CAM y modelos, lo que el futuro nos puede pedir
La utilización de la simulación para predecir el comportamiento de un material mecanizado pretende estudiar la influencia de los parámetros de mecanizado (geometría de herramienta, estrategias y condiciones de corte, etc.) sobre el rendimiento de la operación. Los modelos permiten reducir el número de piezas que se desechan debido a los errores producidos durante el proceso de fabricación de las mismas.
En esta línea, los fabricantes de los softwar de CAM también se actualizan día a día integrando en sus software nuevas aplicaciones que pretenden proporcionar una mayor robustez al propio proceso de mecanizado estando algunas de ellas basadas en la modelización del proceso o en funciones que permiten la optimización del proceso.
Modelización del proceso de mecanizado
La simulación de procesos de mecanizado ha sido un campo de estudio tradicional en universidades y centros tecnológiucos, pero que no se ha empleado en la industria hasta hace pocos años. De hecho, son muchos los trabajos que se centran en el estudio de un modelo matemático para predecir los esfuerzos de corte, los valores de la rugosidad o incluso la aparición de chatter durante el proceso de mecanizado. Los primeros modelos (años 1950) de mecanizado buscaron calcular la amplitud de las fuerzas de corte con objeto de emplear este valor en los cálculos que se derivan de ésta como son la potencia consumida o el momento sobre el primer rodamiento del husillo. Este tipo de modelos se emplearon y aún se emplean en el dimensionamiento de estructuras de máquinas, accionamientos, husillos, portaherramientas, etc. Estos modelos se basan en datos exclusivamente experimentales. En los años 50 El National Center for Manufacturing Sciences (NCMS) publicó un extenso handbook de mecanizado que contenía gran cantidad de coeficientes e índices de maquinabilidad para las aleaciones más comunes. Sin embargo, este tipo de modelos no consiguen precisar ni el valor exacto de la fuerza ni su variación a lo largo del tiempo.
Por otra parte, desde los años 40 se había estudiado de una forma detallada la denominada Mecánica del Corte buscado relacionar la geometría de operaciones de corte sencillas con el comportamiento del material, obteniéndose así un grupo de valores característicos de la operación tales como la tensión de cizalladura, el ángulo de cizalladura, y el coeficiente de fricción. A pesar de todo, estos métodos solamente son aplicables al mecanizado con herramientas de geometría muy sencilla y aún hoy están en permanente discusión, siendo su aplicación industrial prácticamente nula.
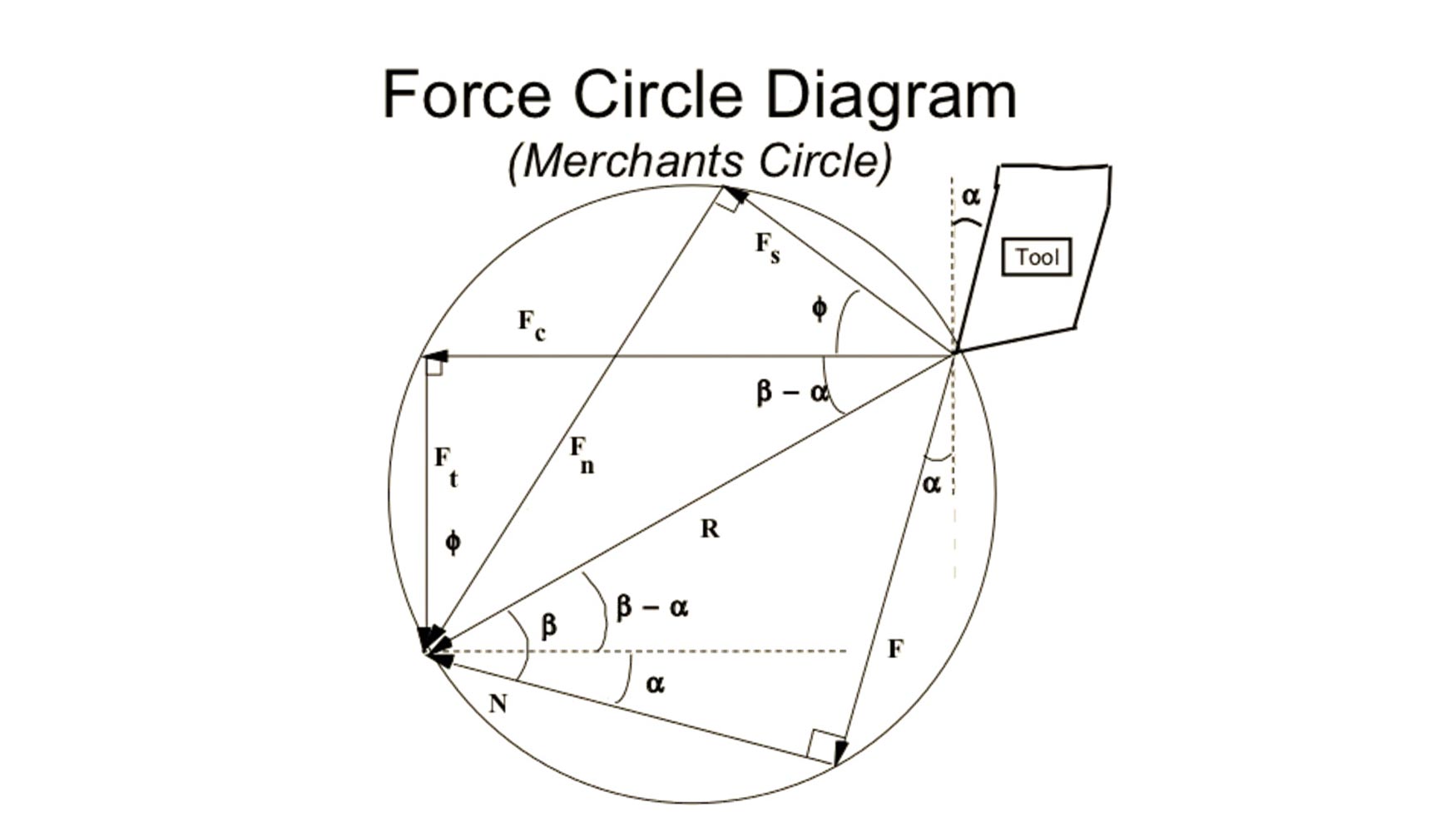
Por otro lado, destacan también los denominados métodos numéricos que estudian la mecánica del corte utilizando el método de los elementos finitos que permite el estudio de campos de tensiones, temperaturas en la zona de corte y deformaciones. Entre los mayores inconvenientes que presenta este enfoque están la dificultad de caracterizar adecuadamente el comportamiento del material a las altas temperaturas y velocidades de deformación, el estudio del rozamiento entre viruta y cara de desprendimiento, y que los tiempos de cálculo aún son demasiado elevados, del orden de días o incluso semanas.
