Fabricación aditiva: Qué es cada tecnología
Desde hace ya unos años se está dando relevancia a la fabricación aditiva, como una serie de procesos capaces de fabricar de forma rápida y directa componentes muy complejos directamente desde su diseño 3D. Las ventajas de estos procesos son obvias, pero es importante recalcar que dentro de la fabricación aditiva se agrupan diferentes procesos que en función de sus características permiten fabricar componentes en diferentes materiales, con grandes diferencias de precisión, calidad superficial y, por supuesto, precio. Dentro de todos estos procesos, una de las aplicaciones de más relevancia y que posiblemente sea la más conocida de todas haya sido el empleo de una tecnología denominada Fused Deposition Modelling (más conocida por su acrónimo FDM) que consiste en la fusión selectiva de un hilo de plástico en un cabezal que a su vez va depositando el material capa a capa, formando una geometría 3D. Esta técnica es la base de todas las impresoras 3D que hay en el mercado y que posiblemente sean los sistemas de fabricación aditiva más conocidos y empleados en la actualidad. De esta forma, la fabricación aditiva (o por lo menos uno de los procesos que la forman) se ha convertido en un fenómeno que va más allá de las empresas o del sector de la fabricación de componentes ya que es utilizado en la actualidad por diferentes usuarios para generar prototipos de urbanizaciones, material deportivo, vestidos o zapatos de moda. Es común observar una impresora 3D en escuelas, universidades, centros de diseño y se está comenzando a plantear su potencial uso doméstico. De hecho, ya hay conocidos grandes almacenes que comercializan impresoras 3D para uso doméstico. Sin embargo, y a pesar de la proliferación de estos equipos también en la industria, la fabricación aditiva engloba a un número mucho más amplio de procesos y aplicaciones.
Comenzando con una breve contextualización histórica, los procesos de fabricación aditiva son herederos de los procesos de Fabricación Rápida de Prototipos (conocidos también por el término inglés Rapid Prototyping) en los que el objetivo final era la creación de un prototipo físico a partir de un CAD 3D, pero que rara vez cumplía con los requisitos mínimos para su uso como una pieza funcional.
Inicialmente, el impacto industrial de estos procesos fue pequeño debido fundamentalmente al alto coste de los sistemas de fabricación rápida de prototipos y a que su uso estaba limitado a la fabricación de un prototipo no funcional. De esta forma, las empresas usuarias de estas tecnologías se concentraban fundamentalmente en el sector médico y aeronáutico/aeroespacial.
A lo largo de la década de los 90 se desarrollaron nuevos procesos de fabricación aditiva, sobre todo en los procesos orientados a la fabricación de piezas funcionales, tanto en materiales poliméricos como metálicos. Así, se comenzó a comercializar sistemas capaces de fabricar piezas funcionales capa a capa mediante fabricación aditiva en materiales como Nylon, ABS o aleaciones metálicas como acero inoxidable o aleaciones base níquel o base titanio. En esta década se pasa a llamar a estos procesos como Rapid Manufacturing o Fabricación Rápida y comienzan a ser utilizados por otros sectores en algunas aplicaciones industriales como la fabricación de pequeños moldes o insertos de moldes de alta complejidad o la fabricación de componentes de plástico para vehículos de competición o de muy alta gama. Sin embargo, el precio de los equipos seguía siendo prohibitivo para la mayoría de las empresas y el nicho de aplicaciones donde la aplicación de las técnicas de fabricación rápida podía ser rentable se reducía a pocos clientes.
De esta forma, en la actualidad, se ha evolucionado hacia la incorporación de nuevos procesos y métodos de fabricación aditiva barriendo un amplio espectro de materiales, calidades de pieza y aplicaciones. Se puede hacer una primera clasificación en dos grandes grupos: Fabricación aditiva para piezas de plástico y para piezas metálicas. Comenzando por las piezas de plástico, destaca la aparición de equipos industriales a costes muy asequibles (por debajo de 10.000€ en muchos casos), capaces de fabricar piezas en materiales como ABS o PLA. La reducción del coste de los equipos, ha permitido a muchas empresas acceder a esta tecnología. La calidad de las piezas, estando todavía lejos de la que se puede obtener por moldeo, es en muchas ocasiones más que suficiente y la tendencia muestra la proliferación de distribuidores tanto de materiales como de máquinas, por lo que es razonable pensar que la fabricación aditiva de piezas de plástico irá a más a lo largo de los próximos años.
