Desarrollos en acero para herramientas
Esta conferencia internacional, que se celebra cada tres años, quiere presentar nueva información sobre la fabricación de aceros, especialmente para herramientas, y promover el intercambio de información entre usuarios, fabricantes, productores de acero e investigadores. Por ello, entre las ponencias se destaca una mezcla continua y profunda de técnicos industriales y científicos especializados.
La producción de moldes y matrices se ve directamente beneficiada de los avances en aceros para herramientas. Como dato orientativo se indica que solo el 0,1por ciento del total de acero producido es consumido para herramientas. Y eso ¿es poco o es mucho? Para un país como España este número es poco representativo porque actualmente no es un país dedicado a producir acero de esta calidad —sólo Sidenor produce este tipo de aceros en España—. Pero por ser el nuestro un país con una gran producción de utillajes, moldes y matrices debe dedicarse la importancia que se merece a estos materiales.
Consecuencia de la globalización que nos toca vivir, es la presencia de profesionales de todos los continentes. Este hecho pone de manifiesto el interés común de todos aquellos que de una u otra manera sufren y gozan de las cualidades de los aceros para herramientas.
Para dar una mayor cobertura a todos los aspectos relativos a la conferencia se dividieron las casi cien presentaciones en diez áreas temáticas: trabajo en caliente, trabajo en frío, aceros para moldes de plástico, aceros rápidos, tratamiento térmico, fatiga de aceros para herramientas, ingeniería de superficie, spray forming y rapid tooling, mecanizado de aceros y tópicos de usuarios finales.
Tres aspectos merecen ser resaltados de esta sexta edición: los esfuerzos para aumentar la productividad de los aceros para trabajo en caliente, la problemática asociada a los nuevos aceros de ultra-alta resistencia y los avances en la técnica de spray forming.
Aceros para trabajo en caliente
Puesto que los equipos de ensayo y control son cada vez más fiables y económicos, se presentaron distintas metodologías que permiten caracterizar el deterioro del útil y por tanto estudiarlo y evitarlo con mayor garantía de éxito —científico de un lado y productivo del otro—Una conclusión generalizada es que las calidades de acero obtenidos por métodos de refusión por arco eléctrico de escoria alargan la vida de los moldes gracias a su homogeneidad estructural y tamaño de grano fino.
Las técnicas más recientes para tratar y recubrir los aceros con elementos de propiedades deseadas también deben ser consideradas en estos materiales. Debe insistirse en que un salto de durezas o desafinidad química entre el componente mayoritario más externo y el núcleo del material será garantía de un fallo prematuro. Dicho de otra manera, debe promoverse un gradiente entre el recubrimiento externo y el núcleo. Desgraciadamente, todavía no se puede dar una formulación y estequiometría que garantice el éxito en todas las aplicaciones. Según el doctor Rajiv Shivpuri de la Universidad de Ohio, la solución al problema puede estar en un sistema de combinación de elementos y compuestos en estructuras formadas por el núcleo de acero EN-X40CrMoSiV5 (W.Nr. 1.2344, AISI H13), una capa nitrurada iónicamente, una interfase de difusión y multicapas tipo TiN+TiBN/TiCN/TiAlN. Con este método han llegado a reducir el porcentaje de material erosionado de la cavidad o punzón y aumentado en cerca de un 5 por ciento la productividad del molde.
Hace solo tres años se auguraba un incremento en el número de componentes basados en aluminio, magnesio y zinc (las llamadas aleaciones ligeras y ultraligeras). Las previsiones se han reducido pero se constata un aumento en el consumo mundial y aplicaciones de materiales. De esta manera se garantiza el contínuo interés por los aceros para trabajo en caliente.
