Mecanizado de fundiciones de alta resistencia
1. Introducción
Habitualmente, fundiciones como la fundición gris GG40 y GG50 han venido siendo utilizadas como bancadas de máquinas debido a la rigidez que presentan este tipo de fundiciones. Además, presentan una relativa facilidad de mecanizado y resistencia al degaste lo que hace que hayan alcanzado en la actualidad prácticamente el total del mercado de este tipo de componentes. Sin embargo, la fundición gris se caracteriza por tener en su microestructura grafito retenido en forma de láminas que limita su resistencia a tracción. Por ello, en este tipo de solicitaciones, la fundición nodular —también conocida como dúctil— se presenta como solución a esta problemática. Su microestructura presenta el grafito en forma nodular/esferoidal lo que hace que, además de presentar una mayor resistencia a tracción, que las fundiciones grises tengan una mayor tenacidad. Finalmente, otra fundición comercializada desde los años 70 es la fundición ADI (Austempered Ductile Iron). Esta fundición es un paso más en la utilización de la fundición nodular donde se la somete a un proceso de austemperizado llegando a duplicar los valores de resistencia a tracción y fluencia frente a la fundición nodular tradicional. Además, presenta una resistencia por kilogramo mayor que el aluminio y una resistencia al desgaste similar al acero [2]. Esto hace que este tipo de fundición sea conocida como fundición de alta resistencia.
2. Producción y características de ADI
A pesar de que el proceso de austemperizado se conoce desde 1930 y la fundición dúctil desde 1938, este proceso no se aplicará a esta fundición hasta los años 70.
El proceso de austemperizado al que es sometida la fundición nodular consiste en un proceso de tratamiento isotérmico donde se busca obtener una matriz con una estructura de bainita con ferrita y austenita retenida [3]. Sin embargo, para conseguir una fundición ADI además del austemperizado se hace necesario someter la fundición nodular original a un proceso previo de austenización con el fin de obtener una estructura homogénea austenítica. En la figura 1 se muestra una gráfica con las temperaturas y tiempo de cada proceso al que es sometida la fundición nodular para transformarla en ADI.
![Figura 1. Proceso de obtención de fundición ADI [4] Figura 1. Proceso de obtención de fundición ADI [4]](https://img.interempresas.net/fotos/1336074.jpeg)
El austempering se realiza habitualmente en hornos de atmósfera controlada y/o sales, según el siguiente ciclo térmico:
- Austenización del material (entre 850-950 °C).
- Enfriamiento brusco, y mantenimiento, a temperatura constante (entre 850-950 °C).
- Enfriamiento final a temperatura ambiente.
Según la temperatura de formación de la estructura de la bainita se diferencian dos tipos de bainita, por lo tanto, dos tipos de ADI.
- ADI superior (Bainita superior, formada entre 350÷450 °C)
- ADI inferior (Bainita inferior, formada entre 250÷300 °C)
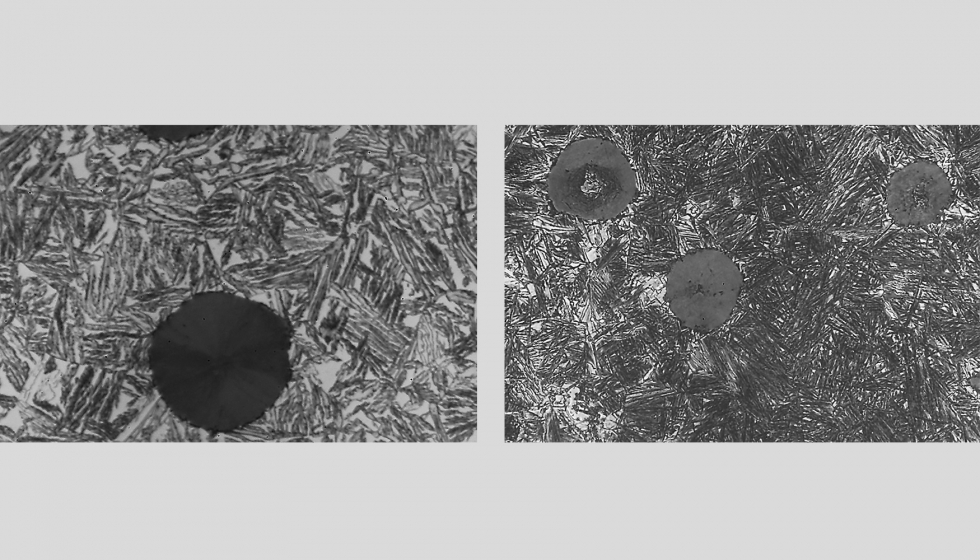
Algunas características de interés del ADI:
- La zona de mayor resistencia, y menor ductilidad corresponde al ADI inferior y la zona de menor resistencia, y mayor ductilidad corresponde al ADI superior.
