El menos convencional de los mecanizados
El proceso de la electroerosión es, hoy en día, un proceso de fabricación utilizado en la industria para el mecanizado de alta precisión de todo tipo de materiales conductores tales como metales, aleaciones metálicas, grafito, cerámicas, entre otros, de cualquier dureza.
Como se ha comentado anteriormente, el mecanizado por electroerosión es llevado a cabo gracias a las descargas o chispas eléctricas que se producen entre dos electrodos sometidos a un voltaje eléctrico y sumergidos en un fluido dieléctrico. Así, el voltaje aplicado a ambos debe ser suficiente para crear un campo eléctrico de mayor valor que la rigidez dieléctrica del fluido utilizado en el proceso.
Básicamente, hay dos tipos diferentes de procesos de electroerosión: el proceso de electroerosión por penetración y el proceso de electroerosión de corte por hilo. En la electroerosión por penetración se reproduce en la pieza la forma de la herramienta utilizada (que se denomina electrodo), mientras que en el proceso de electroerosión de corte por hilo, un cable o hilo de metal (electrodo) es usado para cortar un contorno programado sobre la pieza.
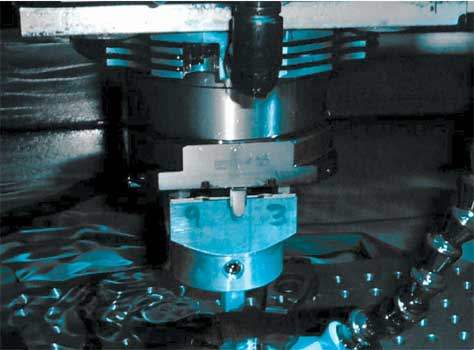
Historia y evolución
La historia de la electroerosión se remonta al periodo de las dos guerras mundiales. Hasta entonces, prácticamente nadie había sido capaz de entrever el potencial de dicha tecnología, ya que se eliminaba igual cantidad de material del electrodo que de la pieza a mecanizar y, además, el mecanismo manual que controlaba el avance daba lugar a más situaciones de cortocircuito que de mecanizado estable. Durante este periodo inicial, la introducción de un sistema de vibración del electrodo, que mejoraba la tasa de eliminación del material, fue el primer intento de control de la distancia del gap. Pero hubo dos científicos de la antigua Unión Soviética que estaban convencidos de que se podían llevar a cabo muchas más mejoras en esta incipiente tecnología de la electroerosión. Los Doctores B. R. y N. I. Lazarenko fueron un matrimonio de científicos Rusos que inventaron el circuito de relajación, representado en la figura 1, además de un sencillo servo controlador que ayudaba a mantener constante la distancia del gap entre la herramienta y la pieza a mecanizar. Lo anterior constituyó un hito crucial en la historia de la electroerosión, ya que hizo que se redujeran las situaciones de cortocircuito y que el proceso se volviera más rentable económicamente.
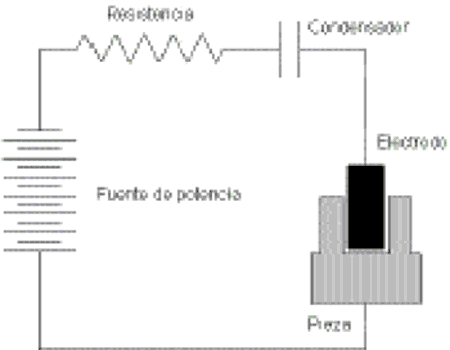
Había diversos problemas que afrontar a la hora de realizar modelos matemáticos del proceso de la electroerosión, tales como la contaminación del gap así como el comportamiento hidrodinámico y termodinámico del fluido de trabajo empleado. Por lo tanto, obtener un modelo que tuviera en cuenta todos los resultados obtenidos a partir de la experimentación práctica era bastante difícil, lo que hizo, junto con la gran demanda de mercado existente (ver figura 2).
