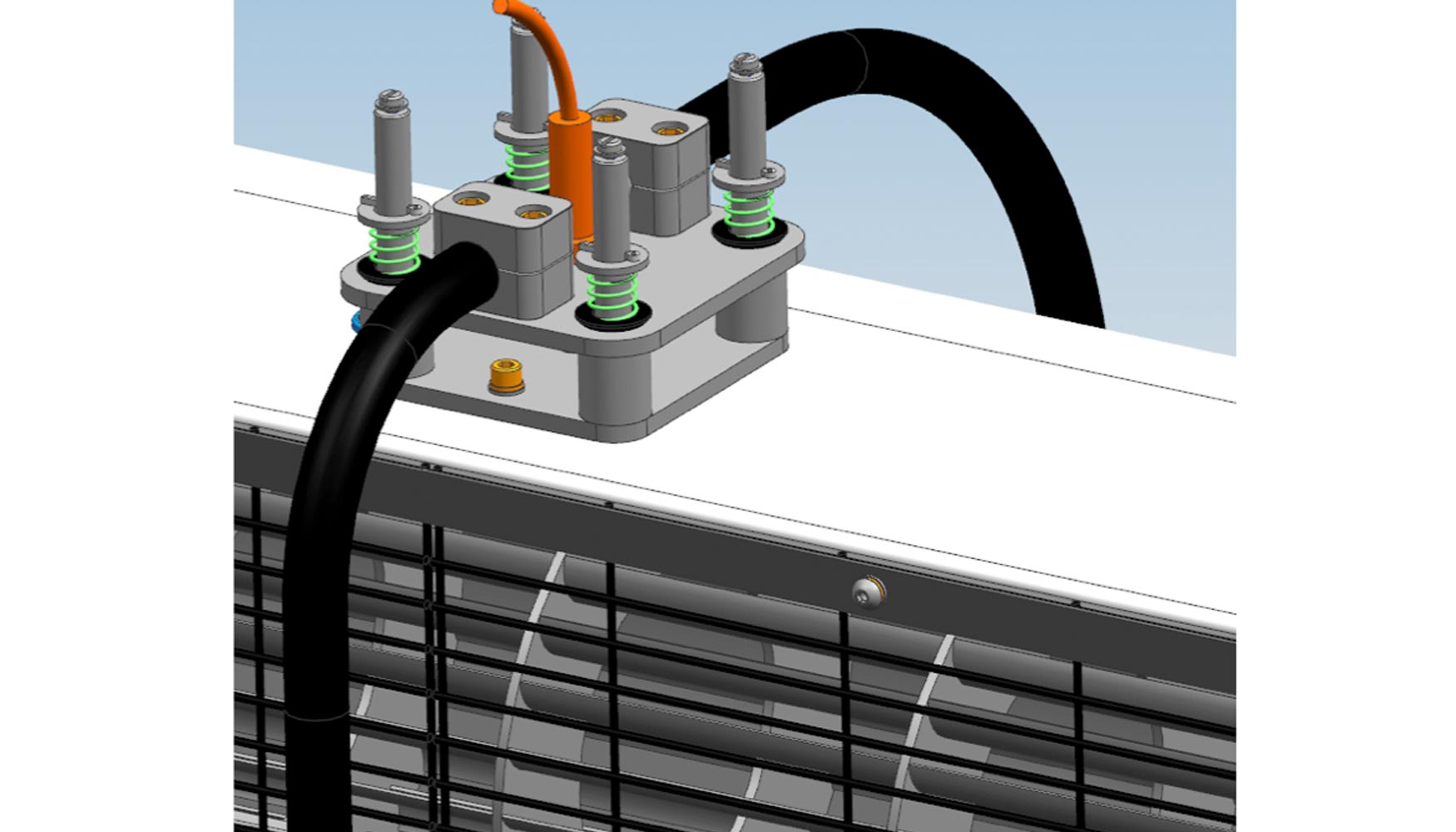
Anteriormente, a la hora de crear nuevos modelos de máquinas, ingeniería de I+D+i realizaba tantos diseños de máquinas como variantes había que introducir, siendo sus ingenieros los encargados de desarrollar, a partir de la lista de materiales utilizada en
el diseño, otra lista diferente adaptada para la fabricación. Deshacían la lista de diseño y mantenían sólo lo que pensaban eran válido para producción.
