Integridad de pieza: ¿Concierne a un mecanizador?
En la actualidad se ha extendido el uso de criterios basados en la mejora de los métodos de cálculo para realizar diseños más ajustados, con menores coeficientes de seguridad y gran ahorro de material. Estos avances tienen que ir ligados a un control absoluto de los sistemas de fabricación, donde la integridad del componente y por lo tanto su comportamiento en servicio pueden ser alterados de forma notable.
1. Concepto de integridad: diseño, fabricación y en servicio
La rotura representa la situación última del comportamiento mecánico de los materiales. Esta viene precedida de inestabilidades o roturas locales asociadas a determinadas características microestructurales del material, tales como defectos, poros o grietas. Estas características pueden estar asociadas a defectos preexistentes generados durante la fabricación o mecanizado, o defectos desarrollados a causa de las solicitaciones en uso del componente. En cualquier caso, estos defectos son los que establecen las condiciones críticas a partir de las cuales se desarrolla la rotura del material y por lo tanto condicionan el campo de aplicación del producto. Un fallo en un componente mecánico puede suponer la pérdida de la funcionalidad del conjunto completo, como por ejemplo en el caso de rotura del eje de dirección ilustrado en la figura. Las roturas pueden suponer casos de fallo catastrófico en el caso de automoción, aeronáutica y otros sectores. Dada la importancia que tiene el controlar que esto no suceda, la clave del éxito parte de analizar y determinar el comportamiento mecánico de los elementos estructurales considerando la existencia de defectos, sea cual sea su origen e independientemente del material en cuestión. La idea es ser capaces de definir unas condiciones o criterios de rotura, todo ello englobado en lo que se conoce como Mecánica de la Fractura.
![Rotura en un eje de dirección [Imagen de INTI Mecánica] Rotura en un eje de dirección [Imagen de INTI Mecánica]](https://img.interempresas.net/fotos/1087563.jpeg)
Como ya se ha comentado, la integridad estructural está asociada al concepto de estado sólido, y tiene que ver con la capacidad de un material, pieza o conjunto para mantener sus características originales a lo largo del tiempo, siempre bajo las condiciones operacionales para las cuales haya sido diseñado.
La integridad, en el término más general, dependerá de factores mecánicos, termodinámicos, químicos y físicos entre otros. Por ejemplo, será interesante controlar los esfuerzos actuantes sobre la pieza o sistema, así como las presiones de trabajo. Por otra parte, el calor puede modificar las dimensiones críticas de componentes, generando deformaciones graves. Factores químicos, como una puesta en servicio en entornos agresivos puede ser importante, por ejemplo en temas relacionados con corrosión de metales. Otros factores como la humedad, la luz solar, etc. pueden desencadenar un deterioro que implique una debilidad en la integridad estructural del material o sistema. Todos estos factores han de evaluarse de forma conjunta, esto es, teniendo en cuenta las interrelaciones entre ellos. Por ejemplo, un componente sometido a ciertas cargas cíclicas en ambientes corrosivos puede no ser problemático a ciertas temperaturas y por el contrario el fallo puede ser catastrófico cuando la temperatura excede de un cierto valor. En resumen, un componente ha de diseñarse según las exigencias del régimen de trabajo y las condiciones ambientales extremas que pueden esperarse durante la vida útil del sistema.
En esta línea, deberá de realizarse el análisis de componentes teniendo en cuenta el comportamiento en servicio de materiales, desde el diseño, dimensionamiento y cálculo de los mismos, pasando por la selección de material así como por el control de los procesos de fabricación, ensamblado y protección.
Un ejemplo de la importancia del proceso de fabricación se recoge en el informe preparado en 2010 por Australian Transport Safety Bureau de título “In-flight uncontained engine failure overhead Batam Island”. En este informe se recoge el análisis realizado en relación al Airbus A380 que el 4 de Noviembre de 2010 sufrió un incidente que provocó el fallo de uno de sus motores. En concreto fue un fallo no contenido de uno de los discos de la turbina de presión intermedia. Las secciones rotas del disco penetraron a través del ala izquierda produciendo además daños estructurales en la aeronave.
El análisis de los componentes del motor muestra la presencia de una zona de rotura a fatiga en una de las conducciones de suministro de aceite al rodamiento de la turbina intermedia. Esta rotura, posible causante del incidente, está asociada a un desalineamiento de agujeros generado durante el proceso de fabricación. Este desalineamiento genera un estrechamiento localizado de una zona concreta de la pared de la conducción, tal y como se muestra en la figura.
![Imagen de componente dañado en el motor del Airbus A380 [ATSB report] Imagen de componente dañado en el motor del Airbus A380 [ATSB report]](https://img.interempresas.net/fotos/1087567.jpeg)
1.1. Influencia de la integridad en servicio
La presencia o aparición de daños en los componentes mecánicos durante su vida en servicio puede tener diferentes orígenes y mecanismos de crecimiento dependiendo de las condiciones ambientales y de los tipos de cargas a los que se ven sometidos. Los principales modos de fallo que comúnmente se observan en componentes durante el servicio son la fractura, la fatiga, la fluencia y la corrosión. El fallo de un componente puede incluir alguno de estos cuatro mecanismos básicos pero también pueden darse interacciones entre ellos en las diferentes etapas del proceso de daño en servicio.
El diseño de componentes y estructuras en ingeniería debe prevenir la aparición de procesos de corrosión bajo tensión, corrosión por fatiga o fracturas frágiles entre otros, además de asegurar un comportamiento en servicio bajo condiciones de seguridad idóneas. Este objetivo puede alcanzarse mediante una adecuada selección de materiales, a través del control del medio agresivo o minimizando el estado tensional.
El diseño basado en el estado tensional consiste en mantener la tensión aplicada por debajo de un umbral de iniciación o de propagación de grietas. En cambio, a pesar de haber realizado un diseño del estado tensional óptimo, las grietas en la superficie del componente se pueden iniciar y propagarse por varias razones: alteración de las condiciones de servicio, presencia de áreas con soldadura inapropiada, variaciones transitorias de la temperatura o cambios superficiales del material (aparición de capa oxidante). Otras veces, la utilización del material idóneo para la aplicación no es económicamente viable o los ensayos realizados sobre prototipos no representan unas condiciones de servicio reales.
Como ya se ha mencionado, las condiciones de servicio que pueden influir en la integridad del componente son el estado tensional y ambiental. En el primer caso es necesario tener en cuenta todas las tensiones a las que va a ser sometido el componente, incluyendo las que aparecen durante las operaciones normales de funcionamiento (principalmente estáticas o cíclicas), tensiones transitorias asociadas al arranque/parada y las inducidas por el proceso de fabricación o por la presencia de soldaduras (tensiones residuales).
Entre todas, las tensiones de tipo transitorio resultan ser las más críticas en el proceso de iniciación y propagación de fisuras, siendo, por otro lado, las que presentan una caracterización más problemática en ensayos de laboratorio. Sin embargo, las tensiones residuales debidas a los procesos de fabricación, a menudo mejoran el comportamiento a fatiga de los componentes y retrasan la aparición y propagación de grietas (en caso de tensiones residuales de compresión). De la misma forma, las tensiones residuales tractivas, agravan el estado tensional global del componente disminuyendo su vida a fatiga.
La caracterización de las condiciones ambientales puede tratarse de una tarea aún más desafiante. Si bien las condiciones ambientales de servicio resultan normalmente bien conocidas, estas pueden variar localmente debido a cambios en la naturaleza del medio, provocando una fuerza inductora en el proceso de fisuración diferente a la esperada. Factores como el cambio en la concentración de iones, procedentes de procesos de corrosión locales, representan un elemento crítico en la iniciación de corrosión por picaduras o corrosión bajo tensión.
La temperatura en servicio también supone una variable crítica para determinar la integridad del componente. Los materiales sometidos a altas temperaturas durante largos periodos de tiempo, presentan fenómenos como la disminución de la resistencia mecánica, aumento de la movilidad de las dislocaciones, procesos de difusión, crecimiento de grano y otros cambios microestructurales que pueden modificar el comportamiento frente a procesos de corrosión. Por ello, es importante conocer las propiedades del material a altas temperaturas como su resistencia al creep o el límite de fluencia.
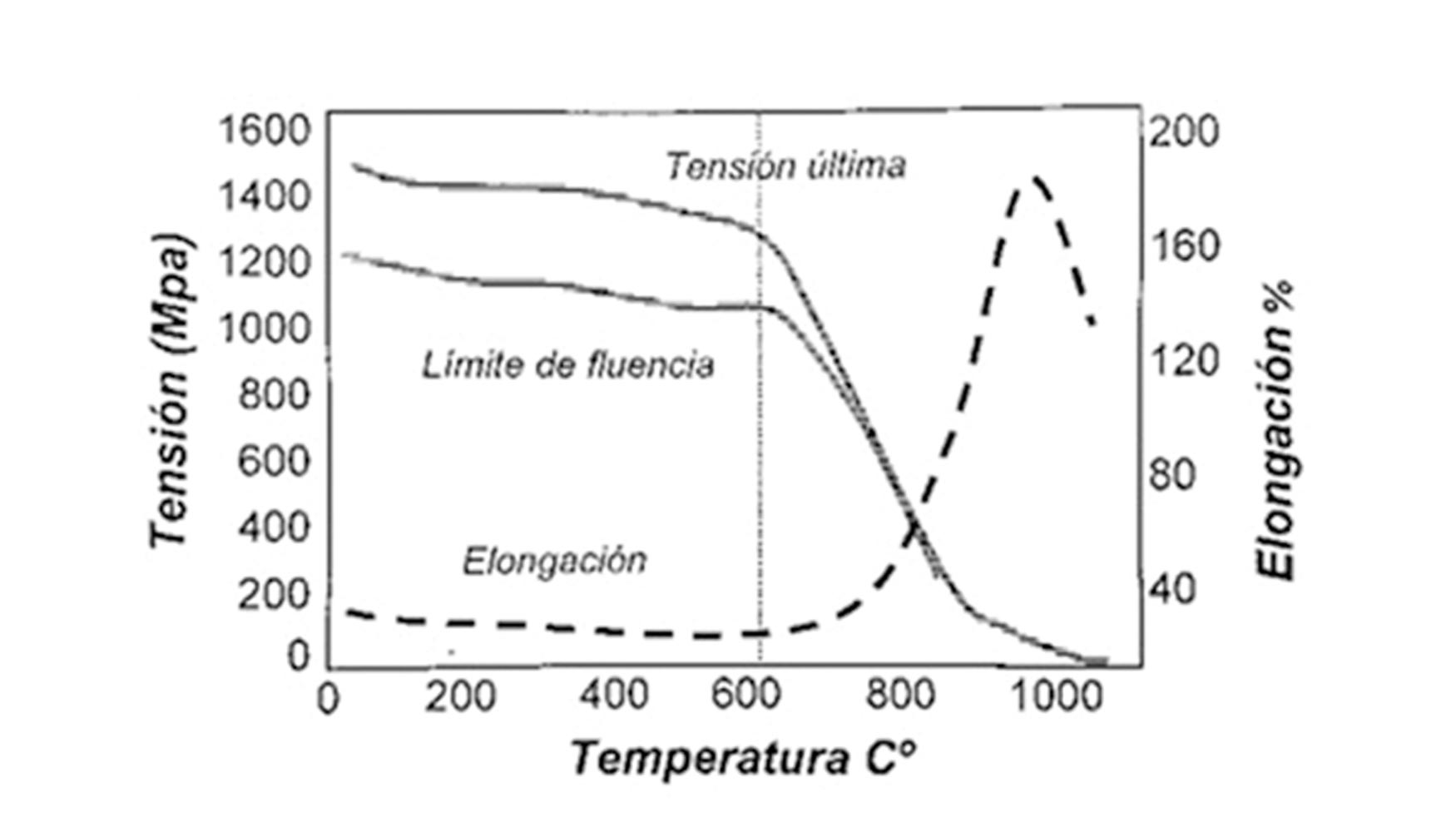
2. Concepto de integridad superficial
Una de las principales consideraciones de diseño a tener en cuenta para aquellos componentes que van a estar altamente solicitados durante su vida de servicio o trabajando en condiciones extremas es el conocimiento de su estado superficial y el de la sub-superficie, modificados en muchas ocasiones por el proceso o procesos de fabricación aplicados, y que, en mayor o menor medida, provocarán alteraciones superficiales que a su vez, podrán o no afectar al comportamiento del componente en su vida útil.
