Materiales metálicos de uso frecuente en aeronáutica: aleaciones ligeras Al-Li
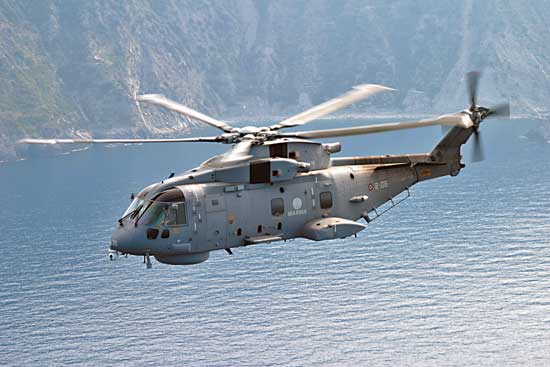
Las primeras menciones sobre aleaciones Al-Li datan del año 1920 en Alemania pero no fue hasta 1957 cuando aparecieron las primeras aleaciones estandarizadas. En ese año una aleación conteniendo litio y bautizada como X2020 se utilizó para la estructura de un pequeño avión militar experimental denominado RA-SCA en Estados Unidos. La razón principal de su aplicación fue la baja densidad y alta rigidez del material pero posteriormente la aleación se retiró de la producción debido a problemas técnicos identificados al analizar el comportamiento de la aleación en condiciones de servicio. Se detectaron problemas relacionados con la segregación de ciertas fases en la microestructura del material, baja tenacidad y ductilidad, y la formación de intermetálicos frágiles y fenómenos de cizalladura de los precipitados Al3Li por el movimiento de las dislocaciones.
A comienzos de la década de los 70 y relacionado con la crisis del petróleo se renovó el interés por las aleaciones ligeras y se pusieron en marcha nuevos proyectos de investigación relacionados con el Al-Li. Se analizaron los problemas de las aleaciones anteriores y se investigó en nuevas composiciones con un menor contenido en litio y mayor presencia de cobre y/o magnesio. Se analizó en profundidad la relación entre la microestructura y las propiedades finales así como el comportamiento de las distintas aleaciones frente a los tratamientos térmicos Por una parte aparecieron una serie de nuevas aleaciones en Rusia bajo la numeración 1400 y finalmente en 1983 dos de los mayores productores de aleaciones de aluminio para la industria aeroespacial, la británica Alcan y la norteamericana Alcoa, anunciaron la introducción de nuevas aleaciones de Al-Li. 2090, 8090, 8091, etc.
La práctica totalidad de los productos fabricados actualmente con aleaciones Al-Li son productos conformados debido a que la elevada reactividad del litio en estado fundido hace inviable la fabricación de productos por fundición a nivel industrial y solo existen referencias de algunos productos fabricados por fundición a la cera perdida.
Las características principales del litio en cuanto a su utilización como elemento aleante en aleaciones de aluminio son las siguientes:
- El litio es el más ligero de los elementos metálicos (densidad 0,534 g/cm3) y su adición a aleaciones de aluminio reduce la densidad de las mismas de manera considerable. Añadiendo un 1% de litio se llega a reducir un 3% la densidad de la aleación
- La adición de litio produce un aumento considerable de la rigidez del material debido a la formación de una fase meta estable. La adición de un 1% de litio puede llegar a suponer un aumento del 6% en el módulo de elasticidad del material.
- Forma a su vez otras fases con el aluminio y la mayor parte de los elementos aleantes comunes en aleaciones de aluminio como el Mg, Cu o Zr (Al3Li, Al2CuLi, Al6CuLi3). Estas fases producen un efecto reforzante de la aleación al impedir el movimiento de las dislocaciones sin un gran detrimento de la tenacidad.
- La adición de litio favorece la soldabilidad de la aleación de aluminio.
- De forma general se puede decir que la adición de litio proporciona mejor resistencia a altas temperaturas que la obtenida por la adición del Zn en aleaciones Al-Zn como el 7075 con la que compiten.
- El comportamiento de las aleaciones Al-Li a bajas temperaturas es excelente y por ello ha sido utilizado para la construcción de tanques criogénicos.
