Análisis del comportamiento de la malla electrosoldada de acero normal frente a la malla romboidal de acero de alta resistencia ante cargas estáticas y dinámicas, para el diseño del solape
Von Rickenbach, G.; Brändle, R. ; Luis-Fonseca, R.; Fischer, G.; y Romero, R., de Grupo Geobrugg; Jarufe, J., de la Universidad de Santiago, Chile; y Cornejo, R., de Grupo Pucobre
26/07/2022Este trabajo presenta el estado del arte en el análisis estático y dinámico de solapes de mallas electrosoldadas y romboidales en rollos, de diferentes calidades de acero, basado en la experimentación realizada por Geobrugg en su Centro de Investigaciones, dejando claramente establecido que la diferencia en las mallas no está solo en los niveles de absorción de energía, sino concluyendo además que en el caso de mallas romboidales de alta resistencia no es necesario el solape, y la transmisión de esfuerzos puede estar totalmente garantizada mediante el empleo de elementos de unión adecuados. Todas estas características, apoyadas en ventajas operativas como el material ligero y la instalación mecanizada, proporciona una mejora considerable en seguridad y productividad, contribuyendo en buena medida al balance económico del proyecto.
Las afecciones al macizo rocoso alrededor de las excavaciones subterráneas ha sido un peligro importante en las minas y túneles. La dilatación de la roca genera pandeo que debe contenerse antes de que cause daños al equipo o problemas de seguridad para los trabajadores de la mina. En minas sísmicamente activas, la ocurrencia de desprendimiento de rocas ha sido ampliamente reconocida como uno de los peligros más importantes en minas y túneles profundos. Si bien existe una amplia gama de casos en los que el peligro de desprendimiento de rocas se puede mitigar a través de secuencias de excavación específicas, procedimientos de reingreso o zonas de exclusión, todavía hay muchas situaciones en las que pueden ocurrir grandes desprendimientos de rocas inesperados, confiando únicamente en el soporte del terreno como la última medida de mitigación, para controlar la seguridad y evitar pérdidas en la producción. Teniendo en cuenta las situaciones anteriores, el soporte del terreno usando como paramento una potente membrana juega un papel importante, ya que contiene la roca fallada/expulsada y proporciona un entorno de trabajo seguro para las operaciones subterráneas.
Si bien es cierto que ha habido logros considerables en la mejora de la resistencia de las mallas —alcanzando más de 26 kJ/m² de capacidad de disipación de energía—, todavía falta investigación sobre el mecanismo de solape y la transferencia de carga entre elementos de malla contiguos.
Introducción
Las minas y los túneles se están excavando a mayor profundidad en un entorno de altas tensiones, lo que está íntimamente relacionado con los requerimientos ante cargas, especialmente en la malla que debe unir el sistema de soporte. En este sentido, el comportamiento de la malla tiene su aspecto más débil en el solape, donde el vínculo entre dos paneles contiguos debe estar garantizado para funcionar como un sistema continuo. A pesar de la relevancia del solape de la malla en el rendimiento del soporte, faltan ensayos sobre el comportamiento mecánico de dicha zona de superposición, y la mayoría de las consideraciones de diseño se basan en estudios obsoletos. La relevancia de los solapes entre mallas en la capacidad de soporte y en la economía de las excavaciones se abordan en el presente trabajo.
Soporte del terreno en excavaciones subterráneas
Papel del soporte superficial
El paramento superficial interactúa con los elementos de refuerzo para crear un sistema de soporte de la superficie integrado (Potvin & Hadjigeorgiou 2020). En este sentido, dicho paramento une los elementos de refuerzo para resistir la deformación de la superficie y evitar que los bloques se desprendan o sean expulsados. Si bien el objetivo inicial del paramento del soporte era retener fragmentos de roca suelta entre los pernos, en condiciones de terreno deficientes -acompañadas de grandes tensiones-, la principal función es garantizar la estabilidad, a partir del control de las deformaciones alrededor de los anclajes. En estos escenarios, la malla y los elementos de refuerzo deben trabajar juntos para generar un sistema capaz de controlar estas deformaciones (fig. 1). En última instancia, el papel de la malla es responder al importante movimiento hacia el interior del macizo rocoso que rodea una excavación y transferir la carga al sistema de anclajes (Villaescusa et al. 2013).
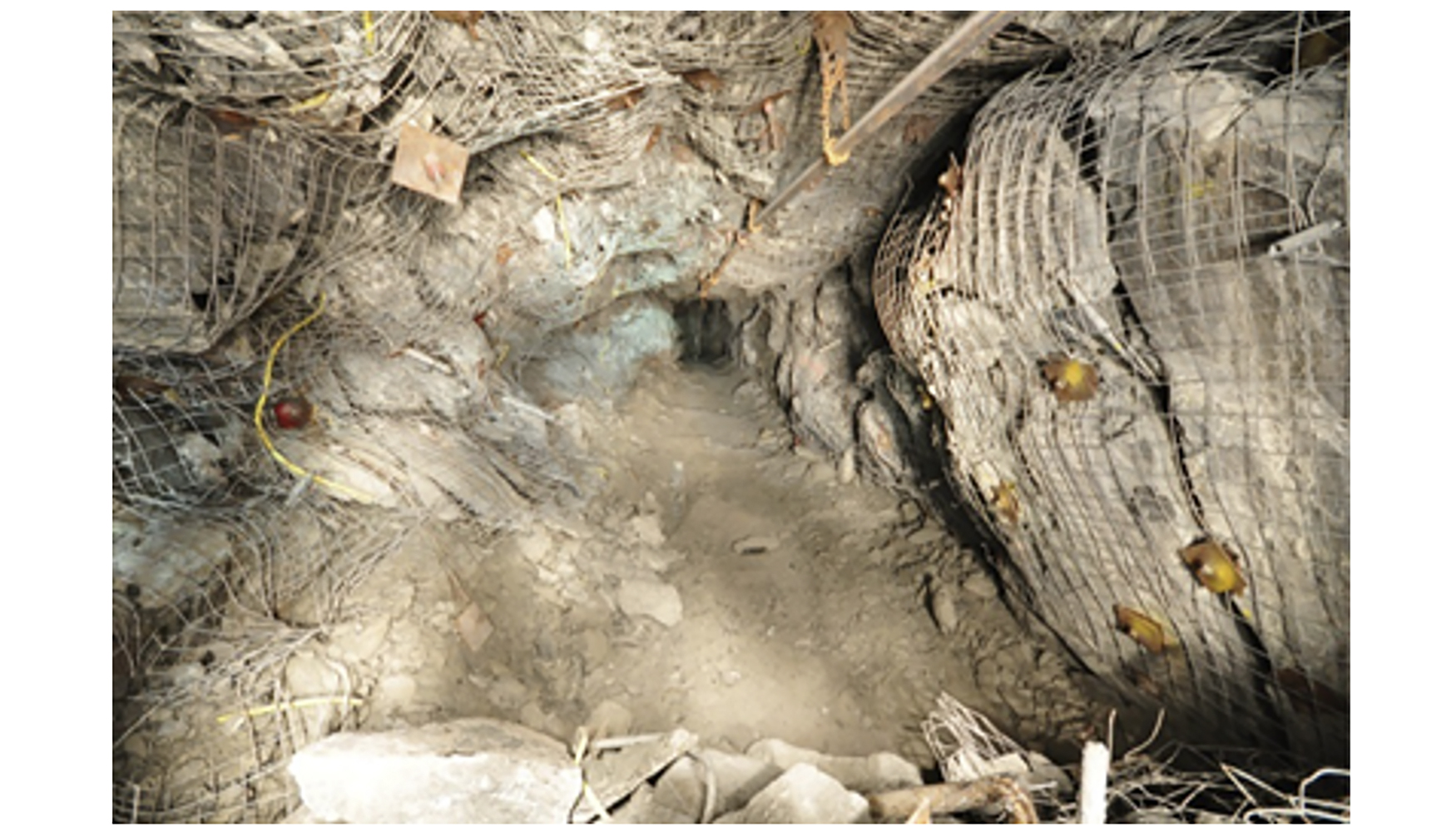
Mallas electrosoldadas y romboidales
Las mallas más utilizadas como parte del paramento en los sistemas de soporte en las minas son la malla de alambre electrosoldado y la malla de alambre de tejido romboidal (fig. 2). La malla electrosoldada corresponde a alambres metálicos unidos ortogonalmente. Esta malla ha sido la preferida en algunas minas debido a su fácil manipulación (Potvin & Hadjigeorgiou 2020).
La malla romboidal de alta resistencia por el contrario, corresponde a una configuración de alambre tejido que permite una mayor capacidad de deformación. Durante muchos años, la malla romboidal ha sido particularmente difícil de instalar debido a su flexibilidad; sin embargo, la instalación mecánica se ha mejorado mucho con el equipo MESHA1, que se puede instalar en cualquier máquina empernadora de dos brazos o jumbo, lo que permite que la malla se desenrolle desde uno de los brazos y el bulonado a las paredes y el techo se ejecute con el otro (Coates 2009, Potvin y Hadjigeorgiou 2020).
Si bien la malla electrosoldada ha evolucionado con cambios en la configuración de los alambres, agregando cordones de alambre al sistema, como la malla de absorción de alta energía (HEA) o agregando dos o más correas de alambre adicionales en los extremos (Louchnikov et al., 2014), la malla romboidal ha mejorado considerablemente el material con el que se construyen los alambres, brindando una alta resistencia a la tracción y al punzonado con muy poco peso, lo que hace que el proceso de instalación sea más eficiente.
1 carrete manipulador que permite la extensión de la malla de forma mecanizada junto con el bulonado
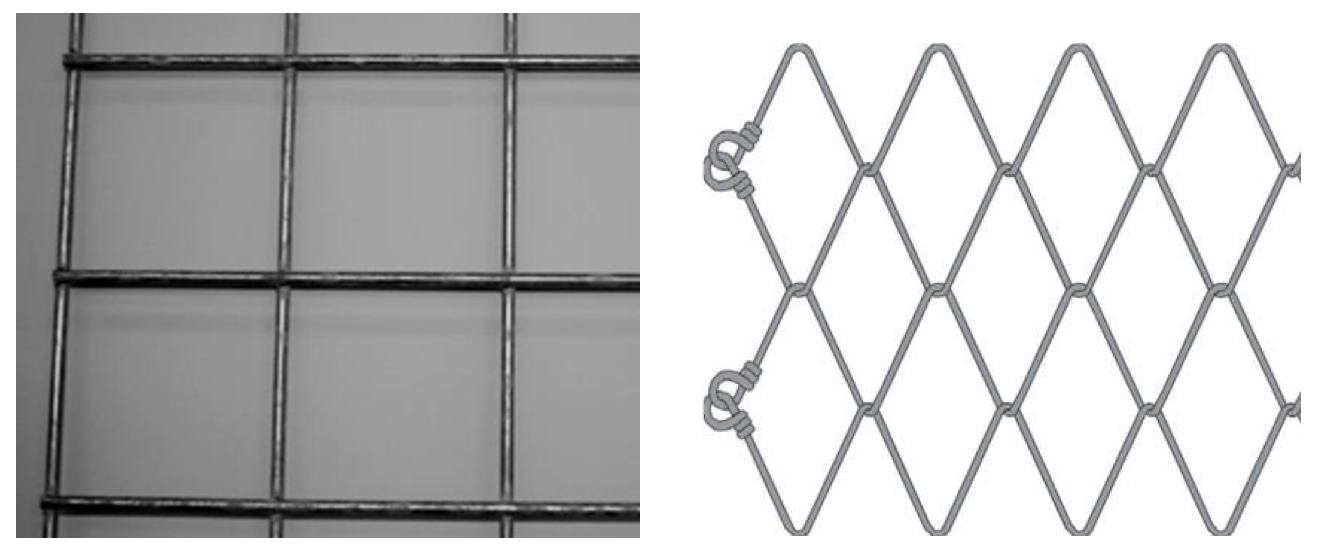
Eriksson 2020 describe una serie de ensayos de carga realizadas en mallas electrosoldadas que concluyen que la capacidad de carga de dicha malla es aproximadamente proporcional a la capacidad de tracción del alambre, pero sobre todo a la resistencia de los puntos de unión (soldadura). Se concluyó que la capacidad de carga cae en el rango de 15 a 45 kN en un rango de desplazamiento de 100 mm a 250 mm. La investigación en la Escuela de Minas de Australia Occidental (WASM) realizada por Morton (2007), se centró en los resultados de carga-deformación de la malla para diferentes configuraciones de restricción (fija o atada en los extremos) resultados de desplazamiento de carga para mallas romboidales y electrosoldadas, donde se puede observar que la capacidad de carga de la malla romboidal es mucho mayor.
