Recubrimiento ecológico mediante proyección térmica de alta velocidad (HVOF)
12 de noviembre de 2010
Hoy en día, Gutmar es la principal empresa catalana dedicada al producto embarcado mecánico del sector aeronáutico y aeroespacial contando, desde hace más de 40 años, entre sus clientes a empresas aeronáuticas internacionales como EADS Eurocopter Francia y organismos estatales tan exigentes como el Ministerio de Defensa.
Para conseguir este objetivo, Gutmar ha realizado un importante esfuerzo en I+D+i, estableciendo alianzas estratégicas con empresas y centros de investigación de reconocido prestigio nacional e internacional, obteniendo de estas alianzas, el conocimiento de nuevas tecnologías que les permitiese desarrollar nuevos procesos y técnicas de producción y montaje.
A título de ejemplo se pueden presentar dos proyectos que hoy Gutmar está desarrollando. Por un lado la substitución de recubrimientos de cromo duro por un tipo de recubrimiento ecológico y no contaminante para el medio ambiente, obtenido por tecnologías de proyección térmica de alta velocidad (HVOF en adelante, proveniente de la denominación inglesa High Velocity Oxy Fuel) y, por otro lado, el desarrollo y fabricación de dos actuadores hidráulicos del tren de aterrizaje del nuevo avión Airbus A400M en los que colabora con las empresas Cesa y Messier Dowty.
Ambos proyectos encajan perfectamente en su estrategia de búsqueda constante de nuevos sistemas y procesos y de hecho, los ha culminado con éxito, ya que los nuevos actuadores del A400M contienen piezas recubiertas con WC-CoCr obtenido por HVOF, desplazando de esta forma a los tradicionales recubrimientos de cromo duro. Actualmente, los actuadores han pasado todos los ensayos de evaluación y se han montado los primeros prototipos que están funcionando perfectamente en los vuelos de certificación.
Dentro de Gutmar, el proyecto de implantación de la tecnología de proyección mediante HVOF nace de la grave problemática suscitada por los recubrimientos de cromo duro electrolítico y la amenaza de prohibición de estos dentro del sector aeronáutico (que posteriormente se ha convertido en una realidad). A nivel mundial se generó entonces la necesidad de encontrar alternativas económicamente y medioambientalmente viables a este tipo de recubrimientos. Fruto de esta necesidad se constituyó en el año 2005 un consorcio de investigación con el nombre de Rampe (Recubrimientos Alternativos a los Metales Pesados contaminantes del medio ambiente) compuesto por centros de investigación (Inta y Tekniker) y empresas aeronáuticas (Cesa, ITP, Aernnova, Sener y Gutmar). Durante tres años se han evaluaron diferentes tipos de alternativas posibles como los recubrimientos de PVD, recubrimientos de CVD, slurries de diferente composición, recubrimientos obtenidos mediante tecnologías láser y recubrimientos de proyección térmica de alta velocidad.
Los excelentes resultados obtenidos con los recubrimientos de proyección térmica generaron la necesidad de instalar en Gutmar un completo equipo de última generación de HVOF, capaz de obtener recubrimientos de muy alta resistencia al desgaste y alta resistencia a la corrosión.
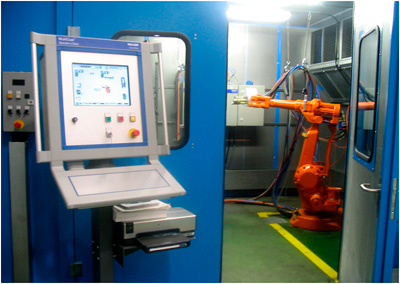
La técnica de HVOF está incluida dentro de la tecnología de proyección térmica, que engloba al conjunto de técnicas capaces de obtener un recubrimiento sobre un substrato sin alteración del mismo, mediante la fusión parcial o total de partículas introducidas en una fuente calorífica. Para la obtención del recubrimiento (metálico o no metálico), se introduce el material deseado en forma de polvo, alambre o cordón en una pistola de proyección térmica que genere el calor suficiente como para conferir al material un estado de plasticidad y a la vez una energía cinética suficiente como para acelerarlo hacia la superficie a recubrir. Cuando la partículas fundidas o semifundidas llegan al sustrato impactan adquiriendo una forma laminar que se adapta a la forma existente, formando el recubrimiento tras solidificar. Los espesores pueden variar desde las decenas de micras hasta en casos extremos algunos milímetros.