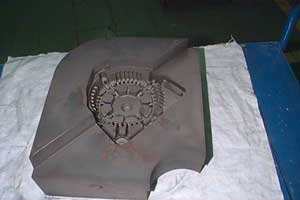
Aceros para chapa de alta resistencia mecánica
Su gran ventaja se convierte en el peor de sus enemigos cuando de transformarlo —léase deformarlo— se trata. Los costes de producción se han incrementado y no precisamente por el coste propio del material. Los esfuerzos se centran ahora en como mejorar la productividad de los aceros para trabajo en frío que se utilizan en la tranformación de chapa. Análisis numéricos de solicitación mecánica de la matriz, composición química y estructura metalográfica, estudio del desgaste del material y propuesta de recubrimientos… se están realizando confiando en que también la metalurgia o la ciencia de materiales dé ahora la respuesta al problema planteado.
El director de investigación y desarrollo de la Volvo Car Corporation puso su experiencia como ejemplo. Para un montante B de acero de Rm=650 MPa y grueso 1,95 mm han conseguido 285.100 piezas sin desgaste ni contratiempos en la matriz con un acero DIN 60CrMoV18-5 (W.Nr. 1.2358) nitrurado iónicamente y recubierto mediante PVD con CrN. Importante es mencionar que a partir de la pieza 186.800 la estampación se hizo sin lubricación extra. Al final de su exposición hacía mención explícita de que la minimización del desgaste de la matriz en la estampación de los aceros de alta resistencia es esencial en los próximos años, puesto que éstos se van a usar de forma obligada y en aumento.
Spray forming: una nueva técnica de producción de aceros
La gran novedad del congreso fue la presentación de aplicaciones de los aceros obtenidos por spray forming. El proceso consiste en pulverizar el acero y hacerlo impactar sobre un blanco. Cuando la pistola es estática y el eje sobre el que se encuentra el blanco también se obtienen lingotes cilíndricos que posteriormente pueden ser mecanizados a gusto del consumidor. En cambio cuando la pistola es dinámica, se puede recubrir un blanco del acero deseado y conseguir directamente la geometría de útil deseada. Este segundo caso corresponde a las aplicaciones de rapid tooling y actualmente el proceso es propiedad de Ford, quién en su planta de Valencia lo ha puesto en práctica para preseries de piezas de carrocería del Focus. El anteriormente mencionado Nader Asnafi resaltaba que el uso de esta técnica en las primeras etapas de desarrollo de un nuevo vehículo les permite disponer de la matriz en solo 2 semanas como máximo, con una tolerancia de ±0,076 mm y una reducción en el coste cercano al 30 por ciento.
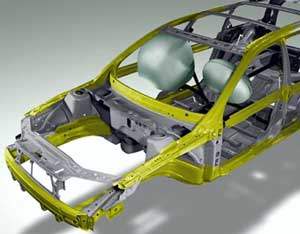
La gran novedad del congreso fue la presentación de aplicaciones de los aceros obtenidos por ‘spray forming’. El proceso consiste en pulverizar el acero y hacerlo impactar sobre un blanco
Desde su creación, la Fundación Ascamm ha dirigido todos sus esfuerzos a mejorar la competitividad de las empresas por la vía de la innovación y el desarrollo tecnológico, la formación, la calidad y la internacionalización, en el subsector de moldes y matrices en particular y en el de transformados metálicos y plásticos en general.
Una de sus principales líneas de investigación es el desarrollo de nuevas técnicas y su incorporación a los utillajes de producción. El objetivo es mejorar las prestaciones del producto y el proceso (optimización del tiempo de ciclo y aumento de la fiabilidad). Las investigaciones cubren las áreas de nuevos materiales, nuevas tecnologías de fabricación y programas asistidos por ordenador para el diseño de los moldes.
Proyectos de la fundación relacionados con el artículo
* Mejora de la productividad de moldes de inyección de aluminio.
* Optimización del comportamiento mecánico de matrices y útiles de conformación
para nuevos aceros de alta resistencia.
* Aumento de la productividad de los moldes de inyección de termoplástico construidos
mediante sinterizado directo de polvo metálico por láser.
* Elección del acero más adecuado a través de un documento-guía.