Nihonseiki Company utiliza la tecnología láser de GE Additive para reimaginar su negocio y el sector de la fundición a presión
La fabricación aditiva ayuda a transformar un fabricante centenario del sector de la automoción
Nihonseiki Co Limited, que forma parte del Grupo GMC Holdings, es un fabricante de moldes de fundición a presión muy consolidado, con 100 años de historia en el diseño, la fabricación y el mantenimiento de moldes de fundición a presión para más de 1.000 clientes, principalmente fabricantes de automóviles japoneses e internacionales, y otros fabricantes de moldes y troqueles. En la actualidad, el Grupo GMC Holdings es el mayor fabricante de moldes de Japón y goza de una excelente reputación en todo el mundo como líder del sector y comprometido con la innovación.
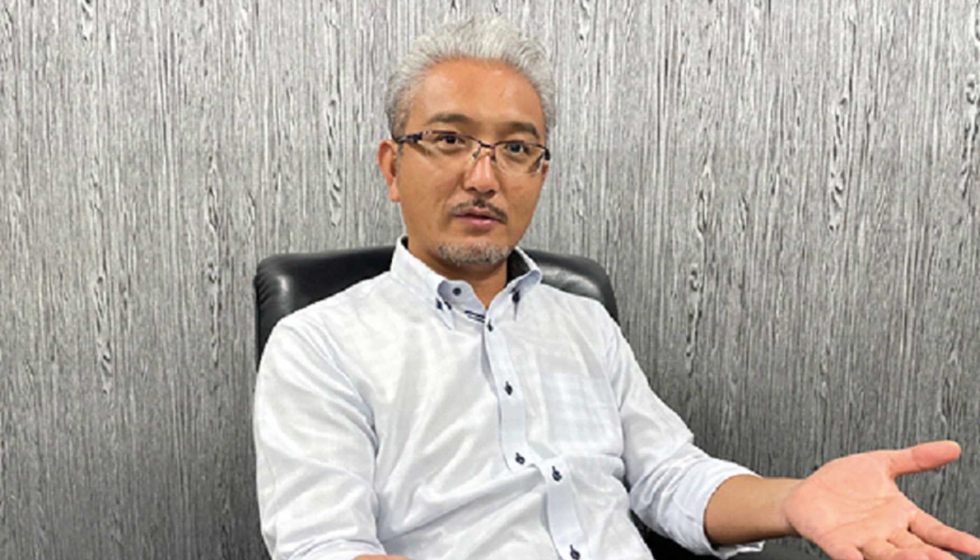
“Nuestra andadura en la fabricación aditiva comenzó en 2015, cuando un fabricante de automóviles se puso en contacto con nosotros para fabricar núcleos (un componente del ensamblaje de troqueles) con canales de refrigeración”, explica Masato Matsubara, director general de Nihonseiki.
“Al principio, empezamos encargándonos de los procesos de posprocesamiento, como el mecanizado, el pulido y el tratamiento térmico de las matrices que otra empresa había fabricado de forma aditiva, utilizando una impresora 3D de metal. Luego, a medida que adquirimos más experiencia y conocimientos, llegamos a la fase en la que podíamos desarrollar nuestros propios diseños de canales de refrigeración”. En 2017, con el fin de trasladar la fundición a la empresa, realizamos un estudio de mercado para evaluar el potencial del uso de impresoras 3D de metal, pero en ese momento todavía había poca demanda de los clientes, por lo que decidimos seguir subcontratando el proceso de fundición", añade Matsubara.
“Entonces, había pocas opciones entre los materiales metálicos que podían utilizarse en las impresoras 3D de metal. En lugar del acero martensítico que se suele utilizar, queríamos probar con el SKD61 (Steel Kogu Dice), que es la aleación de acero para herramientas más utilizada en la fabricación de matrices, pero este material era difícil de conseguir y esta es una de las razones por las que dejamos pasar la idea”, reflexiona Matsubara.
El SKD61 es más resistente y tiene mejor conductividad térmica que el acero martensítico, por lo que su uso en los diseños puede permitir la producción de componentes de herramientas mucho más finos que no se rompen con tanta facilidad, y que pueden prolongar la vida útil dentro del conjunto de la matriz.
