Desarrollo de una plataforma flexible y sostenible para fabricación de gran precisión en piezas complejas de medio y gran tamano
El objetivo fundamental del proyecto es desarrollar una plataforma flexible para la automatización de operaciones de fabricación de gran precisión sobre piezas y estructuras de gran tamaño (por encima de 10 metros de longitud) y fabricar un demostrador del sistema a escala real. El sistema consiste en un robot industrial convencional montado sobre un sistema convencional de puente grúa, existente en cualquier infraestructura industrial, y controlado con un sistema inteligente que le permite corregir su posición en tiempo real.
El sistema permite cubrir recorridos muy grandes, que se traduce en amplias zonas de trabajo para el robot, al mismo tiempo que, al ser un sistema suspendido, no necesita infraestructura de suelo, liberando así las zonas de la fábrica que no se utilicen en un momento dado. Utilizando tecnologías basadas en monitorización laser, el sistema controlará en tiempo real, la posición de la herramienta, montada en el robot, y corregirá el movimiento del robot para conseguir altas precisiones de posicionamiento (±0.4mm en piezas de 100 metros de longitud).
El desarrollo del sistema permitirá obtener calidades y precisiones en piezas de gran tamaño, similares a las que actualmente se obtienen para piezas pequeñas, ya que la precisión del sistema se basa en un sistema óptico, frente los sistemas mecánicos tradicionales, que penalizan la precisión en función de las dimensiones.
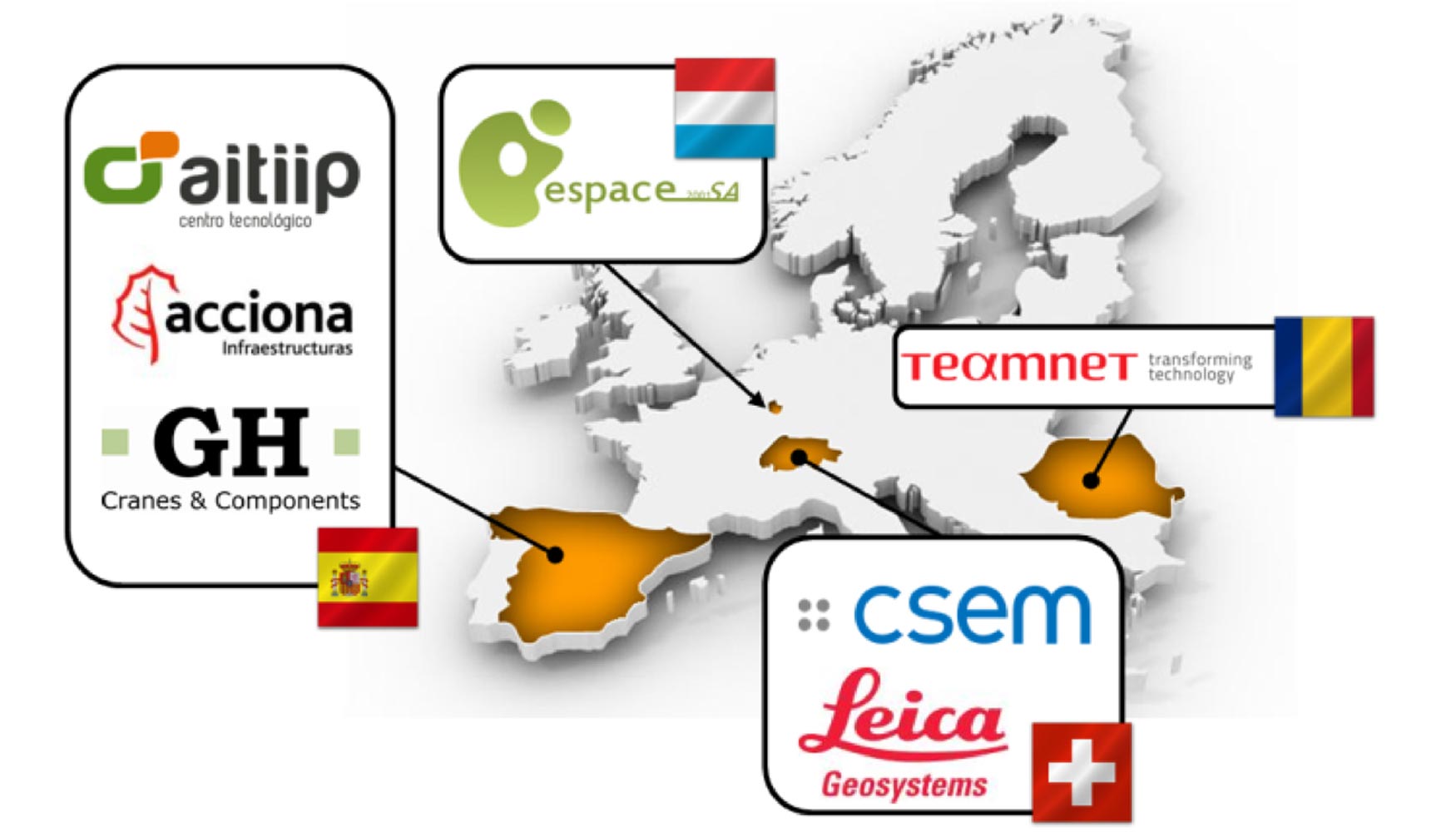
Los sectores de aplicación de esta nueva tecnología, son aquellas que fabrican piezas de grandes dimensiones como Aeronáutica, energías renovables, ingeniería civil, naval, ferrocarril, y en general cualquier industria que fabrique piezas, modelos, moldes o utillajes de grandes dimensiones.