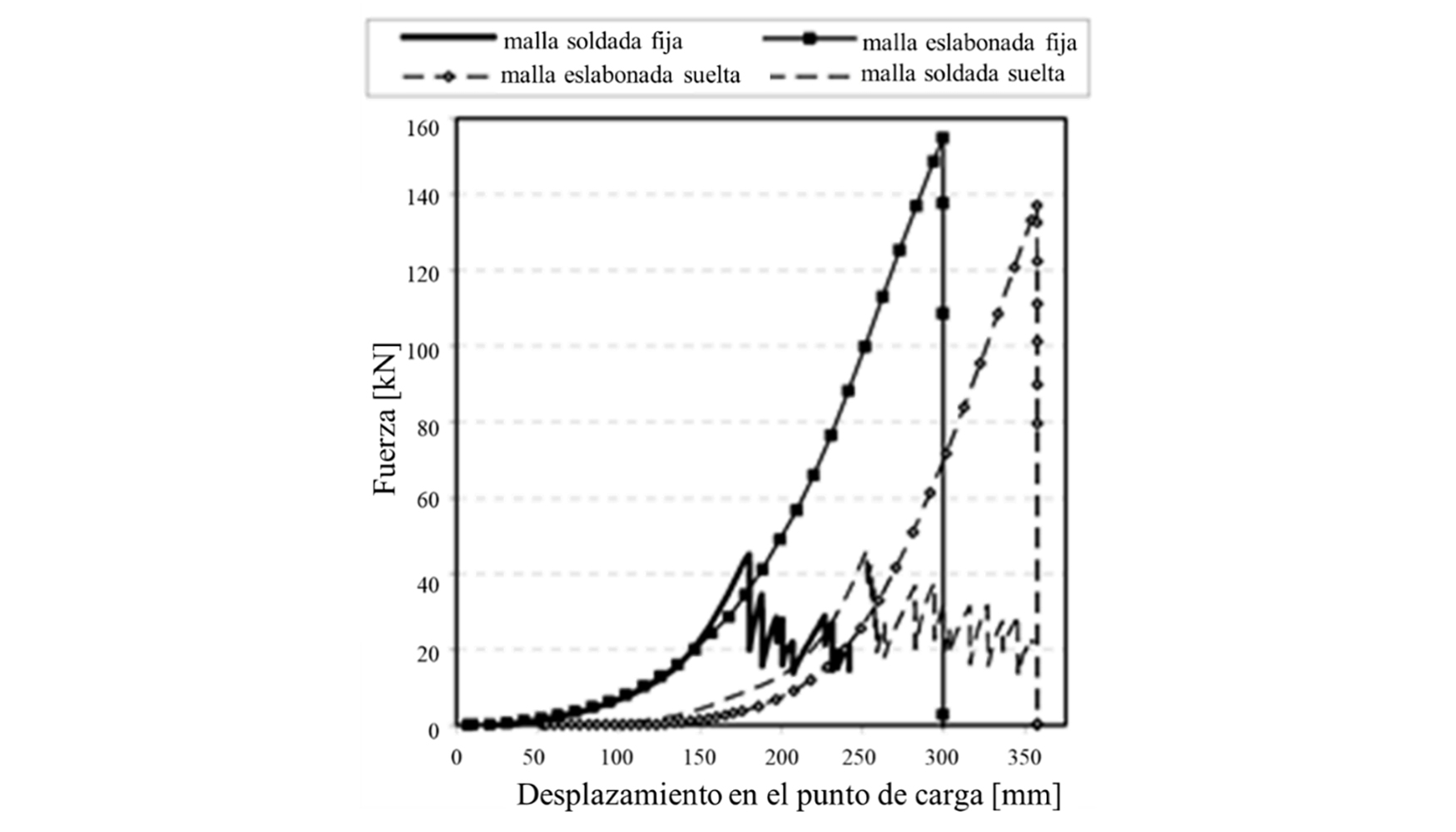
Ensayos de campo a escala natural al solape entre mallas
Malla electrosoldada de acero estándar 100 x 100 x 5,6 mm
Como las zonas de solape pueden ser áreas críticas dentro del sistema de soporte del terreno, cuando se trata de un evento de desprendimiento de rocas, es necesario comprender su comportamiento y la influencia que ejercen en el rendimiento. Para investigar esto, se han realizado dos ensayos de campo diferentes a escala natural y varias pruebas de laboratorio.
El 28 de febrero de 2020 se realizó un ensayo 1:1 en el campo de pruebas de Walenstadt, Suiza, para realizar un ensayo de impacto sobre un soporte del terreno simulado. El sostenimiento del terreno consistió en una losa de hormigón de 100 mm reforzado con fibras estructurales sintéticas, malla de alambre electrosoldado de 5,6 mm con una resistencia a la tracción mínima de 500 MPa y una abertura de 100 mm en ambos sentidos. La malla se instaló fuera del hormigón y dos paneles de malla se solaparon en el medio con 3 aberturas. El conjunto ha sido soportado por 9 pernos tipo Posimix, inyectados con resina en tubos de acero. Se instalaron 3 de los pernos Posimix en el solape de la malla que soporta ambos paneles de malla. El perno central atravesaba el bloque de hormigón de ensayo, garantizando el perfecto guiado a la zona de estudio, y el impacto directo en su área de influencia (fig. 4).
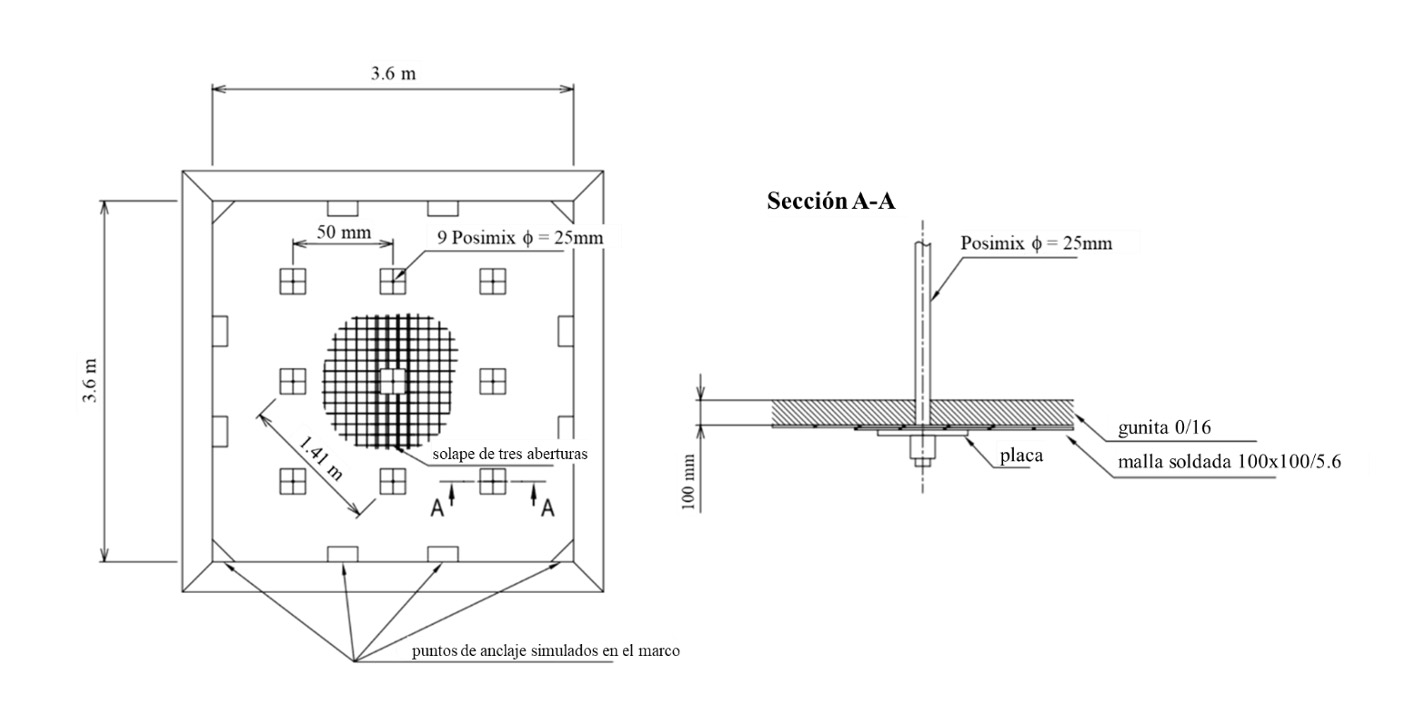
Figura 4. Detalles en planta y alzado de la configuración de ensayo en Walenstadt (100 x 100 x 5,6 mm).
El ensayo consiste en dejar caer un bloque de 6.280 kg sobre el soporte del terreno simulado desde una altura de 0,90 m (ensayo 01) y de 1,00 m (ensayo 02) para alcanzar energías de impacto entre 55 y 62 kJ. Para el ensayo 01, el bloque quedó sujeto por el soporte simulado, pero la malla de acero se rompió y el perno central falló (figs. 5 y 6).
