Tecnologías avanzadas de fabricación para el sector dental
Hoy en día, como resultado de la tendencia hacia lo nano, surgen las llamadas microtecnologías, que no consisten únicamente en un cambio de escala, sino que requieren de un desarrollo teórico completamente nuevo, en parte debido a las estrechas tolerancias y precisiones que exige el trabajar con geometrías micro. Desde Fundación Prodintec, centro tecnológico especializado en el diseño y la fabricación industriales, se ha apostado de forma clara el desarrollo de estas tecnologías, concretamente de dos de ellas que son a su vez complementarias: el micromecanizado y la microinyección.
Desafíos del micromecanizado
El mecanizado tradicional es el proceso de fabricación por arranque de viruta por excelencia. A grandes rasgos, consiste en sustraer material de un bruto o preforma de materia prima mediante la acción de una herramienta giratoria hasta obtener la forma final deseada.
El objetivo del micromecanizado es escalar el proceso de arranque de viruta tradicional para fabricar microcomponentes o componentes microestructurales, y llevar así todas las posibilidades (y también las dificultades) del mecanizado a un nuevo nivel.
Esto requiere de un nuevo desarrollo teórico para adaptarse a los parámetros del proceso que pasan a cobrar mayor importancia al trabajar en esta escala, como por ejemplo el pequeño tamaño de las herramientas empleadas, que hace necesario que el giro de las mismas se efectúe a muy elevadas revoluciones para poder garantizar su integridad y evitar que resulten dañadas al simple contacto con el material en bruto.
Casos de éxito de micromecanizado en el sector dental
Aunque los sectores de aplicación del micromecanizado son muy variados, la experiencia acumulada por Prodintec en estos años indica que son los sectores médico y analítico los que ofrecen mayores posibilidades. Concretamente, en el sector dental se encuentran multitud de aplicaciones, tanto para la fabricación de implantes como de dispositivos correctores, si bien la última palabra la tienen los potenciales clientes de esta tecnología, en cuyas manos está el rediseñar sus productos o proponer nuevas vías hacia la miniaturización de componentes.
Un ejemplo de este hecho lo encontramos en un proyecto acometido por Prodintec para un cliente europeo, que tenía la necesidad de fabricar una serie de brackets prototipo para corrección dental de tipo sublingual y autoligante en acero inoxidable 316L. Dicho bracket constaba de dos piezas diferenciadas: la base y el cierre, que se acoplaban una sobre otra, tal y como puede apreciarse en la vista 3D del diseño CAD.
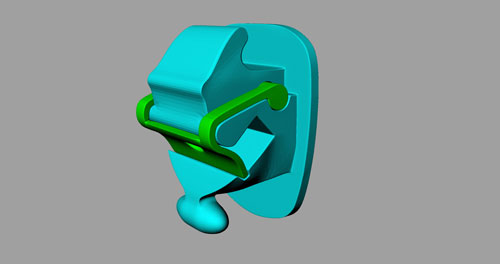
Por otro lado, este bracket presentaba una serie de peculiaridades geométricas que dificultaban su mecanizado. La más relevante es la microtexturización que se encuentra en la cara inferior de la base del sistema (en contacto con el diente), que favorece la adhesión a su superficie.
Este detalle tiene una influencia total sobre el proceso de micromecanizado, puesto que al tener que trabajar sobre las dos caras de la pieza es necesario realizarlo en dos pasos (mecanizado en dos amarres). Primero se mecaniza la forma de la cara anterior, donde acoplará la pieza de cierre y se corta el bruto de material sobrante para proceder a su volteo y al mecanizado de la cara posterior. El volteo es un paso crítico puesto que es fundamental asegurar la precisión en el posicionamiento de la pieza, ya que de lo contrario podrían no coincidir las geometrías de las caras anterior y posterior, lo que invalidaría la pieza por completo. Para solventar este problema, se optó por fabricar una mordaza con un negativo de la cara anterior del bracket mecanizado en su superficie, de tal forma que no hay posibilidad de error al posicionar las piezas tras el primer amarre, y dejando expuesta la cara posterior para proceder al siguiente mecanizado, que incluye la microtextura de adhesión.
