Tecnologías y aplicaciones en fabricación aditiva de materiales metálicos
Introducción
Las tecnologías de fabricación aditiva, additive manufacturing en inglés, se definen como los procesos de unión de materiales para crear objetos, usualmente capa a capa, a partir de datos 3D de un modelo, de forma opuesta a las técnicas de fabricación sustractiva [1]. Estas tecnologías permiten la fabricación directa de objetos 3D a partir de datos o modelos CAD (Computer Assisted Design).
En la actualidad, estas tecnologías permiten fabricar piezas 100% funcionales con un alto valor añadido y constituyen un conjunto de tecnologías emergentes que se están convirtiendo en serias competidoras de los procesos de mecanizado y conformado tradicionales. Este tipo de tecnologías se están introduciendo de una manera creciente en sectores tales como el biomédico, aeronaútica, automoción, molde y matricería y cada vez más en la fabricación de productos de consumo general.
Principales ventajas de las tecnologías de fabricación aditiva
- Reducción del tiempo de lanzamiento al mercado debido a la rapidez del proceso. Se pueden reducir drásticamente muchas de las fases actuales de lanzamiento y validación, así como flexibilizar su adaptación a las demandas en constante cambio del mercado.
- Personalización de productos con una total flexibilidad en el diseño y construcción. Se pueden producir piezas de prácticamente cualquier forma y sin casi limitaciones geométricas. Un ejemplo claro es la fabricación de implantes o prótesis adaptados a las particularidades de cada paciente.
- Ahorro máximo de material. Se elimina el desperdicio de material en forma de viruta de mecanizado… Existen estudio donde se concluye que es posible reducir hasta en un 40% el volumen de material en bruto [3].
- No se requieren útiles, moldes ni troqueles. Las piezas se producen directamente de un modelo CAD 3D con ausencia total de errores humanos en producción y se pueden fabricar series unitarias sin apenas costes extras.
- Se producen piezas totalmente funcionales y sin porosidad residual.
- Fabricación de estructuras cerradas con libertad de diseño. Es posible fabricar piezas con una gran complejidad de forma, con canales internos o estructuras reticulares aligeradas.
- Posibilidad de desarrollar productos multimaterial, ergonómicos o con varios mecanismos integrados en una misma pieza.
El trabajo aquí presentado está precisamente dirigido a analizar y alcanzar estos retos. El avance sobre el estado del arte radica en la definición de las condiciones del polvo y del proceso (parámetros, estrategias de fabricación) que permitan evitar la aparición de defectos, optimizar la densidad de las piezas fabricadas y de su condición superficial y precisión.
Cabe señalar que actualmente existen más de 11.500 patentes y aplicaciones publicadas sobre los procesos de fabricación aditiva. Cada año se publican más de 1.400 nuevas patentes que abarcan todas las facetas de la tecnología incluyendo: procesos, materiales y software; diversas aplicaciones en medicina, moldes…
Proceso de fusión selectiva por láser (SLM)
El proceso de fusión selectiva mediante láser, en ingles selective laser melting o SLM, es un proceso de fabricación aditiva desarrollado recientemente para materiales metálicos [4] [5] [6]. El proceso se describe en detalle en la Ref. [6]. Se basa en la fusión mediante la acción de un láser de polvo metálico predepositado en capas muy finas y uniformes sobre una plataforma de trabajo; el proceso se repite capa a capa hasta completarse la pieza. El láser genera en cada capa el contorno de la pieza a construir fundiendo el polvo. La plataforma desciende a lo largo del eje z tras finalizar cada capa una distancia igual al espesor de la capa trabajo (habitualmente entre 20 y 50 micras). Los procesos de aplicación y fusión se repiten de forma sucesiva hasta que se completan todas las capas que constituyen la pieza final.
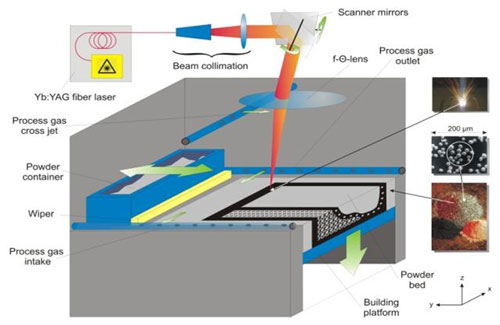
Figura 1: Descripción el proceso SLM.
