Design and tuned of a machine of cut by laser type portico multicabezal of big dynamic
Lazpiur S.A., in collaboration with
1. Introduction
One of the main advantages of the processes of cut by laser of fine sheets is the big speed of admissible advance [1]. Thus, the machines of cut by laser have to have some dynamic capacities the highest possible to take out benefit of this characteristic and do that the times of cycle of the pieces to manufacture are the smallest possible. Lazpiur S.A., in collaboration with IK4-Tekniker, has developed a machine of cut by laser of sheet.
So that a process of cut of sheet by means of laser was profitable, the times of cycle of the machine have to be very low what requires that the dynamics of the machine was especially high. The usual complex form of the pieces cut by means of this process does that the time of cycle was even more dependent of the dynamic capacities (acceleration and jerk) of the machine.
In this work reflect the steps followed for the design, manufacture and tuned of the machine. Initially, it defines the architecture of the machine and the dynamic conditions (speed, acceleration and jerk) to fulfil with the times of cycle required, with which will realizar a first design. Next, it will realizar a theoretical model based in finite elements that will allow to analyse the dynamic behaviour of the machine, facilitating the realisation of changes in the accionamientos and structure and analyse his effect. Finally, after the manufacture of the machine, will happen to a phase of put point in which it will verify that this fulfils with the requests established.
2. Design
Has opted by an architecture type portico for the design of the machine. To increase the productivity of the same go to use two porticos that will mount two cabezales of cutting each one (Figure 1). Like this, at the expense of a greater size of machine (roughly, 3 metres of route in X and 2 metres of length of portico) and the consistent reduction of his dynamic capacities, will be able to cut 4 sheets at the same time.
Have used linear motors for the generation of movement of all the axles of the machine. When avoiding the flexibilities and inertias of the husillos, attachments, axles, etc. the linear motors allow greater accelerations and positionings with a greater bandwidth [2].
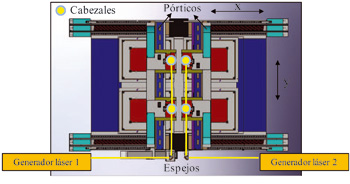
The time of cycle of each one of the pieces will depend on the dynamic limitations imposed: speed, acceleration and jerk maximum. The maximum speed is defined by the process of cutting and, in the clear-cut application, will be of 1 m•s-1. The maximum acceleration comes limited by the accionamiento, in this case the linear motors elected (Tecnotion TBW30 and TBW18), and the total mass to move. Because of the complexity of the geometries to cut in this type of machines, the jerk (derived of the acceleration in the time) has an important effect in the times of cycle. To a greater value of jerk will correspond him a lower time of cycle. However, a value high can give place to an excitation of the ways of vibration of the machine and a loss of precision in the geometry attained, by what the configuration of this parameter is important. The Table 1 sample the values predefinidos of acceleration and jerk in each axis.
The requests of high dynamics prevent the setting of the generator laser on the mobile parts of the machine and, therefore, has to be situated in the fixed part (bancada). For the transmission of the do laser from the generator (fixed part) to the cabezales (mobile parts) goes to use a system of reenvío by means of mirror. Of this way, a same generator laser can feed to the two cabezales of a same portico.
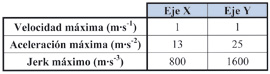
3. Theoretical model
With the bases presented in the previous section has realizar a first design of the machine of the that has developed a model of finite elements. The model indicates the existence of a way of flexión of the portico appears to 35 Hz (Figure 2) that goes to have a direct influence in the position of the do.
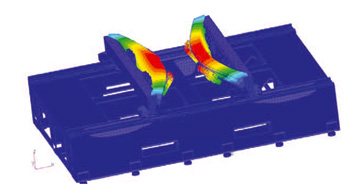
Next, has realizar a theoretical model of the machine, usually called ‘Virtual Machine', that groups the dynamics of the structure, obtained by means of the analysis FEM, and the part of control [3]. It has implemented the architecture of typical control of these applications, with a bow of speed (PI) and one of position (P). Like this application requires of an error of minimum follow-up so that the form of the pieces was acceptable implement so much the feedforward of speed as of acceleration. Entering the temporary signals generated using a program CAD/CAM and a simulator of CNC Fagor like input of the model can study the dynamic answer of the machine and verify that when applying the dynamic conditions (acceleration and jerk) predefinidas in each axis (Table 1), the geometrical precisions obtained are satisfactory.