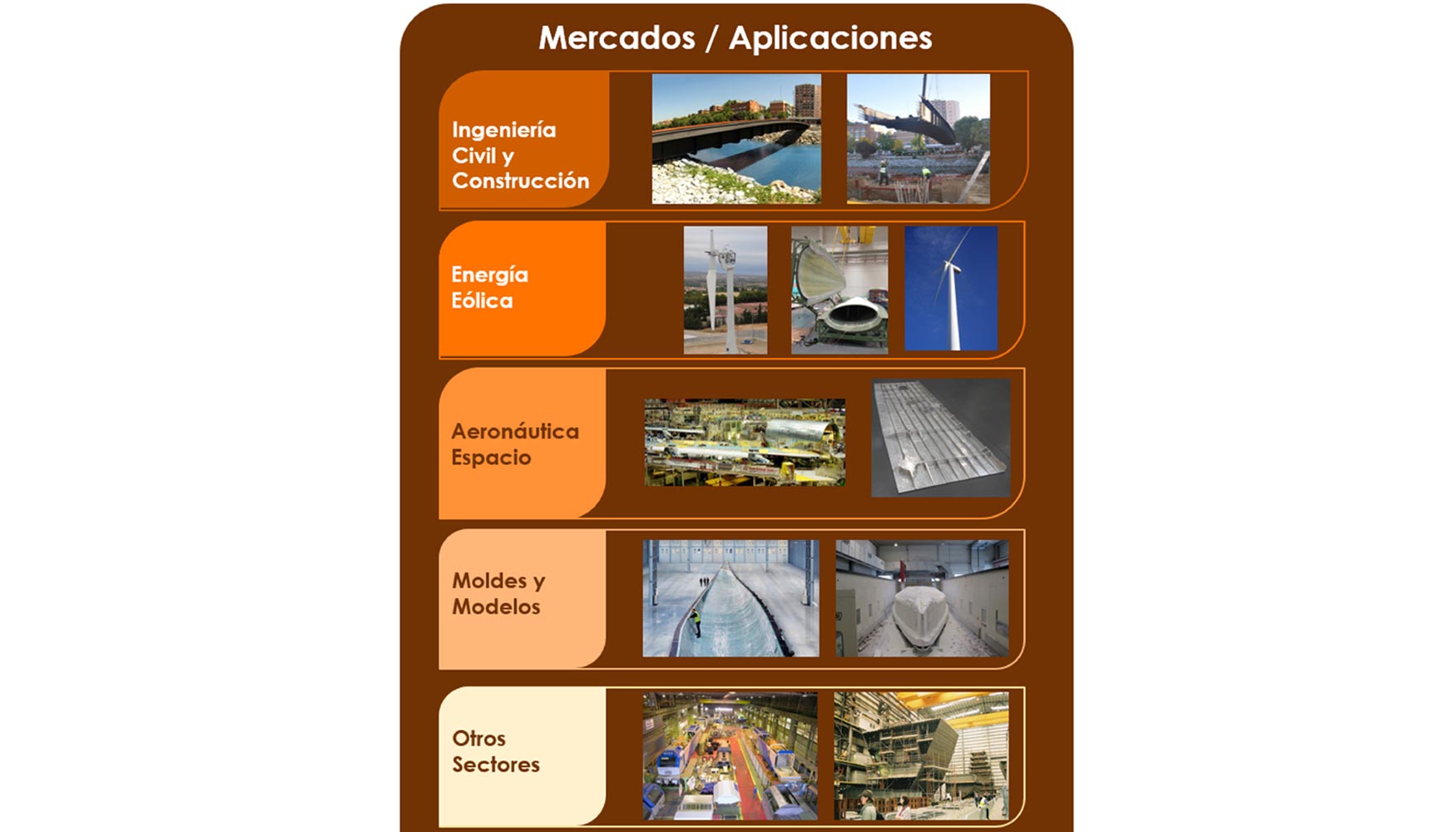
Contexto
Uno de los mayores retos a los que se tiene que enfrentar la industria actual es la fabricación y reparación de grandes piezas (más de 10 metros).
Los procesos de fabricación actuales como mecanizado, fresado, lijado, pulido, desbarbado, soldadura, remachado, atornillado o pintado, que se realizan sobre estas piezas, siguen haciéndose de forma manual, principalmente debido al tamaño de las máquinas necesarias, y a las altas inversiones que conllevarían, en el caso de que fueran viables. Por esta razón, no existen todavía sistemas automáticos que puedan realizar estas operaciones de forma autónoma, con la precisión requerida por los sectores industriales objeto de esta investigación.
Una revisión del estado actual de la técnica revela que es muy dífícil desarrollar un sistema robusto y suficientemente preciso para realizar tales operaciones, ya que el error de posición crece exponencialmente al mismo tiempo que se incrementa el tamaño de la máquina, generando errores que acumulan fallos provenientes de diferentes fuentes, que incluyen el error en la fabricación mecánica de la propia máquina.
Existe un gran salto cualitativo y cuantitativo entre las tolerancias obtenidas sobre productos pequeños respecto a grandes piezas y estructuras. Por ello resultaba inminente la necesidad de realizar nuevos desarrollos que permitan extrapolar la calidad con que se procesan las pequeñas piezas a tamaños mayores.
