Electroforesis como alternativa a los tratamientos convencionales
Rosalina Pérez, Jorge Rodríguez y M. Belén García, de Cidetec
09/07/2021La electroforesis o Deposición Electroforética (EPD por sus siglas en inglés, Electrophoretic Deposition), es un proceso coloidal cuya ventaja principal radica en su capacidad de depositar recubrimientos en muy poco tiempo, sin necesidad de equipamiento costoso y a precio competitivo. El principio básico de la EPD se basa en que las partículas dispersas o suspendidas en un medio líquido son atraídas por el sustrato conductor de carga opuesta, al aplicar un campo eléctrico, para formar así el depósito electroforético o recubrimiento.
Algunas otras ventajas destacables de esta tecnología son:
- Control fácil del espesor del recubrimiento simplemente ajustando el voltaje y el tiempo aplicado.
- Máxima utilización del material, generalmente es posible conseguir un aprovechamiento del material en torno al 95 - 98%.
- Alta eficiencia en transferencia, es decir, es posible recubrir componentes de geometría compleja, incluyendo orificios, espacios limitados, etc.
- Uniformidad del recubrimiento en toda la pieza, independientemente de su geometría.
- Posibilidad de automatización y gran capacidad de producción.
Las pinturas por electrodeposición son mezclas compuestas por agentes formadores de película, disolventes, aditivos y pigmentos. Estas pinturas se presentan como una dispersión acuosa estabilizada mediante cargas positivas o negativas, dando lugar a la electrodeposición catódica (cataforesis) o la electrodeposición anódica (anaforesis), respectivamente (ver figura 1).
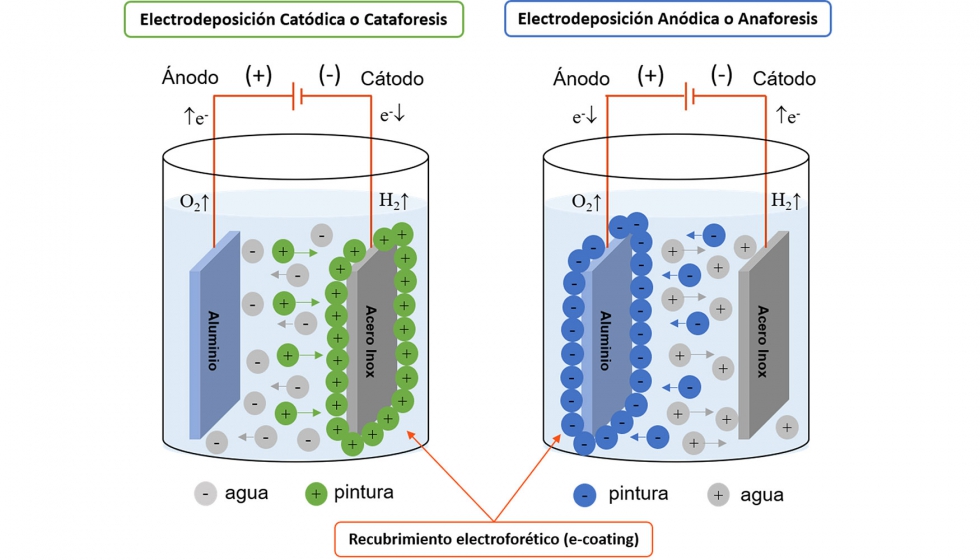
Los recubrimientos electroforéticos de pintura son también llamados: E-coating, electropainting y/o Electrocoat y se aplican industrialmente desde 1960 (ver figura 2). Es un proceso muy utilizado como primera capa de pintura (imprimación) para la protección contra la corrosión de la carrocería y otros componentes del automóvil, entre otras aplicaciones.