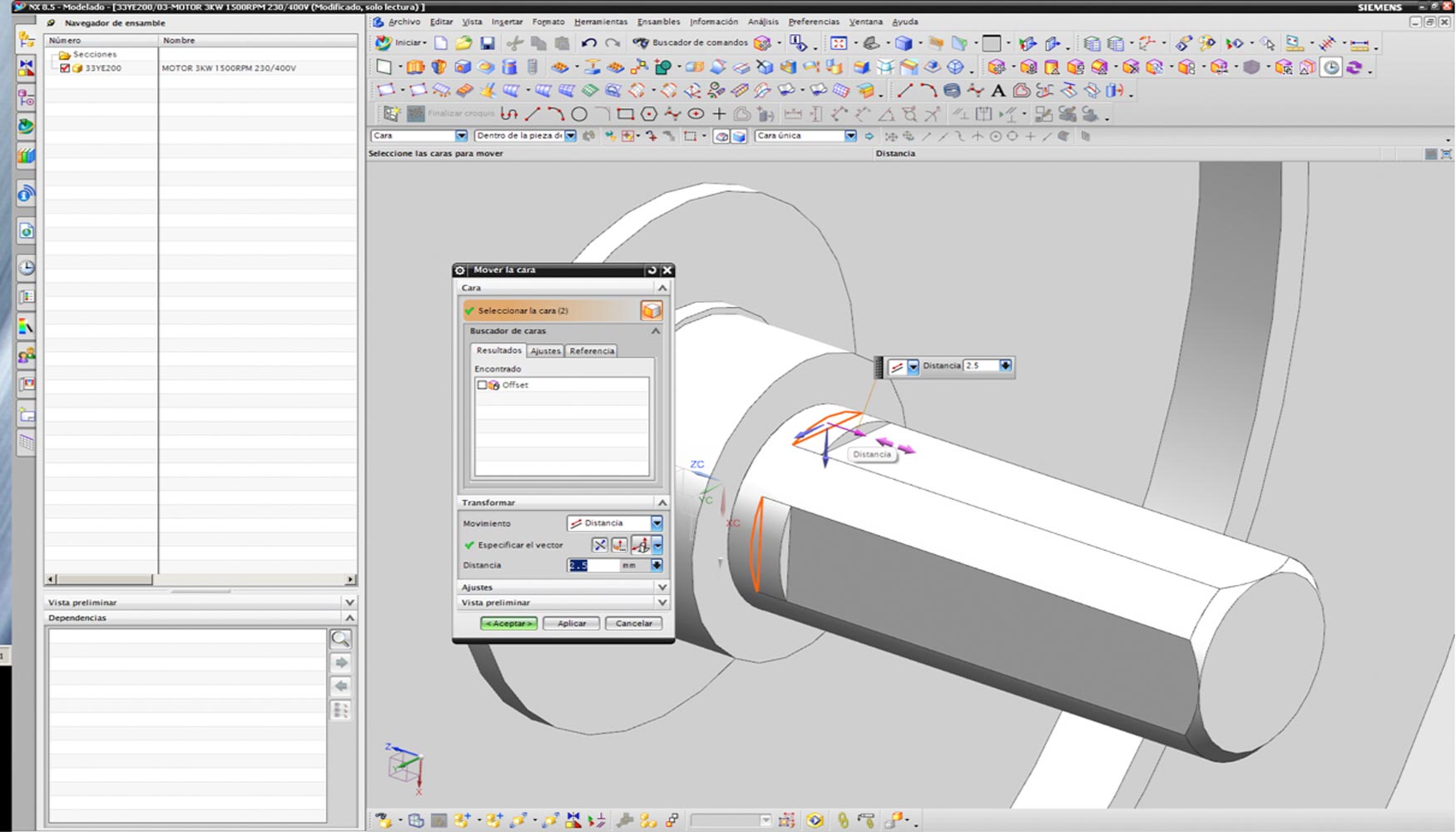
“A la hora de modificar una pieza, que interviene en
30 modelos, no tienes que descargar los 30 archivos de ensamblaje y luego volver a cargarlos; ahora dentro del mismo archivo en el que trabajes, ejecutas la variante y Teamcenter y NX lo gestionan”, comenta José Ricardo Vanaclocha, ingeniero I+D+i en Istobal.
Esta dinámica obligaba a realizar grandes esfuerzos por parte del departamento de ingeniería cada vez que se sacaba una máquina al mercado. “Se necesitaba mucho tiempo para generar una cantidad muy importante de documentación dado que cualquier modificación tenía que hacerla I+D+i sobre una estructura adaptada a fabricación”, explica Salvador Cardona. “Tenían que documentar la modificación en todos aquellos planos donde intervenía. En definitiva, un trabajo muy voluminoso y burocrático para este departamento que no aporta valor al producto”.
Istobal se ha beneficiado del uso de NX y Teamcenter para gestionar estructuras de producto complejas, evolucionando a un proceso automatizado y centralizado en el que los diseñadores trabajan a partir de un modelo único a modo de estructura básica de familia, sobre el que se aplican variantes. En vez de empezar un modelo de cero cada vez, pueden desarrollar toda la gama de producto incorporando las variantes necesarias a las estructuras modulares.
