During the process of manufacture of a piece induce plastic deformations no homogéneas, contractions/thermal sensors dilatations and transformations of phase that comport the apparition of residual tensions
Prediction of distortions generated in the process of mechanised of a component of rolling
During the process of manufacture of a piece induce plastic deformations no homogéneas, contractions/thermal sensors dilatations and transformations of phase that comport to the apparition of residual tensions. These tensions are presents in the material in absence of external strengths due to the fact that it exists an internal balance of the same, that is to say, are car-balanced.
The majority of the pieces go through different processes of manufacture until obtaining the final product. Therefore, they are used to to have a record of residual tensions that goes modifying during the different processes, well because it applies them a thermal sensors cycle, well because it deletes material or by other causes.
The final tolerances that these pieces have to fulfil does very interesting the prediction of distortions that can cause the different processes. Of this form, is possible to apply preventive measures to the beginning of the cycle of development of the product controlling the times of process and reducing the risk to lose the quality of the product.
In the present work have studied the distortions that generate in the production of a component of a rail vehicle, specifically of a wheel of train (see figure 1). The first aim has been to know the real causes of the distortion that produces the fault of tolerances after the mechanised final. The second aim has been to pose possible alternative to these causes, that can go through change the strategies of mechanised, modify geometry of game, …
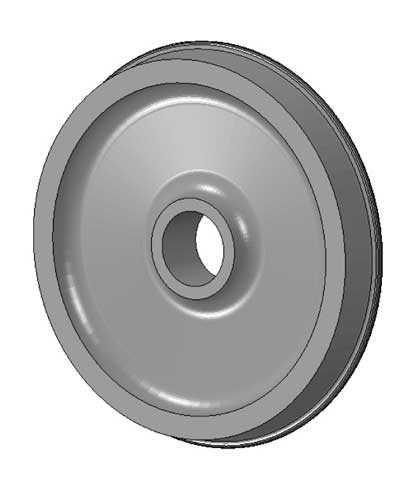
To obtain the final distortions after the final process of mechanised has to split of a state of previous residual tensions. In this case concrete, assumes that the residual tensions are practically generated by the thermal sensors treatment of temper previous under the hypothesis that the material is free of tensions at the end of the phase of warming.
Of this way, first has obtained the field of residual tensions simulating the process of temper. Afterwards it has simulated the process of mechanised using a methodology simplified based in the elimination of material. This elimination no only alters the microstructure but it also disturbs the balance of residual tensions of all the volume giving place to distortions so that they arrive again to car-balance.
1. Simulation of the process of manufacture
As it has commented previously, the simulation of the final distortions requires to take into account all the record water up. This involves the need to simulate all the influential important processes in his state of residual tensions. All the simulations have carried out using the software of finite elements Abaqus. When treating of a geometry of revolution, have used models axisimétricos in the different simulations realizar.
1.1. Process of manufacture
The process of manufacture of the wheel of train can resumir by means of the flow of diagrams showed in the figure 2. As it observes , his manufacture consists of four main phases in which they go creating and modifying the residual tensions.
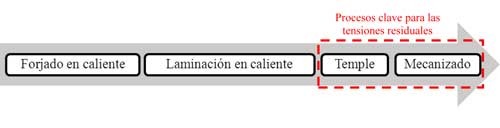
The process begins with the forged in hot where gives him a preforma to the initial block of steel. These preformas are laminados in hot to obtain the profile of the wheel as it observes in the figure 3to. Afterwards it gives him the temper by means of different streams of water in the extreme of the same with the aim to achieve the mechanical properties wished. This does that it was not possible to pose treatments of alivo of tensions. To finalise, realizar the mechanised final by means of turning with which attains the section of the figure 3b.
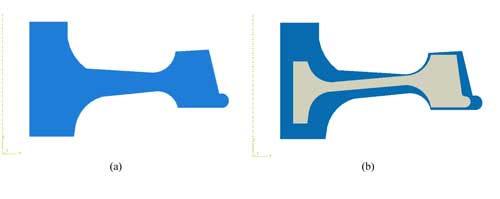
Can do the hypothesis that the main processes that influence in the final distortions are the temper and the mechanised since the tensions of forge and laminación are deleted to a large extent during the warming to the temperature of homogenisation. Basing in this, in the following sections explains in what consists the simulation of each one of them.
1.2. Simulation of the treatment of temper for the determination of the state of residual tensions initial
Under the hypothesis that the previous processes are despicable for the prediction of the distortions, has simulated the process of temper splitting by the geometry obtained after the laminación in hot (figure 3to). This geometry has been obtained by optical systems of measurement based in the triangulation of the do laser. Like this, it has obtained the section of the wheel after the laminación.
