Gefasoft confía en XTS para el control de calidad de piezas cilíndricas de chapa mediante inspección óptica
La empresa Gefasoft Automatisierung und Software GmbH, con sede en Regensburg, Alemania, ha desarrollado una instalación de comprobación especialmente compacta para el control óptico de piezas cilíndricas de chapa. Esta instalación se utiliza para comprobar de forma fiable difusores de airbags de vehículos con un total de once estaciones de cámara con tiempos de inspección variables. La gran flexibilidad de transporte de los componentes mediante XTS permitió paralelizar los procesos de control individuales de la compleja secuencia de comprobación, optimizando así la capacidad de producción.
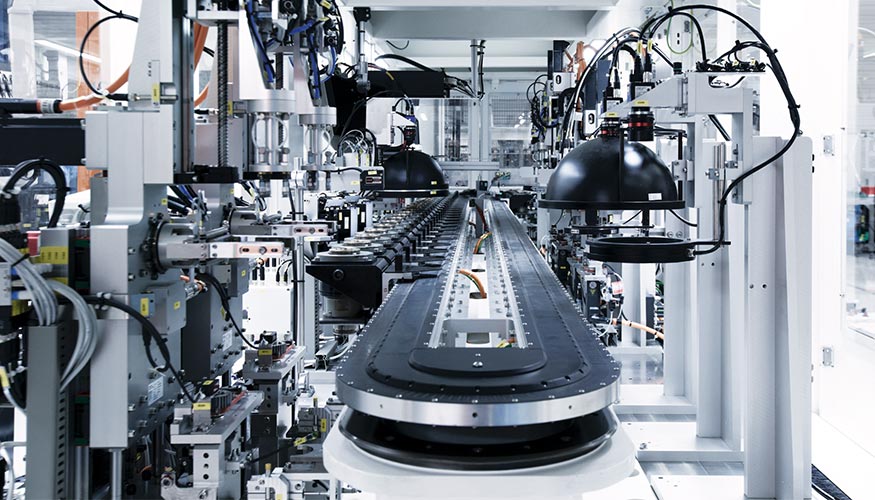
Habitualmente, la inspección óptica automática de componentes requiere una serie de cámaras en varias estaciones de control conectadas en serie o en paralelo para cubrir todos los criterios de inspección de componentes con geometrías complejas. Esto también es válido para la instalación de control Sova-VIS 16 de Gefasoft Automatisierung und Software GmbH en Regensburg, que comprueba difusores para airbags de vehículos. Estos componentes de chapa de embutición profunda, en forma de copa, que presentan diversas variantes y un diámetro de unos 60 mm, se consideran componentes críticos para la seguridad y deben someterse a un exhaustivo control de la superficie interior y de la superficie exterior antes de su procesamiento posterior.
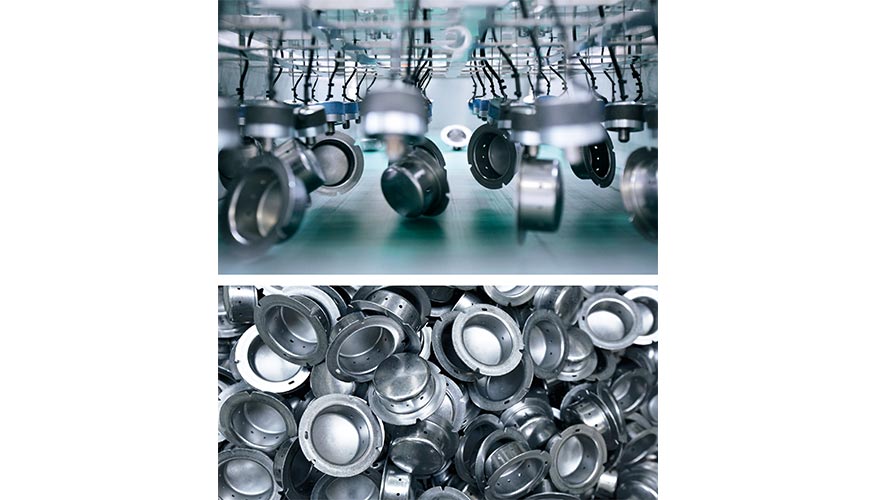
Los difusores, como componentes de conexión críticos para la seguridad entre los airbags de vehículos y los dispositivos de hinchado o generadores de gas, deben controlarse de forma rápida, eficiente y fiable. Foto: Beckhoff.