- De forma general se puede afirmar que la resistencia a fatiga de las aleaciones Al-Li es superior a las de las aleaciones Al-Zn.
- La resistencia a la corrosión de las aleaciones Al-Li es elevada después de la aplicación del tratamiento térmico adecuado.
En definitiva, la combinación de la baja densidad de las aleaciones Al-Li, su conformabilidad y su excelente balance de propiedades mecánicas hace que sea un candidato ideal para aplicaciones en el fuselaje de aviones y helicópteros
En contra partida también existen una serie desventajas o factores negativos que hay que considerar a la hora de seleccionar aleaciones de Al-Li para una aplicación determinada.
- El precio del litio es elevado comparado con otros elementos aleantes comunes en aleaciones de aluminio (Zn, Cu, Mg etc.) y en consecuencia las aleaciones que contienen litio son entre 2-4 veces más caras que otras aleaciones convencionales.
- La tenacidad de las aleaciones no es elevada en comparación a aleaciones Al-Zn.
- Las propiedades mecánicas de las aleaciones Al-Li son muy sensibles a la homogeneidad de la microestructura y composición
- El litio es un elemento altamente reactivo y toxico por lo que la manipulación del litio en la fabricación de la aleación y la posterior manipulación de la aleación en operaciones de mecanizado o reciclado debe tener en cuenta este factor.
Dando un repaso a la historia de este tipo de aleaciones, la aleación X2020 producida en Estados Unidos en los años 50 fue la primera aleación de aluminio comercial conteniendo litio. Era una aleación de la serie 2000 que contenía 3% de litio y además un 4% de cobre, un 0,5 % de manganeso y Cadmio como elementos aleantes principales. Paralelamente se desarrollaron aleaciones Al-Mg-Li en Rusia tales como las aleaciones 1429, 1420 y 1421 y desde 1964 la empresa rusa Kumz ha ido desarrollando nuevas aleaciones utilizadas principalmente por la industria aeroespacial rusa. Estas aleaciones sin embargo presentaban una ductilidad y tenacidad demasiado baja y en los siguientes años se desarrolló una nueva generación de Al-Li pertenecientes a las series 2000 (Al-Cu-Mg-Li-Zr) y 8000 (Al-Li-Cu-Zr) en los que se reducía la concentración de litio hasta un 2%.
Las aleaciones más conocidas de esta segunda generación son probablemente la 8090 (Al-Li-Cu-Mg), 2090 y Weldalite 049 fabricadas por Alcan, Alcoa y Pechiney. Son aleaciones comercialmente disponibles actualmente aunque están siendo progresivamente sustituidas por la nueva generación de aleaciones Al-Li.
La aleación 8090 presenta una composición Li - 2,45, Zr - 0,12, Cu - 1,3, Mg - 0,95. Fue desarrollada para competir con las aleaciones Al-Cu como la 2024 frente a las cuales presenta un 10% menos de densidad y un 11% más de rigidez. Además de ello presentaba una mejora sustancial del comportamiento en temperaturas criogénicas. La aleación está disponible en forma de placas, tubos extraídos y forja y puede utilizarse en aplicaciones soldadas. La aleación 2090 presenta una composición Cu - 2,7, Li - 2,2, Ag - 0,4, Zr -0,12. y se desarrolló como alternativa a la aleación 7075.-T6 frente a la cual presenta un 8% menos de densidad y un 10% más de rigidez. La nueva aleación ofrecía además un mejor comportamiento frente a la corrosión en ensayos realizados simulando un ambiente marino. Fue registrada en 1984 y desde entonces se han desarrollado un gran número de tratamientos térmicos específicos. Presenta ciertas características que conviene remarcar. Por una parte presenta una anisotropía de las propiedades a tracción superior a las aleaciones convencionales así como un excelente comportamiento frente al crecimiento de grieta en fatiga, la necesidad de una operación de trabajo en frio para obtener sus propiedades óptimas.
Posteriormente se desarrolló la aleación 2091 pensado para reemplazar a la aleación 2024-T3 frente a la cual presentaba unas mejoras similares además de una mayor tenacidad.