La interacción proceso-material puede producir efectos muy diferentes según cada caso particular. En función del tipo de energía puesta en juego (mecánica, térmica, química, eléctrica), de su intensidad y de las propiedades del material del componente, se producirán unas alteraciones superficiales que podrán afectar a las propiedades mecánicas de los componentes y, a la larga, a la fiabilidad del componente en cuestión. Como ejemplo están las tensiones residuales, los cambios de dureza o la microestructura del material, entre otros.
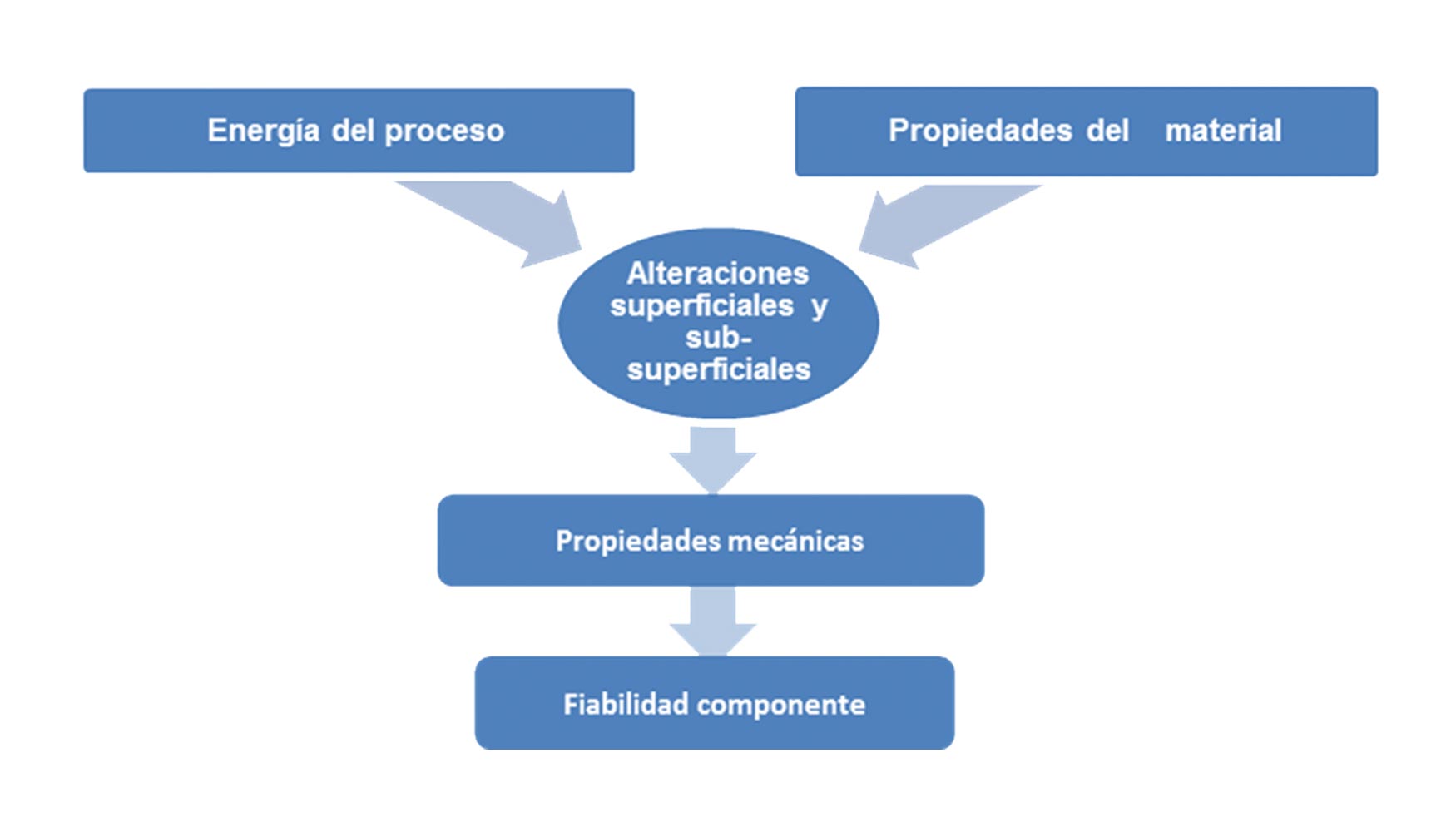
El concepto de Integridad Superficial incluye, de forma global, dos tipos de efectos que se producen debido a la interacción proceso-material: los efectos exteriores y los interiores. Los primeros se analizan a través de la textura superficial, incluyendo los conceptos de rugosidad, ondulación y pendiente, así como los macro-defectos que incluyen aquellas imperfecciones fácilmente detectables a simple vista. Los segundos, localizados en la sub-superficie, producen alteraciones que abarcan desde transformaciones microestructurales, hasta zonas afectadas por el calor, tensiones residuales, variaciones de dureza, deformaciones plásticas, generación de microgrietas y otros.
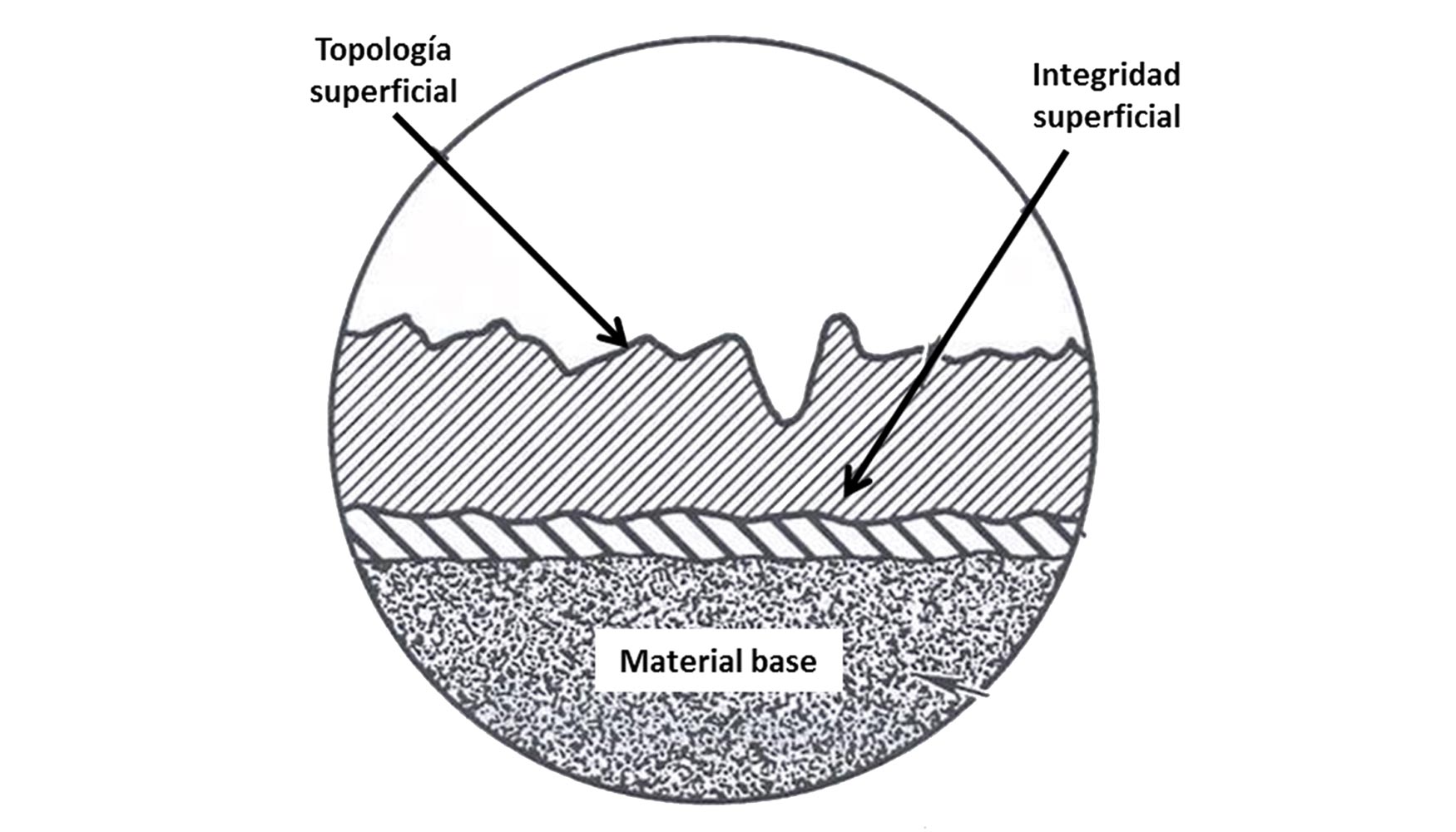
Aquellos procesos que aplican energía mecánica tienden a generar tensiones residuales en las capas subsuperficiales, grietas de nivel macro-microscópico, deformaciones plásticas, pliegues, huecos o inclusiones y variaciones de dureza, principalmente. Los procesos que aplican energía térmica tienden a generar cambios metalúrgicos como fenómenos de recristalización y cambios en el tamaño de grano, material resolidificado, cambios de fase, zonas afectadas por el calor y cambios de dureza. Los procesos que aportan energía química provocan ataques intergranulares, contaminación química y corrosión. Los procesos basados en la aplicación de energía eléctrica pueden producir cambios en la conductividad o en las propiedades magnéticas de los materiales.
Es de vital importancia conocer tales alteraciones, sobre todo en aquellos componentes que vayan a estar altamente solicitados en su vida útil, o trabajando en condiciones muy extremas (incluidas las atmosféricas), dado que el desconocimiento de las mismas podrá llevar al fallo del componente mucho antes de lo esperado.
Para mejorar la integridad superficial los fabricantes de piezas críticas, como por ejemplo los fabricantes de piezas para el sector aeronáutico, deben analizar y seleccionar las condiciones de mecanizado óptimas que permitan minimizar las tensiones residuales (principalmente las de tracción) y distorsiones que se generen en la pieza, eliminar grietas y otras alteraciones que puedan disminuir la resistencia a fatiga y a la corrosión y, por último, mantener la topografía de la pieza en rangos que aseguren la funcionalidad de las piezas.
2.1. Fatiga normal: Defectos
Cuando se habla de la integridad superficial de una pieza o componente de un sistema mecánico, es imposible hacerlo sin mencionar el fenómeno de la fatiga. Como se sabe, la fatiga de materiales estudia el comportamiento resistente de elementos o componentes de máquinas sometidos a tensiones variables en el tiempo, las cuales van provocando un continuo deterioro del material del componente, momento en el que se pueden generar pequeñas grietas que se van propagando llegando a ocasionar el fallo de la pieza. Aunque pueda parecer muy lejano o poco común, se estima que la inmensa mayoría de los fallos mecánicos, en torno a un 90%, son fallos debidos a fatiga, esto da una idea de lo importante que resulta este fenómeno en la industria. Por tanto se ve que es fundamental realizar el diseño de numerosas piezas con criterios de vida a fatiga, ya que es raro el elemento de un sistema mecánico que no trabaje con cargas variables en el tiempo.