Concepto
Entre los sectores industriales descritos anteriormente, el proyecto Megarob se centrará en la fabricación de grandes componentes como piezas de aeronaves, cascos de barco, palas y mástiles de aerogeneradores, paneles de vagones de ferrocarril, y los moldes y utillajes que las piezas de este tipo requieren.
Los principales problemas a los que se enfrentan los fabricantes de esta tipología de piezas son:
- Dificultad para obtener alto nivel de precisión.
- Necesidad de mover las piezas entre diferentes emplazamientos dentro de las plantas de producción, para realizar las diferentes operaciones programadas.
- Realización manual de gran cantidad de operaciones, esto implica gran cantidad de rechazos que merman la competitividad de las empresas fabricantes.
- Gran cantidad de utillajes para operaciones manuales. Dichos utillajes requieren grandes inversiones.
- Elevados tiempos de fabricación, sobretodo en operaciones hechas a mano.
El desarrollo propuesto en Megarob alcanzará niveles de precisión en el posicionamiento de +/-0,216 mm +0,5 μm/m, lo que supone +/- 0,4 mm en piezas de 100 metros de longitud. El sistema descrito tiene que solucionar diferentes problemas tecnológicos, pues en definitiva éste consiste en un robot industrial, montado sobre una estructura convencional de puente grúa, para permitir el acceso a grandes áreas de trabajo.
El principal problema a solucionar es conseguir los niveles de precisión requeridos para las piezas. De hecho, el robot por sí mismo tiene una precisión limitada. Si además va montado sobre un puente grúa, que le añade tres movimientos de translación, dichos errores teóricamente deberían incrementarse de forma exponencial, como consecuencia de la adición de ejes y el aumento drástico del tamaño de la máquina.
La metodología de trabajo de Megarob consiste en dividir el total del área de trabajo que puede cubrir el puente grúa en sectores tridimensionales, con una determinada forma geométrica. Cada sector será un área de trabajo zonal. El puente grúa trasladará al robot a la primera de dichas zonas. Una vez alcanzada la posición, esta será monitorizada de forma precisa mediante el uso de un sistema laser tracker.
Para ello diferentes objetivos se dispondrán en la base del robot, permitiendo la definición inequívoca de la posición del mismo en el espacio.
A partir de aquí el robot ejecutará los movimientos programados, mediante un sistema CAM, para realizar la operación de fabricación prevista para dicha zona.
Incluso monitorizando la posición de la base del robot, los análisis realizados durante el proyecto desvelan nuevas fuentes de imprecisiones en el posicionamiento derivados de diferentes fuentes:
- Imprecisiones derivadas de la descripción cinemática del propio robot.
- Desvíos que aparecen como consecuencia de la debilidad estructural del mismo. Los robots industriales son estructuras de eslabones relativamente flexibles, y con holguras en los ejes. Como consecuencia de ello la aplicación de fuerzas se traduce en desplazamientos de la estructura, y como consecuencia desvíos respecto de las posiciones programadas.
- Las fuerzas de corte que se generarán provocarán desplazamientos por la razón descrita en el punto anterior.
- Posibles desplazamientos de la base del robot como consecuencia de fuerzas de inercia y de corte, debidos a la falta de rigidez del puente grúa.
Para minimizar dichos efectos, durante todos los movimientos del robot, dentro de una zona de trabajo, se monitorizará la posición de la herramienta, montada sobre el último eje del robot, mediante objetivos de laser tracker. La frecuencia de monitorización de la posición será de 1000 Hz, permitiendo conocer la posición exacta en la que se encuentra la herramienta 1000 veces por segundo.
Durante el proyecto Megarob se ha desarrollado un sistema de control que permite recalcular la cinemática inversa del robot a dicha frecuencia, y por tanto el robot corregirá su posición 1000 veces por segundo para intentar llevar la herramienta a su posición programada.
Con esta implementación el sistema Megarob será capaz de realizar operaciones de fabricación y reparación, sobre piezas, molde y utillajes de más de 10 metros, mediante fresado, taladrado, lijado, recanteado, pulido, atornillado, soldadura, pintado e incluso verificación dimensional sobre piezas de los sectores descritos.
Es especialmente notable la ventaja que ofrece la posibilidad de realizar una verificación dimensional en tiempo real, no solo de la pieza, sino incluso de las trayectorias descritas por las herramientas. De esta forma, se asegura un chequeo 100% de las geometrías de las piezas procesadas, no habiendo posibilidad de defectos desde este punto de vista.
Corrección en tiempo real
La corrección de la posición en tiempo real pretende eliminar tanto los errores de posicionamiento intrínsecos del robot como los errores dinámicos del sistema. Por defecto, los robots industriales se caracterizan por tener una alta repetibilidad, pero una baja precisión absoluta. Esto significa que el robot tendrá un error de posicionamiento variable respecto a una base fija, que en cada momento dependerá de la posición y los ángulos adoptados por sus ejes. Además los robots industriales tienen una baja rigidez estructural, que impide absorber alteraciones derivadas de las fuerzas de corte. En procesos de fabricación, como el fresado, el taladrado, el recanteo o el pulido, requerirán que el robot soporte una serie de fuerzas, que además van a ser variables durante su ejecución, que en un diseño convencional basado en robots industriales provocarían una desviación de la posición del robot respecto de la trayectoria teórica programada (resultando una baja tolerancia dimensión y mala calidad superficial en el caso del fresado), generando además otros efectos adversos como posibles daños en el sistema, en la pieza de trabajo, reducción de la vida de las herramientas, entre otros. Esto derivaría en la generación de defectos sobre la pieza final, que además presentaría unas bajas tolerancias dimensionales.