La aleación Weldalite 049 presenta una composición Cu - 5,4, Li - 1,3, Ag – 0,4, Mg - 0,4, Zr - 0,14. Es una aleación que presenta como característica principal su gran soldabilidad. Presenta además una gran resistencia mecánica en diversos estados de temple. Es una aleación con una respuesta muy elevada frente al envejecimiento natural después de una etapa de cold work (tratamiento T3) pero también a un tratamiento de tipo T4 sin el endurecimiento por medio del estirado en frio (cold work).
Posteriormente han sido las dos grandes multinacionales de la industria del aluminio, Alcan y Alcoa las que han proseguido en la investigación de nuevas aleaciones de Al-Li dirigidas principalmente a las necesidades de la industria aeronáutica y para competir con materiales como los materiales compuestos reforzados con fibra de carbono para la fabricación de fuselajes y perfiles extruidos de los nuevos modelos de avión. Las nuevas aleaciones como el AA2094, AA2096, AA2097, AA2099, AA2199, AA2196, AA2197, AA2198 y AA2050 están basadas en la combinación de los elementos Cu-Li-Mg-Ag-Zr y presentan características de una gran conformabilidad y mejora en la tenacidad y ductilidad.
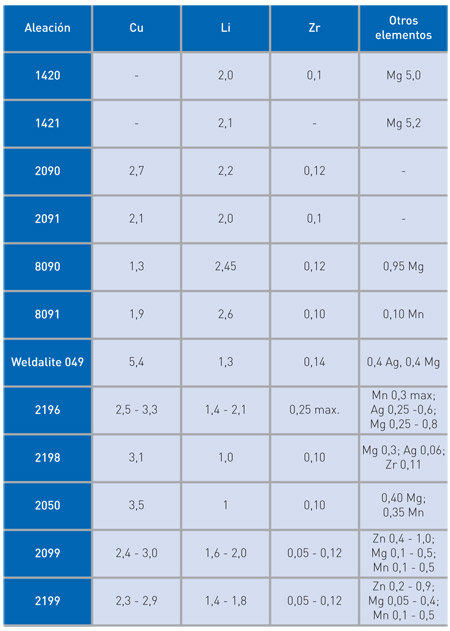
La última generación de las aleaciones Al-Li presenta una menor relación Cu/Li en comparación a las anteriores aleaciones. Pertenecen al sistema Al-Cu-Li-Mg y presentan también presencia de algunos elementos aleantes adicionales como la plata, circonio y manganeso. Los ejemplos más notables son las aleaciones 2050 de placas de espesor medio-alto que ha sido seleccionada por Airbus y Bombardier para su utilización en los aviones Airbus 350 XWB y de las series C respectivamente. La aleación 2196 en forma de aleaciones extruidas y la 2198 que se presenta en forma de chapa fabricados por la empresa Alcan y las aleaciones, 2099 y 2199 de Alcoa.
Estas aleaciones presentan una conformabilidad y características mecánicas superiores a las aleaciones precedentes debido al intenso trabajo realizado para controlar la microestructura de las aleaciones y los correspondientes tratamientos térmicos.
Existe una elevada variedad en cuanto a la forma y dimensiones de los materiales suministrados y la cantidad de tratamientos térmicos aplicables es también muy elevada teniéndose que estudiar cada aplicación individualmente.
La tabla 2 presenta algunos valores de propiedades mecánicas típicas alcanzables por estos materiales.
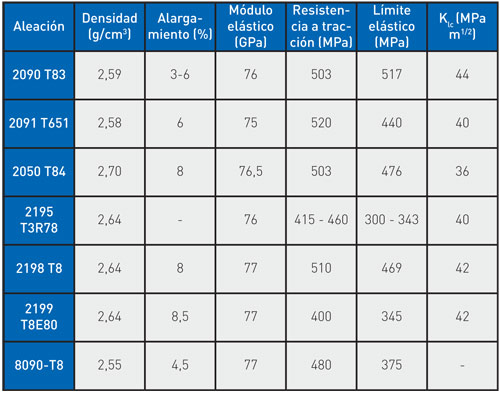
Las aleaciones de aluminio que contienen litio son tratables térmicamente y presentan una microestructura y una secuencia de precipitación de fases durante el tratamiento térmico muy compleja debido a la presencia de diferentes fases meta estables. El diagrama de fases calculado de la aleación binaria Al-Li es sencillo pero, sin embargo, se complica cuando entran en juego elementos como el Cu, Mg o circonio en la aleación.
