Déjese transportar... a la personalización en serie
Hoy en día los consumidores prefieren los productos personalizados y exclusivos y a menudo están dispuestos a pagar más. Por ejemplo, asistimos a la proliferación de las fundas para smartphones con imágenes personalizadas. Aunque el coste sea 5 o 6 veces superior al de una funda estándar, la demanda es cada vez mayor.
Este fenómeno abre un panorama de oportunidades realmente interesante para la industria manufacturera, siempre y cuando la gestión de los pedidos individuales sea compatible con los costes y los tiempos de la producción en serie.
Uno en un millón, no uno de un millón
El cambio de la reproducción a la producción específica para el cliente ya es una realidad en algunos segmentos industriales, tales como la impresión, el embalaje y la automoción. En el caso de la impresión, el cambio ha resultado más sencillo en gran parte gracias a la llegada de la impresión digital industrial, que ha eliminado la etapa de pre-impresión y ha permitido el desarrollo de máquinas de post-impresión altamente flexibles. En la industria del embalaje ya se pueden fabricar las (relativamente) pocas piezas necesarias para una campaña promocional o el lanzamiento de un nuevo producto, sin revolucionar los planes de producción.
Incluso en el sector automovilístico puede fabricarse un vehículo personalizado sin que ello represente ningún coste adicional para el cliente.
¿Cuál es el factor que ha permitido estos tres casos de estudio? En una palabra: Integración. Gracias a la progresiva digitalización de todos los niveles de la fábrica y a la presencia generalizada de las tecnologías de automatización, ya es posible adaptarse a las últimas tendencias de compra.
La reactividad y la flexibilidad de los procesos productivos permiten obtener objetos personalizados a ritmos de producción en serie, pero sin que ello comporte un aumento del coste unitario. Ello se traduce en una ventaja competitiva y en un atractivo margen para las industrias manufactureras, sea cual sea su tamaño.
A pesar de que la carrera para conseguir un valor añadido mediante la personalización del producto ya ha comenzado, en otros segmentos todavía se echa en falta el grado de automatización necesario a nivel de línea y de planta.
Actualmente sigue siendo necesario parar las máquinas para cambiar el formato o para activar una parte diferente de la máquina, necesaria para crear las distintas variantes del producto. Ello consume mucho tiempo de producción y anula en gran parte las ventajas de la producción en serie.
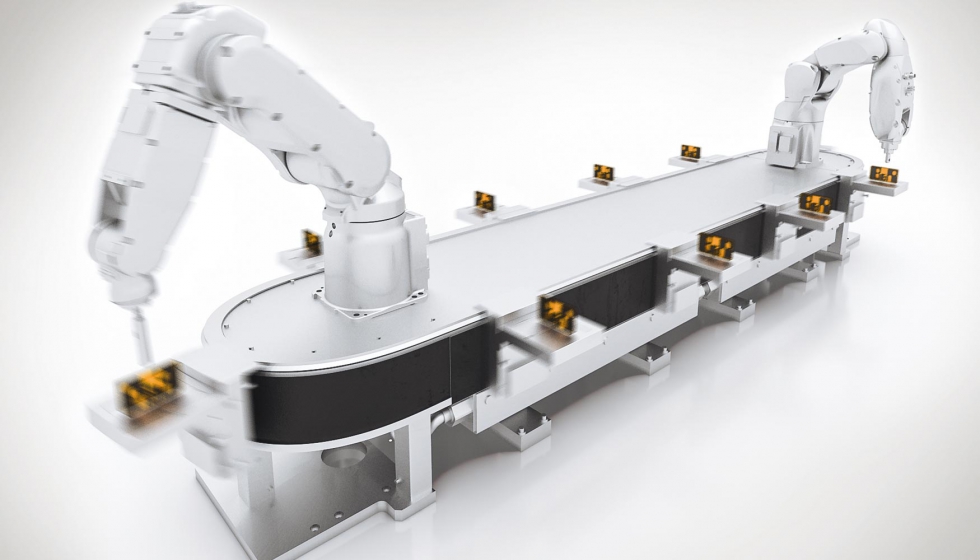
El aspecto vital de la producción personalizada
Los sistemas de transporte representan a menudo un cuello de botella en el ciclo de producción, por lo que deben poseer unas características de flexibilidad, integración y facilidad de mantenimiento similares, cuando no superiores, a las de las otras piezas móviles.
