AsorCAD explica paso a paso el proceso de diseño y fabricación con tecnología 3D de unos guantes especiales para practicar atletismo en silla de ruedas
Diseño y fabricación con tecnología 3D de guantes especiales para atletismo en silla
Jordi Madera, atleta paralímpico internacional y embajador de SportUniverse con más de 17 años en el mundo de la competición, está situado en el Top 10 de los mejores atletas del mundo en las disciplinas de maratón y media maratón. El impresionante palmarés de Jordi cuenta con el récord de España de velocidad en media maratón, 800 y 10.000 metros; es campeón de España de ciclismo en ruta, de paratriatlón y de atletismo en pista en 200, 400, 800, 1.500 y 5.000 m; y cuenta con el primer puesto en competiciones internacionales en Oensinger (Suiza), New Castle (Reino Unido) y Lisboa (Portugal) y tercer puesto en la maratón internacional de Chicago (Estados Unidos).
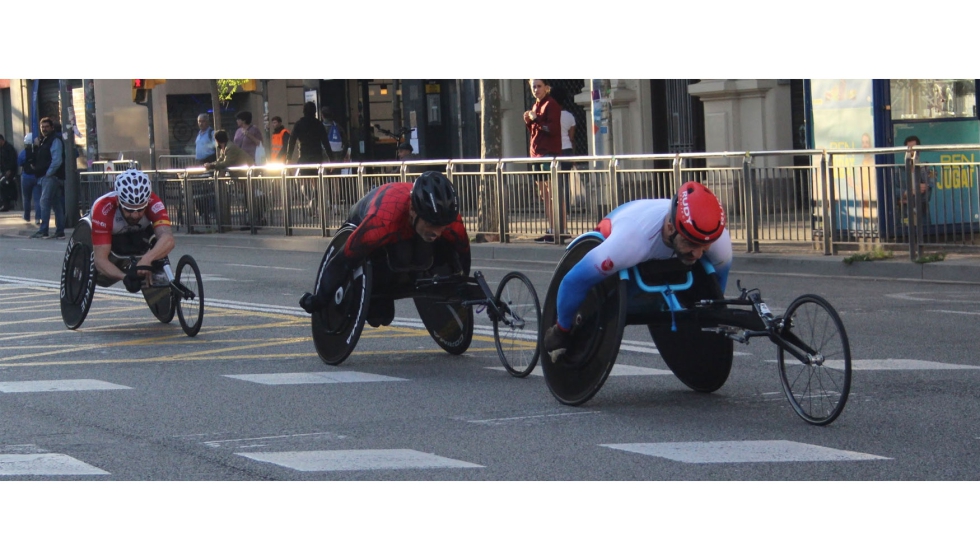
Foto 1: Jordi Madera liderando la Maratón de Barcelona, en mayo de 2022.
Para ello, desde AsorCAD le aconsejaron la tecnología 3D con la que trabajan habitualmente y que puede ser la solución, tanto para obtener el diseño a medida mediante el escaneado 3D de los guantes y conservarlo para siempre, como para la fabricación de nuevos guantes mediante fabricación aditiva, con una impresora 3D.
El primer paso era entender qué tipo de guantes serían los mejores, más allá de comprobar que el diseño fuera el más adecuado desde el punto de vista ergonómico:
- Deben de ser totalmente ajustados a las manos del atleta para evitar molestias o incluso lesiones.
- Que pesen lo menos posible; en alta competición cada gramo cuenta.
- Deben ser resistentes, ya que como informó Jordi, los guantes impactan contra la rueda una media de 60-70 veces por minuto durante la carrera.
- Deben ser impermeables y que aguanten cambios de temperatura sin deformarse.
- Su fabricación debería de ser sencilla, rápida y sin un alto coste, para poder disponer de las unidades necesarias fácilmente y en el menor tiempo posible.
