Componentes estructurales livianos para máquinas-herramienta eficientes y de elevada productividad
La reducción al mínimo de la masa de la máquina permite reducir el consumo de recursos materiales en la fase de construcción, y el consumo de recursos energéticos en la fase de uso. Las tecnologías que intervienen en esta metodología abarcan desde la concepción de nuevas arquitecturas de máquina hasta el desarrollo de nuevos conceptos estructurales combinados con materiales innovadores, pasando por la integración de elementos de control activo de vibraciones y accionamientos de baja inercia.
1. Introducción
La ecoeficiencia de las operaciones de mecanizado se puede medir en términos de relación entre su productividad, medida en volumen de viruta evacuado (Material Removal Rate-MRR en inglés), y su coste, tanto económico como medioambiental [1]. En lo referente a la primera parte de esta relación, la productividad de las operaciones de mecanizado suele estar limitada en la gran mayoría de los casos por la aparición de vibraciones autoinducidas, en especial para el caso de vibraciones por chatter regenerativo [2,3]. La aparición de este tipo de chatter viene definido por los siguientes parámetros: el material de la pieza, el tipo de herramienta, los parámetros de la operación de mecanizado y los parámetros modales del sistema máquina-pieza [4]. Estos parámetros están todos ellos relacionados con la operación de mecanizado excepto los parámetros modales de la máquina, que para una posición concreta, sólo pueden ser modificados si se rediseña o modifica la máquina. Por todo ello, las máquinas-herramienta suelen estar sobredimensionadas, intentando asegurarse que durante la fase operativa la máquina no se verá afectada por la aparición de estas vibraciones. El problema reside en que este sobredimensionamiento va en contra del segundo factor de la ecoeficiencia, los costes económicos y medioambientales, ya que una máquina sobredimensionada afecta tanto a los costes de fabricación como a los de operación, a los que hay que añadir el coste medioambiental asociado al consumo de recursos energéticos y materiales [5].
Por todo ello, el presente trabajo presenta una metodología para diseñar fresadoras que alcancen un objetivo predeterminado de productividad y que a la vez minimicen los costes económicos y medioambientales que están asociados a su ciclo de vida, integrando de esta manera los conceptos de productividad y ecoeficiencia.
2. Metodología para el diseño de máquinas-herramienta productivas y ecoeficientes
2.1. Requisito de rigidez dinámica para asegurar mecanizados estables
En [6] se presenta la resolución de un problema de valores propios de orden ‘n’ asociado al problema de estabilidad de las operaciones de mecanizado. En dicha resolución, se obtiene una ecuación que proporciona la relación entre la frecuencia de chatter, la profundidad de corte y la velocidad de corte, a partir de lo cual se pueden determinar los diagramas de lóbulos de estabilidad y los diagramas de frecuencia de chatter:
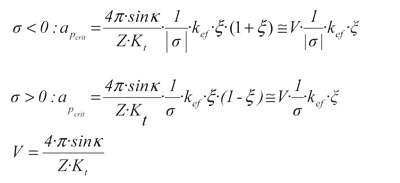
- * apcrit: Profundidad crítica de pasada
- * κ: Ángulo de inserción de la herramienta
- * Z: Número de dientes de la herramienta
- * Kt: coeficiente de corte tangencial del material que va a ser mecanizado
- * σ: Factor direccional
- * kef: Rigidez efectiva en punta hta., kef =Ɯ2/{Φ}2; Ɯ=√(K/M), Φ= vector modal
- * ξ: coeficiente de amortiguamiento
La ecuación (1) indica que si se quiere obtener un determinado objetivo de profundidad de pasada –y por ende un determinado objetivo de productividad- para un caso concreto de herramienta y material de pieza, el producto entre la rigidez efectiva kef y el coeficiente de amortiguamiento ξ del modo asociado al chatter deberá superar un determinado valor umbral, a partir del cual el mecanizado será estable.