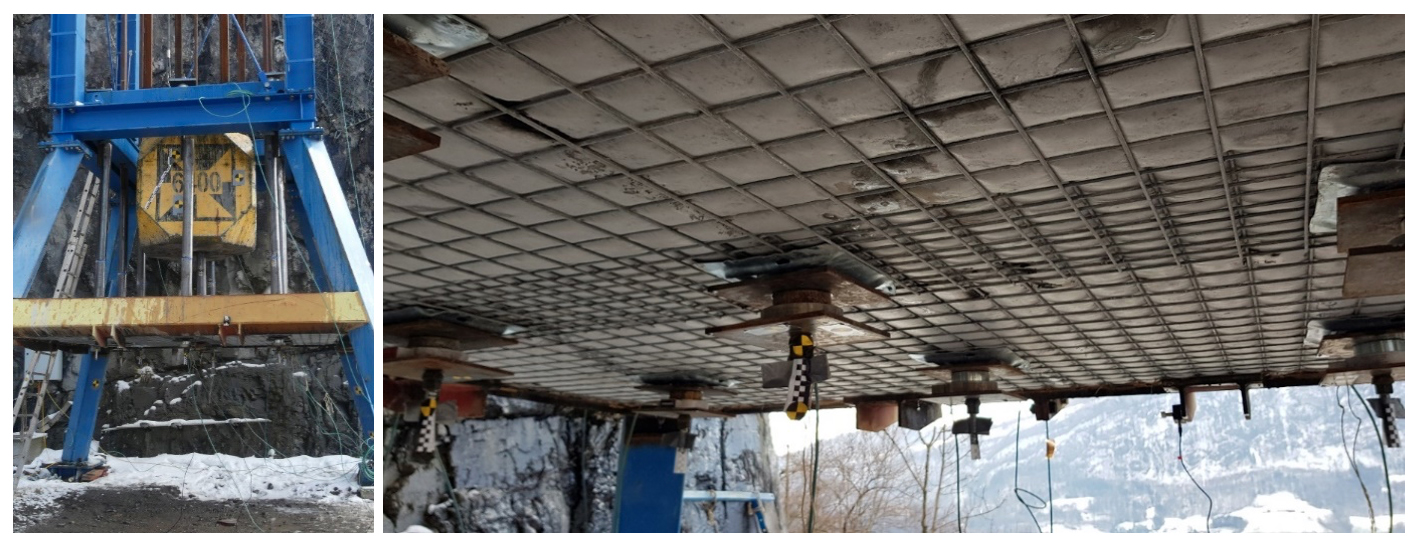
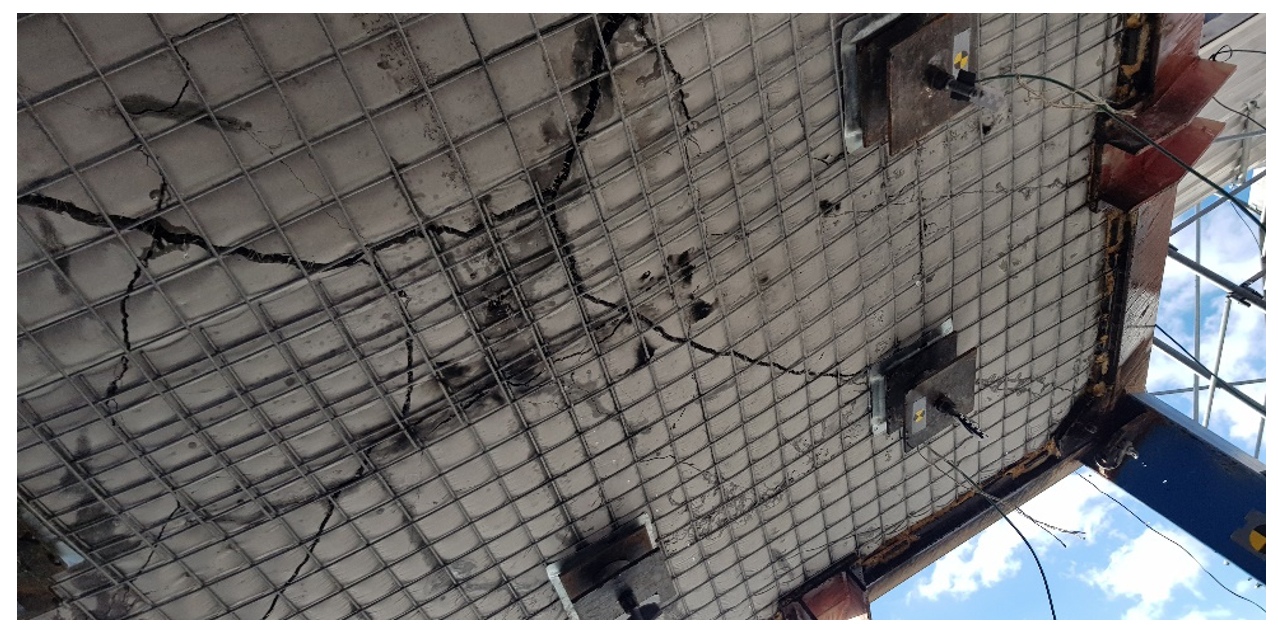
En el caso del ensayo 2, el bloque no fue soportado por el sistema y atravesó el conjunto de malla y losa de hormigón.
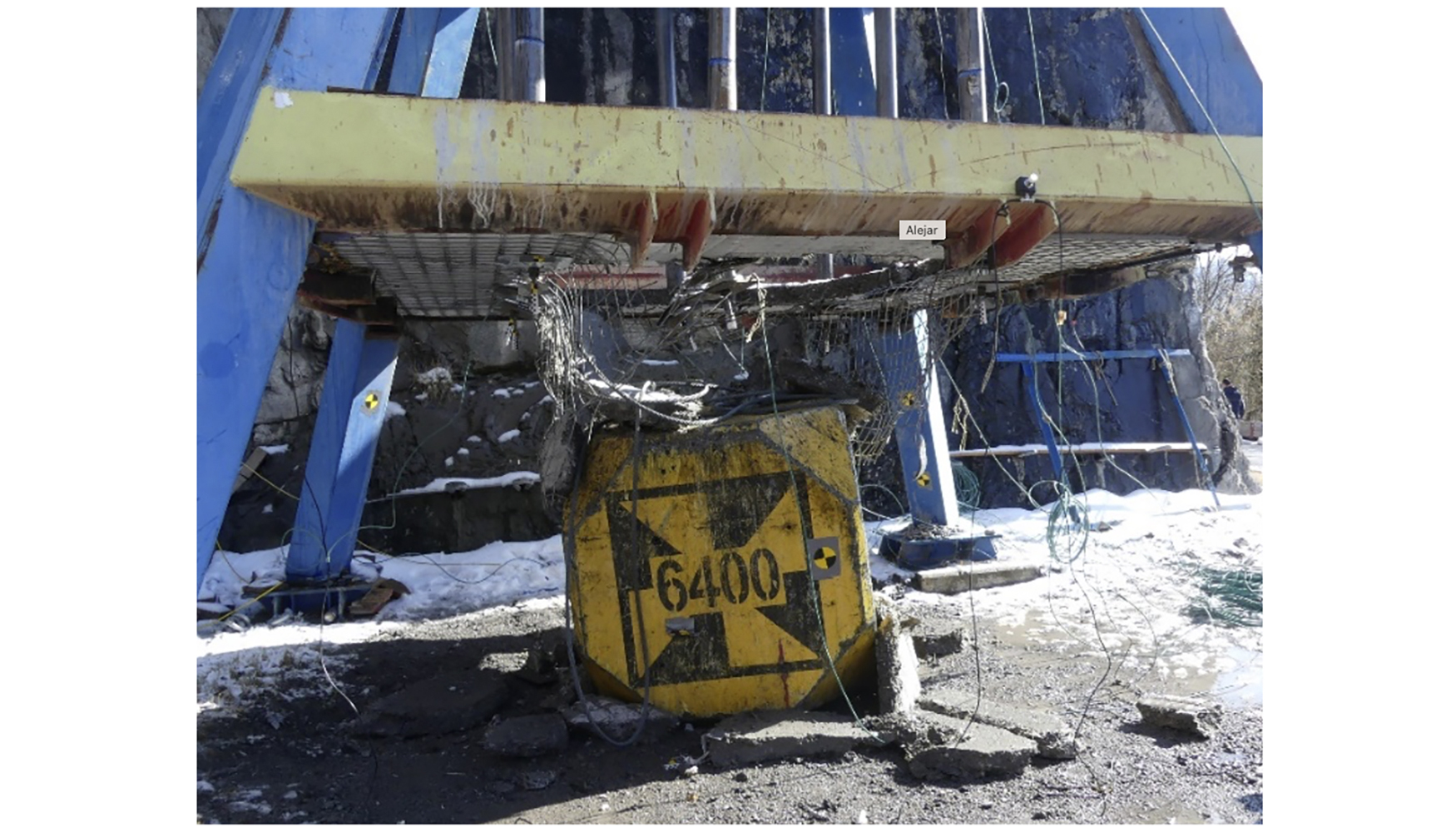
Malla romboidal de alta resistencia MINAX 80/4.6
El 13 de marzo de 2020 se realizó un segundo ensayo de campo a escala natural en Walenstadt, Suiza, sobre la misma losa de hormigón de 100 mm de espesor reforzado con fibras estructurales sintéticas, reemplazando la malla electrosoldada por malla romboidal tipo MINAX 80/4.6 con una resistencia mínima a la tracción de 1.770 MPa y una abertura del círculo interior de 80 mm.
La malla MINAX 80/4.6 se instaló fuera del hormigón y dos hojas de malla se superpusieron en el medio con 3 aberturas superpuestas. El conjunto fue soportado mediante 9 pernos Posimix, inyectados con resina en tubos de acero. Instalando 3 de los pernos Posimix en el solape de la malla que soporta ambos paños. El perno central atravesaba el bloque de hormigón de ensayo, garantizando el perfecto guiado a la zona de estudio, y el impacto directo en su área de influencia (figs. 8 y 9).
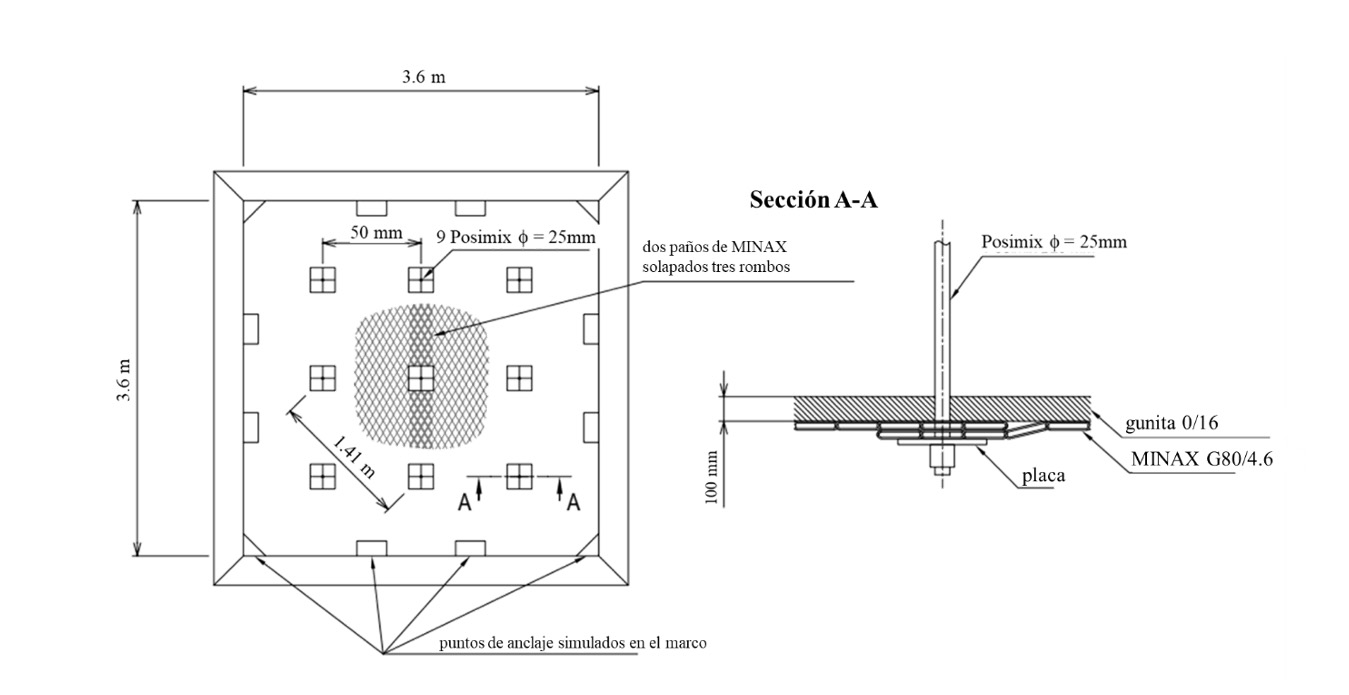
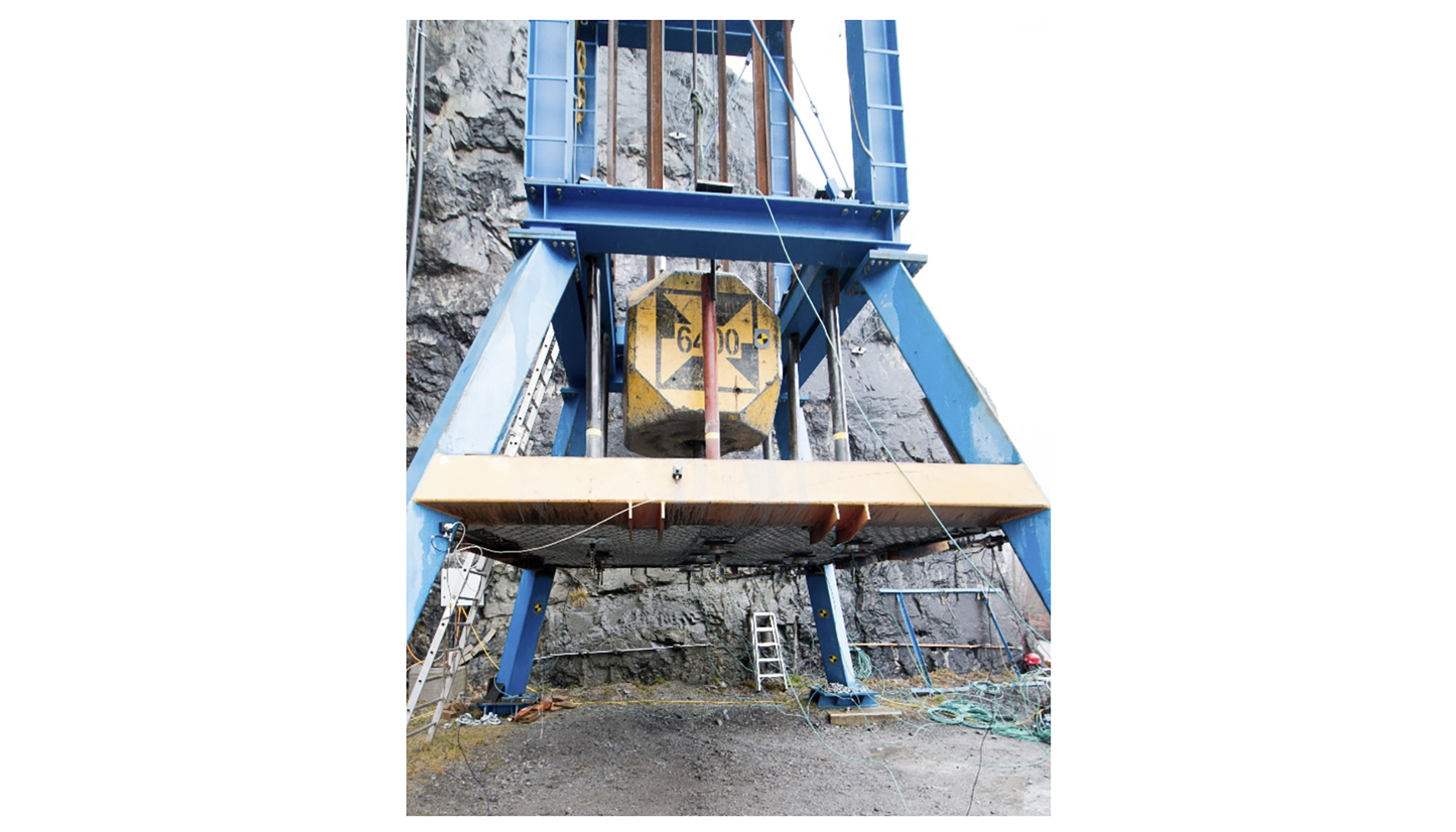
Para los ensayos 01 y 02, el bloque de 6.280 kg se dejó caer sobre el sistema de soporte desde una altura de 0,94 y 0,93 m para alcanzar una energía de impacto de 58 y 57 kJ. En ambos casos el bloque fue retenido. En el ensayo 02 algunos alambres de la malla rompieron, pero el bloque se mantuvo controlado (figs. 10 y 11).