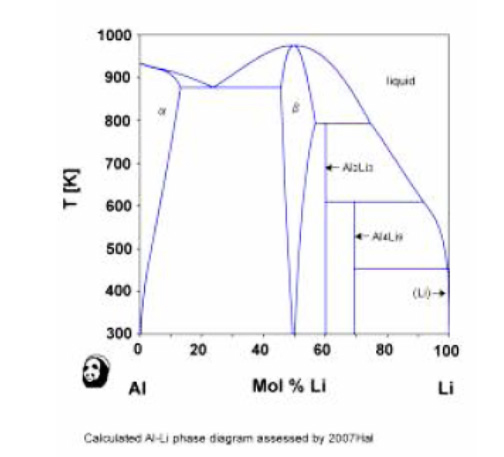
Dependiendo de la aplicación de las aleaciones se puede impulsar, mediante la selección de la concentración de los elementos aleantes y el tratamiento térmico conveniente, la aparición de otras fases como la fase T2 (Al6CuLi3) para conseguir un incremento adicional de la tenacidad o partículas de Al2CuMg que forman la fase S’.
A continuación se detalla el papel más importante de los elementos aleantes principales:
El circonio se añade a las aleaciones de Al-Li para formar dispersoides que actúan como inhibidores de la re cristalización. con el fin de presentar una microestructura más fina y un mejor comportamiento frente a fatiga.
Por su parte el manganeso se añade por el incremento de la resistencia de la aleación que conlleva al añadirse en niveles inferiores al 5%.
También forma dispersoides incoherentes con el cobre Al20Cu2Mn3 que mejoran la tenacidad y comportamiento a fatiga de las aleaciones a través de mecanismos de homogeneización del movimiento de deslizamiento de las dislocaciones.
Las aleaciones Al-Li modernas presentan también la presencia de una cierta cantidad de cinc para mejorar las propiedades frente a la corrosión de las aleaciones y magnesio para mejorar la resistencia mecánica.
La incorporación del magnesio y la plata en aleaciones Al-Li-Cu está basada en los efectos conocidos de estos dos elementos aleantes en las aleaciones de Al- Cu y se ha demostrado que tienen un papel determinante en la respuesta al tratamiento de envejecimiento y en consecuencia a la resistencia máxima en alcanzable. La combinación de un 1,3% de litio con el magnesio y plata puede suponer un aumento del 100% en el límite elástico de la aleación.
Hasta el año 2005 las aplicaciones de las aleaciones Al-Li se habían restringido a su utilización en aplicaciones militares para aviones de combate, tanques criogénicos y aplicaciones espaciales tales como la utilización de la aleación 2195 en el tanque externo de las lanzaderas espaciales de la NASA. La baja densidad de las aleaciones y sus propiedades mecánicas habían atraído el interés de otros sectores como el de la aviación comercial pero su alto coste unido a algunas dudas surgidas sobre características de resistencia a la corrosión, tenacidad y ductilidad que presentaban las primeras generaciones de las aleaciones Al-Li desarrolladas impidieron su aplicación a gran escala.
Posteriormente el desarrollo de nuevas aleaciones creadas por las grandes empresas productoras de aluminio como respuesta a la amenaza de otros materiales alternativos como los materiales compuestos de matriz orgánica y el incremento en los requerimientos mecánicos de las nuevas generaciones de aviones como el Airbus 350 o el Boeing 787 han vuelto a actualizar el interés de la industria aeroespacial en las aleaciones aluminio-litio.
