Adaptación del proceso de aplanado por rodillos a las nuevas tendencias
La competitividad y especificaciones requeridas por los consumidores en el mercado durante los últimos años, han impulsado al desarrollo de nuevos materiales y procesos de fabricación que aporten mejoras en lo que se refiere a sostenibilidad medioambiental, seguridad y precio. En este contexto, se ha prestado especial atención a los aceros de alta resistencia (foto 1) por su elevado límite elástico, a nuevas aleaciones de aluminio que ofrecen una mayor resistencia y un peso menor a los aceros, e incluso a materiales ligeros como el magnesio que pese a su baja conformabilidad se está convirtiendo en un material atractivo debido a su baja densidad. El interés por estos materiales ha sido principalmente relevante en la industria automovilística, donde las restricciones medioambientales y económicas impuestas en los últimos años han promovido el desarrollo de automóviles ligeros, lo cual está ligado directamente con la reducción del consumo de combustibles y la reducción de la generación de CO2. El uso de estos materiales supone un nuevo desafío para los fabricantes ya que muestran una conformabilidad limitada, una fuerte influencia del springback y un elevado nivel de tensiones residuales. Además del drástico incremento de las fuerzas necesarias para ser conformados, el desgaste de herramientas, aparición de grietas, etc. La situación ha llevado a los fabricantes a adaptar los procesos de conformado existentes o desarrollar nuevo procesos para estos materiales.
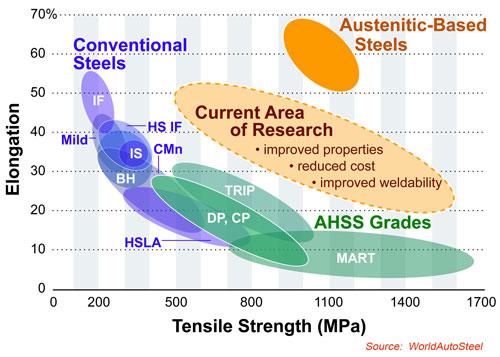
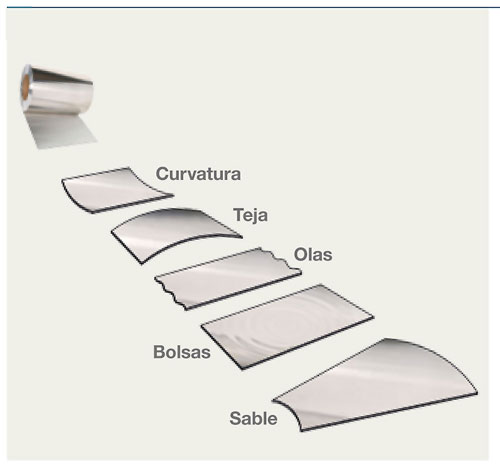
Aplanado por rodillos
Una máquina aplanadora de rodillos está formada por dos líneas de rodillos. La línea superior está diseñada con una basculación que provoca que la deformación inducida por los primeros rodillos sea elevada y que esta vaya decreciendo a medida que se avanza hacia los últimos rodillos. La chapa pasa a través de los rodillos y se dobla alternativamente provocando que las fibras de la superficie estén sometidas a esfuerzos de tracción y compresión.
El proceso de aplanado consiste en una elongación plástica de chapa con el objetivo de unificar las longitudes de todas las fibras longitudinales y transversales, para que las tensiones internas sean minimizadas y homogéneas (foto 3). Existe una controversia acerca de cuáles deben ser los parámetros que definan las condiciones óptimas para las que se considera que una chapa presenta una buena calidad de aplanado. Una chapa aparentemente plana puede contener un elevado nivel de tensiones residuales en su interior que hacen que su calidad no sea óptima para los procesos posteriores de conformado.