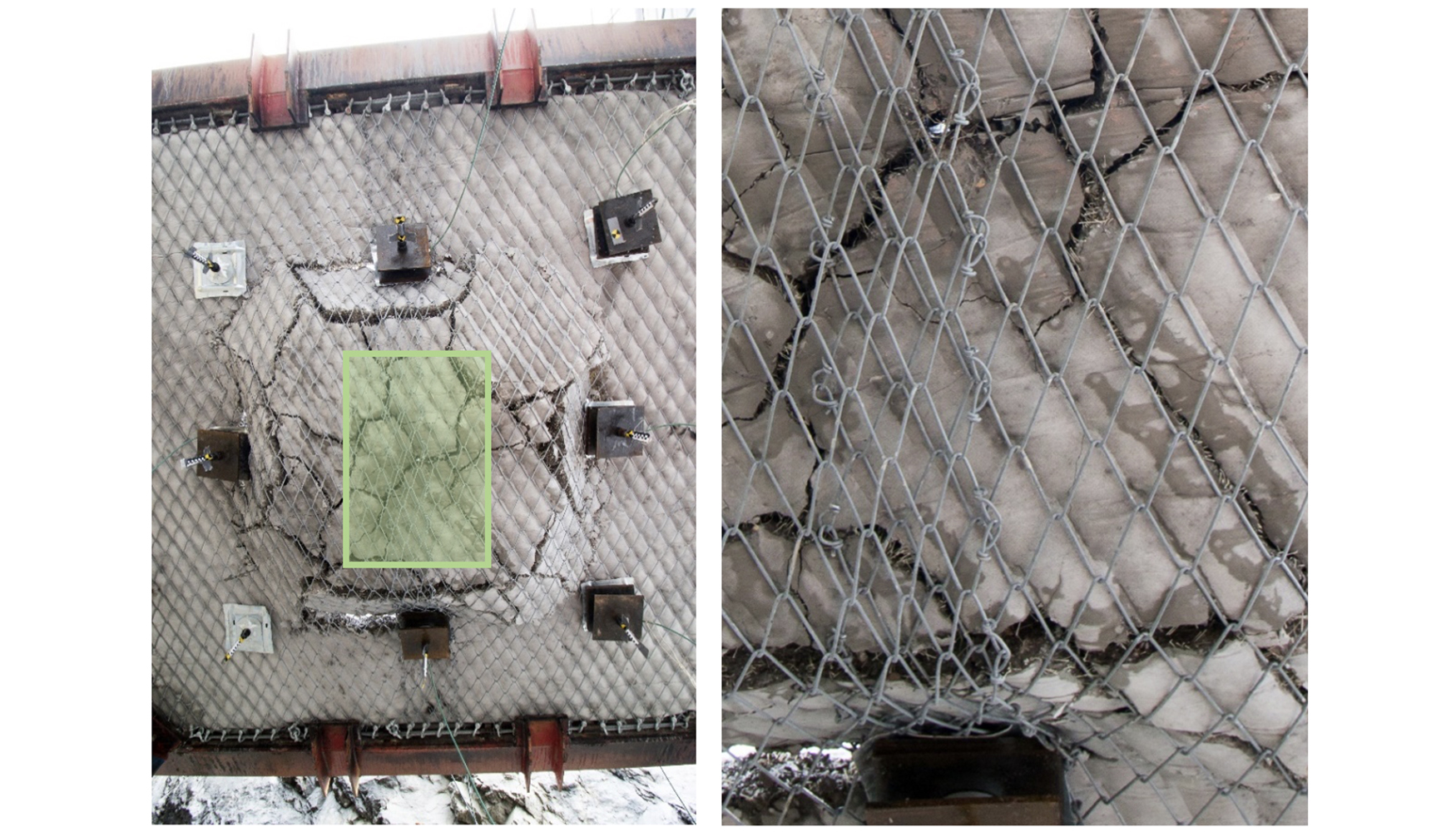
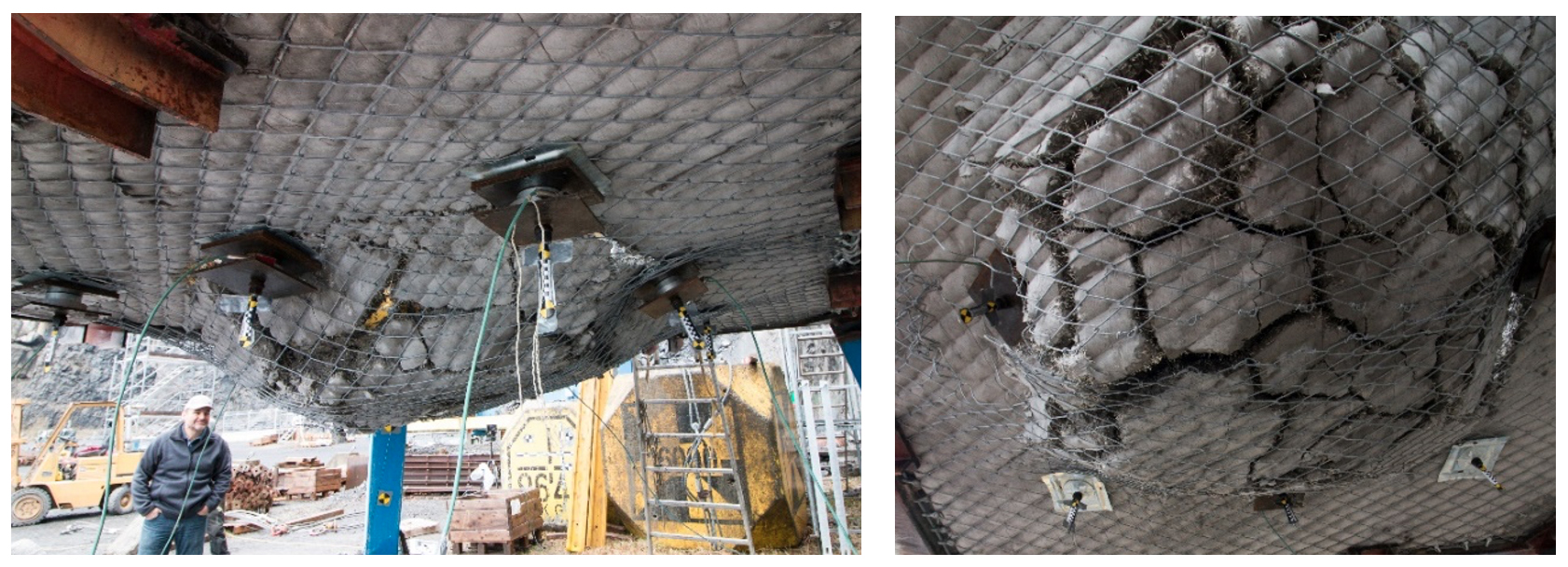
Resultados comparativos de los ensayos de campo
Con los dos ensayos antes descritos se puede calificar cuál fue el comportamiento del sistema con MINAX 80/4.6 en comparación con la malla electrosoldada (5,6 mm 100 x 100) cuando ocurre un evento en una zona de solape. Cómo la malla electrosoldada falló tras el segundo impacto de alrededor de 60 kJ, mientras la MINAX 80/4.6 pudo soportar la carga y absorber y distribuir la energía (fig. 13).
Los datos del acelerómetro mostraron un pico de corta duración para la configuración de la malla electrosoldada durante el impacto del bloque (fig. 12). Esto se puede explicar con la geometría de la malla de soldadura donde los alambres corren rectos y en forma ortogonal y se fijan entre sí en todos los cruces. Por lo tanto, la tensión en los alambres de la malla electrosoldada alcanza los valores de rotura a la tracción con deformación limitada. Mientras los alambres MINAX forman un diamante, que se puede estirar a pesar de que el alambre de alta tensión no es dúctil. Como las espiras de la malla de alta resistencia son flexibles, la MINAX amortigua y disipa la energía del impacto.
