Samuel Rütsche, ingeniero de estructuras de Aris Piccard: "El SLS es muy adecuado para el sector aeroespacial, porque permite utilizar componentes muy ligeros e integrar varias funciones en una sola pieza"
La impresión 3D lleva la cohetería estudiantil a nuevas cotas
Con su cohete híbrido, el proyecto estudiantil Piccard alcanza una altitud de más de 6 kilómetros y establece un nuevo récord mundial. Para la construcción de su cohete ganador, el equipo se basó en varias tecnologías de impresión 3D, como el sinterizado láser selectivo.
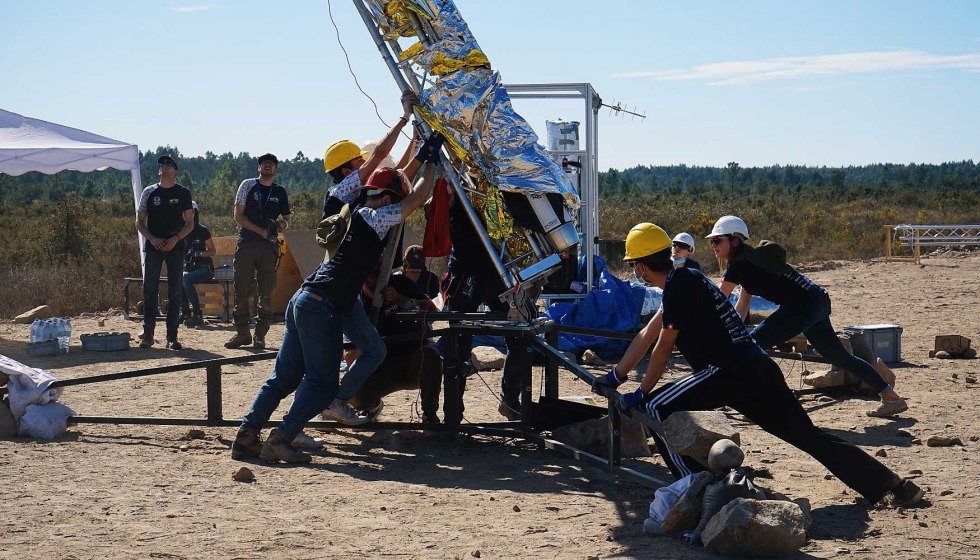
En la competición EUROC 2021, el cohete Piccard estableció un nuevo récord mundial en la categoría híbrida. Fuente de la imagen: Aris Piccard.
Un lanzamiento inaugural para recordar
El European Rocketry Challenge EUROC en Portugal el pasado mes de octubre. En el paisaje desértico se oye la voz de un altavoz: "¡Tres...dos...uno...encendido!" Lo que sigue es un momento de silencio que parece una eternidad. Pero entonces, un motor estalla y el cohete Piccard se eleva directamente hacia el cielo, estableciendo un nuevo récord mundial con una altura de vuelo de 6.500 metros. Un momento histórico para la Iniciativa Espacial Académica Suiza Aris: nunca antes ningún cohete híbrido de esta categoría, investigado y desarrollado por estudiantes, había volado tan alto.