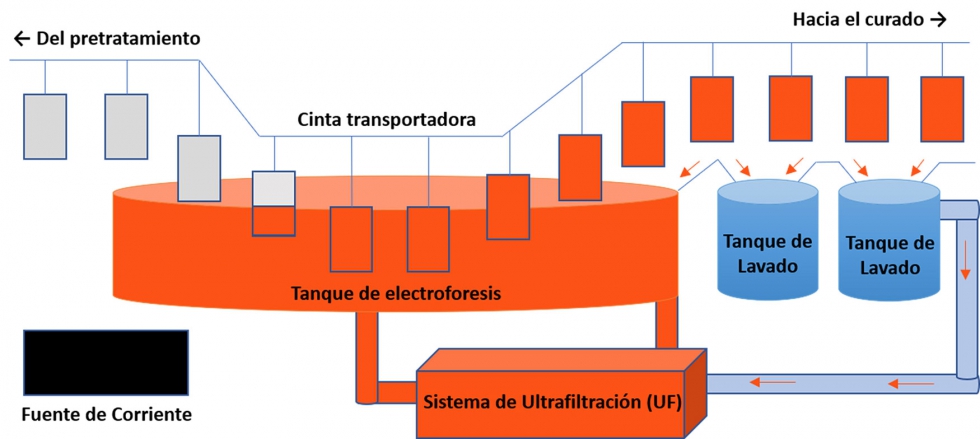
Debido a las propiedades anticorrosivas que proporciona la cataforesis, se ha impuesto a nivel mundial, contando con una gran cantidad de instalaciones cataforéticas industriales. Una de sus principales ventajas frente a la anaforesis es su mayor versatilidad, ya que permite recubrir un mayor número de materiales de manera óptima. Además, la difusión del hidrógeno durante la formación del recubrimiento aumenta la fuerza dieléctrica y ayuda al control del espesor de la capa. No obstante, su desventaja principal es precisamente esta generación de hidrógeno, cuando ocurre en exceso puede incluso interrumpir la formación del recubrimiento.
La anaforesis, por su parte, se utiliza principalmente con metales y/o aleaciones como el aluminio, magnesio, titanio o zinc, donde la capa de óxido actúa como barrera, proporcionando una mayor protección frente a la corrosión. Durante la anaforesis, la evolución del gas, en este caso oxígeno, es menor y disminuye sustancialmente la interrupción de la formación del recubrimiento. Como desventaja, cabe mencionar que no es apta para recubrir sustratos sensibles a la oxidación. Así, en el caso de los aceros, por ejemplo, no es posible obtener recubrimientos anaforéticos de calidad directamente sobre el sustrato, pero sí es posible depositar recubrimientos anaforéticos óptimos sobre el acero galvanizado.
Durante los últimos años la anaforesis ha llamado la atención de la industria aeronáutica, debido a la creciente necesidad de utilizar materiales ligeros con altas prestaciones obtenidas mediante recubrimientos sostenibles. Actualmente, la mayoría de las piezas aeronáuticas fabricadas en aluminio son resistentes a la corrosión a través de tratamientos basados en Cr (VI). El sistema convencionalmente utilizado por esta industria es el Anodizado Crómico (Chromic Acid Anodizing, CAA, por sus siglas en inglés) acompañado por una imprimación con Cr (VI) y un acabado final (top-coat). No obstante, el Cr (VI) presenta un grave problema relacionado con su demostrada toxicidad, carcinogenicidad y tendencia a bioacumularse. Es por ello que, a día de hoy, existen diferentes normativas y directrices europeas que limitan y regulan su uso y empleo en determinadas aplicaciones. Concretamente, su uso acaba de ser autorizado hasta 2024 y a partir de esa fecha se espera un endurecimiento de las políticas europeas.
Por esta razón, uno de los retos del sector aeronáutico y en general de los sectores en los que se emplean recubrimientos basados en Cr (VI), es la sustitución de este tipo de sistemas convencionales por una alternativa sostenible que posea propiedades similares. En este contexto, Cidetec está activamente trabajando en el desarrollo de recubrimientos anaforéticos, capaces de cumplir con los mismos requerimientos que los actuales basados en Cr (VI). La figura 3 muestra un diagrama esquemático para la protección de aluminio (ejemplo: AA7075) y las alternativas de sustitución del CAA y la imprimación, por medio de la anaforesis: Alternativa 1 -> 3 µm de Anodizado en Sulfúrico (SAA) más 20 µm de anaforesis alcanzado > 3000 h en NSS y Alternativa 2 -> 20 µm de anaforesis alcanzando > 1.000 h en NSS.
