La fabricación aditiva al alcance de las pequeñas empresas
El mercado de la fabricación aditiva está creciendo al ritmo del 30% cada año en todos los aspectos, desde materiales hasta software, equipos, etc., liderado principalmente por EE UU, China y Japón. La venta de materia prima está también en constante incremento mientras que la maquinaria ha vivido un auge en las ventas, de 2013 respecto a 2012, del 26%, una tendencia que se mantiene a lo largo de este año. Así de optimista presentó Felip Esteve, director de Aserm (Asociación Española de Rapid Manufacturing) la jornada sobre Actualización de las posibilidades que ofrecen las técnicas y tecnologías de fabricación aditiva e impresión 3D a las pymes industriales’ organizada en noviembre en el Parc Tecnològic del Vallès y que contó con la participación de empresas como la Fundación Ascamm, Hewlett-Packard, Roland DG, Hofmann Innovation Ibérica, Comher-Stratasys o Ultrasion.
Los principales mercados clientes de la fabricación aditiva (RM, Rapid Manufacturing) son los fabricantes de piezas metálicas y plásticas, el sector aeronáutico, el médico-dental, la automoción, los fabricantes de bienes de equipo. “En Europa, por ejemplo, la principal demanda es la pieza metálica, por delante de los EE UU, tanto en volumen de fabricación como calidad”, apuntó Esteve, “lo que supone una oportunidad para las empresas industriales de estos países”.
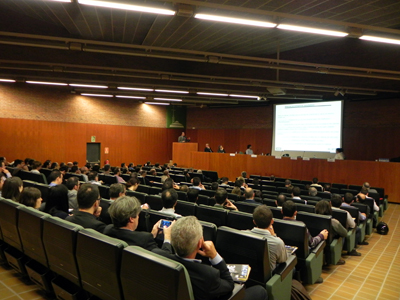
Un nutrido número de empresas usuarias y potenciales de tecnologías 'rapid' acudieron a la jornada organizada por Aserm en el Parc Tecnològic del Vallès (Barcelona).
Asimismo, apuntó que la estimación por parte de Aserm en cuanto a venta de máquinas para este año será de unas 200 unidades, destinadas especialmente para trabajos en automoción, médico-dental, bienes de equipo y bienes de consumo y recordó el auge que está viviendo también la impresión 3D “más doméstica, con unas ventas que rozarán las 1.750 unidades, destinadas a la formación, las pymes, empresas de diseño, pequeños talleres, etc.”. Para Esteve, esta ‘revolución’ supone una gran oportunidad para todas las empresa que sepan ver el potencial del RM y apuesten decididamente por él, “conociendo todas las posibilidades que les ofrece y que jornadas como ésta quiere facilitar”.
Elegir la tecnología más adecuada
Xavier Plantà, de la Fundación Ascamm, hizo un repaso a la larga experiencia que el centro tiene con la fabricación aditiva. “Una tecnología tan moderna que viene ¡del siglo XX!”. El reto es saber dónde está el negocio, qué empresas pueden encontrar en el RM una oportunidad. Según Plantà, “la fabricación aditiva supondrá nuevos En productos personalizados —‘costumizados’— nuevos materiales pero también nuevos software más especializados en RM y, en definitiva, todo aquello que nos podamos imaginar”. “España, hasta ahora ha sido cliente de tecnología —añadió— y es necesario que las empresas sepan desarrollar aquella necesaria para posicionarse en las primeras posiciones como fabricantes”. En este sentido, apuntó que “hay que saber combinar las tecnologías existentes a fin de obtener los mejores productos. Quizá no es necesario realizar toda la producción en mecanizado o todo en RM”.
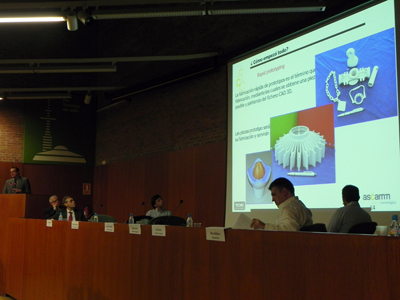
En conclusión, para Plantà, hoy en día existen diferentes técnicas manufactureras pero “ninguna puede hacerlo todo con todo tipo de material. Ello supone una oportunidad en investigación muy importante”. Asimismo, apuntó que existe todavía desconocimiento por parte de las empresas en cuanto al diseño des de otro punto de vista: la fabricación 3D. “Las empresas deben aprender a utilizar esta tecnología para sacarle el máximo provecho”.