De esta manera, si se considera la máquina como un sistema de un grado de libertad con una rigidez efectiva asociada kef, un coeficiente de amortiguamiento asociado ξ y un factor direccional asociado σ variable con respecto a la dirección de mecanizado α dentro del plano de trabajo,σ = σ(α), definiendo una nueva variable σmax como el valor máximo en valor absoluto del factor direccional, σmax≥| σ(α) | ∀α, el objetivo de productividad se traduce a un objetivo de rigidez dinámica que sigue la expresión que se muestra en la ecuación (2).

De esta manera, un objetivo de productividad para una operación concreta de mecanizado y cuantificada en forma de un objetivo de una profundidad mínima de corte apcrit, exige que el factor kef ξ del modo limitante de la máquina frente a chatter supere un valor umbral que depende tanto de la operación de mecanizado considerada (factor V) como de la orientación del modo y la dirección de mecanizado (factor σmax).
Criterios de diseño para alcanzar objetivo de rigidez dinámica con mínima masa
A partir de la Ecuación (2), se deduce que un objetivo de productividad determinado puede ser conseguido con un mínimo de masa en la máquina por medio de dos enfoques complementarios entre sí:
- Reduciendo el valor del coeficiente σmax mediante una variación de la orientación del modo, de manera que se pueda reducir la rigidez efectiva del modo kef en la misma proporción a la vez que se mantiene el valor objetivo de apcrit. Lo habitual es que en un diseño de máquina haya poco margen para modificaciones de diseño de calado, pero es posible conseguir variaciones reseñables en el coeficiente σmax con estrategias tan simples como cambiar la orientación del cabezal o de la mesa de mecanizado, tal como se muestra en la Figura 1. Para el caso concreto de la Figura, se cambia la orientación relativa entre el modo a flexión del carnero con relación a la dirección de mecanizado, consiguiendo de esta manera una reducción del 15% en el valor de σmax sin que se haya modificado la masa de la máquina, por lo que se crea un margen para reducir la rigidez efectiva del modo en un 15% -y por extensión una reducción de la masa de la máquina- sin que dicho aligeramiento afecte a la productividad de la máquina.
- Optimizando la relación entre el factor kef ξ del modo y la masa que interviene en dicho modo. Para esta opción, son posibles dos sub-opciones:
2a. Rigidizar el modo sin incrementar la masa de los componentes estructurales. Una posibilidad es, por ejemplo, reforzar el sistema de guiado en aquellos modos en los que los guiados aportan una gran fracción de energía de deformación. En cambio, si nos encontramos con un modo en el que son los componentes estructurales los elementos que aportan la mayor parte de la energía de deformación, un enfoque muy efectivo es el de reemplazar el material estructural por otro de mayor módulo específico.
2b. Incrementar el amortiguamiento modal sin incrementar la masa de los componentes estructurales. Como referencia, los actuadores inerciales constituyen una manera muy eficiente de introducir amortiguamiento estructural en cualquier sistema mecánico sin que intervenga una cantidad significativa de masa [7]. Otro enfoque muy eficiente para incrementar el amortiguamiento modal, en este caso para modos en los que intervienen sistemas de guiado, es el de introducir guiados redundantes en dichos sistemas [6].
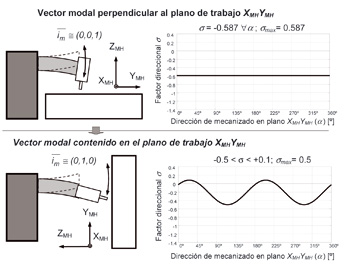
3. Aplicación a una fresadora de Nicolás Correa
Nicolás Correa ha decidido aplicar esta metodología para el diseño de fresadoras productivas y ecoeficientes a su línea de fresadoras Euro. Se trata de una familia de fresadoras de pórtico fijo y mesa móvil y carnero vertical, que ofrece capacidades de desbaste y semiacabado y que está orientada al sector de la mecánica general. La Figura 2 muestra una fresadora de dicha familia. Equipada con un electromandrino de alta velocidad, alcanza velocidades de avance de 30 m/min y aceleraciones de 3 m/s2.
