Fabricación aditiva robusta y fiable con la nueva Lasertec 30 SLM 3rd Gen
DMG MORI sienta nuevas bases para la fabricación aditiva con la presentación de la Lasertec 30 SLM 3rd Gen en su jornada de puertas abiertas en Bielefeld, Alemania, celebrada del 11 al 14 de junio.
Esta nueva plataforma para la fabricación aditiva ha sido diseñada desde cero utilizando todo el know-how de diseño aditivo y de máquina-herramienta dentro de DMG MORI. Con su nueva área de trabajo de solapamiento total de láser cuádruple, y un volumen de construcción de 325 x 325 x 400 mm, se apunta al centro de la demanda del mercado. La Lasertec 30 SLM 3rd Gen es la nueva referencia en cuanto a robustez y repetibilidad.
La Lasertec 30 SLM 3rd Gen se basa en los puntos fuertes de las versiones anteriores y se adapta a los requisitos de los clientes en un mercado de fabricación aditiva en constante evolución. La característica más obvia al mirar bajo las cubiertas es que la estructura básica de la Lasertec 30 SLM 3rd Gen utiliza piezas de fundición. El mismo material y los mismos principios de diseño que se utilizan en la mayoría de las fresadoras y tornos de DMG MORI. El uso de fundición es una práctica habitual para DMG MORI, pero es nueva en la fabricación aditiva. Es un material que garantiza la mejor rigidez y previsibilidad para la fabricación.
A diferencia de las máquinas-herramienta, en una Lasertec 30 SLM 3rd Gen no existen fuerzas dinámicas derivadas del movimiento de los ejes. Sin embargo, los cambios de temperatura que provocan dilataciones térmicas dentro de la máquina son inevitables. DMG MORI tiene años de experiencia en minimizar el efecto y compensar los cambios de temperatura dentro de sus productos. Se ha tenido mucho cuidado para asegurar que la cámara de proceso sea una unidad aislada dentro de la máquina. Por lo tanto, la cámara de proceso flotante es libre de expandirse en todas las direcciones durante las variaciones de temperatura. Por el contrario, las ópticas están montadas en el bastidor rígido del pórtico de fundición. La distancia en Z entre la óptica y el lecho de polvo se mantiene constante mediante la calibración del recubridor con respecto a una superficie de referencia. Además, el eje Z se compensa activamente para cualquier desplazamiento. Por lo tanto, pueden eliminarse los problemas relacionados con la distancia entre la óptica, la superficie superior del lecho de polvo y los problemas asociados con la capa de recubrimiento.
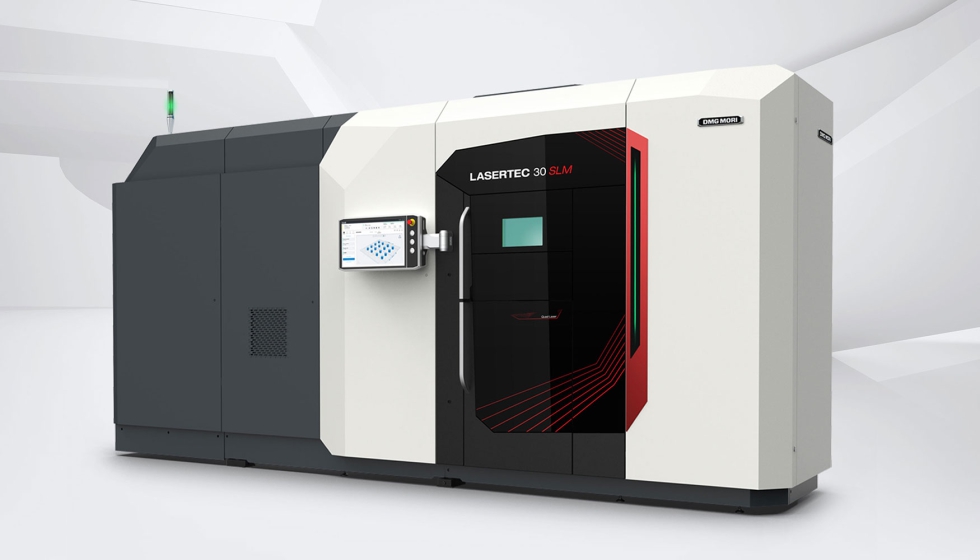
Para reducir el tiempo entre trabajos de construcción y aumentar la flexibilidad, las unidades rePLUG de DMG MORI han supuesto una importante ventaja competitiva respecto a los productos SLM anteriores. El rePLUG es una unidad autónoma de procesamiento automatizado de material en polvo que puede intercambiarse con otras unidades rePLUG. Los clientes existentes con procesos cualificados, que suelen encontrarse en las industrias aeroespacial y médica, aprecian y confían en el sistema rePLUG para garantizar el uso continuo de polvo de máxima calidad. El polvo sobrante de la zona de trabajo se tamiza, almacena y prepara para su reutilización, todo ello bajo una atmósfera de gas inerte