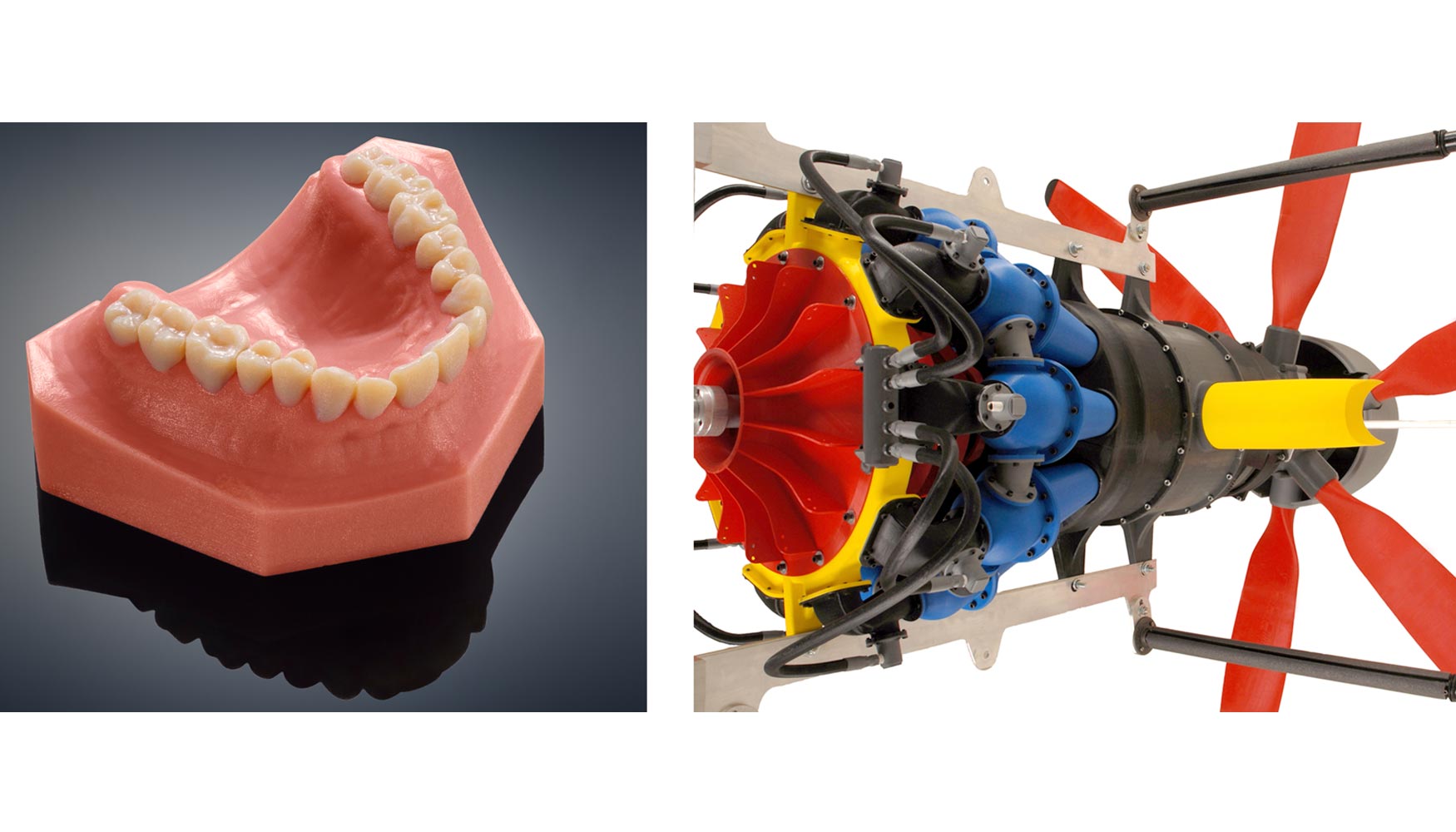
Izq., modelo de la dentadura inferior de un paciente. Dcha., modelo completo de un turbofan (Stratasys).
En cuanto a la fabricación aditiva de piezas metálicas, el escenario actual muestra algunas tendencias comunes a las planteadas en piezas de plástico, pero con la importante particularidad del alto precio de los sistemas. Para dar una idea del coste que supone un sistema de fabricación aditiva capaz de fabricar piezas metálicas, el coste puede superar los 600.000€ en muchos casos, siendo mucho más elevado si se desea un sistema capaz de fabricar piezas de tamaño medio-grande. Este hecho hace que la implantación de las técnicas de fabricación aditiva para piezas metálicas sea mucho más lenta y limitada a empresas que necesiten fabricar piezas muy complejas y de muy baja tirada.
Tal y como se ha comentado, la fabricación aditiva es, por tanto, un grupo de tecnologías que pueden ser más o menos accesibles pero que presentan diferentes capacidades y aplicaciones. Así, a lo largo de los siguientes apartados, se tratará de dar una idea de cuando es rentable aplicar los procesos de fabricación aditiva y de los tipos de procesos de fabricación aditiva que existen actualmente en el mercado.
¿Cuándo es conveniente utilizar procesos de fabricación aditiva?
Una de las primeras dudas que puede surgir entre los posibles usuarios de algún proceso de fabricación aditiva es: ¿De verdad necesito incorporar una máquina de aporte de material? Se trata de una duda más que razonable, ya que no solo se trata de adquirir un sistema con su coste inicial, sino de incorporarla e integrarla dentro de la empresa con todas sus consecuencias… Formación de personas, integración del proceso dentro de la empresa, necesidad de mantenimiento, etc.
En términos generales, es importante recalcar que los procesos de fabricación aditiva son muy eficaces frente a otros procesos alternativos en las siguientes condiciones:
- Creación de un prototipo o primera pieza para su validación.
- Fabricación de una pieza única o tiradas muy bajas.
- Fabricación de piezas extremadamente complejas.
Si se da una o varias de estas condiciones, los procesos de fabricación aditiva pueden ser la mejor alternativa o incluso la única forma de fabricar la pieza. Sin embargo, hay ocasiones donde los procesos de fabricación aditiva pierden sus ventajas y pueden no ser la mejor opción.
Por ejemplo, a pesar de que en la última década se ha avanzado en incrementar la calidad de las piezas fabricadas, una de las principales desventajas de los procesos de fabricación aditiva es la relativa baja calidad de las piezas en comparación con las obtenidas por moldeado o mecanizado. En general, estos procesos no alcanzan los niveles de acabado superficial y tolerancia dimensional de los procesos convencionales, por lo que es habitual que se realicen operaciones de acabado posterior. De esta forma, si es necesario fabricar una tirada media-alta de piezas y/o existen altos requisitos de calidad superficial y tolerancias, los procesos de fabricación aditiva pierden efectividad.