Son numerosos en la literatura los fallos por fatiga de componentes de máquinas debido a una mala condición de integridad superficial del material del componente, ya sea por un defecto en una operación de mecanizado o defecto de tipo metalúrgico del propio material. Quizá los casos más famosos e impactantes se encuentran en el campo aeronáutico, uno de cuyos ejemplos se puede ver en la siguiente fotográfica del fallo ocurrido en Pensacola (Florida) en 1996, en el que durante el despegue se produjo el fallo no contenido por fatiga del disco o buje del fan, debido a un taladro incorrectamente realizado con daño metalúrgico.
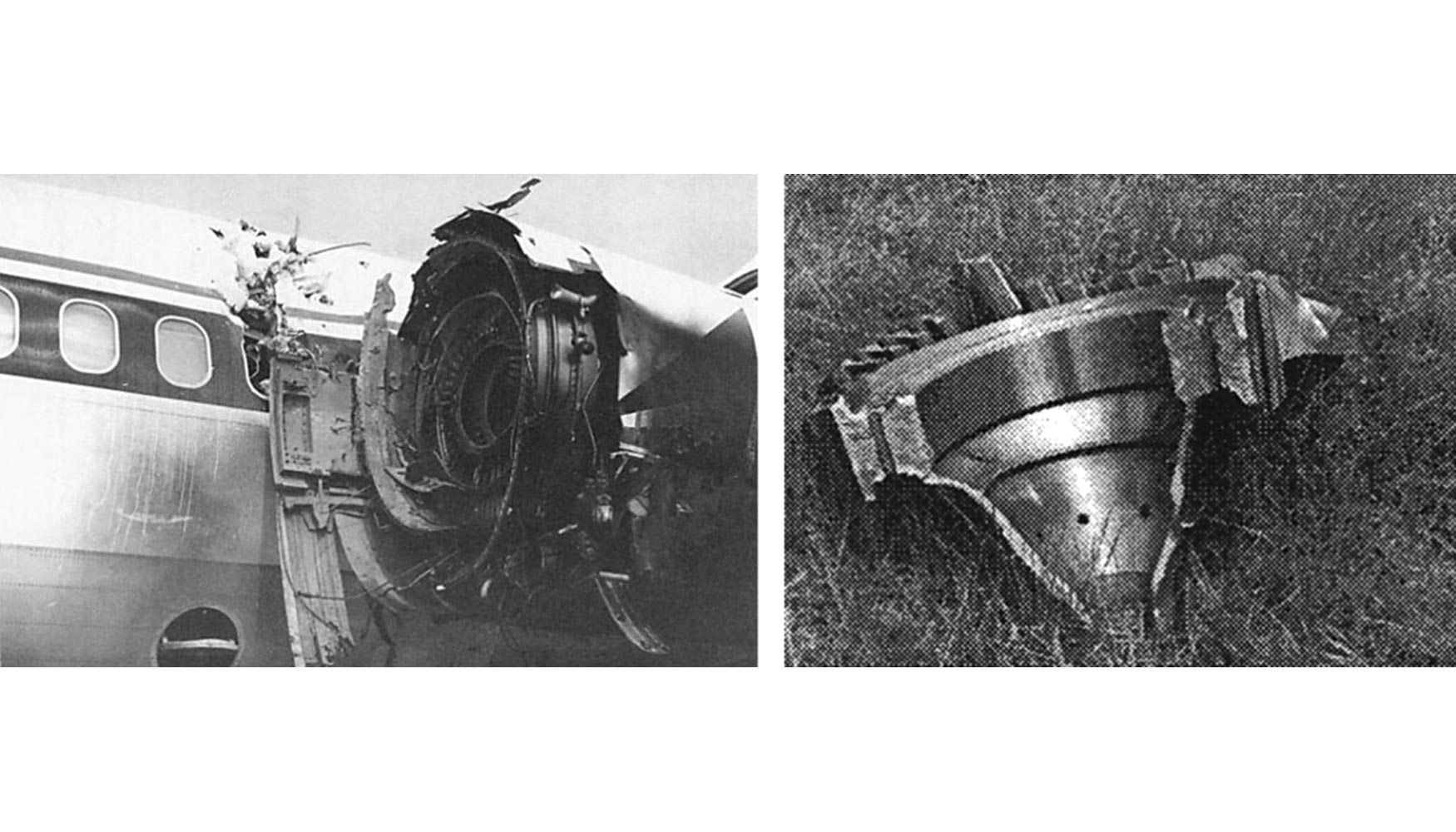
Los métodos utilizados en el análisis y diseño a fatiga pretenden simular el comportamiento de una pieza en servicio, de forma que se conozca de un modo aproximado la vida esperable del componente final, aunque estos métodos implican una capacidad de cálculo elevada y compleja, además se ha de estar seguro que se ha seleccionado el método correcto para el elemento en cuestión entre todos los disponibles para el cálculo a fatiga. Esto hace que en ocasiones resulte innecesario el empleo de criterios de fatiga en el análisis y diseño de determinadas piezas, si su fallo no va a comprometer un sistema o no va a suponer daños personales o económicos. En cambio existen otros campos donde el cálculo a fatiga de los componentes es absolutamente necesario, por ejemplo en el sector aeronáutico.
Los componentes de aeronave, tanto de motor como de estructura, son especialmente delicados en su fabricación. Todo proceso de fabricación de estos componentes lleva aparejadas operaciones de monitorización e inspección, desde un simple taladrado o roscado, hasta una soldadura, pasando por operaciones de grandes torneados. Con ello se pretende mantener un control de ciertos parámetros como fuerzas o potencias de la operación, que en caso de rebasar ciertos niveles límite, puedan indicar un estado de desgaste de la herramienta no indicado para su uso. Las operaciones ejecutadas de esta forma conllevan riesgos que deben cuantificarse mediante la realización previa de estudios de integridad superficial.
La fatiga y la integridad superficial están claramente relacionadas ya que una grieta de fatiga empieza la mayoría de las veces en la superficie de las piezas. Un buen análisis de integridad superficial se encargará de mantener la superficie y subsuperficie de las piezas en un estado óptimo, garantizando la no presencia de defectos que puedan constituir focos de aparición de grietas, que más adelante se puedan propagar por los sucesivos ciclos de funcionamiento del elemento. Entre los defectos del material más comunes, ya comentados anteriormente, que hay que tratar de evitar a toda costa por su capacidad de ser puntos de generación de grietas de fatiga, están por ejemplo marcas superficiales no esperadas, pequeños poros en el material debidos a impurezas o fallos en el proceso de fabricación, zonas afectadas térmicamente como consecuencia de una operación de mecanizado, como un taladro realizado no adecuadamente, u otros tipos de operaciones que impliquen procesos térmicos como láser o electroerosión por ejemplo, los cuales tienen que ser debidamente acabados para garantizar un estado de integridad superficial correcto de la pieza. Muchos de estos procesos tienen en común que producen daño metalúrgico, dejando la microestructura de la superficie alterada, con zonas de mayor dureza que pueden constituir puntos de concentración de tensiones originarias de grietas de fatiga. No sólo los defectos pueden ser origen de inicio de grietas, sino que también una operación de fabricación que aparentemente está bien realizada puede ser un problema. Por ejemplo, un torneado con unas condiciones de avance demasiado elevadas, que no presente necesariamente una microestructura alterada, pero en el que sea visible a simple vista el típico rallado sensible al tacto, puede generar problemas, ya que la superficie con numerosos picos y valles constituyen zonas de concentración de tensiones que puede provocar el inicio de una grieta que lleve al fallo de la pieza.
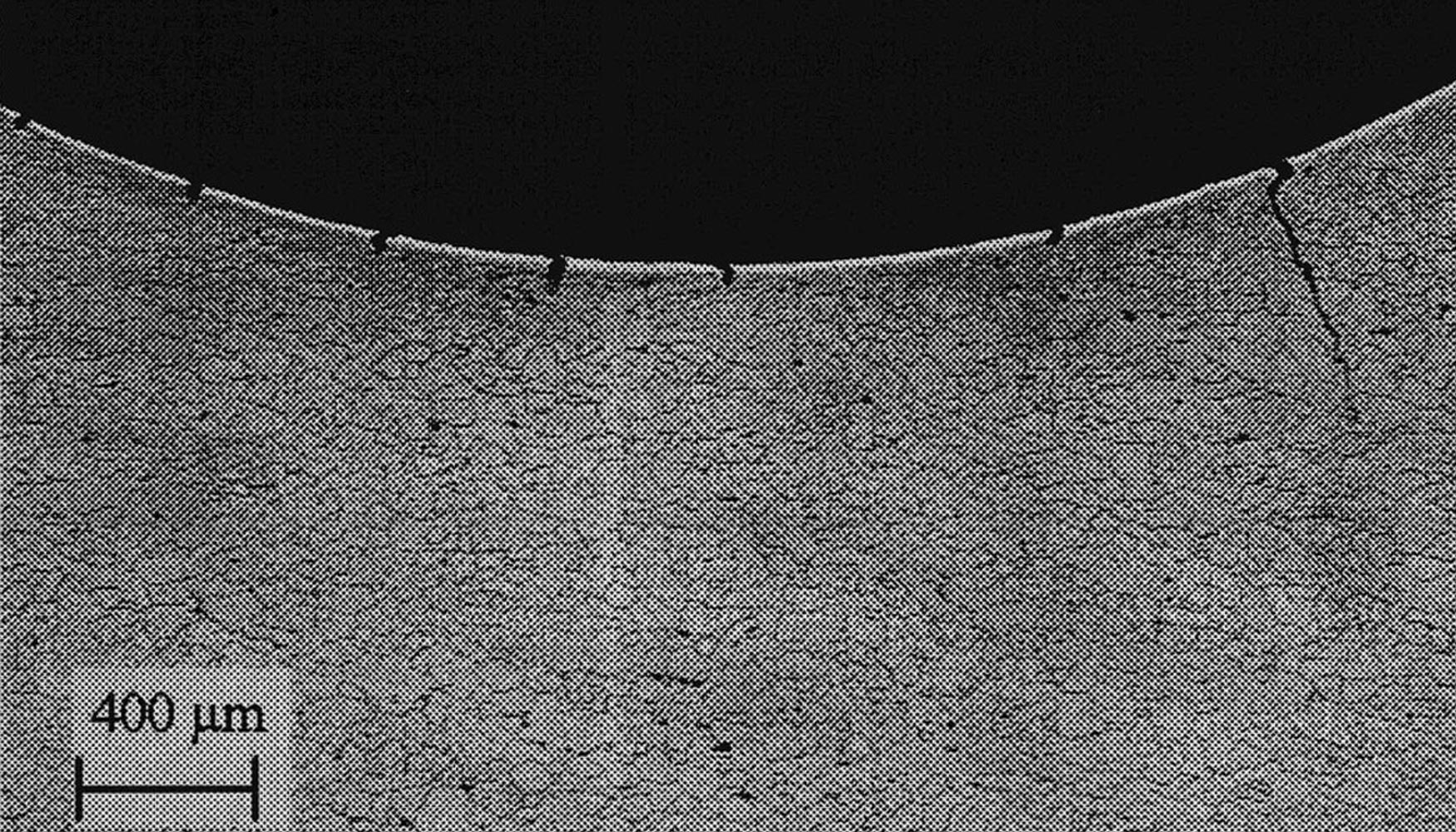
En concreto, dentro del ámbito del mecanizado por arranque de viruta propiamente, son muchos los factores que pueden influir en la vida a fatiga de un componente de máquina. Uno de los factores es el desgaste de la herramienta, ya que una herramienta con cierto nivel de desgaste va a dejar la pieza mecanizada en peores condiciones de integridad que una herramienta nueva, puesto que al ir variando la geometría del filo de corte a medida que su desgaste va avanzando, ésta corta peor el material, provocando una deformación excesiva y no deseada de los granos del material en la superficie de forma que la dureza superficial es mayor debido al endurecimiento por acritud. También influyen otros factores como la geometría de la herramienta, pudiendo haber geometrías positivas o en cambio más negativas y robustas, hecho que modifica el perfil de tensiones residuales en la subsuperficie del material del componente, lo cual resulta de vital importancia, siendo preferibles las tensiones residuales de compresión a las tractivas, para retardar todo lo posible la propagación de grietas de fatiga. En definitiva, hay que tratar de conseguir siempre que los procesos de fabricación se realicen en las mejores condiciones si se quiere alargar al máximo la vida de los elementos del sistema, hecho que se ve reforzado por los numerosos estudios que muestran como la vida a fatiga de probetas con mejores condiciones de integridad superficial es mucho más elevada.
