Instalación Metso para el aprovechamiento como árido de la roca procedente de la excavación de los Túneles del Proyecto Follo Line en Oslo, Noruega
La Norwegian National Rail Administration firmó a mediados de marzo del pasado año un contrato por valor de 8.700 millones de coronas noruegas (unos 1.000 M€) con un consorcio formado por Acciona, grupo mundial español de energías renovables e infraestructuras, y Ghella, una empresa constructora italiana con una amplia experiencia en obras subterráneas. El proyecto consiste en el diseño y construcción de dos túneles gemelos de 20 km de longitud del Proyecto Follo Line.
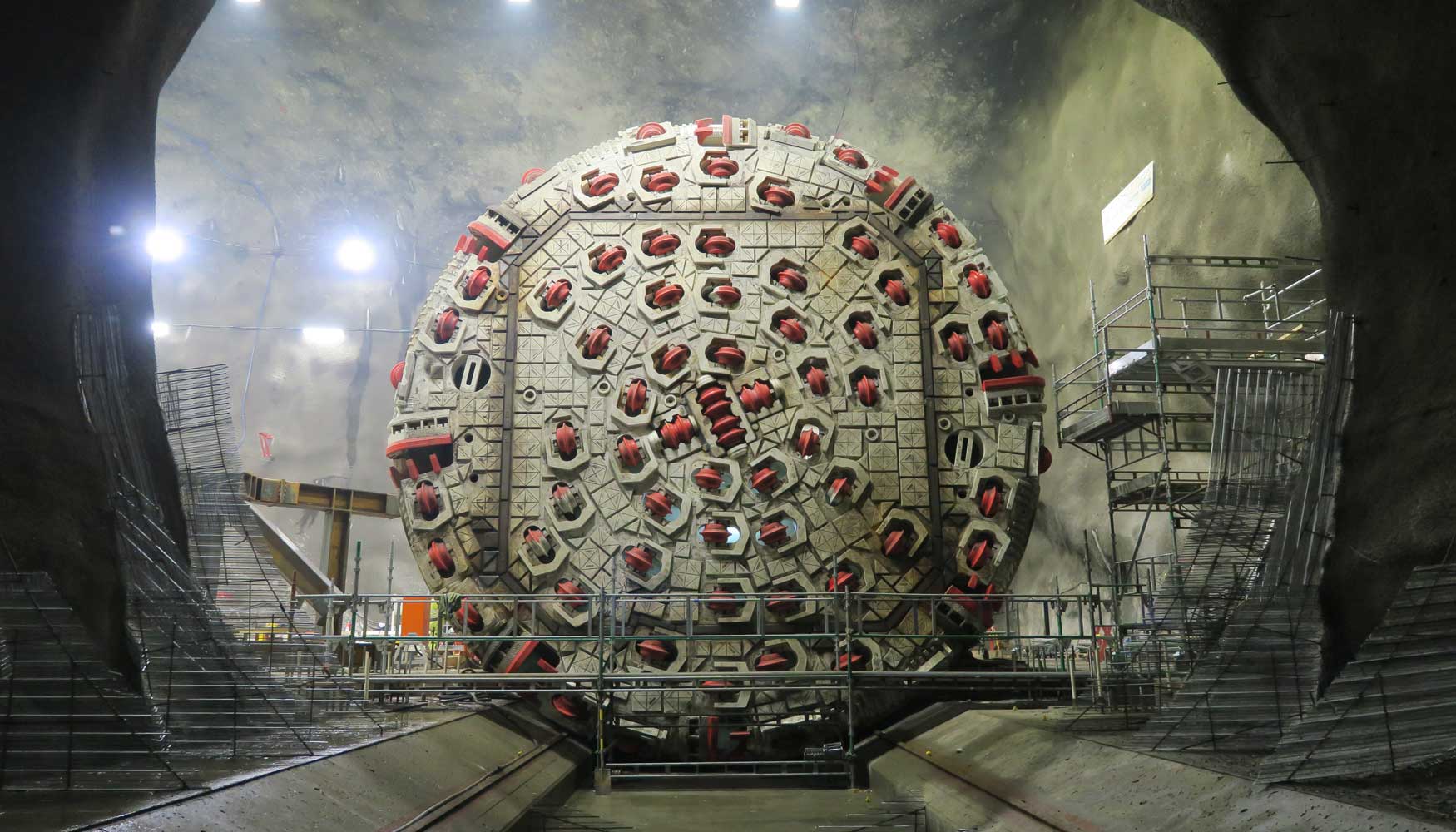
Se trata del segundo y el mayor de los cuatro contratos EPC (llave en mano) incluidos en el proyecto Follo Line, el mayor de infraestructuras de Noruega hasta la fecha. Una vez terminados, los túneles gemelos, diseñados para que por ellos circulen trenes de alta velocidad, hasta a 250 kilómetros por hora, serán los túneles ferroviarios más largos de Escandinavia.
Los túneles enlazarán las ciudades de Oslo y Ski formando el eje central del desarrollo interurbano hacia el sur de la capital noruega. Para la construcción de los túneles gemelos se utilizarán cuatro tuneladoras simultáneamente, algo nunca visto en Noruega. Dos tuneladoras perforarán hacia el norte en dirección a Oslo y las otras dos perforarán hacia el sur, en dirección a Ski.
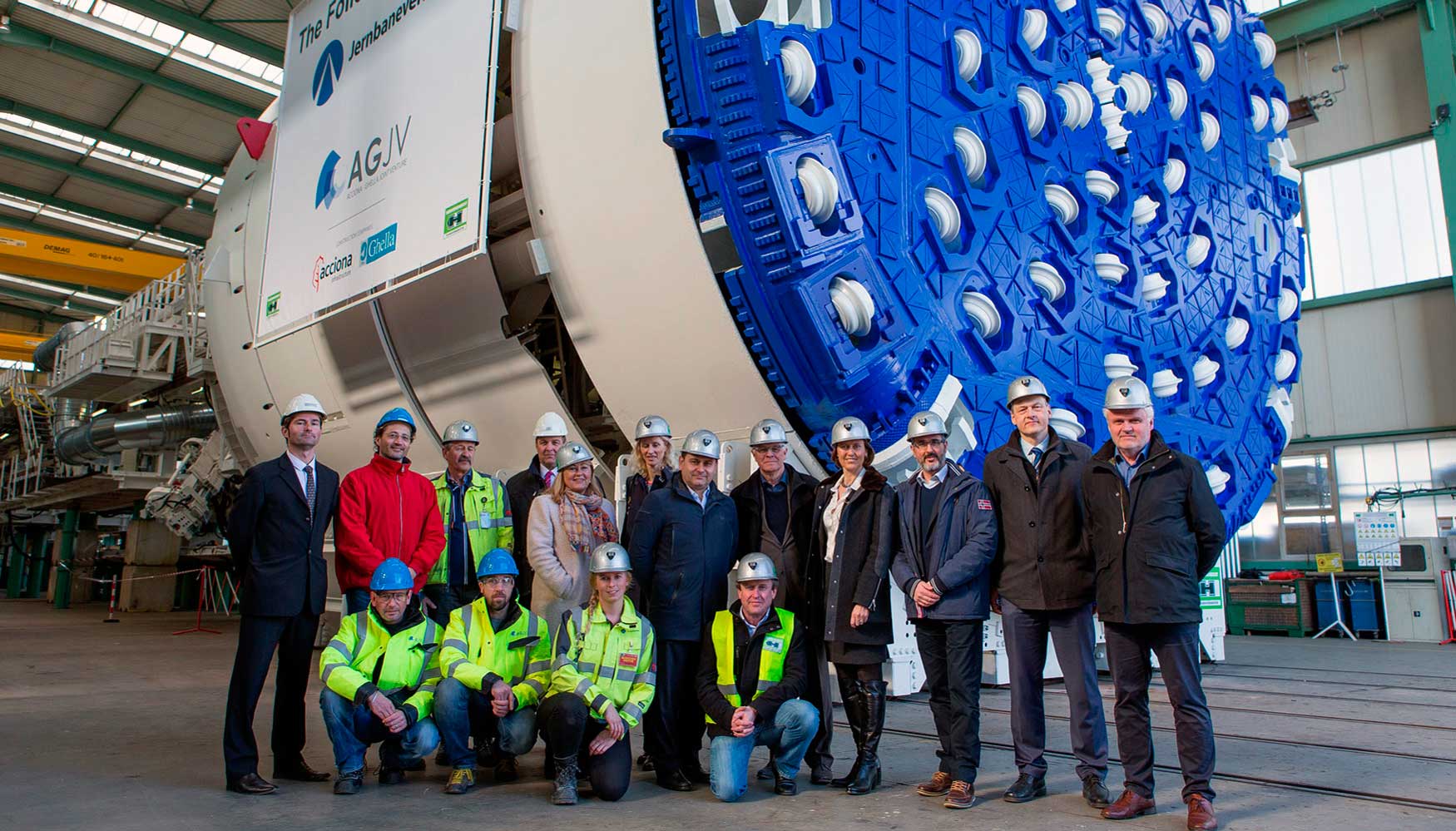
Foto 1.- Entrega de la primera tuneladora Herrenknecht para el proyecto Follo Line (Noruega).