A principios de 2021, Nihonseiki recibió una propuesta de Mitsubishi Corporation Technos, el socio de ventas autorizado de GE Additive en Japón, para un material equivalente al SKD61 que puede utilizarse en sus impresoras 3D de metal.
Tras estudiar de nuevo la demanda del sector y de los clientes, Nihonseiki decidió adquirir dos sistemas Concept Laser M2 de GE Additive, capaces de ofrecer una mayor precisión, geometrías más detalladas y formación de superficies lisas.
A lo largo de 2021, Nihonseiki ha creado un sistema de apoyo total que va desde el diseño de la impresión metálica en 3D; la fabricación hasta el mantenimiento. Hasta la fecha, la empresa ha propuesto, fabricado y entregado soluciones que mejoran la refrigeración interior de las matrices con núcleos que utilizan acero martensítico para muchos clientes, pero ahora está planeando un cambio total al material equivalente al SKD61.
La aceleración de la adopción de vehículos eléctricos impulsa la adopción de la tecnología aditiva en la industria del automóvil
A medida que se acelera el cambio a los vehículos eléctricos en todo el mundo, se espera que crezca aún más la demanda de productos más ligeros que utilicen piezas de aluminio. Este cambio, del que se dice que es una enorme revolución que se produce una vez en el siglo, también está trayendo consigo nuevos retos y nuevas oportunidades de negocio para Nihonseiki.
Minimizar el peso es uno de los problemas más acuciantes a los que se enfrentan los fabricantes de automóviles, y en el caso de los vehículos eléctricos, un vehículo más ligero es también esencial para aumentar la autonomía máxima. Para reducir el peso, los componentes de acero prensado se sustituyen por piezas de aluminio fundido, lo que significa que se espera una mayor y más rápida integración de las piezas de aluminio fundido y un aumento del tamaño de las piezas y de las matrices.
Entre las piezas que se está estudiando sustituir por aluminio, una que interesa especialmente a Nihonseiki es la carcasa de la batería. Las carcasas de las baterías de los vehículos eléctricos son cada vez más ligeras y se fabrican con más frecuencia en aluminio, pero también son cada vez más grandes, lo que supone un mayor riesgo de alabeo durante la fundición.
Matsubara es optimista sobre las posibilidades de la aditiva metálica: “La refrigeración interna de las matrices es la clave para reducir el alabeo en las piezas grandes de aluminio. Actualmente estamos centrando nuestros esfuerzos en la refrigeración interna de las matrices mediante la impresión metálica en 3D. A medida que nos esforzamos por mejorar las piezas individuales y prolongar su vida útil, también estamos tratando de encontrar la mejor manera de incorporar la refrigeración interna en el diseño básico de las matrices. Además, a medida que los productos se vuelvan más complejos, la dificultad de diseñar matrices para la fundición de aluminio aumentará considerablemente. Como los enfoques convencionales tienen dificultades para hacer frente a esta creciente complejidad en el diseño y la fabricación, creo que el uso de un enfoque basado en conceptos totalmente nuevos con la impresión 3D en metal abrirá un camino para superar estos desafíos”.