En la tecnología SLM se utiliza un láser como fuente de energía para fundir el polvo. Mucho de los materiales metálicos aptos para este proceso son susceptibles a la oxidación. Por este motivo el proceso SLM se lleva a cabo en cámaras cerradas y habitualmente en atmósferas protectoras (no oxidantes). Es habitual trabajar con aleaciones de titanio o cobalto-cromo en atmósferas inertes de argón.
En la actualidad existen distintas marcas comerciales de equipos SLM. Entre ellas las más relevantes son Electro Optical Systems (EOS), Realizer GmbH, Renishaw y SLM Solutions GmbH, las dos últimas surgidas de MTT Machines [6]. La compañía americana Concept Laser comercializa también esta tecnología con el nombre alternativo de Laser Cusing, si bien se trata de la misma tecnología. Aunque la gama de materiales procesable puede variar en función de las características de cada equipo, a día de hoy se pueden procesar una gran variedad de materiales metálicos entre los que se incluyen aceros inoxidables, aceros de herramienta (H13), aleaciones de titanio (TiAl6V4 y TiAl6Nb7), aleaciones de cobalto cromo, aleaciones de aluminio (AlSi12Mg y AlSi10Mg), aleaciones de bronce y aleaciones de níquel (INC625 e INC718).
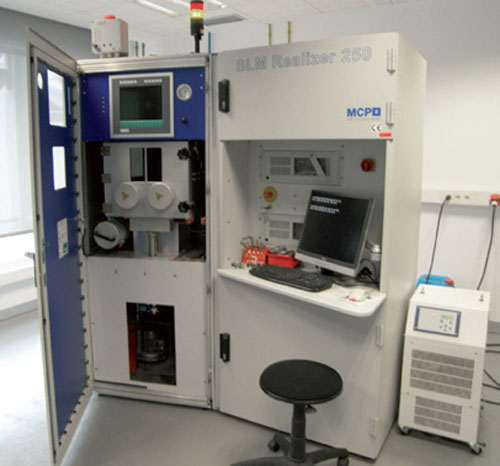
Figura 2: Equipamiento SLM Realizer 250 de IK4 Lortek.
Aplicaciones SLM
En este apartado se muestran algunos ejemplos reales de piezas y componentes fabricados mediante SLM en las instalaciones de IK4 Lortek. Los componentes fabricados se describen por sectores con el objetivo de ilustrar las capacidades y potenciales aplicaciones del proceso SLM.
1. Sector biomédico
Los implantes médicos son una de los nichos de mercado más importantes de la tecnología SLM. Al igual que el cuerpo humano, se trata de piezas personalizadas y únicas. La tecnología SLM tiene un gran número de ventajas en esta aplicación entre las que destacan: la posibilidad de fabricación de formas complejas y personalizadas, la inmediatez en el desarrollo de una solución (a partir de una tomografía de la zona a reconstruir se puede diseñar a medida un implante), la reducción del tiempo y de las complicaciones quirúrgicas (se puede ajustar el implante en modelos antes de la operación sobre moldes o esqueletos fabricados en polímero a partir de la zona a reconstruir) y la posibilidad de fabricación de estructuras ligeras y graduales con una mayor compatibilidad biomecánica, confort y osteointegración.
IK4 Lortek ha trabajado durante los últimos años en el desarrollo de implantes y prótesis maxilofaciales (coronas y puentes dentales, reconstrucción de mandíbula), para traumotología (rodilla, cadera) y neurocirugía (implantes craneales y de corporectomía). Los trabajos realizados se han llevado a cabo con distintos grupos médicos del hospital de Basurto. Para la fabricación de estos implantes se ha trabajado con aleaciones cobalto-cromo, titanio y acero inoxidable.
