Mantenimiento predictivo de bajo coste
Sólo a través de la innovación tecnológica, el mantenimiento industrial podrá convertirse en la llave que nos lleve hacia una nueva generación de plantas industriales: más eficientes, más productivas, más competitivas, más inteligentes.
La optimización de la cadena de producción, se presenta como uno de los factores más importantes para ganar posiciones en un mercado tan competitivo como el de hoy en día. Reducir los tiempos de ciclo, disminuir los costes de producción, identificar las oportunidades de mejora de procesos y, en definitiva, aumentar el rendimiento de las plantas industriales, son los puntos clave para que el sector industrial aumente su mercado y su competitividad. En unos tiempos en los que la industria debe realizar grandes esfuerzos para conquistar pequeñas porciones de mercado, y cuando ciertos sectores industriales consideran hasta el tercer decimal en el coste del producto, la fiabilidad de la maquinaria representa una importante característica a tener en cuenta para no perder posiciones en el sector.
Los costes asociados a fallos de máquinas, especialmente las relacionadas con cadenas de producción masiva o las que trabajan con materia prima de alto coste, pueden provocar un efecto dramático en las empresas; no solo por el coste directo en la sustitución de piezas y horas de mano de obra, sino también por el tiempo de inactividad que, en según qué sectores, puede medirse en días. De acuerdo con los informes oficiales de la Unión Europea sobre las pymes en el sector industrial, se observa que, en algunos países, la eficiencia general de los equipos cae hasta un 60-70% debido al bajo rendimiento de la planta. Este hecho tiene un efecto directo en la producción y, en consecuencia, en los rendimientos económicos, por lo que se deben buscar soluciones si queremos alcanzar niveles de competitividad en un mercado cada vez más globalizado.
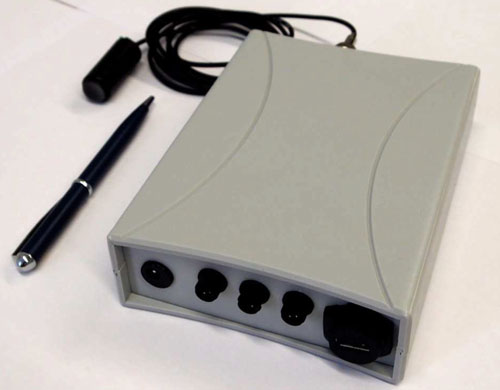
La monitorización de la evolución de los procesos y del estado de la maquinaria asociada, permitiría al personal de planta analizar y administrar la información para llevar a cabo las mejores acciones de cara a la optimización de la producción. Una reacción temprana permitiría una gestión óptima de las alarmas, y la detección de oportunidades para la mejora de las operaciones y la minimización de las anomalías.
En este sentido, algunos sectores tecnológicos se están posicionando como pieza clave para incrementar los niveles de productividad industrial. El mercado de sensores ya mostraba hace unos años que transductores con cierto procesado de señal embebido se vislumbran como el futuro de la monitorización industrial. El paradigma del mantenimiento se mueve hacia maquinaria que incluye su propio sistema de diagnóstico que, integrado con el resto de máquinas, muestre el estado de la planta de manera continua y centralizada. Sin embargo, a diferencia de las grandes empresas, que disponen de ciertas partidas presupuestarias para mejorar el mantenimiento de sus plantas, los nuevos desarrollos de sistemas de supervisión avanzados quedan lejos del alcance de la pequeña y mediana empresa.
Debido a esta situación, múltiples iniciativas I+D+i están siendo presentadas con un enfoque claro hacia la mejora de rendimiento productivo en las pymes. La Unión Europea, está dedicando grandes esfuerzos para incentivar el desarrollo de nuevos conceptos tecnológicos que ayuden a aumentar el rendimiento productivo industrial y, de esta manera, no perder el paso a las grandes referencias en este campo como son Estados Unidos, China, Japón, Brasil, Rusia e India entre otros.
Una de estas acciones, a través de la Agencia Europea de Investigación, es la cofinanciación de proyectos que permitan el desarrollo, implementación y validación de tecnología económicamente asequible que demuestre los beneficios de implantar sistemas de mantenimiento inteligente, y se mejore así la competitividad y la productividad del tejido industrial generado por la pequeña y mediana empresa.