Recientemente, Acciona Construcción terminó con éxito, y tres meses antes de lo previsto, la ejecución de los túneles logísticos del proyecto ferroviario Follo Line, realizados por el método de perforación y voladura.
Estos túneles logísticos, que servirán de acceso a los empleados y al material durante la fase de construcción de los túneles ferroviarios principales, se han perforado a una profundidad de 100 metros en Åsland, cerca de Oslo, Noruega.
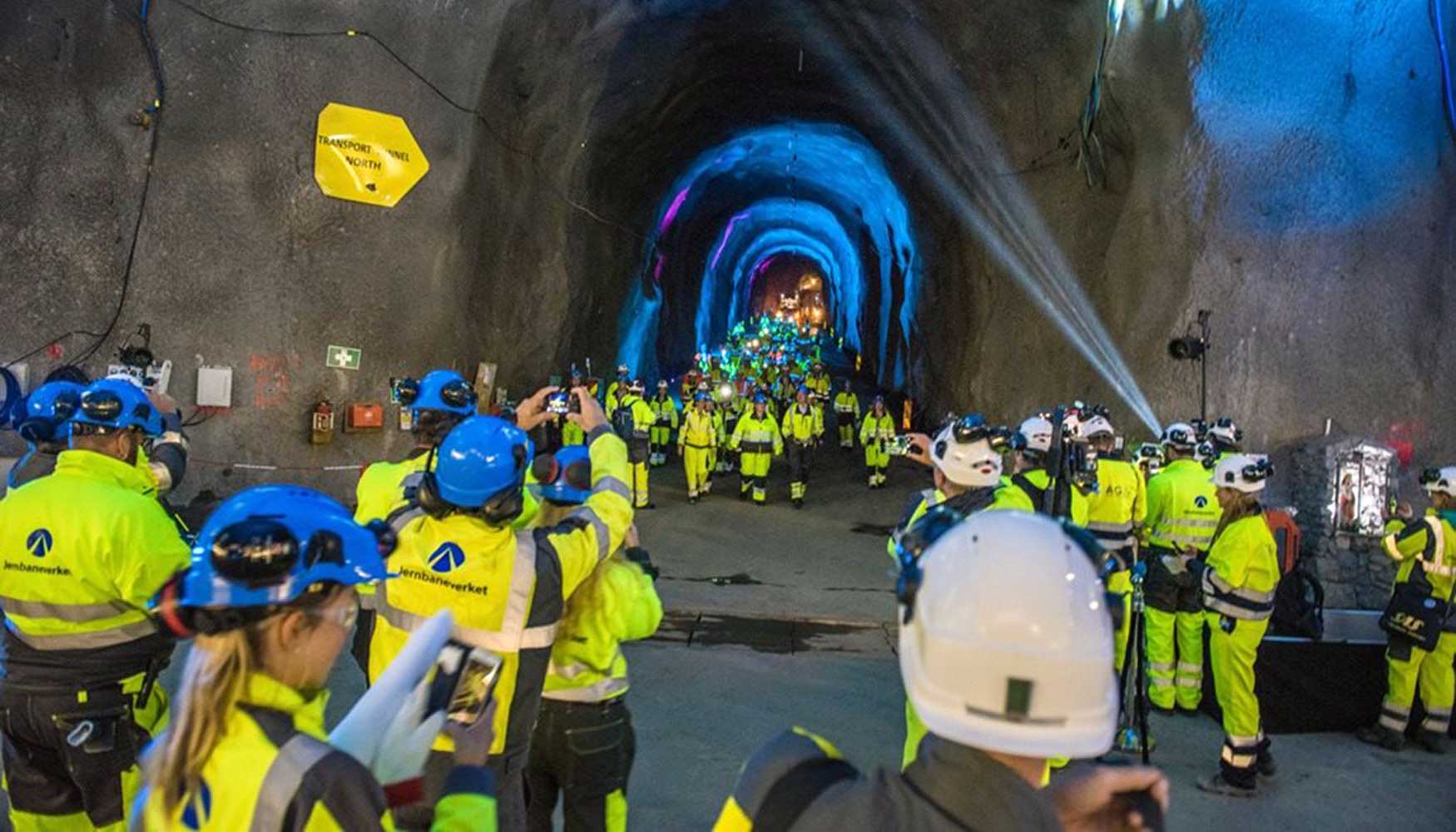
Los trabajos continuarán con la excavación del túnel de rescate, de 2,7 kilómetros de longitud, y con el acondicionamiento del nuevo sistema de túneles para proceder al montaje de cuatro tuneladoras en unas cavernas interiores. Está previsto que estas máquinas se pongan en funcionamiento en otoño de este mismo año.
Acciona lidera el consorcio responsable del proyecto Follo Line. Se trata de un contrato EPC que incluye el diseño y la construcción, entre otros, de dos túneles gemelos, excavados mediante cuatro tuneladoras de 10 metros de diámetro con sistema de doble escudo. El diseño de estos túneles, de un diámetro interior de 8,75 metros y una longitud de 18 kilómetros cada uno, permitirá la circulación de trenes de alta velocidad, hasta 250 kilómetros por hora.
Esta infraestructura está promovida por la Administración pública Noruega de Ferrocarriles (Jernbaneverket), y cuando sus obras concluyan, en 2021, será el túnel ferroviario más largo de Escandinavia. El Proyecto Follo Line, la mayor iniciativa de infraestructuras de transporte de Noruega, comunicará las ciudades de Oslo y Ski, formando el eje central del desarrollo interurbano hacia el sur de la capital noruega.