Por otro lado, la mayoría de los procesos de fabricación aditiva tienen limitaciones de tamaño de pieza, por lo que en ese caso es necesario dividir la pieza en subcomponentes y unirlos posteriormente.
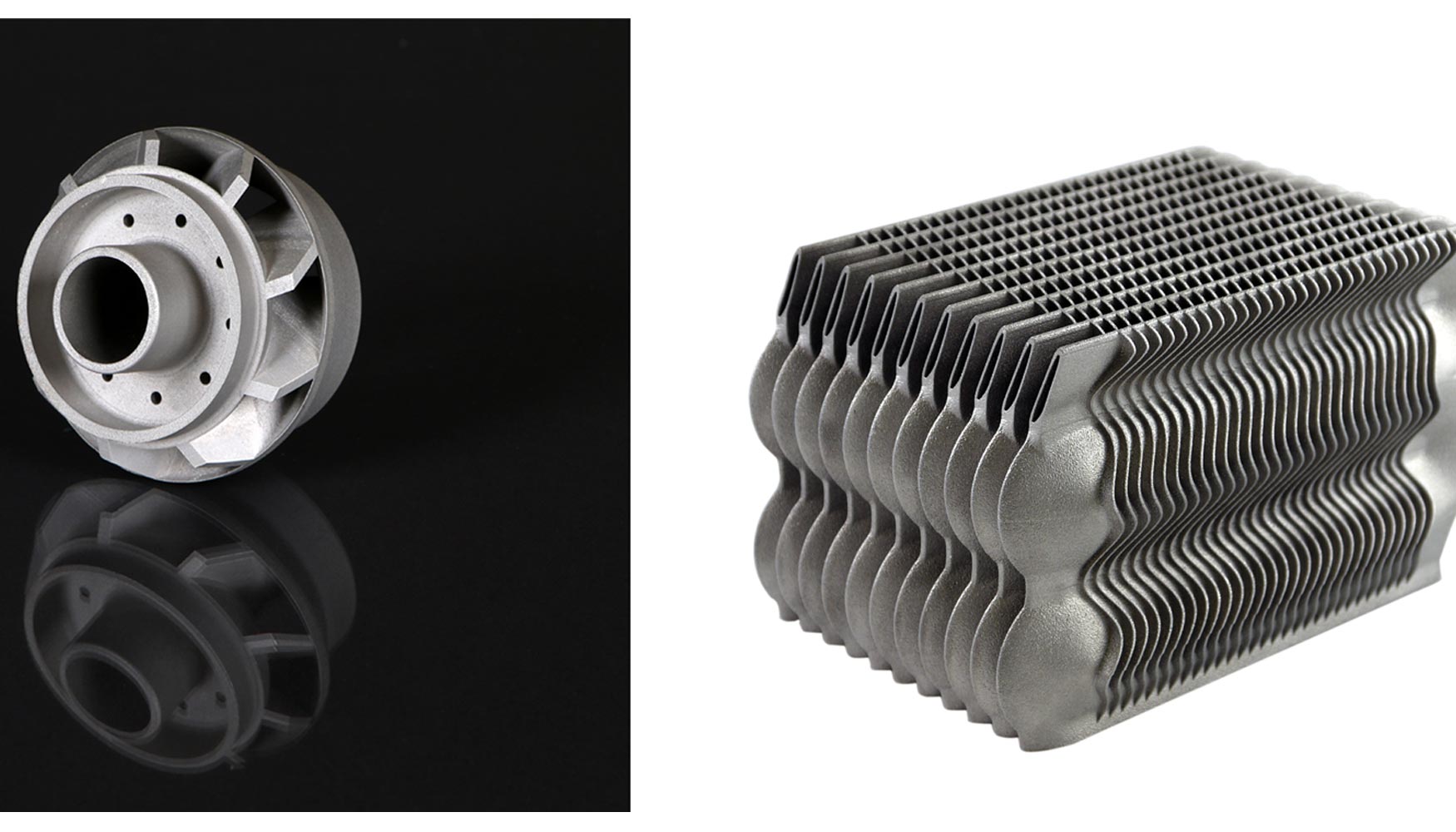
Izq., impeller fabricado en metal (3D Systems). Dcha., intercambiador de calor fabricado por SLS (EOS).
Principales procesos de fabricación aditiva en la industria
Tal y como ya se ha comentado anteriormente, el término fabricación aditiva engloba a un conjunto de procesos que presentan grandes diferencias tanto en capacidades como en aplicaciones. Así, por ejemplo, a la hora de cuantificar la calidad de las piezas, hay procesos que consiguen resoluciones por debajo de las 50 micras, como es el caso de las máquinas PolyJet para piezas de materiales poliméricos o algunos sistemas de fabricación de piezas metálicas mediante lecho de polvo. En el otro extremo, los sistemas de Laser Cladding (también conocidos como Laser Material Deposition) o las impresoras 3D fabrican piezas con precisiones que pueden superar las 100 micras y con calidades superficiales que requieren un pulido o mecanizado posterior. Se puede llegar a conclusiones similares si se habla de precio, versatilidad en materiales, etc. Así, a continuación se mencionan y describen brevemente los principales procesos de fabricación aditiva que se utilizan en la industria.
- Fused Depositon Modelling (FDM): El proceso se basa en un cabezal que se mueve en un plano y funde un filamento de plástico. El material se va aportando capa a capa y se crea una pieza 3D. Es la base de las conocidas impresoras 3D y su principal ventaja es el bajo coste del equipamiento junto con la posibilidad de trabajar en diferentes materiales poliméricos.