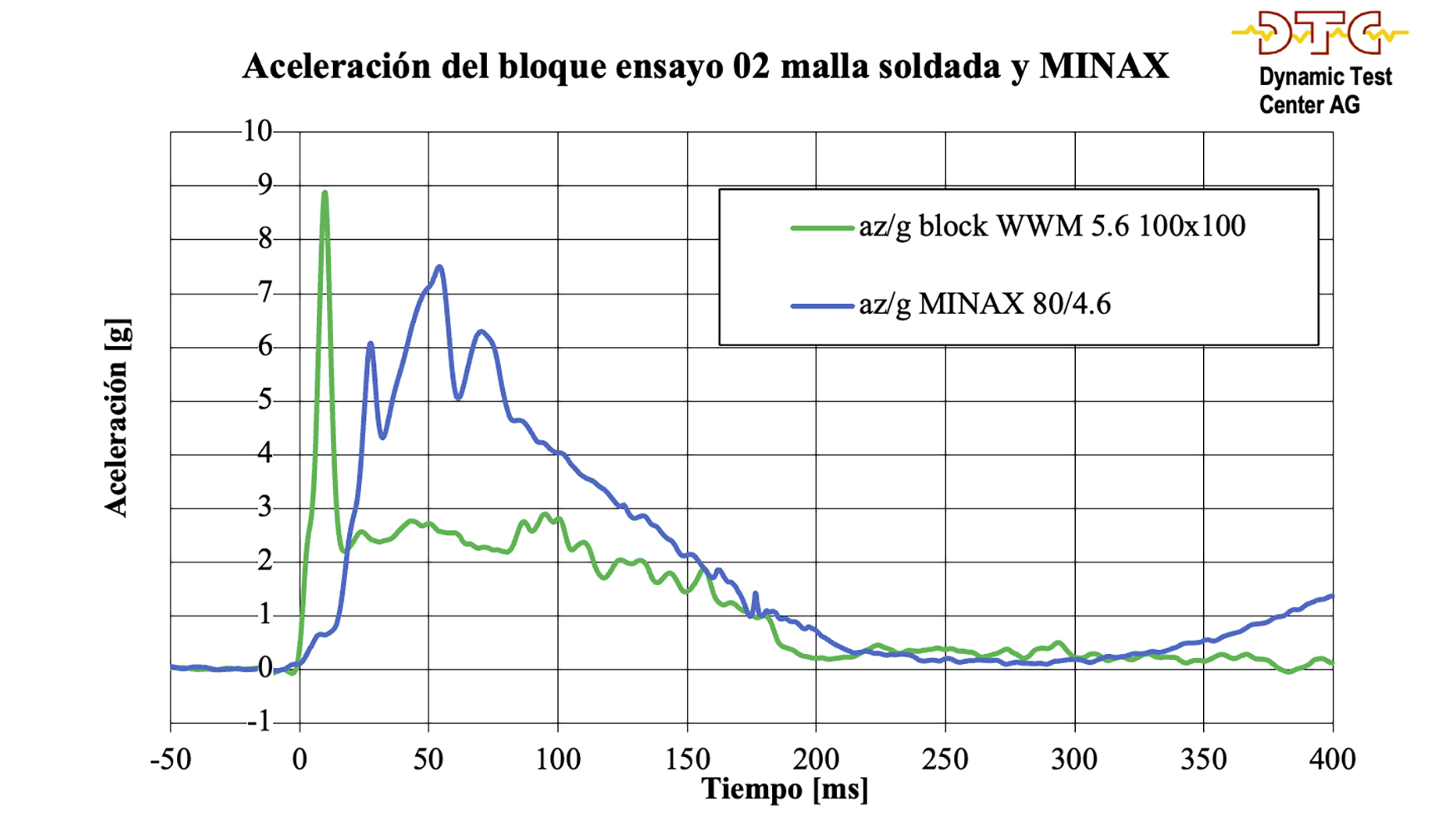
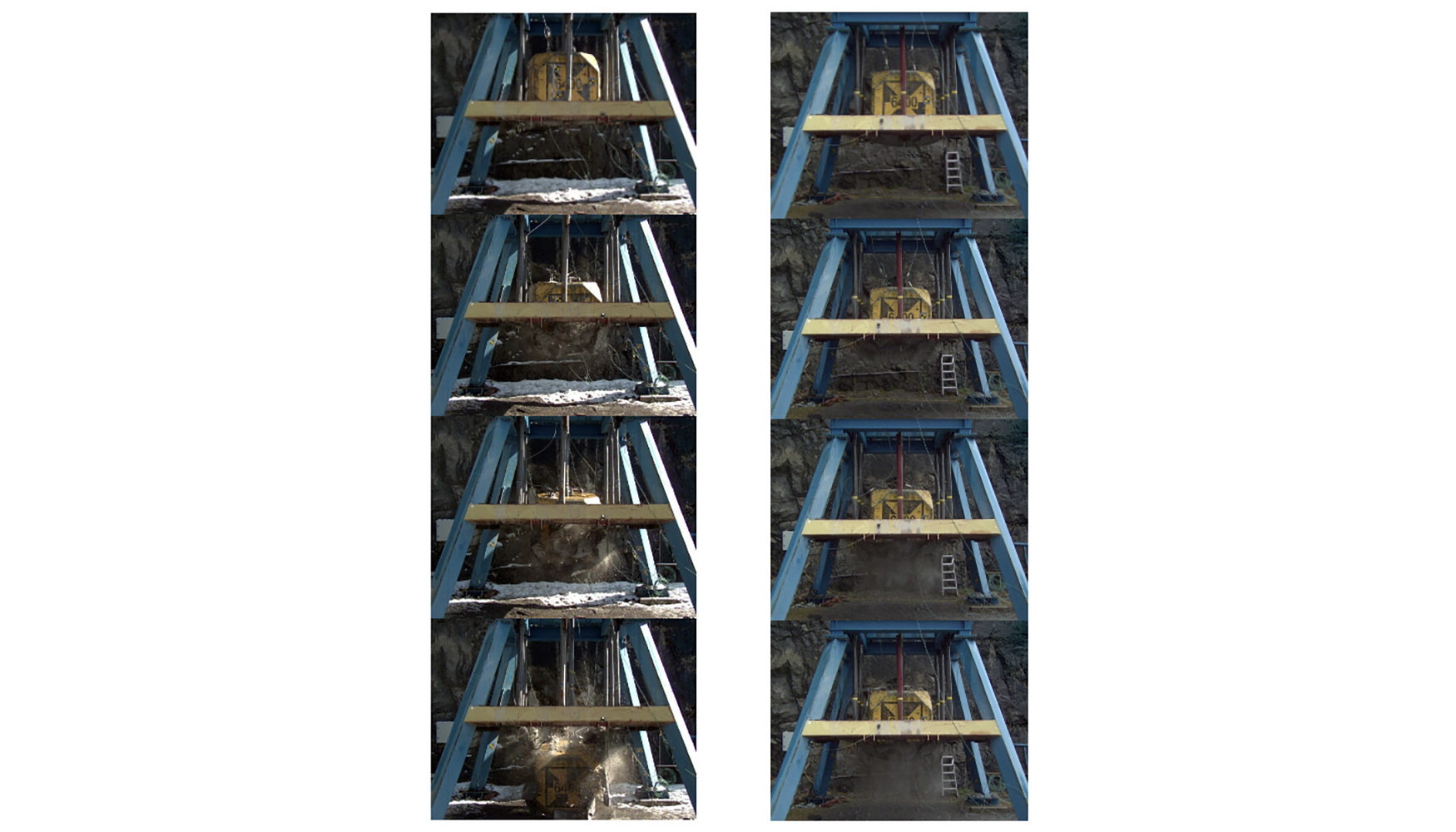
Ensayos de laboratorio realizados a mallas romboidales de alta resistencia
Es importante que el sistema de soporte garantice el trabajo eficiente de las mallas que permita la distribución de los esfuerzos dentro del patrón de pernos. Sin duda, una de las propiedades más importantes de estas membranas es la resistencia a la tracción. Las mallas aquí referidas están compuestas por un tejido homogéneo de espirales de alambre de acero de alta resistencia (> 1.770 MPa), es decir, están fabricadas de un solo material en toda su superficie.
Para garantizar la transmisión de esfuerzos de un paño a otro en ambos sentidos se utilizan elementos de conexión (cables, grapas de conexión o espiras de la propia malla).
A continuación, se realiza un análisis de los resultados obtenidos en ensayos de laboratorio de resistencia a la tracción según el procedimiento descrito en el anexo B de la norma EAD 230025-00-0106, para mallas romboidales de alta resistencia de dos aperturas, en diferentes condiciones de conexión, para comprender la supuesta función que cumple el llamado solape.
Según el funcionamiento de la malla romboidal enlazada se definen dos direcciones, la principal es longitudinal (perpendicular al eje del rollo, que coincide con el avance del túnel) mientras que la secundaria es transversal (paralela al eje del rollo y al avance de la excavación del túnel).
Análisis en la dirección longitudinal
El primero de los análisis se realiza en la dirección longitudinal, se determina la resistencia a la tracción zl [kN/m], el ensayo sobre dos tipos de muestras:
- Una malla continua o dos tramos unidos con una sola espiral de malla romboidal
- Dos secciones de malla conectadas por un cable de acero
La figura 14 y la tabla 1 resumen datos y resultados para mallas MINAX 65/4 y MINAX 80/4 con dos conexiones estándar, costura mediante una espira de la propia malla o mediante un cable acero.
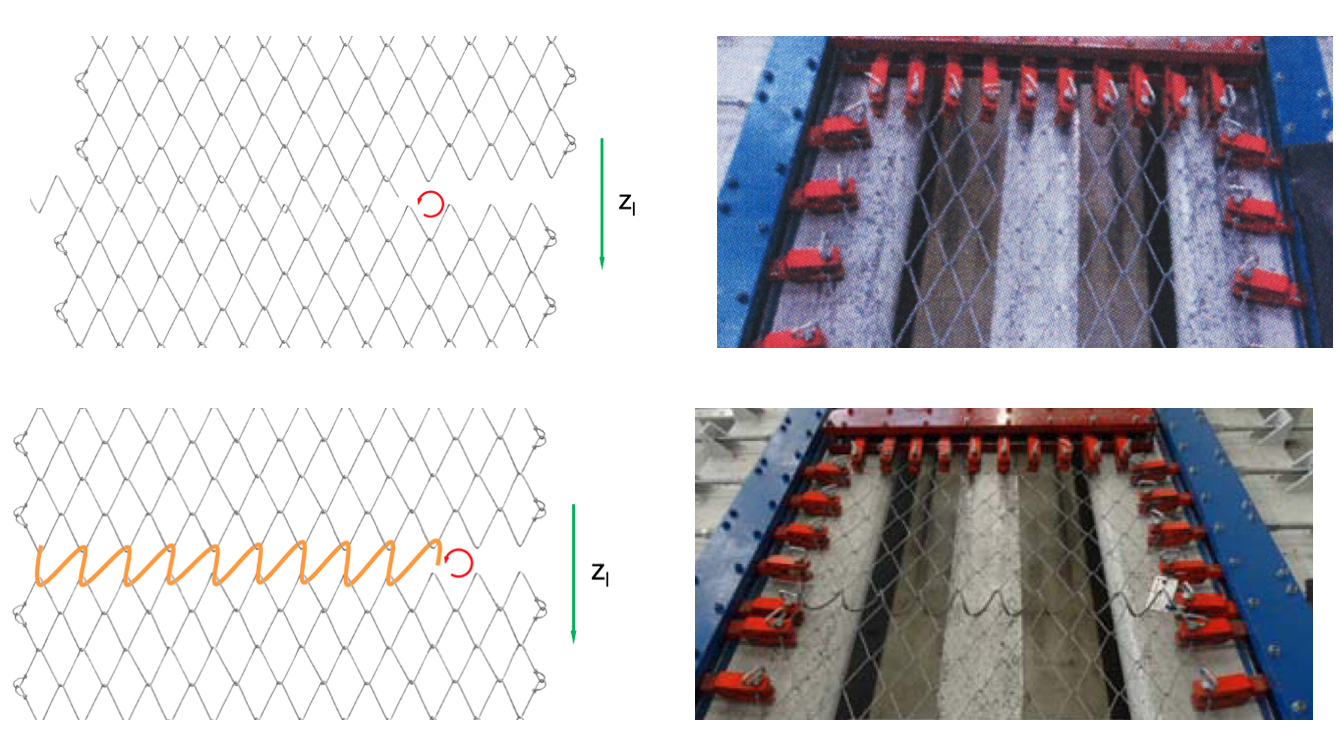
Figura 14. Dos secciones de malla romboidal unidas por espiral (arriba) y por cable de costura (abajo) (Macák 2020, Duricová 2016).
Nº | Nombre | Ancho b [m] | Espirales [un/m] | Conexión |
1,2,3 | MINAX 65/4 | 1,020 | 13 x 10 (transv. x long.) | spiral 65/4 |
4, 5 | MINAX 65/4 | 1,020 | 13 x 10 (transv. x long.) | 6mm [6x7+FE] |
Nº | Nombre | Ancho b [m] | Espirales [un/m] | Conexión |
1, 2, 3 | MINAX 80/4 | 1,005 | 10 x 8 (transv. x long.) | spiral 80/4 |
4, 5 | MINAX 80/4 | 1,005 | 13 x 8 (transv. x long.) | 6mm [6x7+FE] |
Como se puede observar en ambos gráficos (fig. 15), existen dos grupos claros de resultados, los de la derecha con deformación a rotura por debajo de 130 mm (65/4) y 140 mm (80/4), corresponden a las muestras conectadas con cable de 6 mm, mientras que los valores de la malla conectada con una espiral alcanzan la rotura con valores de deformación en torno a los 50 mm (65/4) y 55 mm (80/4), consiguiendo un valor de deformación del orden del 3,1-3,9 % (para el 80% de la carga de rotura) respectivamente.