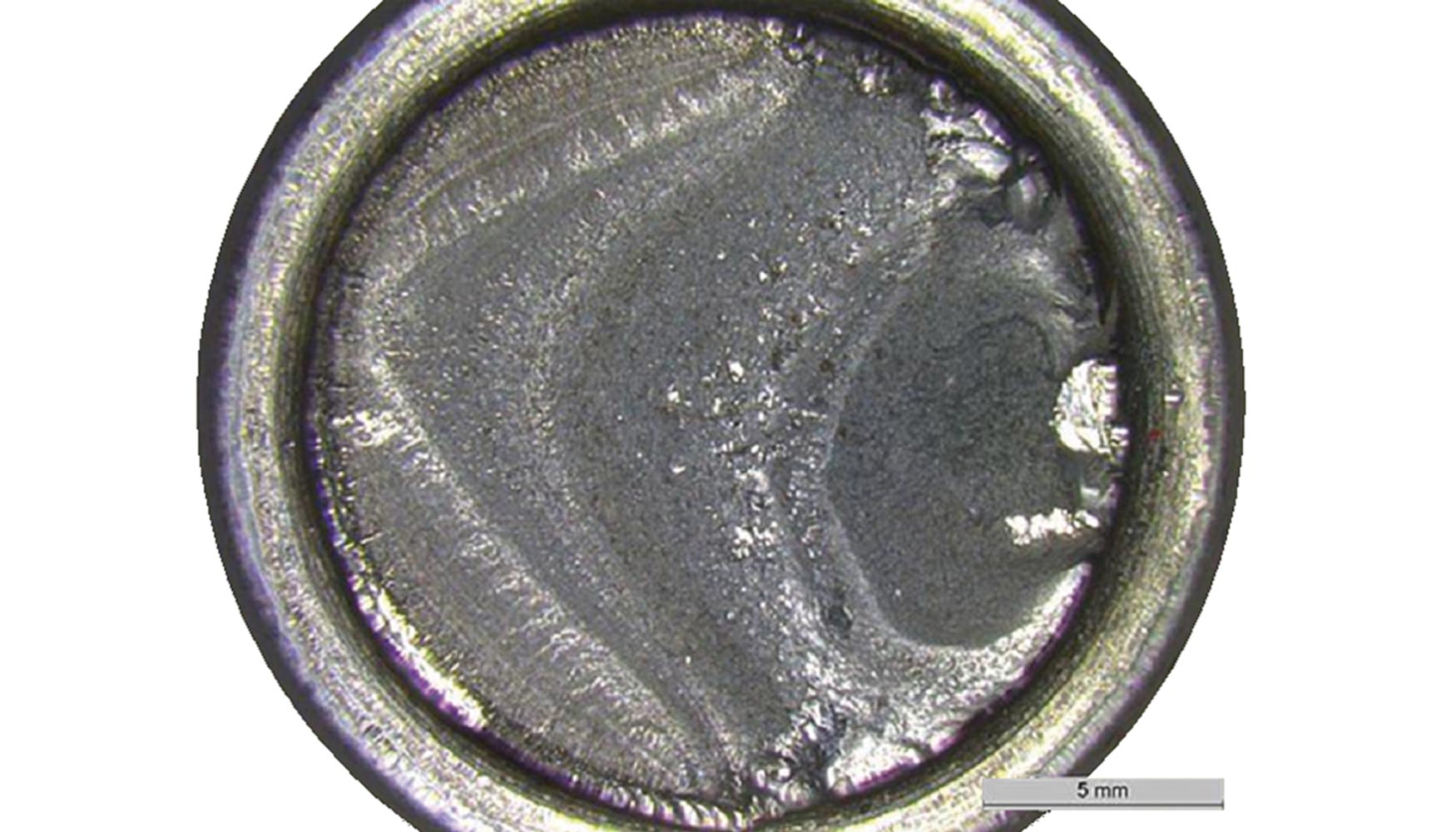
2.2. Fatiga superficial
El origen de la fatiga superficial se debe a los elevados esfuerzos cortantes originados en el contacto entre sólidos, que unidos al carácter variable de los mismos, pueden producir una dislocación de la estructura del material, generándose una microgrieta bajo la superficie. Esta grieta puede evolucionar y propagarse hasta alcanzar la superficie, produciéndose entonces un desprendimiento de material denominado picado, pitting.
La fatiga superficial es una forma de fallo común en elementos que trabajan sometidos a altas presiones de contacto y a un alto número de ciclos. Elementos típicos de sufrir este tipo de fallo son las levas, rodamientos y dientes de engranajes.
![Pitting en los flancos de un engranaje helicoidal. [Fuente: www.car-truck-parts.com] Pitting en los flancos de un engranaje helicoidal. [Fuente: www.car-truck-parts.com]](https://img.interempresas.net/fotos/1087577.jpeg)
Al fenómeno inicial de agrietamiento pueden sumarse otros factores tales como la oxidación del interior de la grieta, o la posibilidad de que el lubricante penetre en la grieta y actúe como una cuña hidrostática. En todo caso, es la existencia de un problema de fatiga superficial la que en un principio deteriora el sistema, siendo la causa inicial a evitar.
Para evitar este fenómeno es conveniente introducir tensiones residuales de compresión en las superficies, dado que la propagación de grietas se produce en los ciclos de tracción. Estas tensiones se pueden conseguir con tratamientos superficiales, tipo granallado o bombardeo de perdigones, o bien ser dejadas por el propio proceso de mecanizado aplicado (rectificado, torneado), aunque en este caso es un problema determinar si son de tracción o compresión.
La dureza es un factor difícil de evaluar en relación a este fenómeno. Si bien es cierto que la elevada dureza actúa contra la propagación de grietas, también es cierto que reduce la acomodación por deformación de las superficies (generándose por tanto contactos más localizados y tensiones de contacto más altas). Por este motivo suele ser conveniente disponer en el contacto dos materiales de diferente dureza, con objeto de que uno de ellos se acomode a la forma del otro.
3. Casos o ejemplos de componentes críticos
3.1. Ejemplo de pieza hibrida (TBH)
En el exigente campo de la motorización aeronáutica, los análisis de vida a fatiga son absolutamente necesarios en componentes catalogados como críticos. Componentes críticos de motor son todos aquellos cuyo fallo pueda poner en peligro la aeronavegabilidad del aparato o puedan causar daños personales a la tripulación. Todos los componentes rotativos son componentes críticos, y algunos componentes estáticos también reciben esta catalogación. Normalmente este tipo de componentes trabajan con un nivel de tensiones muy elevado por lo que están sujetos a estrictos controles, y ya desde su fase de diseño deben ser concebidos con criterios de vida a fatiga, normalmente de ciclos bajos (LCF), que garanticen su correcto comportamiento en servicio.
Un ejemplo de componente de este tipo se encuentra en la parte trasera de un motor de turbina de gas, por ejemplo el motor tipo turbofan tan utilizado en la aviación comercial. Se trata de una estructura estática mecanosoldada de disposición radial y de grandes dimensiones que tiene muchas funciones diferentes, por ello un fallo de este componente implica con toda seguridad el fallo catastrófico de ese motor, sino un problema mayor.
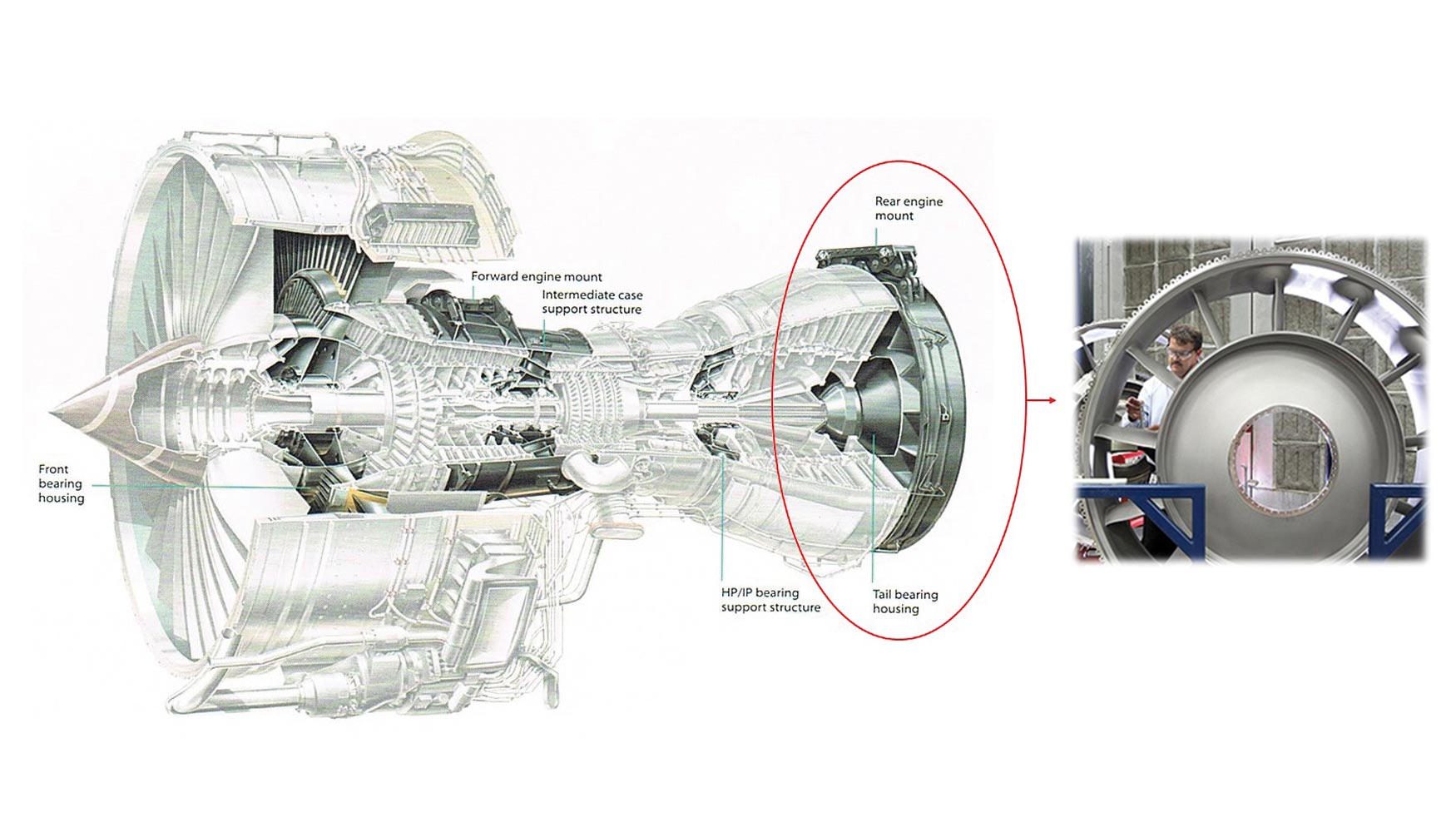
Entre las funciones principales de este componente, está la de servir de soporte estructural de la turbina, soportando todos los elementos internos de esta, como ejes, discos, carcasa, etc. además de suponer uno de los dos puntos de conexión del motor al ala del aparato, teniendo que sostener por tanto mucha masa suspendida, con sus inercias. Pero quizá su misión fundamental sea la de servir de apoyo del rodamiento de la turbina de baja presión, asegurando la alineación entre las partes rotatorias y las estáticas, de ahí que su nombre sea en inglés Tail Bearing Housing (TBH), traducido algo así como alojamiento de rodamiento trasero. Pero además tiene otras funciones como la aerodinámica para girar la corriente de gases de salida de la turbina hasta ponerla axial.