Tradicionalmente, en la industria se establece como criterio para obtener una buena calidad de aplanado, que al menos entre un 70-80 % del espesor de la chapa haya plastificado, es decir, que el 70-80% del espesor de la chapa haya alcanzado el límite elástico en algún momento del proceso. Normalmente este máximo de plastificación se alcanza entre el 3º y 4º rodillo y luego se va reduciendo hasta que en la salida la chapa se encuentra totalmente en rango elástico. Sin embargo, hay autores que consideran el nivel de tensiones residuales a la salida o la propia curvatura de la chapa como parámetros más indicativos de la calidad de aplanado.
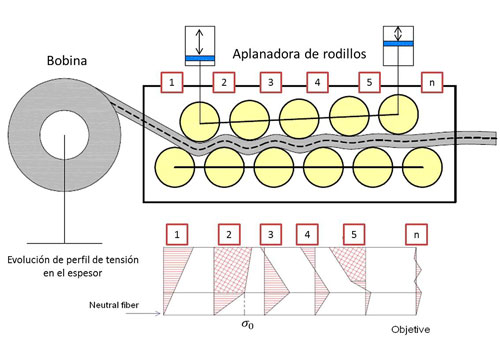
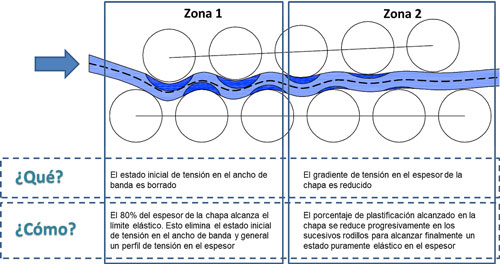
Cómo se aplana
El proceso de aplanado puede dividirse en dos partes, la primera se corresponde con lo que sucede en los primeros rodillos de la aplanadora, y la segunda parte se corresponde con lo que ocurre en el resto de rodillos (foto 4). En la primera parte, la penetración que ejercen los rodillos, y por lo tanto la deformación que sufre la chapa es mayor. En esta sección la chapa desarrolla zonas de deformación plástica que se va incrementando a medida que se dobla entre los rodillos, hasta llegar a un máximo de espesor plastificado, que suele alcanzarse en el 3º y 5º rodillo. La finalidad de esta primera sección de grandes deformaciones es que la mayor parte de las fibras del espesor alcancen el límite elástico y por lo tanto queden plastificadas, mientras que la zona central, cercana a la fibra neutra, permanecen en región elástica. De esta forma, se consigue suprimir el gradiente de tensión en el ancho de la chapa. Sin embargo, debido a los fuertes doblados en esta zona, un perfil de tensiones se genera en el espesor de la chapa. Por eso, después de la primera parte, la penetración ejercida sobre la chapa va disminuyendo hasta que en la salida, los rodillos apenas la deforman. La finalidad de la segunda parte es la de eliminar gradualmente la curvatura de la chapa y reducir el gradiente de tensiones generado en la primera sección a lo largo del espesor, para obtener a la salida una chapa en la que el espesor se encuentre en rango elástico y con un reducido y homogéneo perfil de tensiones residuales.
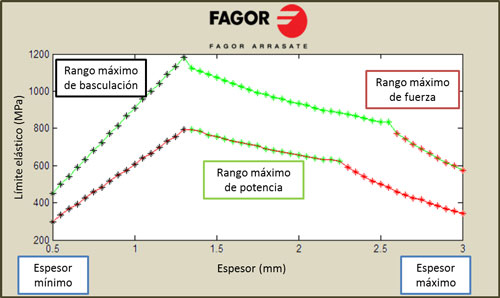
Variables de proceso y limitaciones de la máquina
Hay diferentes factores involucrados en el proceso de aplanado, y de ellos depende el resultado final del aplanado de la chapa. Por ello Fagor Arrasate en colaboración con la Universidad de Mondragón está desarrollando herramientas de cálculo de gran precisión adaptadas a las nuevas tendencias en materiales que permiten analizar cómo influyen las variables del proceso en la calidad de aplanado y así poder optimizar el diseño de máquina sin necesidad de realizar un gran número de ensayos experimentales.
Los principales factores implicados en el proceso son:
- Diámetro de los rodillos.