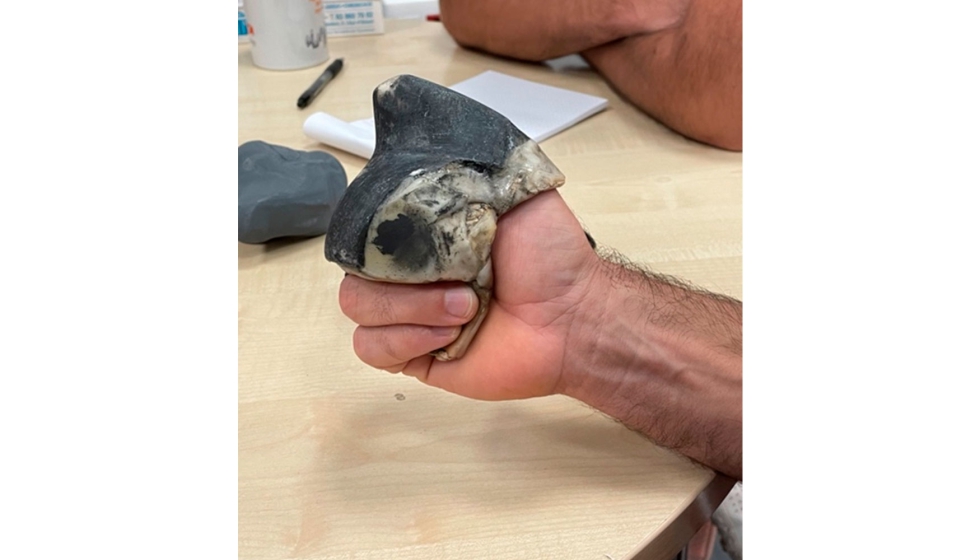
Foto 2: Guante original y postura en mano derecha.
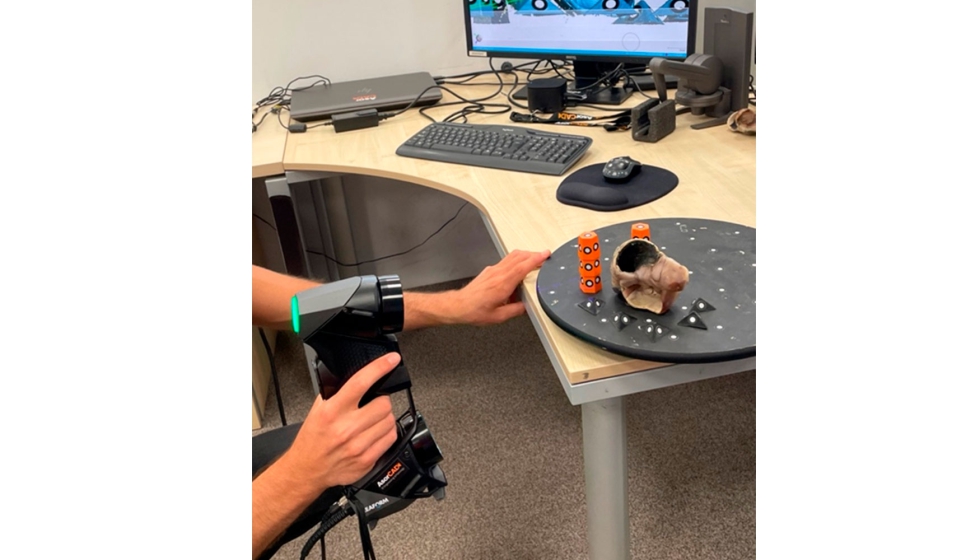
Foto 3: Primer escaneado del guante original.
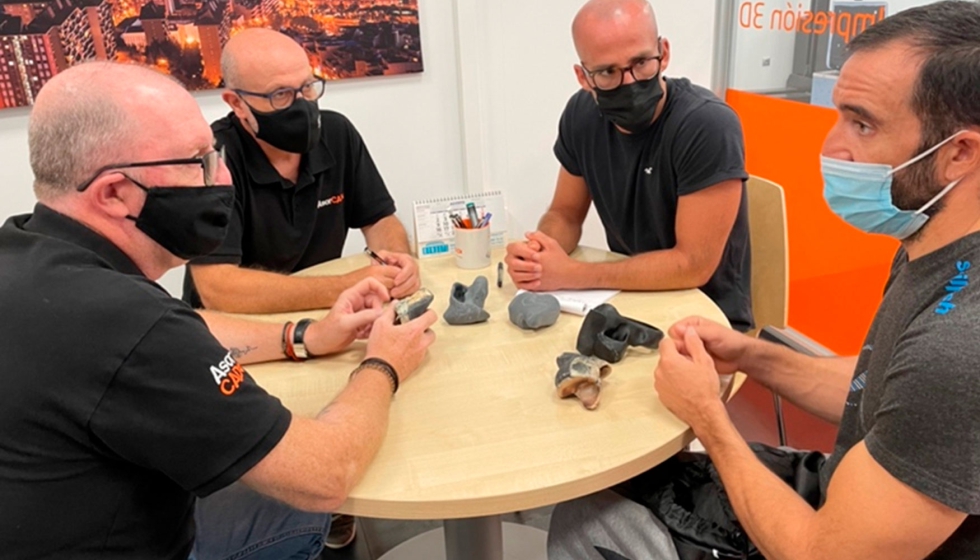
Foto 4: Reunión previa para abordar el proyecto del equipo técnico de AsorCAD con el atleta Jordi Madera.