Un componente como este está, por tanto, sujeto a cargas mecánicas de todo tipo, además de cargas térmicas con motivo de los numerosos ciclos de vuelo de la aeronave. Las cargas mecánicas pueden ser de presión, de inercia, de maniobra, de manejo y transporte, o condiciones especiales entre otras. Por su parte las térmicas se pueden dividir en estacionarias o transitorias. Todo este conjunto de solicitaciones conllevan que el componente deba ser diseñado bajo criterios de fatiga mecánica y fatiga térmica, así como realizar un exhaustivo plan de control e inspección durante su fase de fabricación, asegurando que todas y cada una de las operaciones se ha realizado de forma correcta, manteniendo la integridad superficial bajo control.
Así pues, además de los comunes controles de procesos elementales como taladrados, roscados, torneados, fresados, etc., donde se controlan diferentes parámetros máquina y de herramienta, es necesaria la realización de controles más avanzados como inspección de todas las soldaduras mediante radiografías de rayos X, para detectar cualquier tipo de defecto como poros, microgrietas o zonas afectadas térmicamente anexas al cordón de soldadura. También por tratarse de un elemento con paredes delgadas ensamblado por partes, es muy importante el papel de las distorsiones después de la soldadura, lo cual no debe afectar a las operaciones posteriores de torneado de los diferentes anillos interior, exterior y bridas de amarre. Al igual que en otras piezas rotativas, en este caso también se ha de eliminar toda incertidumbre posible en lo relativo a la calidad interna de algunas operaciones de taladrado y roscado, sobre todo en los taladros circunferenciales realizados en ambas bridas de amarre del componente, los cuales están sometidas a grandes esfuerzos a pesar del reparto homogéneo de cargas debido al alto número de ellos, tantos como 140 taladros por cada brida aproximadamente.
Por lo comentado anteriormente se deduce la importancia de este elemento en un motor aeronáutico, y la importancia que cobra el aseguramiento de una alta integridad estructural y superficial del material después de todas las operaciones necesarias para su fabricación.
3.2. Ejemplo de corrosión galvánica en uniones de materiales disimilares mediante friction drilling
El taladrado por fricción o friction drilling es un procedimiento no convencional para generar agujeros en elementos metálicos de poco espesor. Este proceso se emplea comúnmente en uniones de chapas en sectores como el de calderería o de transporte. Debido a su posible uso en uniones de materiales disimilares, se trata de un ejemplo claro donde se puede estudiar la integridad de la unión frente a la aparición de corrosión galvánica.
La base de este proceso es la fricción generada por el rozamiento entre la herramienta de metal duro y la pieza. Esta herramienta produce calor en el metal, ablandándolo y permitiendo, gracias a la penetración de la punta y su avance, el arrastre del material reblandecido, generándose un agujero con una copa cónica. Sobre esta copa, además, puede realizarse un roscado, de forma que puede hacer la función de tuerca cuando empleamos elementos de fijación como tornillos.
![Operación de Friction Drilling [Fuente: www.buildlog.net] Operación de Friction Drilling [Fuente: www.buildlog.net]](https://img.interempresas.net/fotos/1087582.jpeg)
Una aplicación interesante de este procedimiento podría ser dentro del sector transportes, las uniones entre acero y aluminio presentes en las estructuras de los remolques de camiones o en autobuses. Al igual que sucede con el sector automovilístico, el peso del vehículo es de especial importancia, dado que la disminución del peso de los elementos constituyentes de éste ofrece la atractiva opción de aumentar la capacidad de carga del vehículo, pudiendo transportar más peso en menos viajes, con lo que disminuirían los costes de transporte del producto.
Existen diferentes tipos de corrosión que podrían afectar a la unión entre acero y aluminio mediante el proceso de friction drilling. Sin embargo, la más crítica es la corrosión galvánica, por estar dos (o tres en caso de utilizar tornillos en la unión) materiales diferentes en contacto, pudiéndose formar una pila galvánica.
La corrosión galvánica, ocurre cuando dos o más metales diferentes se acoplan electrolíticamente en presencia de un ambiente corrosivo. Uno de ellos se corroe preferentemente mientras el otro es protegido de dicha corrosión. Cualquier metal se corroe cuando se acopla con otro con un potencial más positivo o más noble en la serie galvánica. Al mismo tiempo, el metal más noble se protege de la corrosión.
Para poder conocer cuál, de los dos, es el metal que se corroerá, se puede utilizar la serie fem estándar o la serie galvánica. La serie galvánica representa la reactividad relativa entre los materiales metálicos cuando éstos están sumergidos en agua de mar. De este modo, cuanto más positivo sea el potencial del electrodo más noble será el metal y más inerte, comportándose como cátodo y reduciéndose. Por el contrario, cuanto más negativo sea el potencial, tendrá un mayor comportamiento anódico.
Es de gran importancia señalar que una de las características fundamentales del aluminio en cuanto a su oxidación en contacto con otro metal se refiere, es la formación de una capa de alúmina (Al2O3), que cuando cubre completamente la superficie del aluminio, debido a su gran adhesión al aluminio base y su baja porosidad, lo pasiva, evitando que la oxidación siga profundizando en el aluminio. Además, sirve de protección catódica al acero, aunque por muy poco tiempo, ya que la velocidad de formación de la capa de alúmina es muy elevada. A partir de ese momento, el aluminio se comporta como un material inerte, imposibilitando la creación de una pila galvánica entre éste y el acero.
En definitiva, si se ponen en contacto acero y aluminio, al principio se producirá una pila galvánica que provocará la oxidación superficial del aluminio, creando una barrera que lo protegerá, y una vez formada completamente la capa de alúmina, no se producirá ningún tipo de reacción electroquímica entre ambos metales. Teniendo esto en cuenta, los modos de corrosión que pueden afectar a la unión entre acero y aluminio son los mismos que afectarían a ambos metales por separado: la oxidación, la corrosión por erosión, la corrosión intergranular, la corrosión por picadura, la corrosión por aireación diferencial, y la corrosión bajo tensión.
Además del análisis teórico de la corrosión galvánica, se pueden realizar ensayos experimentales para determinar la resistencia a la corrosión de la unión. Para ello se emplea una cámara de niebla salina donde se introducen las probetas de uniones realizadas mediante friction drilling con diferentes calidades de tornillos y se someten al normalizado ensayo de cámara de niebla salina (ASTM B117).
En este ensayo las muestras son sometidas a una temperatura de 35°C y a una solución en forma de niebla de agua con 5% NaCl durante un periodo de tiempo comprendido entre 24 y 1000 horas. Cada cierto número de horas de ensayo se analizan las muestras comprobando la aparición de óxido, las zonas más afectadas por la corrosión y el tipo de corrosión que se ha producido. De esta forma se puede verificar el comportamiento a la corrosión del par de metales acero-aluminio y la integridad de la unión generada por friction drilling, así como la calidad de tornillo idónea para este tipo de uniones.
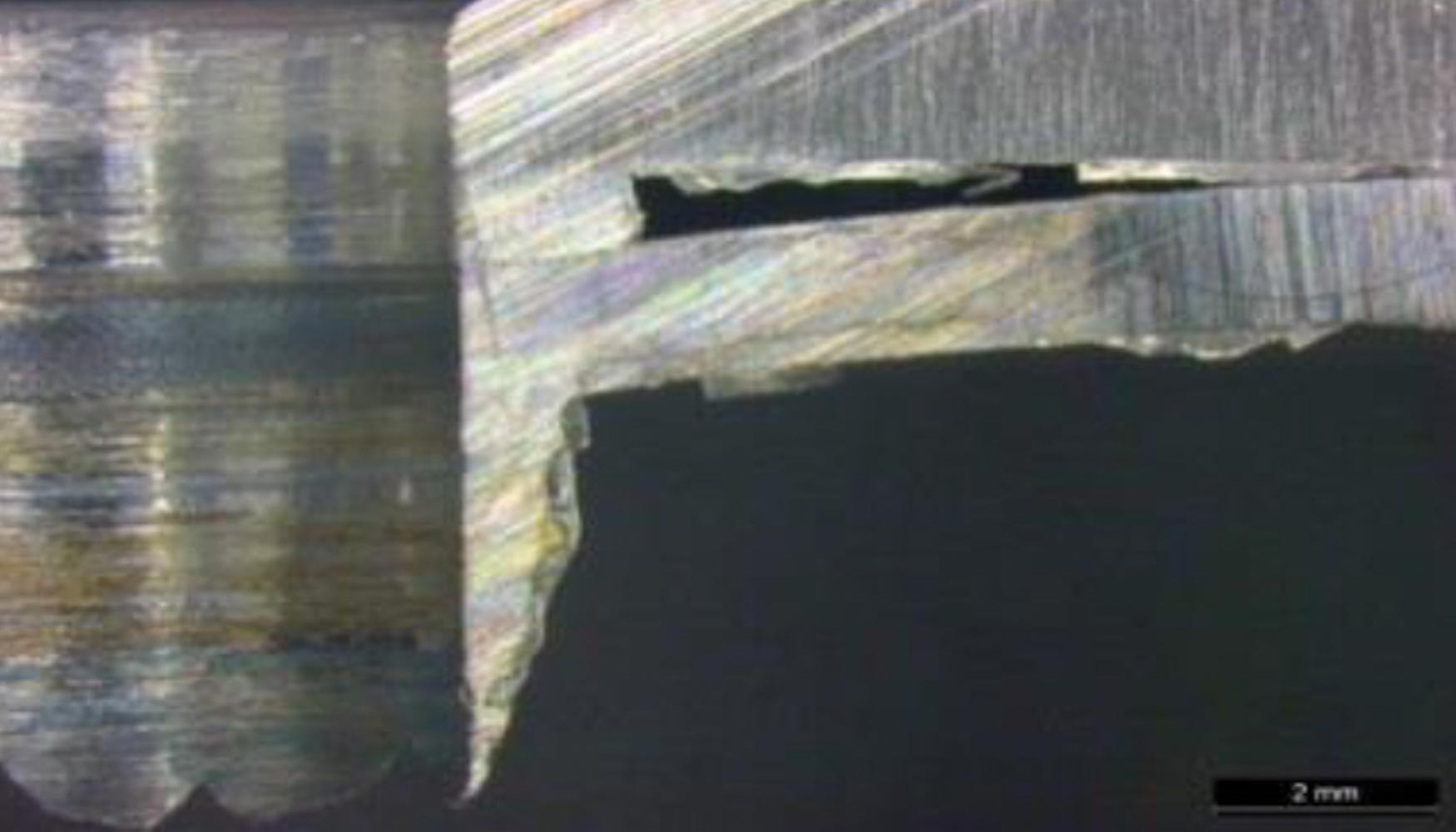
4. El laboratorio de integridad
Vista la importancia que tiene el conocimiento de la integridad superficial que dejan los procesos de fabricación, principalmente en aquellos componentes que vayan a estar sometidos en su vida útil a cargas dinámicas variables y condiciones ambientales severas, en este apartado se tratará de hacer una breve descripción de los ensayos/análisis más habituales a realizar para conseguir tal fin.