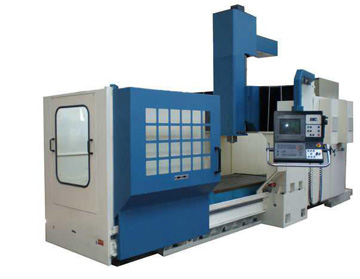
Figura 2. Fresadora 'Euro' de Nicolás Correa.
El carnero vertical tiene una sección aproximada de 350 x 400 mm2 y pesa unos 370 kg. Como caso de estudio para la metodología, se va a proceder a rediseñar este carnero, ya que es el componente estructural móvil de peso fijo más voluminoso. La mesa presenta una masa mayor, pero el peso móvil total está ligado al peso variable de la pieza que se va a mecanizar.
3.1. Estudio analítico y modal de la fresadora de Correa
Como punto de partida para el rediseño del carnero de la máquina Euro, se ha desarrollado un modelo MEF que ha permitido obtener los modos propios de la máquina:
Modo 1: Flexión lateral del pórtico en el plano YZ.
- kef1 = 27.387 N/m; ξ1 = 1,1 %; (kefξ)1 = 301,25 N/m
- Modo 2: Flexión frontal del pórtico en el plano XZ.
- kef2 = 46.339 N/m; ξ2 = 1,2 %; (kefξ)2 = 556,07 N/m
- Modo 3: Flexión frontal del carnero en el plano XZ.
- kef3 = 22.895 N/m; ξ3 = 2,7 %; (kefξ)3 = 618,16 N/m
- Modo 4: Flexión lateral del carnero en el plano YZ.
- kef4 = 44.186 N/m; ξ4 = 1,2 %; (kefξ)4 = 530,23 N/m
Dicho estudio analítico ha sido complementado con un análisis modal experimental, que ha permitido medir los valores reales de las frecuencias propias de la máquina y sobre todo, los valores reales de los coeficientes de amortiguamiento modal. A continuación, si se considera para el estudio una operación de desbaste de acero F-114 con un plato de 125 mm, 9 filos de ángulo de posición 45º y con una inmersión radial del 80% en concordancia, y se considera que el rango de velocidades de trabajo de dicha herramienta se encuentra en el rango de 400 a 600 rpm, se obtiene un diagrama polar de profundidades críticas de pasada tal como se muestra en la Figura 3.
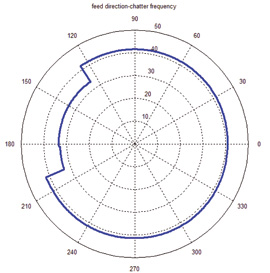
A partir de un proceso de identificación de frecuencias de chatter con frecuencias estructurales de la máquina, se ha llegado a la conclusión de que las frecuencias de chatter de dicha combinación máquina/proceso están asociadas a los modos 3 y 4 de flexión del carnero en los planos verticales XZ e YZ. De este dato se pueden extraer algunas conclusiones de interés:
i) Si se reduce la masa y la rigidez asociada a dichos modo y en paralelo se incrementa en la misma proporción el amortiguamiento asociado a dichos modos, se conseguirá mantener la productividad de la máquina con un menor empleo de recursos materiales y con una reducción del consumo energético en la fase de uso
ii) Si se reduce la masa y la rigidez asociada a los modos no limitantes de la máquina verificando en todo momento que dichos cambios no alteran el carácter no limitante de dichos modos, se conseguirá mantener la productividad de la máquina con un menor empleo de recursos materiales y con una reducción del consumo energético en su uso
A partir de este estudio analítico y experimental de la Euro, se han implementado los siguientes cambios de diseño mecánico para reducir el peso del carnero y a la vez mantener e incluso incrementar la productividad de la máquina:
1) Aligeramiento del carnero mediante una combinación de estructuras reticulares y materiales ligeros -> Reducción de la rigidez efectiva kef de los modos limitantes asociados al carnero
2) Introducción de un sistema de amortiguamiento activo en el carnero aligerado -> Incremento del amortiguamiento modal ξ de los modos limitantes asociados al carnero
A continuación se va a proceder a explicar en detalle cada una de estas dos estrategias para aligerar el carnero y mantener e incluso aumentar la productividad de la máquina.