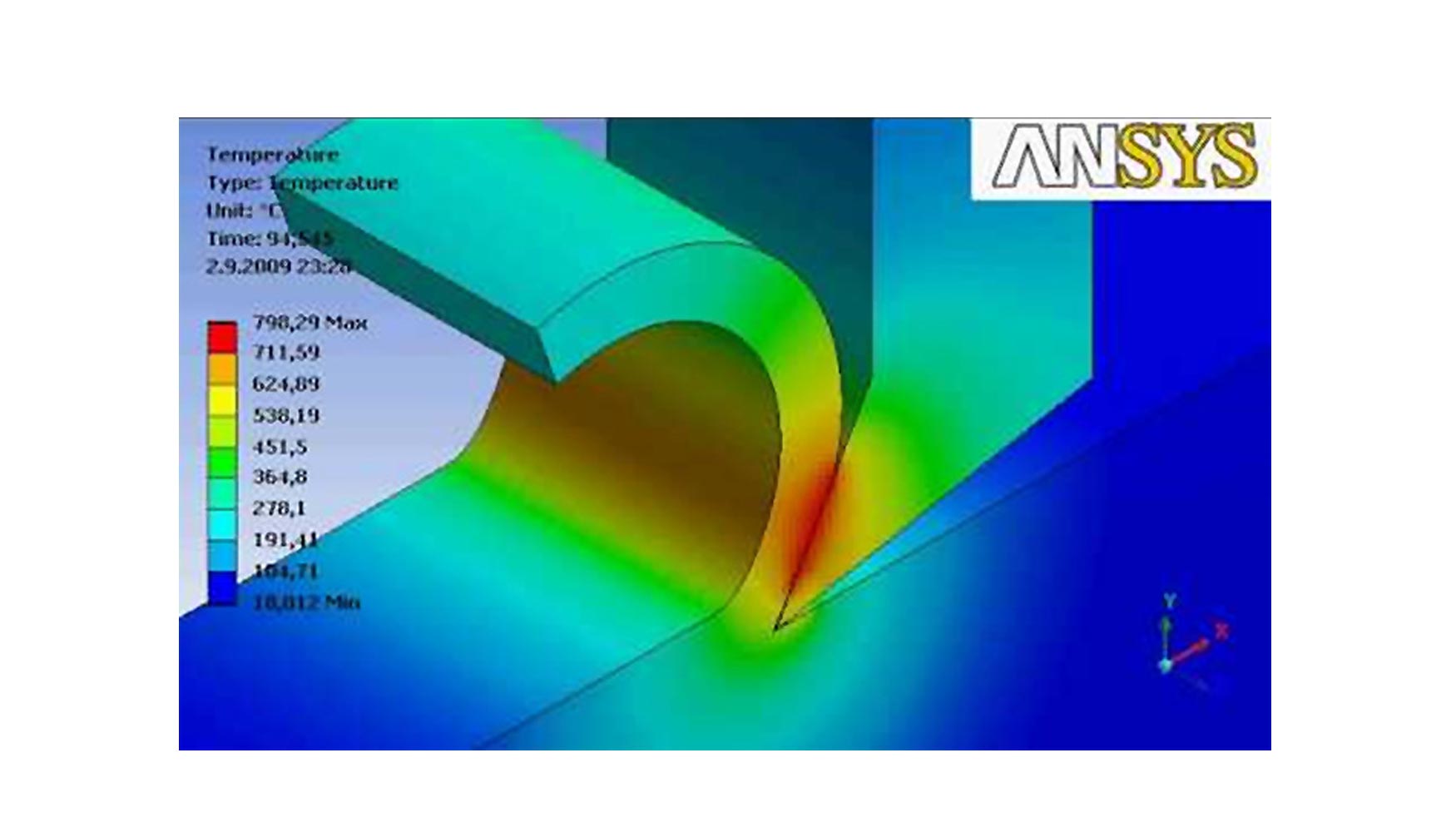
A diferencia de los métodos anteriores, los métodos estáticos y dinámicos tienen en cuenta la rigidez estática y los parámetros modales del sistema para obtener las fuerzas de corte. Este tipo de métodos se centra en el estudio del chatter entendido como un fenómeno regenerativo ampliamente aceptado como causa de las vibraciones autoexcitadas en máquina herramienta. El mayor inconveniente es su coste computacional y las simplificaciones asumidas en esa línea. De hecho, una de las principales dificultades a la hora de emplear este tipo de simulacionss de forma efectiva es poder disponer de datos fiables de la máquina como su rigidez, amortiguamiento, etc. La introducción de este tipo de datos de forma aproximada conlleva a que este tipo de modelos no proporcione datos lo suficientemente fiables.
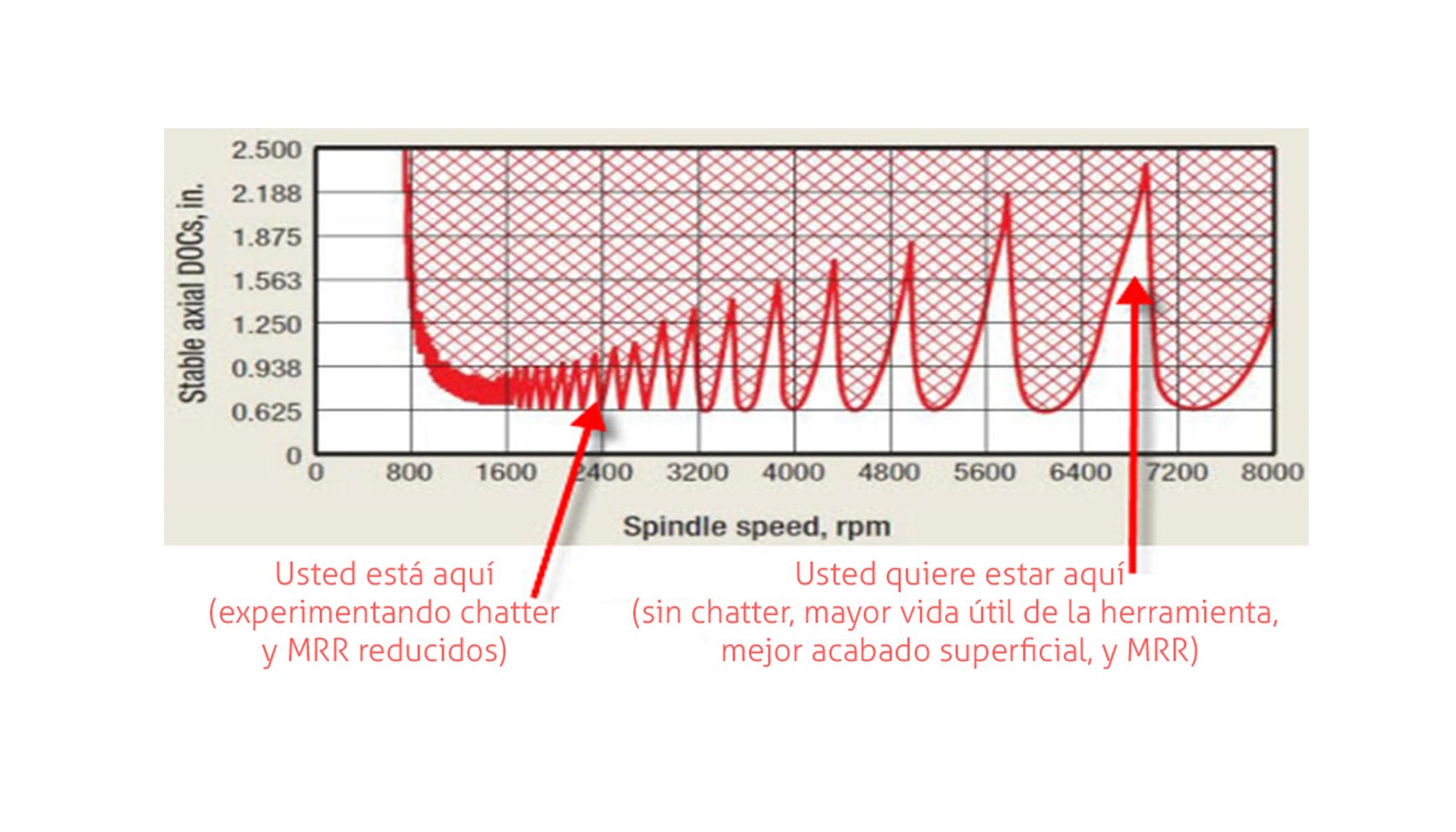
Otro grupo de destacado dentro de la modelizacion del proceso de mecanizado son los métodos empíricos que relacionan variables como el material de pieza, condiciones de corte, características de la herramienta, con las fuerzas de corte y la energía consumida. Dichas relaciones se obtienen a partir de ensayos experimentales en los que se miden las fuerzas y la potencia consumida. A pesar de todo, son métodos poco precisos que dependen en muchos casos de los datos que suministra el fabricante de las herramientas para realizar las correspondientes estimaciones.