El plan diabólico de HP: conquistar el mercado
HP presentó, de la mano de Ed Davis, 3D Business Chief Technologist, y Aleix Oriol, director del Programa de Soluciones Media de la firma, su apuesta más innovadora: la tecnología Multi Jet Fusion, cuyo centro tecnológico se ubica en la sede que la firma tiene en Sant Cugat del Vallès (Barcelona). Se trata de una impresora 3D diseñada para ser hasta diez veces más rápida y precisa que otros modelos de características similares con la que pretende lograr su “plan diabólico: dominar el mercado de la fabricación aditiva”. El objetivo de HP con la tecnología Multi Jet Fusion se basa en reducir el tiempo de impresión, incrementar la resolución de las piezas obtenidas y bajar el coste general de producción. El sistema de esta impresora 3D se basa en la combinación de polvo como componente principal y varios agentes que asisten en la fusión y la definición final de cada pieza impresa. Una tecnología que se define por su propio nombre: Multi, múltiples materiales líquidos; Jet, que son empujados; Fusion, a un ‘fusionador’ de material.
Multi Jet Fusion quiere además aportar un plus en cuanto a diseño. “No basta con que la pieza terminada sea de calidad. Queremos que, además, tenga un buen aspecto, que sea bonita. Y siempre bajo el concepto de plataforma abierta”. Multi Jet Fusion es además la “puerta de entrada de HP al mercado de las máquinas profesionales en empresas fabricantes y subcontratistas, no para uso propio”, apuntó Davis.
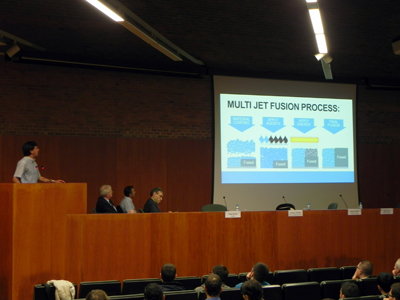
Aleix Oriol, director del Programa de Soluciones Media de HP, presentó la parte técnica de la última innovación de la firma: la tecnología Multi Jet Fusion, una impresora 3D basada en la combinación de polvo como componente principal y varios agentes que asisten en la fusión y la definición final de cada pieza impresa.
Por otra parte, el campo de investigación de HP está centrado en la introducción de colores en piezas funcionales “pero no sólo color, también textura, propiedades como la conductividad eléctrica, rugosidad, transparencia, etc.”. En definitiva, el objetivo es desarrollar una plataforma tecnológica con la que obtener materiales avanzados para lo que abren la puerta a colaborar con empresas que estén trabajando en cómo manipular las propiedades punto a punto de los materiales para, en el futuro, poder producir “piezas totalmente distintas a lo que hoy nos podamos imaginar”.
Aleix Oriol expuso la parte más técnica de la solución. “Multi Jet Fusion se basa en la fusión de un termoplástico” —al menos en sus inicios, si bien tienen previsto introducir más materiales para mayores usos, como cerámica o metal— “mediante dos procesos síncronos que tienen lugar dentro de la impresora por lo que en un único movimiento se va creando una capa sobre otra. El detalle es que la fusión es capa a capa y no punto a punto”.
Soluciones de ‘sobremesa’
Pau Núñez, de Roland DG, presentó la nueva aventura de la compañía en la impresión 3D, basada en esterolitografía. Se trata de la máquina ARM-10, semiprofesional, “de sobremensa”, que utiliza una resina fotopolimérica como material. “La diferencia con otras tecnologías es que no utiliza un punto de luz láser sino la de un proyector, de abajo a arriba, proyectando la imagen capa a capa, por lo que el producto impreso se desarrolla en posición invertida”. La ARM-10 está pensada para formación, profesionales de diseño industrial, de joyas, sector médico-dental, etc.
Fabricación de piezas funcionales
Hofmann Innovation —empresa pionera en Laser Cusing— mostró, de la mano de José Antonio Jaldo, director comercial en España, sus soluciones especialmente aplicadas en sectores como el médico y el aeronáutico. Hofmann cuenta con una línea de fabricación capaz de desarrollar piezas reales y funcionales. “Con la fabricación mediante Laser Cusing se obtienen composites en poco tiempo, prototipos de la noche a la mañana y componentes iguales que el original, con las mismas características materiales. Además, permite realizar el test en el túnel de viento inmediatamente, sin tiempos de espera, lo que repercute en una reducción de costes”. Por otra parte, concretamente en el sector médico, Jaldo expuso la fuerza con que ha entrado la fabricación aditiva, “gracias a la posibilidad de trabajar en diferentes materiales como el cromo cobalto utilizado en piezas dentales”.