- Estereolitografía (SLA) y PolyJet: Se obtienen piezas a partir de resinas líquidas que se curan con un haz de luz. El proceso originario fue la estereolitografía, pero posteriormente se desarrolló el denominado polyjet que se basa en curar la resina con múltiples haces de luz UV. El resultado es una pieza con excelente calidad tanto en precisión dimensional como en acabado superficial. A pesar de que en los últimos años se han desarrollado materiales que imitan a los principales polímeros industriales, la principal desventaja que plantean estos procesos es la necesidad de utilizar materiales especiales.
- Fusión selectiva de lecho de polvo (SLM, SLS, …): Se basan en la fusión selectiva de una capa de polvo que se ha depositado previamente. El proceso se realiza dentro de una cámara precalentada y que puede tener una atmósfera controlada para evitar la oxidación. La pieza resultante se obtiene a partir de la fusión y posterior resolidificación capa a capa, pudiendo obtener piezas en diferentes materiales, incluyendo materiales metálicos, polímeros industriales, etc.
- Inyección directa de material (DLMD, Laser Cladding, …): El proceso consiste en la fusión de un material base y en la inyección de un material (tanto en forma de polvo como de hilo) en el baño fundido. El resultado es el aporte de un material sobre un material base. Este proceso se emplea tanto para fabricación aditiva de detalles o estructuras sobre una pieza previamente fabricada, como para reparar zonas dañadas. La principal ventaja es que se puede aplicar sobre piezas que se han fabricado por forja, fundición, .., y se pueden aportar una gran cantidad de materiales incluyendo diferentes aleaciones metálicas, materiales cerámicos, mezclas de componentes, …
Además de estos, existen otros procesos o variantes de éstos que pueden emplearse en la industria, pero con menor presencia que los citados. Por otro lado, dado que industrialmente, los procesos de fusión selectiva de lecho de polvo y de inyección directa de material están adquiriendo cada vez más relevancia, a continuación se hace una descripción más profunda de estos procesos.
Fabricación aditiva mediante fusión de lecho de polvo
La fabricación aditiva mediante fusión de lecho de polvo, también conocida como Selective Laser Melting o SLM, es uno de los procesos de fabricación aditiva más extendidos, sobre todo para la fabricación de piezas metálicas. El proceso se basa en fabricar piezas 3D mediante la fusión de una capa de polvo que se ha depositado previamente sobre la capa generada en la operación anterior. El material en polvo se funde únicamente en aquellos puntos donde se requiere añadir material, resultando así en un aporte selectivo de material.
Este tipo de procesos se basan en repetir siempre los mismos pasos. En primer lugar se deposita una capa de polvo de espesor constante en una placa base. Posteriormente, una fuente de calor (que puede ser un láser o un haz de electrones) funde el material que se desea aportar. La resolidificación del material fundido crea una capa consolidada de material. Una vez que se ha creado una capa, se deposita una nueva capa de polvo de espesor constante, que se vuelve a fundir sobre la capa aportada anteriormente. Repitiendo el proceso se consigue generar una pieza en 3D capa a capa.
El motivo por el que se emplea un láser o un haz de electrones como fuente de calor es que por un lado, son fuentes de calor capaces de concentrar la energía en un punto muy pequeño, por lo que se pueden fabricar piezas con una resolución muy pequeña. Por otro lado, son fuentes de calor que pueden ser guiadas a alta velocidad, con lo que se consigue incrementar la productividad de estos procesos.
En general, se parte de un archivo CAD que se descompone en capas y se calculan una serie de trayectorias por cada una de las capas. Posteriormente, el material se funde por la acción de un láser guiado por un escáner galvanométrico, el cual sigue las trayectorias generadas. El proceso es similar tanto para piezas de plástico como para piezas metálicas, variando el tipo de láser y las condiciones de proceso según el material. Además, para la fabricación de piezas metálicas es necesario disponer de cámaras de atmósfera controlada para evitar la oxidación de las piezas mientras se están fabricando.
El proceso de SLM se desarrolló en 1995 por el Fraunhofer Institute ILT de Aachen, Alemania. Partiendo de un proyecto de investigación, se generó la patente alemana DE 19649865 junto con a la compañía F&S Stereolithographietechnik GmbH, la cual también participaba en el proyecto. A comienzos de la década del 2000, esta empresa se alió con MCP-HEK GmbH, que posteriormente pasó a llamarse MTT Technology GmbH, y por último se denominó SLM Solutions GmbH, que es en la actualidad una de las marcas referentes en sistemas de SLM. A esta empresa, se le pueden sumar otras empresas como EOS, que es líder del mercado en este tipo de máquinas, Renishaw, Concept Laser, 3D Systems o Arcam, que utiliza un haz de electrones como fuente de calor.
Independientemente del sistema empleado, las bases del proceso son similares. En primer lugar se generan capas de un modelo de CAD que oscilan entre 20 y 100 micras de espesor, dependiendo de la resolución que se quiera obtener y el tamaño de polvo empleado. Lógicamente, a medida que se reduce el espesor por capa, se incrementa la resolución de la pieza pero es necesario fabricar más capas por lo que se reduce la productividad.
Las capas de polvo se distribuyen dentro de una cámara de atmósfera controlada mediante un mecanismo que permite el movimiento de una regla que uniformiza el espesor de polvo y una guía que permite el desplazamiento vertical de la base una vez que se termina cada capa. Mediante la combinación de estos dos elementos se distribuye el polvo capa a capa. Es importante controlar la atmósfera en la que se realiza el aporte de material, siendo lo habitual emplear Argón, mezclas de Argón y Helio o incluso Nitrógeno, con el objeto de reducir al máximo la cantidad de Oxígeno presente.