Los tiempos totales de mecanizado son de aproximadamente 10’ para la base y 50’ para el cierre. Las herramientas utilizadas fueron fresas de 0,1, 0,3 y 0,4 mm de diámetro. Se utilizó además una fresa de 0,05 mm de diámetro para la microtexturización de la cara posterior del bracket.
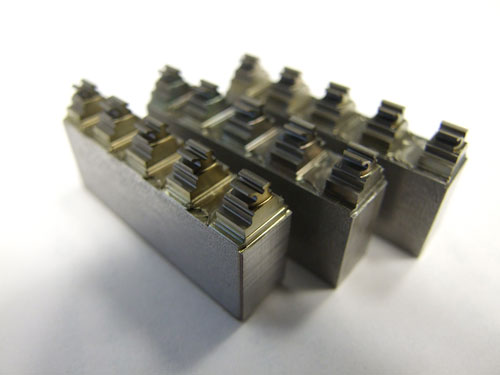
El conocimiento en profundidad del proceso de micromecanizado de los técnicos de Prodintec y la elección de las estrategias de mecanizado más adecuadas hicieron posible fabricar con éxito las piezas, que sirvieron al cliente para avanzar en su proyecto propio de desarrollo de un nuevo sistema de corrección dental y corregir ciertas carencias detectadas durante la operación de montaje sobre una réplica de dentadura humana.
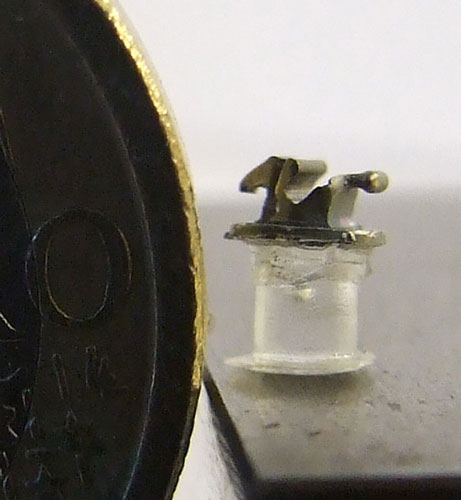
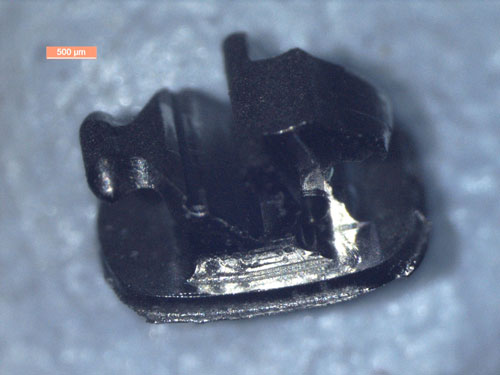
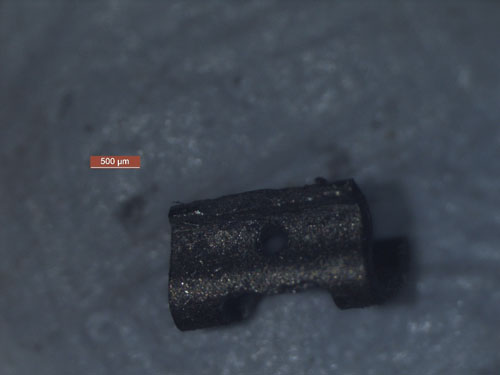
Fabricación de piezas micro a gran escala
La otra gran apuesta de Prodintec en el ámbito de las microtecnologías es la microinyección. Este proceso productivo está claramente orientado a la fabricación de grandes lotes de piezas, de forma muy estable y repetitiva, y con el mínimo coste unitario, ya que es posible conseguir ratios de producción muy altos.