La primera vez que se planteó trabajar
de esta forma, alguien dijo que eso era imposible: “Imagínate en un entorno
de diseño una persona trabajando en
un modelo con todas las variantes de máquinas, es inmanejable”, comenta José Ricardo Vanaclocha, ingeniero de I+D+i. de Istobal. Así tal cual tenía razón. Gracias a la excelente integración de NX con Teamcenter sí ha sido posible.” “En el entorno de diseño, con NX y Teamcenter se encuentran todas las variantes dentro de la misma lista de materiales de un producto, ” continúa Vanalocha. “Aplicas la que quieras trabajar
y el sistema suprime las piezas que no intervienen en ella, mostrándote sólo las que sí. A la hora de modificar una pieza, que interviene en 30 modelos, no tienes que descargar los 30 archivos de ensamblaje y luego volver a cargarlos; ahora dentro del mismo archivo en el que trabajes, ejecutas la variante y Teamcenter y NX lo gestionan”.
Las herramientas de gestión de estructuras de Teamcenter ha sido clave agilizar los procesos de ingeniería. Por ejemplo, Istobal consiguió reaccionar rápidamente al éxito conseguido con la máquina Tracer OH1, diseñada para el mercado de EE UU con requisitos muy locales de diferente voltaje y frecuencia. “Pudimos adaptarla al mercado europeo en muy poco tiempo, manteniendo los componentes comunes y cambiando los particulares para cada país”, indica Jaume Bou, ingeniero de I+D+i.
Integración completa con el ERP
En la elección de Teamcenter como solución PLM influyó mucho su plena integración con el ERP corporativo al ser una herramienta abierta. Cuando ingeniería de I+D+i termina el diseño de un modelo y todas sus variantes, la información se transfieren de forma automática a dicho sistema. En ese momento, ingeniería de producción asigna las rutas, los tiempos y las operaciones oportunas para completar la producción y lanzar los procesos de fabricación de las máquinas.
Cuando el diseño se envía al área de Formación y Documentación para que creen los planos de despiece de esas máquinas para las líneas de montaje y para los técnicos SAT (Servicio de Asistencia Técnica), Istobal se apoya en el software Cortona 3D para