En marcha las dos primeras tuneladoras
El pasado 7 de septiembre, la primera ministra noruega, Erna Solberg, bautizó con los nombres de ‘Reina Eufemia’ y ‘Reina Ellisiv’ las dos primeras tuneladoras con las que Acciona, en consorcio con la italiana Ghella, construirá el túnel ferroviario más largo de Noruega dentro del Proyecto Follo Line y ha presidido la puesta en marcha de la primera de ellas por parte del Ministro de Transportes y Comunicaciones, Ketil Solvik-Olsen.
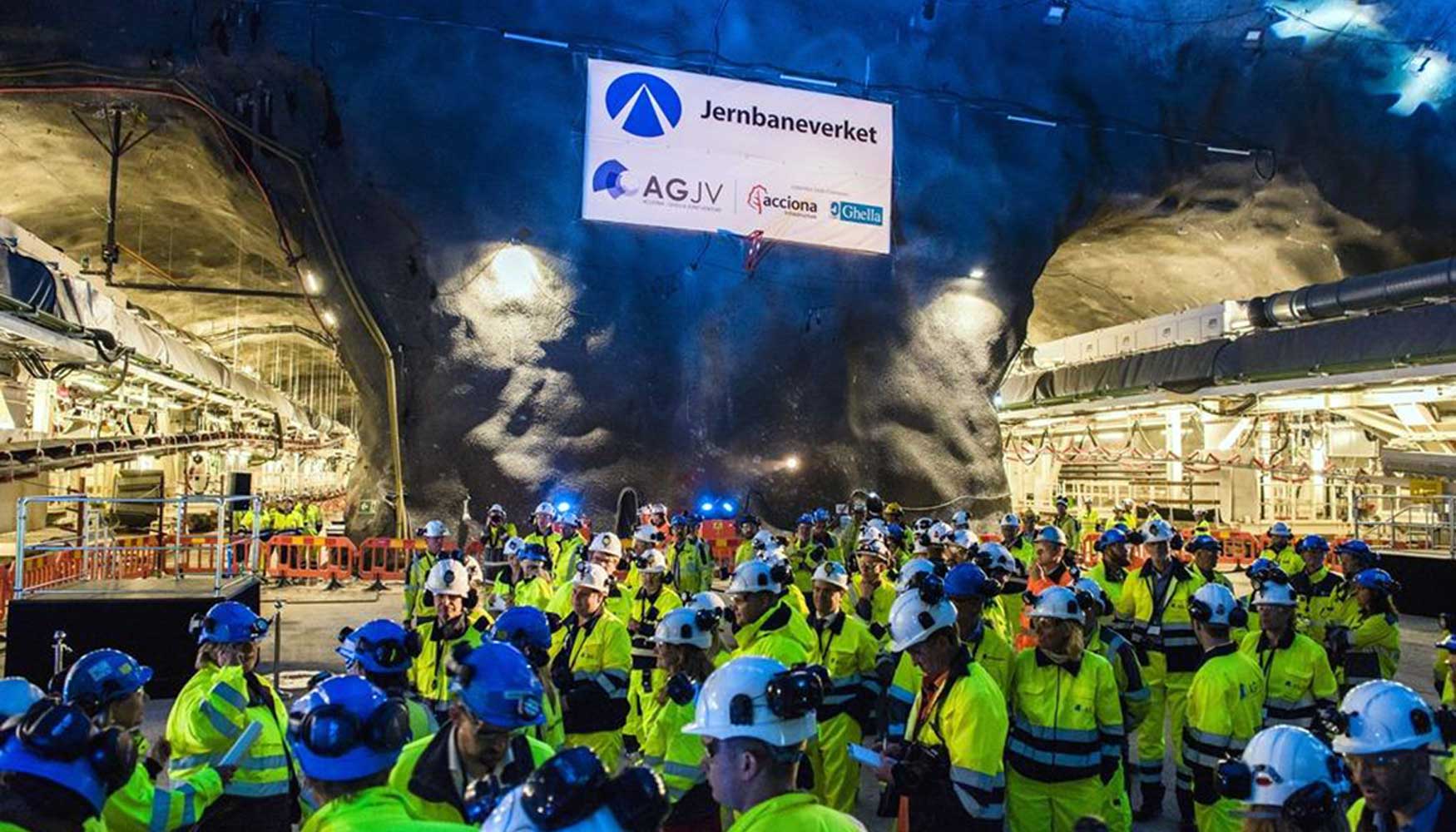
El acto del bautismo y la puesta en marcha marcan el comienzo de la excavación de lo que será el túnel ferroviario más largo de Escandinavia en un proyecto donde se utilizarán tuneladoras por primera vez en Noruega. En total, cuatro tuneladoras de 150 metros de largo cada una excavarán un túnel de 18,5 km. Todas ellas han recibido nombres femeninos, como es tradicional en la tunelación. En este caso, llevarán los nombres de mujeres relevantes relacionadas con las comunidades por las que discurre el nuevo corredor Follo Line.
El bautismo se celebró en el interior de una gran sala de montaje, a un kilómetro de la entrada del túnel por Åsland (Oslo). Estas dos máquinas partirán de Åsland y excavarán en dirección a Oslo.
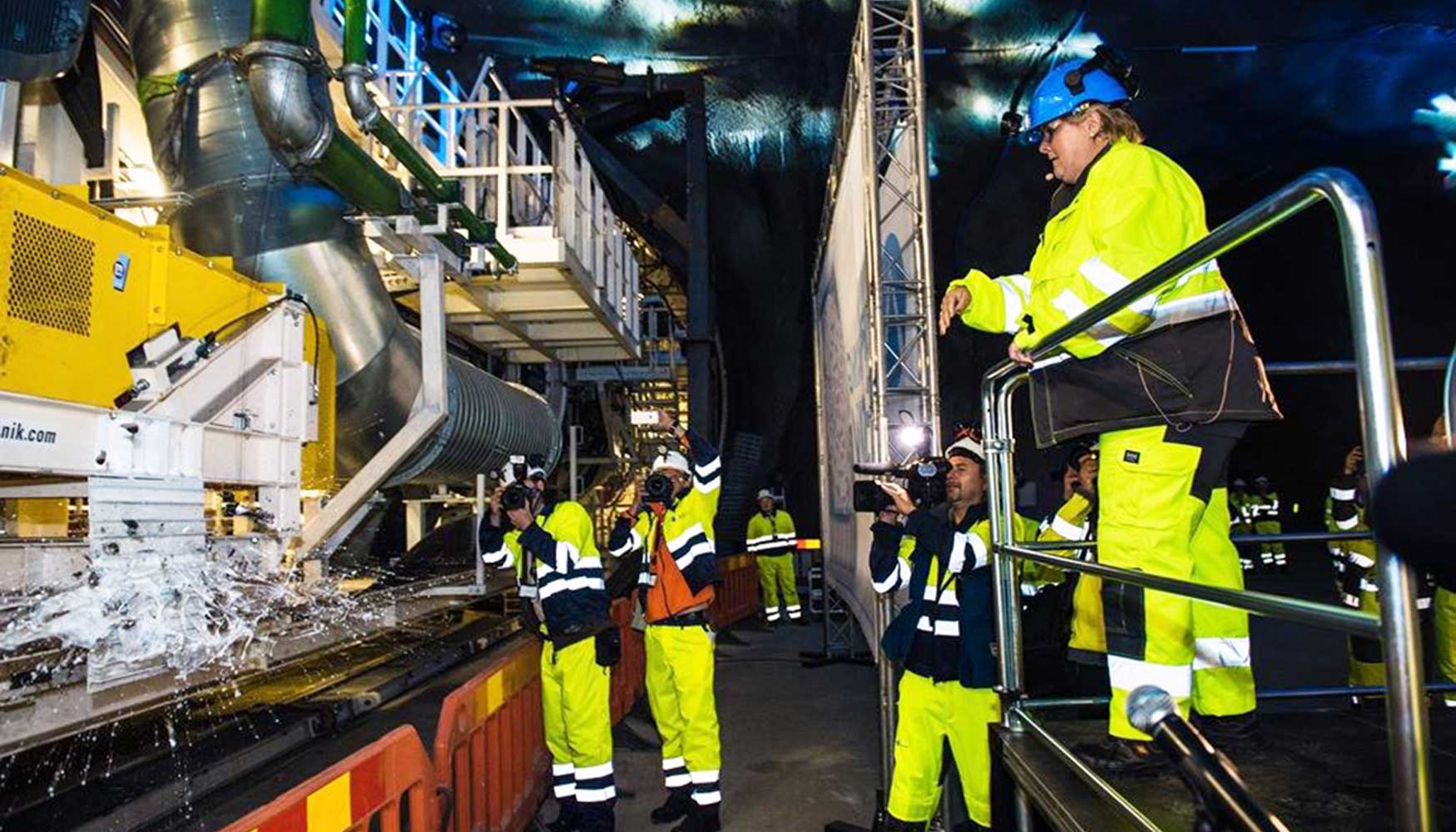
Foto 4.- Bautismo y puesta en marcha de la primera tuneladora por la primera ministra noruega.