Un enfoque mucho más preciso que los métodos puramente empíricos son los conocidos como modelos semi-empíricos, también denominados mecanísticos. Estos modelos tienen de empíricos que parten de unos coeficientes que caracterizan el binomio material/herramienta a través del cálculo de los coeficientes para cada material mediante ensayos sistemáticos. En estos métodos se considera el filo como una sucesión de elementos diferenciales. A cada elemento diferencial se le aplica el modelo propuesto y se realiza una integración a lo largo del filo para obtener la resultante de la fuerza. La integración del modelo discreto/diferencial a lo largo del filo se realiza atendiendo a la inmersión de la herramienta en el material, calculada de forma muy exacta. La gran aplicabilidad de estos métodos los hace muy adecuados para el cálculo de fuerzas de corte en mecanizados muy complejos.
Integración de los modelos de mecanizado en el software de CAM
A pesar de la cantidad de modelos de fuerzas desarrollados por muchos autores, estos modelos predictivos de fuerzas de corte no han sido integrados por los propios software de CAM como una herramienta extra a la hora de elegir las trayectorias más apropiadas para cada mecanizado. Lo que frecuentemente ocurre con estos modelos de fuerzas es que se ven limitados a ser utilizados en el propio software en el que han sido programados. Además, los datos proporcionados suelen estar desligados de la operación de mecanizado que se desea optimizar. La integración de estos modelos en un CAM permite correlacionar los datos de las fuerzas de corte estimadas con la posición de la herramienta en un punto y operación concreto.
Dado que los modelos representan una herramienta en la búsqueda de la estrategia óptima de mecanizado y condiciones de corte, a continuación se muestran un par de ejemplos de la integración modelos en un software de CAD/CAM (NX de Siemens) desarrollados en el Taller de Fabricación del Departamento de Ingeniería Mecánica de la Escuela de Ingenieros de Bilbao. Los modelos se integran dentro del software de CAM como una aplicación más del propio software.
Integración en CAM: Selección de dirección de mecanizado con mínimo esfuerzo de corte