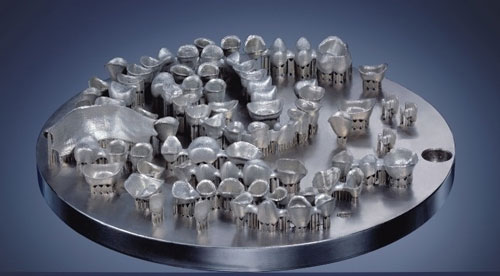
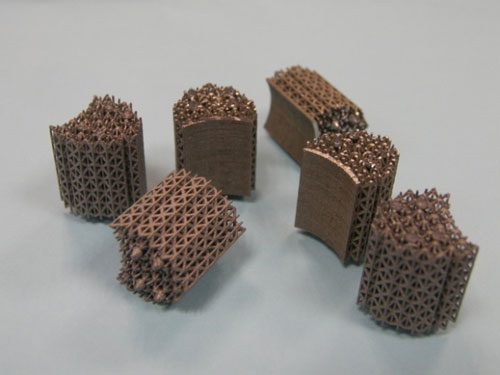
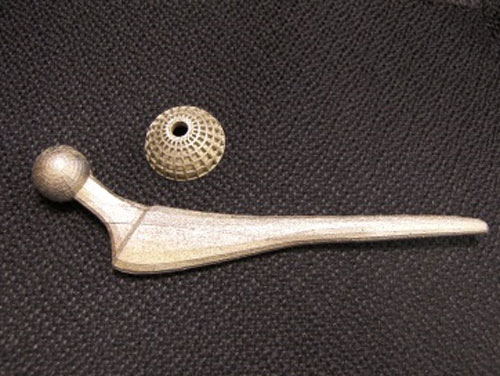
Figura 3: Coronas y puentes dentales, implantes de columna e implante de cadera fabricados por IK4 Lortek.
A parte de los propios implantes y prótesis, la fabricación de instrumental quirúrgico es otra de las aplicaciones de la tecnología SLM. En la siguiente Figura se incluye un detalle de guías de corte y placas de fijación desarrolladas para una intervención de cirugía maxilofacial reconstructiva en IK4 Lortek.
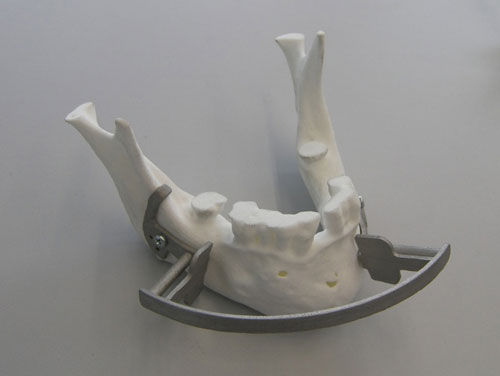
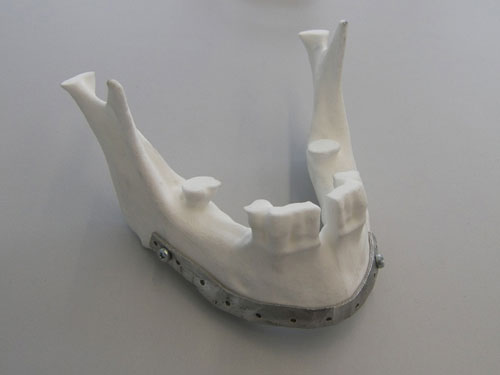
Figura 4: Guía de corte y fijación para cirugía maxilofacial fabricados por IK4 Lortek.
2. Sector molde y matricería
La libertad de diseño que ofrece la tecnología SLM se puede aplicar a la fabricación de insertos y moldes. El objetivo principal de los moldes de inyección y colada es asegurar un enfriamiento adecuado de la pieza. Este enfriamiento depende de la transferencia de calor entre el metal fundido y el molde. Para optimizar este enfriamiento se pueden utilizar componentes fabricados mediante SLM con canales de refrigeración internos que discurran cerca de la superficie. El concepto más habitual es la fabricación de insertos que se colocan sobre bloques de molde prefrabicados. La utilización de estos insertos proporciona una transferencia de calor homogénea (evita el sobrecalentamiento de partes del molde), mejora la calidad superficial de las piezas inyectadas y reduce considerablemente los ciclos de inyección.
IK4 Lortek ha trabajado en el desarrollo de estos insertos para moldes de inyección de polímeros y aluminio.

Figura 5: Insertos para moldes de inyección fabricados por IK4 Lortek.
3. Sectores aeronáutico y automoción
La tecnología SLM permite fabricar estructuras reticulares o de celosía tanto con piel externa como sin piel. Este tipo de estructuras proporcionan un potencial enorme para conseguir un aligeramiento estructural pero hasta ahora era complicado fabricarlas mediante procesos convencionales. Sin embargo, las posibilidades que ofrece la tecnología SLM se están aplicando de una manera cada vez más patente en sectores donde la reducción de peso y el aumento de la relación resistencia frente a peso suponen una ventaja.