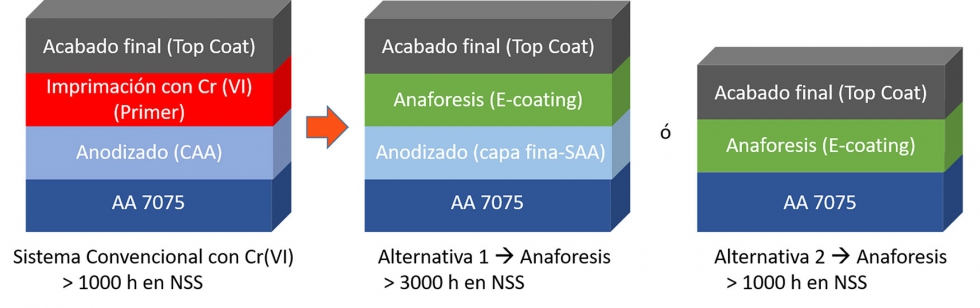
La anaforesis es el único tratamiento orgánico que aplicado directamente sobre el sustrato une las ventajas de ser acuoso (menor generación de COVs) con la ausencia de Cr (VI) (menor toxicidad). Es por ello, que la anaforesis en lugar de la imprimación convencional da lugar a una reducción aproximada del 50% en emisiones (COVs), mientras que, al emplearse como capa final, evita la necesidad de aplicar un acabado final (top-coat), dando lugar a una reducción de prácticamente el 100% de las emisiones (COVs). Además, el uso del tratamiento anaforético lleva a una reducción del consumo energético de un 45 - 50% con respecto al sistema convencional con Cr (VI). En resumen, podemos decir que el sistema anaforético es mucho más sostenible que los tratamientos actuales.
Para desarrollar y escalar el proceso anaforético, Cidetec cuenta con una planta piloto completamente equipada a escala semi-industrial mostrada en la figura 4, la cual cuenta con:
- Línea de pretratamiento completa: Esta línea incluye todas las etapas necesarias para una óptima preparación superficial previo a la anaforesis, como el desengrase, decapado, anodizado y varias cubas de lavado.
- Cuba de anaforesis: Esta cuba está dividida en tres compartimientos; la cuba de deposición anaforética o e-coating, la cuba del rebosadero y la cuba de lavado con permeato.
- Sistema de ultrafiltración (UF): La cuba de anaforesis cuenta con un sistema de ultrafiltración (UF) acoplado, que permite el aprovechamiento del material y el control óptimo del proceso.
- Fuente de corriente y bastidores de titanio versátiles para el tratamiento de diversas piezas de manera individual o simultánea, así como la posibilidad de tratar desde paneles hasta componentes de geometría compleja.