Una de los modelos integrados en el software de CAM selecciona la dirección de mecanizado garantizando el menor de los valores posibles para los esfuerzos de corte en esa dirección. En este sentido, se evaluan los esfuerzos de corte para cada punto del mecanizado y sus posibles direcciones de mecanizado proporcionando el mínimo valor de los esfuerzos de corte posible.
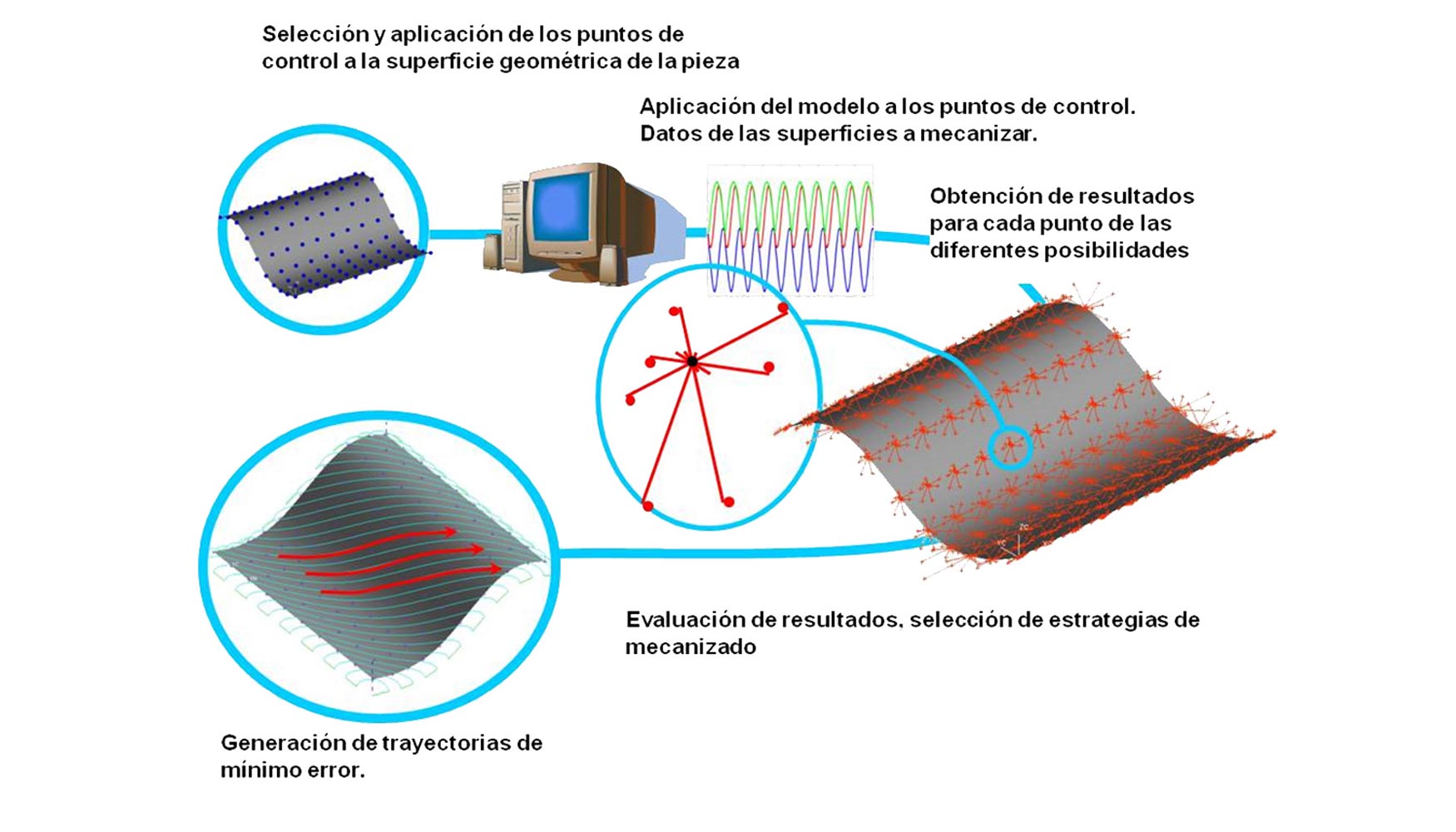
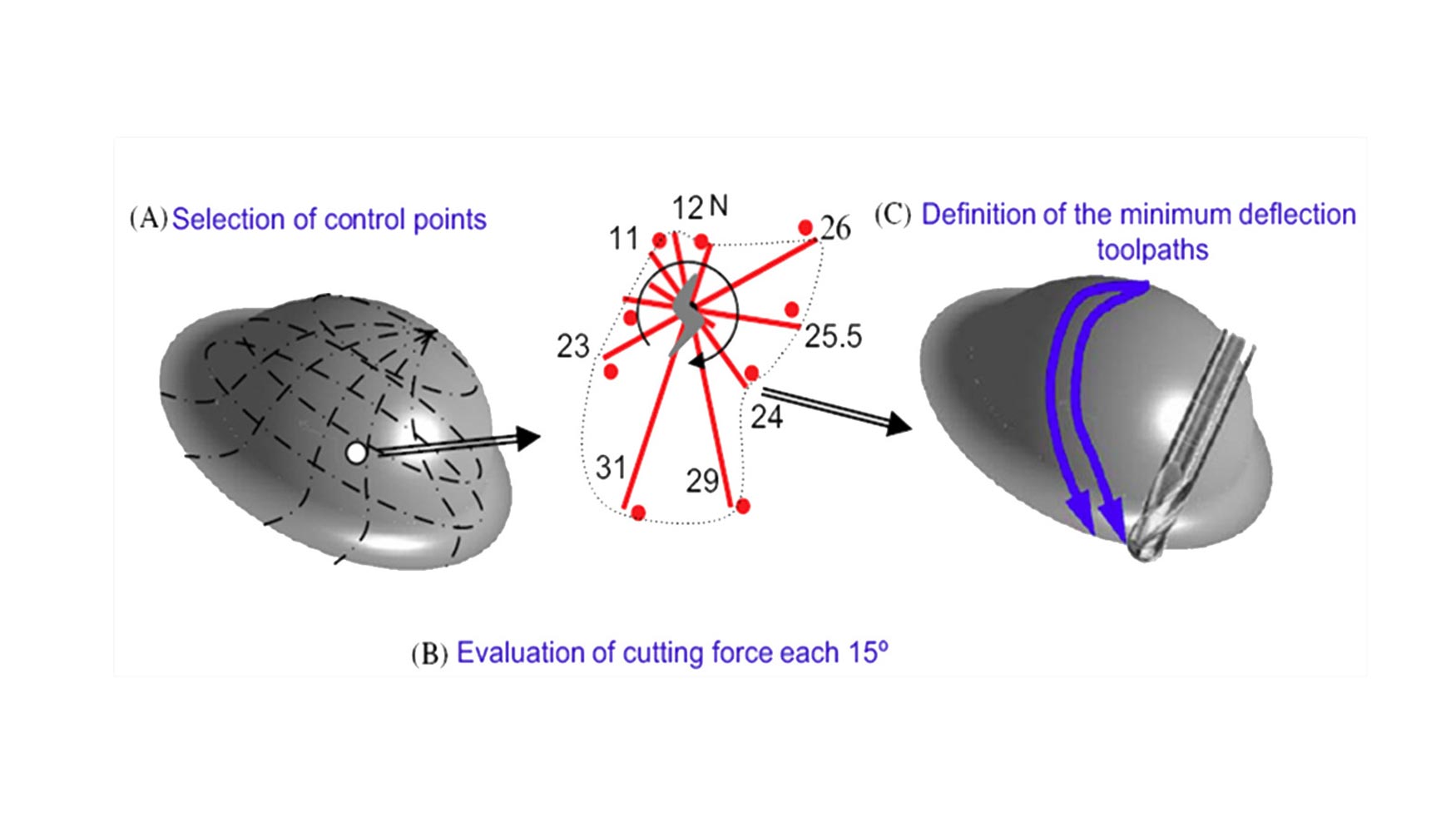
Integración en CAM: Cálculo de los esfuerzos de corte en el punto seleccionado
La función de esta aplicación es establecer un criterio a la hora de la selección de la estrategia de mecanizado basado en los valores de las fuerzas de mecanizado. Se trata de una nueva herramienta para el análisis de las estrategias y condiciones de mecanizado. A efectos prácticos, tras la integración del modelo dentro del software de CAM, el programador encontrará el nuevo comando para el cálculo de fuerzas de corte integrado en la ventana de comandos del software de CAM. Una vez que el programador haya introducido en el programa de CAM todos los datos de entrada necesarios (geometría de herramienta, condiciones de corte, avances y revoluciones, patrón de mecanizado, etc.) el programador analiza la trayectoria obtenida en función de diferentes criterios como pueden ser colisiones, tiempos de mecanizado y otros. Este nuevo comando de fuerzas se agrupa dentro de las herramientas de análisis para la selección de una operación de mecanizado óptima.
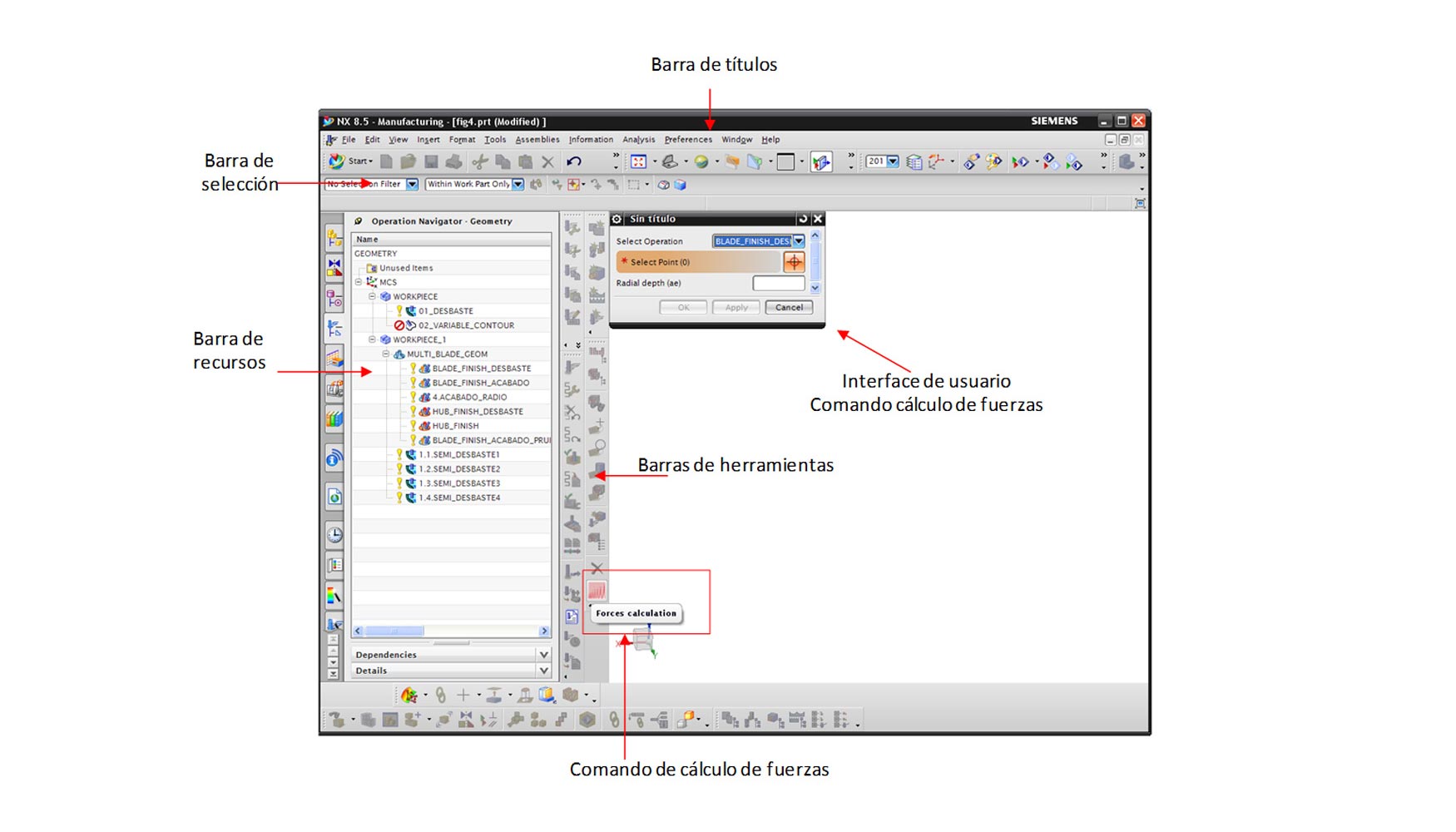
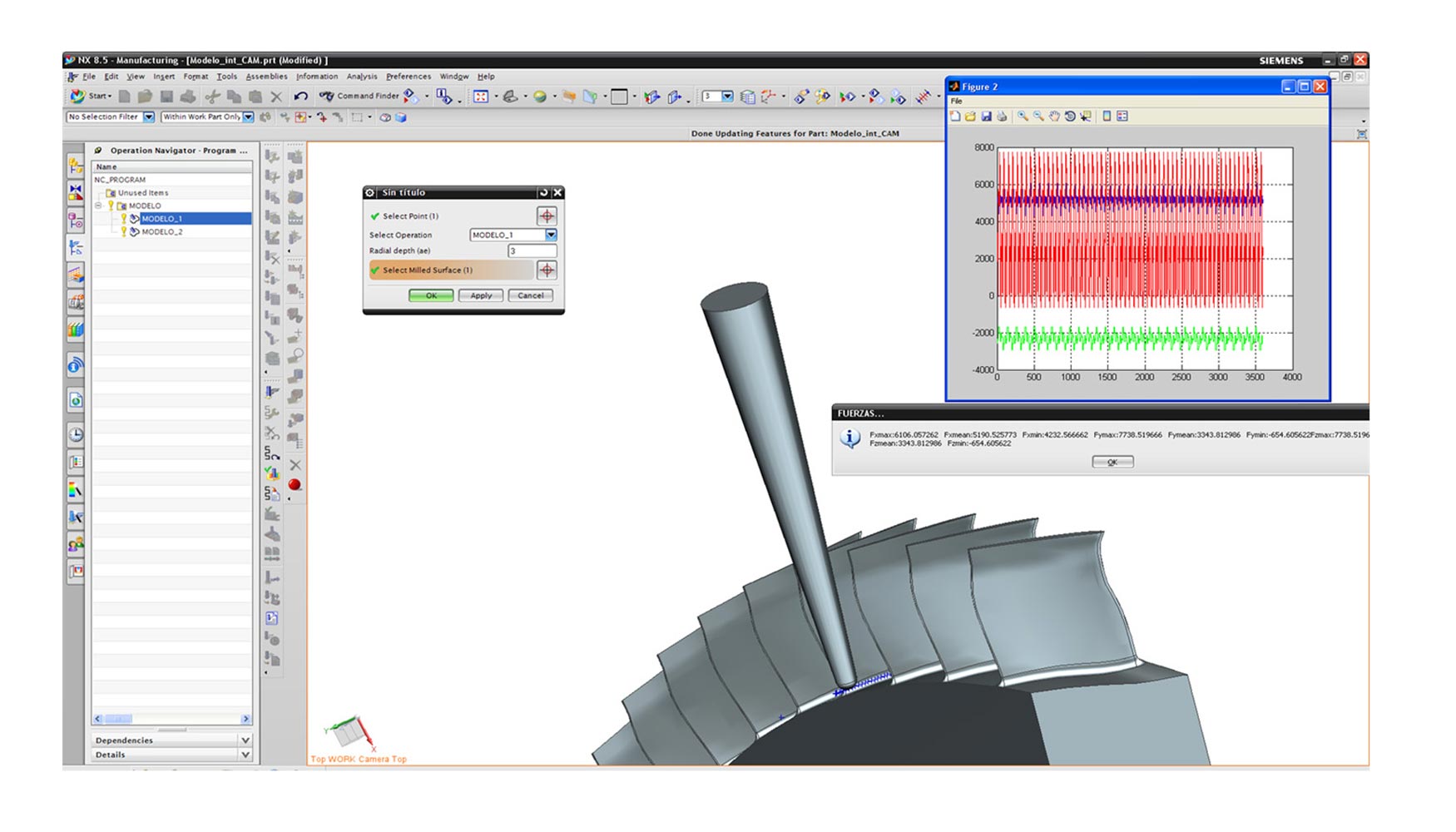
Integración de los modelos de mecanizado en el software exclusivo
Del mismo modo que algunos de los modelos predictivos del proceso de mecanizado pueden integrarse directamente en el software de CAM, son varios los modelos que han evolucionado desde el software en el que han sido programados hasta un software de aplicación exclusiva. Estos softwares pretenden dar respuesta a ciertos problemas recurrentes durante en mecanizado como pueden ser las vibraciones. Este tipo de herramientas recurren a simulaciones y mediciones de ciertos parámetros de corte para detectar el origen del problema y corregirlo online.
