Unión de materiales disímiles sin adhesivos: innovación para la reducción de peso y costes
El creciente interés del uso de los materiales poliméricos en diversos procesos industriales y aplicaciones estructurales y/o avanzadas ha impulsado la investigación de la combinación de materiales disímiles y sus posibles métodos de unión —un factor crítico para la fabricación de componentes que incluyan materiales disímiles—.
En la actualidad, las piezas fabricadas con materiales disímiles, tales como polímero–polímero y metal–polímero presentan una elevada demanda. Por ejemplo, dichas piezas son requeridas ampliamente en industrias como la automoción y aerospacial, donde destaca la fabricación de componentes híbridos a partir de materiales disímiles ligeros tales como aleaciones de aluminio o magnesio y polímeros reforzados [3] [4] [5].
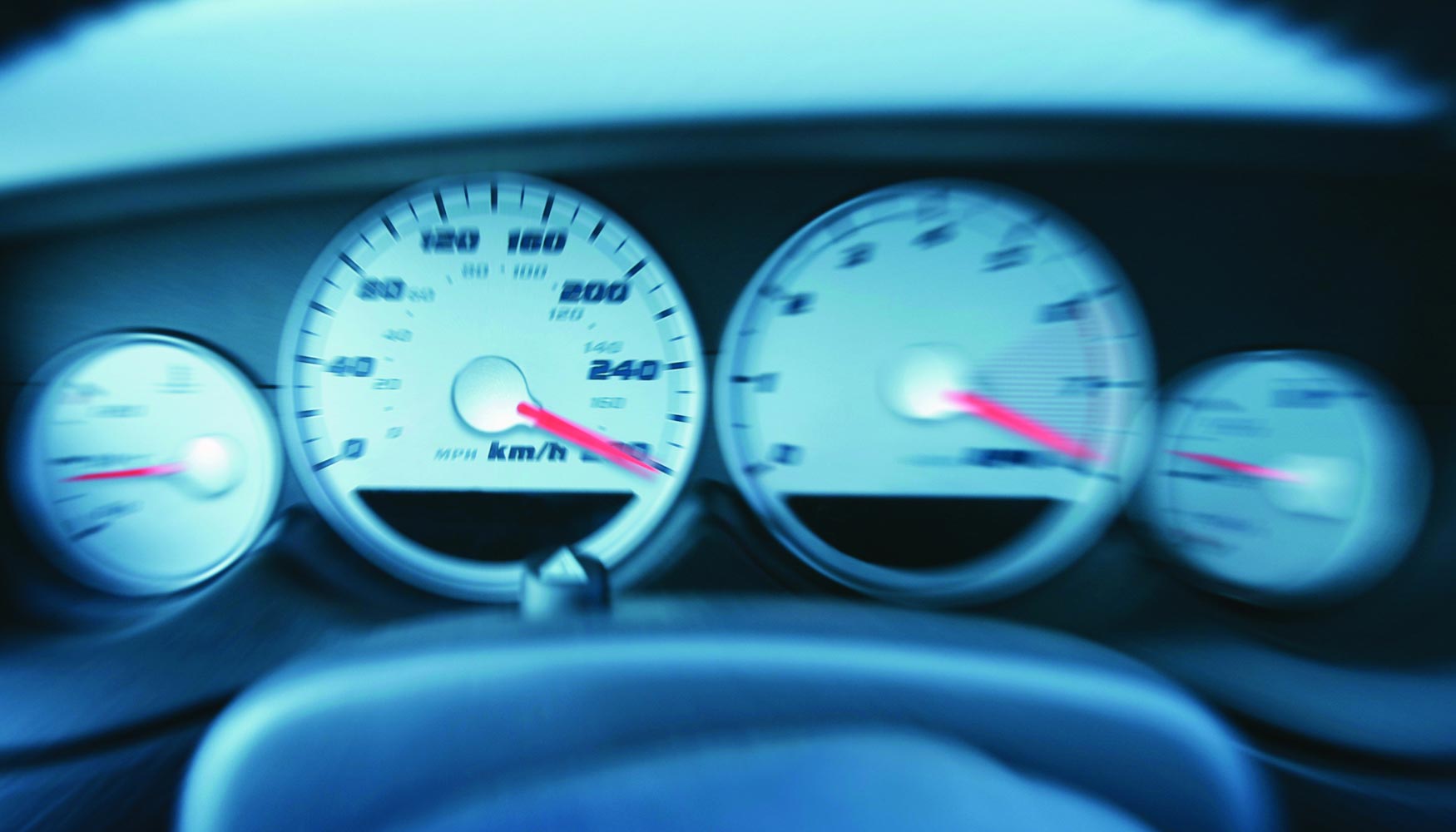
Uno de los principales propósitos para el uso de combinaciones de materiales disímiles es la mejora en la flexibilidad de diseño del producto final, permitiendo a los diferentes materiales ser utilizados de una manera eficiente y funcional basada en las propiedades específicas de cada material. Las uniones polímero – polímero se caracterizan porque facilitan la flexibilidad en el diseño. Un ejemplo típico podrían ser las uniones de composites de matriz termoplásticas y los composites basados en termoestables [6]. Las uniones metal – polímero, en cambio, combinan la resistencia y ductilidad del metal con la resistencia físico-química y la ligereza de los polímeros [5]. Los componentes metálicos se utilizan en secciones donde se requieren alta rigidez y resistencia, mientras que el material plástico proporciona propiedades químicas únicas, y es capaz adicionalmente de integrar funciones a través de la formación de formas complejas mediante procesos de moldeo [7].