Por otra parte, el responsable de Hofmann en España recordó que “con el Rapid Manufacturing es posible aligerar el peso de las piezas unitarias, un factor crítico en sectores como el aeronáutico si lo multiplicamos por todas las piezas que conforman una aeronave. Es un factor diferencial competitivo a la vez que permite a las compañías cumplir con los requisitos de reducción en el consumo de combustible”. En conclusión, para Jaldo, “se trata de una tecnología ‘joven’ con un gran potencial de futuro no sólo para prototipado sino enfocada directamente a sistemas de producción como ya lo está siendo en aeronáutica, dental y la Fórmula 1”.
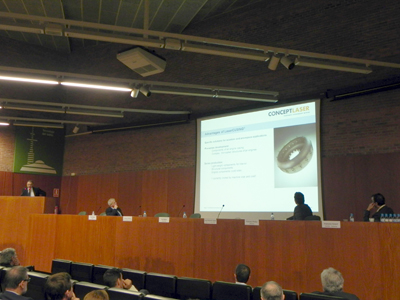
Una fabricación aditiva según necesidades
Por su parte, Francesc Astort, de Comher-Stratasys, expuso en un cuadro clarificador las diferencias entre lo que podríamos llamar ‘impresión 3D’ y la propiamente ‘producción 3D’. Para Astort, existen diferentes tecnologías que dan respuesta a muy variadas necesidades en la industria. Así, mientras la impresión 3D estaría más enfocada al prototipado, la producción 3D permitiría, además, desarrollar producto final. La diferencia continúa también con los materiales utilizados: más limitados en la impresión 3D, mucho más amplios en sistemas de producción. Del mismo modo, la capacidad de trabajo de las máquinas también difiere —una media de 25 x 25 cm en el primer caso frente a piezas de gran tamaño en el segundo—. Igualmente, mientras la impresión 3D está pensada para usuarios cuasi domésticos, en un entorno oficina, la producción industrial requiere de un operador cualificado y se engloba en un laboratorio o centro de producción.
Innovación non-stop
Cerró la jornada Francesc Rivillas, director de operaciones de Ultrasion, una ‘spinn-off’ de Ascamm especializada en soluciones basadas en ultrasonidos y cuyo objetivo es ofrecer “soluciones hasta ahora imposibles a las empresas”. Las aplicaciones más típicas de los ultrasonidos han sido desde la limpieza hasta la soldadura, usos en medicina, corte, etc. En Ultrasion sin embargo se propusieron dar un paso más y “desarrollar una solución para fabricación basada en la adhesión de capas mediante ultrasonidos”.
Hasta la fecha, en Ultrasion están trabajando en diferentes tecnologías como:
- Ultrasion Moulding, basada en la inyección de plástico y que permite una reducción de costes
- Ultrasion Light Alloys, para la desgasificación de material no férrico
- Ultrasion Deposition Modelling, fabricación aditiva donde se funde material plástico
- Nano additivation, basada en nanopartículas en matriz de plástico
- Ultrasonic Micropultrusion, extrusión mediante ultrasonidos para composites
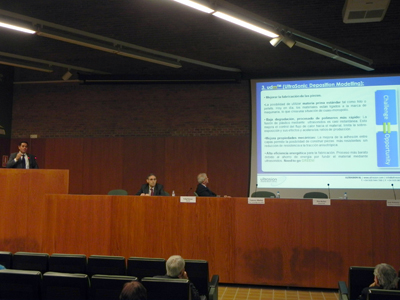
Tejiendo un nuevo polo tecnológico
Conscientes del cambio que la fabricación aditiva supondrá para las compañías, especialmente en las micro, pequeñas y medianas, desde la asociación Aserm y el centro tecnológico Leitat se han propuesto construir un nuevo polo tecnológico donde agrupar a todas aquellas empresas que trabajen para y con esta tecnología.
Así, desde ambas entidades emplazaron, al cierre te la jornada, a todas aquellas firmas presenten en el evento a incluirse en un nuevo ‘mapa’ que están elaborando dentro del proyecto europeo Vanguard en el que participan, hasta el momento, Aserm, Acció, Ascamm, la Fundació CIM y el propio Leitat.