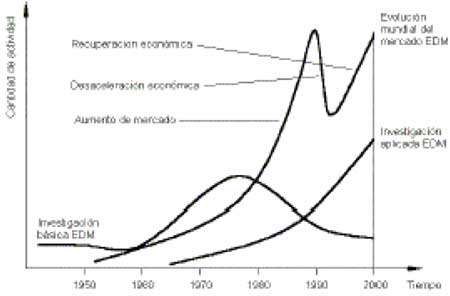
La importante evolución que experimentó el proceso de la electroerosión mediante corte por hilo en los años 70 fue debida a la aparición de generadores con mejores prestaciones de potencia, nuevos electrodos de hilo, la mejora de las prestaciones mecánicas y de automatización de las máquinas, así como una mejora también de los procedimientos de limpieza del gap Gough [3]. Así, a lo largo de los años, la velocidad de trabajo del proceso de corte por hilo se ha incrementado hasta 20 veces el valor de la primera aplicación, mientras que los costes de mecanizado han disminuido, por lo menos, en torno a un 30%. Por otro lado, el acabado superficial se ha mejorado del orden de unas 15 veces mientras que los valores de la corriente de descarga se han multiplicado por 10 veces Jablonowski [4].
Diferentes teorías de la eliminación del material en la electroerosión
- La teoría electro-mecánica
- La teoría termo-mecánica
- La teoría termo-eléctrica
La teoría electro-mecánica sugiere que la erosión de las partículas del material se produce como consecuencia de la intensidad del campo eléctrico que se genera. Dicha teoría postula que el campo eléctrico es el que separa las partículas del material ya que se superan las fuerzas de cohesión de la red del material. Esta teoría desatiende la ocurrencia de cualquier efecto térmico y la evidencia experimental carece de apoyos que sustenten la misma.
La teoría termo-mecánica sugiere la hipótesis de que la eliminación de material en el proceso de la electroerosión se atribuye a la fusión del material debido a las llamaradas (en la nomenclatura anglosajona se denominan como flame jets) que se forman a consecuencia de los diversos efectos eléctricos de la descarga. Sin embargo, esta teoría no concuerda con los resultados obtenidos de manera experimental y falla a la hora de dar una explicación razonable acerca del efecto de la erosión de la chispa eléctrica.
La teoría termo-eléctrica, que es la mejor sustentada de las tres por los datos experimentales, sugiere que la eliminación del material en el proceso de la electroerosión ocurre como consecuencia de la elevada temperatura que se genera debido a la alta intensidad de corriente de descarga. Aunque esta teoría se encuentra bien sustentada por la experimentación, no puede considerarse como la definitiva debido a dificultades en su interpretación.
Mecanismo del proceso de la electroerosión
Aunque no es absolutamente necesario comprender el mecanismo del proceso de la electroerosión para ser un buen operario en lo que respecta a los equipos de dicha tecnología, el conocimiento de lo que realmente sucede entre la pieza y el electrodo, es decir, la teoría de la electroerosión, puede ayudar a encarar la resolución de problemas tales como la selección de las adecuadas combinaciones del material del electrodo y material de la pieza a mecanizar, o de por qué las condiciones que son óptimas en una determinada situación no lo son para otra.
Como se ha citado anteriormente, existen diversas teorías acerca del proceso pero es el modelo termoeléctrico el que mejor ha quedado sustentado por la experimentación práctica. En las siguientes figuras se representa, paso a paso, lo que se cree que realmente sucede durante un ciclo del proceso de la electroerosión. Werner [7], Kahng [8] y Poco Graphite [9].