Proyectando la disposición del sistema para optimizar el tamaño de la línea y programando adecuadamente la clasificación lógica de los productos, puede variarse la velocidad y la aceleración de cada pieza individual también de forma reactiva. Teniendo en cuenta los flujos de producción pueden evitarse los atascos, así como los impactos de productos entre sí o el derrame de los líquidos. De esta forma se mejora la calidad final del producto, se mantienen las líneas limpias, se reducen los residuos y puede aumentarse el rendimiento también en lotes de pocas unidades, incluso hasta de un solo producto. Esta es la personalización en serie.
Con los años se ha pasado de las cintas transportadoras con transmisiones mecánicas a los servo ejes con levas electrónicas. Ahora es el momento de dar un nuevo paso adelante en los sistemas de transporte.
El transporte industrial inteligente - ¿Cómo funciona?
Las soluciones de transporte lineales de nueva generación permiten formar unas líneas compactas y flexibles para la producción eficiente de lotes de cualquier tamaño, incluso unitarios.
La tecnología LLM ('Long-stator Linear Motor', o 'motor lineal con estátor largo'), que es la base de SuperTrack, permite manipular los objetos en producción de una forma rápida, precisa y programable, aplicando comportamientos inteligentes.
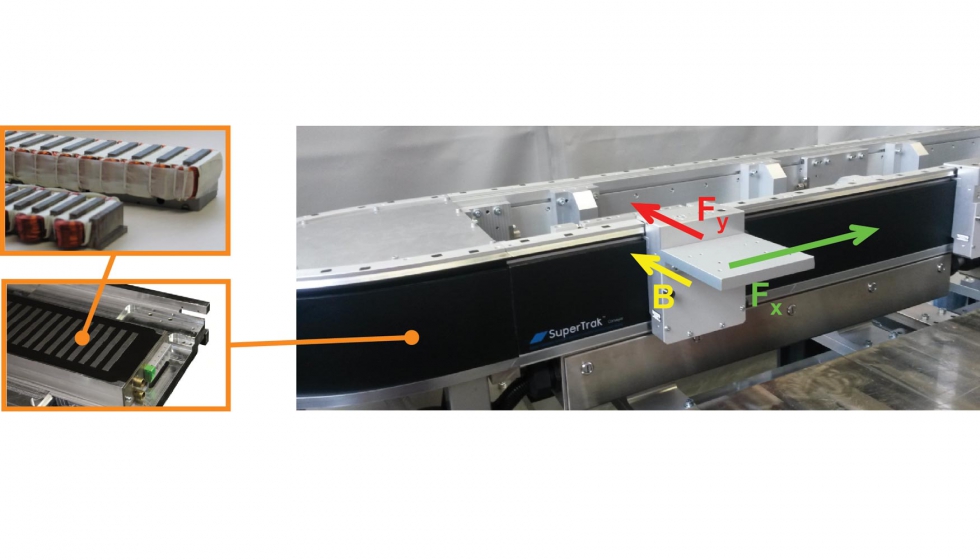
El componente principal de este motor de inducción es un estátor lineal con una longitud de hasta 50 m.
El componente principal de este motor de inducción es un estátor lineal, normalmente de forma ovalada, que combina diversos módulos curvados y rectos hasta formar una línea de transporte de las dimensiones deseadas, con una longitud máxima de hasta cincuenta metros. En la parte interna del estátor encontramos las bobinas de excitación. Encima del estátor, y formando parte integral de él, encontramos un raíl que sirve como guía de deslizamiento para las lanzaderas de transporte.
El componente secundario del LLM no está formado por un solo objeto, sino por varias lanzaderas que se deslizan por la guía situada en el estátor. Estas lanzaderas o plataformas de transporte disponen de unos imanes fijos que los mantienen adheridos al estátor y que, en respuesta al campo generado por éste, desarrollan a su vez el campo inducido que genera la fuerza de propulsión necesaria para mover las propias lanzaderas.
Por lo tanto, a diferencia de los motores rotativos convencionales, el rotor y el estátor están como ‘desplegados’ en una línea y la excitación de las bobinas, distribuidas a lo largo de toda la línea del estátor, se controla para mover las lanzaderas de forma independiente, en lo que sería una evolución del rotor clásico. La información acerca de la posición de cada lanzadera la proporciona un conjunto de sensores distribuidos a lo largo del raíl.