Para el éxito de estas iniciativas, se requiere de empresas con experiencia en sus correspondientes sectores, ya que estas iniciativas cubren la investigación y el desarrollo, la producción, el valor de mercado y la explotación, para arrastrar detrás de ellas a socios, colaboradores y competencia. De manera complementaria, y con el objetivo de desarrollar productos tecnológicamente competitivos, la participación de centros de investigación es fundamental. Así, se sintonizan las innovaciones y desarrollos tecnológicos actuales con las necesidades del sector industrial.
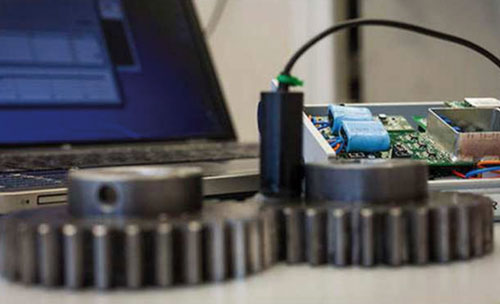
Mosycousis, el mantenimiento del futuro al alcance de la pequeña y mediana empresa
El proyecto Mosycousis es un claro ejemplo de iniciativa público-privada de carácter europeo que tiene como principal beneficiario a las pymes. El Centro de Innovación MCIA, de la Universidad Politécnica de Catalunya, encabeza, junto con otros centros europeos, los desarrollos tecnológicos que permitirán introducir al mercado un sistema de diagnóstico inteligente de bajo coste sobre la base de la detección de emisiones acústicas, para la monitorización y el mantenimiento preventivo de componentes mecánicos en maquinaria industrial.
El concepto detrás de esta iniciativa consiste en la introducción de sensores inteligentes distribuidos por la planta, combinado con un sistema experto como interfaz de usuario para la visualización centralizada de la información, lo que representa un avance significativo respecto a la mayoría de las estrategias de mantenimiento actuales de la pequeña y mediana industria. La monitorización, a diferencia de la mayoría de las soluciones actuales, no se basa únicamente en la adquisición de la magnitud física correspondiente, si no que el propio sensor incluye el procesado de señal necesario para identificar el contenido de la señal y hacer llegar una información ya interpretada al usuario.
A través de productos de este tipo, se puede implementar una monitorización continua donde cualquier indicio de malfuncionamiento sería notificado de manera automática al personal de planta. Esta estrategia, posibilitaría la revisión del equipo bajo petición, y se realizaría la actuación de mantenimiento y la planificación de actividades más adecuada para minimizar el impacto en los índices de producción y calidad del producto. En este sentido, se dejan atrás los clásicos dispositivos manuales que el operario hace servir periódicamente para las revisiones rutinarias, y que no permiten evolucionar del actual mantenimiento preventivo hacia un futuro mantenimiento predictivo.
Con tal objetivo en mente, se constituye el proyecto Mosycousis, liderado por el Centro Tecnológico de Manresa y parcialmente financiado por la Comisión Europea mediante el 7º Programa Marco. En el proyecto participan más de 25 investigadores provenientes de diferentes empresas e instituciones con el objetivo de desarrollar un sensor ultrasónico inteligente, autoalimentado y capaz de establecer automáticamente una red de sensores inalámbricos que ayude al control y al mantenimiento, especialmente en maquinaria rotativa.
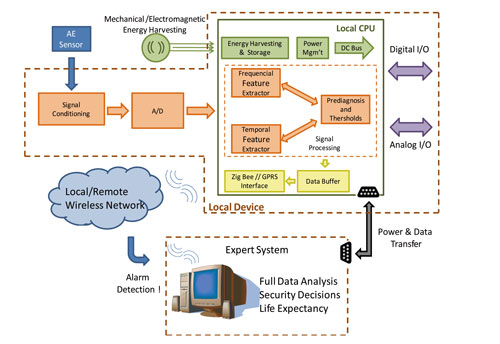
Funcionamiento de Mosycousis.
Mantenimiento predictivo sin complejos
La principal ventaja de la detección a través de emisiones acústicas en comparación con las técnicas tradicionales de vibración es la mejor relación señal-ruido disponible y, por lo tanto, la posibilidad de detectar un fallo o una degradación en su fase inicial.