4.1. Textura superficial-topografías
El que una pieza sea apta para una función dada depende de un conjunto de condiciones, y, especialmente, de sus estados superficiales. El conocimiento de las desviaciones de forma y de rugosidad, ayudan a tener más información al respecto. Actualmente las topografías superficiales realizadas con microscopios con focales sin contacto, permiten su obtención en unos pocos minutos, arrojando una información muy útil a través de los parámetros de rugosidad definidos por la norma correspondiente.
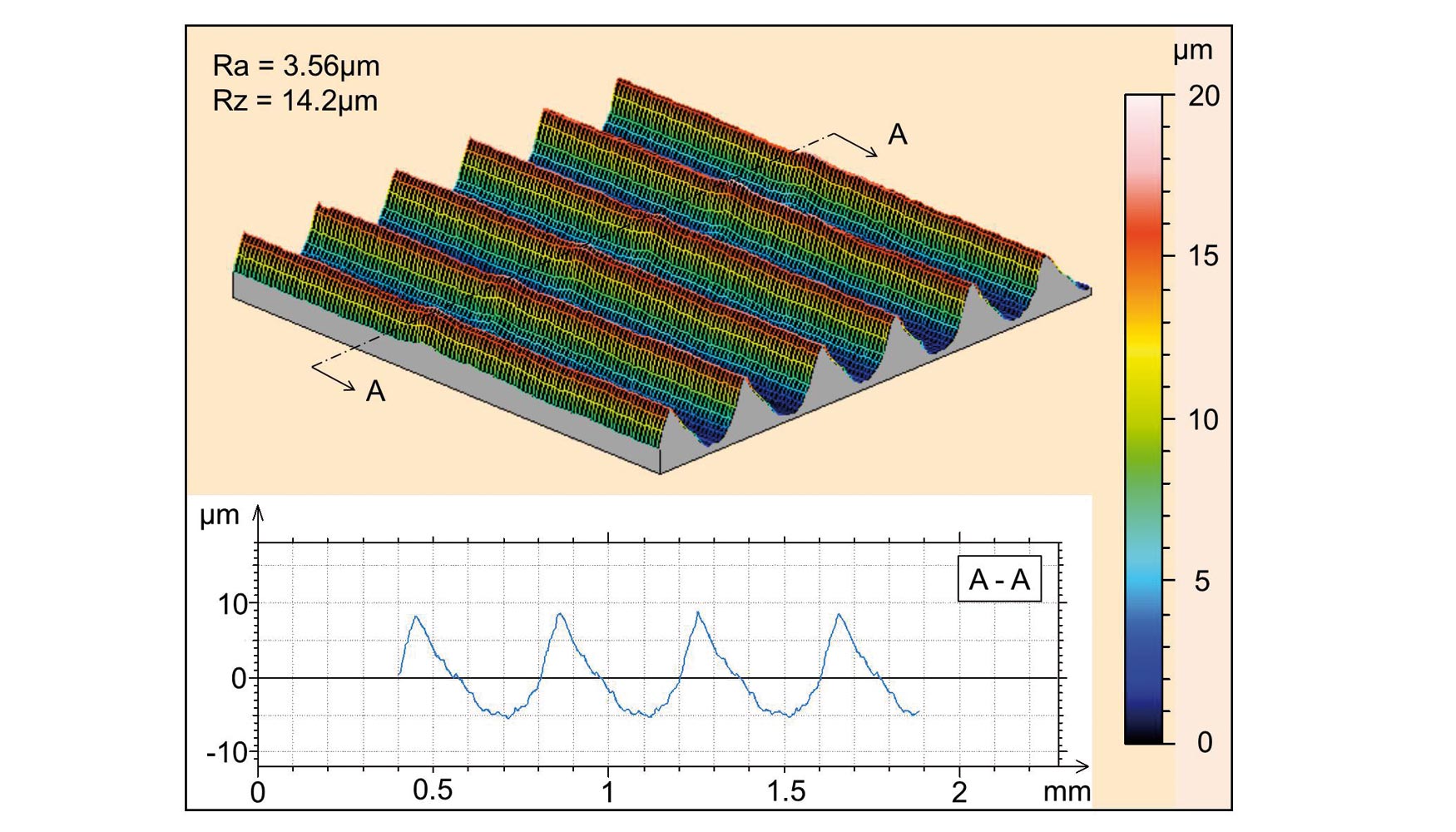
4.2. Métodos NDT
El análisis minucioso de la presencia de grietas o defectos exteriores en la pieza, así como su forma y dimensionamiento, es una práctica habitual en los principios de un estudio de integridad superficial. Para ello, existen una variedad de técnicas o métodos no destructivos, NDT, que sin producir daño alguno al material permiten llevar a cabo dicha tarea. Algunos de ellos son:
Métodos de inspección visual
Se basan en la iluminación de la pieza/probeta con luz para proceder a una inspección visual a nivel macro. Los equipos utilizados son principalmente lentes con aumentos inferiores a 10x.
Ultrasonidos
Estos métodos utilizan ondas ultrasónicas para evaluar el estado en el que se encuentra un material. Los defectos detectados en su interior absorben o desvían las ondas sonoras que llegan a ellos, para luego ser detectados como cambios en las ondas. Se pueden detectar agujeros, delaminaciones, huecos y otro tipo de daños interiores que a simple vista sería imposible.
Métodos magnéticos
Son métodos basados en la medición del ruido magnético de Barkhausen, (RMB), que se viene usando como ensayo no destructivo en la evaluación de cambios microestructurales generados en materiales ferromagnéticos. Esta técnica se basa en medir las propiedades magnéticas de materiales ferromagnéticos. Como ejemplo, en los aceros, estas propiedades son sensibles a los cambios en el material, tales como la microestructura y la presencia de esfuerzos residuales.
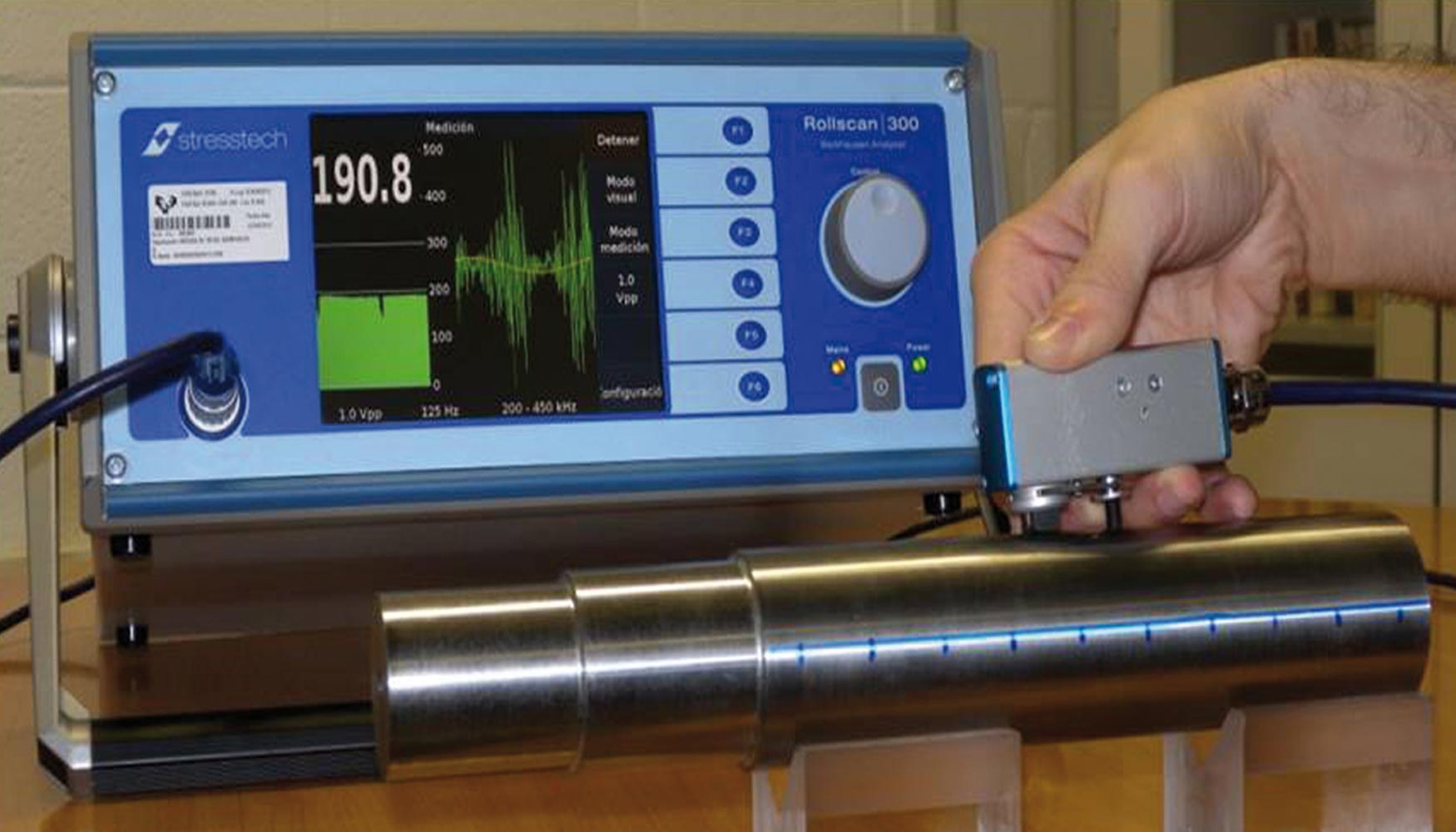
Líquidos penetrantes
Método utilizado tanto en inspección preventiva como predictiva. Consiste en rociar la zona de la pieza a inspeccionar de unas partículas microscópicas que tienen la propiedad de ser fluorescentes cuando se les aplica una luz ultravioleta.
En la imagen puede observarse una grieta en el plato de rampas Malossi MHR, pieza clave en la transmisión mecánica de motos de poco cilindraje.