Existen diferentes técnicas de proyección térmica, como pueden ser la proyección por llama, por plasma (en la que se alcanzan temperaturas superiores a 15.000 °C y que permite el recubrimiento con materiales cerámicos), proyección por detonación, proyección por arco eléctrico, proyección de alta velocidad (HVOF), etc. Cada técnica se aplica en función de las propiedades que se necesitan en el recubrimiento o el tipo de material empleado, aunque es la aplicación mediante HVOF la que permite obtener recubrimiento con una mayor adherencia al sustrato y mayor resistencia a la corrosión (son menos porosos y más densos). Es por este motivo que las técnicas de alta velocidad son más utilizadas en la industria aeronáutica y especialmente en los procesos de sustitución del cromo duro.
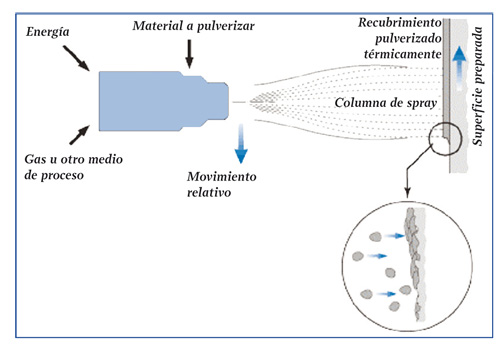
Con respecto a los fundamentos de la proyección térmica de alta velocidad (HVOF), esta técnica se basa en la combustión de oxígeno a alta presión con un combustible gaseoso (hidrógeno, propileno, etc.) o líquido (queroseno). Esta combustión genera una llama de alta velocidad en la que se introducen las partículas del material, generando un haz de proyección de partículas fundidas o semifundidas de gran velocidad (entre 450 y 900 metros por segundo) y temperaturas en un rango de 1.800 a 2.900 °C.
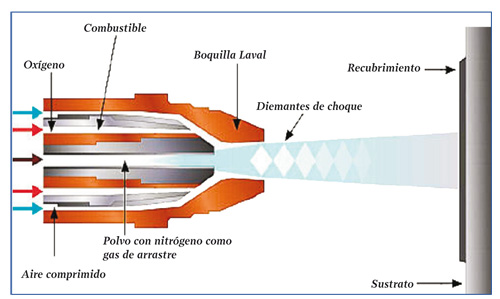
Cuando las partículas fundidas o semifundidas llegan al substrato, impactan adquiriendo una forma laminar que se adapta a la forma existente formando el recubrimiento tras solidificar.
Para asegurar la obtención de recubrimientos de calidad, es necesario realizar un análisis de las aplicaciones o del trabajo al que será sometido la pieza a proyectar, para de ésta forma, poder determinar la composición adecuada del recubrimiento. Una vez determinada la composición, se realiza un exhaustivo control del material de polvo de partida, en laboratorios homologados. En todos los casos, se analiza el tamaño de grano de partícula, la composición química y la determinación de las fases presentes mediante difracción de rayos X.
En el momento en el que la calidad del polvo está asegurada, se inicia un proceso de obtención y optimización de propiedades. Durante este proceso, se establece una intensa colaboración con los laboratorios, ya que es necesario realizar la preparación metalográfica de todas las probetas y de las propiedades del recubrimiento (dureza, adherencia, resistencia a desgaste, resistencia a corrosión, etc.). Una vez optimizadas las propiedades, se obtienen capas densas con muy buenas propiedades y bajas porosidades.
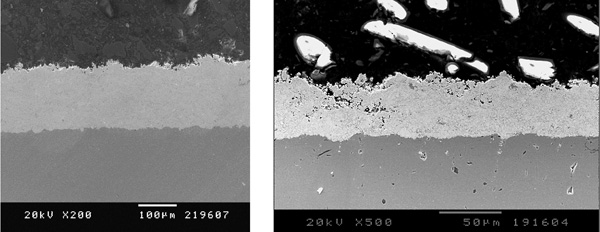
Los recubrimientos obtenidos mediante HVOF, presentan en general las siguientes propiedades:
- Capas densas de elevada dureza, con estructuras muy homogéneas
- Proceso optimo para la deposición de carburos (WC-CoCr, WC-Co, Cr2C3-NiCr, etc.) y superaleaciones
- Excelente resistencia al desgaste y a la corrosión
- Recubrimientos fácilmente rectificables con acabado muy finos
- Facilidad de automatización de proceso y en general con facilidad para enmascarar áreas que no deban ser recubiertas
En particular, capas de WC-Co y WC-CoCr se han aplicado como substitutos del cromo duro con un éxito notable desde hace años, en aplicaciones tales como actuadores, pistones y rodillos hidráulicos, asientos de válvulas, anillos de pistón, turbinas de gases, etc. Estos dos tipos de recubrimientos son extraordinariamente resistentes al desgaste y en el caso de WC-CoCr, es capaz de resistir 500 horas dentro de cámara de niebla salina sin que aparezcan los primeros indicios de corrosión. Con respecto a la temperatura máxima de trabajo, permiten trabajar hasta temperaturas cercanas hasta los 500°C sin disminución de las propiedades. Para aplicaciones a mayor temperatura con buena resistencia al desgaste y excelente resistencia a corrosión, los recubrimientos de Cr2C3-NiCr pueden llegar a trabajar a temperaturas cercanas a 800 °C.