To know the tensional state after the temper, has carried out a simulation termo-mechanical decoupled.
In the first place, has realizar the thermal sensors simulation. The piece is cooled from the temperature of homogenised of temper. Like the temperate realizar by means of different streams of water, these have modelizado using several coefficients of convection in the different zones of the piece. Specifically, they have differentiated two zones as it can see in the figure 4. The coefficient h_1 used in the zone of rolling (red zone) is quite greater that the used in the other surfaces (h_2).
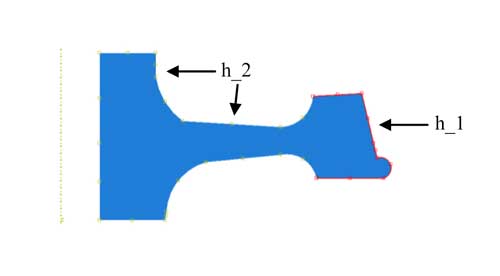
In the figure 5 can see the evolution of the temperature during the simulation of the temper. As it observes , the piece cools from the zone of rolling to inside. Like the cooling is not homogéneo the piece remains tensionada at the end of the process.
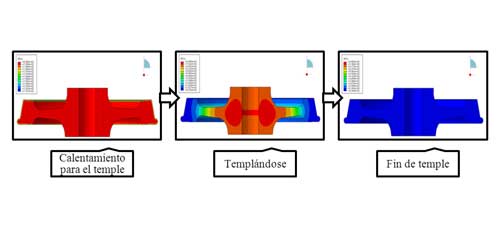
In this model, takes like input the field of transitory temperatures calculated in the previous analysis, and taking into account the mechanical properties of the material in function of the temperature, has obtained a state of residual tensions and corresponding final distortions to the process of temper. In the figure 6to observes the distortion that suffers the geometry laminada initial at the end of the temper. The main steering of contraction is the radial. Regarding the residual tensions, in the figure 6b can see the tangential tensions that remain in the piece at the end of the process. Regarding the magnitude of the same, observes that they are near to the elastic limit. Can see also that because of the process of temper specific, achieve induce residual tensions of compressesion in the zone of rolling, which are balanced by the tensions tractivas of the remaining piece.
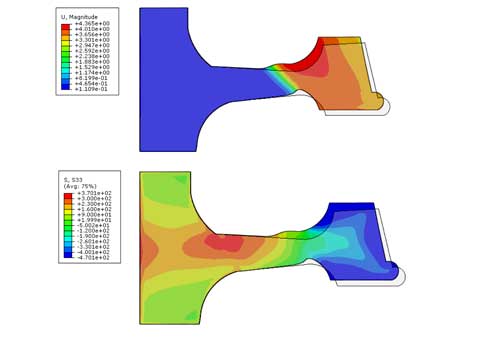
1.3. Simulation simplified of the process of mechanised
Splitting of the geometry and the state of residual tensions final of the process of temper, has realizar the mechanised of the piece with the end to obtain the final geometry required.
Can differentiate two levels of the simulation of the process of mechanised chord to the aim that wants to attain :
i. Simulations on a large scale (elimination of the material): modela the elimination of the material with the aim to predict the final distortions because of the redistribution of tensions that gives . In these models deletes the equivalent volume being able to take into account indirectly the strengths and warmings that produces the own process [1]. This elimination effects by means of the elimination of the corresponding elements to the volume deleted in each step.
ii. Simulations in a small way (learning of the shaving): they centre in simulating the learning of the shaving being able to analyse the strengths of cut, tensions, temperatures, wears, … but always to a very local level.
Since the final aim is the prediction of the distortions, in this case has carried out a simulation on a large scale, assuming the hypotheses that do in said method. As it reports in the bibliography [2] - [3], the residual tensions caused by the learning of the shaving affect especially to the surface of the layer mechanised. In particular, the experimental results reported in [4] suggest that the residual tensions induced by the process of mechanised are limited to a region with a maximum depth of 150-200m. The effect of the mechanised in the basic material is practically invalid. Like the residual tensions induced by the previous processes distribute in all the material, is possible to consider the residual tensions of the mechanised like despicable. For this reason, the process of mechanised can see like a process of relaxation of tensions by the elimination of the material and change of rigidity of the section. This methodology of simulation of distortions by the mechanised explains more in detail in [4].
As it observes in the figure 3b, all the corresponding material to the section coloreada in blue has to be deleted to obtain the final form. The elimination of this material can do in different sequences as long as they take into account the limitations that can have (limitations of the machine tool, accessibility of the tool, time of cycle, …) and the requests that have to fulfil regarding quality (superficial tolerances, geometrical tolerances, …).