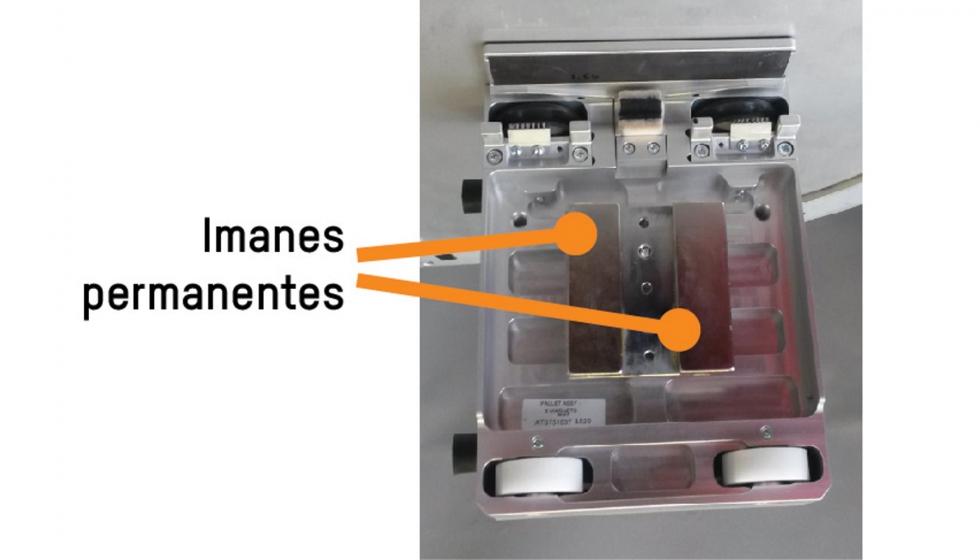
El componente secundario del LLM no está formado por un solo objeto sino por varias lanzaderas independientes.
Flexibilidad y alta tolerancia a los fallos en la producción
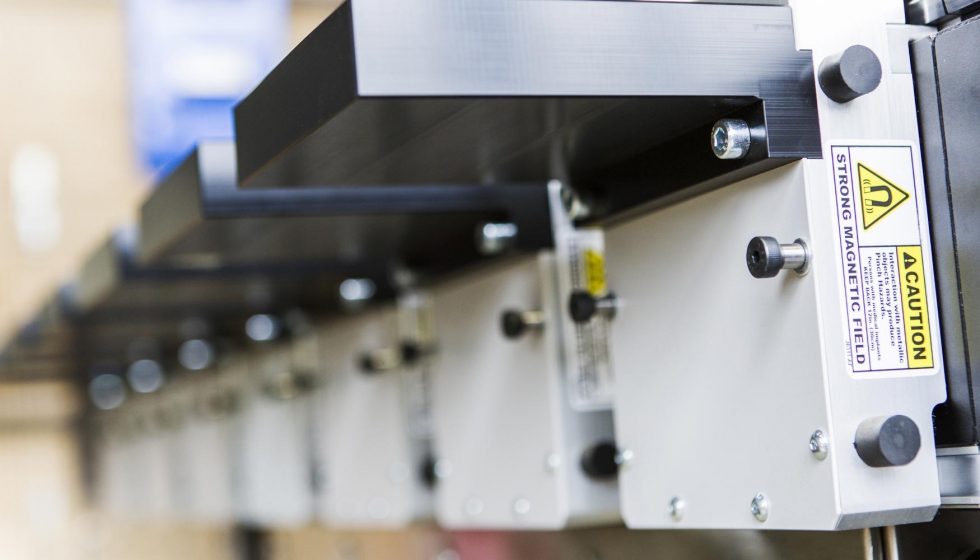
Como hemos dicho, el número de lanzaderas varía según las necesidades y pueden disponer de una superficie de apoyo o de una toma personalizada. Su posición se mide y controla con una precisión de 10 micras, claramente superior a la que puede obtenerse con las cintas transportadoras convencionales.
Puesto que se controlan individualmente, pueden moverse de forma sincronizada o individual, cada uno con su velocidad y aceleración. También pueden coordinarse por ejemplo de dos en dos, para transportar un único objeto con más puntos de agarre. La posibilidad de controlar totalmente cada una de las lanzaderas, independientemente de las otras y de forma integrada con las máquinas, perfecciona el funcionamiento del sistema de transporte y mejora el rendimiento general de la línea.
Para entender cómo, tomemos el ejemplo de una máquina de llenado: supongamos que una de las boquillas de llenado no funciona correctamente (tiene algún defecto de calibración, pierde líquido o está obturada). Pues bien, pueden programarse las lanzaderas para que las botellas no se detengan debajo de esa boquilla concreta, desactivándola para evitar producir botellas que deberían descartarse por no haberse llenado correctamente.