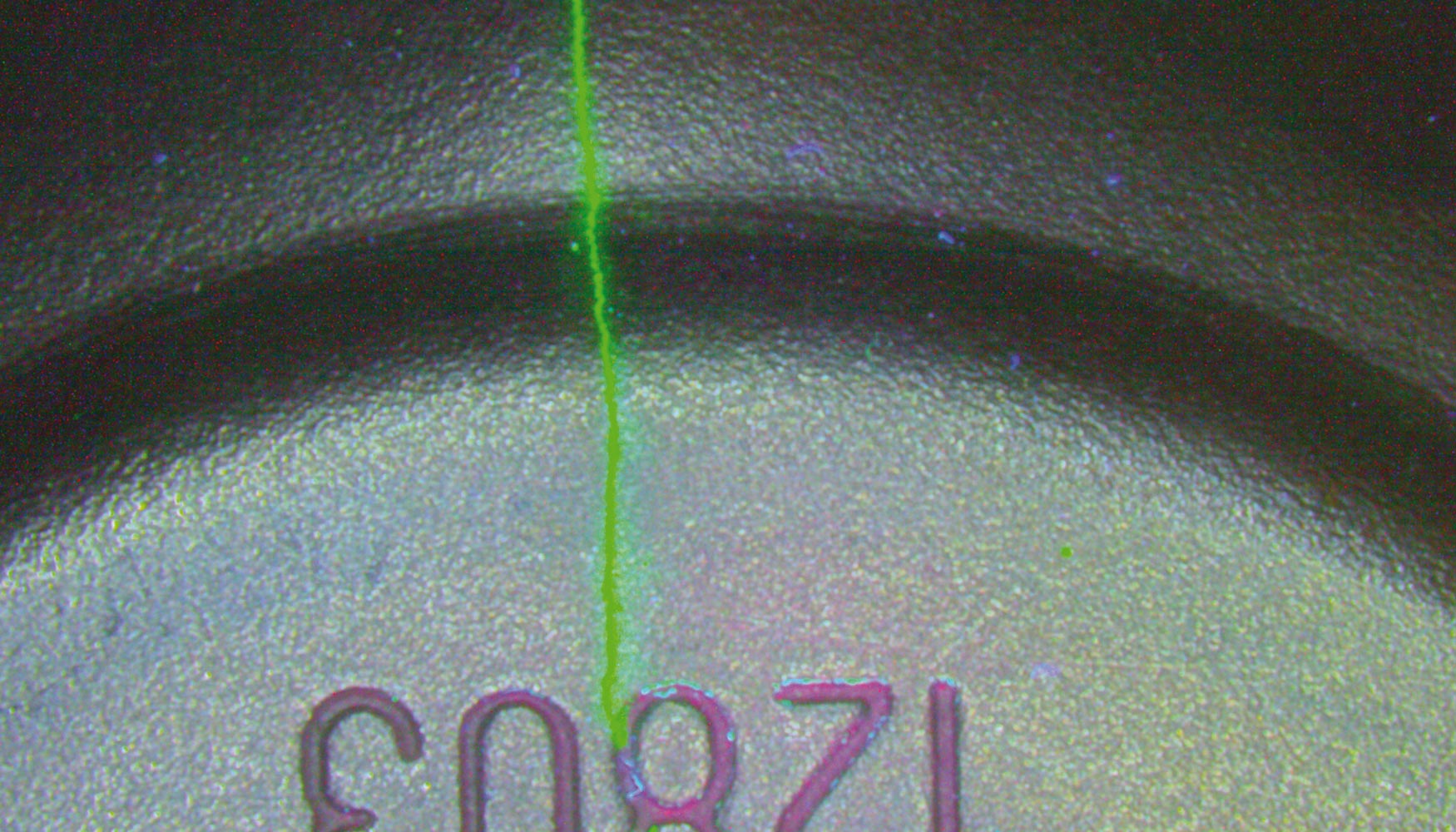
4.3. Metalografía
La metalografía se encarga de estudiar las características estructurales de un metal o aleación, como el tamaño de grano, tamaño, forma y distribución de las fases que comprenden la aleación y de las inclusiones no metálicas, así como la presencia de segregaciones y otras irregularidades que pueden modificar las propiedades mecánicas y el comportamiento general del material. El equipo utilizado para su observación es el microscopio metalográfico, que permite examinar muestras con aumentos que van de 50 a 2000x. Previo a la observación se requiere una preparación adecuada de las probetas con el objeto de obtener una superficie plana, libre de ralladuras y con acabado espejo. En las imágenes presentadas puede observarse el daño superficial provocado por diferentes procesos de fabricación (electroerosión y aporte láser y torneado) sobre diferentes materiales. Puede observarse la presencia de microgrietas, microporosidades, y capa refundida en el caso de la electroerosión y la deformación de granos producida en un torneado de acabado de Inconel con plaquita desgastada.
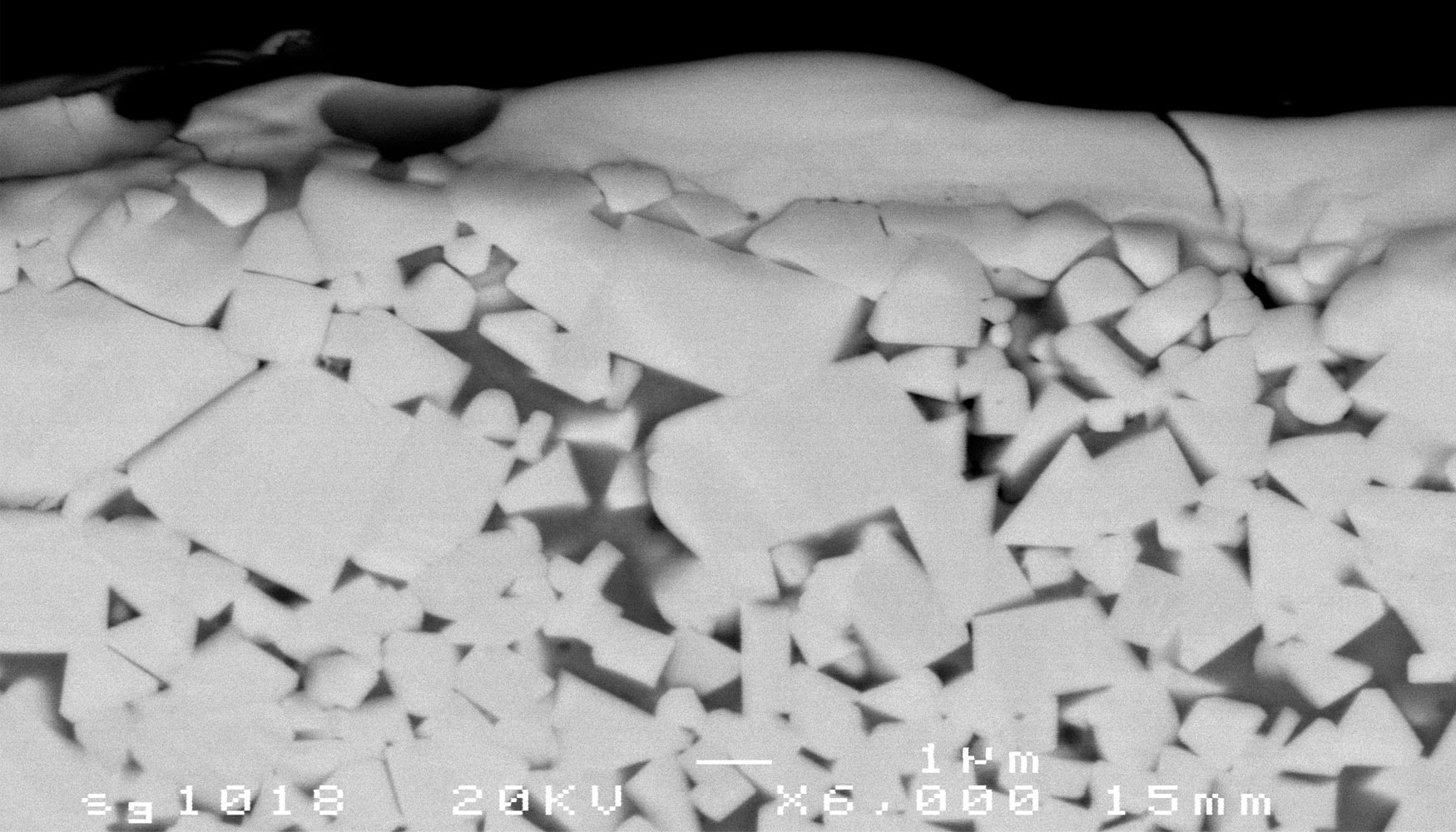
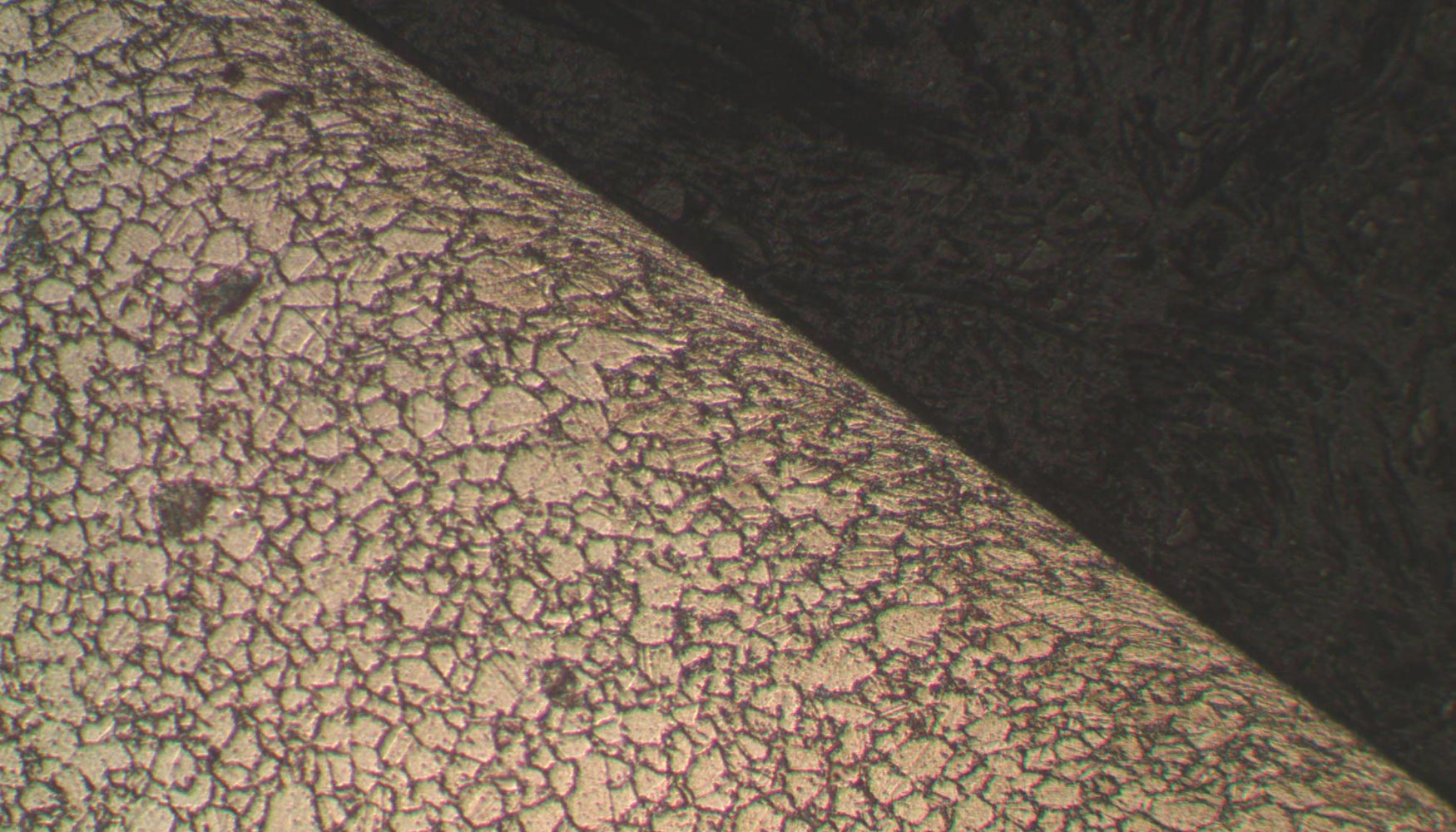
La preparación metalográfica de muestras también permite realizar análisis de microdurezas, muy útiles para comprobar la efectividad de un tratamiento térmico, de un recubrimiento o la zona afectada por el calor provocado por algunos procesos sobre la sub-superficie de los materiales, como la soldadura. En la imagen se presenta un análisis de microdureza Knoop sobre una probeta de Inconel 718 mecanizada a la que se le ha realizado un proceso complementario de bruñido por deformación. Puede observarse como en la zona superficial donde se ha realizado el tratamiento mecánico superficial, el valor de la dureza es sensiblemente mayor.