La utilización de materiales compuestos de matriz orgánica ha aumentado drásticamente en modelos como el Airbus A380, A350XWB y el Boeing 787 pero presentan la desventaja de su coste. Tanto la materia prima como sobre todo la necesidad de adaptar el equipamiento y las instalaciones a la fabricación, unión, mecanizado y reparación de los materiales compuestos de matriz orgánica avanzados supone un sobrecosto importante. A ello hay que añadir los problemas de reciclado de los polímeros termoestables utilizados. Así, la industria del aluminio ha visto en el desarrollo de las aleaciones de Al-Li una oportunidad para contrarrestar el avance de los materiales compuestos para la fabricación del fuselaje y elementos estructurales en los aviones y por ello en los últimos cinco años se han comercializado nuevas aleaciones para responder a esta amenaza.
A continuación repasaremos algunos ejemplos de utilización de este tipo de materiales.
En el sector aeronáutico, mientras que la empresa Boeing evaluó la posibilidad de utilizar aleaciones Al-Li en sus futuros proyectos realizando finalmente una apuesta importante por los materiales compuestos reforzados con fibra de carbono que serán el material base en la construcción del fuselaje de su modelo 787 Dreamliner, el otro gigante aeronáutico, Airbus, parece por el contrario haberse inclinado por otros materiales para los fuselajes de sus próximos aviones y las aleaciones de Al-li de última generación tienen una gran posibilidad. Existen de hecho programas de empresas como Airbus o Bombardier en donde se han seleccionado aleaciones como el 2050 o el 2196 y que están ya en fase de fabricación.
Por su parte Airbus decidió construir la sección del fuselaje de la cabina en aluminio-litio frente a la estructura monolítica en fibra de carbono que había sido evaluado anteriormente. Las razones técnicas principales de la selección de la aleación de aluminio frente al material compuesto se basan en la mayor resistencia del primero frente al impacto de objetos externos. Por otra parte, Airbus utiliza la aleación 2099-T83 en forma de perfiles extruidos en el fuselaje y suelo. (ver detalle en figura 5).
La misma aleación seleccionada por Airbus será aplicada también por Bombardier en sus nuevos modelos de la serie C. Aviones diseñados para el rango de 100-149 pasajeros y en los que el material de Alcan Engineered Products denominado Airware supondrá el 20% en peso del avión. Esta nueva aleación está compuesta por aluminio, cobre, litio, magnesio y plata y es la respuesta de Alcan a la amenaza de los materiales compuestos de matriz orgánica. Sus características principales son las de una elevada resistencia mecánica, tenacidad y resistencia a la corrosión. Los aviones serán fabricados finalmente por Shenyanng Aircraft Corp. (SAC) en China y se espera que estén operativos en el año 2013.
Un último ejemplo del importante impulso que ha supuesto la selección de las aleaciones Al-Li para componentes estructurales del modelo A350 de Airbus lo constituye la Commercial Aircraft Corporation de China Ltd. (COMAC) que ha suscrito en 2010 un acuerdo con Alcoa para el desarrollo de componentes para su Nuevo modelo ARJ-21 y el C919.
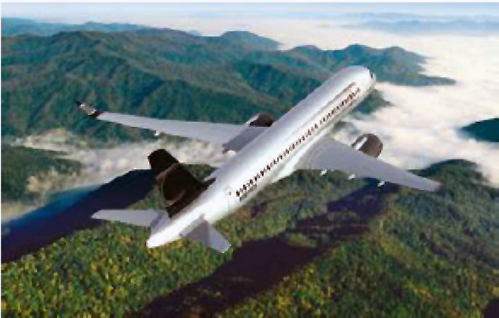
Otro sector donde ya se utilizan aleaciones de Al-Li es el de los helicópteros siendo el caso del fuselaje del helicóptero de AgustaWestland EH101 el más conocido. En la figura 4 se detallan los componentes del fuselaje fabricados en Al-Li (color azul).