Esta excepción, con un sistema inteligente programado como SuperTrak, se realiza a través del software simplemente eligiendo el interface de control de la boquilla concreta y desactivándolo con un simple toque en la pantalla táctil. Todo ello sin necesidad de parar la máquina. Una vez sustituida la boquilla o el sensor, o eliminada la causa de la avería sea cual sea, puede reactivarse la boquilla para que las lanzaderas vuelvan a detenerse debajo de ella.
Adecuado para entornos difíciles
SuperTrak ha sido especialmente desarrollado para su funcionamiento ininterrumpido en entornos industriales, que por naturaleza son difíciles. Por esta razón, tanto su carcasa como todas las partes móviles han sido diseñadas para componer un sistema fiable, seguro y con un mantenimiento extremadamente sencillo.
El mantenimiento de los segmentos individuales del estátor y las lanzaderas puede realizarlo fácilmente una sola persona, sin utilizar herramientas especiales. Si es necesario, puede sustituirse fácilmente cualquier tramo del estátor, accediendo solo a él y sin necesidad de desmontar parte del circuito. La pista se restablece en cuestión de minutos y el sistema puede reiniciarse.
El mantenimiento ordinario de las lanzaderas también es muy sencillo, y no es necesario que intervengan técnicos especializados: basta con enganchar la lanzadera a una barra con dos chavetas de fijación, hacer palanca y separar la lanzadera del estátor (al cual está adherida por simple contacto magnético). Y ya está. Se limpian las ruedecillas, se lubrica un poco y vuelve a colocarse.
La única superficie de contacto entre la lanzadera y el estátor es la de la guía, por lo que la fricción creada es muy baja. Ello, además de generar menos calor y de reducir la cantidad de energía disipada, garantiza un nivel de ruido bajo.
La menor fricción también comporta que no sea necesario utilizar demasiado lubricante y que se genere un menor número de partículas por la abrasión. El raíl se mantiene limpio y bien lubricado durante largos períodos de tiempo y muchos ciclos de actividad, se ahorra aceite y se mejoran los periodos de mantenimiento. Todo ello se traduce en un tiempo medio de reparación y mantenimiento muy bajo, aumentando el nivel de productividad de toda la planta.
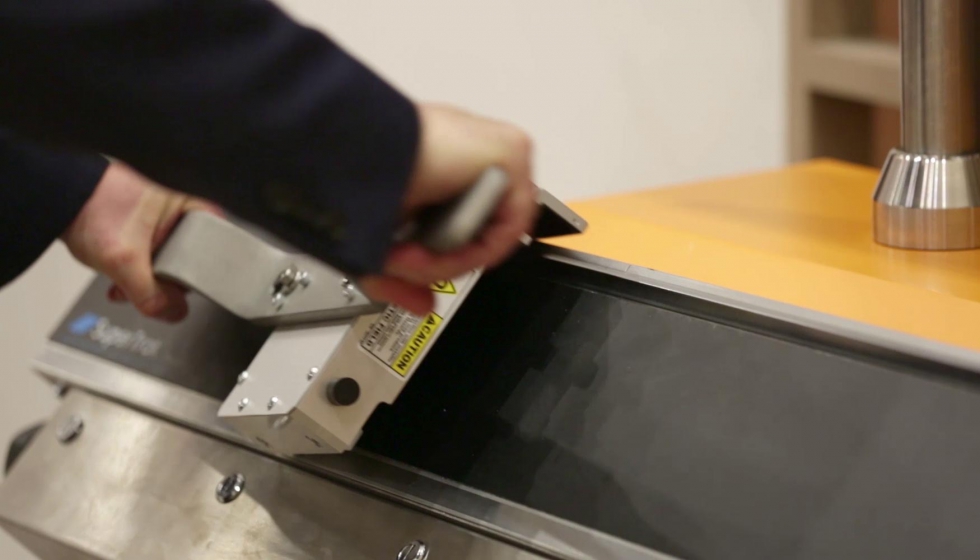
Los trabajos de mantenimiento en las lanzaderas son sencillos y no se requieren conocimientos ni herramientas especiales.