El electrodo cargado se acerca a la superficie de la pieza a mecanizar, habiendo entre ambos un aceite aislante que se conoce con el nombre de fluido dieléctrico. Aunque un fluido dieléctrico es buen aislante, una diferencia de potencial lo suficientemente elevada puede producir que el fluido se rompa dando lugar a fragmentos iónicos que permiten que se establezca un paso de la corriente eléctrica entre el electrodo y la pieza de trabajo. La presencia de las partículas metálicas y de grafito que se encuentran en suspensión en el fluido dieléctrico pueden ayudar a la anterior transferencia eléctrica de dos formas diferentes. Por un lado, las partículas, que son conductores eléctricos, ayudan en la ionización del aceite dieléctrico y, además, pueden transportar la carga eléctrica directamente. Por otro lado, dichas partículas pueden hacer la función de catalizador en la ruptura eléctrica del fluido. Así, el campo eléctrico creado es mayor en el punto donde la distancia entre el electrodo y la pieza es menor. En esta fase del proceso (ver la figura 3),
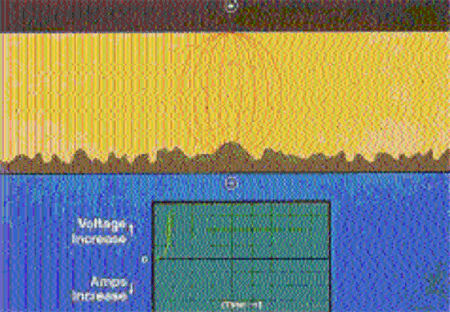
En la siguiente fase (ver la figura 4), mientras que aumenta el número de partículas iónicas, las propiedades aislantes del fluido dieléctrico comienzan a disminuir a lo largo de un estrecho canal, que se sitúa donde el valor del campo eléctrico es más elevado. Es justo en este momento cuando la diferencia de potencial alcanza su valor máximo, siendo el valor de la intensidad de corriente todavía nulo.
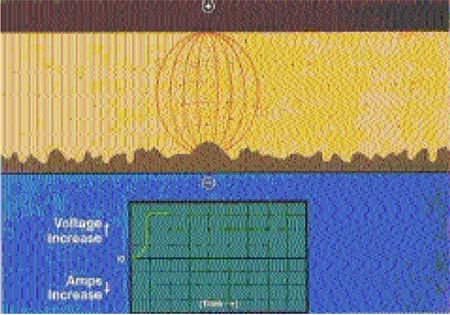
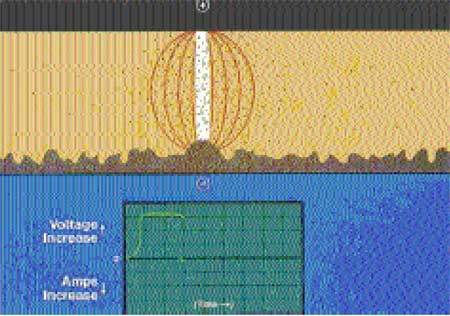
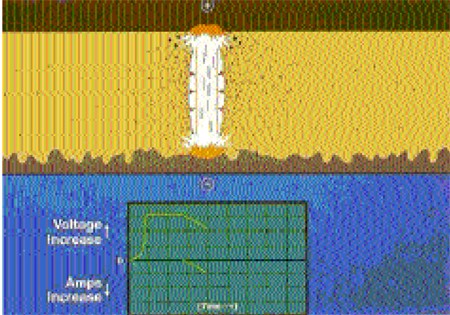
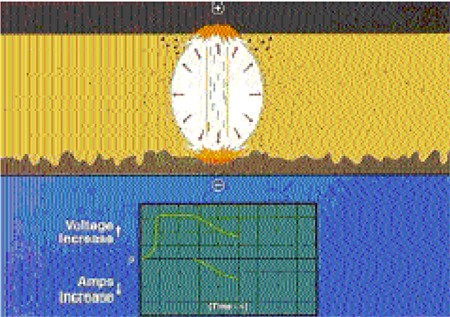
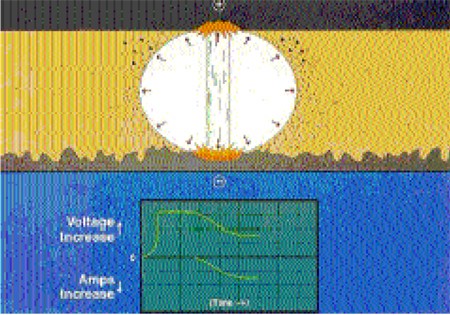
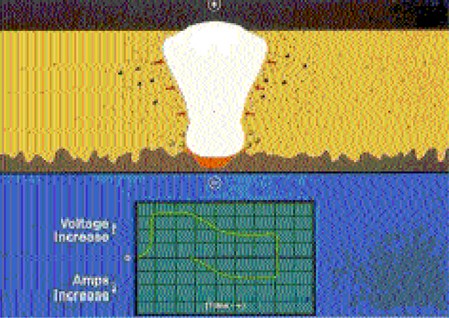
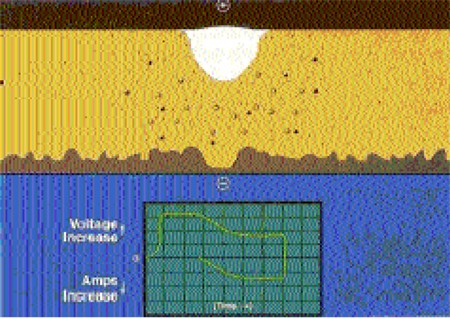
Existen también algunos estudios, tales como en Schumacher [11], en los que se afirma que la contaminación de la zona del gap de trabajo, debido a las partículas erosionadas en el proceso, tiene influencia sobre el proceso de ignición, la localización de la descarga eléctrica así como la anchura del gap.