El segundo paso del proyecto ya se centró en el diseño y la fabricación de los guantes, detallado en estos 10 pasos:
1. Escaneado 3D de los guantes originales fabricados por Jordi, para obtener la geometría y el dibujo en CAD que se usará para diseñar los nuevos guantes. Se usó el escáner 3D óptico de tecnología láser HandySCAN Black Elite, a una resolución de 0,3 mm. El tiempo de escaneado y procesado de imágenes fue de 50 minutos (fotos 5 y 6).
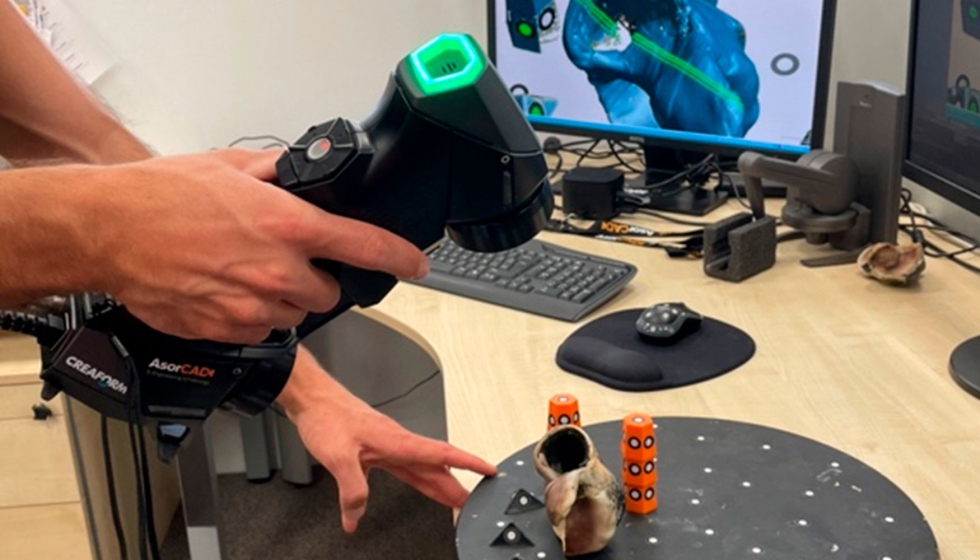
Foto 5: Escaneado 3D del guante original de la mano derecha.
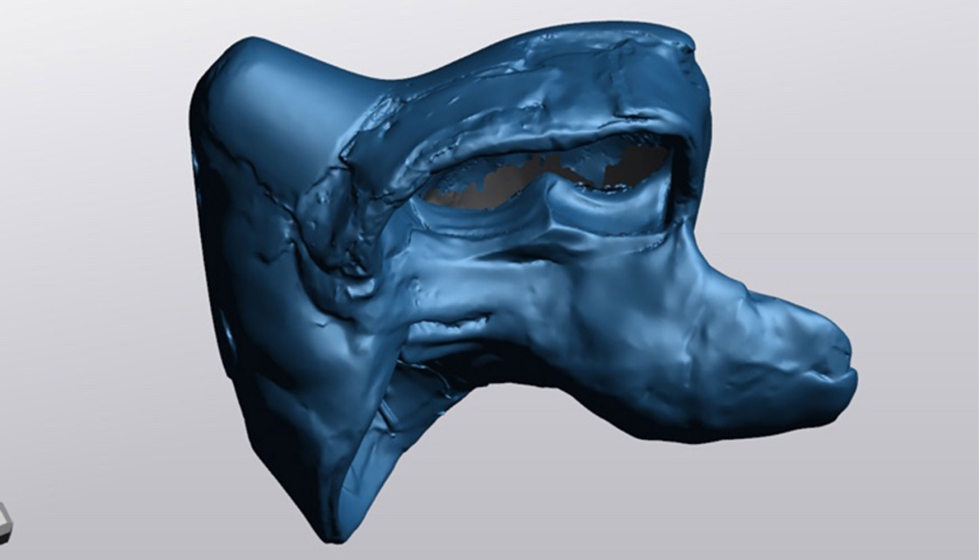
Foto 6: Resultado del escaneado del guante original.