- La distancia entre rodillos.
- El número de rodillos.
- El tipo de material.
- El espesor de la chapa.
- La curvatura inicial que tiene la chapa.
Una aplanadora no es capaz de procesar cualquier tipo de material. Cada máquina presenta una configuración específica que le permite procesar materiales que se encuentran dentro de un rango de espesores y resistencia determinado. En particular, cada máquina tendrá una serie de características que la definen:
- Máxima penetración que pueden realizar los rodillos superiores.
- Fuerza total máxima que es capaz de soportar su estructura.
- Fuerza máxima que es capaz de soportar un rodillo.
- Potencia total máxima proporcionada por el motor.
- Par máximo por rodillo.
Todas estas variables definen la curva de capacidad de una máquina aplanadora (foto 5). Mediante estas curvas quedan reflejadas todas las combinaciones de espesor y límite elástico de una chapa que pueden ser procesadas por una máquina específica sin superar el rango de trabajo (región bajo la curva).Un rendimiento óptimo de la máquina aplanadora que se diseñe teniendo en cuenta todos estos factores, debe asegurar:
- Alcanzar un porcentaje de plastificación en el espesor suficiente para eliminar los defectos (generalmente estimado en 80%).
- Las tensiones residuales a la salida deben ser mínimas.
- No se debe exceder la fuerza máxima ni par admisible por la máquina.
Estudio del comportamiento de materiales
Según la teoría de plasticidad, debido a los cambios microestructurales durante los procesos de cargas cíclicas a las que se ve sometido la chapa durante el proceso de aplanado, las propiedades físicas y la respuesta de tensión en el material se van modificando en el transcurso del proceso. En particular, los materiales pueden sufrir un endurecimiento o ablandamiento cíclico. La intensidad con la que el material endurece o ablanda en cada ciclo se reduce a medida que aumenta el número de ciclos hasta alcanzar un valor de saturación. Dada esta situación, en la que la chapa modifica su comportamiento en cada rodillo por estar variando su curva de histéresis, resulta interesante profundizar en el estudio del comportamiento de material cuando se ve sometido a este tipo de cargas. Por ello, Fagor Arrasate, en colaboración con la Universidad de Mondragón, ha realizado la caracterización de una amplia gama de materiales cuando estos son sometidos a cargas cíclicas de tracción y compresión con el objetivo de modelizar su comportamiento. Los materiales caracterizados han sido minuciosamente seleccionados con el objetivo de cubrir toda la demanda del mercado actual. En concreto, entre los materiales que han sido estudiados se encuentran aceros dulces, aceros de alta resistencia, aceros inoxidables, aleaciones de aluminio y magnesio. Para la caracterización de los materiales se han llevado a cabo ensayos de cargas cíclicas. Para ello se han diseñado distintos utillajes para llevar a cabo los ensayos experimentales con el objetivo de obtener el comportamiento del material sometido a cargas cíclicas de tracción y compresión (foto 6). Las curvas cíclicas de tracción-compresión obtenidas durante los ensayos para los distintos materiales caracterizados han revelado la diferencia de comportamiento entre las familias de materiales. Por lo general, a medida que aumenta el límite elástico de los materiales, el endurecimiento cíclico del material disminuye y el conocido Efecto Bauschinger aumenta. Este fenómeno consiste en el hecho de que al deformar un metal en una dirección hasta que se ha sobrepasado su límite de elasticidad, y deformándolo después en la dirección contraria, su límite de proporcionalidad en esta última dirección es menor. En la foto 6 se observa el resultado de algunas curvas obtenidas para diferentes aceros colocados en orden creciente de límite elástico (foto 7). Estas curvas han sido usadas para la determinación de un modelo de material que sea capaz de predecir cómo se comportan estos materiales cuando son sometidos a cargas cíclicas. El resultado de la modelización ha demostrado que los materiales de alto límite elástico tienden a comportarse hacia un modelo más cinemático, mientras que los materiales de bajo límite elástico suelen comportarse según dictan los modelos isotrópicos. Por este motivo en este estudio se ha optado por el uso de modelos mixtos de endurecimiento isotrópico y cinemático que comparten las propiedades de los dos modelos para predecir el comportamiento de los materiales.