- La tenacidad a la fractura, con un KIC = 40-70 Mpa para las estructuras de bainita inferior, y un KIC = 70-100 Mpa para las de bainita superior.
- EI límite de fatiga a flexión rotativa, con unos valores entre 300-350 Mpa para las estructuras de bainita inferior, y entre 400-450 Mpa para las de bainita superior.
Una fundición ADI de alta calidad debe estar definida por un mínimo de 100 nódulos por mm2; una nodularidad del 85%; una química consistente; y un máximo del 1,5% de carburos, inclusiones y micro-contracturas. En función de la temperatura a la que se someta a la fundición durante el proceso, existen hasta 5 grados con distintas características mecánicas. En la tabla 1 se muestran las propiedades mecánicas de éstas según la especificación estándar ASTM A536-84.
Grado |
Tensión última (MPa) |
Tensión de fluencia (MPa) |
Elongación (%) |
60-4-18 |
414 |
276 |
18 |
60-45-12 |
448 |
310 |
12 |
88-55-06 |
552 |
379 |
6 |
100-70-03 |
689 |
483 |
3 |
120-90-02* |
827 |
621 |
2 |
Tabla 1. Propiedades mecánicas fundición ADI [5]. (* Templado y revenido).
Por otra parte, una de las características que lleva a este tipo de fundición a ser conocida como de ‘alta resistencia’ es debido a la mayor resistencia al desgaste que presenta frente a otro tipo de fundiciones y aceros. En esta línea en 1989 Kovacs realizó una serie de ensayos de resistencia a abrasión donde la fundición ADI mostraba un mejor comportamiento que la fundición nodular o incluso que el acero sometido al proceso de austemperizado. Como se muestra en la figura 3, la diferencia de la fundición ADI frente a un acero austemperizado puede llegar hasta el 20% en durezas de 30HRc.
![Figura 3. Ensayo de abrasión [6] Figura 3. Ensayo de abrasión [6]](https://img.interempresas.net/fotos/1336076.jpeg)
2.1. Usos de la fundición ADI. Su inclusión en el mercado
La aplicación del tratamiento térmico de austempering ha supuesto una nueva mejora en las características de las fundiciones esferoidales, que hace factible su aplicación en piezas hasta ahora fabricadas exclusivamente en acero. Algunas de las ventajas que ofrece el ADI son:
- Buena resistencia al desgaste.
- Poca distorsión inducido por el tratamiento térmico.
- Capacidad de amortiguación de vibraciones.
- Facilidad de mecanizado.
- Mínima relación coste económico/límite elástico.
- Buena combinación de propiedades mecánicas resistencia –ductilidad.
- Obtención directa de geometrías cercanas a la final (Near Net Shape).
La principal aplicación de la fundición ADI es su utilización en lugar del acero en diseños ya existentes. Los sectores en los cuales más se utiliza la fundición ADI:
- Piezas del sector ferroviario (Bujes, ruedas de vagonetas, zapatas, ..)
- Piezas del sector de automoción (Suspensión)
- Piezas del sector de la construcción (Dientes de excavadora etc..)
- Fabricación de engranajes.