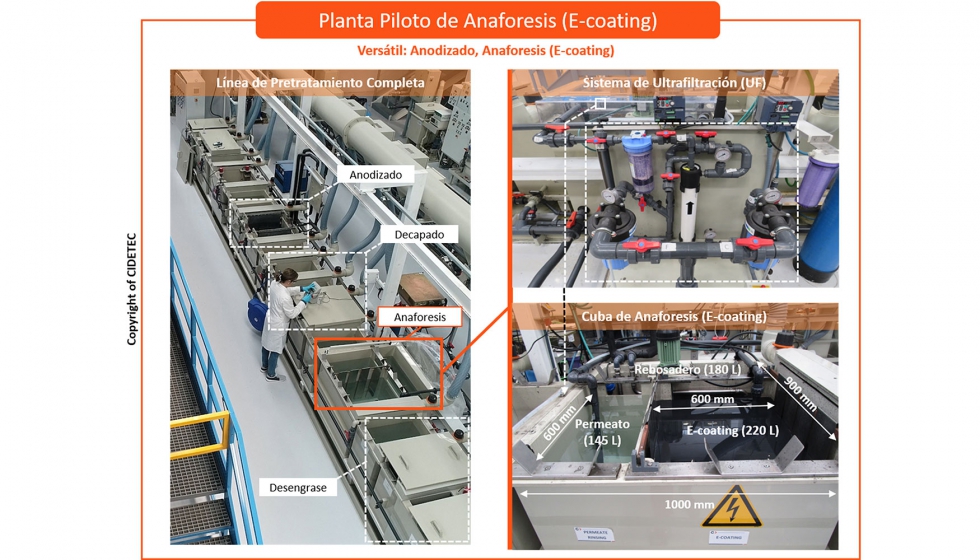
Uno de los proyectos destacables, a nivel europeo, en el que ha participado Cidetec como coordinador en torno a la anaforesis, es el proyecto Ecoland ‘Development of ECO-friendly protection procedures for LANDing gear aluminium alloys’. Clean Sky 2 Joint Undertaking under the European Union's Horizon 2020 research and innovation programme under grant agreement No. 785412 (marzo 2018 – enero 2020).
Los resultados más relevantes de este proyecto fueron publicados en dos artículos de la revista Galvanotechnik. A modo de resumen, se compararon el sistema tradicional con Cr (VI) vs. las alternativas sostenibles de anaforesis (e-coating), y se obtuvieron muy buenos resultados en resistencia a la corrosión (NSS). La anaforesis ha demostrado ser una alternativa competitiva libre de Cr (VI) alcanzando > 3.000 h en NSS, utilizando 3 µm de anodizado en sulfúrico (SAA) previo a 20 µm de anaforesis y > 1.000 h en NSS aplicando 20 µm de recubrimiento anaforético directamente sobre el sustrato (AA2024 y AA7075).
Dentro de este proyecto se realizaron ensayos de validación del sistema anaforético siguiendo los estándares marcados por la industria aeronáutica. En la Tabla 1 se muestran los excelentes resultados para los ensayos de adhesión en seco y húmedo, resistencia al rayado, resistencia al gravillonado, resistencia química y corrosión (NSS).
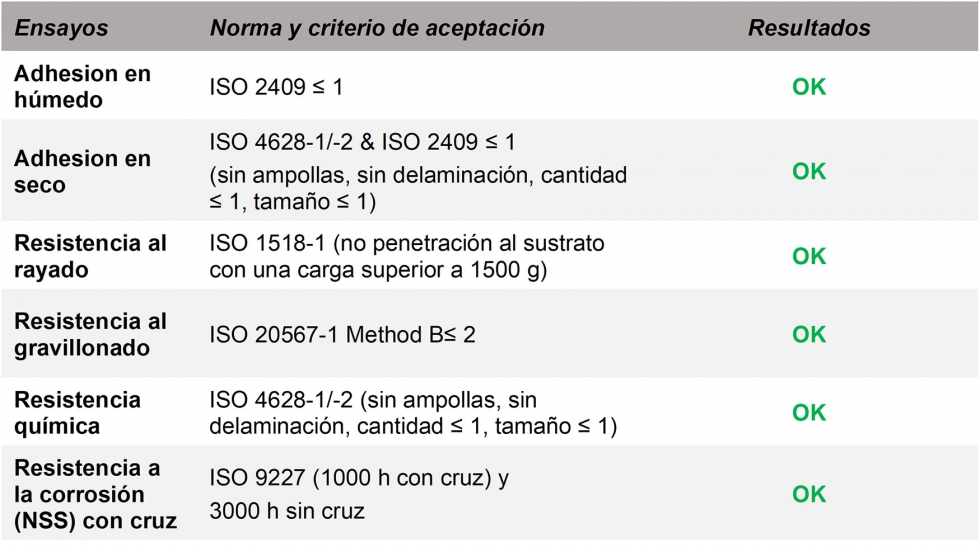
Para demostrar la escalabilidad del proceso, se utilizaron dos prototipos reales de geometría compleja provenientes de los trenes de aterrizaje. En la Tabla 2 se muestra los prototipos evaluados, donde fue posible obtener excelentes resultados en la resistencia a la corrosión (NSS) superando las 1000 h en NSS sin defectos, para ambos prototipos (AA7075).