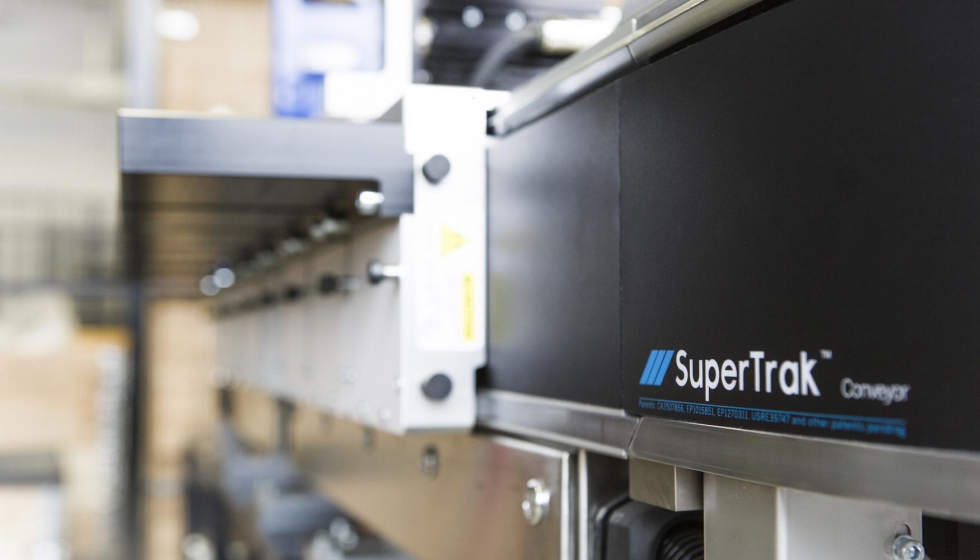
Los segmentos de la pista y las lanzaderas pueden sustituirse fácilmente sin necesidad de desmontar la pista.
Un eje como los otros...
Volvamos al tema de la integración y la interconectividad, unos aspectos esenciales si se desea conseguir una fábrica inteligente. SuperTrak, al igual que todos los demás tipos de ejes presentes en las líneas, incluidos los sistemas de control numérico y los robots, se controla y programa desde el entorno único de desarrollo Automation Studio de B&R. Las lanzaderas individuales también pueden coordinarse con los componentes de control numérico y con los robots presentes en la línea, creando un sistema automatizado que puede realizar eficazmente cualquier secuencia de producción.
Además de una perfecta sincronización, permite implementar una sofisticada lógica de control a toda la línea. El resultado es un mayor rendimiento, una alta calidad de los productos y una menor cantidad de residuos.
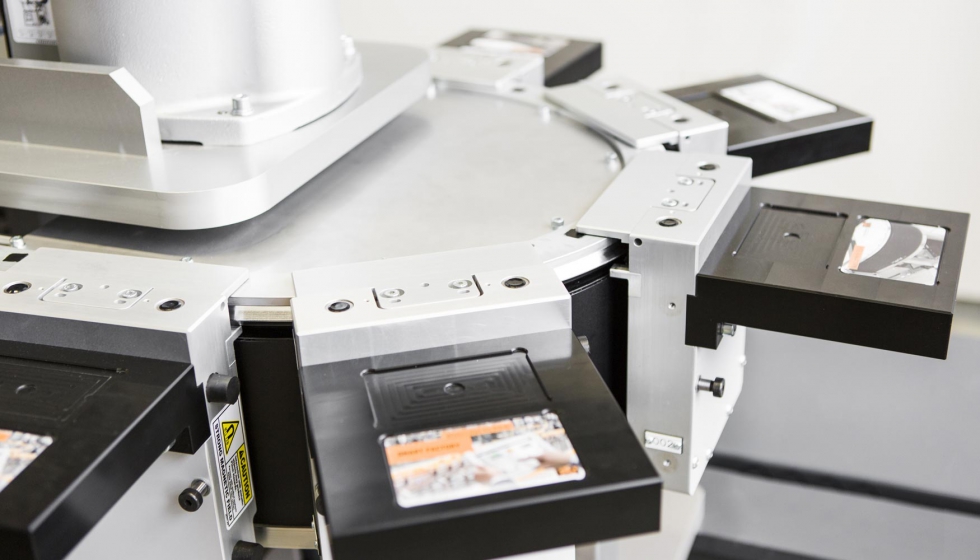
Gracias a la integración de SuperTrak en el sistema de control, la sincronización con los sistemas de control numérico, los robots y los demás ejes es perfecta, incluso en las curvas.
Integrado y conectado
La integración con el sistema de control de la máquina, gracias a la programación en Automation Studio, abre un sinfín de posibles aplicaciones.
