Entrevista a David Costa, desarrollador de negocio de productos y gestor de soporte técnico de Pilz
Pilz ha presentado el sistema de comunicación estandarizado IO-Link Safety, disponible también para la seguridad funcional. David Costa, desarrollador de negocio de productos y gestor de soporte técnico de la compañía experta en automatización segura, detalla en esta entrevista las características del sistema y las ventajas que ofrece su integración.

¿Qué novedad supone el IO-Link Safety de Pilz para la automatización segura?
La principal ventaja que nos aporta el protocolo IO-Link radica en su independencia. Es una solución de comunicación independiente del fabricante y del bus de campo de seguridad utilizado por parte del controlador. IO-Link Safety está pensado para integrar sensores, actuadores y mecatrónica en cualquier sistema de automatización existente, independientemente del bus de campo utilizado, garantizando los más altos estándares de seguridad.
Asimismo, el crecimiento de IO-Link standard nos muestra que es un sistema ampliamente utilizado a nivel mundial, con un gran crecimiento año tras año.
¿Por qué motivo ha apostado Pilz por esta tecnología?
Dado el crecimiento constante del standard IO-Link, Pilz apuesta por un protocolo independiente, universal, que permita a nuestros clientes reducir tiempos de puesta en marcha, incrementando así la productividad y optimizando los procesos.
¿Cuál es la importancia de que se trate de un sistema de comunicación punto a punto y estandarizado?
IO-Link es la comunicación entre campo y control, a nivel más bajo. La estandarización de la conexión M12 5polos implica que tenemos una alta flexibilidad, independencia del controlador, y su protocolo aguas arriba y una gestión automática de la parametrización en caso de avería o sustitución.
¿Cómo contribuye a la mejora de la productividad y a la reducción de costes?
La simplicidad es la clave. Vivimos en un mundo donde la oferta del mercado es brutal, pero habitualmente implica adaptación o modificaciones. Cuando estamos en un standard como el IO-Link Safe, todo es mucho más fácil. Simplemente debemos cargar el fichero de descripción del dispositivo en el controlador y conectarlo. Toda la parametrización y configuración se hace desde el Máster IO-Link Safe y queda almacenada en él. Esto implica que, en caso de avería, el tiempo de máquina parada queda reducido enormemente.
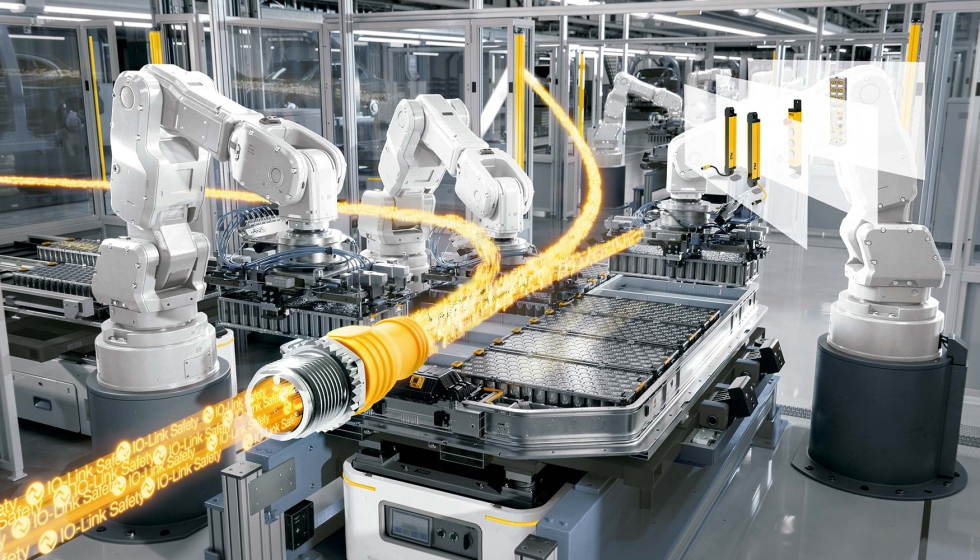
¿Qué otros beneficios destacables aporta?
Aparte de mantener la seguridad, el disponer de IO-Link implica tener un nivel de información relevante sobre el estado de los componentes y, por lo tanto, poder anticipar una posible avería o programar un mantenimiento antes de una parada de máquina. Además, el uso de conectores estandarizados y cables no apantallados abarata la solución.
¿En qué sectores industriales puede marcar la diferencia integrar IO-Link Safety?
IO-Link e IO-Link Safety tienen cabida en todos los sectores industriales, pero sobre todo en aquellas instalaciones donde el volumen de sensórica en campo sea elevado y su configuración compleja. IO-Link Safety lo simplifica.
¿Qué condiciones son necesarias para poder instalar el sistema?
Se requiere de un controlador Máster de IO-Link Safety compatible con el protocolo de comunicación de bus de campo del PLC de control de la máquina. Nada más.
¿Hay que tener formación específica para poder usarlo?
La integración de IO-Link Safety requiere de conocimientos sobre la configuración de un PLC Máster, algo que cualquier programador o integrador de automatización tiene. Simplemente se deberá complementar con conocimiento sobre seguridad industrial, al mismo nivel formativo que se requeriría para integrar seguridad en un sistema cableado convencional.