Inspección por rayos X: las latas de metal no tienen por qué suponer un reto
La seguridad alimentaria es una de las principales preocupaciones de la industria de los alimentos y las bebidas y, a medida que entran en vigor normativas como la Ley de Modernización de la Inocuidad de los Alimentos (FSMA), los fabricantes deben garantizar que tienen implementado un programa de inspección de productos sólido. Esto no solo garantiza la conformidad, sino que también reduce notablemente la probabilidad de costosas retiradas de productos, así como los riesgos asociados a los consumidores que darían lugar a esta necesidad.
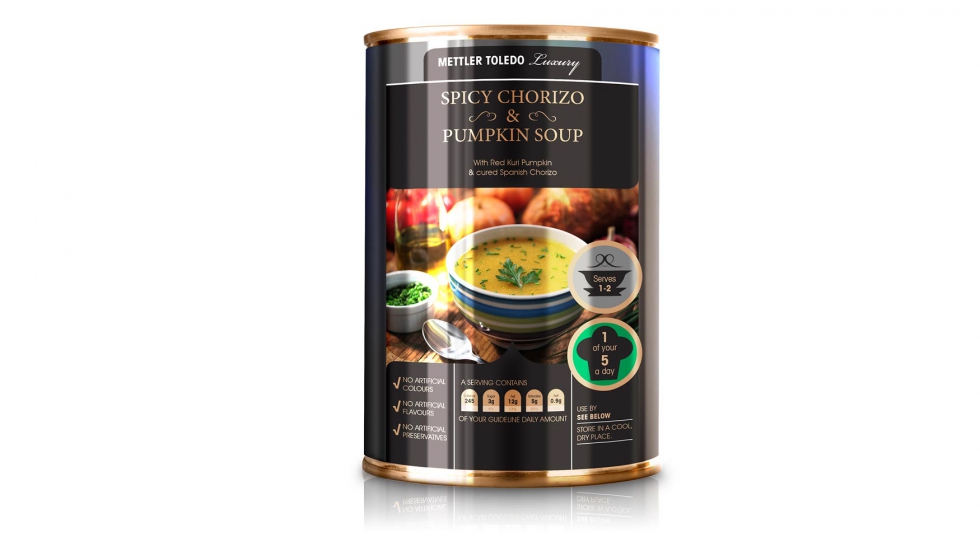
Las latas de metal resultan más difíciles de inspeccionar que los envases de baja densidad porque el propio envase presente una mayor densidad a los rayos X. Además, las características del envase pueden crear áreas complicadas de inspeccionar, como las paredes laterales acanaladas y la base con niveles. Los contaminantes se pueden ocultar dentro de molduras internas, por ejemplo, y las velocidades de línea (que son especialmente rápidas en el sector de los alimentos y las bebidas) pueden dificultar las detecciones precisas. Las líneas de alta velocidad requieren la captura de imágenes de alta resolución, y los dispositivos de rechazo deben poder retirar los envases supuestamente contaminados de la producción y estar listos para la siguiente lata de la línea.
Las máquinas de rayos X disponibles actualmente en el mercado están diseñadas para inspeccionar y rechazar latas con una exactitud muy alta y a una velocidad de hasta 1.800 ppm. El reto consiste en que se presente un producto repetible a la máquina de rayos X cada una de las veces. El sistema memoriza las plantillas de productos que se encuentran dentro de parámetros aceptables y, en caso de un producto sea incoherente en cuanto a su presentación, este se rechaza inmediatamente. Cuando hay problemas con los propios envases o imperfecciones de envasado, se pueden producir falsos rechazos. Los clientes pueden utilizar máquinas de rayos X como herramientas de análisis de las causas si experimentan un elevado número de falsos rechazos. De esta forma, se pueden mejorar los procesos de producción en una fase más temprana de la línea.