2. Corte en sección de los guantes: se seccionaron los guantes de manera virtual, usando el diseño obtenido del escaneado, para acceder a las zonas interiores del guante que no se podían escanear porque eran inaccesibles desde fuera.
3. Impresión 3D de las secciones de los guantes, para obtener la geometría y una visión interior del guante que no se pudo escanear. Para ello se usó la impresora 3D Makerbot Method X de tecnología FDM a una resolución de 0,2mm y grosor de 0,8mm en material PLA. El tiempo de impresión 3D fue de 12 horas para cada sección.
4. Escaneado 3D del interior de los guantes: Para conseguir el diseño perfecto y adaptado totalmente a las manos de Jordi, se tomó el guante seccionado impreso en 3D y se aplicó plastilina en la parte interior, el atleta se puso los guantes seccionados haciendo presión sobre la plastilina, consiguiendo así una geometría perfecta de las manos dentro del guante en la postura correcta. Esta geometría resultante se escaneó con el escáner 3D de tecnología de luz estructurada GO!Scan Spark a 0,3 mm de precisión. También se escaneó el guante seccionado con la mano del deportista en la plastilina, para tener un control del volumen de los dedos y poder dibujar el resto de la pared interna de los guantes. El tiempo de escaneado y procesado en esta ocasión fue de 40 minutos (fotos 7, 8 y 9).
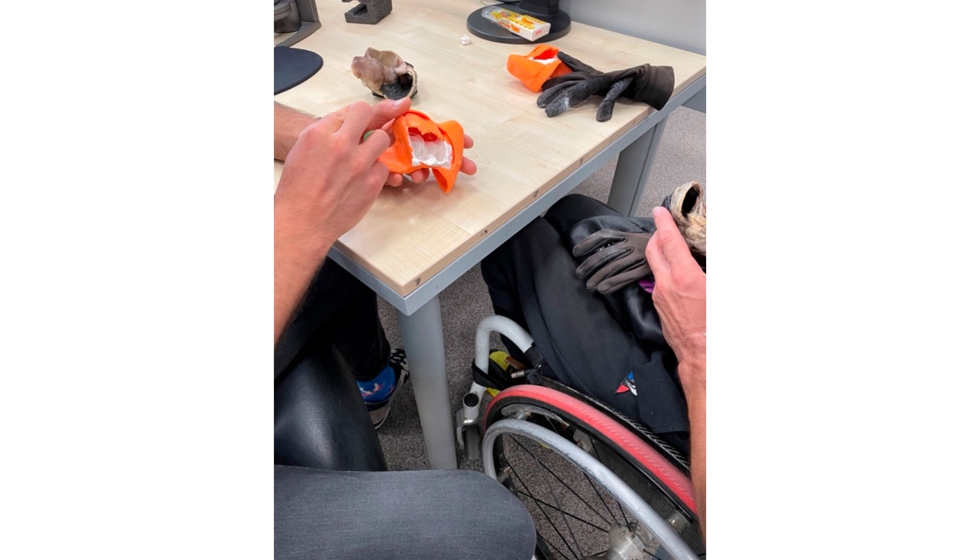
Foto 7: Preparación de interior del guante prototipo.