Mientras una lanzadera se desplaza a lo largo de la línea transportando un producto, un brazo robótico puede realizar diversas operaciones siguiendo trayectorias complejas. Supongamos que dos lanzaderas se desplazan sosteniendo un objeto y que un robot antropomórfico sigue su trayectoria para efectuar un marcado. Una aplicación como ésta requiere una sincronización perfecta de 8 ejes: 6 para el robot y 2 para las lanzaderas. Imaginemos ahora que esto ocurre mientras las lanzaderas se deslizan sobre un tramo curvo del estátor... ¿Parece imposible? Pues es lo que ocurre normalmente en la producción con un sistema SuperTrak.
La comunicación, basada en el protocolo Ethernet Powerlink en tiempo real, garantiza que la sincronización de los ejes se realiza de una manera determinista, rápida y segura.
El hecho de poder programar el comportamiento de las lanzaderas de forma independiente conlleva otras ventajas. Por ejemplo, puede acelerarse una lanzadera cuando se tiene vía libre hacia la siguiente estación de trabajo, reduciendo el tiempo de transporte de las piezas y aumentando la productividad.
Además, se evitan los atascos (las acumulaciones de productos en un punto de la línea), que son el principal motivo de daños debido al derrame de líquidos o a la rotura o caída de objetos.
Pensemos una vez más en nuestra línea de embotellado, donde las botellas de cristal se deslizan velozmente debajo de la máquina etiquetadora. En vez de chocar entre sí y desgastarse, como sucede con los medios de transporte convencionales, las botellas no se tocan y quedan totalmente intactas. Así, con la misma velocidad de producción se obtiene una mejor calidad del producto.
Los atascos en la fábrica se reducen drásticamente
SuperTrak le permite elegir y variar la forma del transporte, aprovechando mejor el espacio ocupado y —gracias a la compacidad del control— dejar un espacio vacío en la parte central, que puede utilizarse para colocar otros dispositivos (sensores, actuadores, robots, etc.). En la gran mayoría de los casos, ello conlleva una notable reducción de los atascos en la planta.
Los productos se guían en cada etapa del proceso mediante un sistema inteligente que gestiona cada una de las lanzaderas, controlando el transporte de cada producto individual y entregándolo en el siguiente punto de la fabricación, justamente en el momento adecuado.
A diferencia de las cintas transportadoras convencionales, con SuperTrak se reduce la necesidad de emplear zonas de recogida que actúen como zona intermedia entre una máquina y otra. La eliminación de dicha zona intermedia contribuye enormemente a la reducción del tamaño general.
Cambio rápido mediante el software
SuperTrak optimiza los tiempos de conmutación necesarios para los distintos productos fabricados en la misma línea. Los prolongados tiempos de inactividad necesarios para cambiar las guías y otras partes mecánicas se han reducido sustancialmente o se han eliminado por completo.
Ello se debe a que, de acuerdo con la filosofía de integración completa implementada por B&R, el sistema de transporte está programado en el entorno omnicomprensivo de desarrollo del software Automation Studio. Los programadores pueden aprovechar las numerosas bibliotecas y módulos de funciones, listos para configurar el movimiento de las lanzaderas mediante el software. Tan pronto como el operario selecciona otro trabajo desde el panel, el sistema de transporte cambia automáticamente y se adapta a las nuevas dimensiones y al nuevo proceso.
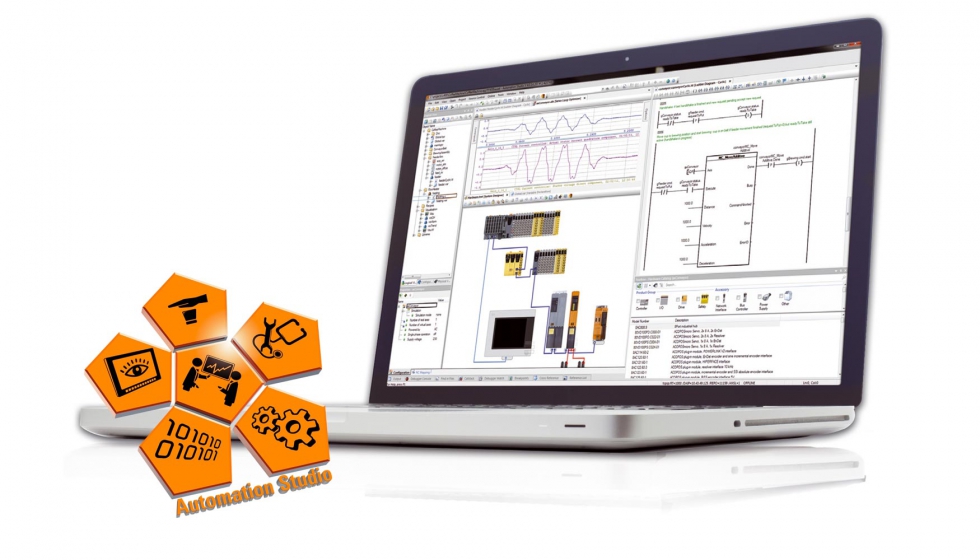
La programación del nuevo sistema de transporte lineal se realiza en el entorno de desarrollo del software Automation Studio.