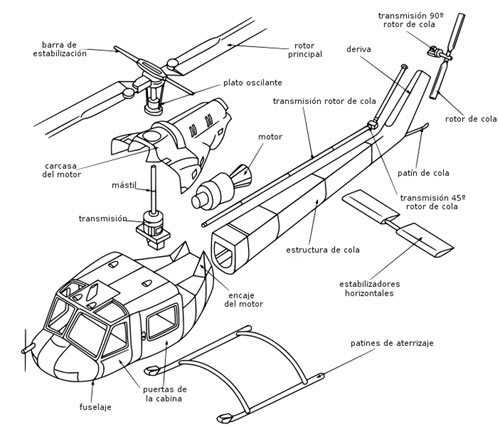
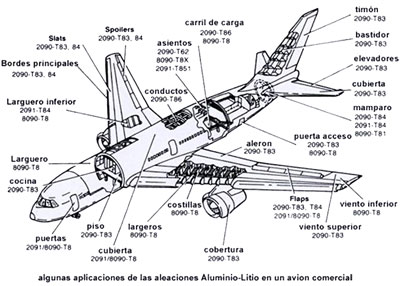
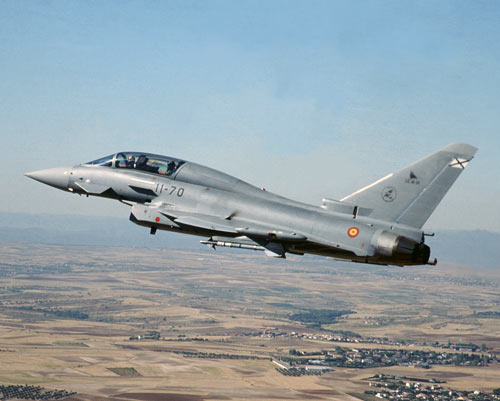
En otra aplicación militar el avión de combate avanzado Eurofighter Typhoon también presenta componentes fabricados con aleaciones Al-Li. (ver figura 5). El 70% de la superficie del avión está fabricado con material compuesto reforzado con fibra de carbono y el 15% contiene aluminio y titanio siendo el 12% material compuesto reforzado con fibra de vidrio y un 3% de otros materiales.
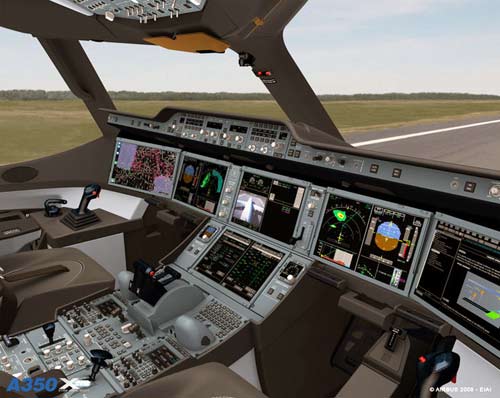
Otras aplicaciones comerciales de las aleaciones Aluminio-Litio se encuentran en el sector espacio y tanques criogénicos. La NASA lleva aplicando aleaciones Al-Li en sus programas espaciales desde hace más de diez años como material para la construcción de los tanques de combustible de sus lanzaderas y cohetes (ver fotos 9 y 10) y para la fabricación de piezas estructurales.
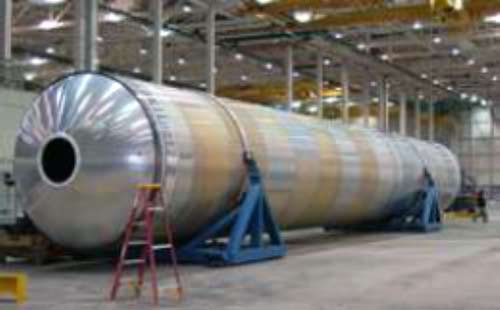
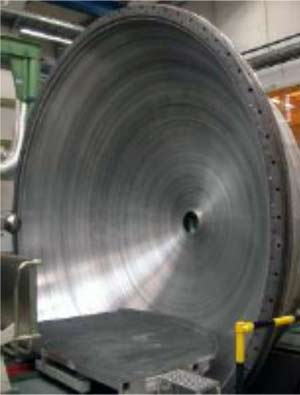
Para concluir algunas consideraciones en relación con su procesado y conformado.