la creación de manuales de montaje. Su sencilla integración con NX permite importar la geometría diseñada y generar vídeos para facilitar el trabajo de los técnicos, tanto propios como de sus distribuidores, quienes acceden a esta información en un portal de documentación online.
La conexión con su sistema de gestión empresarial ha permitido a los ingenieros de I+D+i beneficiarse de la herramienta
de Análisis de Impacto que proporciona Teamcenter. “Cada vez que necesitamos modificar una pieza tenemos que saber en qué máquina o prototipo interviene. Para ello, antes debíamos entrar en el ERP. Ahora podemos verlo directamente en Teamcenter dentro de nuestro ambiente, sin tener que utilizar otro sistema”, apunta José Ricardo Vanaclocha.
Con este nuevo planteamiento, el departamento TIC, apoyándose en las áreas de Producto e I+D+i, ha diseñado
un configurador de producto integrado directamente con su ERP corporativo fiable, simple e intuitivo, que permite realizar cualquier configuración en cada uno de los modelos para su posterior fabricación. Dicha herramienta está siendo utilizada por más de 150 comerciales y distribuidores de Istobal, y los pedidos introducidos se lanzan a fabricar una vez a la semana.
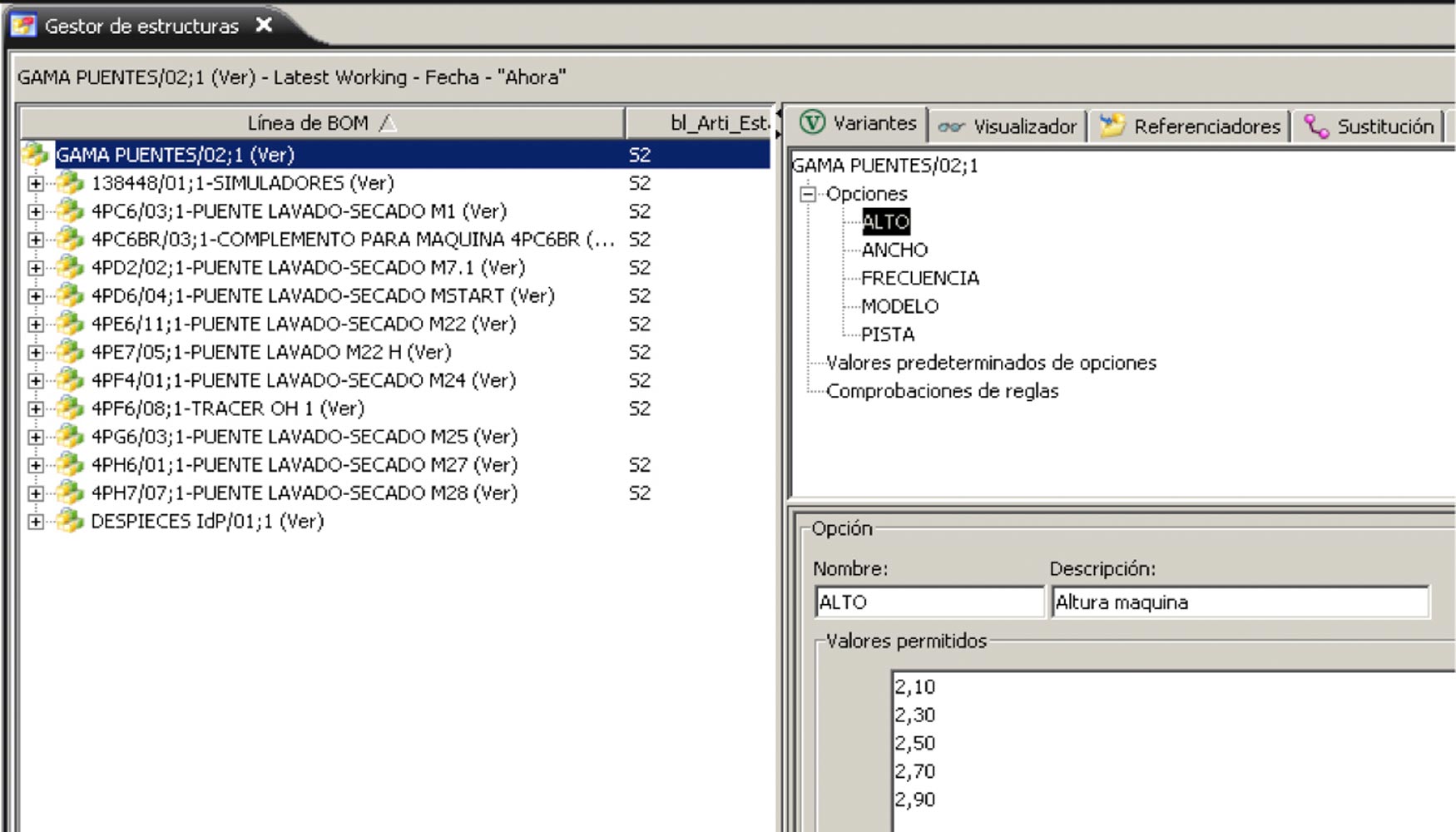
“A la hora de modificar piezas, Synchronous Technology permite el modelado directo sin importar el árbol de operaciones... En nuestro actual proceso de diseño, decidimos borrar los árboles de las piezas y trabajar sobre la geometría original. Ahorras mucho tiempo”, añade José Ricardo Vanaclocha, ingeniero I+D+i
en Istobal.
NX: modelado y simulaciones
Contar con una herramienta de diseño CAD 3D como NX es fundamental para poder afrontar los múltiples retos a los que se enfrenta diariamente el departamento de I+D+i. Y entre sus capacidades avanzadas, Syncronous Technology es crucial. “A la hora de modificar piezas, permite el modelado directo sin importar el árbol de operaciones. Antes tenías que averiguar cómo estaba hecha y daba pie a malinterpretaciones y errores. De hecho, dentro de la estructuración de trabajo que hemos afrontado, decidimos borrar los árboles de las piezas y trabajar sobre la geometría original. Ahorras mucho tiempo”, detalla Vanaclocha.