Actualmente, las fundiciones ADI están desplazando paulatinamente a la fundición nodular y aceros forjados debido a su superioridad mecánica. Este fenómeno se ha desarrollado principalmente en el sector automovilístico, donde aceros forjados e incluso aleaciones de aluminio han sido sustituidos por fundiciones ADI en piezas como cigüeñales, bielas, componentes de la caja de cambios y discos de embrague entre otros. En la figura 4, se muestra a modo de ejemplo el aspecto de un cigüeñal hecho de ADI ya finalizado. Gracias a la utilización de este material en el sector se ha conseguido aumentar la resistencia a desgaste y fatiga de dichas piezas a la vez que se reduce el peso de los automóviles y se ahorra en costes de fabricación. La fundición ADI ha demostrado ser ya en producción masiva un material sustitutivo del acero forjado con ahorro de costos, servicio más suave y silencioso y menor peso. Cuando se efectúa la mecanización antes del tratamiento de austemperizado se pueden obtener importante ahorros.
![Figura 4. Cigüeñal fabricado en ADI [7] Figura 4. Cigüeñal fabricado en ADI [7]](https://img.interempresas.net/fotos/1336077.jpeg)
Sin embargo, donde la fundición ADI destaca por su excepcionalidad es en la fabricación de engranajes debido no sólo a sus superiores características mecánicas ya descritas a lo largo del artículo frente a los aceros sino porque siguen presentando una mayor capacidad de amortiguación que éstos y lubricación gracias a sus nódulos de grafito, lo que se traduce en un menor ruido durante su funcionamiento [8].
En este contexto, la fabricación de planet carriers presentes en las multiplicadoras hacen de la fundición ADI la primera opción a seleccionar por el diseñador. En este tipo de piezas, la fundición ADI está sustituyendo a fundiciones de acero, forja e incluso fundiciones nitruradas. Gracias a la utilización de la fundición ADI en la fabricación de estos componentes no sólo se reduce el peso frente a las fundiciones de acero, sino que no necesitan proceso de rebabado en el proceso de acabado; normalmente no necesitan ser sometidos a tratamientos de endurecimientos superficiales; y las tolerancias conseguidas son más estrechas. En la figura 5, se muestra el montaje de un planet carrier fabricado con fundición ADI.
![Figura 5. Montaje de un planet carrier [9] Figura 5. Montaje de un planet carrier [9]](https://img.interempresas.net/fotos/1336078.jpeg)
La fundición ADI es por tanto, en aspectos generales, superior a los otros tipos de fundiciones como la nodular o gris, pero por lo que realmente destaca es porque también es capaz de competir con los aceros y llegar a sustituirlo en muchos de los casos con el fin de obtener productos más robustos. Al mismo tiempo, permite ahorrar costes de producción. Este concepto, muy arraigado en el sector automovilístico, permite su expansión en este sector.
3. Fundición grafítica esferoidal GGG70
Las fundiciones esferoidales se comenzaron a fabricar comercialmente en los años 40-50. Este tipo de fundición aportó una mejora sustancial de las propiedades mecánicas (resistencia y ductilidad) respecto a las fundiciones grises, tradicionalmente conocidas como hierro colado. Las fundiciones esferoidales son más resistentes y dúctiles que las fundiciones grises laminares. Las propiedades mecánicas llegan a ser parecidas a las de aceros.
Pequeñas adiciones de magnesio y/o cesio a la fundición gris en estado líquido producen la esferoidización del grafito. Para controlar el tamaño y distribución de los esferoides de grafito, la fundición puede inocularse antes, durante y después de la etapa de nodulización. El magnesio actúa como agente nodulizante y el cesio para reducir la sensibilidad del magnesio a la acción del plomo, bismuto, estaño, antimonio y titanio, que inhiben la formación de grafito esferoidal.
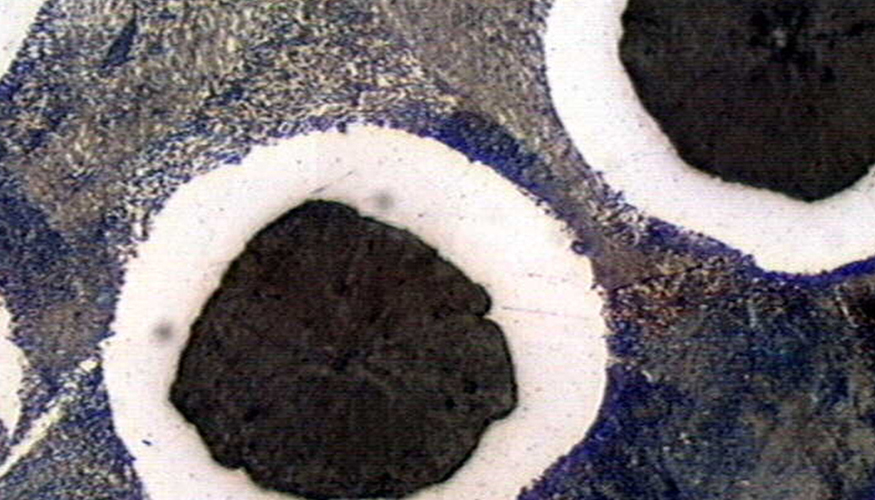
Las principales aplicaciones de la fundición esferoidal son: Válvulas, cuerpos de bombas, compresores, maquinaria de construcción, maquinaria para el trabajo del papel e industria maderera, cigüeñales, pistones, componentes del automóvil (pinzas de freno) y de maquinaria, brazos de suspensión, colectores, etc.