En aplicaciones estructurales, es muy importante maximizar eficientemente la contribución de la unión de cada material con el fin de asegurar unas óptimas propiedades mecánicas, pero obteniendo una solución competitiva en cuanto a peso y coste [7].
Los métodos de unión de materiales disímiles más frecuentemente empleados son las fijaciones mecánicas y el pegado mediante adhesivos. Sin embargo, estos procesos de unión presentan algunas limitaciones, tales como la concentración de esfuerzos, la necesidad de una superficie amplia de preparación, el peso adicional y las emisiones perjudiciales para el medio ambiente.
Los sistemas de unión emergentes mediante soldadura/térmicos y/o combinación de sistemas se consideran más adecuados para la unión de materiales disímiles polímero – metal y polímero – polímero para conformar un composite estructural. La selección del sistema de unión más adecuado ha de tener en cuenta:
- su facilidad de incorporación (preparación previa requerida por las superficies de unión, tiempo de procesado, fijación durante la preparación del laminado o posterior al desarrollo del composite),
- las propiedades de adhesión demandadas por la pieza,
- el tipo de cargas al que vaya a estar expuesta, etc.
En función del sistema de unión seleccionado, no se debe descartar la posibilidad de rediseñar la pieza para minimizar el efecto de este sistema sobre el rendimiento del composite (aumentar espesor del laminado en zonas críticas y utilización de sistemas de refuerzo).