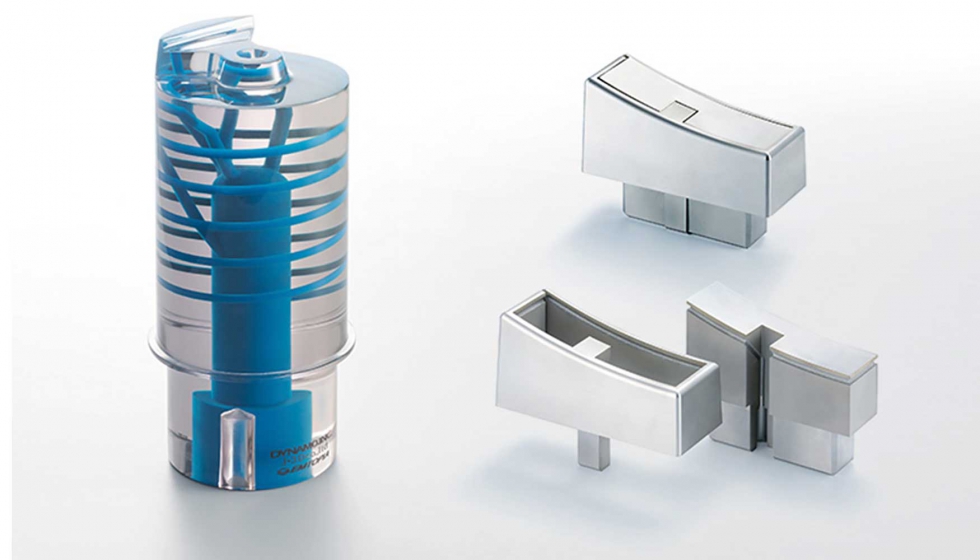
La libertad de diseño de los canales de refrigeración mejora el rendimiento de la refrigeración interna de los componentes de fundición a presión de aluminio
La empresa está utilizando la tecnología de aditiva metálica de GE Additive para resolver los retos de diseño de los canales de refrigeración en la fabricación de piezas de fundición a presión. Nihonseiki puede ahora producir matrices que incorporan canales de refrigeración internos de cualquier forma y crearlos en zonas que de otro modo serían inaccesibles con los procesos de mecanizado convencionales.
El aumento de la eficacia de la refrigeración de las matrices permite que el aluminio inyectado se enfríe no sólo de forma más uniforme, sino también más rápidamente, lo que permite reducir el tiempo total del ciclo y mejorar la calidad. Esto no sólo aumenta la eficacia de la producción, sino que también mejora la calidad de la fundición.
Las matrices de fundición a presión de aluminio se inyectan con una aleación de aluminio líquida calentada a 660 °C. El aluminio se deja enfriar y luego se retira. Para aumentar la eficacia de la producción es necesario reducir el tiempo que se tarda en enfriar tanto la matriz como el aluminio inyectado. Esto se consigue creando canales de refrigeración dentro de la matriz para hacer circular el refrigerante y acelerar el proceso de enfriamiento. Reducir el tiempo de refrigeración de la matriz significa diseñar canales de refrigeración que puedan enfriar toda la matriz de manera uniforme, aunque la fabricación convencional todavía puede crear sólo canales rectos.
Así las cosas, Nihonseiki pretende ofrecer un apoyo integral a sus clientes en áreas como las herramientas de simulación del flujo de refrigerante, en combinación con las libertades de diseño de la fabricación aditiva, que permiten visualizar la transferencia de calor a lo largo del ciclo de fabricación, para demostrar la mejora potencial en la distribución de la refrigeración (calidad) y la tasa de refrigeración (coste) que ofrecen estas soluciones.
En el futuro, la empresa espera situarse a la vanguardia de la fabricación utilizando todas las tecnologías acumuladas hasta la fecha, como el análisis de las condiciones de fundición con simulación de flujos y el cálculo de propiedades mecánicas. También está apoyando el desarrollo de nuevos métodos de fabricación.
