Rusell Compact Sieve dispara la eficiencia en el centro de fabricación aditiva de New Balance
Fundada en 1906, New Balance Athletics, Inc., informalmente conocido simplemente como New Balance, es uno de los mayores fabricantes de calzado deportivo del mundo. Basado en la innovación, la corporación tiene como objetivo sortear las prácticas convencionales de la industria y proporcionar productos excepcionales para atletas profesionales y consumidores diarios. Una de las últimas innovaciones de New Balance ha sido la instalación de un laboratorio de fabricación aditiva junto con la producción del primer calzado impreso por láser. El Zante Generate es la primera deportiva con suela impresa por 3D del mundo. Compuesta de elastómero TPU Duraform, la revolucionaria zapatilla se ha hecho usando un proceso de sinterizado por láser; que convierte este polvo en secciones cruzadas sólidas usando un láser.
Un laboratorio de doble propósito usado para la investigación y desarrollo de un nuevo producto, las instalaciones de fabricación aditiva procesan una variedad de polímeros diseñados con diferentes gradaciones incluyendo poliuretano termoplástico (TPU) y nylon. Inicialmente, el laboratorio de New Balance empezó procesado pequeños lotes de trabajo.
Sin embargo, buscando una transición del laboratorio a una mayor escala de comercialización, New Balance acudió a Russell Finex, compañía mundial de tecnología de separación por malla fina, buscando una solución más eficiente para conseguir un incremento del rendimiento y una mejora de la fluidez del polvo.
Después de varias reuniones técnicas y la realización de pruebas de comportamiento y resultados del producto en la instalación de prueba especializada de Russell Finex, New Balance adquirió un tamizador industrial Russell Compact Sieve y Vibrasonic Deblinding System. Esta combinación no solo cumple las necesidades de incremento de rendimiento de este gigante atlético, sino que también asegura la pureza de los polvos procesados. El Russell Compact Sieve es un tamiz industrial versátil de alta capacidad que tiene la mitad de altura que un tamiz tradicional. Equipada con suspensión de goma, el revolucionario tamiz permite una operación más silenciosa – tan baja como 70dBA. Diseñado para minimizar el tiempo de limpieza, la unidad permite el fácil desmontaje sin necesidad de herramientas; permitiendo a los operadores acceder fácilmente a la malla filtrante.
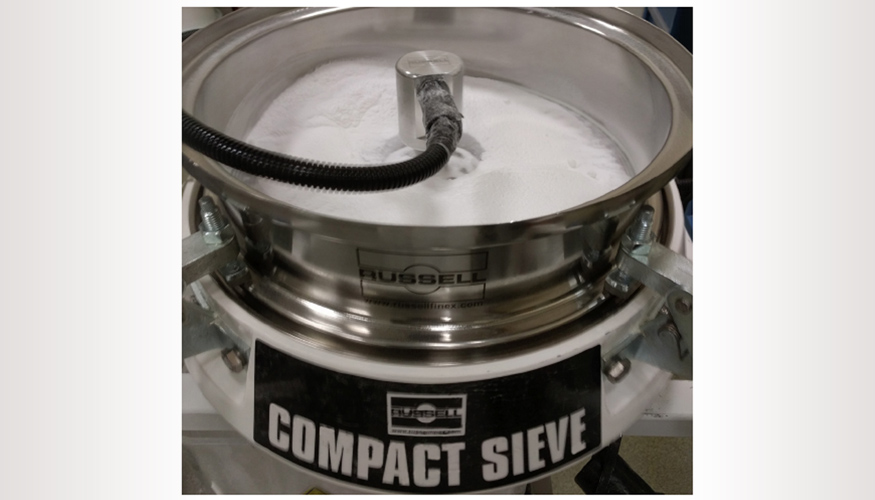
Figura 1. Tamizador Russell Compact Sieve en New Balance.
- Productividad incrementada consiguiendo una distribución de partículas por tamaño precisa.
- Diseño compacto que se ajusta fácilmente a las instalaciones existentes y áreas con espacio limitado.
- Cegado o colmatado de la malla eliminado con el Russell Vibrasonic Deblinding System.
De acuerdo con Daniel Dempsey, ingeniero senior de Fabricación Aditiva en New Balance, el sistema de tamizado por ultrasonidos, es una ventaja extremadamente valiosa para el laboratorio permitiendo un procesado sin interrupciones de los diferentes materiales variando la distribución del tamaño de partículas. Para los inventores de la tecnología de decolmatado para tamices por ultrasonido, el Vibrasonic Deblinding System patentado de Russell Finex asegura que los polvos difíciles y frágiles son rápidamente procesados. Además, el sistema asegura que el equipo continúa funcionando en su rendimiento óptimo, mantiene las tasas de rendimiento, maximiza la vida de las pantallas de las mallas, y minimiza la pérdida de producto en buen estado.
“Poniéndolo en términos numéricos”, afirmó Dempsey, “tamizar 20 kg de material usando el equipo OEM que ya teníamos llevaría aproximadamente ocho horas. Con el tamiz [Russell Finex] equipando el sistema Vibrasonic, podemos hacer la misma cantidad en básicamente diez minutos”.
Ahora el tamizador Russell Compact Sieve con el sistema de decolmatado Vibrasonic Deblinding System se utiliza en el laboratorio de fabricación aditiva de New Balance diariamente.