En cuanto a los materiales, en el caso de plásticos se pueden utilizar polímeros industriales como Nylon, ABS o polímeros reforzados y en el caso de metales se pueden fabricar piezas en aleaciones base Níquel o Titanio así como en acero inoxidable o aceros de herramienta. Incluso existe la posibilidad de fabricar piezas de metales preciosos. El requisito principal es que el material se encuentre en formato polvo con tamaños de polvo por debajo de 50 micras. En muchos casos, los materiales son suministrados por el propio fabricante del sistema de fabricación aditiva.
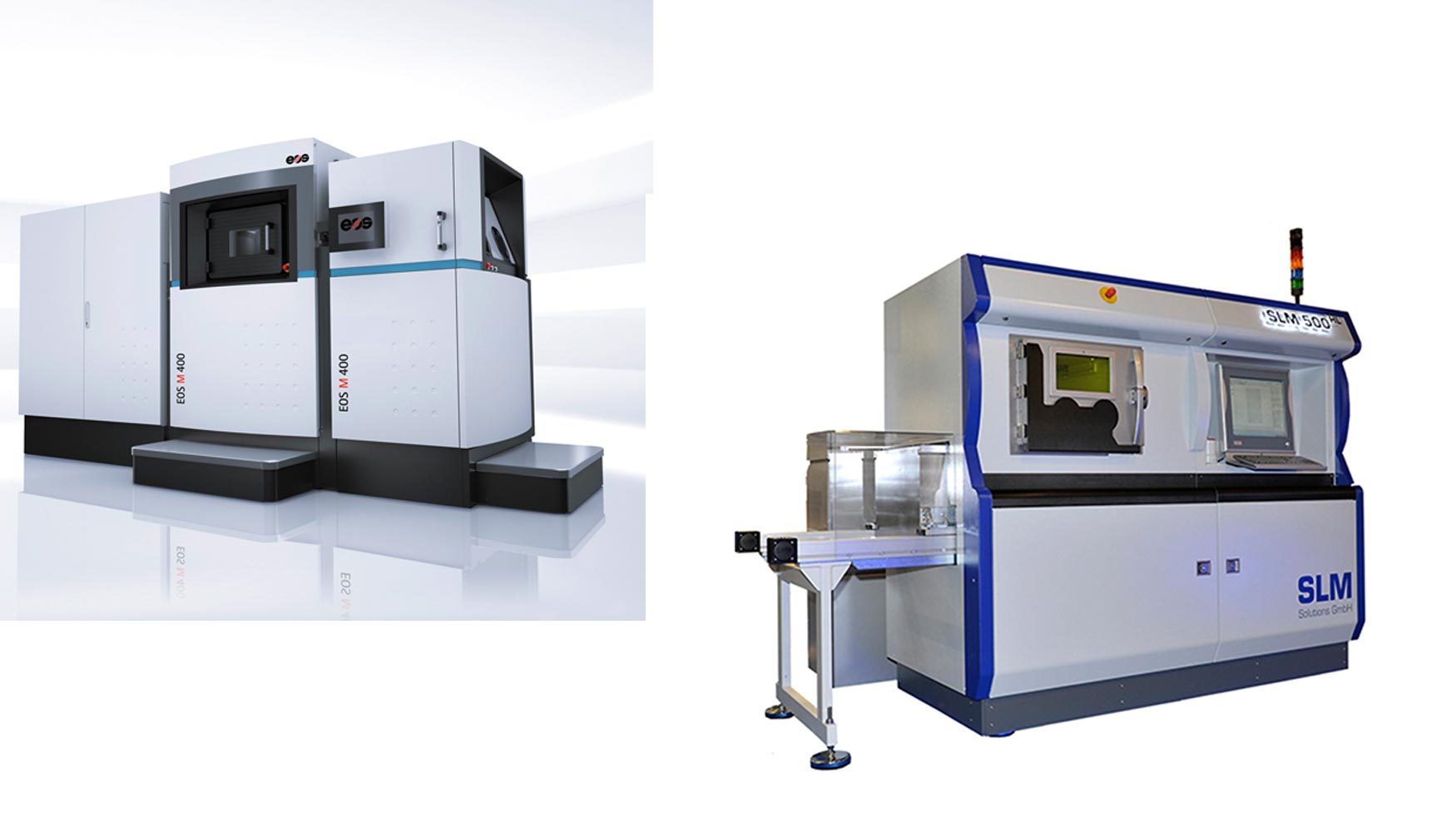
Izq., máquina de fabricación aditiva EOS M400. Dcha., máquina de SLM solutions SLM 500 HL. Ambas preparadas para fabricación de piezas metálicas.
Tal y como se ha comentado anteriormente, a pesar de que hay diferentes soluciones en el mercado, las bases de la tecnología son comunes. La principal ventaja que introducen este tipo de sistemas es la posibilidad de fabricar una pieza desde cero y conseguir geometrías muy complejas (incluyendo cavidades interiores y paredes delgadas) con precisiones y calidades superficiales razonablemente buenas. Por otro lado, la principal desventaja que plantean es la limitación de tamaño de las piezas, ya que tanto la cámara de atmósfera protegida como el sistema de espejos que guía el láser presentan una limitación de tamaño. Así, si se desea fabricar una pieza por fabricación aditiva de gran tamaño, es necesario utilizar otros métodos como el aporte directo de material o DLMD (Direct Laser Material Deposition). Otra desventaja es que a pesar de que el guiado del láser es a alta velocidad, se tardan varias horas (incluso días) en fabricar una pieza. De esta forma, este tipo de procesos pueden ser muy efectivos para producir una pieza única, pero no son competitivos si es necesario fabricar una tirada alta.