Todas las caracteristicas mecánicas, fisicas y estructurales de esferoidales vienen definidas en la norma, GGG-70 (DIN 1693-73 ductile cast iron grade). Algunos ejemplos prácticos de la fundición grafitica esferoidal GGG-70 son:
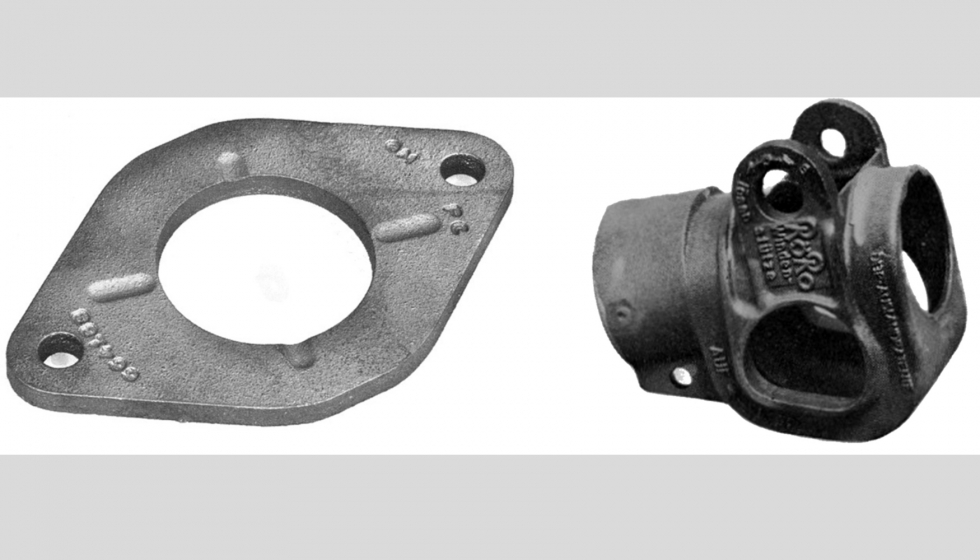
4. Fundición CGI o gris vermicular
A veces aparece el grafito de forma vermicular (forma de lombriz), como consecuencia de una retención en la fundición antes de verterla en el molde, lo cual lleva un enfriamiento más lento que hace que pierda efectividad la inoculación provocada por el magnesio y el cesio.
Actualmente se produce fundición vermicular a partir de una nodulización del grafito mediante adicción de esferoidizantes, pero el resultado final es un grafito en forma de lombriz. Se puede decir a groso modo que el grafito de la fundición vermicular es intermedio entre el grafito laminar y esferoidal, consiguiéndose las características físicas del grafito laminar y las características mecánicas del esferoidal, aunque sin llegar a los niveles de estos. La composición en grafito de una fundición vermicular será así de un 80% en grafito vermicular y el resto, un 20%, en grafito esferoidal o compacto.
Las fundiciones vermiculares se utilizan para la fabricación de bloques de motor, colectores, etc.