Destaca en este campo el trabajo llevado a cabo por Y. Altintas miembro del Laboratorio de Fabricación y profesor de la universidad British Columbia en Vancouver. El software CutPro está basado en un modelo dinámico (enfoque analítico y temporal) de los procesos de mecanizado. Este tipo de modelos disponen de una serie de parámetros dinámicos (m, c, k) correspondientes al binomio herramienta/pieza que son obtenidos de forma previa a las simulaciones. El software proporciona un módulo de análisis modal en 3 dimensiones que permite filtrar y tratar la función de transferencia que permita obtener los modos fundamentales. Además, el software también dispone de un módulo de acoplamiento de receptancias que simplifican la caracterización experimental gracias a una biblioteca de datos dinámicos correspondientes a herramientas y máquinas. Recientemente ha salido al mercado también el software ShopPro que proporciona una simulación virtual del proceso de corte en operaciones de fresado en 5 ejes considerando la trayectoria y la sección de viruta para el cálculo de las fuerzas de corte.
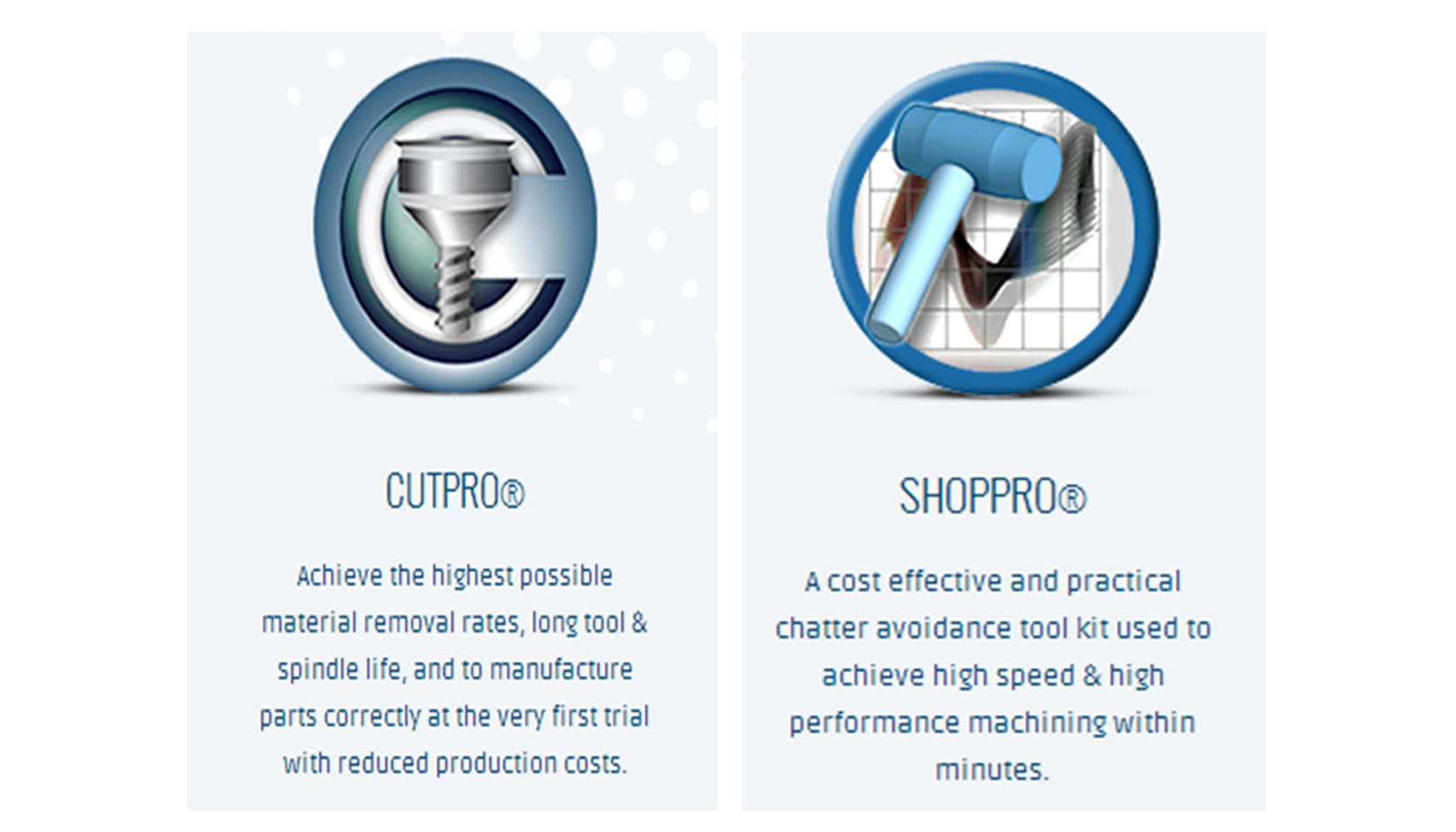
Existen softwares basados en análisis acústicos para la detección de las frecuencias de chatter. Este es el caso de Accord Mill que recurre a la grabación del sonido producido durante el proceso de mecanizado con un micrófono. El análisis de la señal acústica (basado en la transformada de Fourier FFT) permite en primer lugar filtrar la señal, en segundo lugar detectar las frecuencias de chatter y en tercer lugar visualización de la frecuencia de chatter y en tercer lugar proporcionar la velocidad óptima teniendo en cuenta la velocidad de partida, el número de filos de la herramienta y velocidad máxima de rotación permitida. Gracias a este análisis, el programador dispone de una serie de datos útiles para la mejora del programa. Otro ejemplo de software basado en el análisis acústico es Harmonizer. De la misma forma que Accord Mill, el principio básico de esta herramienta es el análisis del ruido durante el proceso de mecanizado. Harmonizer surge como resultado de las investigaciones para el control y reducción de las vibraciones en mecanizado llevadas a cabo en el MLI de Las Vegas bajo la dirección del profesor J. Tlusty. Se busca una velocidad de giro estable en función de la profundidad de corte en la que se eviten frecuencias de chatter.

