Últimos avances en el corte de acero inoxidable con tecnología plasma
Las tecnologías empleadas más habitualmente para el corte de acero inoxidable en espesores grandes son el plasma, las sierras de cinta y chorro de agua. Y en espesores pequeños el láser y la cizalla. El uso del plasma aporta principalmente (1) mayor velocidad respecto a la sierra de cinta y al chorro de agua; (2) capacidad de cortar espesores superiores que el láser o la cizalla y (3) la versatilidad de cortar en una gama mayor de espesores que va desde décimas hasta 160 mm.
La tecnología actual de corte por plasma ha mejorado notablemente en aplicaciones con acero inoxidable. Una gama más extensa de gases de corte y gases de protección, así como una mayor eficiencia permiten mejorar sustancialmente este proceso, incrementando las velocidades de corte y obteniendo acabados muy superiores. La gama de espesores finos va desde 0,8 a 6 mm, la gama de espesores intermedios de 6 a 50 mm y los espesores grandes van desde 50 a 160 mm. El último modelo de Alta Definición de Hypertherm, el HPR800XD corta acero inoxidable desde 0,8 hasta160 mm, pudiendo elegir entre una extensa gama de procesos y amperajes. Seleccionando el amperaje ideal para un espesor concreto podemos determinar el equilibrio perfecto entre productividad (velocidad) y calidad (acabado).
Algunos clientes habituados a cortar acero al carbono, que amplían su gama de corte al acero inoxidable experimentan algunas dificultades a la hora de obtener una buena calidad de corte. Deben de tenerse en consideración determinados factores para obtener resultados satisfactorios: 1) Selección del gas adecuado, 2) Velocidades de corte y 3) Tecnología necesaria para cada espesor. Cuando se corta acero al carbono, emplear el oxígeno como gas de corte y el aire como gas de protección puede resultar más que suficiente para obtener excelentes resultados en toda la gama de espesores. El acero inoxidable, en cambio, nos obliga a emplear distintos gases y tecnología de consumibles dependiendo del espesor que queramos cortar.
Una correcta selección de los gases es fundamental. La combinación aire/aire es la más habitual para cortar a alta velocidad con un coste muy reducido, sin embargo el acabado del corte queda muy oxidado y obliga en la mayoría de los casos a repasar la pieza, lo que supone incorporar operaciones secundarias al proceso. Dependiendo del acabado necesario, existen distintas soluciones. Usar nitrógeno como gas plasma y gas de protección (N2/N2) nos permitirá aumentar la velocidad de corte, al tiempo que obtenemos un acabado más limpio y sin restos de óxido, aunque permanece ese color negro característico similar al del corte con Aire/Aire.
Otra característica que se da habitualmente con esta combinación es el borde superior redondeado y un exceso de angularidad.
Aquellos usuarios que busquen mayor definición, un aspecto brillante, borde superior definido con poca angularidad y poca rebaba deberán emplear gases especiales. Los gases de plasma que incluyen una proporción de hidrógeno mejoran la definición de los bordes y mantienen el color original del metal. Los 2 gases especiales más habituales son el H35 (35% hidrógeno y 65% argón) y F5 (5% hidrógeno, 95% Nitrógeno).
Ventajas y desventajas de las distintas combinaciones de gas:
Gas plasma |
Gas protección |
Resultado |
Aire |
Aire |
Pro: Rápido, poca rebaba, bajo coste, bordes definidos |
Contra: Superficie ennegrecida, áspera y altamente oxidada. Se requiere repasar la pieza |
||
N2 |
N2 |
Pro: Superficie menos rugosa que con aire. Poco óxido |
Contra: Borde negro, borde superior redondeado y angularidad |
||
Agua |
Pro: Bordes plateados, borde superior definido, bajo coste, no humos |
|
Contra: Gestión de residuos (agua sucia), posibilidad de colisión de la antorcha si se corta bajo agua |
||
F5 |
N2 |
Pro: Bordes plateados, borde superior definido y poca angularidad |
Contra: Limitación de espesor de corte. Máx. 20mm |
||
H35 |
N2 |
Pro: Color dorado y/o azulado y bordes muy bien definidos |
Contra: Mezcla de gas no disponible en todos los países. Sólo a partir de ciertos espesores (deja rebaba en espesores finos) |
Diferencias visuales provocadas por distintos gases en acero 304L:
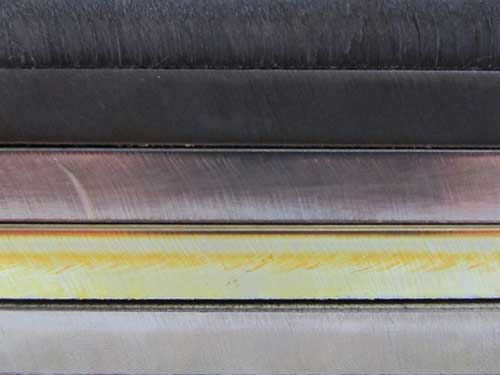
Esto nos lleva a la siguiente consideración: para obtener buenos resultados cortando acero inoxidable con plasma es básica una selección adecuada del material. El 304L es un acero austenítico y el más empleado a nivel mundial. Cuando empleamos los mismos parámetros para cortar 304L que cualquier otro acero austenítico, por ejemplo el 316L, se puede generar rebaba.