En el caso de Megarob, la corrección en tiempo real se realiza a nivel de control de movimientos del robot. Un robot convencional controla su posición mediante la monitorización de la posición de sus articulaciones, generando una serie de errores acumulativos, al tener una máquina configurada a base de cinemática serie, que además se vería afectada de otros errores de la cadena cinemática derivada de los 3 ejes translacionales implementados en el puente grúa. La forma de solucionar el problema, que adopta Megarob, es el control de la posición absoluta de la herramienta del robot, que se puede conseguir monitorizando en tiempo real la posición de la misma y corregirla hasta la posición teórica. La compensación se realiza de forma continua, en bucle cerrado, con una frecuencia de 1 milisegundo, y aunque se realiza a nivel de los motores del robot, la variable de control es la posición cartesiana de la herramienta.
La validación de la funcionalidad de la monitorización y la corrección en tiempo real de la herramienta se ha realizado mediante la construcción de una celda prototipo en las instalaciones de CSEM, socio del proyecto.
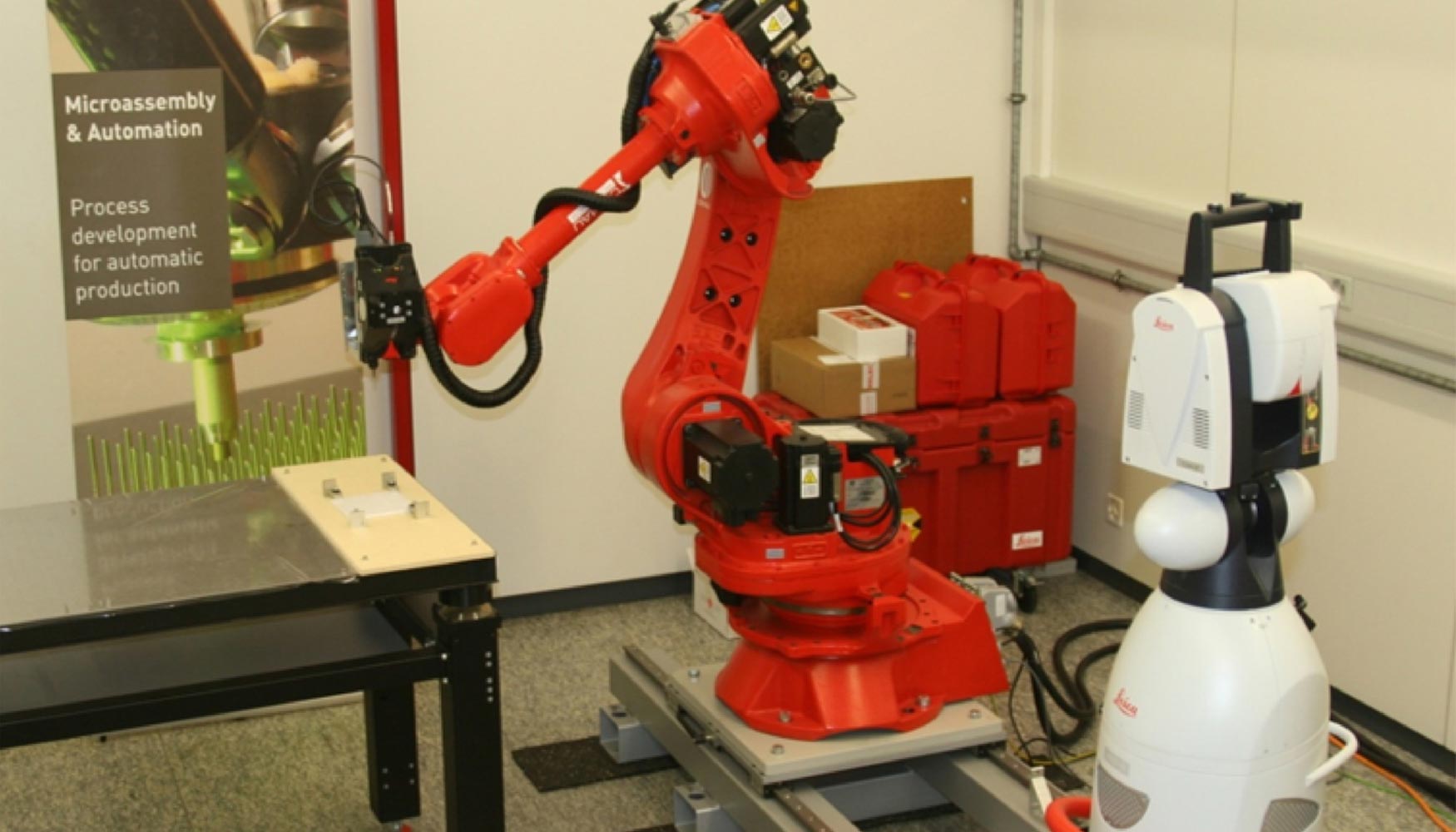
Todo el desarrollo realizado en esta línea para el proyecto Megarob ha permitido obtener altas precisiones en el posicionamiento de la herramienta.