Más adelante, otras dos tuneladoras comenzarán a perforar en dirección al nuevo centro de transporte público en Ski. Serán bautizadas con los nombres de la vendedora Anna de Kloppa y la cochera y operaria de transbordador Magda Flåtestad. Cada una de las tuneladoras pesa cerca de 2.400 toneladas, y excavará cada una unos 9 kilómetros del túnel de la nueva línea de doble vía entre Oslo y Ski.
Estas tuneladoras están especialmente diseñadas y fabricadas para excavar la durísima roca noruega de la colina de Ekeberg. Han sido construidas en la fábrica de Herrenknecht (Alemania) y posteriormente transportadas a Noruega en secciones, donde se han vuelto montar en la sala subterránea de Åsland. Se prevé que su trabajo concluya a finales de 2018. Subcontratistas y proveedores, tanto noruegos como extranjeros trabajan en Åsland bajo contrato con Acciona y Ghella. En el equipo, está representado un amplio abanico de nacionalidades.
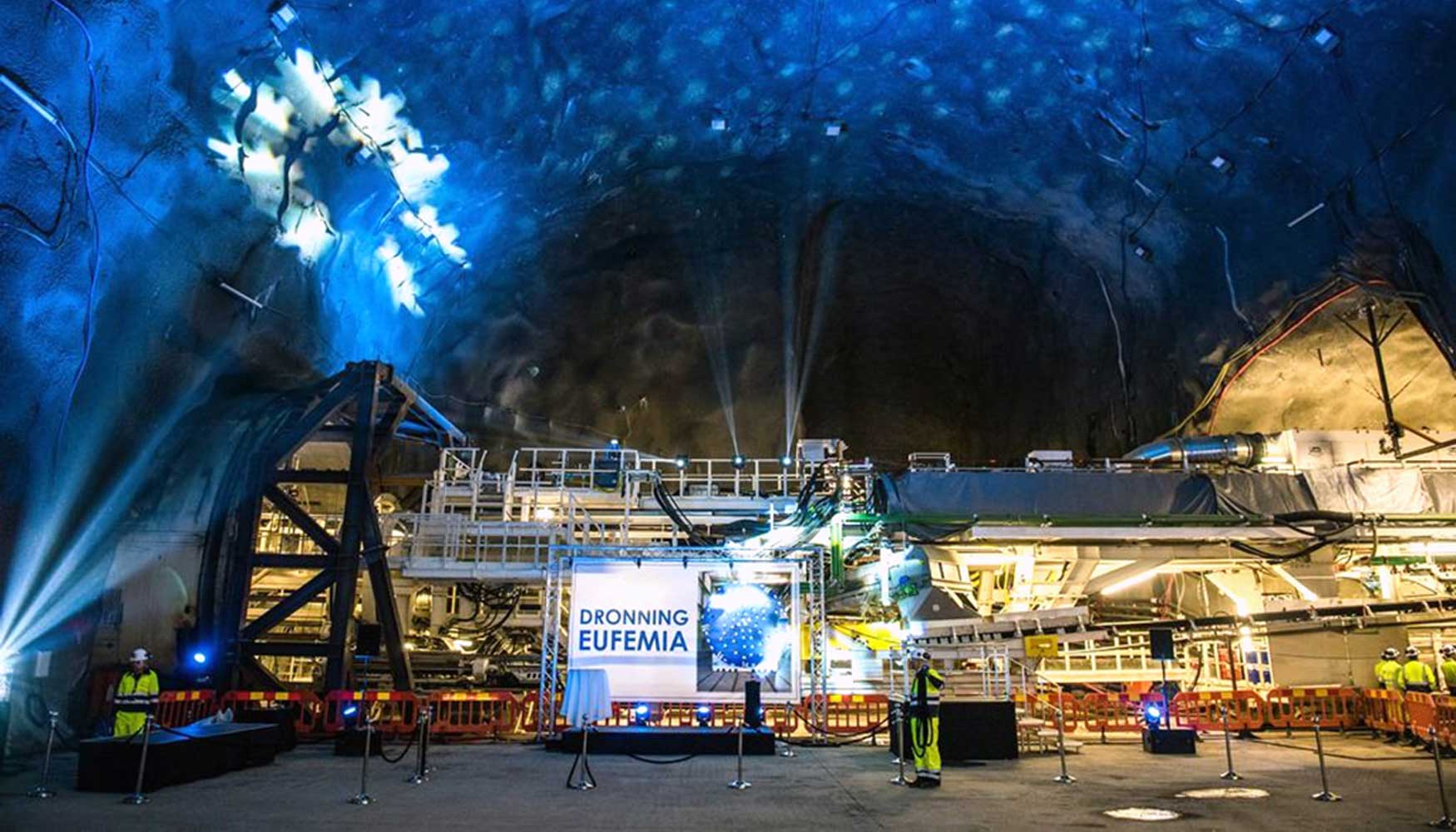
Tratamiento de la roca procedente de la excavación de los túneles
Una vez se inicie la excavación de los túneles principales, la roca extraída será tratada mediante distintos grupos de trituración y cribado Metso para su reducción a gravillas y arenas. Estos grupos –actualmente en fase de puesta en marcha-, se espera que la instalación esté en funcionamiento en el tercer trimestre de este año.
Dichos grupos están constituidos por dos grupos de trituración LT330D y LT7150B de Metso, una criba móvil ST 2.8 y otra estacionaria CVB 202 y un grupo de tratamiento de arenas.