Por otro lado, aparecen el mercado paquetes que incluyen diferentes módulos para el análisis de frecuencia y la adquisición de datos. Así, MetalMAX incluye tareas de caracterización modal gracias al software TXF, simulación predictiva del proceso mediante MilSim, y optimización de la velocidad gracias a la monitorización acústica proporcionada por Harmonizer.
La sensorización es una herramienta frecuente en este tipo de aplicaciones como es el caso del desarrollo llevado a cabo en colaboración entre la universidad de Nantes y Airbus y denominada SMARTIbox (Spindle Measuring and Analysing Relevant Tool for Industry Box). SMARTIbox analiza las frecuencias de corte y los armónicos del husillo de alta velocidad mediante la sensorización de los esfuerzos de corte y sus frecuencias. Este desarrollo permite establecer ciertas leyes de comportamiento predictivas para definir los ciclos de verificación y mantenimiento antes de alcanzar umbrales que puedan ser perjudiciales para el cabezal.
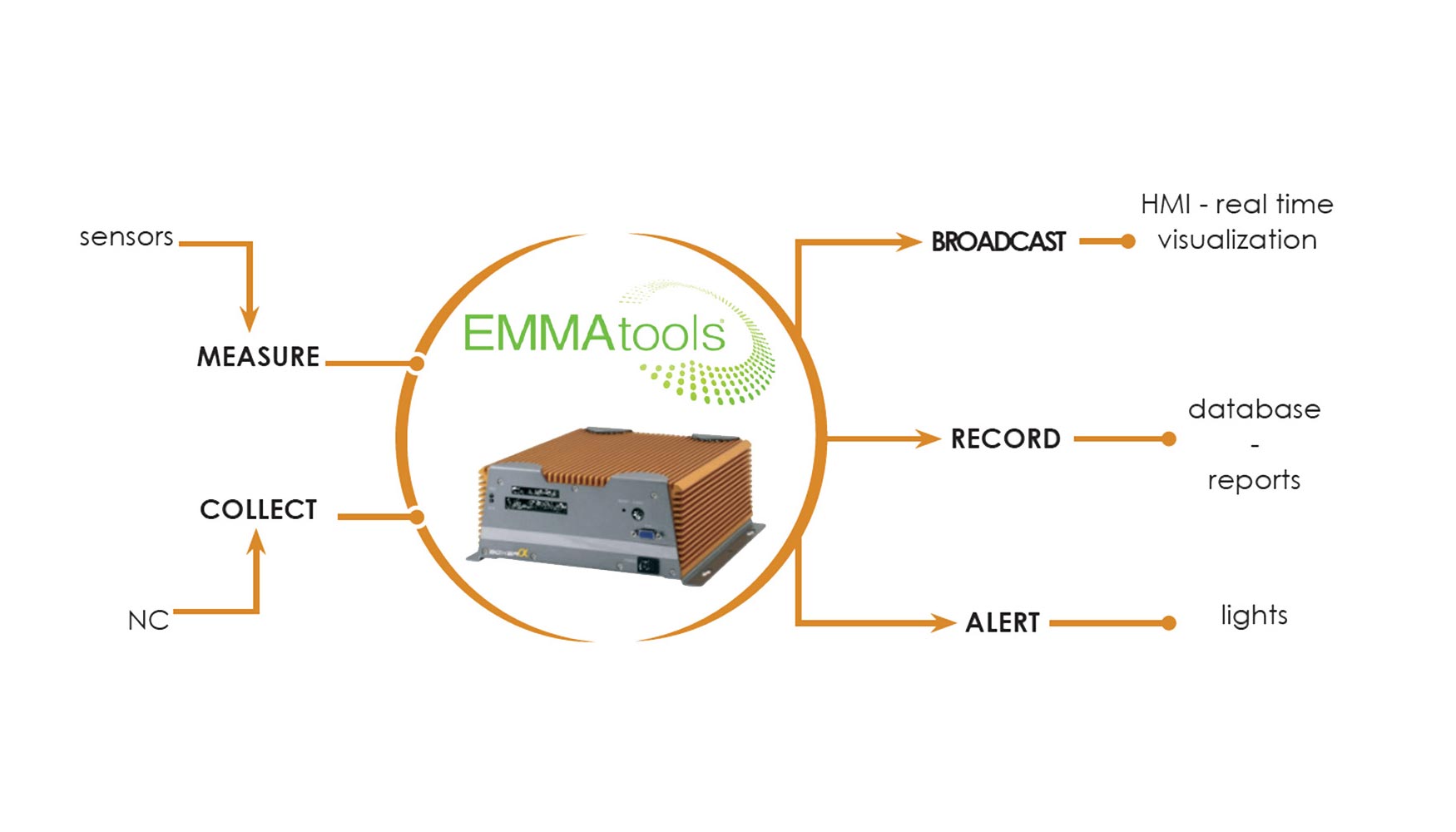
Otro software que se suma a la resolución de los problemas de chatter online es Machining Navi. Lo más destacable de Machining Navi es su integración en el control numérico de la máquina con su consecuente accesibilidad y su aplicabilidad. El software de Okuma recurre a la sensorización del valor de la vibración para corregir la velocidad y modificar su valor hacia valores de corte estables. Otra de las ventajas es la posible utilización de la aplicación de forma automática tomando las decisiones durante el mecanizado o bien mediante la acción del operario corrigiendo desde teclado la velocidad ante cualquier percepción de inestabilidad en el corte.
UPV/EHU: Una de las últimas novedades desarrollada por el Dpto. de Ingeniería Mecánica de la Universidad del País Vasco UPV/EHU consiste en el desarrollo de un software propio para el análisis de procesos de mecanizado. En la transformación de un componente, éste pasa por distintas etapas sufriendo condiciones muy variables de operación. Por ello, a lo largo de la producción de una pieza, es necesario el uso de herramientas sistemáticas que ayuden a resolver los distintos problemas que puedan surgir, aconsejando al operario en la toma de decisiones.
El desarrollo de esta aplicación tiene el objetivo de ofrecer una solución a usar por el personal de los distintos departamentos de la empresa como una herramienta más para la mejora de la calidad del producto. Con ella, se estima resolver algunos de los problemas dinámicos más comunes de una forma intuitiva y ágil. La aplicación debe ser útil tanto para el diseñador de un componente (estrategias, trayectorias y CAM) como para el operario o los ingenieros de diseño de una nueva máquina-herramienta.
Utiliza códigos (modelos mecanísticos) predictivos propios generados en Matlab y administrados de forma eficiente por lenguaje Visual C.