El litio es un elemento muy volátil lo que dificulta la fabricación de las aleaciones Al-Li que debe realizarse bajo atmosfera controlada. Existen diversos métodos de fabricación de las aleaciones de Al-Li entre las cuales están los procesos de pulvimetalurgia, la colada directa y procesos de solidificación rápida como la deposición por atomización.
Alcan y Alcoa, los dos grandes productores de esta aleación utilizan procesos derivados del proceso tradicional de metalurgia de lingotes (ingot metallurgy) a través de procesos semicontinuos de enfriamiento directo.
La colada directa es el método tradicional de fabricación pero el proceso de sprayado aporta mayor flexibilidad y está siendo adoptado también para la fabricación de estas aleaciones. Consiste básicamente en la atomización del compuesto Al-Li en estado líquido y en su deposición bajo atmosfera de Argon o helio.
Por último existe también la posibilidad de fabricar estas aleaciones por meltspinning o templado giratorio. Son variantes pulvimetalurgicas en los que el material liquido no es atomizado sino que una pequeña corriente del metal cae sobre una rueda metálica que gira rápidamente donde solidifica. El resultado es un material en forma de hilos o copos de 20-50 micras de espesor y varios milímetros de diámetro.
En cuanto al conformado, las aleaciones de Al-Li presentan en general una buena conformabilidad y actualmente hay aleaciones comercialmente disponibles en forma de materiales extraíbles, forjables y conformables por los procesos tradicionales de conformado.
Una de las propiedades de las aleaciones Al-Li que más interés presenta para la industria aeroespacial es su superplasticidad lo que posibilita conformar componentes que no pueden fabricarse en otras aleaciones con las que puede llegar a competir disminuyendo además la desventaja en cuanto al coste de la materia prima.
En cuanto a la fundición de aleaciones de aluminio-litio, ésta presenta serias dificultades por la naturaleza reactiva del litio. Por una parte las aleaciones en estado fundido tienden a absorber hidrógeno de una manera sensiblemente superior a otras aleaciones y también existe el problema de pérdida del litio a esas temperaturas. La fusión de las aleaciones en atmósferas que contienen O2, N2 o vapor de agua plantea el problema de la aparición de defectos en forma de absorción de gases.
La industria aeronáutica ha mostrado interés en la tecnología de la fundición a la cera perdida de estas aleaciones por las ventajas que presenta en cuanto a la posibilidad de obtención de piezas muy complejas con forma casi final. Históricamente se han realizado muchos esfuerzos en desarrollar esta tecnología y alguna de las grandes fundiciones en Estados Unidos como Howmet o Hitchiner ofrece la posibilidad de fundir aleaciones Al-Li para piezas para el sector aeronáutico.
Debido a los problemas técnicos comentados, a la falta de desarrollo de aleaciones específicas para la fundición y al elevado coste de la fabricación de piezas la fabricación de componentes fundidos de Al-Li es meramente testimonial y se restringe a la fabricación de series cortas y prototipos.
Por último, el tratamiento térmico convencional para las aleaciones Al-Li consiste en una etapa de solubilización en la que los elementos aleantes se disuelven en el aluminio hasta obtener una estructura homogénea y compuesta de una única fase, temple para obtener una solución solida supersaturada y el tratamiento final de envejecimiento artificial.
Debido a la reactividad del litio a elevadas temperaturas el tratamiento térmico de estas aleaciones presenta un mayor grado de complejidad que otras aleaciones convencionales utilizados en aeronáutica requiriendo la utilización de atmosferas de composición controlada y la aplicación de tiempos de ciclo y temperaturas específicas.
Conclusiones
Las características de ligereza y excelentes propiedades mecánicas de las aleaciones de aluminio conteniendo porcentajes de litio entre un 1-3% fueron descubiertas hace más de 50 años pero la utilización comercial de estas aleaciones a gran escala ha sido posible únicamente en los últimos anos. Las razones principales del uso restringido de estas aleaciones ha sido la del elevado coste en comparación a otras aleaciones de aluminio con las que competía (aleaciones de las series 2000 y 7000) y la existencia de aspectos técnicos sin resolver en las aleaciones Al-Li desarrolladas hasta entonces tales como su pobre tenacidad y ductilidad, el comportamiento frente a la corrosión o la falta de desarrollo de tratamiento térmicos y superficiales adecuados.