Laser cladding
En el proceso de laser cladding o aporte directo de metal, también conocido por sus siglas en inglés, DLMD, a diferencia de lo que ocurre en procesos de lecho de polvo, el material de aporte es introducido directamente en el baño fundido en forma de hilo o material en polvo sobre un material base. Así, la principal diferencia respecto a los procesos de fabricación aditiva de lecho de polvo, es que en este caso, se parte ya de una pieza fabricada por métodos convencionales (fundición, forja, mecanizado, …) y sobre ella se aporta material para generar una estructura o un detalle. También es posible aplicar material en una zona desgastada para su recuperación o directamente generar un recubrimiento de otro material.
El baño fundido es generado por la acción localizada de un láser, el cual, además del material base funde también el material aportado. El movimiento relativo entre la fuente láser y el material base da lugar a la creación de un cordón de material añadido, y solapando dichos cordones, a la obtención de una capa de material aportado. Este proceso de aporte de material puede ser empleado para la reparación de una zona dañada o desgastada, para la generación de recubrimientos con distintas propiedades que el material base, o incluso, para la fabricación directa de piezas de geometría compleja. El laser cladding combina una gran versatilidad de formas con una integridad estructural buena, además, es posible emplear gran variedad de materiales de aporte como aceros, aleaciones de base níquel, aleaciones de titanio e incluso materiales cerámicos. Asimismo, es posible combinar distintos materiales para obtener una capa de aporte con propiedades personalizadas y específicamente adaptadas a una aplicación concreta. Por último, cabe señalar que tanto el cabezal óptico como el sistema de inyección de material pueden ser integrados en una máquina herramienta convencional o un robot.
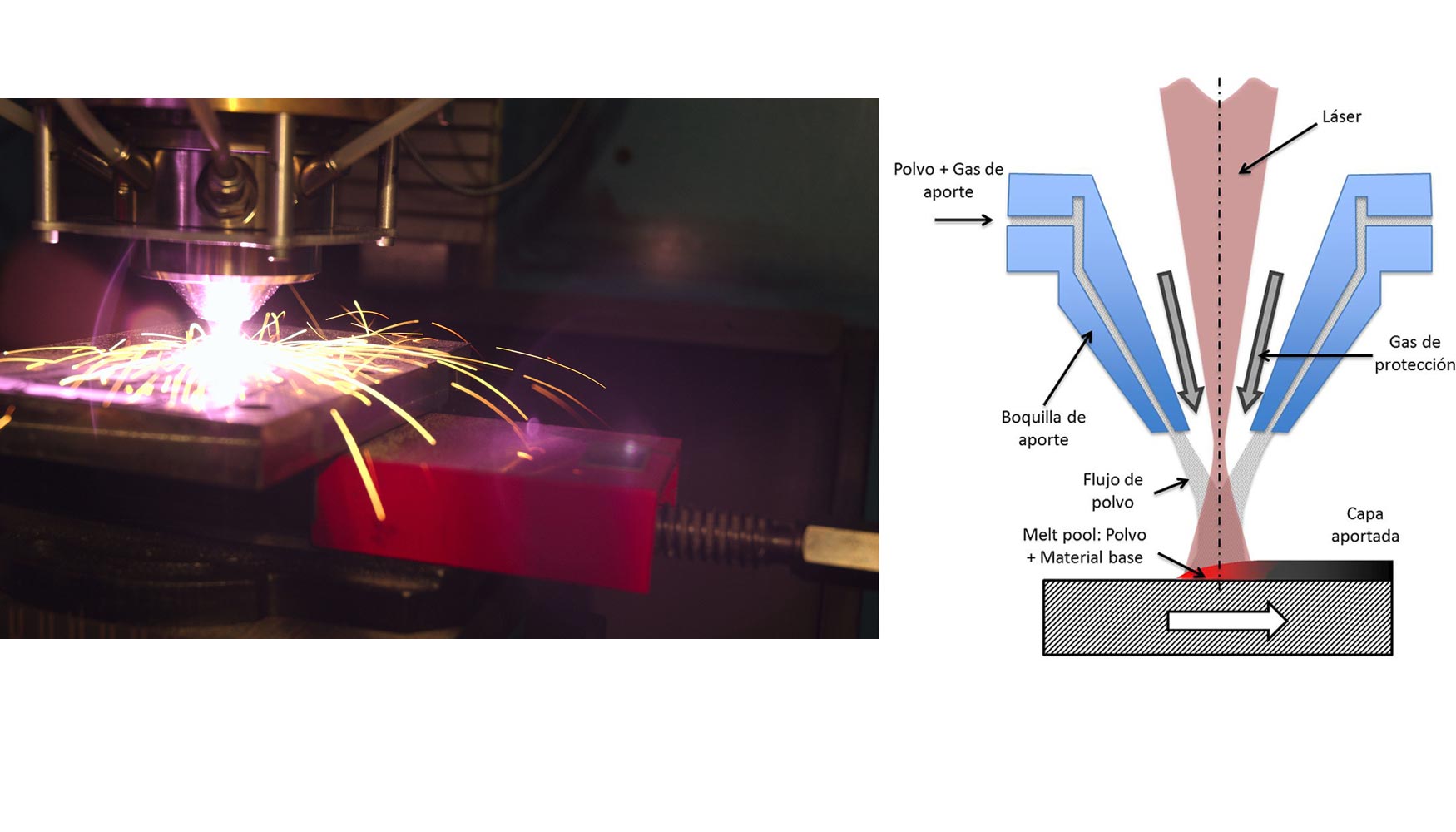
Izq., proceso de laser cladding. Dcha., esquema del proceso.