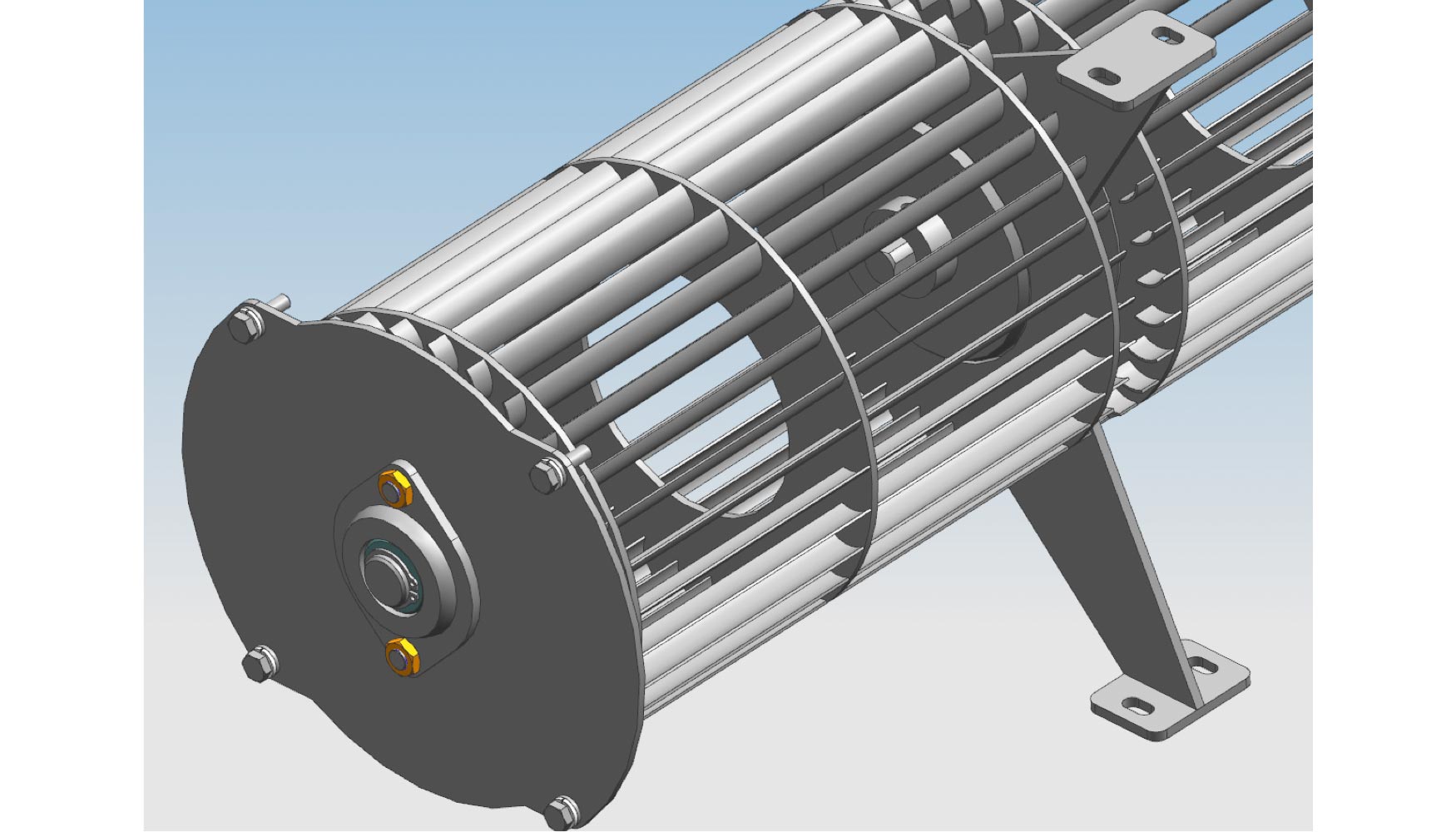
la creación de manuales de montaje.
Las capacidades de simulación de NX aseguran la eficacia del trabajo de ingeniería. Los ingenieros de Istobal utilizan NX CAE para simular variaciones en los productos, como la fuerza y los materiales. “El cálculo estático de los diseños nos permite no sobredimensionar las piezas y garantizar
que se ajustan a las necesidades reales; de esta manera, evitamos tener que realizar múltiples pruebas o prototipos consiguiendo ahorros en costes innecesarios”, comenta David Primo, ingeniero de I+D+i.
Istobal ha lanzado al mercado un revolucionario sistema de secado denominado Smartflow para su gama
de puentes de lavado M’NEX, en cuyo desarrollo ha sido básico la utilización del módulo Flow de NX que permite realizar el cálculo del fluido dinámico.”Con él podemos analizar y simular el comportamiento del aire en la entrada y salida de la tobera de secado”, afirma Primo, “Hemos conseguido un secado muy eficiente porque reduce el consumo eléctrico en un 60% y el nivel sonoro en más de siete decibelios respecto al resto de sistemas de secado”. Este logro pone en valor el interés de Istobal por realizar productos sostenibles con el Medio Ambiente.
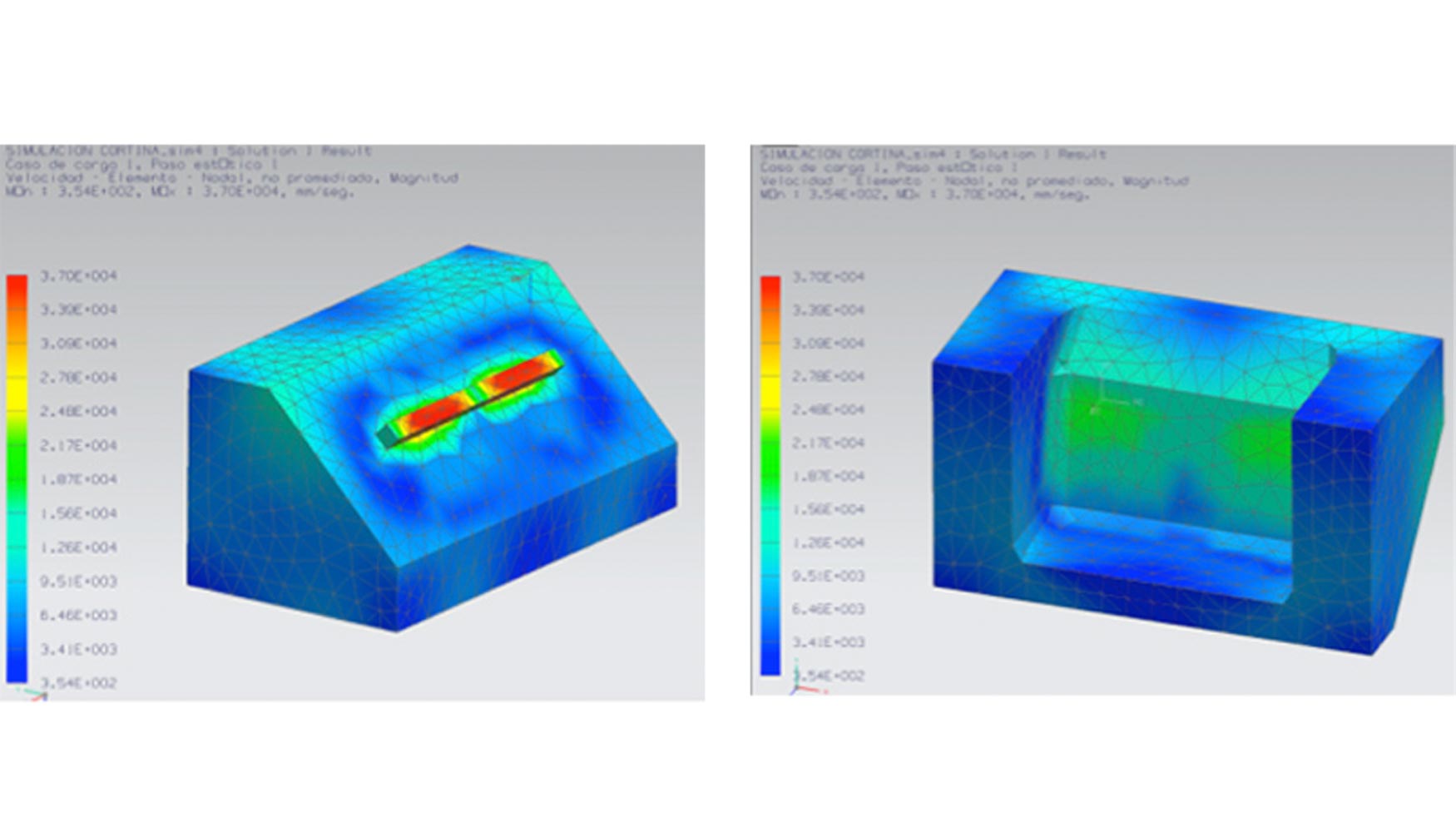
Beneficios que impactan en el negocio
Con la implantación de NX y Teamcenter
el día a día del trabajo de los ingenieros de I+D+i se ha visto muy beneficiado, como resultado del aprendizaje y un entorno amigable e intuitivo. Agilidad, flexibilidad, fluidez y ahorro en tiempo, son las valoraciones más repetidas. Pero hay otras muchas que además de incidir en las labores propias de ingeniería tienen un impacto muy beneficioso en el negocio en sí de la compañía. NX y Teamcenter proporcionan un