Las siguientes imágenes ilustran los errores de posicionamiento del robot sin utilizar la compensación de la posición en tiempo real, y cómo mejoran drásticamente cuando se implementa dicha funcionalidad.
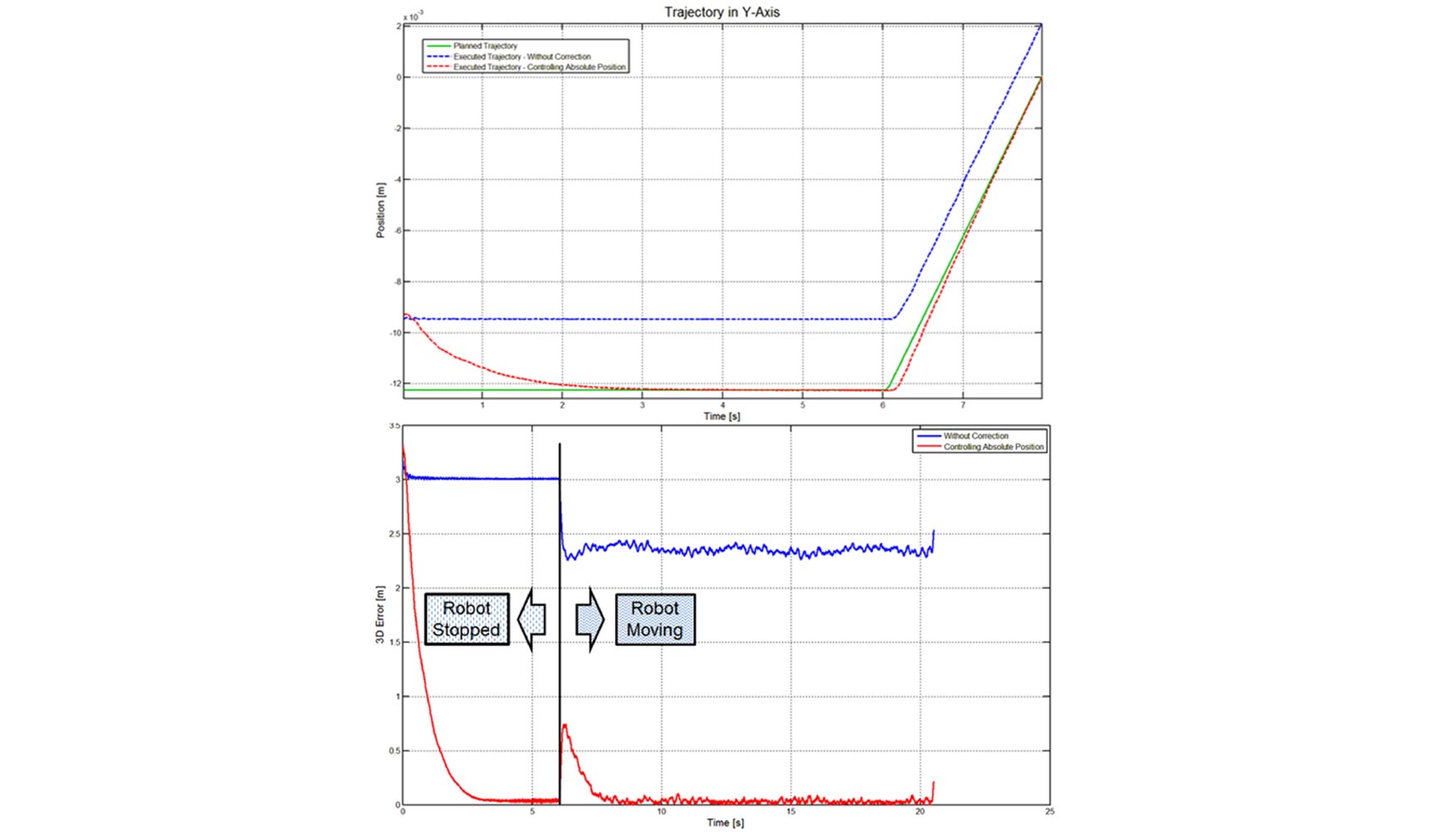
Como se observa en la imagen de la celda prototipo previa al desarrollo del demostrador final, el robot se ha integrado sobre un sistema de guía lineal, para poder implementar alteraciones externas, como las que generará el puente grúa en el sistema final. Dicha guía lineal está desconectada del controlador del robot, por lo que no se puede considerar como un eje integrado en el sistema robótico. Los movimientos lineales sobre dicho carro serán entendidos como perturbaciones externas al sistema. En la siguiente imagen se observa cómo el robot ejecuta movimientos lineales, con y sin compensación, cuando se introducen perturbaciones mediante el eje lineal.