El proceso tradicional de inyección comienza con la fusión de la materia prima (normalmente un polímero termoplástico), que luego se introduce a presión en la cavidad de un molde para adquirir la geometría deseada. Este molde es la parte más importante de todo el proceso, y su diseño y funcionalidad resultan críticas, puesto que influye no sólo en la calidad del producto final, sino también en la del todo proceso (tiempos de enfriamiento, flujo del material a través de sus cavidades…).
La microinyección no consiste sólo en un cambio de escala con respecto al proceso tradicional de inyección. Prodintec cuenta con equipamiento diseñado específicamente para microinyección, con prestaciones que lo distinguen de los equipos de inyección convencionales, como por ejemplo el contar con un proceso de inyección dividido en tres pasos: plastificación, dosificación e inyección. De esta forma, el material que se va a inyectar a continuación no ‘espera’ en la zona de plastificación, continuamente sometido al efecto térmico y a esfuerzos de cizalla, que pueden acabar degradándolo, si no que es introducido con una precisión del orden del milímetro cúbico en una precámara (llamada de dosificación), que asegura su homogeneidad y la ausencia de zonas degradadas. A continuación, un pistón de inyección de alta velocidad lo conduce hacia la cavidad del molde a elevada velocidad, de forma tal que no existe tiempo de residencia que pueda llegar a deteriorarlo.
Las garantías que ofrece la microinyección a la hora de evitar zonas deterioradas en las piezas hacen que esta tecnología tenga buena acogida en el sector médico, implantología y farmacéutico de cara a la producción de piezas desechables, de las que es necesario fabricar muchas unidades a un coste muy contenido, como elementos de empaquetado (envoltorios, recipientes en miniatura…), elementos clínicos auxiliares (cánulas, pinzas, soportes variados…) o dispositivos de análisis (chips de detección).
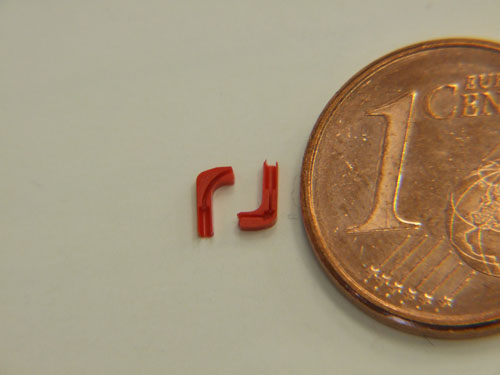
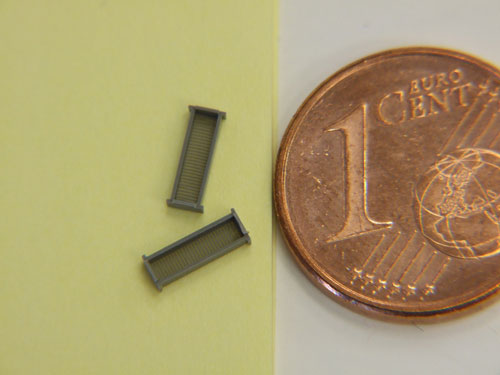
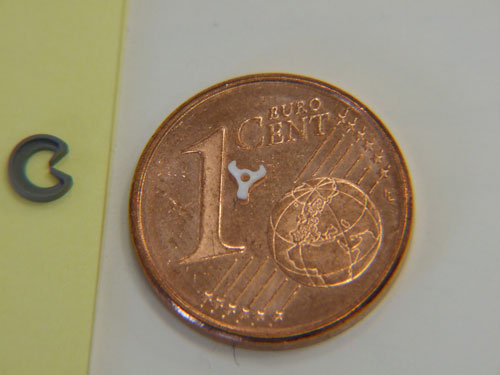
Figuras 6, 7 y 8: Ejemplos de piezas microinyectadas para aplicaciones médicas.