El proceso de Laser Cladding se puede instalar por tanto en una máquina convencional y poder realizar operaciones de aporte de material de alto valor añadido. En la actualidad, las principales aplicaciones se centran en la reparación de componentes de alto valor añadido y, en particular, en la reparación de puntas de álabe de turbinas aeronáuticas e industriales. También se puede aplicar para el recubrimiento de componentes con otros materiales. En este campo, destaca el empleo de instalaciones de aporte por láser en el recubrimiento de herramientas para la minería o extracción de petróleo. En cuanto a la fabricación directa de componentes, comienzan a comercializarse instalaciones para este propósito. Destaca en este punto la estadounidense Efesto, que oferta un equipo capaz de fabricar piezas de gran tamaño dentro de una cámara de atmósfera protegida.
Al contrario que en el caso de las máquinas de fabricación aditiva mediante lecho de polvo, no hay tantas soluciones comerciales cerradas, sino que hay compañías especializadas que se dedican a integrar todos los equipos necesarios en una célula de aporte láser. También se puede partir de una máquina existente e instalar un láser y un alimentador de polvo en una. En cuanto a la programación de trayectorias y ajuste de parámetros. De nuevo hay una gran carencia de elementos comerciales y muchas veces se dan soluciones “a medida” para cada cliente. En general, la programación se basa en la utilización de programas CAD/CAM comerciales y se adaptan los programas al control de la máquina o robot que guía el cabezal de aporte. En cualquier caso, se han desarrollado algunas soluciones comerciales cerradas que se basan en integrar una fuente láser, un alimentador de material, un cabezal de aporte y una plataforma cinemática. Dependiendo del tipo de cinemática existen dos soluciones diferenciadas, las que emplean un robot y las que emplean un sistema de ejes cartesianos con dos ejes de rotación. En general las que emplean manipuladores robóticos suelen ser más económicas pero con menor precisión que las de cinemática cartesiana. Así existen fabricantes como TRUMPF GmbH que ofrecen ambas soluciones, o fabricantes como HUFFMAN LLC que se centran exclusivamente en el uso de plataformas de cinemática cartesiana. Entre las diversas soluciones comerciales destacan las células de OPTOMEC y RPM innovations & Efesto LLC que son capaces de obtener piezas con muy buena precisión y calidad que minimizan el trabajo necesario de acabado mediante mecanizado.
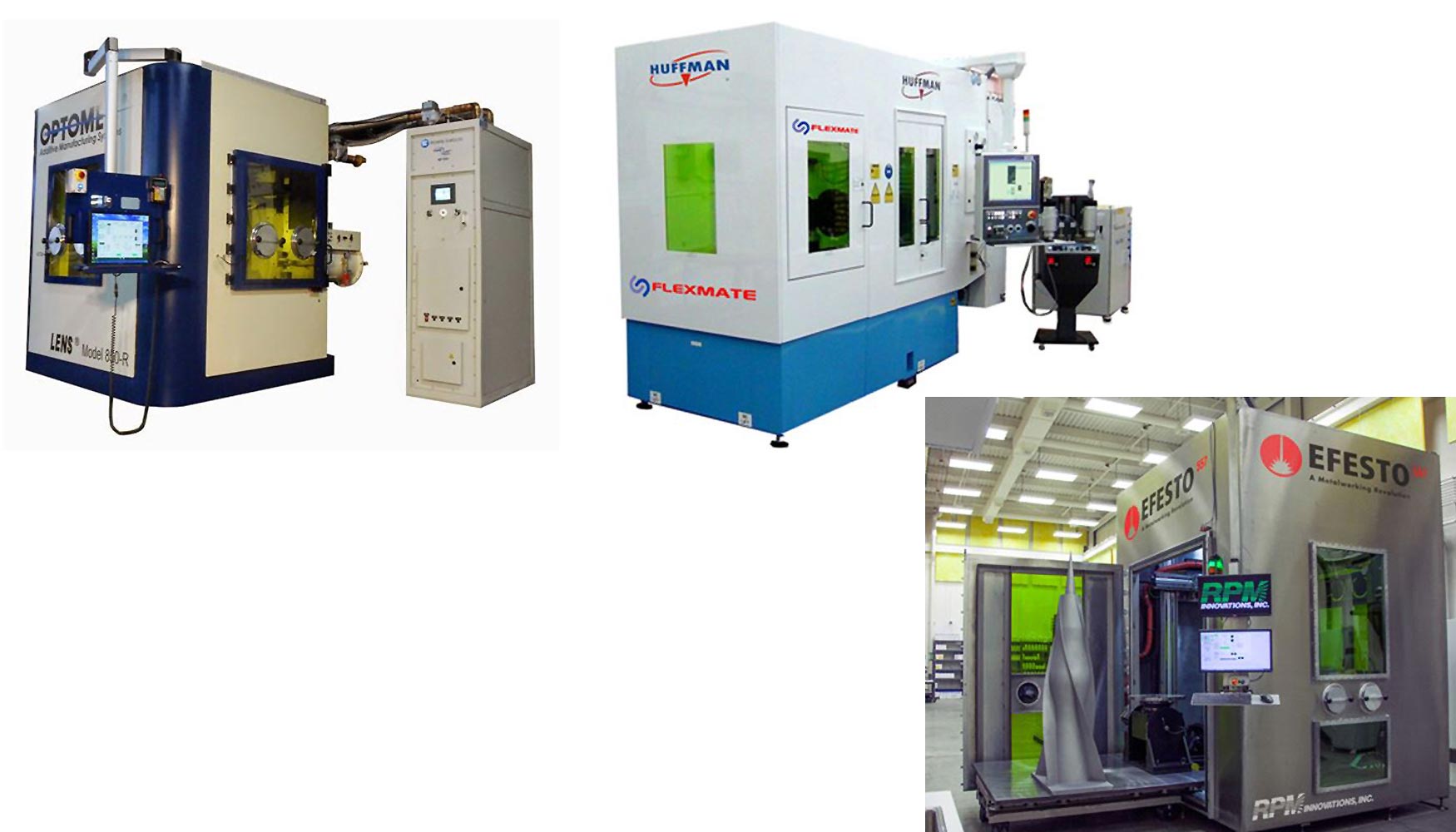
Izq., Optomec 850-R. Centro., Huffman HC-254. Dcha, RPM innovations 557-3.