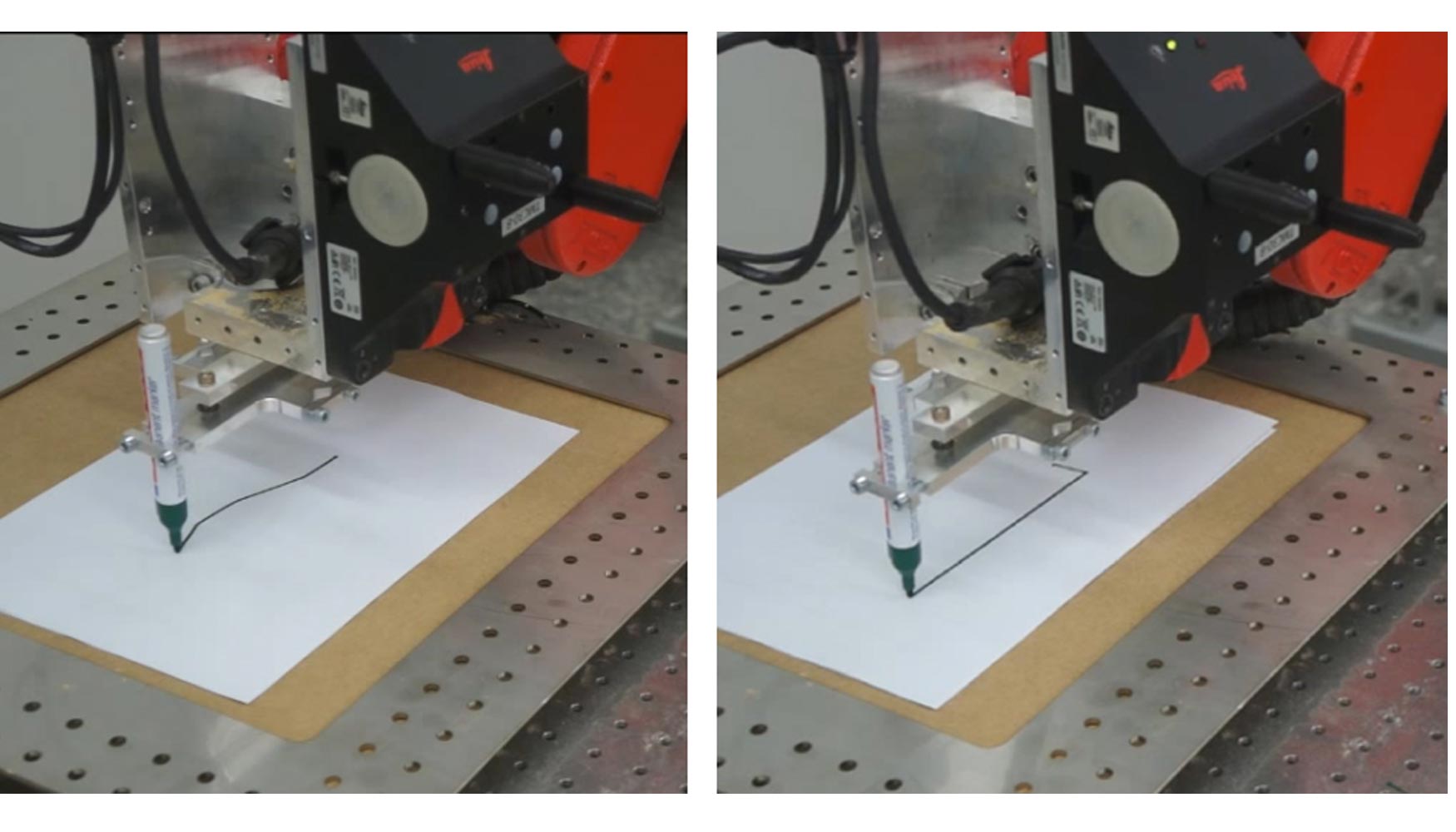
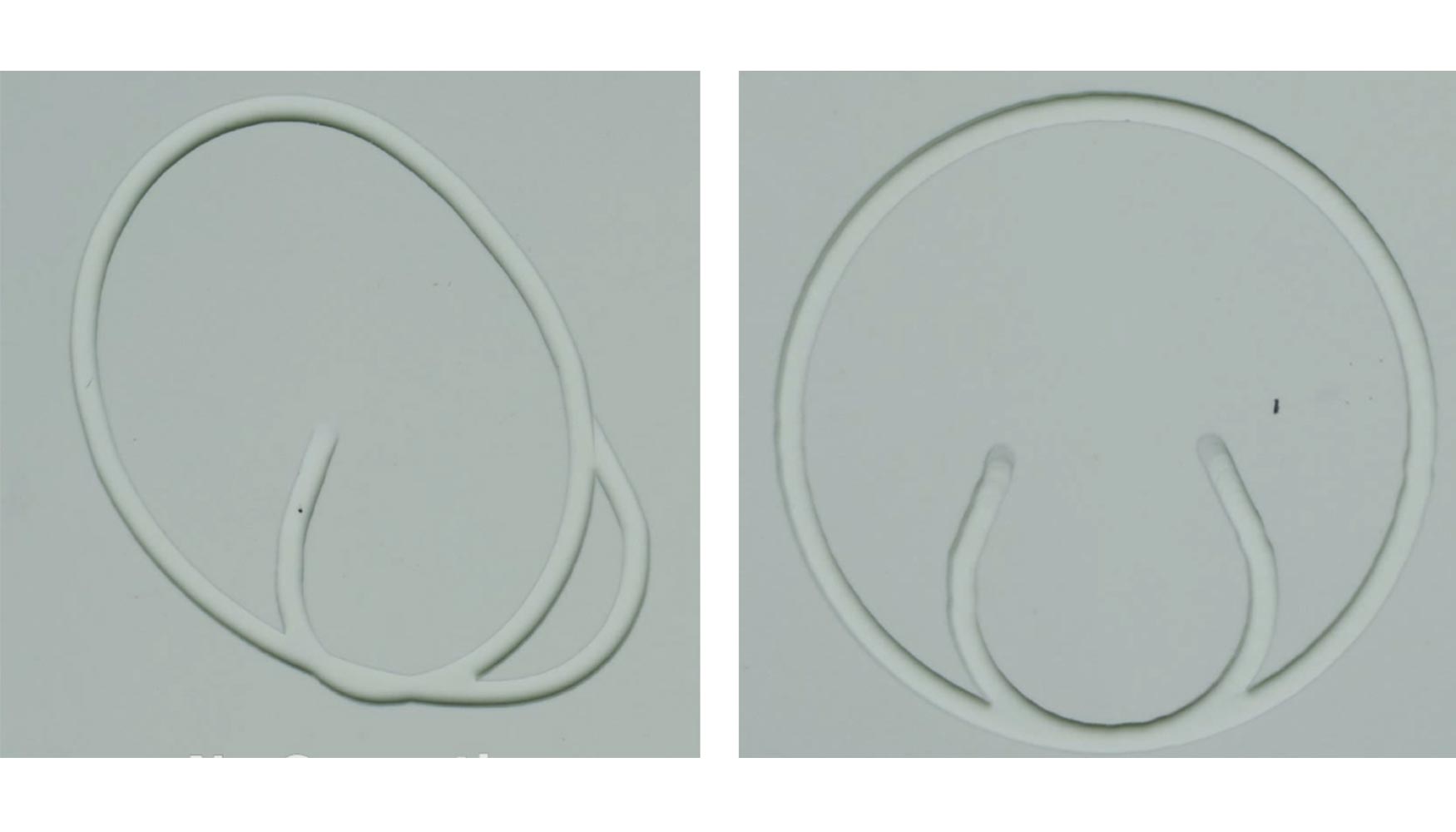
Demostrador Megarob a escala real
Todo el desarrollo realizado durante el proyecto Megarob se va a plasmar en la realización de un prototipo demostrador a escala real que se está implementado actualmente en las instalaciones de Aitiip Centro Tecnológico y va a estar a disposición de las empresas de forma totalmente funcional a partir de noviembre de 2015.