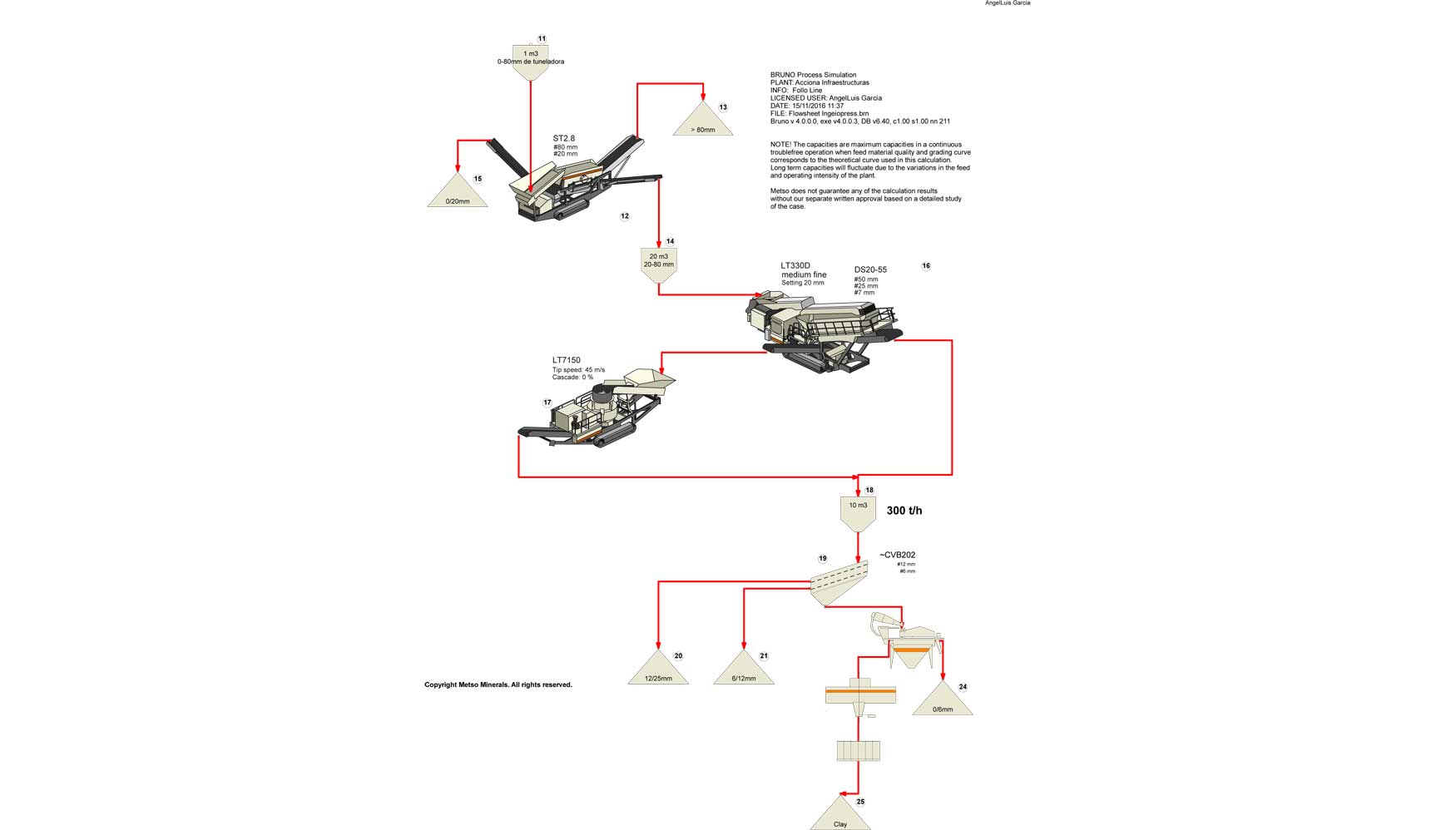
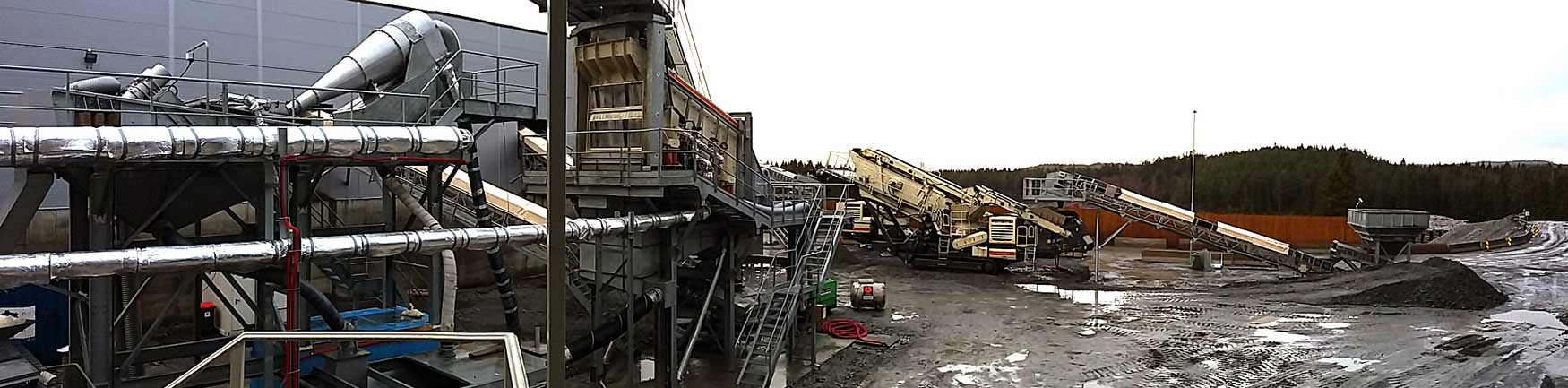
LT330D
El grupo móvil Lokotrack 330D es una unidad de trituración sobre orugas autopropulsada, equipada con un triturador de cono Metso GP330 de última generación, diseñado para altas exigencias en las aplicaciones más difíciles y con alto rendimiento en la trituración de roca dura. Cuenta con una abertura máxima de alimentación de 230 mm y una salida de 18-40 mm según reglaje. El accionamiento se realiza mediante un motor eléctrico de 315 kw de potencia.
El grupo está equipado además con: una criba DS 20-55 de tres bandejas de dimensiones de 5.550 x 2.000 mm y una superficie de cribado de 11 m2 por bandeja; un transportador principal de 1.200 mm de anchura y 10 m de longitud, con accionamiento eléctrico del tambor; dos transportadores de elevación de 1.200 mm de anchura y 6 y 7 m de longitud, con detector de metales incluidos. El transportador de sobretamaños tiene una anchura de 1.600 mm y 8 m de longitud. Cuenta además con dos transportadores laterales de 800 mm de anchura y 7 m de longitud.