Estos sistema de unión emergentes se centran en romper las barreras de los métodos de unión de las estructuras multicomponentes de materiales disímiles, usando tecnologías de unión medioambientalmente sostenibles (libre de imprimaciones que emitan solventes orgánicos) y reduciendo el número de pasos de procesado con la finalidad de producir componentes multimateriales estructurales y/o propiedades avanzadas y económicamente viables.
La selección entre unión adhesiva, mecánica o por soldadura es una de las mayores decisiones que deben tomarse. Existen diversos parámetros que influyen en dicha elección (figura 2).
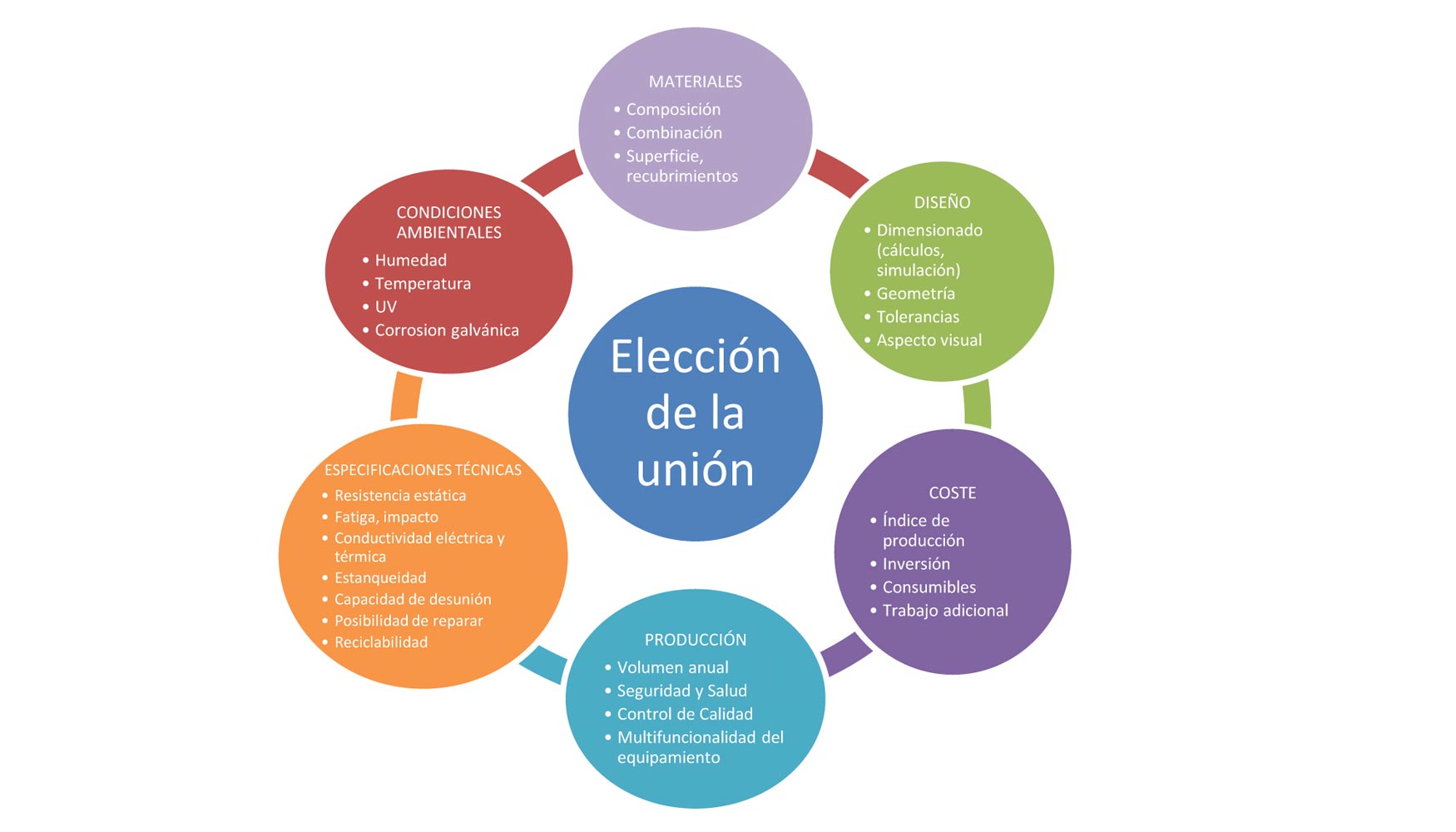
En la actualidad, se están investigando técnicas muy prometedoras de soldadura y métodos de unión de materiales disímiles con la finalidad de solucionar los problemas relacionados con las técnicas de unión tradicionales (unión mecánica y mediante adhesivos). Algunos ejemplos de estas tecnologías emergentes son la soldadura mediante láser, soldadura mediante ultrasonidos, así como soldadura mediante fricción por puntos, soldadura por fricción-agitación.
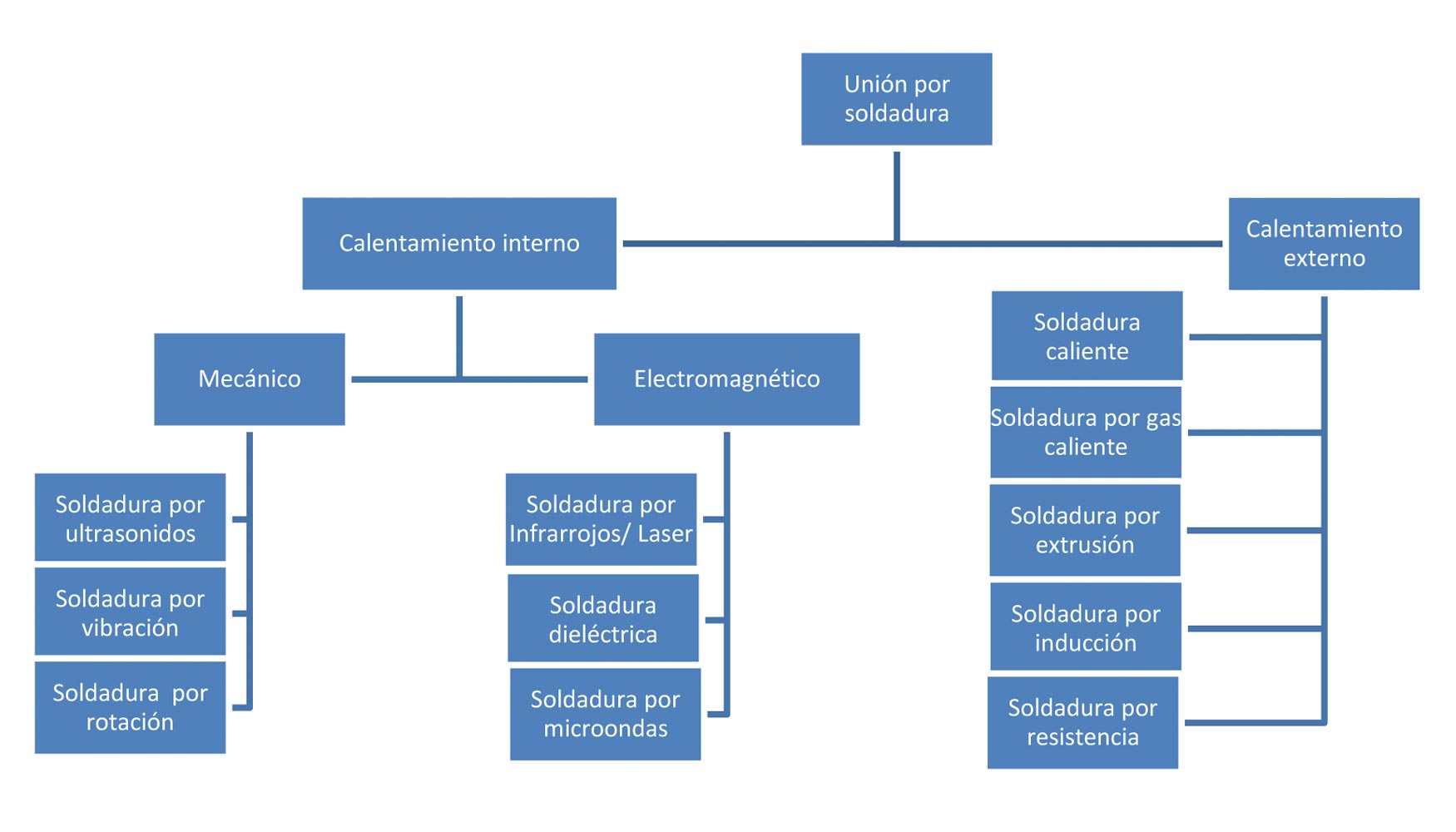
La aplicación efectiva de los procesos de unión por soldadura/térmica requiere de una compresión exhaustiva del comportamiento de los materiales (metal-polímero, polímero-polímero) en dichos procesos, así como el conocimiento de la capacidad y limitaciones de los procesos de unión cuando se refiere a la unión de materiales disímiles.
De las técnicas de unión por soldadura/térmica hasta ahora investigadas, la soldadura por metal-polímero por ultrasonidos parece ser el método más prometedor para estructuras híbridas, y ha sido empleada exitosamente en la unión de metal y polímeros reforzados con fibra