3.2. Aligeramiento del carnero
Con el objetivo de reducir de manera radical el peso del carnero y con restricción de mantener las dimensiones exteriores del mismo, se ha reconcebido de raíz su concepto, empleando una estructura reticular y modular, tal como se muestra en la Figura 4.
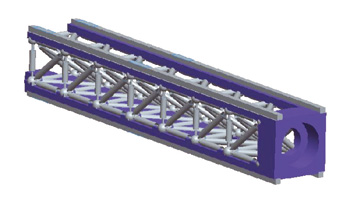
Sobre dicho concepto de estructura modular y reticular, se ha ido optimizando su diseño de detalle en base a un proceso iterativo en el que han intervenido variables tales como el material de las barras y nudos, diámetros interiores y exteriores de las barras, etc. El criterio que se ha seguido es el de reducir al máximo la rigidez dinámica del carnero en los modos limitantes, es decir, reducir las rigideces efectivas kef de los modos, y en paralelo, incrementar el amortiguamiento del carnero empleando un actuador inercial. Teniendo en cuenta que un actuador inercial es capaz de amortiguar de en torno a un 60-75% de los modos estructurales de una máquina herramienta [8], se ha puesto como objetivo que la reducción de la rigidez efectiva esté en dicho rango del 60-75%. De esta manera, la productividad que puede alcanzar la máquina no se verá afectada pese a que la rigidez del carnero –y por ende su masa- haya sido reducida de manera considerable.
Al respecto, la Tabla 1 muestra de una manera estructurada las principales características de la nueva versión del carnero.
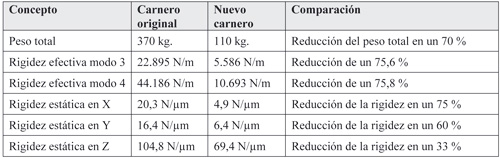
La Tabla 2, por su parte, presenta las principales características del carnero modular.

Una vez que se ha diseñado el carnero modular y aligerado, a continuación se va a proceder a integrar en dicho carnero un amortiguador activo biaxial, de manera que el efecto conjunto del carnero y el amortiguador se traduzca en un mantenimiento global de la productividad de la máquina
3.3. Introducción de amortiguamiento activo en el Demostrador
La Figura 5 muestra un innovador concepto de actuador inercial biaxial que ha sido desarrollado ad-hoc para el presente caso por la empresa belga Micromega [9].

Figura 5. Amortiguador inercial biaxial desarrollado por Micromega.
Este amortiguador activo biaxial desarrollado por Micromega tiene una fuerza máxima de 250 N, pesa 15 kg. y sus dimensiones exteriores son de 250x150x120 mm. Su potencia máxima es de únicamente 250 vatios, por lo que su efecto sobre el consumo global de la máquina es insignificante.
Una vez concluidos tanto el diseño del carnero como del amortiguador activo biaxial, se ha procedido al diseño en detalle del conjunto y su posterior lanzamiento a fabricación. La Figura 6 muestra una visión global del carnero, donde se pueden ver tanto el amortiguador inercial -externo al perfil del carnero- como las barras de tubos de fibra de carbono, debidamente protegidas por un plástico exterior transparente.
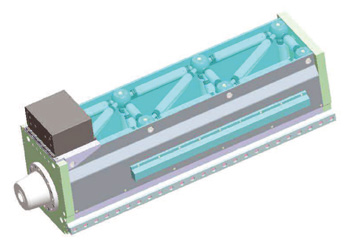
Una vez que el carnero aligerado y modular sea construido y montado, se procederá a integrarlo en la máquina ‘Euro’ para poder realizar ensayos experimentales de validación, incidiendo de manera especial en el consumo energético y en la productividad alcanzable con dicho carnero.