Resultado de emplear los mismos parámetros de corte con el 304L que con el 316L en 5 mm:
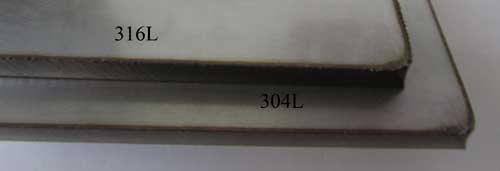
En el 304L el corte es limpio y apenas se genera rebaba. Para obtener un corte aceptable en el 316L usando los parámetros del 304L es necesario aumentar ligeramente la velocidad de corte y la presión del gas de protección. Cada material reacciona de manera diversa al efecto del plasma. La extensa gama de aceros inoxidables existentes obliga a disponer de una amplia variedad de tablas de corte para obtener buenos resultados.
- Otra dificultad que plantea el corte de acero inoxidable con tecnología plasma es la aparición de restos de material fundido. Si cortamos acero al carbono con O2/Aire, la dureza de la rebaba es mucho menor que cortando acero inoxidable, por lo que la rebaba resultante en la parte inferior de la chapa se elimina fácilmente. En cambio, la rebaba que se forma al cortar acero inoxidable es mucho más difícil de eliminar. Los siguientes 5 factores pueden reducir e incluso llegar a eliminar la formación de rebaba sobre el acero inoxidable:
- Estado del generador
- Selección de gas
- Presión de gas
- Velocidad de corte
- Altura de corte
Un método para prevenir la formación de rebaba es el de hacer girar el gas de protección en sentido contrario al del gas plasma. Esto favorece que la rebaba se adhiera al esqueleto (o resto de la chapa) en lugar de a la pieza cortada.
Perforar acero inoxidable presenta dificultades debido a las propiedades del material derretido. La rebaba se acumula alrededor de las perforaciones en la parte superior de la chapa y genera problemas a la hora de anidar las piezas en el programa y dificulta el movimiento de la antorcha. Para perforar acero inoxidable de más de 50 mm es preciso ajustar el desplazamiento de la antorcha para esquivar las acumulaciones de material que se han generado después de perforar. Otro sistema es perforar, parar, eliminar los restos de material y proceder a cortar la pieza una vez quede sin residuos sobre la superficie.
Restos de material después de perforar: La altura de los restos supera la altura de corte normal de la antorcha
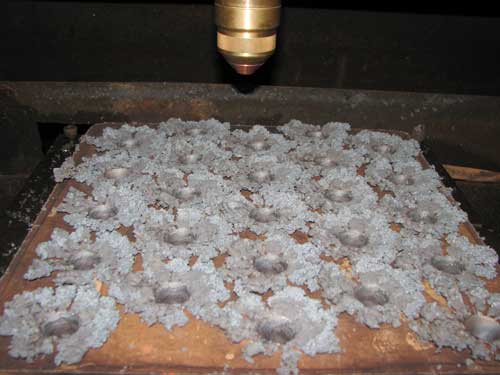
Avances técnicos recientes
La calidad de corte en acero inoxidable de espesor pequeño se obtiene con la tecnología Alta Definición de Hypertherm, desarrollada en un principio para aplicaciones en acero al carbono. Por primera vez, se ha aplicado esta misma tecnología al corte de acero inoxidable obteniendo excelentes resultados. La combinación de alta presión de gas y la boquilla ‘vented’ favorecen una constricción mayor del arco plasma y en consecuencia una calidad de corte superior. Cuando la constricción del arco es mayor podemos emplear una boquilla con un orificio más pequeño y una densidad mayor de energía. El nuevo diseño de la boquilla incrementa su vida útil gracias a flujos de aire a mayor presión, que a la vez que mantienen los consumibles más refrigerados, permiten constreñir aún más el arco.
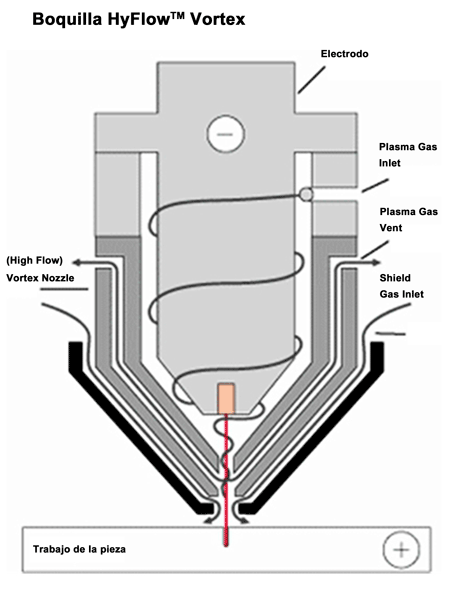
HDi (HyDefinition inox), la nueva tecnología de Alta Definición de Hypertherm específica para acero inoxidable se traduce en una excelente definición del borde superior, acabados limpios y una angularidad inmejorable. Las tecnologías más avanzadas tanto en el diseño de las antorchas como de los consumibles favorecen una calidad de corte constante, así como una mayor vida útil de los consumibles.