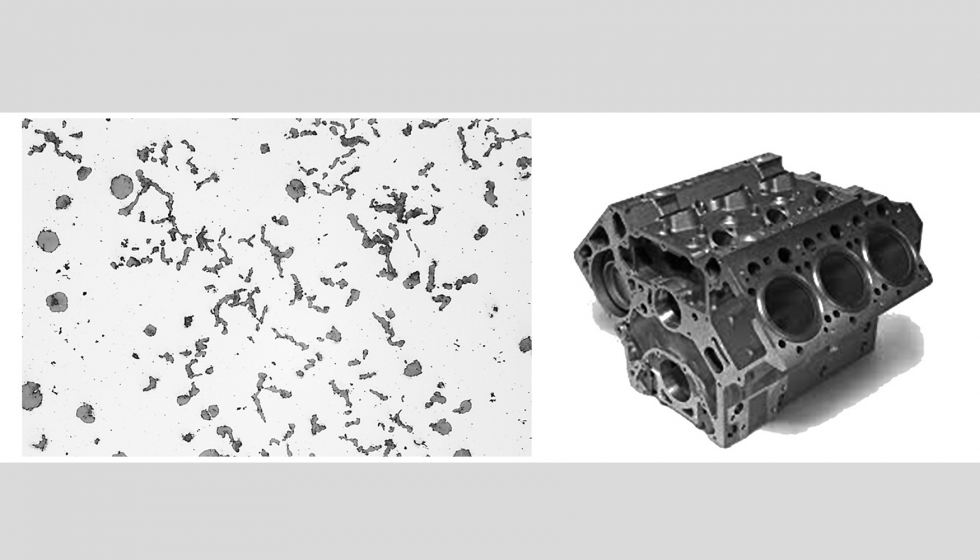
5. Caso de estudio
A continuación se muestra un ejemplo práctico basado en la experiencia del grupo de Fabricación de Alto Rendimiento de la UPV/EHU. En concreto, nos referimos a ensayos de caracterización de machos de roscar sobre fundiciones ADI llevados a cabo en el taller mecánico de la Escuela de Ingenieros de Bilbao.
En cualquier operación de mecanizado de fundiciones ADI en primer lugar hay que distinguir el grado del ADI que se vaya a trabajar (los grados más bajos tienen valores de resistencia a la tracción de 850 MPa y los más altos llegan hasta 1.600 MPa), por tanto en este caso la dificultad de roscado puede variar muy considerablemente según el grado, y la forma de roscar habrá que adecuarla. Así, los grados más bajos se pueden roscar directamente con macho después de haber taladrado previamente el agujero, y los grados más altos y exigentes tendrán que hacerse con macho, después del agujero previo, pero dos etapas, antes y después de completar el tratamiento térmico de temple (temperizado) de la pieza o recurrir al método más lento pero seguro como es el roscado por interpolación en una fresadora.
En nuestro caso, hemos roscado ADI-900 que corresponde al grado más bajo y por tanto menos resistente, y que hemos podido roscar con macho, en una fresadora vertical Ibarmia ZV 25/ U600. El objetivo de los ensayos era encontrar los machos más adecuados en geometría y recubrimiento para roscar ADI-900 en condiciones industriales.
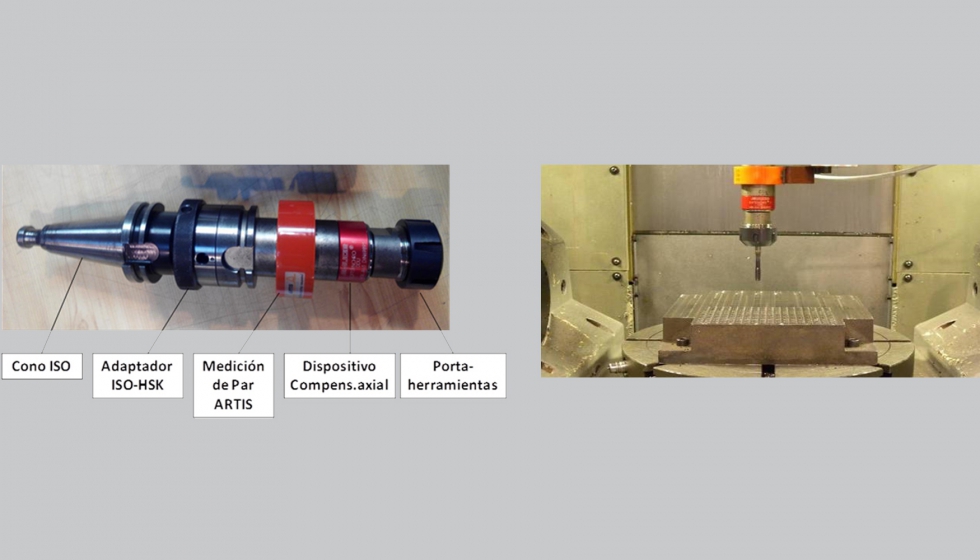
En los ensayos, nos hemos encontrado que el ADI es un material muy heterogéneo en su estructura, lo cual hay que tener en cuenta respecto al modo de roscar y supone tomar algunas precauciones. A los ADI les afecta la heterogeneidad general que se da en las fundiciones, en las que se forman rechupes, hay inclusiones, etc, . En este caso, en la fase de solidificación de la fundición según la composición y la calidad y los parámetros de la fundición se produce la distribución y nucleación del grafito, a lo que se añade posteriormente el tratamiento térmico de austenización y de temple. De modo que en el conjunto del proceso de fundición y tratamiento térmico deben de respetarse unas composiciones, unas temperaturas, unas velocidades y tiempos de enfriamiento específicos en función del espesor de la pieza, etc, para obtener en cada punto la microestructura requerida de ADI. Se trata de un proceso complejo y difícil, por lo que el resultado suele ser un material poco homogéneo y de propiedades mecánicas y de dureza distintas a lo largo del volumen de la pieza. En nuestro caso, nos hemos encontrado con piezas en las que la variación de la dureza era del 30% en distintos puntos dentro de la misma. Esta variación de las condiciones de la pieza afecta al taladrado previo y al roscado, de modo que hacen aconsejable el uso de elementos intermedios entre el cabezal y la herramienta que atenúen las diferencias del material. En nuestro caso hemos empleado un dispositivo de compensación axial SoftSynchro de Emuge.