XTS compensa las diferencias de tiempo y simplifica las extensiones
Mientras que algunas de las tareas de control requieren una sola captura de imagen, otros requisitos del catálogo de errores requieren una sofisticada tecnología de iluminación con múltiples capturas de imágenes. Sobre todo, la pared interior del difusor representa una superficie funcional crítica, que debe ser comprobada detalladamente para detectar los defectos más pequeños en la superficie de acero con tamaños que rondan los múltiplos de 10 µm. Para conseguir la resolución de imagen requerida, se utilizan cámaras de barrido lineal delante de las cuales se gira la pieza. En particular, el giro completo de la pieza requiere algo más de 2 s de tiempo de captura. El resultado es una distribución muy poco homogénea de los tiempos de captura de imágenes entre las distintas estaciones de control.
Si todas las estaciones de cámara estuvieran concatenadas con un sistema de transporte rígido –por ejemplo, una mesa rotativa– la estación con el tiempo de captura de imágenes más largo determinaría el tiempo de ciclo más corto del sistema de transporte y, por lo tanto, limitaría la capacidad de producción. Sin embargo, con XTS como solución extremadamente flexible, las estaciones de control más rápidas pueden funcionar de forma secuencial, mientras que las más lentas y, por lo tanto, de las cuales se dispone varias, pueden alimentarse de forma paralela con componentes. El director de Marketing de Gefasoft, Georg Schlaffer, comenta al respecto: “En la instalación de control Sova-VIS 16, el tiempo de captura de imágenes muy heterogéneo de los pasos de control condujo a la búsqueda de un concepto de máquina con un transporte flexible y asíncrono de los componentes, para resolver de forma elegante la tarea establecida en condiciones de espacio limitadas. El sistema XTS de Beckhoff con sus Mover controlables de forma independiente cumple estos requisitos de forma muy convincente. De este modo, a pesar de contar con estaciones de control individuales con tiempos de ensayo más largos, se puede alcanzar un tiempo medio de ciclo de 1,9 s por componente. Gracias al uso del sistema XTS, también fue posible conseguir un footprint significativamente menor en comparación con otras soluciones y, por lo tanto, cumplir con los requisitos de espacio del cliente final”.
Christian Schärtl, director de ingeniería de Gefasoft, añade: “El cliente final especificó un tiempo de ciclo inferior a 2 s debido a la gran demanda de estos componentes. Sin embargo, dos de los controles duran casi 4 segundos, es decir que estas estaciones tuvieron que ser duplicadas y paralelizadas para cumplir con el requisito. Esto es posible gracias a la flexibilidad del sistema XTS. Todas las soluciones con portapiezas y desvíos, basados en correas o cadenas, habrían sido mecánicamente mucho más complejas y probablemente no habrían alcanzado el tiempo de ciclo de 2 s, y esto con una necesidad de espacio considerablemente mayor”.
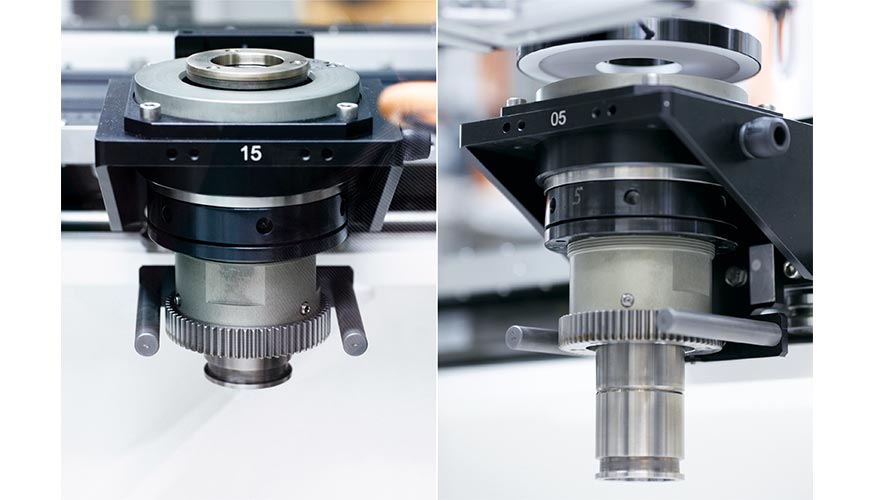
Mover XTS con un mandril de soporte en la parte superior (izquierda) o inferior (derecha) soportan el difusor a ser controlado en la orientación “sombrero” o “copa”. También puede verse la corona dentada para girar el componente en el Mover delante de la cámara de barrido lineal. Foto: Beckhoff.