dentro de un circuito cerrado. Esto no sólo minimiza la oxidación o la acumulación de humedad, sino que también reduce la posible exposición del operario al polvo. Una importante consideración de seguridad. Para otros clientes, el rePLUG facilita enormemente el cambio entre distintos materiales. Otros componentes relacionados dentro de la propia máquina pueden limpiarse con la misma facilidad, lo que convierte a la Lasertec 30 SLM 3rd Gen en la máquina más rápida del mercado para cambiar entre materiales. Esto amplía enormemente la gama de aplicaciones para las que se puede utilizar una sola máquina.
Por primera vez en una DMG MORI Lasertec SLM, además, es posible cambiar el contenedor de construcción rápidamente. Esto aumenta aún más la eficiencia de la máquina, ya que no es necesario esperar a que se enfríe el trabajo de construcción. Durante el funcionamiento, las cubiertas del depósito de material y de la zona de trabajo se guardan en el interior de la zona de trabajo. Se utilizan para cerrar el contenedor de impresión al retirarlo y para garantizar que se mantiene la atmósfera de gas inerte en el interior de la máquina. El siguiente trabajo de construcción puede iniciarse rápidamente sin una nueva inundación de gas inerte.
Las interrupciones durante la fabricación se minimizan aún más mediante el control por cámara de la superficie del lecho de polvo. Después de cada capa, se escanea la superficie en busca de anomalías antes de que se mueva la recubridora. Si hay un saliente que no se detecta a tiempo, la recubridora bidireccional está equipada con un mecanismo de protección contra colisiones para acortar el tiempo de inactividad posterior. Al entrar en contacto con un saliente que sobresale de la bancada, la recubridora se desacopla inmediatamente del sistema de accionamiento, evitando así daños mayores.
El nuevo diseño del flujo de gas inerte sobre el lecho de polvo garantiza un flujo laminar constante durante el funcionamiento. El flujo de gas secundario por debajo del cristal protector tiene por objeto evitar la acumulación de residuos en el cristal protector. El diseño similar al de un túnel de viento garantiza un rendimiento del flujo de gas sin precedentes. El propio cristal de protección está bajo observación constante mediante un sistema de cámara secundario que avisa si hay algún problema. En la zona del cristal de protección hay iluminación adicional para ayudar al operario a comprobar y limpiar el cristal de protección entre los trabajos de construcción.
DMG MORI pone mucho énfasis en la facilidad de uso y la ergonomía de la máquina. Reducir el contacto del operario con el polvo es una consideración primordial. Otro aspecto clave en el que destaca la Lasertec 30 SLM 3rd Gen es en el entorno operativo CELOS X. CELOS X guía al operario a través de todos los pasos necesarios para poner en marcha un trabajo. Por ejemplo, le pide que limpie el cristal de seguridad y le muestra cómo hacerlo. También guía al operario a través del proceso de rellenado de polvo o cómo deben realizarse las comprobaciones y el mantenimiento diarios. La guía de CELOS X es importante para la adopción de procedimientos operativos seguros y eficaces en el taller.