Entrevista a Detlef Zühlke, presidente del consejo de administración de SmartFactoryKL
Conexión en red, organización independiente y flexibilidad forman parte del concepto de Fábrica del Futuro. Y SmartFactoryKL no es ninguna visión sino que ya es una realidad. Los investigadores de la iniciativa tecnológica en la localidad de Kaiserslautern (Alemania) han diseñado una instalación de investigación y demostración para la fábrica del futuro. El catedrático Detlef Zühlke, presidente del consejo de administración de SmartFactoryKL, habla sobre la integración de aparatos y aplicaciones de la electrónica de consumo al mundo de la fábrica.
Señor Zühlke, ¿cuáles son las diferencias más marcadas entre la fábrica actual y la fábrica del futuro?
La fábrica actual se caracteriza por unas estructuras de control de tipo jerárquico con unas propiedades muy horizontales. Los sensores y actuadores del nivel de campo se conectan mediante líneas de señales o sistemas de bus de campo al PLC (control de memoria programable) o controles CN. Estos a su vez están acoplados unos con otros a través de sistemas de bus de campo. La ingeniería de sistemas de este tipo está muy orientada en las señales y depende mucho del hardware. En el futuro, ‘Industria 4.0’ conectará todos los elementos para formar unos nodos de red inteligentes que se interconectan sin ninguna jerarquía a través de una red estandarizada. Esto significa que cada sensor y cada actuador, así como cada PLC puede comunicar con los demás participantes en la red, tanto en sentido horizontal como en sentido vertical.
¿Qué consecuencias se darán para el mecanizado con arranque de viruta?
Si utilizamos los correspondientes estándares como TCP/IP, OPC Unified Architecture o servicios por web, conseguimos crear una independencia del hardware dentro del proceso de ingeniería y permitir al mismo tiempo configuraciones dinámicas de instalaciones según el conocido principio ‘Plug and Play’. Esta nueva arquitectura no solo puede utilizarse de forma sumamente eficaz a nivel de instalaciones, sino que además podría incorporarse también a las máquinas herramienta. Sin duda, en un principio, el circuito de accionamiento interior funcionará primero de forma cerrada, por ejemplo, con Sercos (Serial Realtime Communication System), la interfaz digital estandarizada a nivel mundial para la comunicación entre controles y participantes de bus de campo.
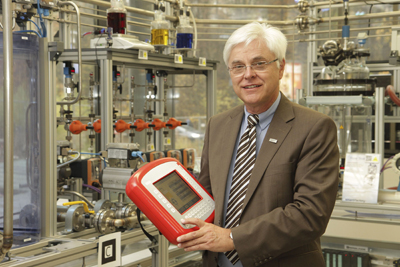
¿Cuál es el papel de la simulación y virtualización, o bien, la separación del mundo físico del mundo de datos para la fábrica del futuro?
Este papel va a tener mucho peso. El nuevo mundo solo podrá aportar los incrementos esperados de la eficacia si al a vez simplificamos mucho la ingeniería. La forma más razonable de conseguirlo, es un acoplamiento estrecho y bidireccional de la gestión del ciclo de vida del producto (PLM) y del mundo del control.
¿Cómo pueden los modernos medios de comunicación como teléfonos inteligentes, tabletas o Google Glass, etc. ayudar en este desarrollo?
Estas inteligentes tecnologías de la vida diaria gozan en la actualidad de una importancia considerable. Nos permiten un acceso fiable, económico y sobre todo móvil a los datos de la instalación. El operario de la máquina puede seleccionar su tecnología de interacción siempre, de tal modo que esta le ayude de forma ideal. Esto puede verse especialmente claro en el área de mantenimiento. Hoy en día somos capaces de identificar con un coste mínimo mediante una cámara integrada las máquinas o sus componentes, consultar los datos de servicio y mantenimiento y descargar la documentación actual. Todo ello permitirá un empujón claro en lo que a la eficacia se refiere.