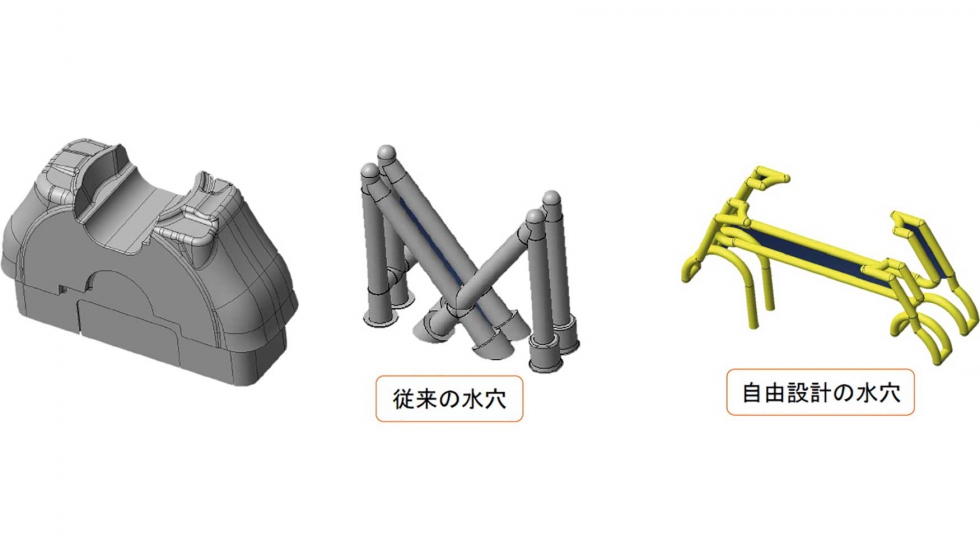
Reestructuración para combinar los puntos fuertes y especializarse en la fabricación aditiva y la I+D para sentar las bases del futuro de la industria de troqueles
Este grupo está abriendo puertas en el negocio de la fabricación aditiva con un marco que combina la fuerza de cada entidad: Nihonseiki a cargo del diseño y la fabricación de troqueles, la innovación tecnológica y las propuestas de tecnología; Tooling Innovation como base de fabricación aditiva; y Dynamo a cargo de la fabricación y venta de piezas de troquel. El grupo cuenta con más de 200 máquinas-herramienta repartidas entre las tres empresas, así como con numerosos y destacados ingenieros de diseño y CAM. Está abriendo la puerta al futuro con el lema “No hay pieza que no podamos fabricar”.
La fábrica también actúa como laboratorio para colaborar con fabricantes que poseen tecnologías similares y para crear nuevos métodos de fabricación con empresas afines, trabajando juntos para avanzar en las tecnologías de fabricación aditiva.
En la actualidad, la empresa se ha propuesto transformar la industria de la fundición a presión de aluminio, pero está desarrollando su negocio para expandirse a otros campos en el futuro. Nihonseiki lleva 100 años satisfaciendo las necesidades de sus clientes con soluciones totalmente novedosas en el sector de las matrices. Ahora, a través de la fabricación aditiva, pretende hacer tambalear las creencias convencionales de la industria de las matrices sobre lo que puede ser una matriz y lo que puede conseguir la fundición a presión.
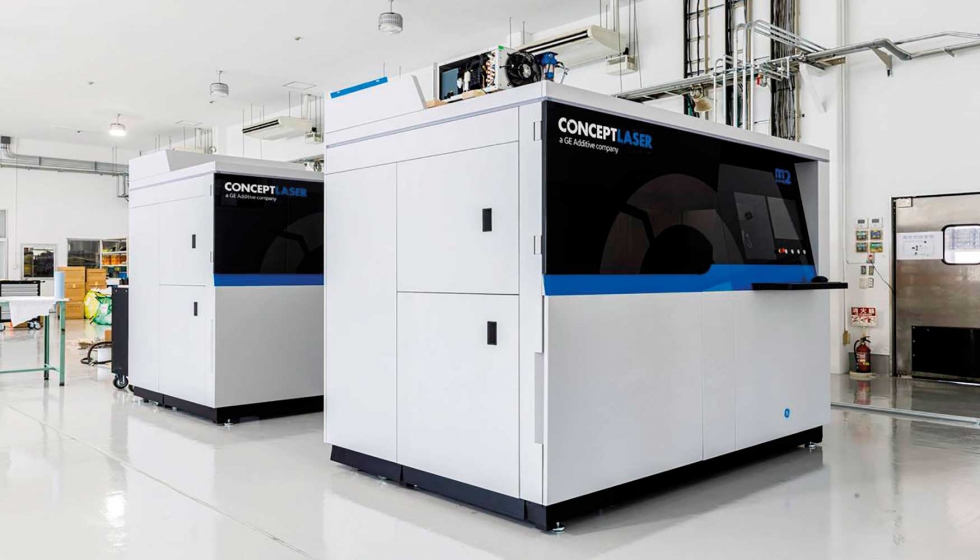