entorno de colaboración entre las distintas sedes internacionales. “El tener toda la información centralizada en un único punto permite que personas en distintos lugares y en distintos momentos puedan acceder sin problemas. Además, nos libera de fallos, al evitarse la duplicidad de dicha información”, valora Marisol G. Castillo, jefe de I+D+i.
Esa colaboración se asienta también en las capacidades de NX para importar y exportar múltiples formatos, lo que permite modificar y editar diseños de componentes de proveedores y colaboradores externos.
“Algo muy importante también es la trazabilidad que tenemos de cada pieza, podemos saber cuándo se ha realizado
o modificado y quién lo ha hecho. Estos registros nos ayudan a ver cómo se ha evolucionado cuando nos solicite el mercado más opciones y actualizaciones. Además, es clave para asegurar la calidad tanto de nuestros procesos internos, como la que nos exigen proveedores, clientes
y diferentes normativas”, complementa Marisol G. Castillo.
La nueva organización de trabajo y configuración de estructuras de producto con variantes ha generado una reducción en el tiempo de diseño y de estructuración de cada una de las máquinas del 50%. “Eso supone contar con más tiempo para diseñar nuevos modelos y, por lo tanto, para innovar. Como resultado, en los últimos años el número de patentes registradas
ha ido aumentando respecto a años anteriores”, comenta la jefe de I+D+i.
Igualmente se ha mejorado el ‘time-to- market’ de sus productos en un 50%. Como prueba, apunta la remodelación de la gama de puentes que se está acometiendo para abarcar más alturas y dimensiones: “Sin NX tardaríamos unos 6-9 meses en lanzarla al mercado, y tenemos previsto hacerlo en 2-3 meses”, apunta Marisol. Esa rapidez en presentar nuevas propuestas al mercado ha supuesto que la rotación de productos en sus catálogos haya pasado de un 15% a un 60% en los últimos años.
Istobal ha reducido el número de piezas y referencias en torno a un 60%-70% en la lista de materiales, lo que se traduce en reducción de horas de trabajo y ahorros en costes de gestión.