4. Tuned
After the validation of the design proceeds to the manufacture and setting of the machine and to his back tuned. In this phase detect errors in the greater cut that the estimated in the theoretical model developed.
Firstly, observes that when substituting the cabezal laser by a tooling in which it mounts a rotulador the geometry achieved is considerably better, similar to the obtained in the theoretical model. Like this, it concludes that the system of mirrors for the detour of the laser is little rigid and does that the own do arrive to the cabezal with an oscillatory movement. This phenomenon has been foreseen since these elements had not been included in the model of finite elements. Fortunately, endow of a greater rigidity to this system results simple, deleting the swings.
In spite of having solved this problem, follow observing errors in the geometry of the piece although to an a lot lower scale (also observed in the theoretical model). In spite of reducing the dynamic restrictions of the axles and minimise, like this, the possibility to arouse the way of vibration of the portico, do not observe improvements. Analysing the profiles of acceleration of consign them generated by the numerical control for each axis observes that in a lot of points do not respect these dynamic restrictions (ladders of acceleration in the Figure 3.To that they do not respect the limit of jerk), arousing the ways of vibration of the machine. These points coincide with the instants in that the CNC has to generate a round of one of the multiple alive edges that have the pieces to cut. After testing different options to do the redondeos (circulate, parabolic, curves of Bezier…) and play with the parameters configurables does not achieve avoid that the dynamic restrictions are not exceeded. In fact, the problem to realizar transitions between segments to soften the paths does not have to to be totally dominated by the manufacturers of numerical controls and at present follow realizar works around this subject [4-5]. Deleted the suavización in the transitions, that is to say, tracing alive edges, observes that the dynamic behaviour is much better (Figure 3.b) And the quality of the pieces improves notably, going in inside the acceptable limits.
5. Conclusions and future lines
Has designed and manufactured a machine of cut by laser of sheet. Because of the high productivity demanded, has opted by an architecture type multipórtico in which 4 cabezales laser work of simultaneous way. This architecture, with a big length of portico, does that the machine was a system with a dynamics limited by what the correct selection of the dynamic restrictions (acceleration and jerk maximum) and of the configuration of the bows of control earns a big importance to obtain pieces of acceptable quality and inside the times of cycle required.
Before the manufacture and tuned of the machine has realizar a theoretical model in which engloban so much the structure of the machine like the control of the axles of movement to verify the dynamic behaviour of the same. The results obtained in the real machine agree with the obtained in this theoretical model. For future works suits to include in the theoretical model the system of detour of the do of the laser.
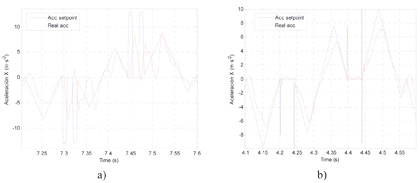
After the realisation of this work have seen several points with which could optimise the behaviour of the machine:
- Modify the system of transmission of the do laser to avoid the swings of the do caused by the vibrations of the mirrors (p. And. Optical fibre).
- Modify the strategies of round of alive edges to attain paths softer and fast (at present the machine detains in each alive edge).
- Application of systems axis on axis [6] that are especially contrived for this type of machines that combine long routes with high dynamic provision and/or big precision.
References
[1] N. Dahotre, S. Harimkar; Laser Fabrication and Machining of Materials, Springer, 2008.
[2] And. Altintas, To. Verl, C. Brecher, L. Uriarte, G. Pritschow; Machine Tool Feed Drives, CIRP Annals - Manufacturing Technology, v60-2, p 779–796, 2011.
[3] And. Altintas, C. Brecher, M. Weck, S. Witt; Virtual Machine Tool, CIRP Annals - Manufacturing Technology, v54-2, p 115–138, 2005.
[4] X. Beudaert, S. Lavernhe, C. Tournier; Feedrate interpolation with axis jerk constraints on 5-axis NURBS and G1 tool path, International Journal of Machine Tools and Manufacture, v57, p 73–82, 2012.
[5] S. J. Yutkowitz, Apparatus and Method for Smooth Cornering in to Motion Control System (SIEMENS), United States Patent – US 6922606 B1, 2005.
[6] M. Armendia, J. Madariaga, I. Ruiz of Argandoña; Axis On Axis System To Improve Machine Tool Productivity, 9th International High Speed Machining, March 2012.