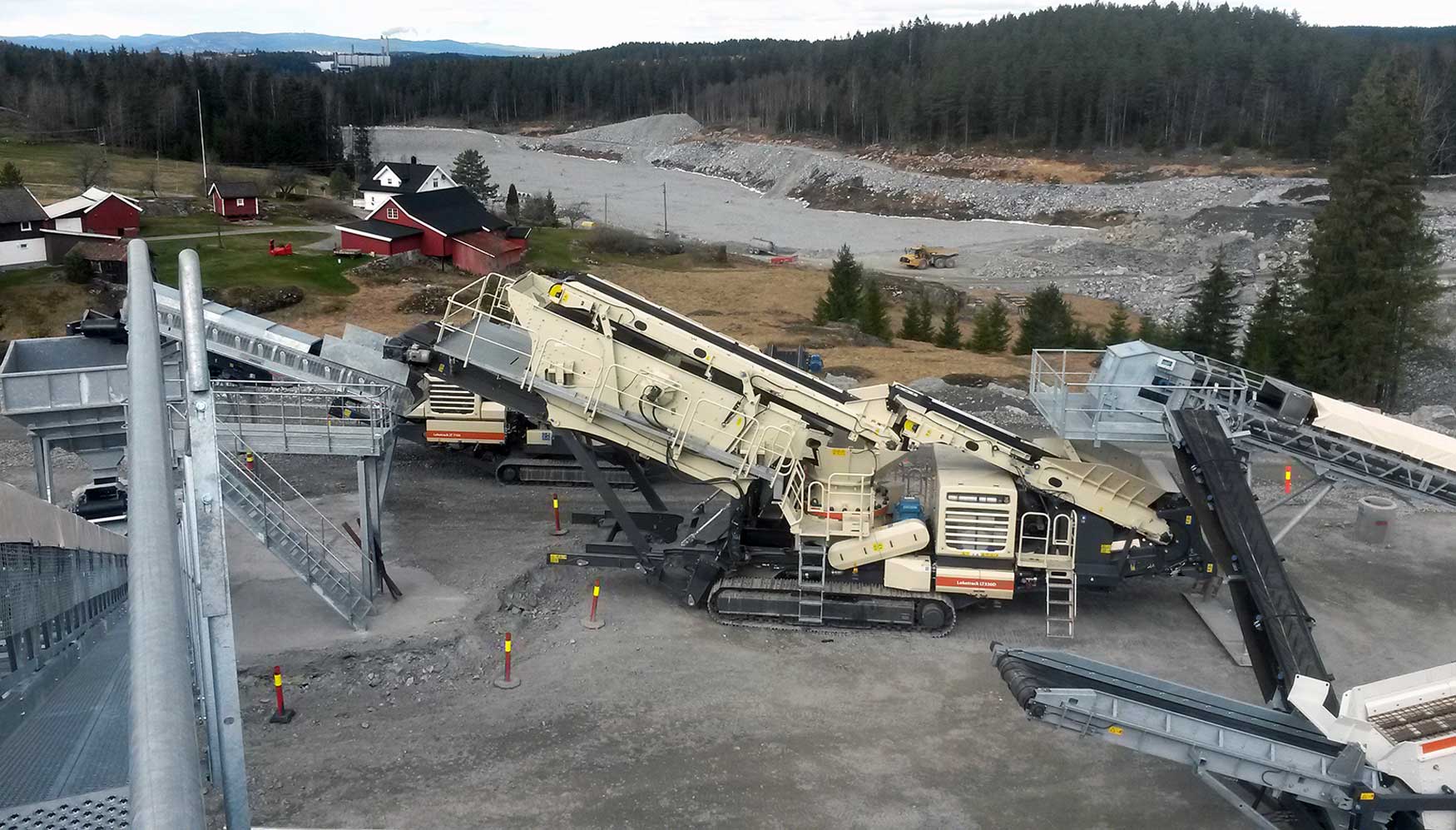
LT7150B
Es una planta móvil de trituración sobre orugas equipada con un triturador de impacto de eje vertical Barmac VSI 7150, idóneo para producir áridos de alta calidad en la etapa final de trituración, y caracterizado por el sistema de trituración de ‘piedra sobre piedra’. El rotor del triturador acelera el material y descarga continuamente sobre la cámara de trituración. Dentro de esta, las partículas alcanzan una gama de velocidades entre 45-70 m/s. El triturador está accionado accionado por un motor hidráulico directo, eliminando la necesidad de cintas transportadoras, lo que permite ajustar completamente la velocidad punta mediante el panel de control automatizado. La abertura máxima de alimentación es de 45 mm.
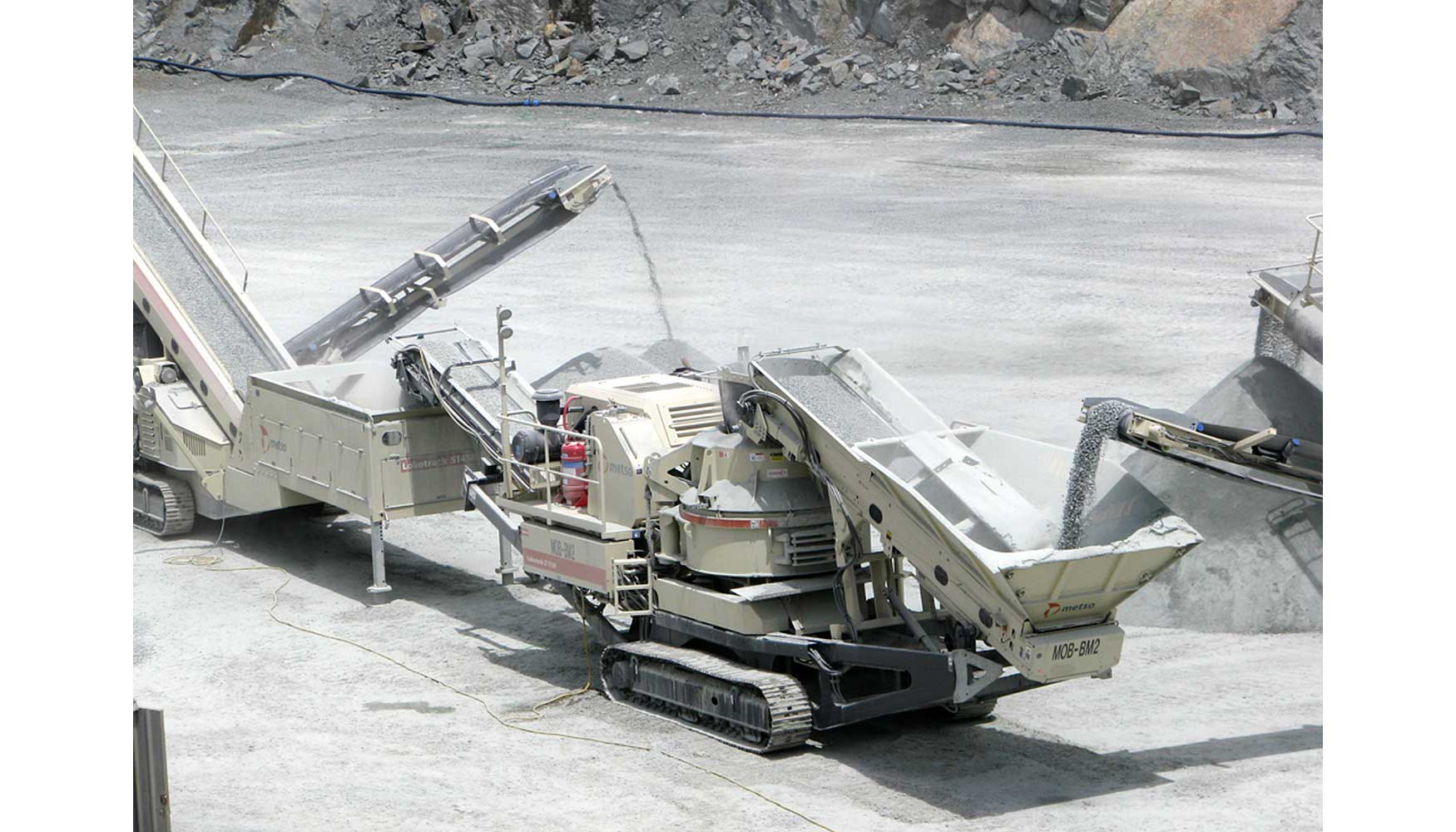
El transportador principal tiene una anchura de 800 mm y 10 m de longitud, con una altura descarga sobre el suelo de 3,1 m y está accionado por motor hidráulico.