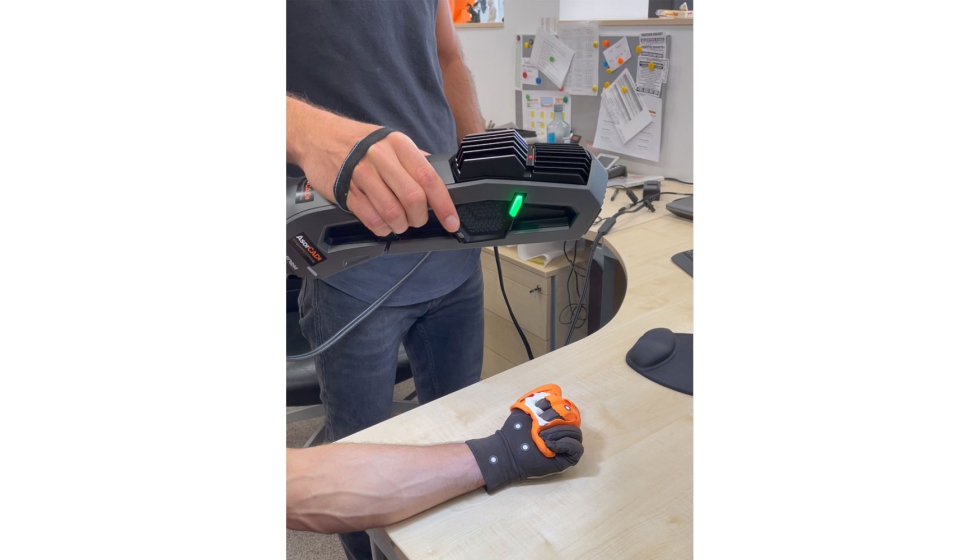
Foto 8: Escaneado 3D de prototipo con postura óptima.
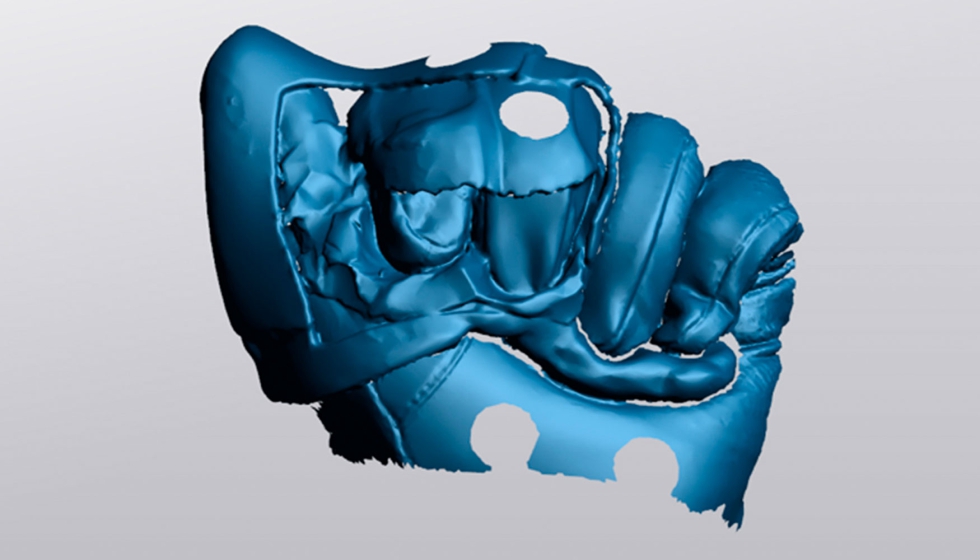
Foto 9: Resultado del escaneado del prototipo con postura óptima.
5. Diseño del primer prototipo: se perfeccionaron las irregularidades y se suavizaron las formas de los dos escaneados, para ello se usó el software de Geomagic Freeform Plus durante unos 40 minutos.
6. Fabricación del primer prototipo: se hizo la fabricación con la impresora 3D Makerbot Method X de tecnología FDM en material PLA Tough a una resolución de 0,2 mm y grosor de 1,2 mm. Para ello fueron necesarias 15 horas por cada guante. El atleta se colocó los guantes y los probó durante un entrenamiento para detectar los puntos que se debían corregir.
7. Diseño del segundo prototipo: Jordi reportó que los guantes le molestaban en la zona distal de los dedos. Se modificaron los puntos concretos donde el deportista sentía molestias y se aprovechó para suavizar el aspecto externo de los guantes. El software utilizado es de nuevo Geomagic Freeform Plus y el tiempo necesario fueron 3 horas.