4. Conclusiones y perspectivas de explotación industrial
El presente documento ha presentado una metodología de diseño orientada a concebir fresadoras en las que se aúnan una elevada productividad con un reducido impacto medioambiental, aspecto éste relacionado en gran medida con el consumo de recursos materiales en la fase de construcción y el consumo energético en la fase de uso. El enfoque se ha basado en romper el vínculo entre una interacción estable máquina-pieza durante el proceso de mecanizado y la necesidad de conseguir elevadas rigideces mecánicas por medio de componentes estructurales de gran peso.
El diseño de un carnero ligero y modular dentro de una visión de una fresadora ecoeficiente y productiva, en el que se ha conseguido una reducción hasta un 70% en su peso con respecto al carnero original, junto con la integración de un amortiguador biaxial ha permitido conseguir un conjunto final capaz de mantener la productividad original de la fresadora pese a la notable reducción en el peso del carnero.
Todo ello lleva a la conclusión de que un enfoque multidisciplinar orientado a maximizar la relación entre la masa involucrada en una máquina herramienta y la productividad que se alcanza con dicha máquina repercute de manera beneficiosa tanto al proveedor de máquinas como al usuario de las mismas, ya que por una parte se reducen los costes de fabricación y adquisición de las máquinas, y por otra se reducen también los costes de explotación. De hecho, este beneficio mutuo, combinado con una concepción modular de las máquinas que permita una rápida configuración de máquinas ligeras y productivas, puede permitir establecer nuevos modelos de negocio en el sector manufacturero entre proveedores y usuarios de máquinas herramienta.
5. Agradecimientos
Los autores de este trabajo quieren agradecer a la Comisión Europea por la financiación del proyecto ‘NMP-246020-2- DEMAT- Dematerialised Manufacturing Systems: A new way to design, build, use and sell European Machine Tools’ dentro del 7º Programa Marco de Investigación y Desarrollo Tecnológico, así como al Ministerio de Ciencia e Innovación por la financiación del proyecto ‘Desarrollo de un Sistema Inteligente Híbrido para optimizar la interacción máquina-proceso en los procesos productivos orientados al sector eólico y de transporte (FOEHN) CIT-020000-2009-12’.
Referencias
[1] J. Zulaika, F.J. Campa, L.N. Lopez de Lacalle, “Light machine tools for productive machining”, 80 pp, ISBN 978-1-61324-644-3, Nova Publishers, New York, 2011
[2] J. Zulaika, F.J. Campa, J.A. Altamira, L.N. Lopez de Lacalle, G. Urbikain, “Using Stability Lobe Diagrams for the Redesign of a Machine-Tool based on Productivity and Ecoefficiency Criteria” 12th CIRP Conf. on Modelling of Machining Operations, San Sebastian, 2009
[3] J. Tlusty, M. Polacek, The stability of machine tool against self-excited vibrations in machining, International Research in Production Engineering (1963) 465–474.
[4] J. Zulaika, F.J. Campa, New Concepts for Structural Components, in: L.N. Lopez de Lacalle, A. Lamikiz (Eds.), Machine Tools for High Performance Machining, Springer Verlag, 2008, pp. 47-73.
[5] A. Dietmair, J. Zulaika, M. Sulitka, A. Bustillo and A. Verl, “Lifecycle Impact Reduction and Energy Savings through Light Weight Eco-Design of Machine Tools”, 17th CIRP International Conference on LCE, Anhui, China, May 2010.
[6] J. Zulaika, F.J. Campa, L.N. Lopez de Lacalle, “An integrated process–machine approach for designing productive and lightweight milling machines”, International Journal of Machine Tools and Manufacture, Volume 51, Issues 7–8, July–August 2011, Pages 591-604, ISSN 0890-6955
[7] A. Ganguli, A. Deraemaeker, M. Horodinca, A. Preumont, 2005, “Active damping of chatter in machine tools - demonstration with a 'hardware-in-the-loop' simulator”, Journal of Systems & Control Engineering 15: 359-369.
[8] L.N. López de Lacalle, A. Lamikiz, “Machine Tools for High Performance Machining”. ISBN: 978-1-84800-379-8. Springer-Verlag, Londres, 2010.
[9] www.micromega-dynamics.com