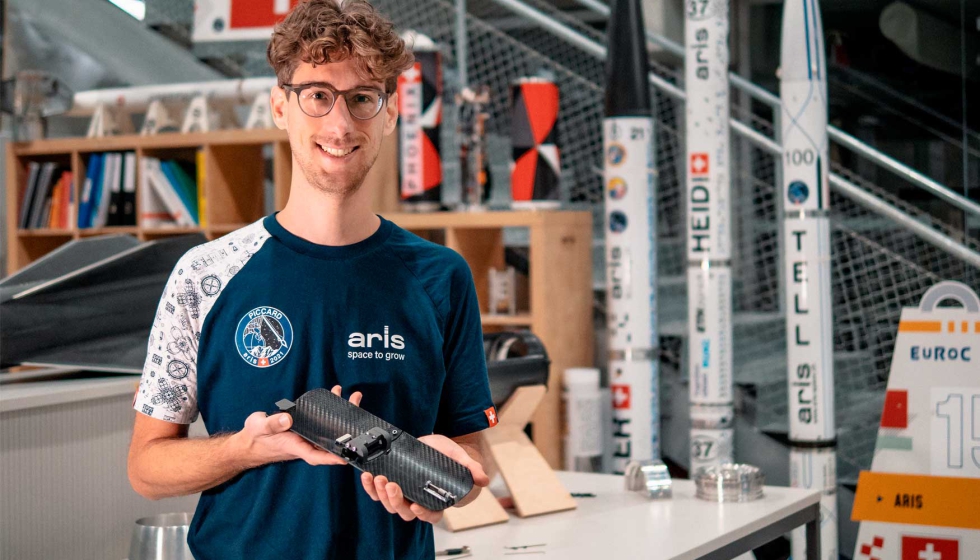
Construir un cohete en menos de un año
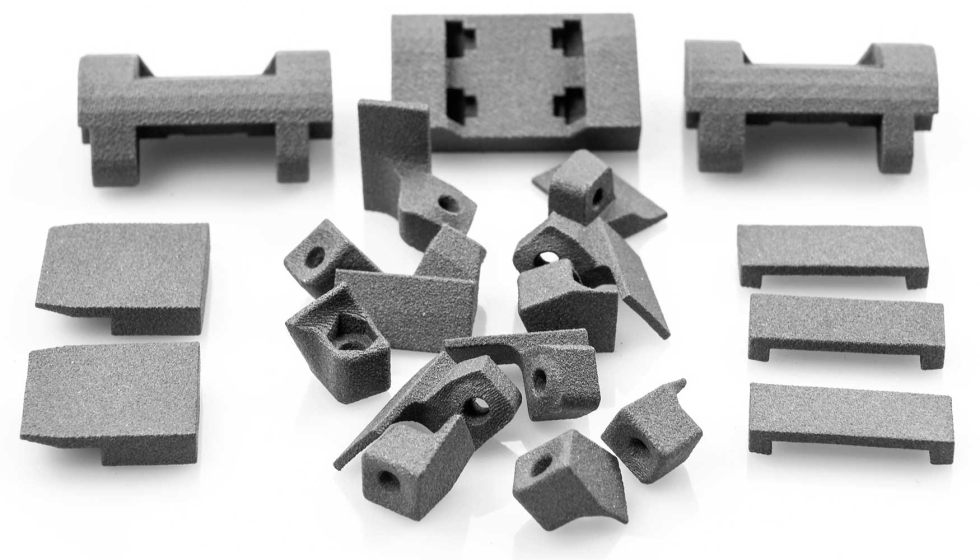
Un mecanismo de acoplamiento avanzado
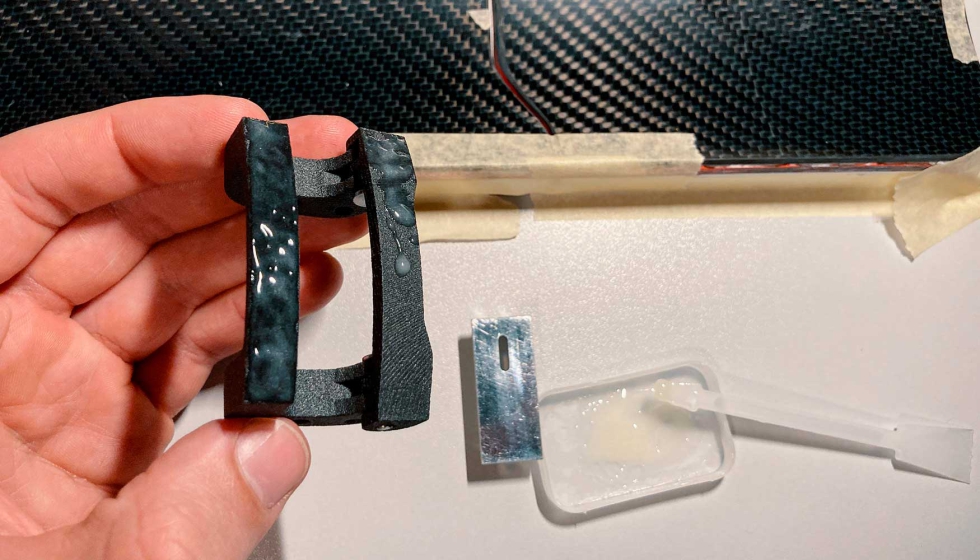
Una bisagra de escotilla sinterizada por láser
Para desarrollar y probar rápidamente sus diseños, el equipo Piccard se basó en prototipos FDM. Para las piezas estructurales más exigentes, como la bisagra de la escotilla, el sinterizado selectivo por láser (SLS) era la mejor solución. “El SLS se puede utilizar muy bien en el sector aeroespacial, porque permite fabricar componentes muy ligeros e integrar varias funciones en una sola pieza”, señala Samuel. Posteriormente, Sintratec fabricó y patrocinó las piezas de nailon PA12 necesarias. Según Samuel, “las propiedades del material de las piezas de Sintratec son (casi) isotrópicas y tienen una mayor resistencia a la temperatura que nuestras impresoras FDM”, una ventaja clave cuando se trata de las condiciones extremas en las que tienen que funcionar estas piezas.