8. Fabricación del segundo prototipo: se hizo la fabricación con la impresora 3D Makerbot Method X de tecnología FDM en material PLA Tough a una resolución de 0,2 mm y grosor de 1,2 mm. Para ello fueron necesarias 15 horas por cada guante. Jordi volvió a probar los guantes de la nueva versión prototipo 2 y señaló que aún sentía molestias en la zona distal de los dedos índice y corazón de ambas manos. Además, nos pidió la posibilidad de incorporar un sistema de sujeción de los guantes a las manos mediante cintas, para darle más estabilidad durante las carreras. Se aprovechó el reajuste del diseño del prototipo 3 para incorporarlo (fotos 10 y 11).
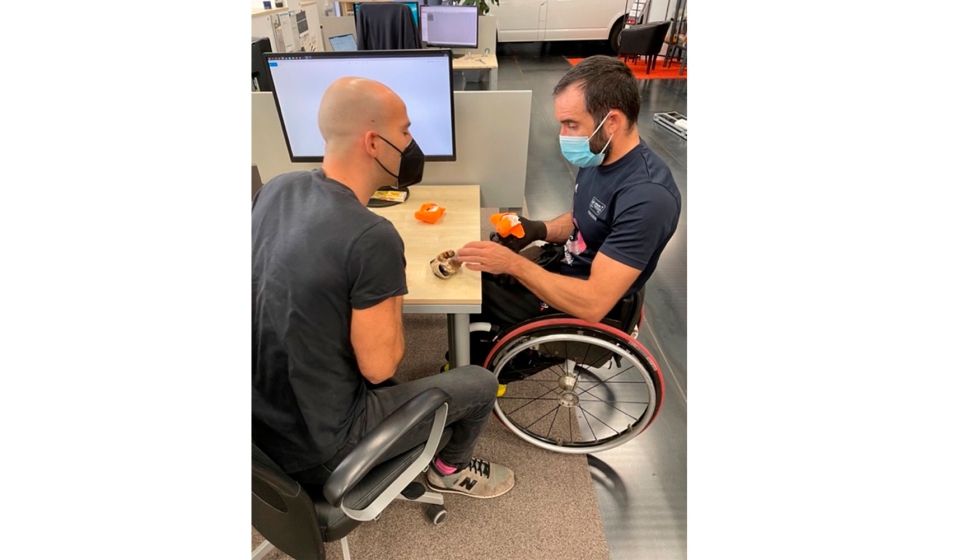
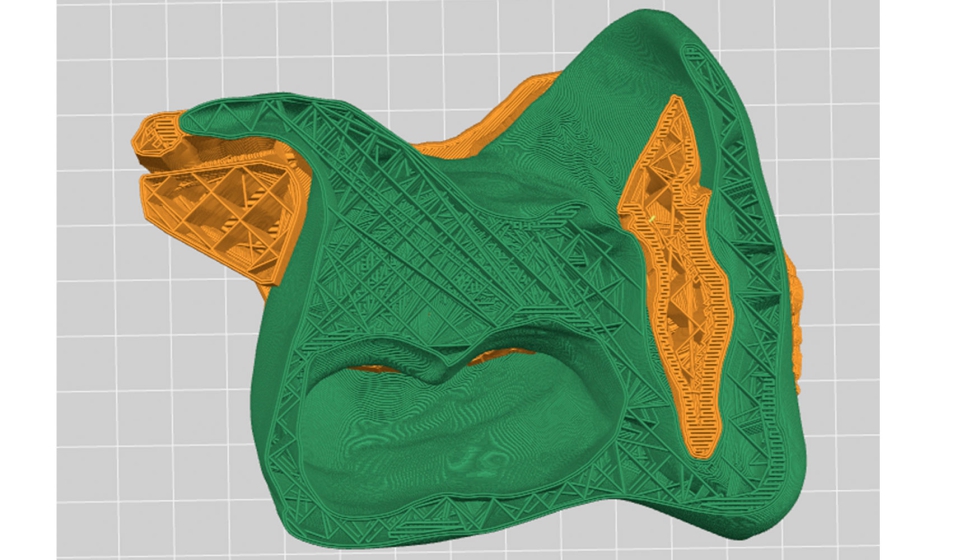
9. Diseño del tercer prototipo: se ajustaron las geometrías en las zonas distales de los dedos índice y corazón de ambos guantes y se incorporaron en el diseño los anclajes para el sistema de sujeción de los guantes a las manos, mediante cintas. El software utilizado fue nuevamente Geomagic Freeform Plus y el tiempo necesario fueron 3 horas.