Se alimenta mediante un alimentador de banda de 1.000 mm de anchura y 6 m de longitud, con una capacidad de tolva de 5 m3.El grupo está accionado por un motor diésel Cat C13 Tier 4 de 310 kW de potencia a 1.800 rpm. La transmisión de potencia es hidráulica.
Las dimensiones operativas del grupo son de 15,7 m de longitud, 3 m de anchura y 4,6 m de altura. Su peso operativo es de 30 t.
Criba ST 2.8
Se trata de una compacta planta móvil de precribado sobre orugas, equipada con una tolva de alimentación de 11 m3 de capacidad; y una criba inclinada de 2 bandejas de 4,8 m de longitud y 1,5 m de anchura con una superficie de cribado de 7,4 m2, lo que le permite producir un material más limpio y mejorar la separación de finos. La inclinación de la criba puede oscilar de 10 a 17º.
El grupo está accionado por un potente motor Caterpillar C4.4 de 75 kW de potencia que cumple las últimas regulaciones de emisiones y un nuevo sistema hidráulico con un menor consumo de combustible.
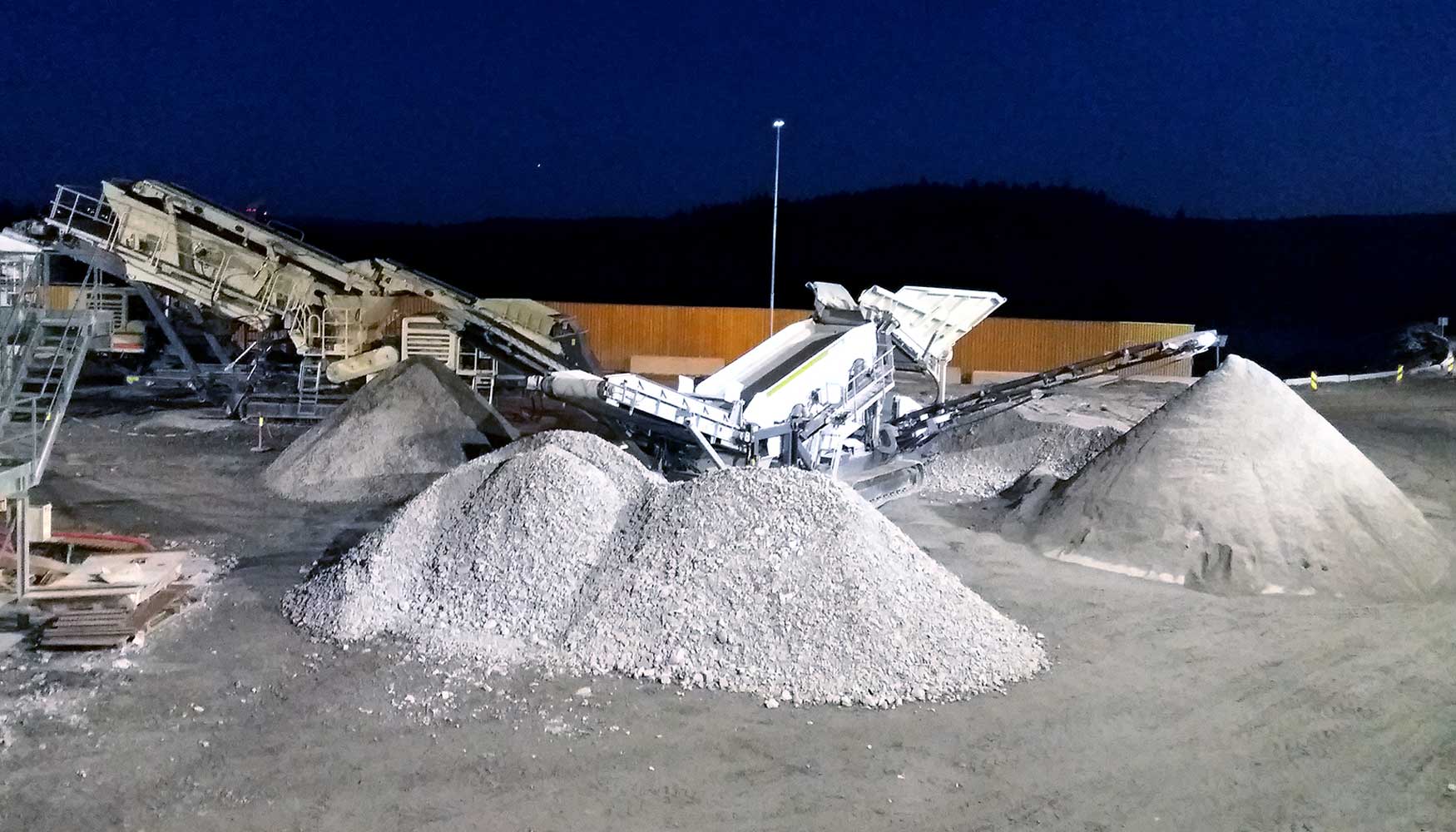
Las dimensiones operativas son de: 14, 4 m de longitud, 15,1 m de ancho y 4,97 m de alto. El peso del grupo es de 26 t.
Criba vibrante estacionaria CVB 202 con sistema de lavado de áridos
Las cribas inclinadas Metso de la serie CVB se caracterizan por su posibilidad total de configuración y están diseñadas para incorporar cualquier tipo de medio de cribado para una máxima flexibilidad operativa a la vez que para un mantenimiento seguro y simple.
En concreto, el modelo CVB 202 descrito cuenta con 2 bandejas de 1.870x4.880 mm cada una y una superficie de cribado de 9,1 m2. Equipa 2 vibradores modulares para el movimiento circular del material. La inclinación de la criba oscila desde 12 a 22º y su peso operativo es 10 t.