Debido a la gran cantidad necesaria de estaciones de inspección con cámaras, el trayecto de transporte del XTS, sobre el que se mueven un total de 30 Mover, tiene una longitud aproximada de 11 m. El trayecto de transporte se ha equipado con un sistema de guiado especial de Hepco debido a que los Mover son relativamente pesados. La masa desplazada de aproximadamente 4 kg por Mover es el resultado de los requisitos del soporte de los componentes con unidades de elevación y de giro. Esto se debe a que los difusores deben girar con precisión delante de las cámaras de barrido lineal y deben ser transportados en dos posiciones (“sombrero” o “copa”) para el control de la parte superior y la parte inferior.
Desde el comienzo, el objetivo era una única máquina de control con la que se pudiera automatizar completamente la antigua inspección visual de los difusores, desde la retirada automática de un palé hasta el apilado o la clasificación mediante robot. La alternativa de una separación de las tareas de control en varias instalaciones independientes no era una opción rentable para el cliente final. Además de la compleja logística entre las instalaciones y la necesidad de más espacio, la separación y alimentación de los difusores a partir de contenedores de material a granel también hubiese requerido un gran esfuerzo. Según Georg Schlaffer, el sistema XTS también ofrece una ventaja adicional: “Con XTS se pueden integrar más puestos de trabajo de forma flexible a lo largo del trayecto. Esto garantiza que es posible adaptarse a posibles tareas futuras”.
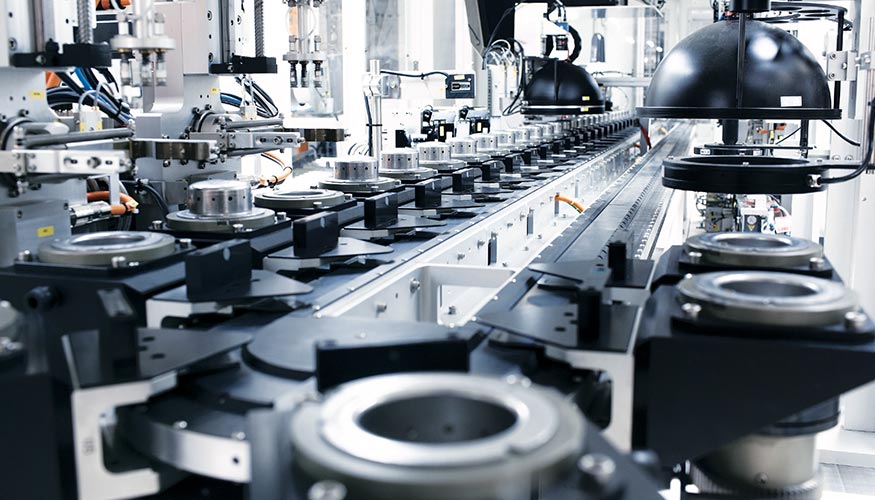
Las piezas de chapa controladas en la orientación ‘sombrero’ y ‘copa’ pasan mediante el transporte flexible XTS por las secuencias de control paralelizadas. Foto: Beckhoff.
Una instalación de control para todo el proceso
Los componentes se alimentan a la instalación de control mediante cajas de rejilla para piezas a granel después de desengrasar la superficie. A continuación, una pinza los transfiere individualmente de una cinta de alimentación al sistema XTS. El soporte de las piezas en el Mover XTS requiere una orientación de la posición de giro del componente. Para ello, en la posición de transferencia se encuentra integrada una estación de cámara que detecta la orientación angular de la pieza y supervisa adicionalmente el tipo de variante del difusor. En la parte superior del difusor hay una marca para la identificación del lote, que se comprueba en una primera estación de cámara.