10. Fabricación del tercer prototipo: se cambió la posición de la impresión primando la alineación de las capas en la zona donde el guante impacta con la rueda, haciéndolo así más resistente, a pesar de que esto conllevara un mayor gasto de material y tiempo de fabricación. Se hizo la fabricación con la impresora 3D Makerbot Method X de tecnología FDM, en material PLA Tough a una resolución de 0,2 mm y grosor de 2 mm. Para ello fueron necesarias 21 horas por cada guante.
Diseño definitivo de los guantes
Fabricación definitiva de los guantes
Se hizo un estudio de los refuerzos necesarios en la estructura interna (o mallado) de las piezas, para evitar la rotura prematura de los guantes y finalmente se decidió utilizar la impresora sPro230 de 3dSystems de tecnología SLS con una resolución de 100-120 µm y precisión de 0,2 mm. El tiempo necesario para la fabricación de cada guante fue de 21 horas.
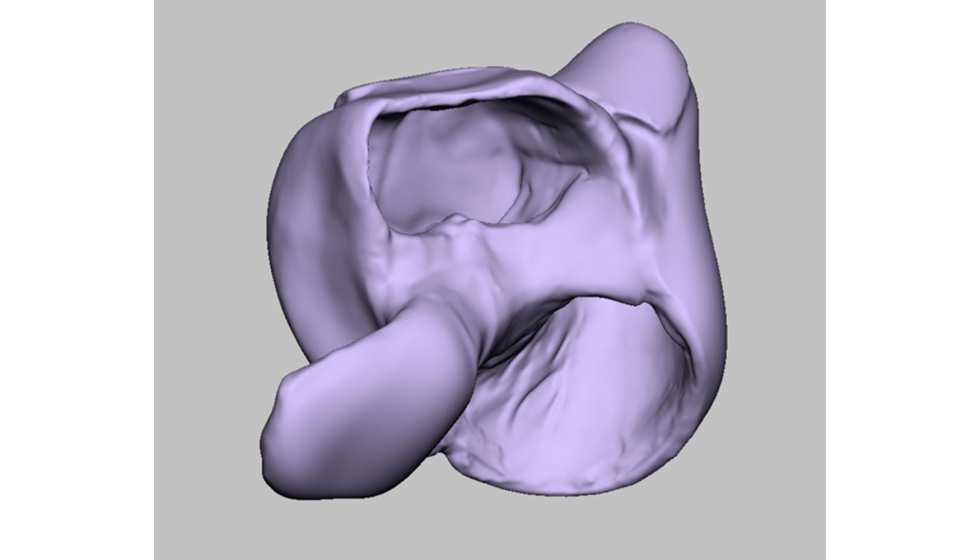
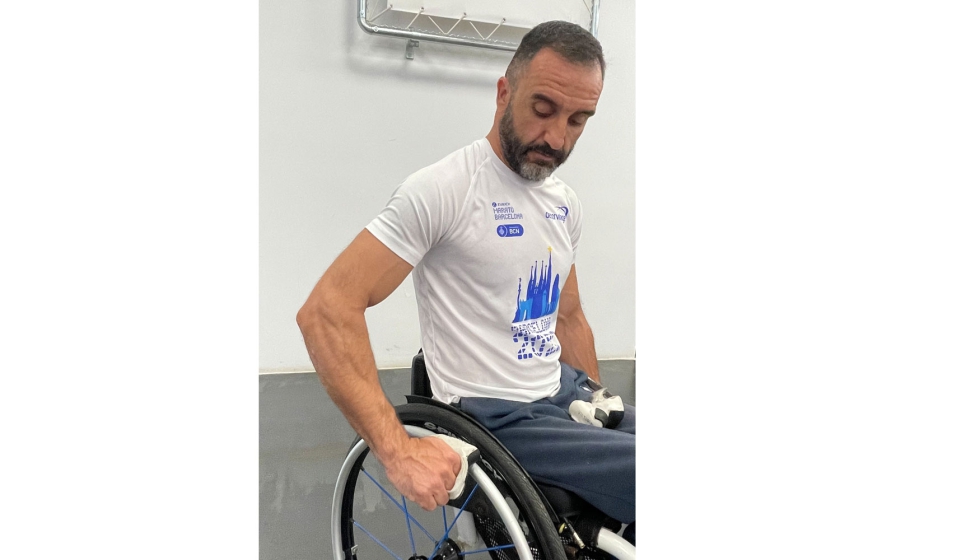
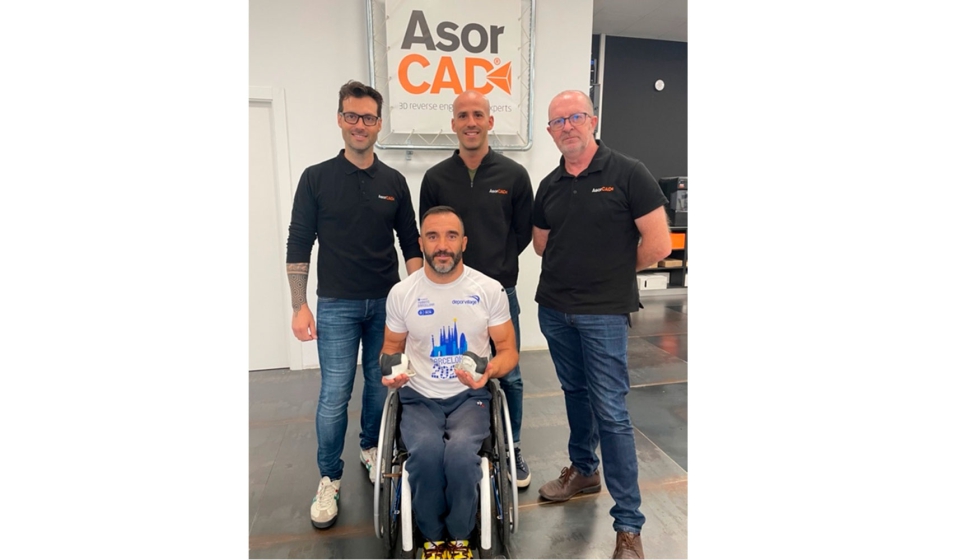
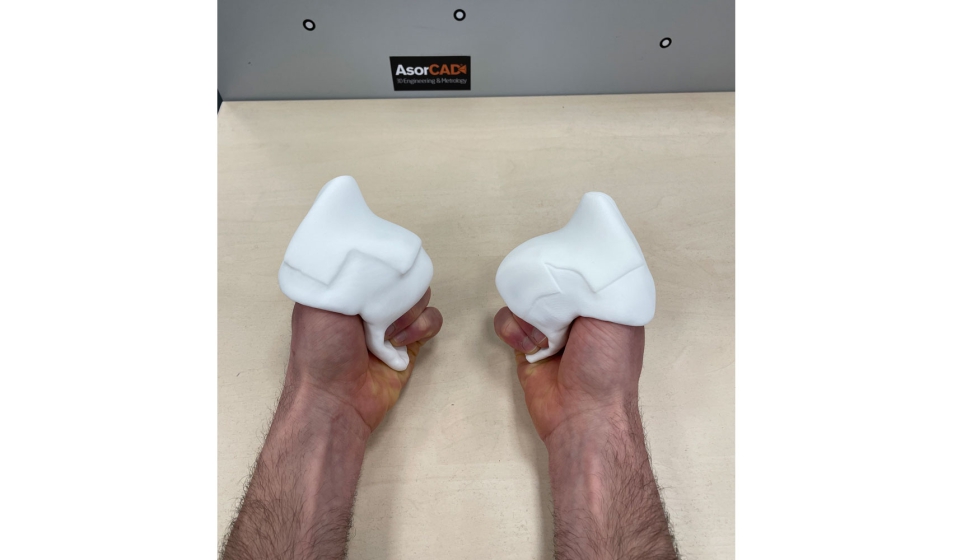