de vidrio. La unión por fricción-rotación presenta resultados similares a la soldadura ultrasónica. Sin embargo, una limitación de esta técnica es que está principalmente recomendada para materiales con bajo punto de fusión y no es aplicable a metales muy gruesos. La soldadura mediante láser de metales/polímeros puede usarse para conseguir uniones estables entre estructuras híbridas metal y polímeros. Entre las ventajas de este método destacan la rapidez y la alta adaptabilidad del proceso. En general, estas nuevas técnicas emergentes ofrecen prometedoras alternativas a la unión de materiales disímiles metal-polímero o polímero-polímero mediante las tecnologías tradicionales [8].
Algunos de los métodos más innovadores, como la soldadura por fricción (Friction Stir Welding-FSW), microondas, ultrasonidos, inducción, rotación, láser o resistencia térmica para la unión de materiales disímiles sin adhesivos son más rápidos y limpios que los métodos tradicionales.
Referencias
[1] A. B. Abibe et al. Journal Thermoplastic Composite Materials. 24 (2011) 233.
[2] H. E. Friedich. Journal Advanced Engineering Materials. 5 (2003) 105.
[3] C. E. Bakis et al. Journal Composite Construction. 6 (2002) 73.
[4] W. S. Kim et al. International Journal Adhesives. 30 (2010) 408
[5] F. Balle et al. Journal Advanced Engineering Materials. 11 (2009) 1.
[6] C. Ageorges et al. Composites: Part A. 32 (2011) 1603.
[7] S. Droste et al. Bonding & Joining, 3rd Annual SPE automotive composite conference(Michigan, 2003).
[8] P. Kah et al. Techniques for joining dissimilar materials: metals and polymers. Rev. Adv. Maer. Sci. 36 (2014) 152-154.