Además como es bien conocido entre los roscadores, sin el acoplamiento de compensación axial se ha constatado que se produce cierto retraso de sincronización entre el paso del cabezal y el del macho, de forma que al roscar aparecen sobre la herramienta esfuerzos de tracción que hemos podido medir. Por tanto el empleo de los sistemas de compensación axial además de atenuar las diferencias resistentes del material, está aconsejado para minimizar los posibles desajustes de sincronización entre el giro y el avance del cabezal y el paso del macho, en todas las fases de producción del agujero roscado. Se puede decir que su uso redunda en mejorar la calidad de los agujeros roscados y en alargar la vida de la herramienta.
En nuestro caso los ensayos han consistido en roscar agujeros ciegos de M8x20 mm, roscas normalizadas de paso 1,25 mm, para lo que hemos empleado machos de corte con agujero de refrigeración axial interior por el que aplicada la taladrina se facilita la evacuación de los fragmentos de viruta en sentido contrario al del avance del macho por los canales entre los dientes. La refrigeración se ha realizado con emulsión de aceite en agua al 7%, habitual del taller. Los ensayos de roscado se han realizado a Vc=30 m/min, que es una velocidad de corte bastante elevada para este material, ya que se pretendía ensayar en condiciones de trabajo representativas de la industria.
Se ha prestado atención a la calidad del taladrado de los agujeros previos de ?6,8 x25 mm. Se ha empleado un portaherramientas de apriete hidráulico, en lugar de las pinzas de tres apoyos, y vigilado que el mango de la broca no deslizara por la boquilla (como nos ocurrió en alguna ocasión) para que los errores de los agujeros taladrados fueran mínimos y luego no afectaran al roscado posterior.
Entre todo el abanico de geometrías de los machos, en el caso de roscar ADI, por tratarse de de un material exigente de viruta fragmentada y corta, la geometría aconsejada suele ser de pocos dientes de chaflán y de canales rectos, sin hélice, de modo que los dientes resulten más robustos. Con entradas cortas, el par de giro se convierte a través de pocos dientes de corte en fuerzas de corte elevadas. En nuestro caso, los machos han sido de 4 dientes por vuelta, o de 4 canales rectos. Respecto a los dientes, el ángulo de desprendimiento, para roscar ADI suele ser nulo y la zona de alivio entre la cara de incidencia del diente y el agujero mínima, para que no se produzca una fricción excesiva del ADI sobre la cara de incidencia, ni su adhesión en esta zona, y el diente conserve su robustez.