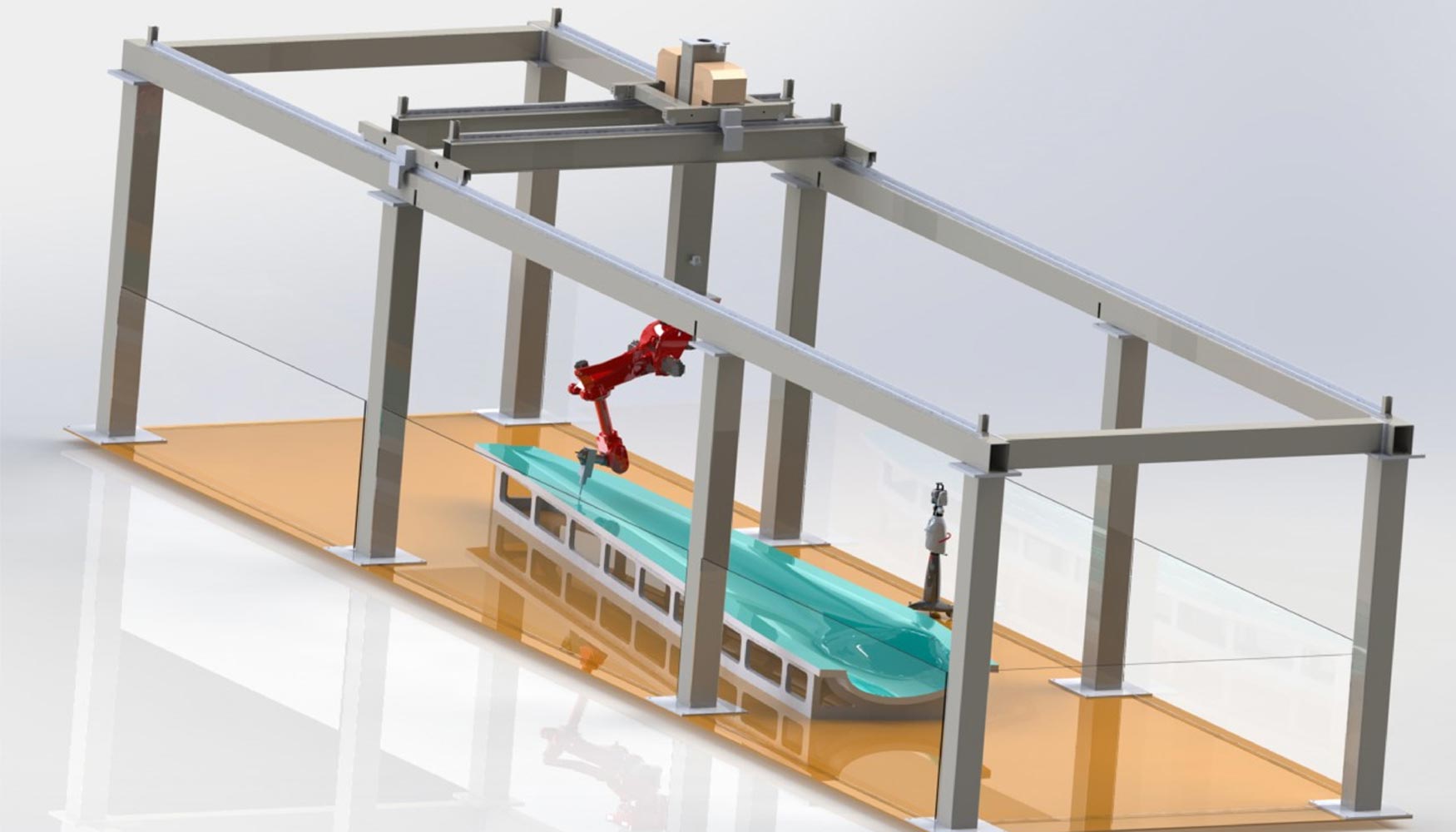
El sistema Megarob instalado en Aitiip Centro Tecnológico incluirá el sistema de programación basado en CAM para la programación automática de todos los movimientos, además de todo el sistema de control, incluyendo la monitorización en tiempo real, y la corrección de la posición de la herramienta.