Comportamiento reactivo
Administrando el movimiento mediante el software puede coordinarse claramente el transporte para facilitar todas las etapas de la fabricación. Pero existe otra consecuencia, menos evidente pero gratificante, de la integración y programación del transporte en el entorno de desarrollo del software: se tiene la posibilidad de aprovechar los sofisticados algoritmos de control del movimiento, que comportan unas grandes ventajas.
Imaginemos, por ejemplo, que debe transportarse un recipiente con líquido: en un sistema tradicional, simplemente se aceleraría el producto a lo largo de su línea, normalmente con un perfil de aceleración constante hasta lograr la velocidad deseada, y después decelerando al alcanzar el punto de llegada. Lo que sucede es que el líquido empieza a oscilar y en muchos casos se derrama, se desperdicia materia prima y se debe parar la línea para limpiarla. En ocasiones el daño es incluso más grave, porque el recipiente se cae. La solución más sencilla sería reducir la dinámica para controlar las oscilaciones, pero esto influye en el índice de producción.
Existe una alternativa: se calculan los parámetros físicos del recipiente y del líquido y se aplica una técnica especial conocida como 'anti-sloshing' (antiderrames). En la práctica, se modulan la velocidad y la aceleración de forma que se minimizan las oscilaciones del líquido. El tiempo total de transporte será el mismo, o incluso mejor, y además no se producirán derrames. Podrán transportarse a alta velocidad recipientes llenos de líquido sin que se desperdicie ni una gota.
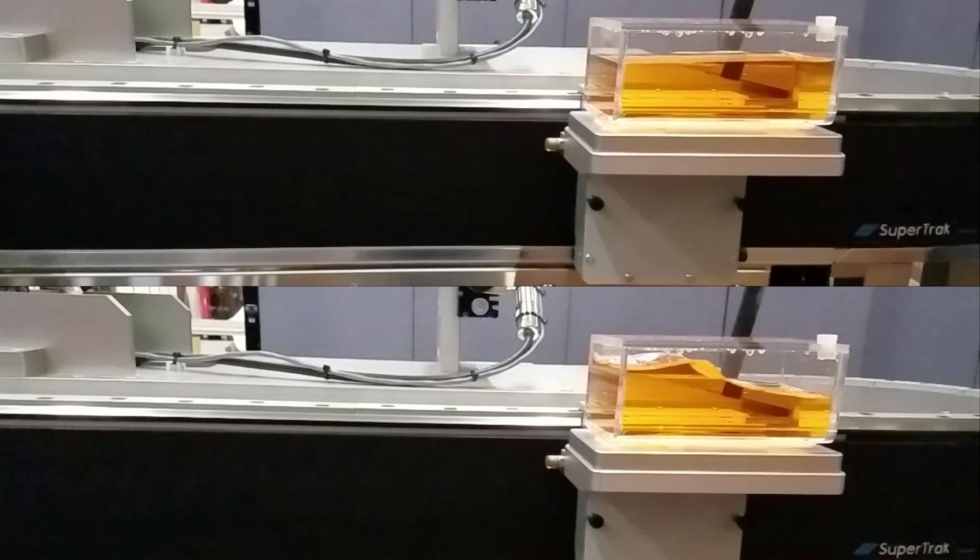
La programación con Automation Studio permite implementar sofisticados algoritmos de control del movimiento como el antisloshing (antiderrames).
Resumen de SuperTrak
SuperTrak es el único sistema de transporte inteligente del mercado con un diseño sólido y fiable, diseñado para su uso sin compromisos en entornos industriales. Fabricado para soportar elevadas velocidades durante largos ciclos sin interrupciones en entornos difíciles, se ha diseñado para garantizar un mantenimiento sencillo; así se obtiene la alta disponibilidad y la flexibilidad necesarias para la producción en serie personalizada.