Una vez que las piezas se combinaron con la escotilla, el mecanismo funcionó como estaba previsto y proporcionó un carenado del cohete sin problemas durante el despegue. “Esto hizo que nuestro cohete no se derritiera bajo el sol y, por tanto, contribuyó al éxito del lanzamiento que tuvimos en octubre”, resume Samuel.
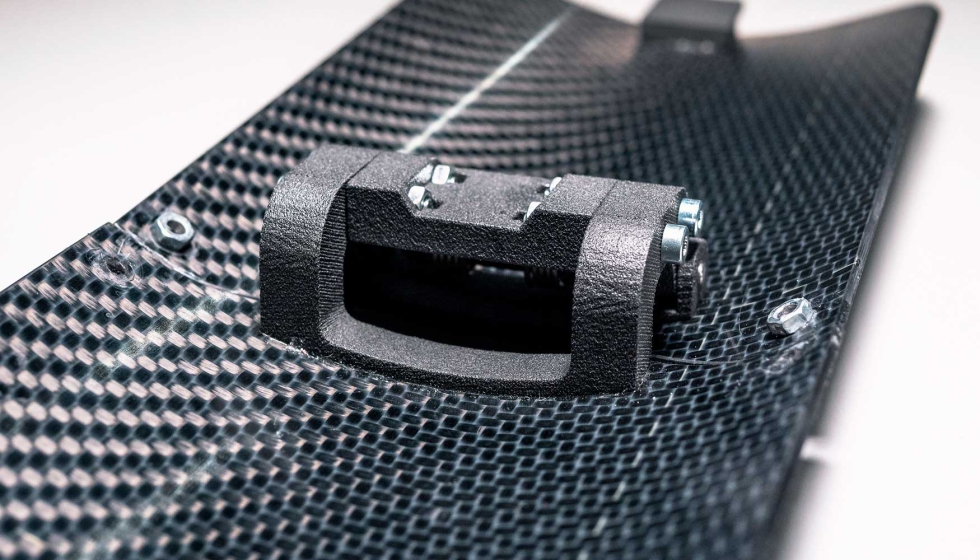
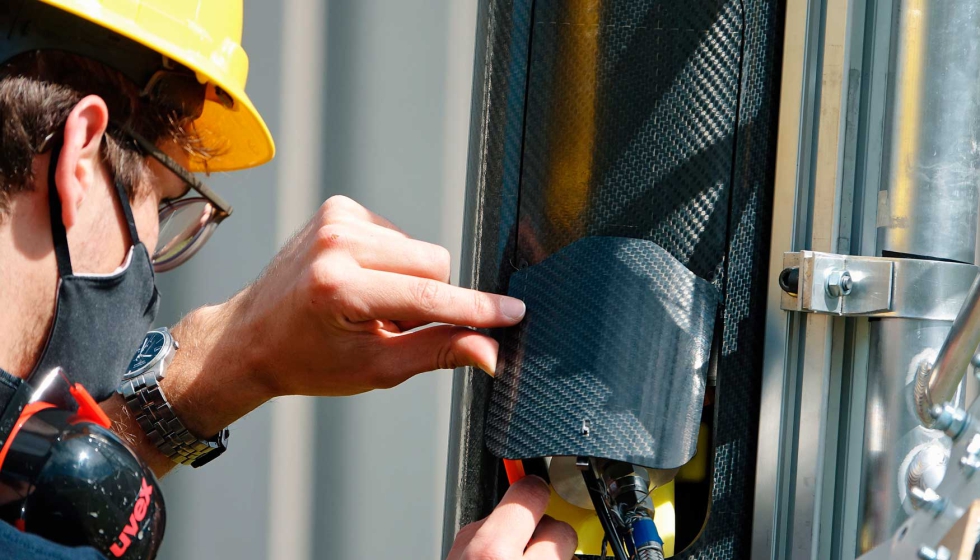