Se ha elegido como material para el sustrato del macho el acero rápido posteriormente recubierto en lugar de metal duro, ya que aunque éstos sean más duros y de mejor rendimiento, por su mayor porosidad son más frágiles, y se ha dado más relevancia a la tenacidad y la seguridad de los de acero rápido. Los de metal duro tienen el riesgo de que si se rompiera un diente al roscar podría quedar un trozo del macho alojado en la pieza, de modo que podría llegar a invalidarla.
Se han ensayado varios recubrimientos comerciales de base aluminio titanio de Metal Estalki (Platit) sobre machos de sustrato de HSS-Poli Metalúrgicos. Entre los ensayados destacan el conocido AlTiN y el recubrimiento que mejor resultado ha dado, que ha sido el de AlTiSiN-Gradiente que combina unos buenos valores de coeficiente de fricción, buena resistencia a elevadas temperaturas y buena adhesión del recubrimiento al sustrato del macho. En recubrimiento del tipo gradiente hay una capa con TiN y de AlN, pero en la que varían su concentración de modo inverso entre ellas, ofreciendo el nitruro de titanio una buena adhesión al sustrato y el nitruro de aluminio una buena dureza superficial en la parte exterior del recubrimiento. De todas formas, la mejora del rendimiento del recubrimiento que mejor resultado ha ofrecido el AlTiSiN-G frente al menos bueno ha sido del orden de un 10%, medido con el par medio de roscado. Se ha empleado el par medio de roscado como indicador de deterioro de los machos dado que un macho a medida que se desgasta y se redondean las aristas de corte va requiriendo más par y potencia para producir una rosca igual.
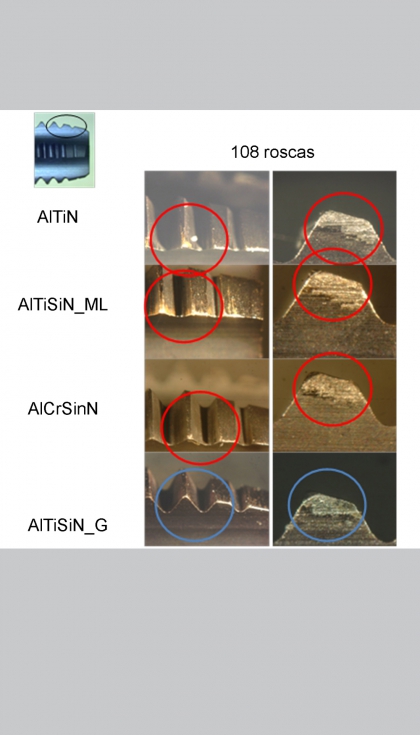
Cabe mencionar que todas las roscas producidas empleando el sistema de compensación axial han sido OK, comprobadas con el calibre Pasa-No pasa M8 H6, y sin embargo en algunas pruebas realizadas con roscado rígido en otra fresadora vertical, prescindiendo de la compensación axial, se han producido roscas no válidas.
Bibliografía
[1] http://www.prtr-es.es/ Visitada el 19/10/2016 a las 16:45.
[2] http://www.sandvik.coromant.com Visitada el 19/10/216 a las 18:10
[3] Sierra, H. y Ortega, J. Temperatura de transición de la fundición nodular austemperada no aleada. 2004. Revista Universidad EAFIT. Vol. 40, 134. pp. 80-89.
[4] Acosta, M., Martínez, M., López, J. 2000. El tratamiento de los hierros nodulares en el mejoramiento de los materiales en la industria automotriz. Publicación Técnica No. 148. Sanfandila, Qro.
[5] Keough, J., Hayrynen, K. 2010. Designing with austempered ductile iron (ADI). ASF Proceedings. American Foundry Societey. Paper 10-129. pp. 1-15.
[6] Kovacs B., Keough J., Pramstaller, D. 1989. The austempered ductil iron process. Final report to the Gas Research Insistute, NTIS No. PB89190946LP.
[7] http://www.glcrankshaft.com/eng/production.asp. Visitada el 20/10/2016 a las 11:55.