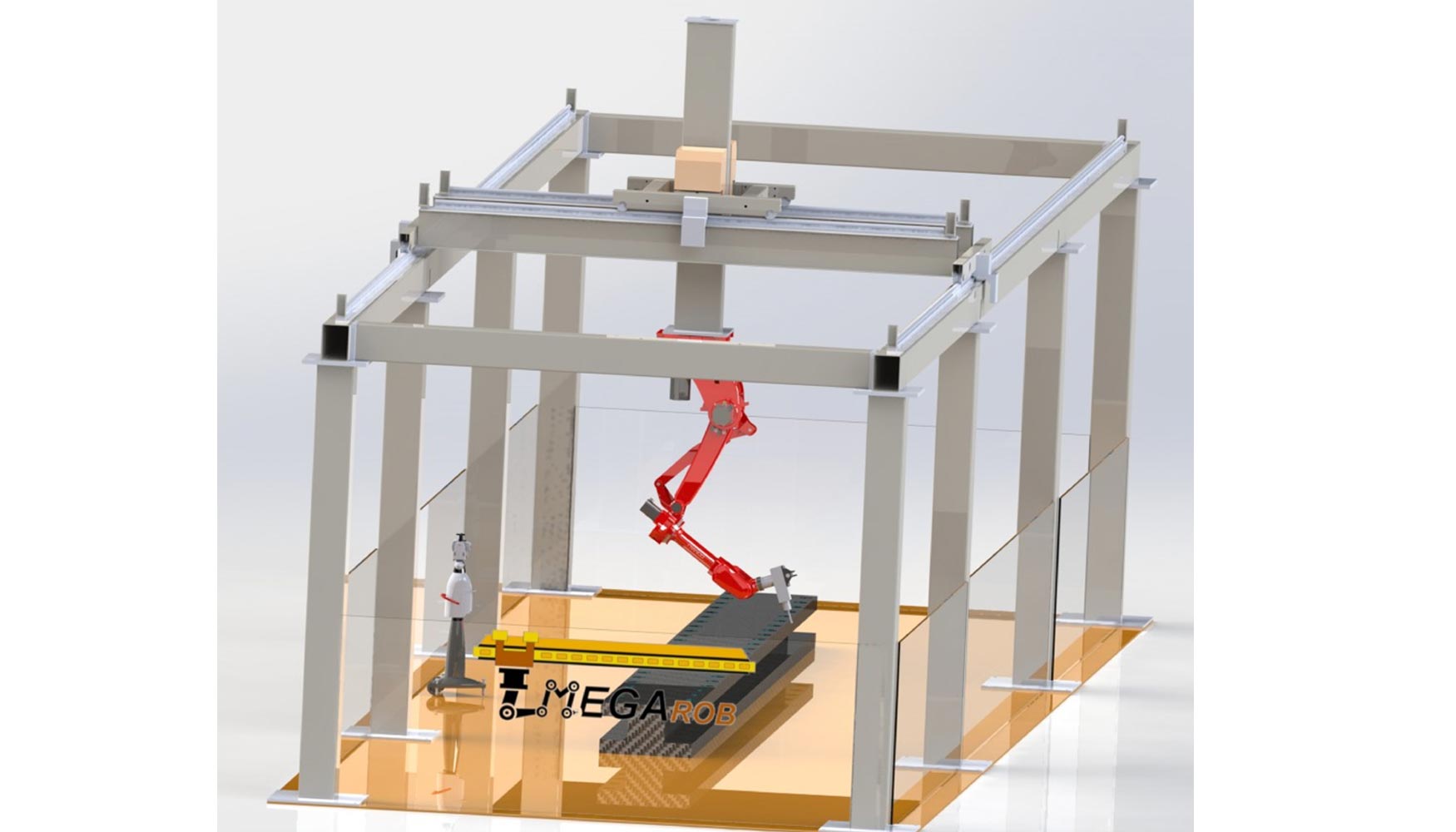
El área de trabajo de este prototipo será de 20 x 5 x 3 metros.
Previamente, durante la ejecución del proyecto Megarob se realizarán procesos de corte, fresado y taladrado sobre dos demostradores tecnológicos diferentes.
- Viga de material compuesto desarrollada y fabricada por Acciona Infraestructuras.
- Componente de material compuesto desarrollado y fabricado por Aitiip Centro Tecnológico.
El objetivo de la realización de estos dos demostradores es la validación de todas las funcionalidades fijadas para el sistema.