Tras el control de la marca de lote, se controla la parte interior del difusor. Para ello, primero es necesario girar los componentes en el Mover, de la orientación “sombrero” a la orientación ‘copa’, es decir, con la apertura hacia arriba. Los componentes se levantan del Mover con una pinza, se giran 180° y se vuelven a colocar sobre el Mover. Mientras tanto, el mandril interior se retrae para que el componente se centre en su diámetro exterior y se fije apoyado sobre la brida. Para el control de la superficie se utiliza una cámara de barrido lineal, delante de la cual se gira la pared interior del componente. Christian Schärtl comenta al respecto: “Un verdadero desafío representó la limitación espacial, dado que cuatro direcciones de iluminación y la cámara tenían que encontrar espacio dentro del componente con un diámetro interior de aproximadamente 60 mm. La solución fue diseñar una unidad integrada de iluminación y cámara que penetra en el componente, mientras que un servomotor se acopla al mandril giratorio del Mover desde el exterior. Para ello se desarrolló además un sistema electrónico de control rápido para la iluminación. La inserción de la unidad de iluminación en el componente y el giro tardan un poco más de 2 s. Por este motivo, para lograr el tiempo de ciclo de la línea de 1,9 s, se dispusieron dos de estas estaciones de control”.
Las estaciones de volteo van seguidas de una estación de control para las desviaciones de material de la parte interior y una estación para controlar el fondo del difusor. En una estación de cámara final en este primer trayecto lineal del sistema XTS se controla si la brida del componente presenta defectos. Por lo tanto, hay seis estaciones de cámara a lo largo del primer trayecto lineal, en el que se duplican las estaciones de cámara de barrido lineal para la inspección de la pared interior, así como las estaciones de volteo, es decir que se cuenta en total con nueve posiciones de trabajo.
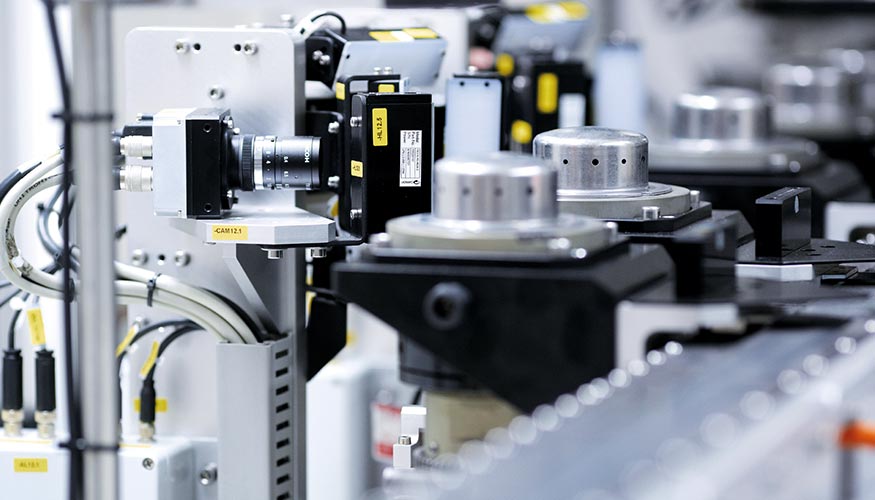
Con XTS, Gefasoft fue capaz de optimizar el control de calidad de piezas cilíndricas de chapa. Foto: Beckhoff.
Después de que los Mover han pasado la curva de 180° del XTS, otras estaciones de cámara así como una estación de impresión para marcar los componentes comprobados son operados en el trayecto lineal de retorno. En primer lugar, los componentes en los Mover se giran de la orientación ‘copa’ a la orientación ‘sombrero’, antes de que la pared exterior del componente se gire ante una estación de cámara de barrido lineal, de la cual también se disponen dos unidades. A continuación, le siguen el control de la parte superior de la brida, una impresora de inyección de tinta sincronizada con el movimiento del Mover XTS para el marcado de componentes defectuosos controlado por cámara y un marcador láser para la codificación de las piezas buenas. Al final del segundo trayecto lineal XTS, los componentes son retirados del Mover por un robot Fastpick Stäubli TP80 y depositados para su posterior procesamiento.