Los valores máximos de resistencia promedio (284 kN/m y 218 kN/m) se alcanzan cuando se utiliza una espiral de alambre como conexión. Los valores de resistencia se mantienen en 91-94% (260 kN/m – 205 kN/m) cuando se realiza la conexión con cable. Se concluye que la espiral de alambre garantiza la máxima transmisión de los esfuerzos y la mínima deformación. El cable, si bien es efectivo en la distribución de carga, agrega una deformación no deseada.
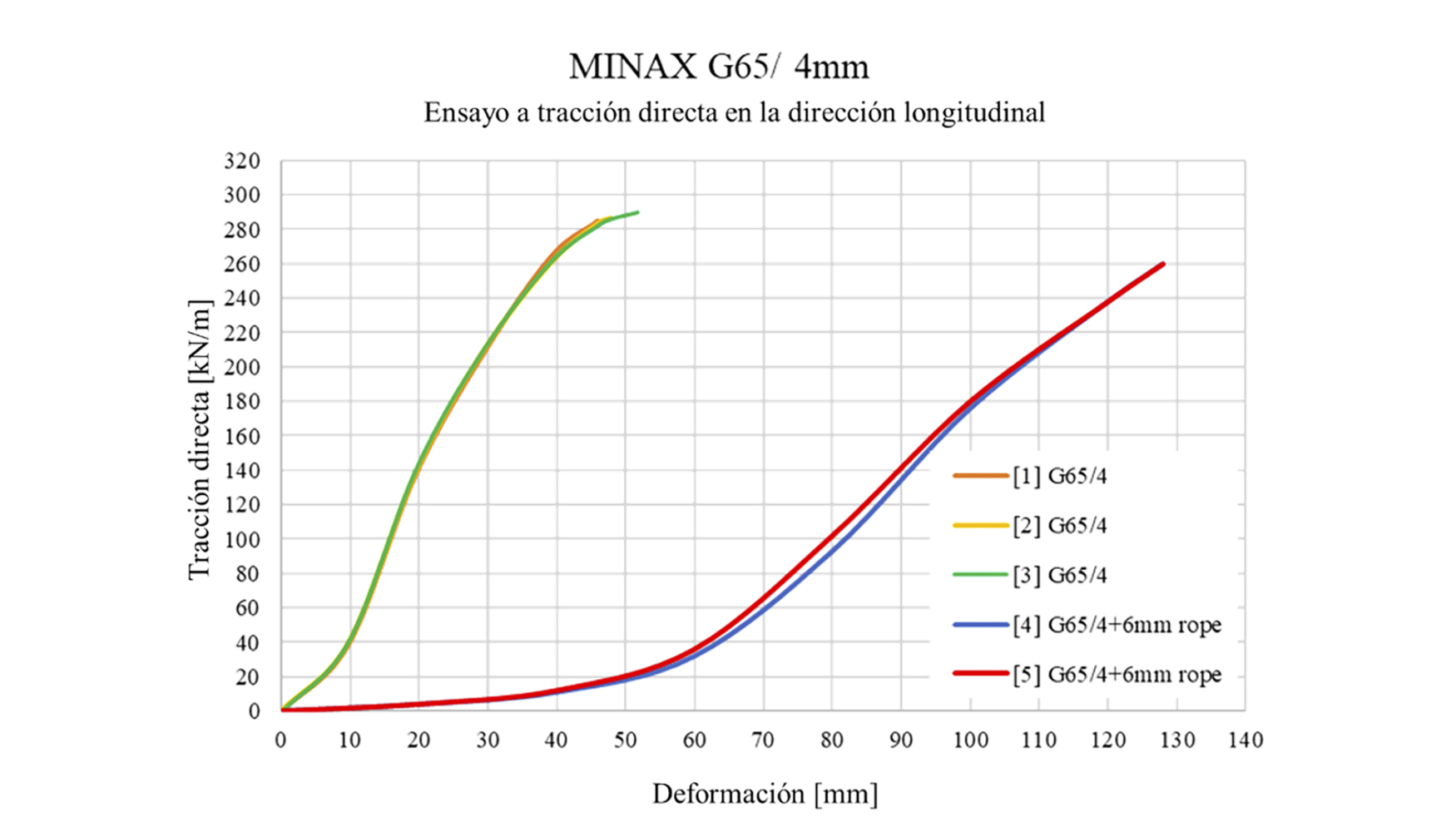
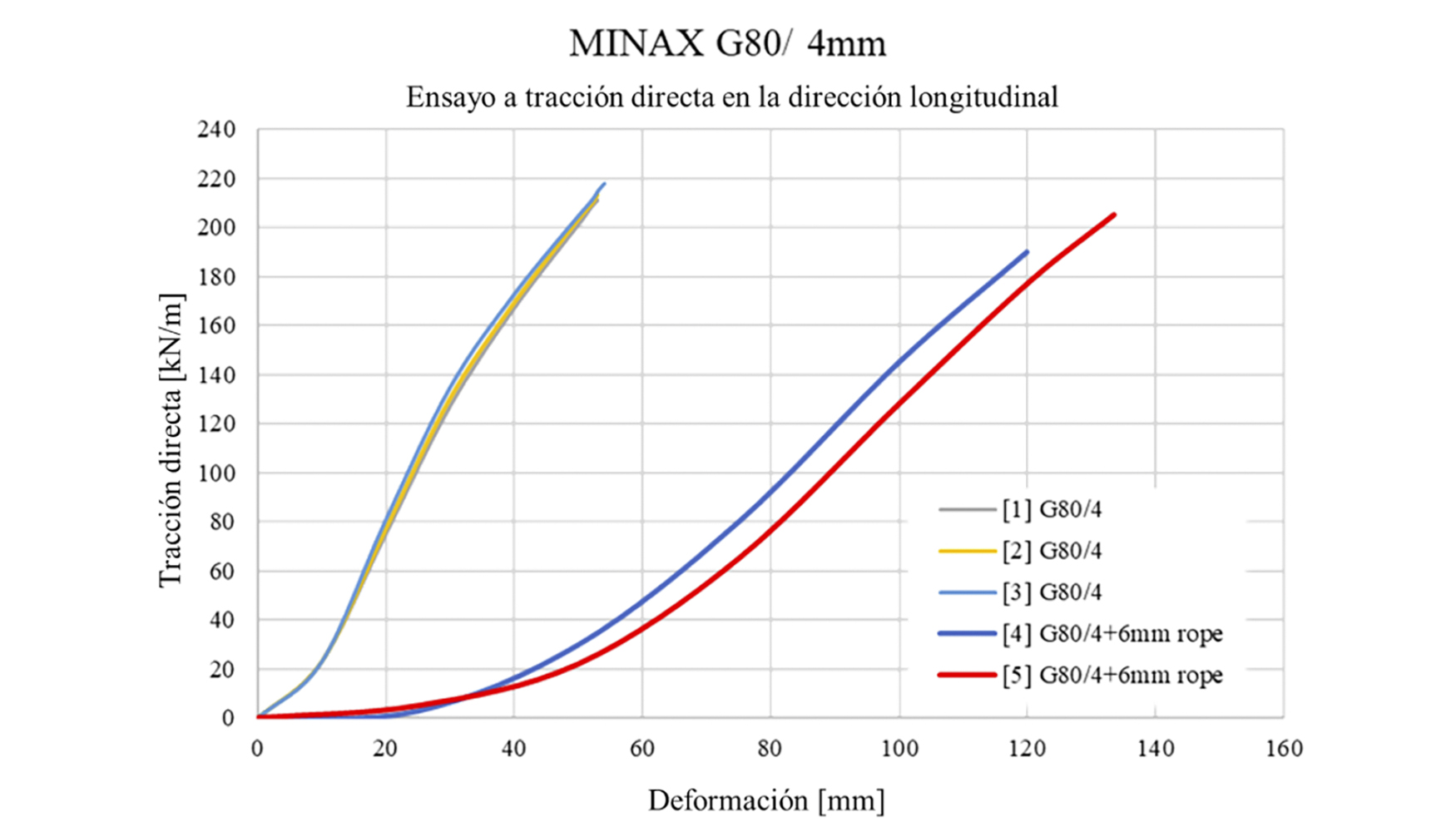
Análisis en la dirección transversal
El segundo análisis se realiza en la dirección transversal. Presupone la unión entre rollos de malla adyacentes (en la dirección de avance), en la que tradicionalmente se realiza el solape. En el laboratorio se determina la resistencia a la tracción directa zq [kN/m], el ensayo se realiza para dos tipos de muestras descritas en la figura 16 y la Tabla 2:
- Dos secciones de malla conectadas por clips tipo T3, 2 clips por diamante (fig. 15 arriba)
- Dos secciones de malla conectadas por una costura de cuerda de acero (fig. 15 abajo)
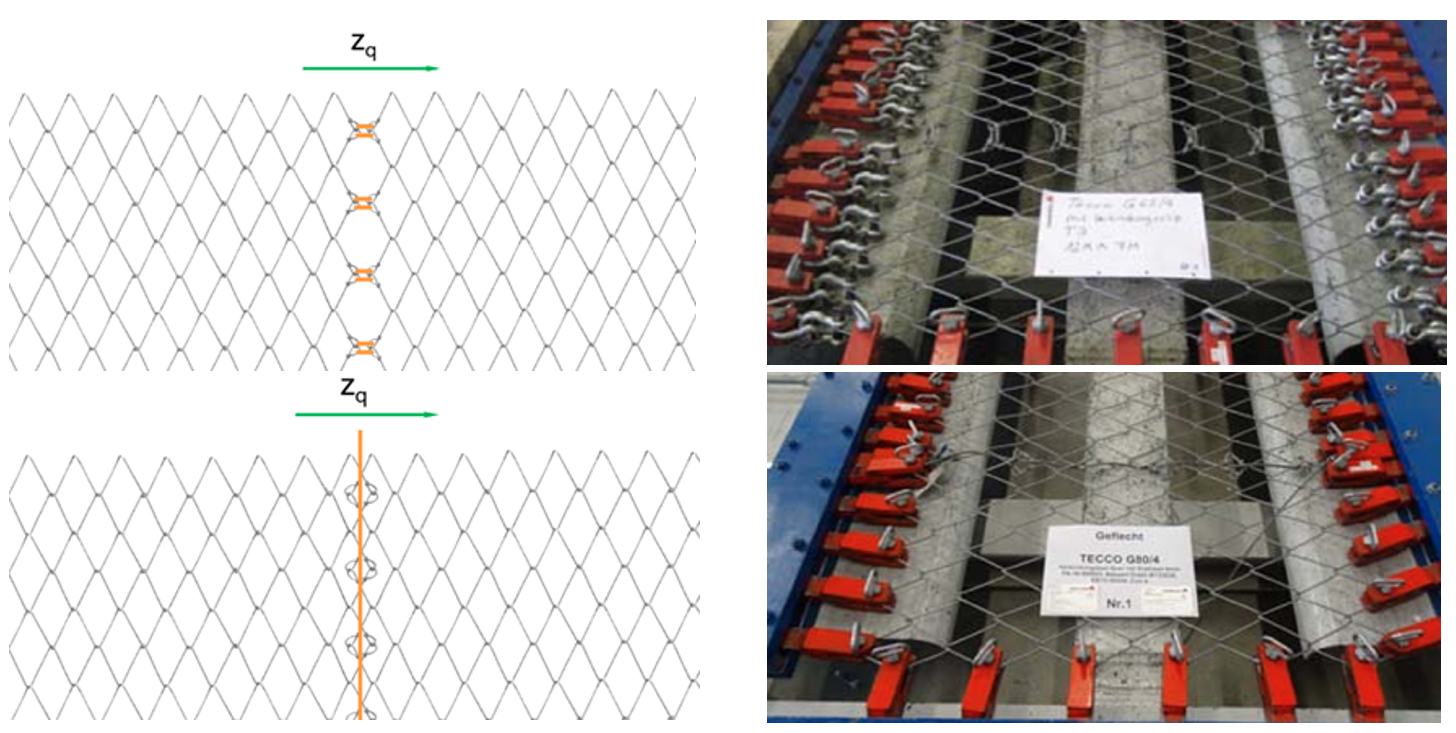
Figura 16. Dos secciones de malla unidas por clips tipo T3 (dos por rombo arriba) y mediante cable (abajo) (Duricová 2015, 2016).