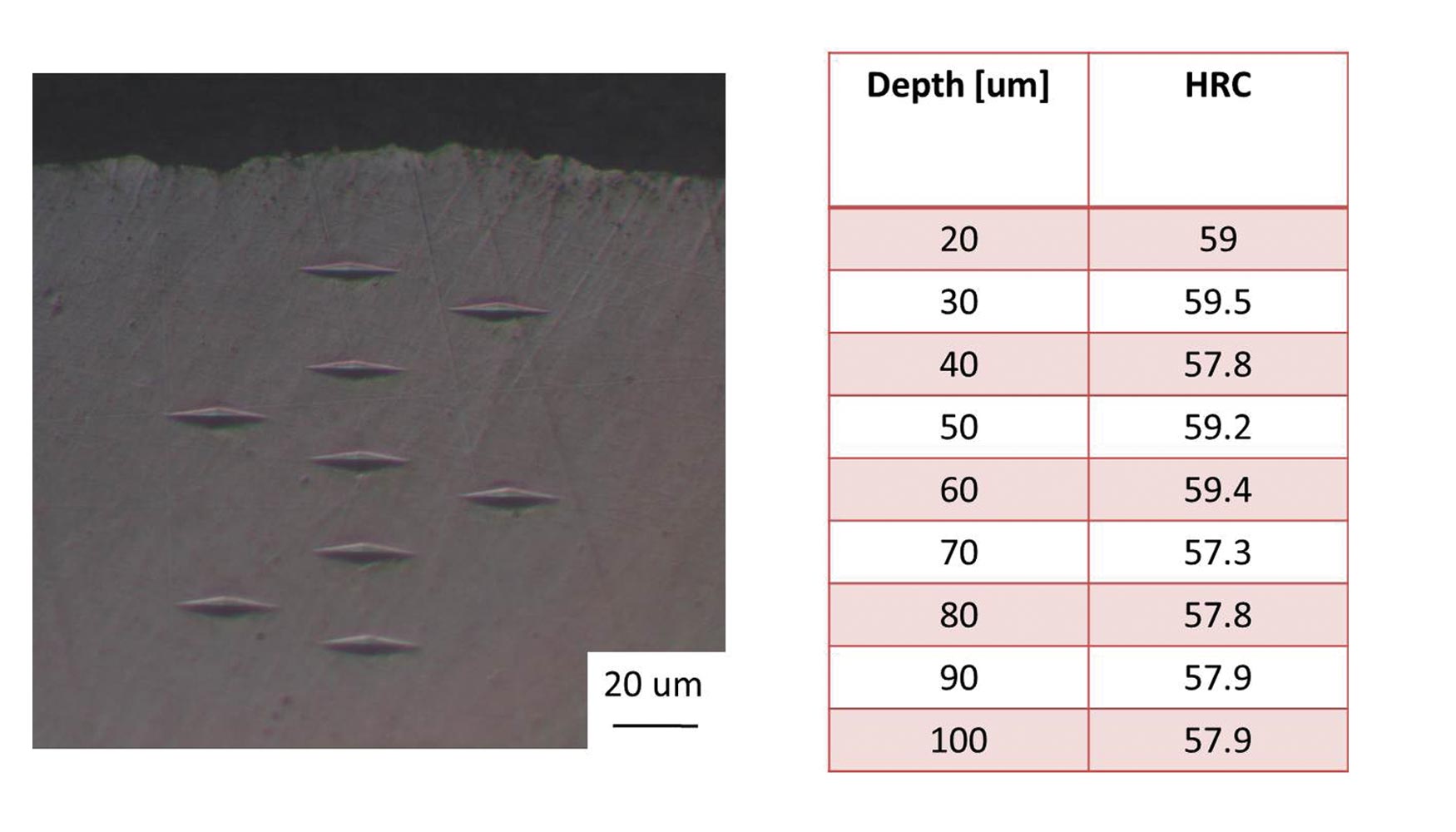
4.4. Tensiones residuales
Los procesos de fabricación tienen una influencia directa en la introducción de tensiones residuales. Mientras las tensiones sean a compresión, favorecerán el comportamiento a fatiga y a corrosión del componente. Cuando las tensiones internas son a tracción, sobre todo en las zonas próximas a la superficie, pueden favorecer el inicio y/o propagación de pequeñas grietas. Por ello, hay casos en los que se hace necesario realizar ensayos que permitan medir estas tensiones y actuar en consecuencia.
Existen diferentes técnicas de medición de tensiones residuales. Por un lado están las no destructivas, como los métodos magnéticos y métodos ultrasónicos y acústicos, que sólo proporcionan información cualitativa. Por otro lado se encuentran las técnicas destructivas, entre las que destaca el uso del método del Hole Drilling, que mide las deformaciones elásticas que se recuperan al practicar un agujero en la zona donde se quiere realizar la medición de tensiones. Estas deformaciones están relacionadas con las tensiones residuales través de la ley de comportamiento de los materiales.
4.5. Ensayos de fatiga y corrosión
El estudio más completo de integridad superficial contemplaría también la realización de ensayos de fatiga y corrosión.
Los ensayos de fatiga tienen por objeto analizar las características resistentes de los materiales cuando trabajan bajo cargas variables, siendo uno de los más utilizados el de flexión rotativa.
En cuanto a los ensayos de corrosión, éstos están normalizados en función del tipo de corrosión presente. El ensayo de corrosión en atmósferas húmedas saturadas, ensayos bajo atmosfera corrosiva, ensayos de corrosión cíclica, ensayos al dióxido de azufre con condensación general de la humedad o ensayos de niebla salina cuporacética, son algunos ejemplos.
Friction stir welding y bruñido por deformación
El proceso de Friction Stir Welding (FSW), es un método de soldadura en estado sólido ideado por The Welding Institute a comienzos de los años 90. Son varias las ventajas principales de este proceso de soldadura, como por ejemplo ausencia de porosidad y de fisuración en caliente de la unión obtenida; no necesidad de preparación de junta ni mecanizado de refuerzo; no se utilizan consumibles para soldar y se trata de un proceso automático. La principal desventaja de este proceso está relacionada con la integridad superficial generada y las propiedades mecánicas de la junta. Durante el proceso, se pueden generar tensiones residuales de tracción que, aunque menores que en otros procesos de unión convencionales, suponen un grave problema reduciendo la resistencia a fatiga del componente final.
Además de mejorar otras propiedades como la dureza superficial y la rugosidad resultante, la aplicación de bruñido por deformación tras el proceso de FSW mejora el campo tensiones en superficie introduciendo tensiones residuales de compresión. En la figura se muestran los valores máximos de tensiones residuales obtenidos en ensayos realizados en la Escuela de Ingenieros de Bilbao (UPV/EHU). Se observa como antes del bruñido las tensiones residuales son de tracción, alrededor de 50-100 MPa. Tras el proceso de bruñido, las tensiones máximas son de compresión. Se aprecia como los valores en dirección perpendicular al bruñido son mayores que en la dirección de bruñido, al igual que sucede con otros materiales y procesos. Los resultados también muestran como la presión es el parámetro más influyente en el valor final de las tensiones, siendo estas más compresivas a medidas que se aumenta la presión.
Técnicamente hablando, el bruñido con bola se presenta como una solución eficiente, de bajo coste y flexible para mejorar las propiedades físicas y mecánicas de aleaciones de aluminio soldadas por FSW. La combinación de FSW y un tratamiento mecánico superficial por deformación, como el bruñido, es una alternativa interesante para este tipo de proceso.
![Proceso de Friction Stir Welding [Imagen de news.cision.com] Proceso de Friction Stir Welding [Imagen de news.cision.com]](https://img.interempresas.net/fotos/1087595.jpeg)
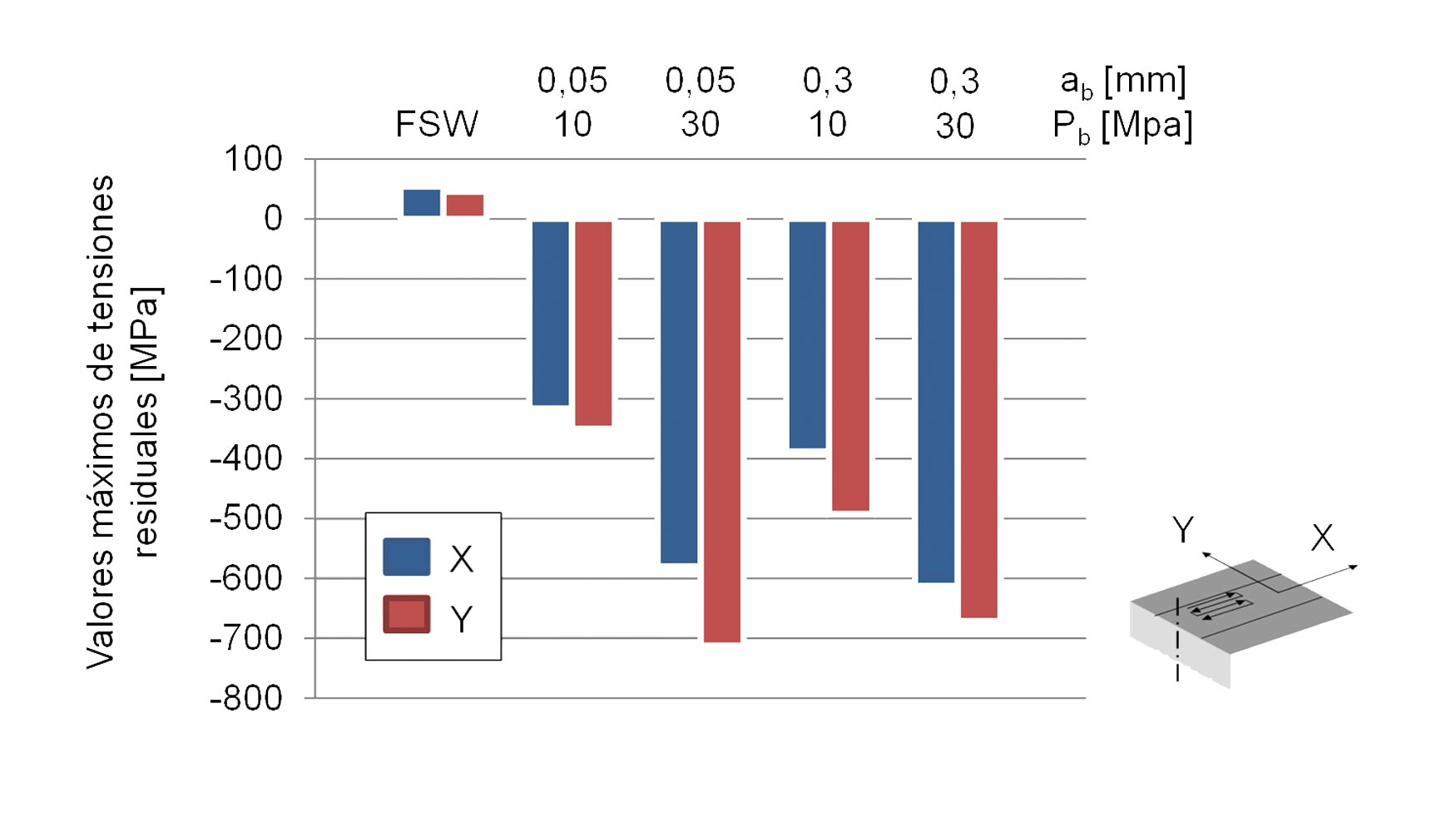