Los avances obtenidos en los espesores de corte pequeños y medios nos llevan de nuevo a la correcta selección de los gases: Empleando H35 eliminamos el óxido en los bordes garantizamos una buena calidad de corte y un aspecto limpio, pero desde un punto de vista de productividad resulta muy lento. El nitrógeno aporta velocidades de corte mucho mayores que mejoran la productividad, pero el borde cortado queda oxidado. Con la consola de gas automática del HPR podemos mezclar H35 y N2 como gas plasma para obtener una velocidad de corte razonable, manteniendo un aspecto bonito de los cortes
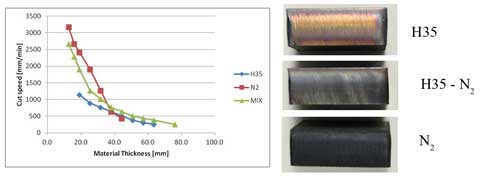
Una correcta selección de la mezcla de gases para cada material es básica para conseguir un equilibrio adecuado entre aspecto y velocidades de corte. Una combinación de gases con exceso de N2 generará un acabado entre gris y negro y posiblemente rebaba. Demasiado gas H35 generará un color dorado sobre la superficie cortada y cierta rebaba.
La tecnología patentada PowerPierce mejora ambos procesos de corte, acero al carbono y acero inoxidable, sobre una amplia gama de espesores, y es la responsable de poder perforar y cortar espesores en acero inox más allá de los alcanzados hasta la fecha. El escudo exterior refrigerado por líquido, evita que se adhieran las proyecciones de metal durante la operación de perforado.
Nueva tecnología
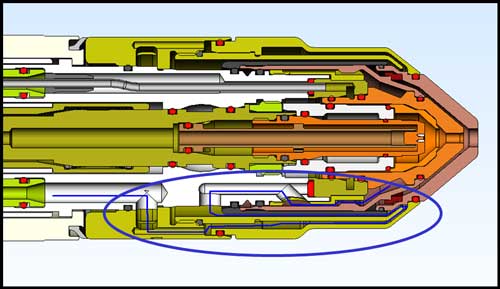
La tecnología del escudo refrigerado evita que las proyecciones de metal se adhieran
- Reduce significativamente la adhesión de partículas metálicas al escudo exterior
- Evita el fundido de las juntas tóricas del interior de la antorcha por la acción del calor
- Reduce los fallos de lectura durante la operación de palpado para determinar la altura
- Evita la obstrucción de los orificios de ventilación del escudo exterior
- Evita que se derritan los orificios
La tecnología para perforar espesores máximos emplea un sistema de seguimiento de antorcha que permite pasar de perforar 45 a 75mm en el caso del HPR400XD y de 75 mm hasta 100 en el caso del HPR800XD. Ensayos realizados en el laboratorio dieron un número máximo de perforados de 50 piezas a 400 A; mientras que se obtuvieron 25 a 800 A.
El nuevo proceso que se muestra a continuación es característico por el tiempo de perforado reducido. En esencia, combina el desplazamiento con la altura de la antorcha, para crear una vía de evacuación para la escoria y que de esta manera no permanezca en el interior del agujero. Por otro lado evita que la escoria caliente esté próxima al extremo de la antorcha. El perforado se realiza los más alejado posible de la chapa, siempre que el generador nos permita seguir manteniendo el arco sin extinguirse y entonces se desplaza la antorcha a cierta velocidad para crear la vía de escape. En el momento en que la antorcha comienza a descender, su desplazamiento cada vez más lento, hasta que se consigue finalmente el perforado y se fija la velocidad normal de corte.
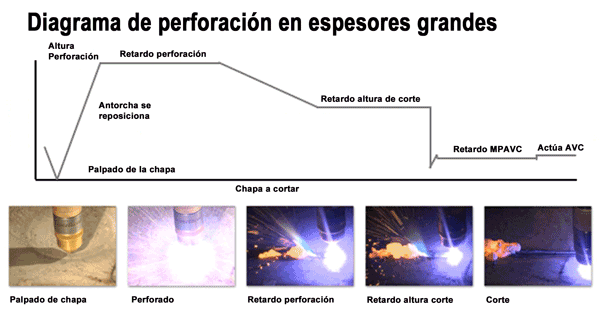
Resumiendo, el uso del plasma para corte de acero inoxidable, tanto en espesores pequeños como grandes puede resultar muy productivo. Una correcta selección de los gases nos aportará cortes limpios y de alta calidad. Las últimas tecnologías mejoran los procesos de corte de acero inoxidable en todos los rangos de espesores.