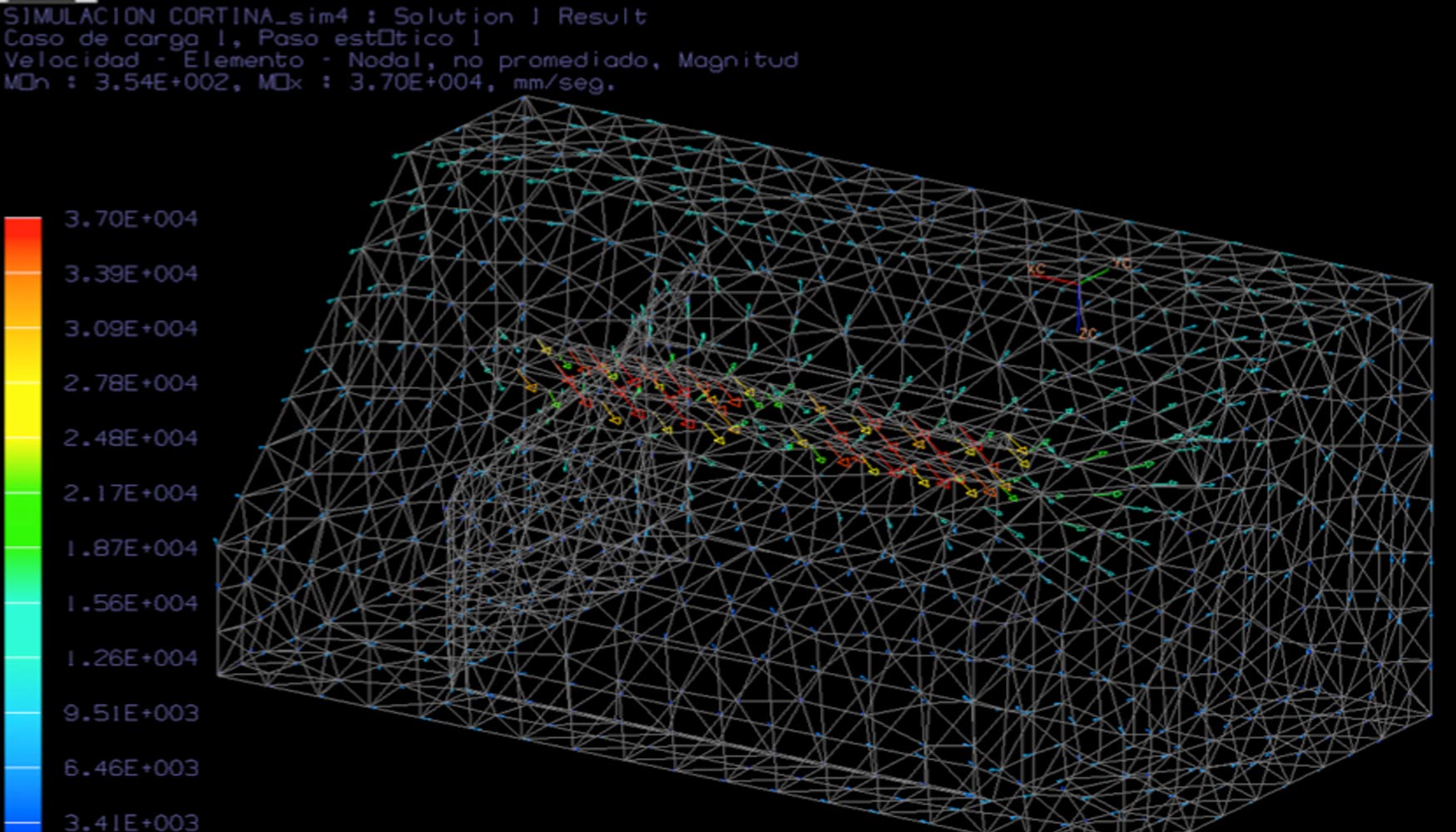
“El cálculo estático de los diseños nos permite no sobredimensionar las piezas y garantizar que se ajustan a las necesidades reales; de esta manera, evitamos tener que realizar múltiples pruebas o prototipos consiguiendo ahorros en costes innecesarios”, explica David Primo, ingeniero de I+D+i en Istobal.
Reasignación de tareas y planes futuros
El siguiente paso dentro de la restructuración organizativa pretende liberar al departamento de I+D+i de sus tareas operativas para que pueda centrarse únicamente en sus funciones creativas,
sin tener que trabajar para un entorno de fabricación ajeno al suyo, lo que podía generar inexactitudes en las listas de producción. Cada departamento podrá trabajar con las listas de materiales que necesita, siendo I+D+i quien creará las de diseño y el departamento de Ingeniería de Producción las adaptará a montaje, incluyendo en ellas todo lo relativo a operaciones, rutas y tiempos, que determinan su fabricación. Ingeniería de Producción pasará a realizar la publicación de éstas en el ERP. “De esta manera, cada departamento aportará el máximo valor al producto centrándose en lo que mejor saben hacer”, reconoce Cardona.