Las fuentes de emisiones acústicas en maquinaria incluyen impactos, fatiga, grietas, fricciones, desgastes y otros. Sin embargo, en la mayoría de los casos, los operarios de mantenimiento estarían satisfechos con un simple y asequible dispositivo capaz de avisar de un fallo inminente en uno de los subsistemas críticos que la componen. En la mayoría de los casos, las vibraciones aparecen después de que el fallo haya repercutido en el rendimiento de la máquina. En este sentido, el proyecto Mosycousis tiene como objetivo desarrollar un sistema de monitorización de maquinaria rotativa para mantenimiento predictivo de engranajes, cojinetes, ejes y acoples mecánicos basados en emisiones acústicas, incluso mientras se encuentran en plena operación debido a la poca afectación de la velocidad de la máquina al método de diagnóstico.
Los avances en tecnologías de transductores, microprocesadores y transceptores posibilitan una nueva generación de sensores inalámbricos inteligentes. Este escenario lleva a un futuro de sensores distribuidos informando de la condición de la planta, facilitando la monitorización estructural de las máquinas sin necesidades de cableado ni instalaciones adicionales. Con el objetivo de proveer redes de sensores realmente autónomas, existe la posibilidad de extracción de las baterías del concepto del sensor y su substitución por sistemas de aprovechamiento de energía del propio entorno, tales como vibraciones, fuentes térmicas o solares.
Conectando diferentes transductores resonantes, basados en cerámicas de bajo coste, se consigue extraer el patrón acústico de los elementos de la máquina bajo monitorización. Estos transductores se conectan a una misma electrónica común para todos ellos, también de bajo coste y bajo consumo que, para una mejor integración con el entorno industrial, se encapsula en un módulo aparte que puede ir situado en alguno de los armarios de control próximos a la maquinaria. En dicho módulo se encuentra el procesador local, que realiza la adquisición de las señales y un procesado para extraer la información útil y generar un diagnóstico de los puntos monitorizados.
Adicionalmente, y para aquellas aplicaciones aisladas o de difícil acceso, se facilita un módulo para el aprovechamiento de la energía del entorno capaz de recuperar energía parásita de fuentes de vibración, fuentes de calor o solar y un sistema de ultracondensadores para su correcto almacenamiento. Durante el funcionamiento normal del sensor, de manera esporádica, información de diagnóstico es enviada mediantes tramas cortas vía radiofrecuencia al sistema experto, que se encontraría instalado en un ordenador en alguna sala de control próxima o en la propia planta. El sistema experto, desde donde se podrá visualizar toda la información generada por la red de sensores, mostrará aquellos puntos críticos de la planta que requieren de una inspección más detallada. El mismo programa analiza en profundidad la información, ofreciendo datos de diagnóstico y de pronóstico mediante el análisis del histórico de evolución. Los procesados incluidos tanto en el sensor como en el sistema experto, traducen los patrones de emisiones acústicas por nivel de degradación de los elementos mecánicos monitorizados, a través de algoritmos basados en inteligencia artificial que evitan hasta un 90% de las falsas alarmas. Después de la detección del fallo, y el análisis completo de las señales por el sistema experto, el personal de mantenimiento podrá llevar a cabo las acciones correspondientes: lubricación, substitución de componentes, monitorización continua de componentes bajo alarma, priorización de las paradas planificadas etc., en función de la política de mantenimiento de la empresa.
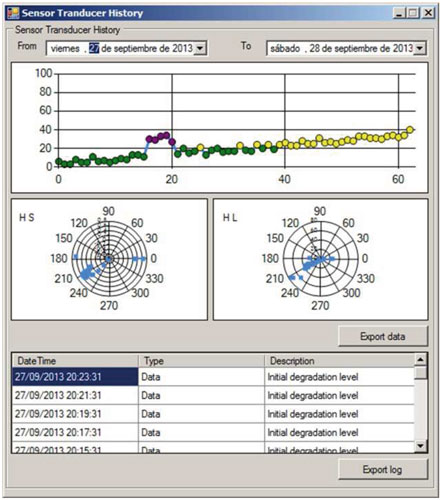
El concepto puede ser aplicado a una gran cantidad de aplicaciones industriales. Sin embargo, la información obtenida puede ser utilizada no solo para un diagnóstico precoz de fallos, si no para integrarlo con información externa y realizar un control adaptativo para extender la vida útil de las máquinas.