Nº | Nombre | Ancho b [m] | Espirales [un/m] | Conexión |
1, 2, 3 | MINAX 65/4 | 1,070 | 8 x 14 (transv. x long.) | clips T3 (2) |
4, 5 | MINAX 65/4 | 1,070 | 8 x 14 (transv. x long.) | 6mm [6x7+FE] |
La figura 17 muestra los resultados para las dos series de ensayo para la malla MINAX 65/4 con las dos opciones de conexión (clips T3 y cable de costura).
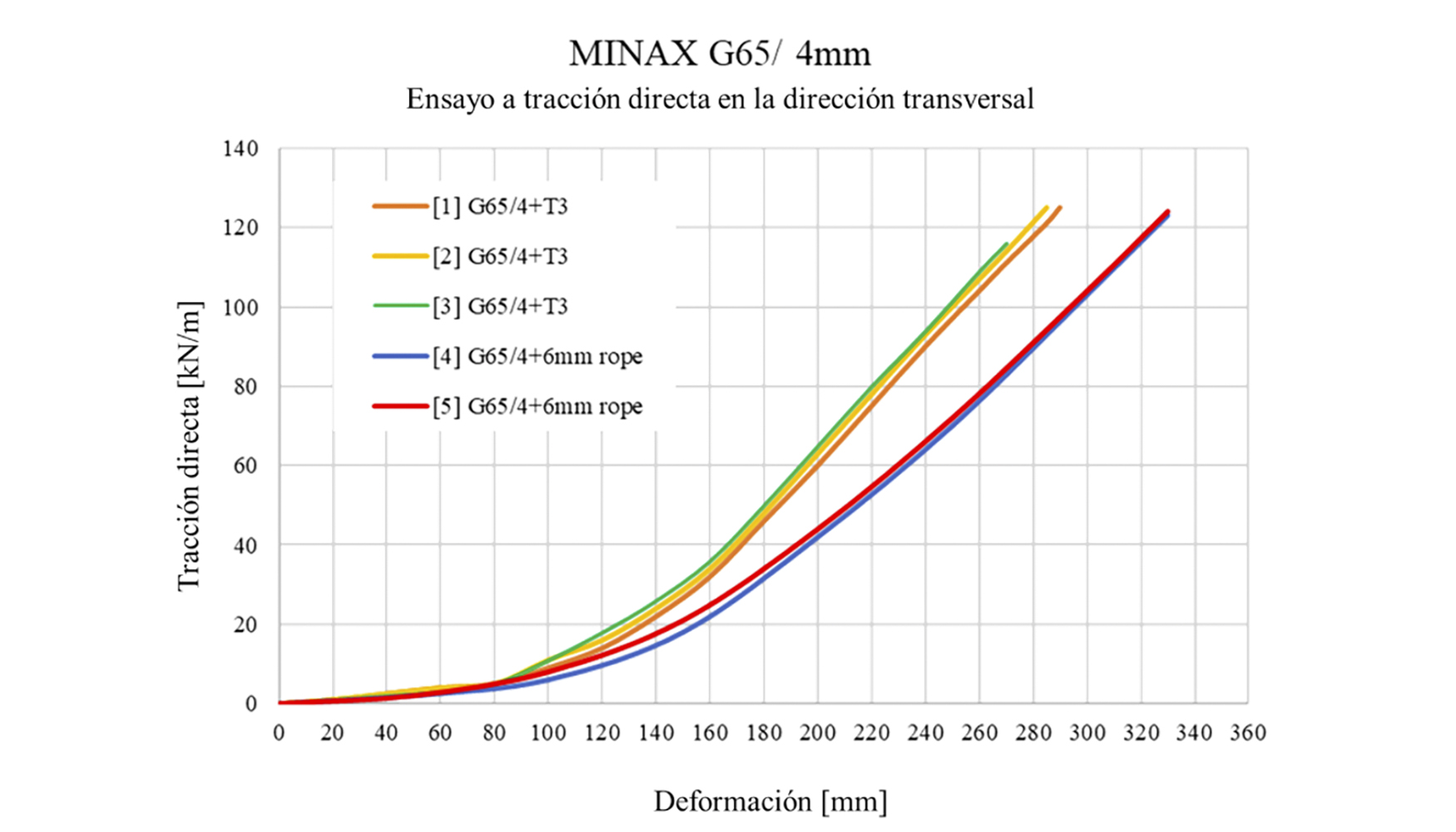
Como era de esperar, la conexión con los clips T3 permite un mayor control de la deformación (290 mm) en comparación con el valor logrado con la conexión con cable de 6 mm (330 mm), alrededor del 88%. Sin embargo, los valores de resistencia a la tracción se mantienen al mismo nivel en ambos casos (125 kN/m).
De estos resultados se puede concluir que con cualquiera de los dos tipos de unión se garantiza la máxima transmisión de esfuerzos, por lo que el solape tradicional no tiene sentido.
Impacto económico del solape
Los procesos en perforación y voladura, así como para aplicaciones TBM, son cada vez más eficientes. Por este motivo, el coste de los túneles se ha reducido. En la figura 18, S. Zare y A. Bruland analizan el costo de la construcción de túneles entre los años 1975 y 2005 para túneles de 60 m2 en Noruega. La conclusión fue que los costos de excavación de túneles se redujeron en un 36%, de 2.582 euros/m en 1979 a 1.572 euros en 2005.
Estudios realizados (Benardos et al. 2013), demuestran que la tendencia a la reducción ha conseguido una asíntota que en los últimos años desciende muy ligeramente por debajo de los 1.000 euros.
Por otro lado, los costos están amenazados por el aumento de la profundidad de los embalses y la dificultad para extraer los minerales. Es por ello que la eficiencia se está convirtiendo cada vez más en un factor clave para la rentabilidad de los proyectos de túneles. En consecuencia, llamaron la atención los elementos individuales para el apoyo del suelo como los pernos, las placas y la malla. Debido a este desarrollo de costos, un análisis de la viabilidad técnica sobre los solapes de malla, así como un análisis de costos adecuado, conducirá a una solución optimizada y a una reducción en el consumo de malla.
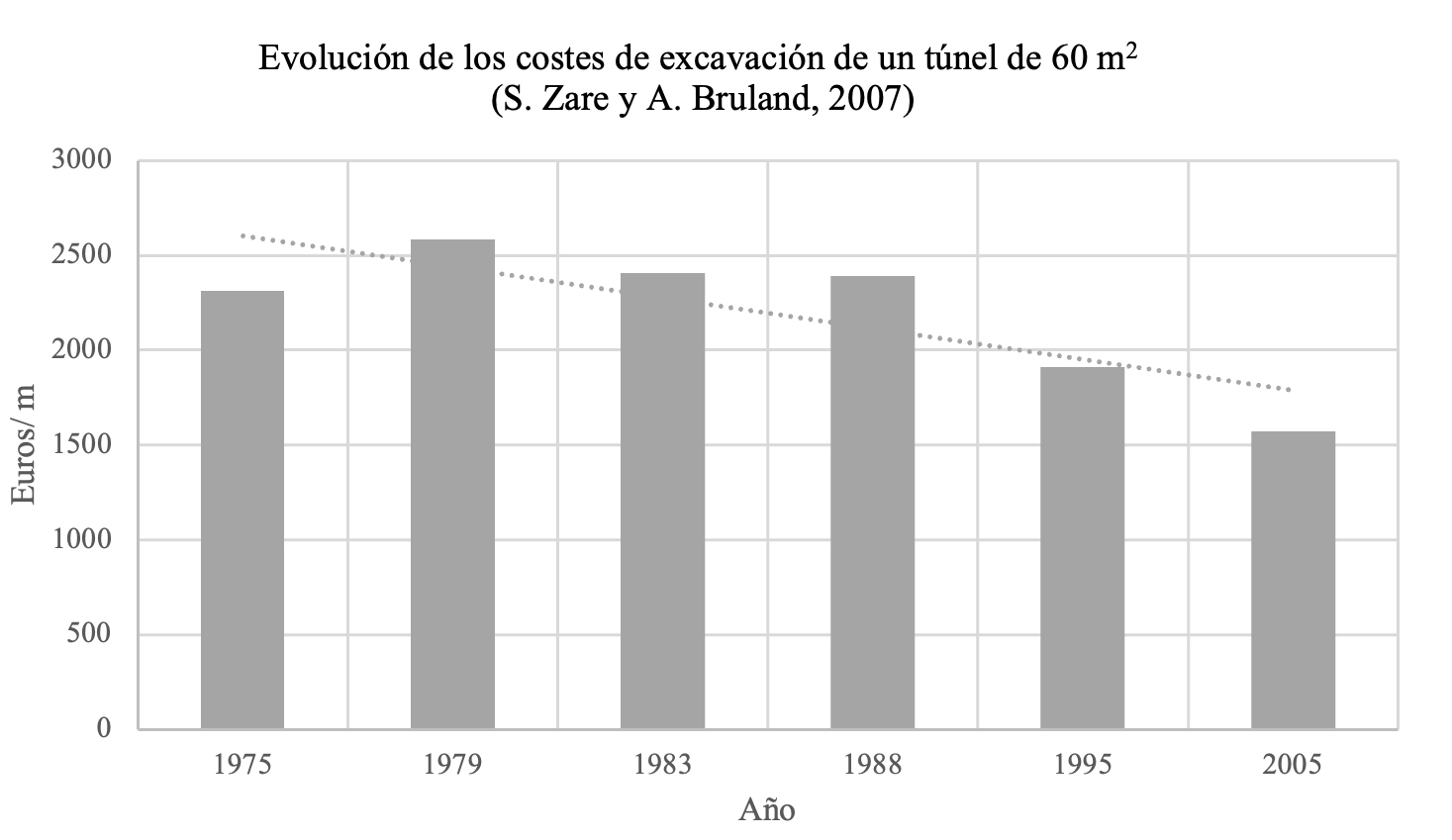
La cantidad de malla utilizada en la construcción de túneles es un factor que afecta el costo total de la excavación. Por lo tanto, una comprensión técnica clara de cuánto solape se necesita para garantizar un soporte del terreno adecuado permite optimizar el empleo de la malla.
Si se considera el costo total por metro lineal de túnel, el costo de la malla como paramento es una parte menor pero vital. En este sentido y sin dejar de lado la importancia del soporte del terreno para la seguridad de cualquier minero, se introduce una tasa de uso de malla en función del ancho de rollo y el solape para garantizar el más alto estándar de seguridad en combinación con la solución más rentable.
Solape 0 | Solape 0 | Solape 0,1m | Solape 0,1m | Solape 0,3m | Solape 0,3m | Solape 0,5m | Solape 0,5m | |
Ancho rollo [m] | Ancho útil [m] | Tasa de uso [%] | Ancho útil [m] | Tasa de uso [%] | Ancho útil [m] | Tasa de uso [%] | Ancho útil [m] | Tasa de uso [%] |
1,0 | 1,0 | 100% | 0,9 | 90,0% | 0,7 | 70,0% | 0,5 | 50,0% |
2,0 | 2,0 | 100% | 1,9 | 95,0% | 1,7 | 85,0% | 1,5 | 75,0% |
2,3 | 2,3 | 100% | 2,2 | 95,7% | 2,0 | 87,0% | 1,8 | 78,3% |
2,4 | 2,4 | 100% | 2,3 | 95,8% | 2,1 | 87,5% | 1,9 | 79,2% |
2,5 | 2,5 | 100% | 2,4 | 96,0% | 2,2 | 88,0% | 2,0 | 80,0% |
3,0 | 3,0 | 100% | 2,9 | 96,7% | 2,7 | 90,0% | 2,5 | 83,3% |
3,5 | 3,5 | 100% | 3,4 | 97,1% | 3,2 | 91,4% | 3,0 | 85,7% |
3,8 | 3,8 | 100% | 3,7 | 97,4% | 3,5 | 92,1% | 3,3 | 86,8% |
3,9 | 3,9 | 100% | 3,8 | 97,4% | 3,6 | 92,3% | 3,4 | 87,2% |
4,0 | 4,0 | 100% | 3,9 | 97,5% | 3,7 | 92,5% | 3,5 | 87,5% |
4,5 | 4,5 | 100% | 4,4 | 97,8% | 4,2 | 93,3% | 4,0 | 88,9% |
En la Tabla 3, la tasa de utilización de la malla se calcula partiendo del empleo de malla romboidal en rollos de alta resistencia. Este tipo de elemento de distribución de carga contribuye a una mayor rentabilidad al requerir menos solape en comparación con los paneles de malla electrosoldada.