Toda la anteriormente vista secuencia del proceso de la electroerosión representa un único ciclo del proceso que puede repetirse hasta 250 000 veces cada segundo. En cada momento, sólo puede estar ocurriendo un único ciclo.
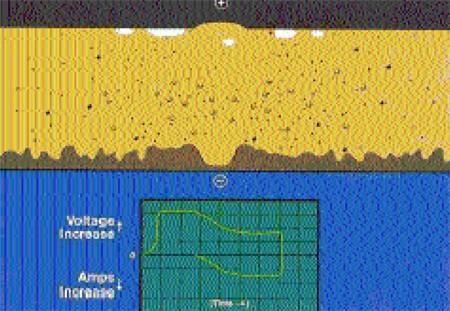
Referencias bibliográficas
- Houman, L., What’s New in Edm Power Supplies and Machines, Society of Manufacturing Engineers, 1973.
- Poco Graphite, Inc., EDM Technical Manual, Poco Graphite Inc., 1993.
- Gough, P.J.C., Advances in EDM technology, Sheet Metal Industries, Mayo 1979.
- Jablonowski, J., What's New in EDMs?, Modern Plastics International, Marzo 1999.
- Kahng, C. H.; Rajurkar, K. P., Fundamental Theories of the Parameters of Edm Process, Society of Manufacturing Engineers, 1977.
- Rajurkar, K. P., Advances in Technology and Reserch of Edm, SME International Conference And Exposition (Michigan), Mayo 1989.
- Werner, A. R.; Olson, P. C., EDM - A Metal Remoal Process, Society of Manufacturing Engineers, 1968.
- Houman, L., What's New in Edm Power Supplies and Machines, Society of Manufacturing Engineers, 1973.
- Poco Graphite, Inc., EDM Technical Manual, Poco Graphite Inc., 1993.
- Rajurkar, K.P; Pandit, S.M., Formation and Ejection of EDM Debris, Journal of Engineering for Industry, Febrero 1986.
- Schumacher, B.M.,About the Role of Debris in the Gap during Electrical Discharge Machining, Annals of the CIRP, 1990.
- Crookall, J.R., An Analysis of EDM Utilisation in industrial Tooling Manufacture, Annals of the CIRP, 1978.
- Rajurkar, K.P., Advances in Technology and Research of Edm, SME International Conference And Exposition ( Michigan), Mayo 1989.
- Ahmed, M.S., Edm Finds a new Role in Manufacturing, SME International COnference and Exposition ( Michigan), Mayo 1989.
- Risko, DG., Machining of Forging Dies Using Electrolytic Machining and Electro Discharge Machining, Forging Technology COnference ( Michigan), Agosto 1992