Las principales utilidades se resumen a continuación:
- Dinámica en punta de herramienta: para el ajuste de una curva obtenida vía experimental y para la obtención de parámetros modales o para la conversión entre variables modales a usar entre modelos tradicionales y modelo multi-modo (en coordenadas modales).
- Simulaciones estáticas de fuerzas de corte para procesos de torneado y fresado: el modelo utiliza como parámetros de entrada la geometría de la placa (radio y ángulo de posición de placa) y la energía específica de corte del material a partir de una biblioteca de materiales. El software creado permite incorporar los efectos de distintas geometrías de placa sobre las fuerzas. El efecto de otros factores como el rompevirutas o los ángulos de inclinación y desprendimiento no se tienen en cuenta directamente pero si se desea mayor precisión pueden llevarse a cabo caracterizaciones ad-hoc para un par concreto material-herramienta.
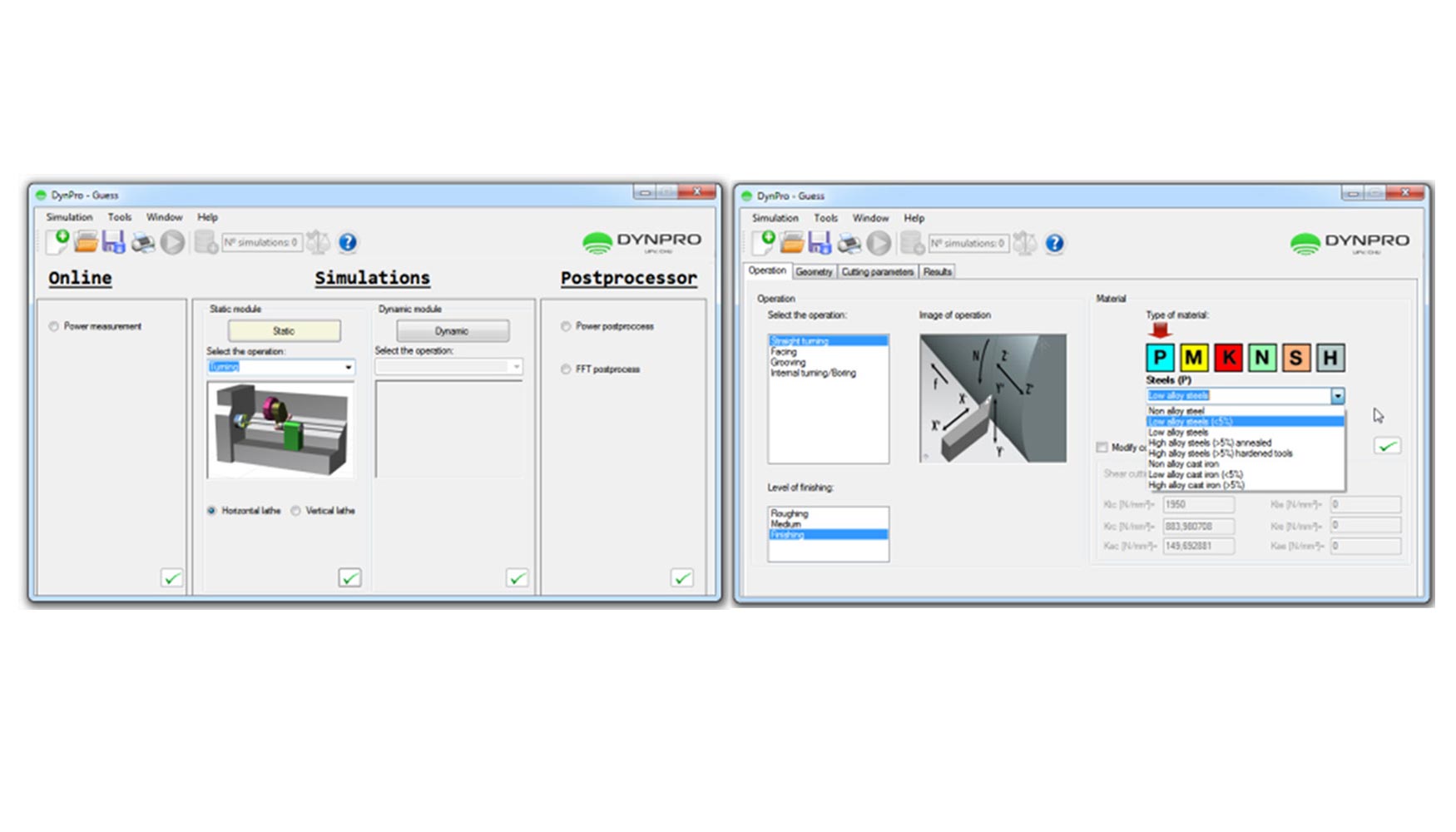
- Simulaciones dinámicas para procesos de torneado y fresado:
o Simulación de sistemas de 1 o varios GDL: presenta los diagramas de estabilidad y el mapeo de autovalores en el mismo rango de trabajo. Permite la incorporación de coeficientes de corte variables y posicionamiento particular de la herramienta.
o Simulación en el dominio del tiempo u obtención de la evolución temporal de fuerzas y desplazamientos de herramienta, con posibilidad de incorporar varios modos sobre distintas direcciones.
- Mecanizado inteligente:
o Criterio de chatter: mediante el análisis y procesamiento de señal grabada durante el corte (fuerzas, ruido, desplazamientos o aceleraciones) aplica la función FFT para visualización de espectro de frecuencias o la obtención del diagrama de Poincaré (periodo a periodo), para establecer la estabilidad del corte.
o Método Harmonizer: para guía de selección de velocidades de giro más adecuadas. Las salidas de esta pestaña son diagramas de lóbulos, de frecuencias de chatter y diagrama de ángulo de desfase, para orientar al operario sobre las velocidades de giro más adecuadas.