Istobal también piensa incorporar la solución NX CAE para el cálculo dinámico
y el de cálculo de fatiga de NX. Con esta herramienta será posible conocer la durabilidad de las piezas diseñadas en las máquinas. Además, se planea aprovechar las múltiples capacidades de integración de Teamcenter para conectarlo con el sistema CAD ePlan en el que se pretende centralizar el diseño de distintos componentes
que actualmente se modelan con otros programas. Estas mejoras enriquecerán el ambicioso proyecto de reestructuración que está ayudando a Istobal a innovar y a mantener su liderazgo en el mercado. “Con las soluciones PLM de Siemens se ha logrado racionalizar cada uno de los procesos que requiere el diseño y la fabricación de nuestras máquinas y reasignar las tareas de cada departamento, permitiendo que cada profesional haga el trabajo que mejor sabe hacer”, resume Cardona.
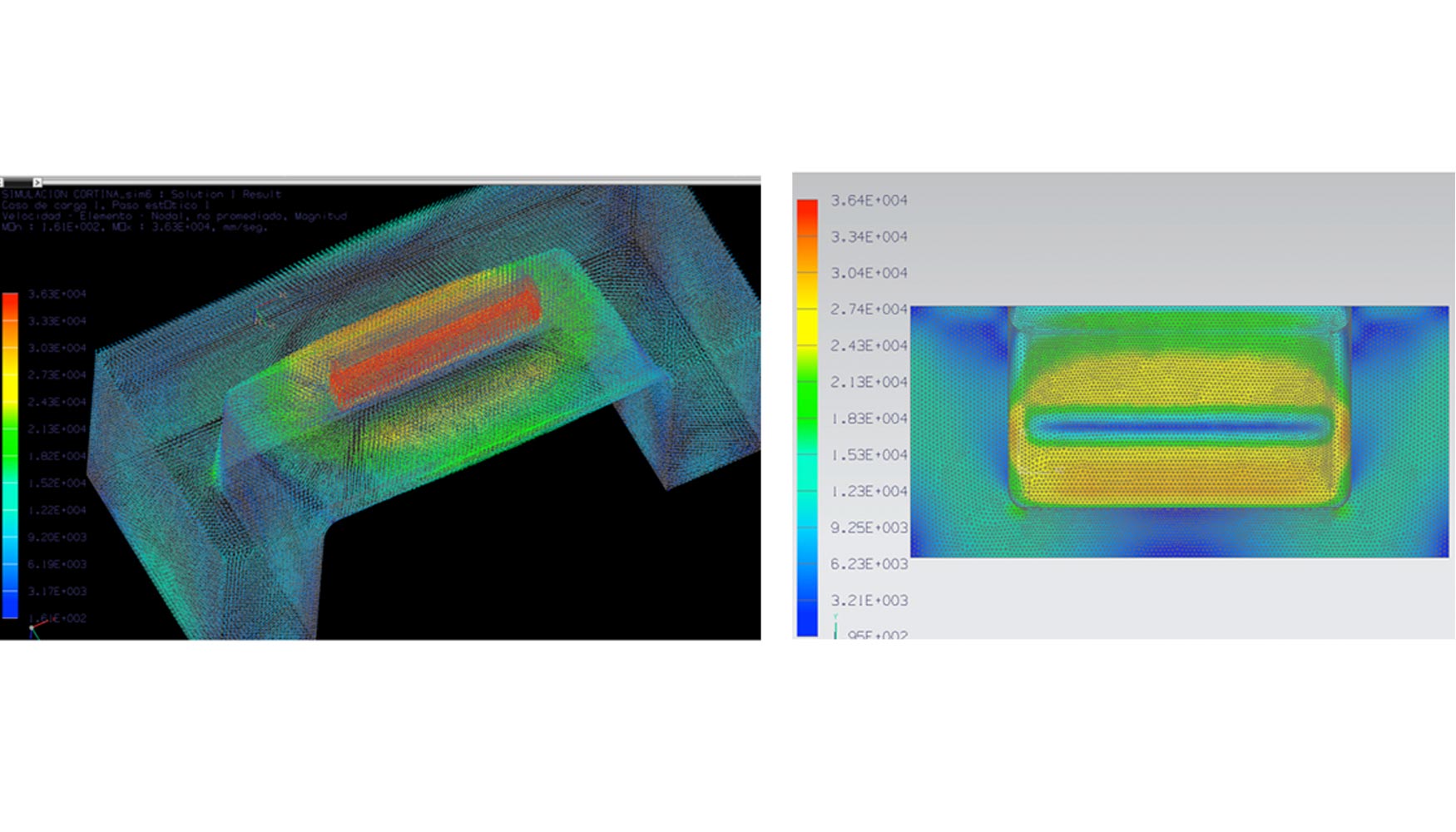
Istobal también piensa incorporar la solución NX CAE para el cálculo dinámico
y el de cálculo de fatiga de NX. Con esta herramienta será posible conocer la durabilidad de las piezas diseñadas en las máquinas.