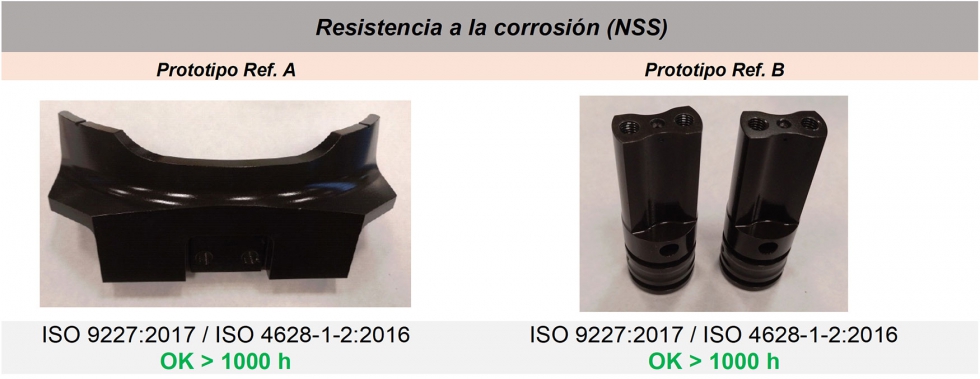
Tabla 2. Resultados obtenidos en corrosión (NSS) para los prototipos de geometría compleja (AA7075).
Durante los últimos años, Cidetec ha apostado por el desarrollo de la anaforesis como proceso alternativo al Cr (VI) para la protección frente a la corrosión de componentes de aluminio utilizados en el sector aeronáutico. Actualmente, Cidetec Surface Engineering investiga activamente en esta línea de desarrollo para aportar nuevas propiedades funcionales al recubrimiento anaforético (autoreparante, mayor resistencia a la corrosión, estética/cambio de color, etc.) y sobre todo para mostrar la versatilidad del proceso para otros materiales y aplicaciones como automoción, ferroviario, construcción, etc.
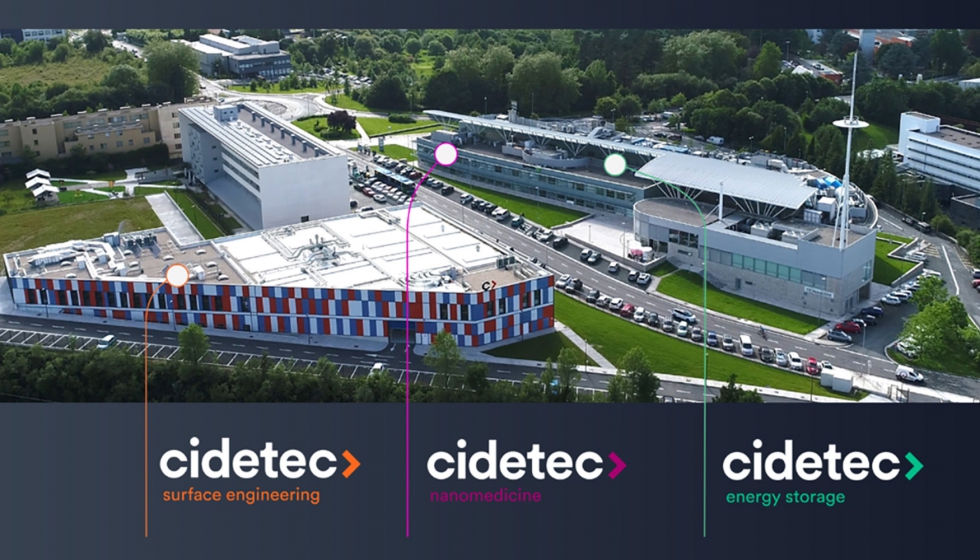