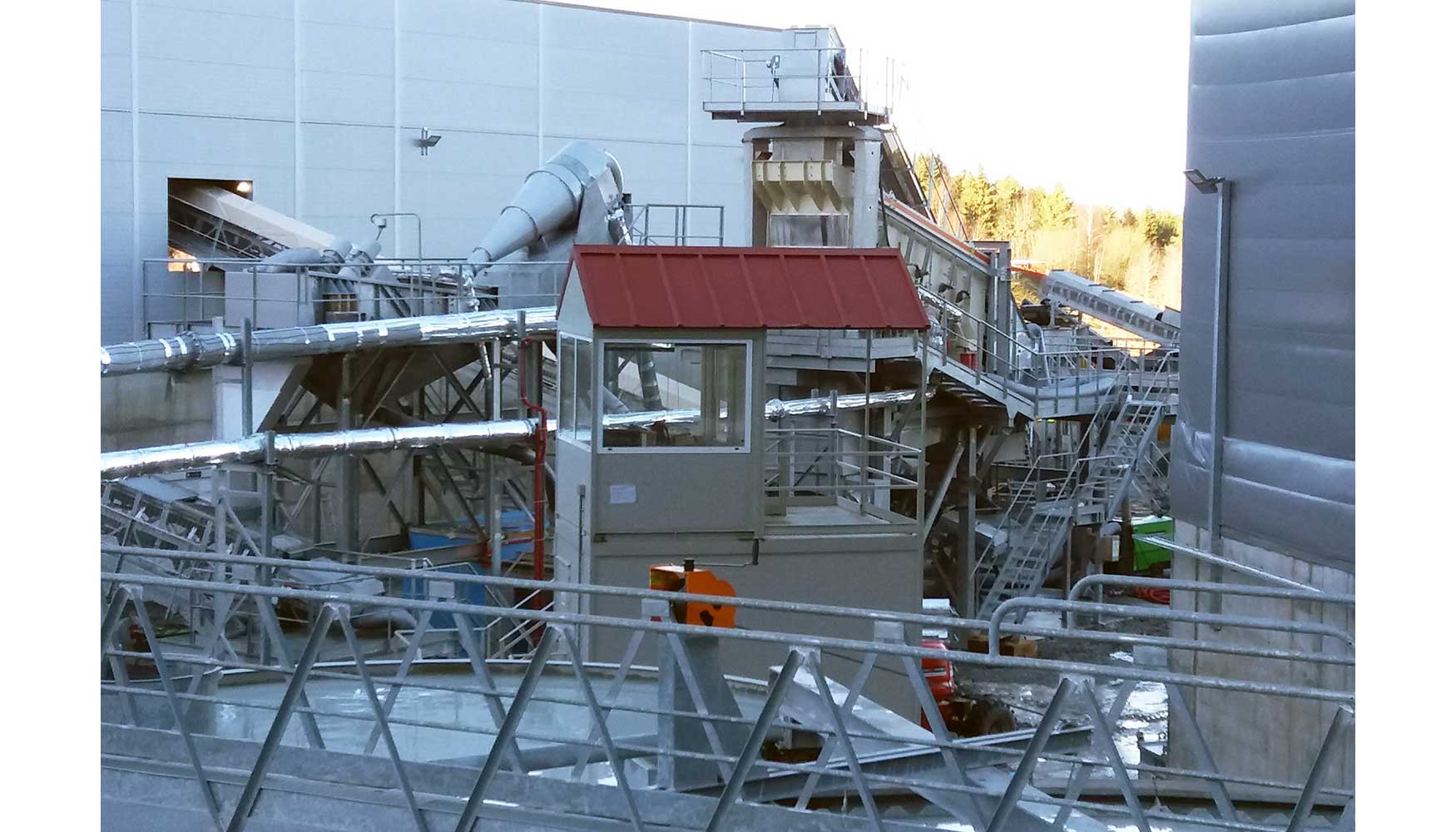
Diagrama de flujo
El diagrama de flujo de esta instalación (Fig. 6) refleja el funcionamiento completo de la instalación:
- La alimentación es un 0-100 de roca granítica procedente de las tuneladoras que excavan los túneles.
- Este 0-100 sufre un proceso de limpieza en una criba ST 2.8 del que se aprovecha el tamaño 20-80 mm.
- Este 20-80 es reducido en circuito cerrado a 0-25 mm mediante un triturador de cono sobre orugas LT330D.
- Para la obtención de un coeficiente de forma excelente todos los tamaños superiores a 6 mm se procesan en un molino de eje vertical sobre orugas LT7150B.
- Todo el 0-25 mm ya con coeficiente de forma excelente se clasifica en una criba estacionaria CVB 202 con lavado para la obtención de gravillas lavadas 12-25 mm, 6-12 mm.
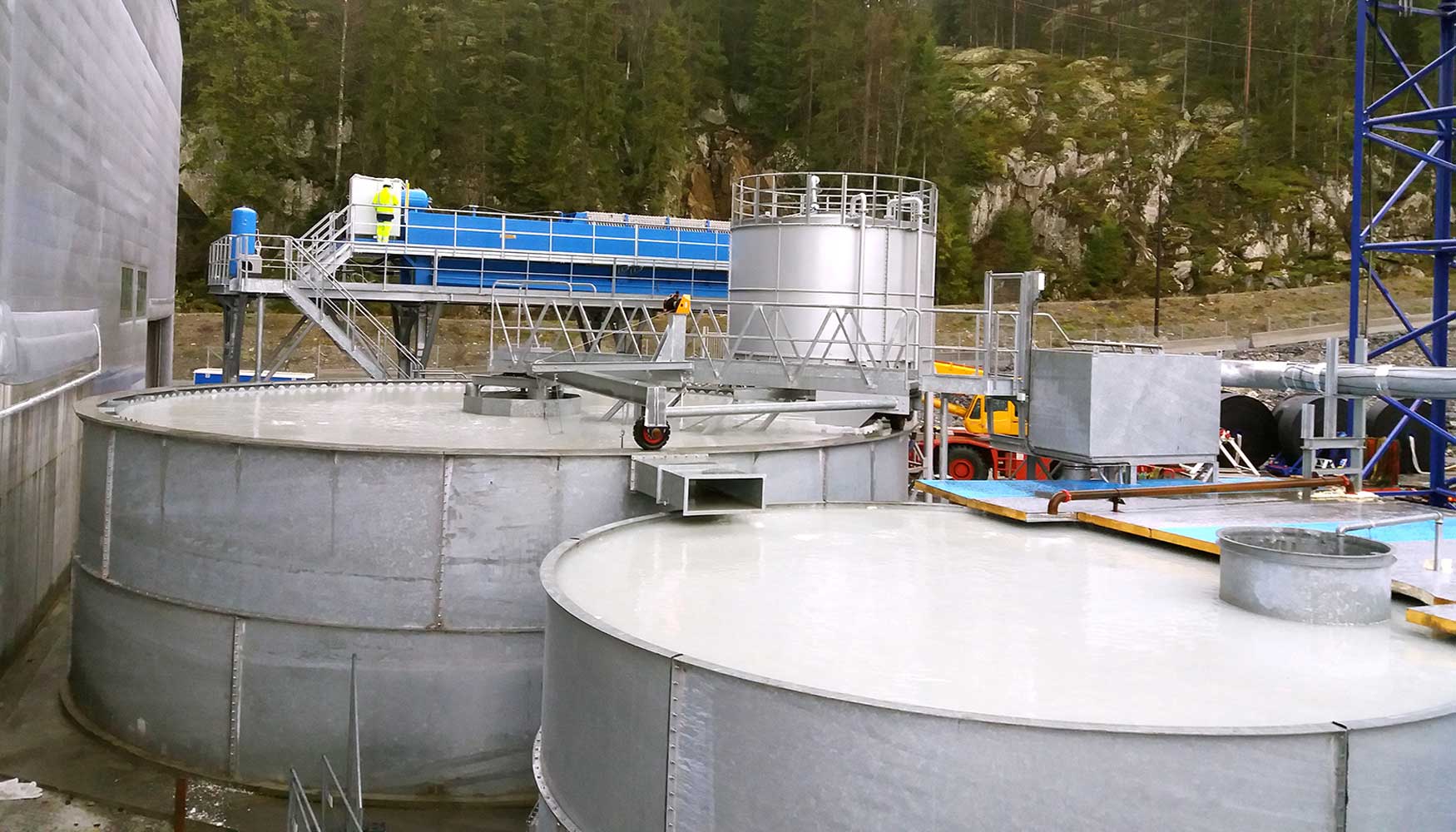
El 0-6 mm resultante se lleva a un grupo de tratamiento de arenas con hidrociclón, tanque espesador y filtro prensa para alcanzar la calidad requerida en este tamaño.