Stellantis utiliza por primera vez el horno eléctrico EcoInCure
Stellantis espera duplicar la capacidad total de su planta en Kenitra con un nuevo taller ‘llave en mano’ de Dürr. La avanzada tecnología de producción permite pintar de alta calidad vehículos eléctricos de manera respetuosa con el medio ambiente y ahorrando energía. Además, se está reutilizando los robots de pintura de otras plantas del Grupo, ahorrando así también recursos.
La nueva planta en el noroeste de Marruecos pretende ser un modelo de optimización energética y, al mismo tiempo, aumentar significativamente la capacidad de producción de Stellantis de vehículos propulsados por baterías y modelos híbridos de las marcas Peugeot, Citroën y Fiat. El nuevo diseño de la planta de pintura puede procesar 30 carrocerías por hora, un ritmo idéntico comparado con la primera planta en Kenitra construida por Dürr en 2019.
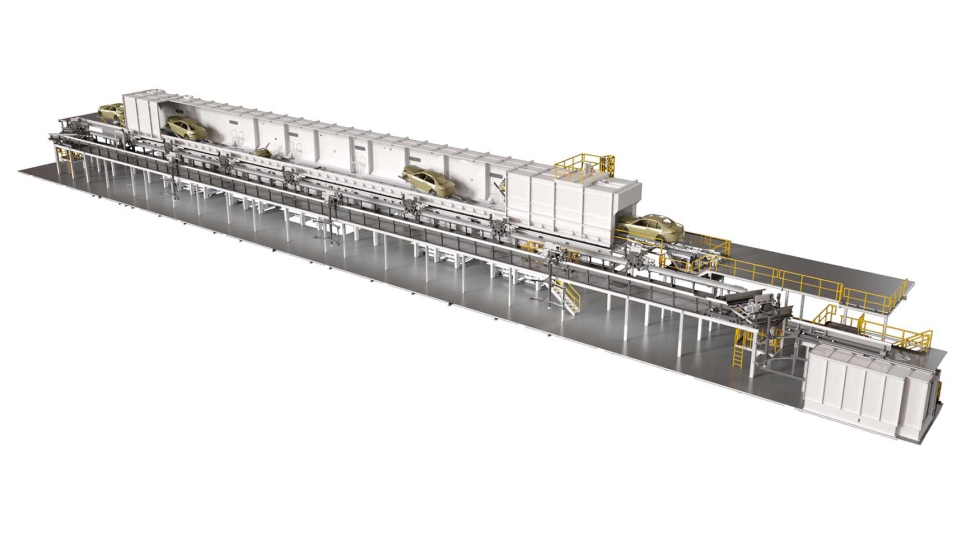
Ahorro de agua, productos químicos y energía calorífica
Stellantis optó por el proceso de inmersión por rotación RoDip patentado por Dürr para el pretratamiento y la cataforesis. Este innovador método hace girar las carrocerías alrededor de su eje, proporcionando así una protección excepcional contra la corrosión, ya que las curvas de inmersión se pueden adaptar individualmente a diferentes tipos de carrocerías optimizando el proceso de inmersión, inundación y drenaje. RoDip consume mucho menos agua, productos químicos y energía calorífica que otras soluciones técnicas, ya que el sistema transportador elimina la necesidad de secciones de entradas y salidas inclinadas dentro y fuera del tanque, acortando de esto modo la longitud del tanque de inmersión hasta seis metros y reduciendo su volumen. El menor consumo de energía y de material también reduce los costes operativos y, por ende, los costes unitarios.
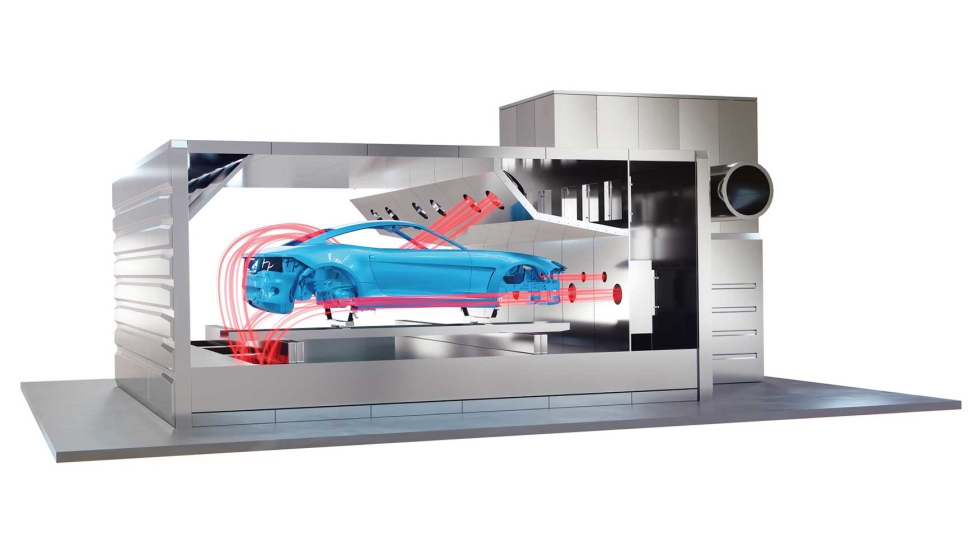
Un 40% menos emisiones de CO2
Después de la cataforesis las carrocerías pasan por un horno eléctrico, que además es la primera vez que se utiliza en una planta del Grupo Stellantis. El horno EcoInCure cuenta con una innovadora conducción del flujo de aire que calienta y enfría las carrocerías de manera uniforme desde el interior hacia el exterior. Este diseño único reduce las tensiones estructurales térmicas y disminuye el tiempo de calentamiento de la carrocería hasta un 30%. Al funcionar con electricidad verde de manera respetuosa con el medio ambiente, la última generación del EcoInCure instalada en la planta de Kenitra permite la independencia de los combustibles fósiles. En comparación con la versión alimentada por gas, el EcoInCure eléctrico reduce las emisiones de la planta de pintura en un 40% y disminuye así significativamente la huella de carbono.
Reutilización para un uso óptimo de los recursos
Stellantis también está mejorando la eficiencia optando por la tecnología 3-Wet (imprimación en húmedo), que permite ahorrar tiempo y energía. El extenso proceso, que incluye pintura bi-tono en tres estaciones de pintura de exteriores, utiliza robots y tecnología de aplicación de las plantas italianas ya existentes. Estos robots están equipados con aplicadores EcoBell2 que se adapten perfectamente a los equipos existentes. Además, los equipos técnicos, como unidades de suministro de aire, calentadores y transportadores, han sido transportados de Europa a Marruecos para su reutilización. Reutilizar la tecnología de producción obtenida de otras plantas es un paso más hacia la sostenibilidad para darle un uso óptimo a los recursos. Además, la reutilización es una herramienta adecuada para construir una planta de pintura dentro de las exigentes limitaciones marcadas por el tiempo y los costes, todo ello sin renunciar a la calidad de recubrimiento ni las prestaciones.