Sin embargo esta situación de paralización en el desarrollo de la tecnología de las aleaciones de aluminio-litio ha sufrido un cambio importante debido principalmente a la necesidad de los grandes constructores de aviones comerciales (Boeing, Airbus, Bombardier, etc.) de acceder a materiales con mejores prestaciones para sus nuevos diseños de aviones de gran capacidad.
La industria aeronáutica necesita para la fabricación de los fuselajes y elementos extraídos de refuerzo materiales que presenten una combinación de ligereza y propiedades mecánicas superiores a las presentadas por las aleaciones de aluminio convencionales como la aleación 7075. La alternativa de la utilización del titanio es excesivamente cara y en este escenario han surgido nuevos materiales como los compuestos reforzados con fibra de carbono.
La industria del aluminio a su vez ha respondido a esta amenaza de pérdida de competitividad de sus aleaciones apostando por el desarrollo de nuevas aleaciones entre las que destacan las nuevas generaciones de aluminio-litio tales como la aleación 2050 de Alcan. El argumento a favor de las aleaciones de Al-Li es la de presentar una combinación de propiedades superior a las aleaciones anteriores y la de poder competir en coste con los diseños en material compuesto reforzado con fibra de carbono.
Los principales argumentos a favor de la utilización de las aleaciones Al-Li se centran en su mejor adaptación a los requerimientos de los modelos de avión de tamaño medio, con un fuselaje más rígido que pueda soportar las solicitaciones cíclicas de un mayor número de aterrizajes y despegues al día.
En concreto, algunos argumentos a favor de la utilización de las aleaciones de Al-Li en contraposición a los materiales compuestos son:
Resistencia al impacto: los fuselajes están sometidos a impactos continuos en las operaciones de carga y descarga de maletas en la bodega y carros utilizados en operaciones rutinarias. Los materiales compuestos reforzados con fibra de carbono presentan una elevada resistencia pero pueden sufrir danos internos debido a estas solicitaciones y al impacto de rayos. En consecuencia se necesita implementar ensayos no destructivos rutinarios para controlar que la estructura interna del material compuesto no ha sufrido danos y se necesita evaluar la necesidad de una reparación para salvaguardar la viabilidad del conjunto. En el caso de las aleaciones aluminio-litio la reparabilidad de las piezas es más sencilla y menos costosa. Una posible solución sería lógicamente añadir una capa más de refuerzo en el caso de los materiales compuestos pero en ese caso las ventajas de coste y peso de los materiales compuestos no sería ya tan tangible.
Procesos de fabricación: la tecnología del aluminio y su aplicación en la industria aeronáutica es una tecnología barata y optimizada. En el caso de los materiales compuestos de matriz termoestable se requieren procesos de fabricación diferentes basados en la utilización de autoclaves, sistemas de vacío y procesos de unión y ensamblaje diferentes.
Coste y durabilidad: el coste de fabricación de los componentes en material compuesto es más elevado pero presentan la ventaja de una mayor resistencia a la corrosión. A pesar de la mejora experimentada en este campo por las últimas generaciones de aleaciones Al-Li los problemas de corrosión son todavía una preocupación para la industria de aluminio. Los materiales compuestos por su parte presentan otro tipo de problemas cuando son sometidos a la atmósfera en condiciones de servicio. Pueden absorber humedad y producir defectos en forma de delaminaciones y no se tienen datos suficientes en cuanto a su resistencia a largo plazo en aplicaciones aeronáuticas estructurales.
Aspectos medioambientales: las aleaciones Al-Li son más fáciles de reciclar que los materiales compuestos y únicamente hay que tener en cuenta la presencia de litio en aleaciones donde no está permitida. La reciclabilidad de los componentes de material compuesto de fibra de carbono es menor y el reciclado es más costoso. Son componentes formados por fibra de carbono, resinas termoestables y normalmente presentan una malla metálica intermedia para soportar el efecto de los rayos.