Respecto a las piezas, para recubrirlas es necesario realizar una preparación muy simple antes de la etapa de deposición. En todos los casos se realiza un desengrase para asegurar una correcta adherencia, seguido de un arenado que dote a la superficie de rugosidad necesaria para que tenga lugar el anclaje de las partículas y la buena adherencia del recubrimiento. En este momento, la pieza está preparada para ser recubierta.
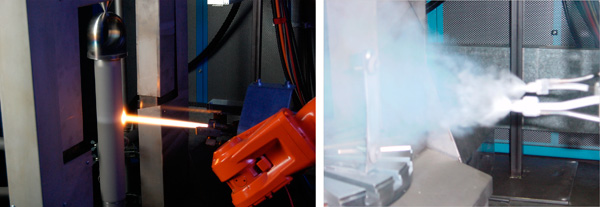
La etapa de deposición de recubrimiento se realiza de forma continua obteniendo los espesores deseados de forma controlada y manteniendo la temperatura de la pieza. Como ejemplo práctico, algunas de las piezas que se fabrican en Gutmar tienen una limitación de temperatura máxima de 170 °C (la llama está por encima de 2.000 °C). Para mantener la temperatura por debajo de 170 °C, se refrigera la pieza con CO2 (que genera una nube a –40 °C) y permite mantener la temperatura de la pieza estable por debajo del límite establecido. En casos menos exigentes, la refrigeración se realizar con aire comprimido, manteniendo la temperatura de la pieza por debajo de 300 °C.
En la siguiente tabla aparece un pequeño resumen de las propiedades de los recubrimientos de WC-CoCr obtenidos en Gutmar.
Propiedades del Recubrimiento WC-CoCr
Propiedad | Valor |
Adherencia | 84 Mpa |
Microdureza HVN 300 g | 1.250 |
Porosidad | 0,15% |
Resistencia cámara niebla salina | 550 horas |
Rugosidad tras rectificado | Ra=0,08 |
Tras la etapa de deposición se puede realizar un rectificado de la superficie para lograr una reducción de la rugosidad. Debido a la elevada dureza de los recubrimientos, se acostumbran a realizar los rectificados con muelas de diamante hasta obtener rugosidades inferiores a Ra=0,1, que les convierten en excelentes superficies para trabajar en componentes sometidos a fricción.
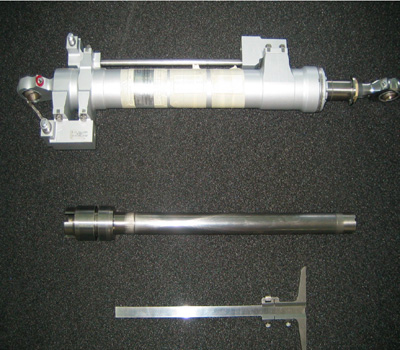
Como ejemplos de aplicación, actualmente Gutmar está depositando recubrimientos de WC-CoCr y WC-Co en toda serie de actuadores hidráulicos, tanto de equipos aeronáuticos como de equipos terrestres (figura 13 y 14), desplazando de forma satisfactoria a los tradicionales recubrimientos de cromo duro. Estas mismas formulaciones y otras como el Cr2C3-NiCr, Inconel (aleaciones base Ni), etc., están siendo depositadas en piezas de sectores tan diversos como sector petroquímico (válvulas de bola, asientos de válvula, etc.), automoción, centrales térmicas, centrales eólicas, etc., con extraordinarios resultados en el aumento de la vida útil de las piezas recubiertas.