'Moulin de Verdonnet', uno de los molinos más automatizados del mundo
16 de septiembre de 2009
Un avance en automatización de molinos de trigo. Moulin de Verdonnet, una empresa familiar francesa, dependía básicamente del trabajo manual para garantizar que sus operaciones se realizaban sin problemas. Sin embargo, la instalación de un nuevo molino automatizado, de la mano de Rockwelll Automation, ha hecho posible que la nueva unidad procese 300 toneladas de trigo diarias.
Desde 1980, la compañía Moulin de Verdonnet desarrollaba su actividad a través de un molino parcialmente automatizado. En consecuencia, la capacidad de procesamiento de trigo se limitaba a unas 150 toneladas por día. Bajo la premisa de iniciar un nuevo desafío empresarial, Moulin de Verdonnet decidió invertir en un nuevo sistema de control, supervisión y seguimiento. Para su correcto funcionamiento, la nueva tecnología precisaba que las instalaciones del molino se administraran de manera automática y a distancia, además de mejorar su rendimiento. El sistema debía ser accesible, escalable y diseñado para ofrecer una larga duración. La compañía gala contrató a Rockwell Automation con el objetivo de desarrollar dicha aplicación en sólo cuatro meses.
Ahorro en los costes de mantenimiento y cableado
La implantación del nuevo molino no debía afectar a la actividad de Moulin Verdonnet. La compañía concedió un plazo de una semana para transferir las operaciones a la nueva unidad, sin que se interrumpieran los repartos añadidos. Durante el proceso, se utilizaron e integraron piezas individuales de equipo existentes y se añadieron y mejoraron prestaciones. La solución propuesta por Rockwell Automation incluía un sistema de distribución, basado en su concepto de arquitectura integrada. Se trata de una tecnología diseñada para minimizar el cableado y reducir el riesgo de averías. Así, dos ordenadores PC supervisan el proceso mientras que un tercero opera como servidor. Dos controladores ControlLogix de Allen-Bradley examinan y controlan la planta de producción. Unas 1.000 E/S se conectan en Flex E/S de Allen-Bradley en todos los niveles de producción y también a la red, junto con 350 motores (algunos de ellos en funcionamiento a través de variadores PowerFlex 70), los controladores y la estación de supervisión.
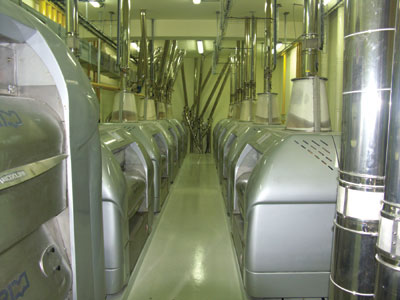
La nueva unidad detecta cualquier avería que se origine, circunstancia que comunica por teléfono al operario de servicio. Ello hace posible que el empleado tome las medidas oportunas, vía telefónica, al respecto. Si el fallo técnico se produce en horario nocturno, los propietarios del molino pueden modificar a modo manual el control sin salir de su domicilio. También pueden determinar las medidas que consideren necesarias para gestionar el incidente, gracias a un dispositivo de supervisión instalado en su vivienda.
La solución Rockwell Automation cumple con las expectativas de la empresa francesa, en cuanto a potencial para la escalabilidad en el tiempo, la adopción de estándares de comunicación (Ethernet, Modbus, Profibus y DeviceNet), sin olvidar la disponibilidad y sencillez de la arquitectura. Además, la nueva unidad proporciona un considerable ahorro energético, debido a su sistema de control. En el momento que recibe una señal de la compañía eléctrica, el sistema inicia y detiene la maquinaria del molino sin ayuda externa. Esto da lugar a tarifas reducidas de electricidad fuera de las horas punta.
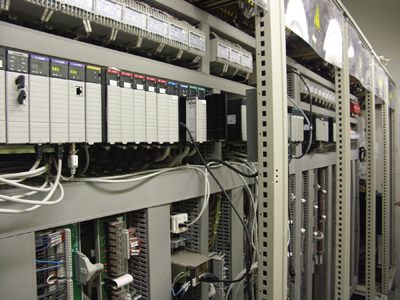
Notable incremento de la productividad
El diseño del hardware y el software influye, de manera positiva, en los costes de mantenimiento y cableado. Además, se ha calculado que el tiempo de improductividad ha sido de tres minutos en más de tres años. Desde el punto de vista operativo, la nueva tecnología ofrece comodidad, rápida capacidad de respuesta, autonomía y flexibilidad. Sin ir más lejos, un solo operario puede supervisar la calidad y producción en las instalaciones, mientras que un molino convencional precisa de cuatro trabajadores para desempeñar las mismas tareas. Con sólo tres clics de ratón, se cambia de una producción a otra y se agiliza la gestión de nuevos pedidos. En síntesis, el tiempo de improductividad se ha reducido a tres minutos en más de tres años.