Para New Balance, usar el tamiz es básico para airear el polvo antes de que el material entre en la máquina de sinterización por láser. Airear el polvo incrementa la fluidez del material, lo que se requiere para un proceso estable de impresión que funciona las 24 horas.
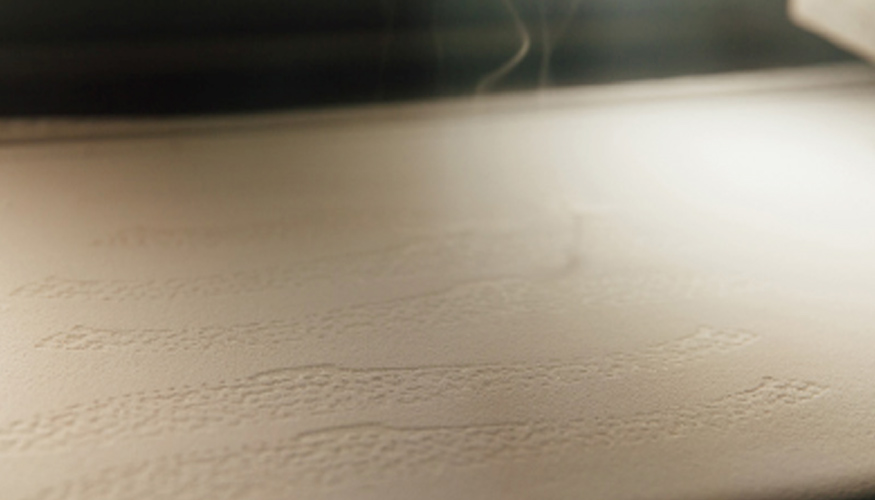
Además de incrementar la fluidez, el sistema de tamizado también ha conseguido proporcionar tiempo libre para el equipo ingeniero del laboratorio de fabricación aditiva ya que tamiza el polvo mucho más rápido que los tamices tradicionales monitorizados durante todo el día. El añadido del sistema de tamizado de Russell Finex para la fabricación aditiva también ha permitido a New Balance experimentar con polvo y completar lotes de trabajo personalizados de una manera mucho más rápida. En relación al mantenimiento, Dempsey afirma, “Nunca he tenido que hacer nada con este equipo salvo utilizarlo y limpiarlo. Es fantástico”.
Dempsey resumió los extensos beneficios del Russell Compact Sieve con tecnología por ultrasonido al afirmar, “El sistema nos permite acelerar el proceso de tamizado, y hemos incrementado drásticamente nuestra capacidad de iterar o abocetar dentro de la empresa debido a que podemos abocetar el artículo directamente y saltar un par de rondas de moldeado por inyección antes de su comercialización. Debemos considerar cómo esto afecta a la calidad del producto, ya que a mayor iteración, mejor producto se conseguirá.” Dempsey también concluyó que la capacidad de tratamiento y tamizado del tamizador Russell Compact Sieve con el Vibrasonic Deblinding System ha sido básico para ayudar a los esfuerzos de investigación en las instalaciones de fabricación aditiva de New Balance.
Durante 80 años, Russell Finex ha fabricado y proporcionado soluciones de separación en malla fina altamente eficaces para una multitud de industrias incluyendo: alimentación, farmacéutica, cerámica, química, polvos metálicos y procesado de agua. Considerado como un especialista global en filtrado y tamizado, el innovador equipo de Russell Finex facilita la seguridad del operario, minimiza los tiempos de inactividad, cumple estrictos estándares de higiene, y asegura que los productos procesados son de la mayor calidad y están libres de contaminación.
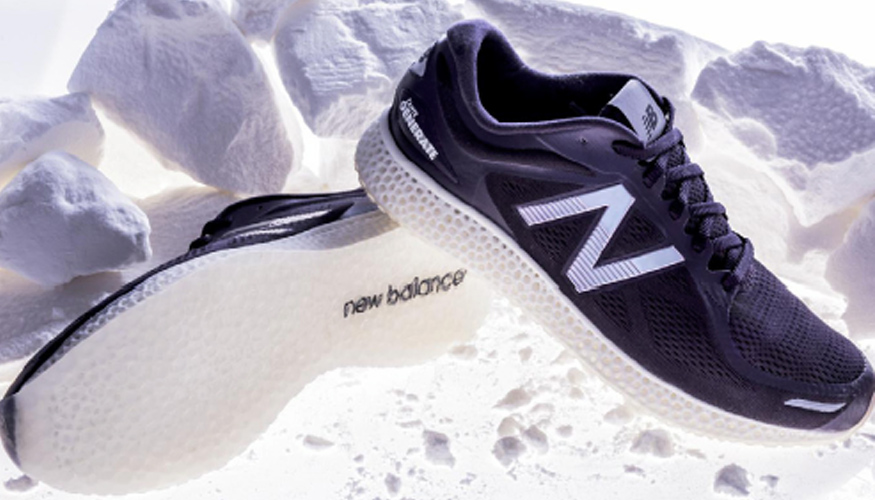
Figura 3. La deportiva New Balance Zante Generate con suela de impresión 3D.
"Poniéndolo en términos numéricos tamizar 20 kg de material usando el equipo OEM que ya teníamos llevaría aproximadamente ocho horas. Con el tamiz [Russell Finex] más Vibrasonic, podemos hacer la misma cantidad en básicamente diez minutos", Daniel Dempsey, ingeniero Senior de Fabricación Aditiva en New Balance