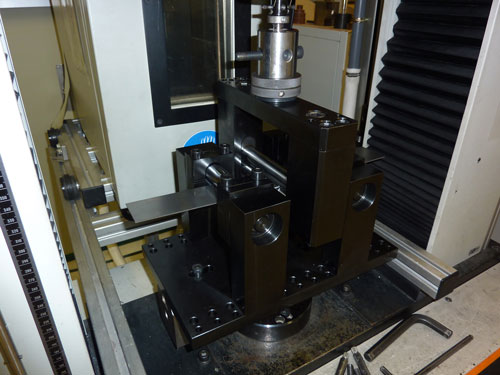

Estrategía para la definición del proceso óptimo de aplanado
La definición de los procesos de fabricación va normalmente acompañados por procesos de optimización, que en muchos casos están basados en métodos de prueba y error. Esos métodos tienen algunas desventajas como los altos costes requeridos y la incertidumbre del resultado final. Con el objetivo de reducir estos costes y afianzar el resultado, en los últimos años se han desarrollado herramientas computacionales capaces de considerar la influencia de las variables del proceso en la calidad final de los componentes y por lo tanto, que ayuden a la optimización del proceso y de las instalaciones. En Fagor Arrasate, se ha hecho una firme apuesta por estas herramientas de cálculo avanzadas con el objetivo de optimizar el proceso aplanado. Estas herramientas resultan de gran interés ya que las máquinas aplanadoras convencionales se encuentran en un momento de adaptación y mejora. La tendencia a usar materiales cada vez con mayores límites elástico y/o bajos módulos de Young ha obligado a profundizar en estudio de las aplanadoras para así asegurar su correcto funcionamiento ante estos materiales avanzados.
El uso de estos materiales implica los siguientes desafíos:
- Las chapas requieren mayores penetraciones de los rodillos, por lo que la aplanadora debe ser capaz de bascular lo suficiente y tener una configuración de rodillos óptima para alcanzar el nivel de plastificación requerido.
- La fuerza total que la estructura debe soportar es mucho mayor, por lo que se requiere de una máquina robusta y resistente
- El par y potencia requerida para procesar estos materiales también aumenta, por lo que se necesitan motores más potentes y componentes más resistentes.
A la vista de los cambios que supone el aplanado de estos materiales, el proceso ha sido estudiado mediante modelos de simulación avanzada, con el fin tener un control total del proceso de aplanado. Para ello se ha seguido la siguiente estrategia de estudio:
- Desarrollo de un modelo de elementos finitos que nos permite simular con exactitud y precisión el proceso de aplanado y todas sus variables. El programa ha sido desarrollado mediante el software de elementos finitos MSC Marc (foto 8) con un modelo de endurecimiento mixto del material para predecir de forma más correcta el comportamiento real de la chapa. Se han simulado diferentes materiales, de diferentes espesores y con distintas configuraciones de máquina con el objetivo de analizar las variables de influencia. El mayor inconveniente de este modelo es largo tiempo computacional requerido (foto 8).
- Desarrollo de un modelo semi-analítico basado en fórmulas analíticas que usan la información obtenida del modelo de elementos finitos. Los modelos analíticos son por lo general menos precisos que los modelos de elementos finitos ya que estos deben realizar algunas suposiciones para realizar una resolución rápida del problema. Sin embargo, mediante la combinación de un modelo analítico con los resultados obtenidos en las simulaciones de elementos finitos, se ha desarrollado un modelo capaz de obtener datos fiables y precisos, con la ventaja añadida de obtener los resultados prácticamente de forma instantánea.
- Validación de los modelos en un prototipo experimental. Dicho prototipo consiste en una aplanadora de tamaño reducido de 13 rodillos de diámetro 45 mm. El prototipo ha sido sensorizado para poder contrastar la información de los modelos presentados anteriormente con los valores obtenidos en los ensayos experimentales. En particular se han instalado:
- Sensores de par en los rodillos.