[8] Keough, J. 1995 ADI – A designer gear material. Gear Technology. pp. 28-29
[9] https://i.ytimg.com/vi/TzdgPOjMUsQ/maxresdefault.jpg Visitada el 20/10/16:38
Mandrinado en fresadora
En sectores como el aeronáutico, eólico, industria petroquímica, etc cada vez se utilizan más las fundiciones de alta resistencia, debido a sus altas prestaciones mecánicas. En un entorno cada vez más automatizado, el uso de máquinas multitarea permite obtener la máxima precisión y capacidad de producción. Piezas de gran tamaño y tolerancias estrictas son fabricadas en grandes máquinas bajo un conjunto de operaciones perfectamente armonizadas entre los cuales se encuentra el mandrinado. El mandrinado o ampliación de un orificio mediante el arranque de material se caracteriza fundamentalmente por ser una operación en la que las fuerzas aplicadas en el corte producen deformaciones considerables, limitando la capacidad de arranque y precisión. Por este motivo, para el mecanizado de fundiciones de alta resistencia el estudio de las fuerzas y parámetros de corte se hace indispensable para poder adaptar las condiciones de los equipos a un régimen de trabajo estable y preciso. Además de las particularidades del propio material, el parámetro que determina la limitación es la esbeltez del agujero, la relación entre su longitud y diámetro. Materiales de menor maquinabilidad y geometrías de mayor esbeltez ahondarán en la complejidad del proceso.
Una forma flexible de adaptarse a diferentes requerimientos dimensionales es el uso de cabezales intercambiables. Estos dispositivos controlados mediante el CNC de la máquina realizan mecanizados de forma totalmente automatizada. Actualmente existen en la industria varias opciones para diferentes situaciones de fabricación, como por ejemplo para adaptar un centro de mecanizado para realizar torneados mediante un dispositivo TA-Center de D’Andrea o para máquinas mayores, U-Troni de D’Andrea, KomTronic de Komet Group o equipos tipo Trevisan.
De forma similar a un torno, el uso de un cabezal de mandrinado en una fresadora permite realizar mecanizados de geometrías de revolución interpolando los ejes Z de la fresadora y el eje U del cabezal. El eje U se convierte en el análogo al eje X del torno siendo el eje Z el eje de rotación del cabezal. Siempre que el espacio dentro de la pieza mecanizada y la longitud y geometría de la herramienta lo permitan, se pueden realizar mandrinados de forma, más allá de los mandrinados convencionales.
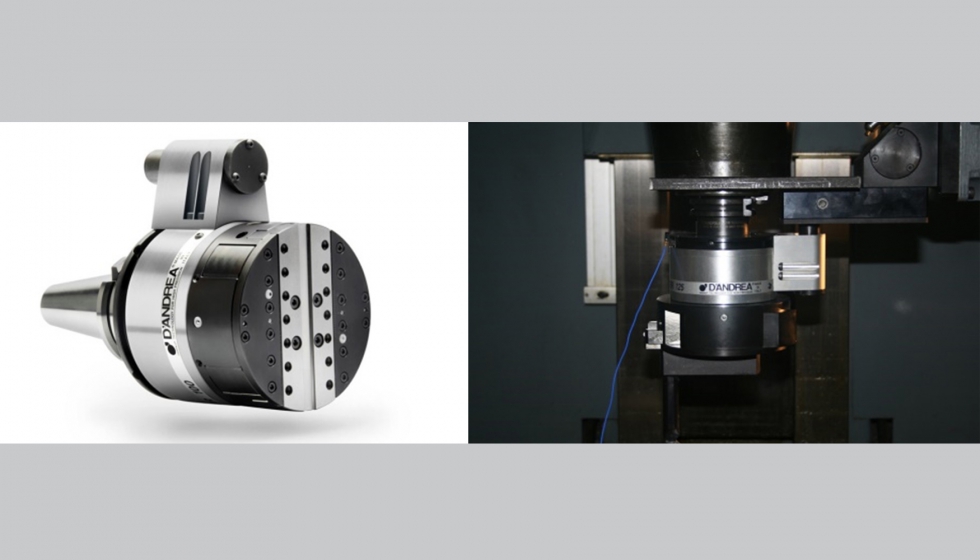
Figura 11. Cabezal de D’Andrea para operaciones de interiores con eje U y medición de vibraciones.