Por último, a lo largo de los últimos años, se han desarrollado una serie de soluciones comerciales híbridas. La idea básica es que partiendo de un centro de mecanizado convencional, se pueden integrar los elementos necesarios para realizar aportes de material, compartiendo la cinemática de la máquina. El resultado es que se pueden combinar operaciones de mecanizado y aporte de material sobre una misma plataforma, lo que permite partir de una pieza simple y añadir material en zonas que se precise más complejidad geométrica y posteriormente realizar el acabado por completo por mecanizado, manteniendo el mismo origen en todo momento. Dos ejemplos de este tipo de máquinas híbridas son la Laser-Tech 65 3D presentada por DMG-Mori Seiki en la Euromold 2013 y la Integrex i-400AM presentada recientemente por Mazak en la JIMTOF 2014.
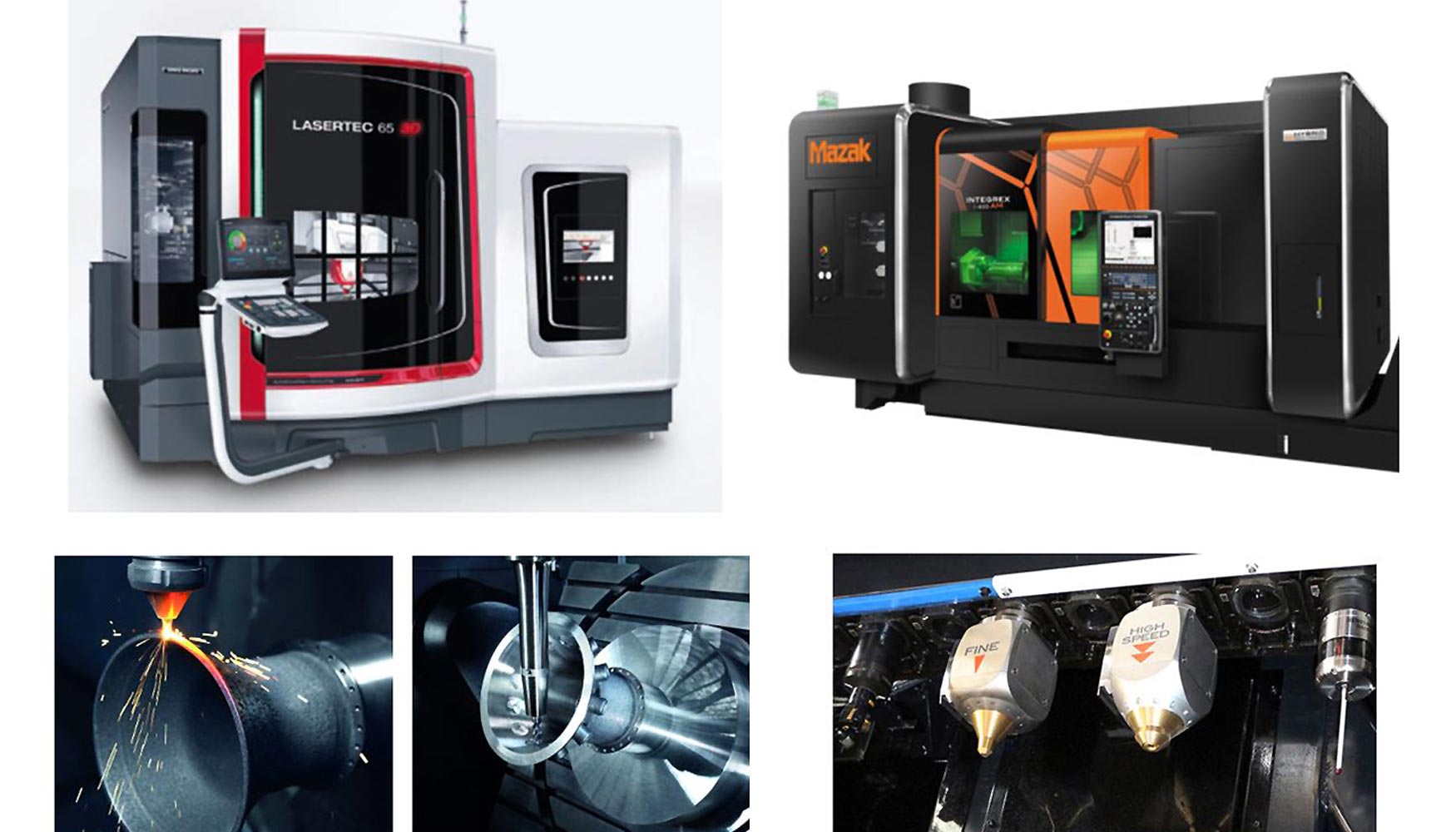
Izq., DMG-Mori Seiki LasertTech 65 3D. Dcha., Mazak Integrex i-400AM.