Una nueva dimensión del acero
Si bien el plegado de chapas de acero no supone ninguna novedad, el conformado tridimensional (3D) permite crear serpenteos, compartimentos abiertos y formas más elaboradas con una sola chapa de acero, eliminando así la necesidad de soldar. El truco consiste en realizar el moldeado 3D sin menoscabo de las propiedades de los aceros de alta resistencia, como bien ha descubierto la compañía sueca Deform en colaboración con SSAB.
Cuando en 1907 se fundó Degerfors Ironworks, la actual Deform, los aceros de alta resistencia, el conformado tridimensional de nuestros días e incluso la soldadura aún estaban por inventar. Para dar forma a las chapas de acero se empleaban prensas hidráulicas y rodillos de flexión antes de unirlas mediante remaches.
Un siglo después, Deform ha desvelado los secretos de la ‘conformación en caliente’ del acero de alta resistencia sin pérdida de las propiedades de este. También ha desarrollado un proceso para el diseño de una chapa individual de acero de alta resistencia con un elaborado contorno, eliminando de este modo la necesidad de soldar varias chapas.
“El mercado del conformado 3D está creciendo, pero se precisa todavía educar a diseñadores e ingenieros sobre la posibilidad de conformar en caliente el acero de alta resistencia”, declara Conny Lundstedt, director de ventas de la firma, que se ha topado con muchos escépticos en la década que lleva en Deform. “Suelen descartar como imposible el conformado en caliente de las calidades de acero de alta resistencia por creer que al calentar este para darle forma van a destruirse sus propiedades, lo cual, en realidad, no es incierto. Ahora bien, nosotros aplicamos un proceso certificado único en el que conformamos en caliente pero solo destruimos temporalmente las propiedades del acero, para luego restaurarlas al tiempo que mantenemos la forma. No hay muchas compañías que sean capaces de hacer esto”.
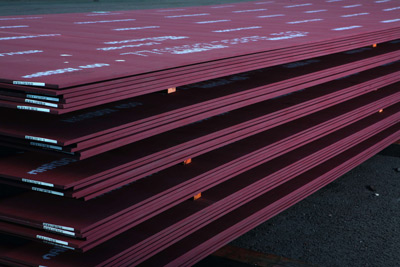
Según Anders Bergstedt, técnico de ventas, el conformado con 3D se opera de forma bastante directa. “Se coloca una chapa fría o caliente entre un molde superior y otro inferior, diseñados por Deform, configurándose de acuerdo al diseño requerido”.
La preservación de la forma y las propiedades de los aceros de alta resistencia tras el proceso de conformado, es lo que, a juicio de Lundstedt, hace de la oferta de Deform algo ‘único’, aparte de popular entre los clientes ‘de alta categoría y alto nivel de exigencia’ en los ámbitos de defensa, marítimo, nuclear y del petróleo y el gas.
Deform considera que el uso de una única chapa en lugar de varias piezas soldadas brinda ventajas tanto a clientes como a usuarios finales. No solo se evitan los puntos débiles en torno a las áreas soldadas, sino que los clientes se ahorran también tiempo y dinero en labores de soldadura. Para los usuarios finales, el uso combinado de aceros de alta resistencia y conformado 3D resulta a menudo en un producto más robusto y ligero que, en el caso de los vehículos, ofrece una mayor seguridad a sus ocupantes.
“Uno de los grandes retos de la industria de nuestros días es la lucha por un entorno sostenible y la reducción de los desechos”, asevera Lundstedt. “El peso es un factor esencial en muchos sectores, y en particular dentro del transporte y la minería, donde cada kilo que se recorta al peso del vehículo puede agregarse a la carga. Cuando un producto o vehículo pesa menos, consume menos combustible y es más respetuoso con el medio ambiente. Además, cuanto menos acero requiere y menos residuos genera, más ecológico será el producto”.
Aunque las ventajas de combinar aceros de alta resistencia y conformado 3D son innumerables. Bergstedt resalta que los clientes deben calcular el rendimiento previsto de la inversión antes de ponerse manos a la obra, ya que los moldes utilizados para la configuración implican un coste inicial. “A veces no tiene sentido invertir en el molde. Debes determinar si va a permitirte ahorrar dinero, mejorar tu producto y optimizar el nivel de protección del mismo. No puedes encargar una pieza de prueba y ver si funciona. Esa es la única desventaja del conformacdo en 3D”.
Deform lleva más de dos décadas trabajando con los productos de acero de SSAB. Emplea Armox en muchas de sus chapas de protección, mientras que Weldox y Hardox se usan en otras aplicaciones. Buena parte de las chapas de Deform son sometidas a prueba en entornos de alta exigencia. Sus chapas de protección para minería se hallan a menudo bajo tanques y vehículos blindados y Weldox se utiliza con frecuencia en el armazón y el casco de presión de los submarinos. En caso de detectarse un paquete sospechoso en un aeropuerto, este se colocará dentro de una cámara de deflagración, con toda probabilidad fabricada a partir de chapa de acero de alta resistencia conformada con 3D, evacuándose luego para su detonación bajo condiciones de seguridad.
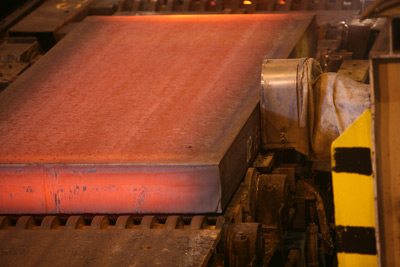
“Cuando se usan chapas gruesas de acero al carbono unidas por soldadura, los contenedores pesan tanto que resultan difíciles de transportar”, explica Lundstedt. “Actualmente los contenedores pueden elaborarse con acero Weldox templado y revenido de conformación tridimensional en caliente. Las dos semiesferas se fabrican de una sola pieza, sin soldadura alguna. Este método, unido al uso de acero Weldox, permite a los diseñadores disminuir en dos tercios el grosor de la cámara sin pérdida alguna de resistencia, lo que resulta en un novedoso contenedor más ligero y fácil de transportar”.
A Deform, la colaboración con SSAB le ha funcionado muy bien y confía en poder afianzarla aún más en el futuro. “Cuentan con aceros de primera calidad y gozan de una excelente reputación a nivel internacional. Por nuestra parte, somos expertos en la conformación por 3D a sus aceros de alta resistencia. Al mismo tiempo nos beneficiamos en gran medida de su red global y excelente soporte técnico”, concluye Lundstedt.
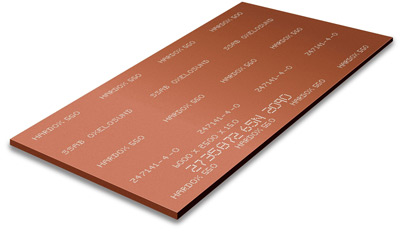