Características
- Diseño sólido – Mantenimiento sencillo
- Fiabilidad de funcionamiento ininterrumpido en entornos industriales
- Cargas elevadas: 10 kg de carga útil
- Posicionamiento preciso: 10 µm
- Ejes externos sincronizados en tiempo real duro
- Integración con sistemas de control numérico y robots
- Línea con una longitud de hasta 50 m
- Programado en Automation Studio como los otros ejes de la línea
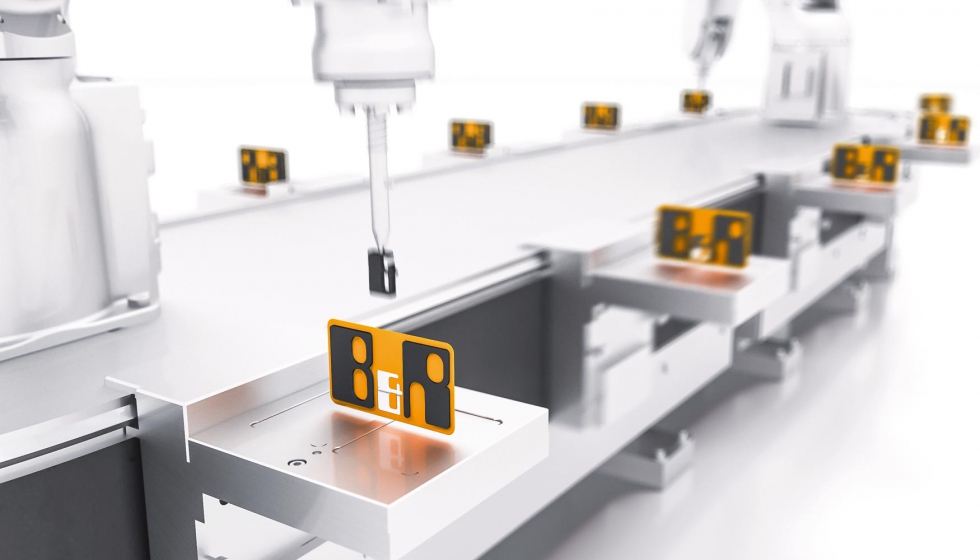
La integración y el control mediante software permiten obtener una producción rentable incluso con lotes unitarios.
Vea SuperTrak en funcionamiento
El sistema de transporte de nueva generación se mueve en perfecta armonía con un robot antropomórfico Racer3 y uno Scara Rebel-S de Comau. El vídeo muestra cómo las lanzaderas, que se mueven a alta velocidad a lo largo del circuito, están perfectamente sincronizados, incluso en los tramos curvos, con los dos robots que realizan trayectorias complejas.
También resultan evidentes los efectos conseguidos gracias al empleo de sofisticados algoritmos para el control del movimiento, tales como el anti-sloshing.
Por último, el vídeo muestra claramente cómo las operaciones de mantenimiento son sencillas y limpias.
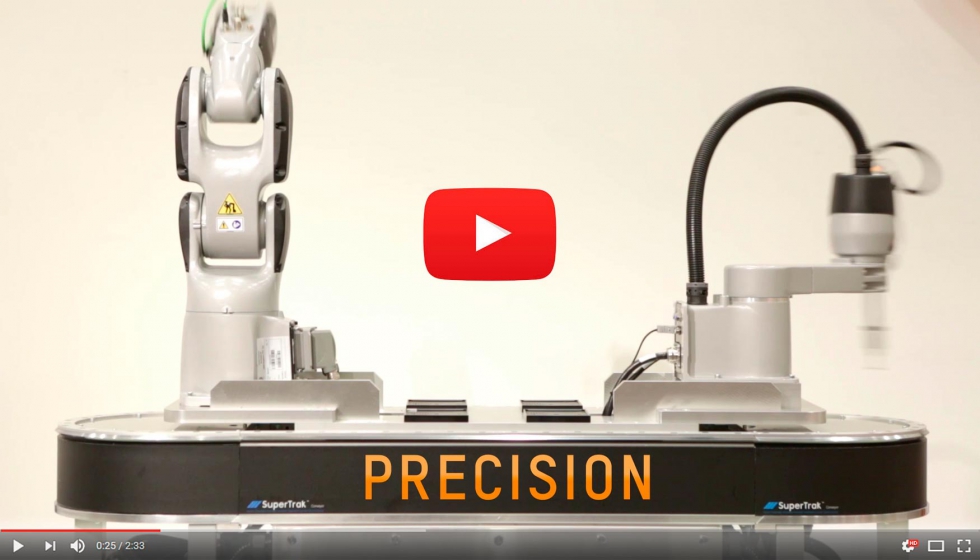