El índice se calcula en función del ancho del rollo y el solape previsto. Se toma como referencia el rollo más pequeño de 1 m de ancho, aunque también muestran anchos de rollo de hasta 4,5 m para evidenciar el claro potencial de aumentar la tasa de utilización con rollos más anchos. Los tamaños de rollo estándar según la experiencia oscilan entre 2 y 3,5 metros.
Si se compara la tasa de utilización de malla para un rollo de 2,5 m de ancho, con un solape de 0 m mientras que la conexión se realiza mediante clips (fig. 19) y un rollo de 2,5 m de ancho con un solape de 0,5 m, el ahorro en la reducción del solape será del 20%. Incluso si el solape pudiera reducirse de 0,5 m a solo 0,1 m, se podría lograr un aumento de la tasa de utilización de malla del 80% al 96%.
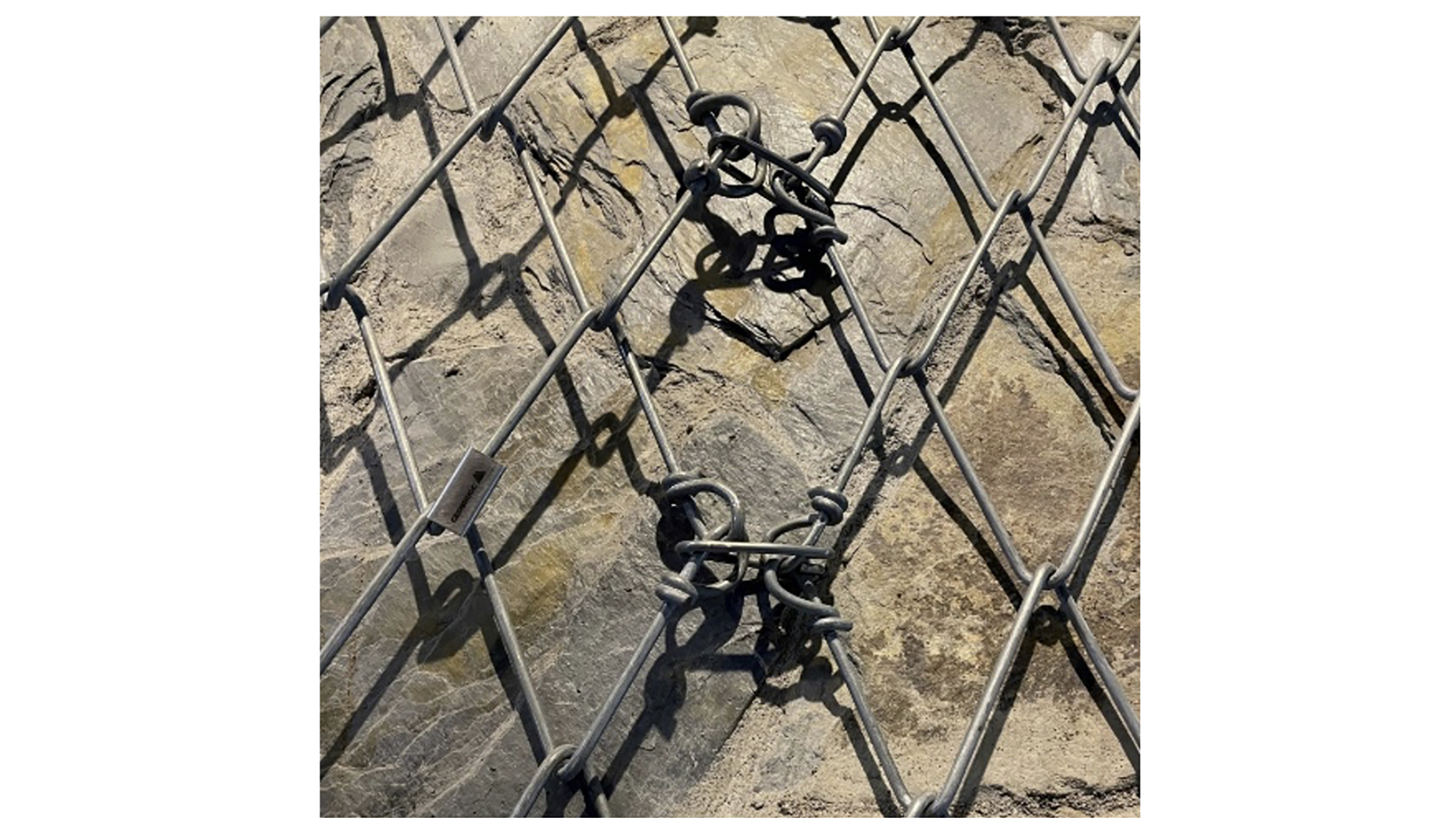
En general, cuanto más anchos sean los rollos, menor será el ahorro real por el efecto de la superposición de mallas, sin embargo por lo general el ahorro en operación podría compensar el material extra correspondiente al área de solape. Si se asume que durante el proceso de perforación y voladura el avance sería de 3,8 m y en lugar de colocar dos rollos de 2,3 m se podría utilizar un solo rollo de 3,9 m con 10cm de solape, el ahorro de tiempo en cuanto a la operación en el túnel se verá recompensado con el costo del solape de mallas. Además, si se considera colocar este rollo de 3,9 m en lugar de dos rollos de 2,3 m o incluso de 2,0 m, se podría eliminar un solape, lo que redundaría en una mayor seguridad en el avance del túnel.
Una optimización en un túnel de 1.000 m de longitud con una sección transversal de 60 m2 podría resumirse como se describe en la Tabla 4.
Ancho rollo [m] | Conexiones [uds.] | 0 | 0,1 | 0,2 | 0,3 | 0,4 | 0,5 | [m] |
2,0 | 500 | 0 | 1081 | 2162 | 3243 | 4324 | 5405 | [m2] |
2,3 | 435 | 0 | 940 | 1880 | 2820 | 3760 | 4700 | [m2] |
2,5 | 400 | 0 | 865 | 1730 | 2594 | 3459 | 4324 | [m2] |
3,0 | 333 | 0 | 721 | 1441 | 2162 | 2883 | 3603 | [m2] |
3,9 | 256 | 0 | 554 | 1109 | 1663 | 2217 | 2772 | [m2] |
4,5 | 222 | 0 | 480 | 961 | 1441 | 1922 | 2402 | [m2] |
En un túnel de 60 m2, donde hay suficiente espacio disponible para maniobrar los rollos, un aumento en el ancho del rollo de 2,0 m a un rollo más ancho de 4,5 m conducirá a una disminución del solape de 500 a 222, lo que supone un aumento significativo de la seguridad. Además, si en paralelo se puede reducir el solape de 0,5 m a 0,1 m, se puede lograr un ahorro total de malla de 4.924 m2. En un caso perfecto, la reducción sería de hasta 0,0 m de solape y la conexión se realizará mediante clips. De todos modos, debido a la sobre excavación en el proceso de perforación y voladura, esto no será factible en la práctica.
Conclusiones
El solape de mallas ha sido identificado por muchos autores, en varias minas, como uno de los puntos más débiles e importantes en el soporte superficial del terreno. La falta de ensayos hasta el momento sobre la transmisión de solicitaciones, en el área de solape, ha generado mucha incertidumbre en el comportamiento de esta interfaz.
Los ensayos realizados en Walenstadt no mostraron una disminución significativa del soporte o la transmisión de solicitaciones de la MINAX 80/4.6 cuando se carga un área con solape. Por otro lado, el ensayo con malla electrosoldada mostró una disminución en la capacidad de soporte en el solape ya que las soldaduras alrededor del área de solape fallan y el solape se abre.
Se necesitarían más ensayos para comprender cuál es la reducción de la capacidad en el área de solape. Esta investigación muestra que el uso de clips para unir paños de malla contiguas es altamente eficiente en términos de resistencia y valor económico en los proyectos.
Los ensayos de laboratorio realizados por Geobrugg han demostrado, por un lado, que la mejor opción para realizar la conexión en el sentido longitudinal es una espiral del propio alambre de alta resistencia, el empleo de cables de conexión es adecuado para la transmisión de cargas pero no lo es desde un punto de vista deformacional. En cambio, en el sentido de avance (transversal), la mejor solución es el uso de grapas de unión tipo T3, que garantiza la transmisión de las cargas sin afectar la deformación.
Ambos resultados permiten afirmar que la distancia de solape, en este tipo de membranas de alta resistencia, es despreciable.
Referencias
- Brändle, R., Rorem, E., Luis, R. & Fischer, G. (2017), 'Full-scale dynamic tests of a ground support system using high-tensile strength chain-link mesh in El Teniente mine, Chile', in M Hudyma & Y Potvin (eds), UMT 2017: Proceedings of the First International Conference on Underground Mining Technology, Australian Centre for Geomechanics, Perth, pp. 25-43, https://doi.org/10.36487/ACG_rep/1710_01_Luis
- Benardos, A. Paraskevopoulou C. y Diederichs, M. (2013) 'Assessing and benchmarking the construction cost of tunnels'. GEO Montreal.
- Duricová, A. (2016) High-Tensile Steel Wire Mesh Tecco G65/4 connected with wire rope of diameter ∅ 6 mm and designation 6x7 + FE, in longitudinal direction. Test report No. 70-16-0035. TSUS. Bratislava
- Duricová, A. (2015) High-Tensile Steel Wire Mesh Tecco G65/4 connected with T3 clips in transversal direction. Test report No. 70-15-0373. TSUS. Bratislava
- Duricová, A. (2016) High-Tensile Steel Wire Mesh Tecco G65/4 connected with wire rope of diameter ∅ 6 mm and designation 6x7 + FE, transversal direction. Test report No. 70-16-0034. TSUS. Bratislava
- Eriksson, F. (2020). Assessment of static performance of LKAB's welded mesh: Laboratory testing and analysis (Dissertation). Retrieved from http://urn.kb.se/resolve?urn=urn:nbn:se:ltu:diva-77249
- Louchnikov, V., Sandy, M., Watson, O., Orunesu, M., & Eremenko, V. (2014). An Overview of Surface Rock Support for Deformable Ground Conditions. In: 12th Asuimm
- Underground Operators Conference (pp. 56-65). Adelaide
- Macák, I. (2020) High-Tensile Steel Wire Mesh MINAX G65/4 in longitudinal direction. Test report No. 70-20-0003. TSUS. Bratislava
- Mercier-Langevin, F. (2019), 'Ground support: a mine manager’s perspective', in J Hadjigeorgiou & M Hudyma (eds), Ground Support 2019: Proceedings of the Ninth International Symposium on Ground Support in Mining and Underground Construction, Australian Centre for Geomechanics, Perth, pp. 29-40, https://doi.org/10.36487/ACG_rep/1925_0.03_Mercier-Langevin
- Villaescusa, E, Thompson, AG & Player, JR. (2013), 'Static and dynamic testing of welded and woven mesh for rock support', in Y Potvin & B Brady (eds), Ground Support 2013: Proceedings of the Seventh International Symposium on Ground Support in Mining and Underground Construction, Australian Centre for Geomechanics, Perth, pp. 187-196, https://doi.org/10.36487/ACG_rep/1304_11_Villaescusa
- Whiting, RK 2017, 'In situ static performance assessment of mine mesh', in J Wesseloo (ed.), Deep Mining 2017: Proceedings of the Eighth International Conference on Deep and High Stress Mining, Australian Centre for Geomechanics, Perth, pp. 747-762, https://doi.org/10.36487/ACG_rep/1704_51_Whiting
- Zare S. & Bruland A. (2007) Progress of drill and blast tunnelling efficiency with relation to excavation time and costs. Underground Space – the 4th Dimension of Metropolises – Barták, Hrdina, Romancov & Zlámal