En particular en el sector aeronáutico, esta tecnología está suponiendo una verdadera revolución y se están consiguiendo reducciones importantes del peso y de los costes de producción. IK4 Lortek ha aplicado esta tecnología para la fabricación de componentes de instrumentación y motores de aviación en superaleaciones base Níquel del tipo INC718 [8] y titanio (TiAl6V4). En estas aplicaciones además se cuenta con la ventaja de la reducción del volumen de material de partida necesario y de la reducción del consumo de combustible.
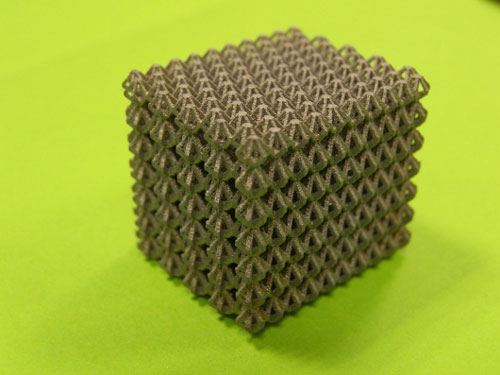
Figura 6: Detalle de estructuras reticulares con y sin piel fabricadas por IK4 Lortek.
El sector de automoción es otro sector donde se están identificando aplicaciones y componentes que se pueden fabricar mediante SLM y que pueden llegar a integrar otras funcionalidades como aislamiento acústico, vibraciones…
4. Sector industria de la ciencia
Por último cabe señalar que la industria de la ciencia es un mercado que demanda soluciones punteras y tecnológicamente avanzadas. La tecnología SLM se está aplicando cada vez más al desarrollo de componentes cuya fabricación mediante tecnologías convencionales es imposible. Con esta tecnología se está dando respuesta a las necesidades de diseño, precisión y funcionalidad esperadas para este tipo de componentes.
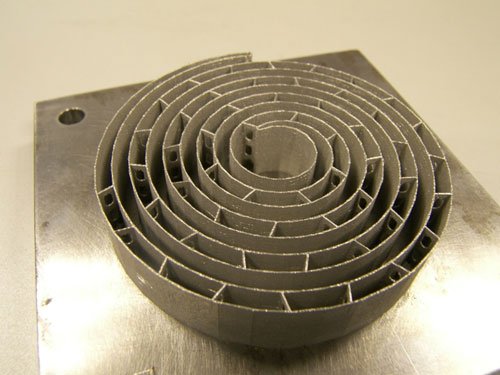
Figura 7: Detalle de un componente para ITER fabricado por IK4 Lortek.
Conclusiones
Las tecnologías de fabricación aditiva en general y SLM en particular, se están volviendo muy atractivas para sectores en los que ya están introducidas como el biomédico, aeronáutico, automoción o molde y matricería. En este trabajo se han presentado varios ejemplos de piezas fabricadas mediante la tecnología SLM para estos sectores. Es de esperar que debido a las ventajas inherentes de este proceso y a los desarrollos que se están llevando a cabo, el número de aplicaciones crezca de manera exponencial en estos sectores y en otros nuevos sustituyendo en parte a los procesos de fabricación convencionales.
Referencias
[1] ASTM F2792-10 “Standard Terminology for Additive Manufacturing Technologies”, www.astm.org: ASTM International.
[3] G. Levy, «The role and future of the Laser Technology in the Additive Manufacturing environment, » Physics Procedia, vol. 5, pp. 65-80, 2010.
[4] J. Kruth, «Material Incress Manufacturing by Rapid Prototying Techniques, » CIRP Annals - Manufacturing Technology, vol. 40, pp. 603-614, 1991.
[5] J. P. Kruth, G. Levy, F. Klocke y T. Childs, «Consolidation phenomena in laser and powder-bed based layered manufacturing, » CIRP Annals - Manufacturing Technology, vol. 56, pp. 730-759, 2007.
[6] T. Wohlers, Wohlers Report 2012 Additive Manufacturing and 3D Printing State of the Industry, Fort Collins, Colorado: Wohlers Associates, 2012.
[7] [Online]. Available: http://www.merlin-project.eu/project/index.jsp.
[8] A. Gibson, D. Rosen y B. Stucker, Additve Manufacturing Technologies: Rapid prototyping to Direct Digital Manufacturing", Springer, 2010.