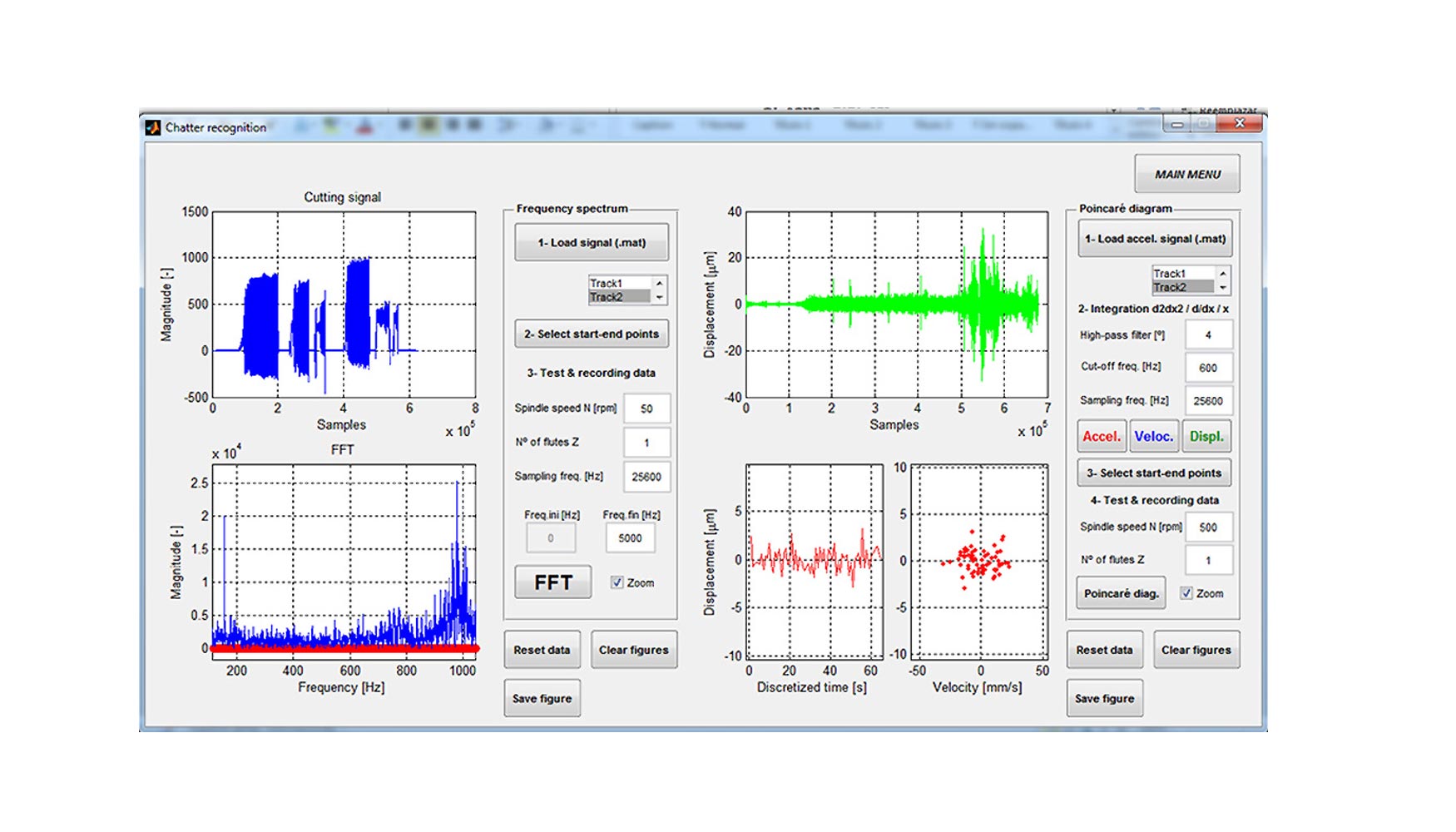
Aplicaciones software CAM
Los propios software de CAM utilizados para programación de las estrategias de mecanizado integran por su parte nuevas funciones orientadas a aumentar los ratios de productividad del proceso de fresado, reducir los movimientos en vacío, reducir la longitud de los programas y por lo tanto el tiempo de mecanizado, etc. La base de estas aplicaciones reside en la mayoría de los casos en la optimización de los avances de la herramienta en cada punto de la trayectoria. Este es el caso de OptiPath de Vericut que varía la velocidad de avance de la herramienta en función de la cantidad de material. La velocidad de avance de la herramienta se ve reducida al aumentar la tasa de arranque de material y viceversa, se aumenta la velocidad de avance de la herramienta con la disminución de la tasa de arranque de material. Así, se consigue mantener la trayectoria optimizando los valores de los avances de herramienta. En la misma línea de trabajo destaca el módulo voluMILL puede integrarse en infinidad de software de CAM (NX, ESPRIT, GibbsCAM, CAMWorks…) con la finalidad de optimizar las trayectorias producidas por el software en el que se integra. Para cumplir con este objetivo se incluyen nuevas estrategias de CAM más eficientes que evitan cambios bruscos de dirección de trayectorias de mecanizado y controlan la cantidad de material a eliminar siendo posible la optimización de avances y revoluciones de la herramienta para alcanzar valores mayores a los programados inicialmente. A la lista de los softwares dedicados a la simulación del proceso y optimización del programa de CN hay que añadir NPro de Y. Altintas.
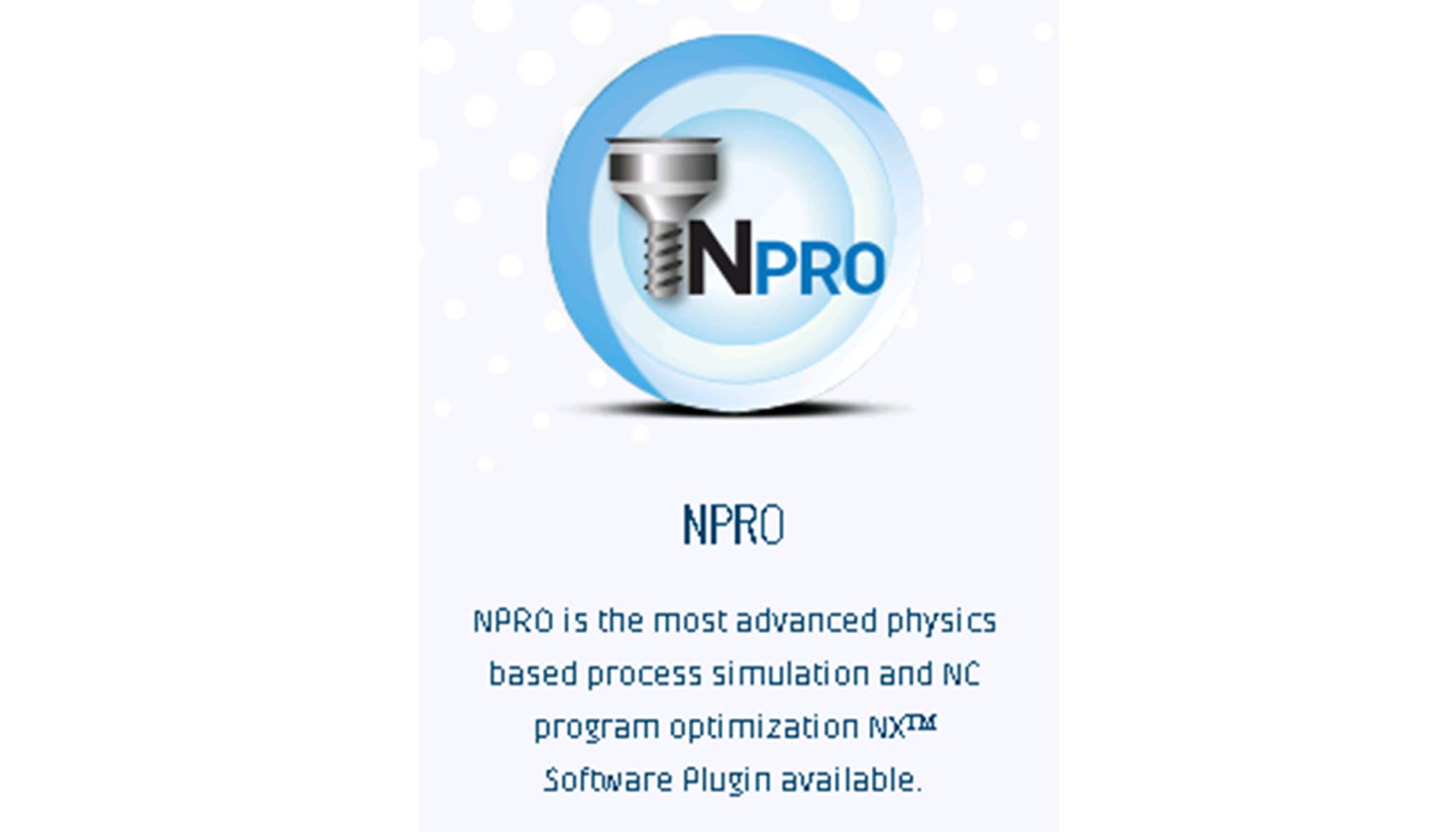
Algunos de estos software trabajan en la línea de lo que podría denominarse segundo posprocesado. Así, Nc Optimizer optimiza los valores de avance de la herramienta en función de la geometría de la pieza y de la cantidad de material a eliminar. Se introduce el programa de control numérico en el software, se optimizan los valores de los avances y posteriormente se introduce en la máquina.
No solamente se optimizan los valores de avances de la herramienta sino que es posible obtener cual la longitud apropiada de herramienta y la minimización de los movimientos de corte en vacío. Optitool de NCSimul es un módulo que se integra en el software de simulación del proceso de mecanizado y está enfocado a la corrección de posibles errores debidos a una mala elección de la longitud de corte de la herramienta. Al mismo tiempo se pueden reducir tiempos de mecanizado en vacío y optimizar por tramos de trayectoria la velocidad de avance de la herramienta en función de la cantidad de material a cortar.