Los sistemas de enlatado pueden usar una tecnología de haz simple o dividido. Los sistemas de haz dividido horizontal son preferibles, ya que aumentan la probabilidad de detectar contaminantes pequeños que puedan estar ubicados en la base o en las paredes laterales de la lata. Hay disponibles sistemas que son más que capaces de hacer frente a las velocidades de línea que requieren los fabricantes, lo que permite que el sistema de inspección no sea el causante de cuellos de botella en la línea. Los sistemas de rechazo que trabajan de forma conjunta con los detectores pueden retirar de la línea productos que se sospeche que contengan contaminantes sin necesidad de reducir el rendimiento.
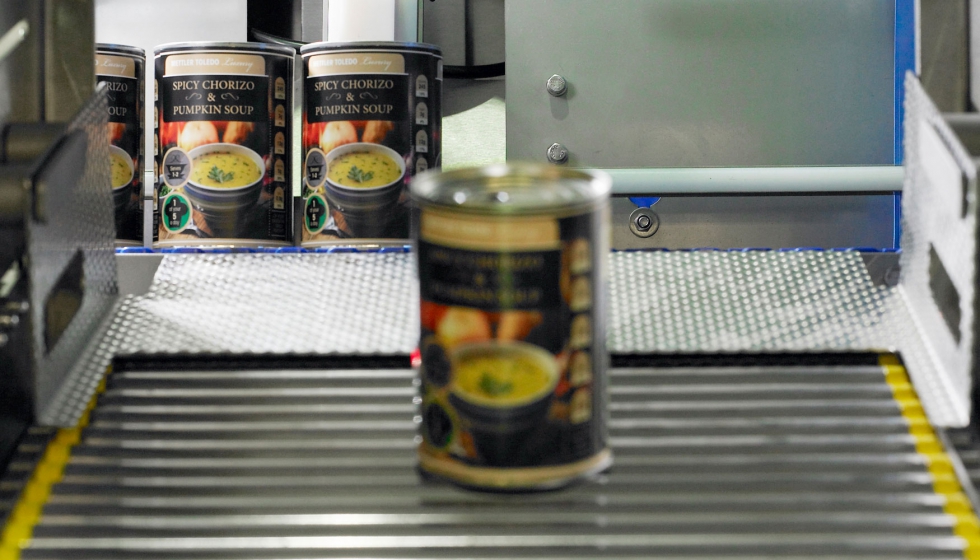
La instalación de equipos de inspección por rayos X avanzados no tiene por qué suponer un reto para los fabricantes. Hay sistemas que pueden instalarse fácilmente en una línea existente y que presentan una gran capacidad de adaptación a los requisitos individuales. Esto mantiene el tiempo de inactividad asociado a la integración al mínimo y garantiza que los clientes puedan empezar a experimentar las ventajas de la inspección de productos por rayos X sin interrupciones importantes en los programas de producción.
Existen diversas opciones de generadores y diodos que se adaptan a todas las aplicaciones y que garantizan una sensibilidad del detector fiable y excepcional. Las opciones de baja potencia también contribuyen a las credenciales ecológicas de los clientes, ya que los sistemas de inspección por rayos X tienen la capacidad de funcionar con bajos niveles de potencia, con lo que se reduce hasta cinco veces el consumo general de energía en algunos casos. Esto, por su parte, contribuye a disminuir los costes de funcionamiento.
Además de las capacidades avanzadas de detección de contaminantes, los sistemas de inspección por rayos X también pueden realizar otros controles de calidad de manera simultánea. Los niveles de llenado, por ejemplo, pueden supervisarse para garantizar que no lleguen productos con un llenado insuficiente a la cadena de distribución de comerciantes. También se pueden detectar los sobrellenados, lo que supone un ahorro para los fabricantes, ya que no se desperdicia producto. Asimismo, se pueden identificar los defectos de envasado, como las abolladuras, y retirar los productos afectados inmediatamente. Estos controles de calidad adicionales aportan un valor añadido, tanto en términos de satisfacción de los clientes como en posibles ahorros de costes, y garantizan que la inversión de capital en tecnología de rayos X se amortizará de distintas formas.