- Células de carga para medir la fuerza soportada por la estructura.
- Dispositivos de medición del consumo del motor.
- Chapas sensorizadas con galgas extensiométricas para medir la deformación que sufre durante el proceso (foto 9).
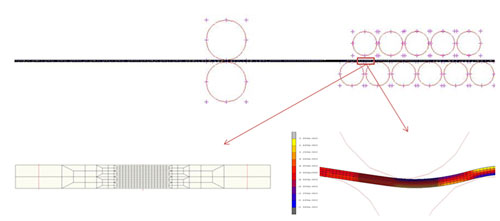
Herramienta software optimizada de Fagor para el diseño óptimo de máquina y proceso
El modelo analítico ha sido implementado en un software personalizado, con una interface fácil e intuitiva que permite calcular las distintas variables del proceso para una configuración de aplanadora determinada de forma prácticamente instantánea. Gracias a la rápida respuesta del programa, la herramienta ha resultado ser muy útil y eficaz ya que permite iterar entre las distintas opciones que ofrece el programa de forma rápida con el fin de encontrar la configuración más óptima. El modelo empleado en el desarrollo de esta herramienta de cálculo contempla la caracterización y modelizado del comportamiento de materiales hecho previamente. De este modo, el programa presenta la opción de introducir los datos del material que va a ser procesado mediante el acceso a una base de datos en la que se encuentra toda la información de los materiales caracterizados o mediante la introducción manual de los datos de un material determinado.
En el programa cuenta con las siguientes funcionalidades:
- Análisis de un caso particular: el usuario debe introducir en la interface la configuración de aplanadora con la que va a trabajar (nº rodillos, diámetros, distancia entre rodillos, etc.), las propiedades del materiales a tratar (espesor, ancho de banda, límite elástico, etc.) y por último las condiciones de trabajo (velocidad de la línea, % de plastificación alcanzado, etc.). El programa propone cual deben ser la colocación adecuada de los rodillos para obtener el nivel de plastificación deseado (presettings). Además permite calcular distintas variables como: el % plastificación, deformaciones, fuerza, par y potencia (foto 10).
- Curvas de capacidad: El software permite calcular curvas de capacidad, en las que el usuario deberá introducir los límites de una aplanadora particular (potencia máxima, fuerza total máxima, par máximo por rodillo, etc.). Con esta información, el programa devolverá un gráfico en el que quedan delimitados los materiales (en términos de espesor y límite elástico) que pueden ser procesados con esa aplanadora (foto 11).
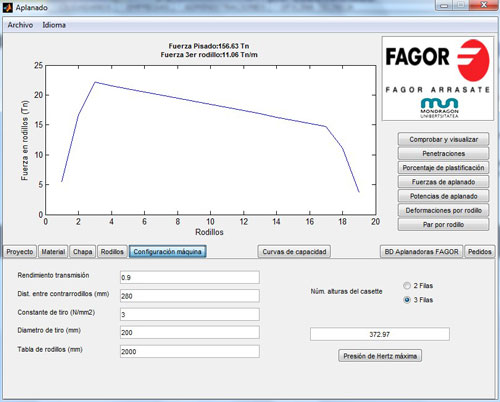
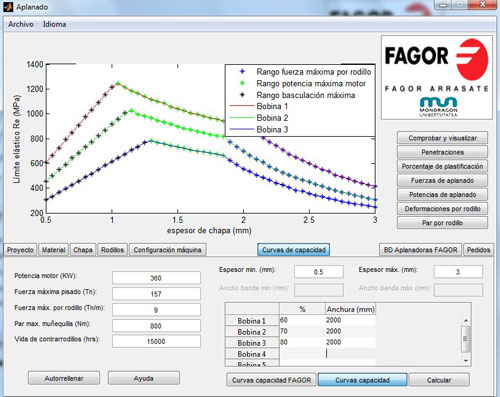