Las posibilidades que ofrece la microinyección al sector dental son enormes, comenzando por el amplio rango de materiales que es posible procesar, desde plásticos comunes hasta plásticos técnicos con características concretas como resistencia a altas temperaturas, desgaste o corrosión. Se trata además de un proceso perfectamente adaptable al entorno de sala limpia, con la ventaja añadida de que es posible minimizar o incluso eliminar la interacción del operario con las piezas desde la fabricación hasta su emblistado. Gracias a la combinación de las tecnologías de micromecanizado y microinyección, es posible conseguir precisiones y tolerancias muy ajustadas, como por ejemplo geometrías en forma de canales de hasta 0,050 mm.
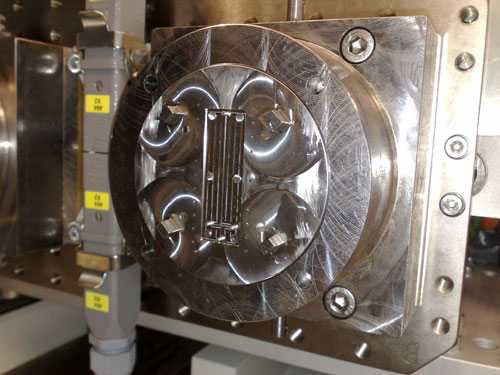
El futuro: microinyección de materiales metálicos y cerámicos
Por otro lado, y siempre dentro del contexto de la microinyección, Prodintec es pionero en la industrialización de la tecnología PIM (Powder Injection Moulding, Moldeo por Inyección de Polvo), que a su vez engloba MIM (Metal Injection Moulding, Moldeo por Inyección de Metal) y CIM (Ceramic Injection Moulding, Moldeo por Inyección de Cerámica).
Esta tecnología permite fabricar grandes series de micropiezas en material metálico o cerámico de forma muy estable y repetitiva. El proceso es similar al de la microinyección de termoplásticos, pero utilizando como materia prima un conglomerado de material base (metálico o cerámico), matriz polimérica y agentes aglomerantes de bajo punto de fusión (ceras, parafinas…). Las piezas inyectadas en este material, denominadas piezas en verde, se someten a un posproceso térmico o catalítico para eliminar todos los elementos de soporte y obtener así micropiezas 100% metálicas o cerámicas.
Ya es posible microinyectar con éxito materiales como aceros de diferentes tipos, cobre, titanio, aleaciones de níquel, alúmina o zirconia, y actualmente se sigue investigando para ampliar este rango de materiales.
Un ejemplo muy claro de aplicación de esta tecnología lo encontramos en el caso presentado anteriormente de los bracket, piezas de complejidad geométrica media que requieren de un laborioso proceso de mecanizado y puesta a punto del mismo. El micromecanizado resultó ser la mejor opción para fabricar una serie corta de validación, pero a la hora de fabricar en serie para comercializarlos, es necesario optar por una tecnología adaptada a la producción de grandes lotes que garantice precisión y repetitividad, para evitar desviaciones de una unidad a otra por desajustes del proceso. Por todo ello, la tecnología MIM sería la mejor opción, ya que para grandes tiradas de piezas permitiría reducir el coste unitario (frente a la alternativa del mecanizado), además de conseguir mejorar la precisión y la calidad del acabado.
En resumen, las tecnologías CIM y MIM abren las puertas a un sinfín de posibilidades y nuevos mercados, como por ejemplo el de los implantes y accesorios dentales. Las virtudes de la microinyección anteriormente mencionadas, unidas a las propiedades intrínsecas de los materiales metálicos o cerámicos hacen que estas tecnologías, aún en fase de maduración, tengan mucho camino por recorrer antes de introducirse de lleno en el mercado. Con unas tasas de producción tan elevadas, una repetibilidad y robustez incomparable y la posibilidad de trabajar con unas precisiones, tolerancias y acabados superficiales óptimos en la escala de la micra, los procesos convencionales de fabricación para todos estos elementos son incapaces de ofrecer soluciones con igual valor añadido.