En este sentido, el sensor ofrece importantes ventajas. Como el sensor está acoplado a la máquina, no contiene puertos específicos ni instalación adicional, y resulta en un diseño compacto y barato comparado con las soluciones comerciales. El procesado de señal en el sensor es simple y rápido, por lo que no se necesita gran cantidad de memoria ni procesadores potentes. Solo los indicadores extraídos son enviados a través de la red en forma de mensajes cortos y esporádicos hacia el sistema experto central. Esto hace que las necesidades de alimentación sean pequeñas y el sensor pueda alimentarse de fuentes de energía parásitas, lo que representa una novedad en el mercado. Los algoritmos avanzados corren en un ordenador estándar de bajo coste y la red inalámbrica no es costosa.
Así, Mosycousis se constituye como un claro ejemplo de una inversión público-privada en I+D+i con el fin de desarrollar y transferir conocimientos tecnológicos al sector industrial y especialmente a la protección e impulso de la pymes. El proyecto se inició en octubre de 2011 bajo la coordinación del Centro Tecnológico de Manresa (CTM), y se desarrollará durante 24 meses. Los socios del consorcio que forman equipo con CTM son la Universidad Politécnica de Cataluña a través del centro de investigación MCIA, el Centro de Investigación Tyndall (Irlanda), el fabricante de transductores acústicos Optel (Rumania), Endeco Technologies (Irlanda) como distribuidor de servicios de mantenimiento en plantas industriales, Ardoran (Estonia) como consultor y experto en la explotación de productos y Sitex45 y Electroarges (Rumania) como plantas piloto. El proyecto es un claro ejemplo del interés socio-económico existente a nivel internacional, con el fin de aumentar la competitividad del sector industrial. Acciones y desarrollos tecnológicos como los considerados en el proyecto Mosycousis permitirán la evolución hacia un sector industrial inteligente y competitivo, retornando a la sociedad la inversión realizada a través de una producción inteligente.
Características técnicas principales del sistema Mosycousis:
- Circuitería de adquisición, acondicionamiento y procesado integrada en el sensor.
El sistema ofrece tres canales de entradas analógicas, conectadas a un convertidor de 14 bits con una frecuencia máxima de adquisición de 2 MHz.
Hasta tres transductores de emisiones acústicas (resonantes y/o de amplio espectro) pueden ser conectados y tratados independientemente. Acondicionamiento de la señal analógica mediante un filtraje pasa banda (50 kHz a 500 kHz), con una etapa de amplificación configurable (de 32 db a 40 db).
Capacidad de almacenamiento de hasta 2 Mb de información preprocesada.
El preprocesado local se soporta mediante un procesador ARM. Los indicadores extraídos para la ejecución de los algoritmos de prediagnóstico se basan en análisis temporal y espectral, así como el análisis del histórico de índices característicos de fallos. Perfiles de operación de bajo consumo.
- Múltiples posibilidades de alimentación
Conexión para 24 VDC estándar.
Módulo de almacenamiento de energía basado en tecnología de supercondensadores.
Hasta tres transductores de captación de energía pueden ser conectados simultáneamente, basados en vibraciones, temperatura y fuentes de luz interior, para extraer de 2 mW a 6 mW de potencia de salida.
- Comunicaciones Puerto USB2.0 para configuración del sensor, descarga de datos y actualizaciones del sistema.
Comunicación inalámbrica local, 802.15.4 (24.4 GHz Zig.Bee), topología en estrella.
Índices de prediagnóstico, alarmas y mensajes de estado de batería.
Comunicación automática unidireccional.
- Sistema experto
Monitorización de la red de sensores e interfaz gráfica de usuario para configuración y visualización.
Parámetros de los algoritmos personalizables a la aplicación.
Procesado de los datos de prediagnóstico y de datos en bruto de emisiones acústicas mediante un módulo gráfico en tiempo y frecuencia.