El PVC se vuelve todavía “más caliente”
Su potencial en este campo, sin embargo, dista mucho de estar agotado. Uno de los principales desafíos que presenta esta amplia utilización del PVC reside en su relativamente baja resistencia al calor. La mayor parte del género PVC se recomienda para temperaturas de trabajo no superiores a 60 o 65°C (con picos hasta 80°C). Más allá de este punto el material se reblandece. Esto tiene consecuencias negativas para su estabilidad dimensional, sobre todo cuando el elemento en cuestión está sometido a cargas mecánicas de algún tipo. Ejemplo concreto del problema lo tenemos en las tuberías de agua caliente o en paneles oscuros expuestos a la luz solar directa (Figura 1).
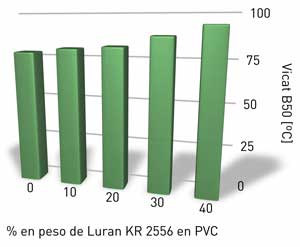
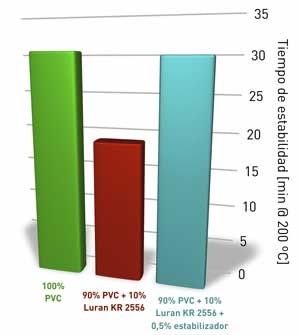
Cómo incrementar la resistencia al calor
Una solución a este problema consiste en utilizar mezclas de PVC y polímeros que tengan una alta temperatura de transición vítrea relativamente alta en comparación con la del cloruro de polivinilo. La mezcla correspondiente debería tener una resistencia térmica mayor que la del PVC puro. Una medida útil para la resistencia al calor de un material plástico nos la proporciona su temperatura de reblandecimiento Vicat B50.. En plásticos de baja cristalinidad la temperatura Vicat guarda correlación con la temperatura de transición vítrea, la cual es predecible en función de una relación simple entre las proporciones de los componentes de una mezcla (relación Gordon-Taylor). Para aumentar la resistencia del PVC al calor, este polímero ha de ser mezclado con cantidades convenientes de otro caracterizado por poseer una elevada temperatura de transición vítrea.
Los copolímeros a-metilestireno-acrilonitrilo (Amsan) se distinguen por una alta afinidad con el PVC a la vez que por una temperatura de transición vítrea elevada. Uno de estos copolímeros (Luran KR 2556) ha sido utilizado por Basf desde comienzos de la década de los 70 en la elaboración de plásticos ABS altamente resistentes al calor (Terluran HH 106 y Terluran HH 112; el número tras los códigos HH indica la temperatura de reblandecimiento Vicat del tipo High Heat correspondiente). En función del nivel de resistencia al calor que se desee, AMSAN substituye una parte del componente SAN habitual (la temperatura Vicat del SAN es prox. 107°C, alcanzando la de Amsan aprox. 120°C).
La idea de utilizar Amsan -o incluso SAN o ASA- para incrementar la resistencia térmica del PVC ha sido debatida durante largo tiempo en el sector. En la actualidad los experimentos realizados por el Centro de Plásticos de Alemania del Sur (SKZ = Süddeutsches Kunststoff-Zentrum) y Basf están ayudando a incrementar la resistencia al calor del PVC en exigentes aplicaciones, de modo económico y sin tener que pasar por la alternativa CPVC.
Elaboración de mezclas en condiciones tolerables
Los primeros experimentos con Amsan en la mezcla permitieron verificar un incremento de la temperatura Vicat mediante la adición de este polímero. Por cada 10 por ciento en peso de Amsan agregado la temperatura Vicat se incrementó aproximadamente en 4°C (Figura 3). En línea con lo esperado, este valor técnicamente relevante supera a los obtenidos mediante adición de cantidades equivalentes del copolímero SAN “clásico” así como de variedades ASA con temperaturas de transición vítrea correspondientemente más bajas.
Por lo general todas las mezclas suelen exhibir menor estabilidad térmica que el polímero de origen. Mientras que las mezclas formadas por PVC y Terluran HH 106 (ABS) o 112 y Luran S 778 T (ASA) se distinguen por unos valores de resistencia al impacto ligeramente mayores, y en ocasiones mucho más altas gracias a una proporción mayor, el incremento en temperatura Vicat y por consiguiente en resistencia al calor como resultado de los cambios en la proporción de Amsan al mismo tiempo trae consigo determinadas pérdidas en cuanto a resistencia a impactos.
Uso de estabilizadores para mejorar la estabilidad térmica
Existen numerosas posibilidades para estabilizar el PVC contra este proceso de degradación. Por ejemplo, la reacción puede ser inhibida mediante captura del cloruro de hidrógeno por aditivos básicos o bien convirtiendo el primer producto intermedio de la descomposición -reactivo alilcloruro- en substancias inocuas. A tal finalidad el fabricante de PVC dispone de gran número de aditivos de demostrada eficacia que actúan según diversos principios de funcionamiento.
Para comprobar si un aditivo estabilizado resulta idóneo para retardar la reacción de descomposición catalítica en presencia de polímeros que contienen nitritos, se llevaron a cabo algunos experimentos con mezclas (PVC+ABS) en el Centro de Plásticos de Alemania del Sur. No solamente se estudiaron los estabilizadores considerados, sino también las cantidades en que era preciso agregarlos. Se procedió a evaluar la estabilidad de cada mezcla en un flujo de hidrógeno calentado a 200°C (DIN 53381-1, ensayo B).
Incluso una ínfima cantidad del estabilizador adecuado resulta suficiente para retardar de modo eficaz la degradación térmica de las mezclas (PVC+ABS). Obviamente se trata de resultados extrapolables a las mezclas (PVC+Amsan).
En un ensayo directo, la adición de un 0,5 por ciento en peso del citado estabilizante bastó para elevar la estabilidad térmica de una mezcla de cloruro de polivinilo + copolímero _-metilestireno-acrilonitrilo (90:10 por ciento en peso: proporción total de nitrilo: alrededor de un 3 por ciento) hasta los niveles correspondientes al PVC en estado puro
Conclusiones
De esto puede derivarse un considerable potencial para aplicaciones que hasta la fecha resultaban irrealizables o problemáticas debido a factores de coste asi como a la baja resistencia térmica inherente al PVC. Las perspectivas para estas mezclas son especialmente prometedoras en el sector de la construcción. En este campo se nos mostrarán con seguridad en el futuro soluciones verdaderamente notables.