When treating of a model axisimétrico, in each step deletes a corresponding disk to the clear-cut section. This approximation is correct due to the fact that in the turning of the piece the speeds of twist are the sufficiently elevated to despise the three-dimensional answer.
The current strategy of mechanised resume in the following operations (figure 7):
- Mechanised of the internal side of the ring
- Mechanised of the orifice of the cube
- Mechanised of the external side of the ring
- Mechanised of the external side of the cube
- Mechanised of the external side of the friso and of the surface of rolling
- Mechanised of the external side of the disk
- Mechanised of the internal side of the cube
- Mechanised of the internal side of the disk
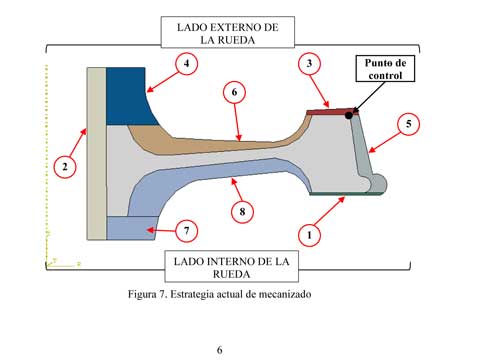
The volume to delete in each operation can discretizar in different commands for the simulation of the mechanised. First it has analysed the effect that has the degree of discretisation in the final distortions. For this, has simulated the current sequence of mechanised with two different densities as it can see in the figure 8. The sequence of the operations is the same that the explained up. With the discretisation 2, in addition to the sequence of operations, in each operation can consider the order in that it deletes the material. For example, in case of the operation 2 of mechanised of the orifice, the commands identified allow to take into account the side by where realizar the hole. Thus, in the discretisation 2 also has indicated the sequence been still in each operation.
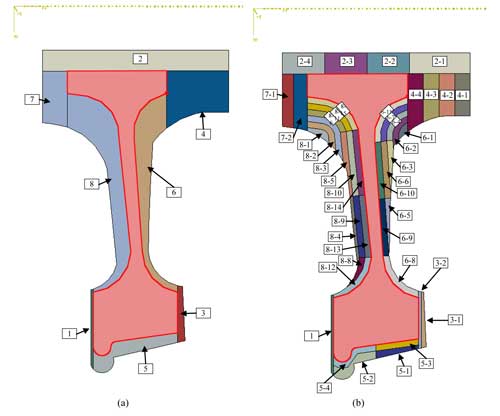
To see the effect of the discretisation, has taken like reference the axial trip of the checkpoint identified in the figure 7. In the graphic 1 can appreciate his effect. There is not too much difference between the two options except for the last step of the desamarre. In the desamarre of the piece gives the elastic recovery of the material. It sees that because of the discretisation, the redistribution of the tensions is not exactly the same and from here that the final distortions are a bit bigger for the case of the discretisation suffices. Nevertheless, the dicretización suffices can consider like a good approximation.
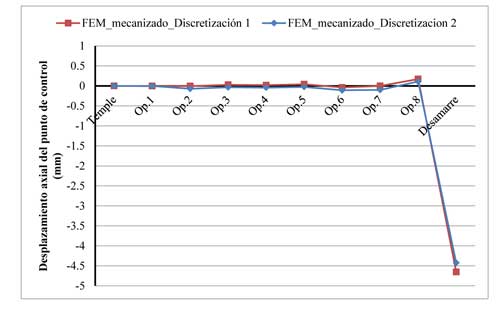
In the figure 8b can appreciate the section deformed at the end of the mechanised and in the figure 9to the redistribution of the axial tensions that has given by the process of mechanised for the corresponding model to the discretisation 2.
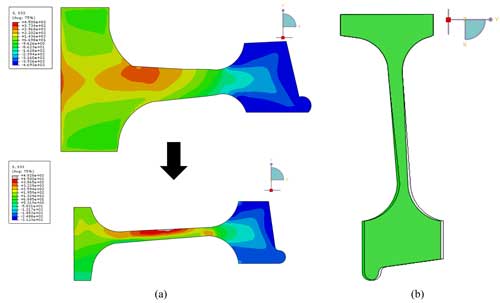
Once quantified the distortion that gives in the process current, the following step has been to pose different alternative of sequences of mechanised with the aim to diminish the distortion of the checkpoint.
Taking into account the limitations and specific requests, have analysed three different alternative. Each alternative describes in the figure 10. In each one of them, the volume of material deleted in each step has identified with two numbers indicated in the section of each volume. The first does reference to each operation and the second to the sequence that follows .
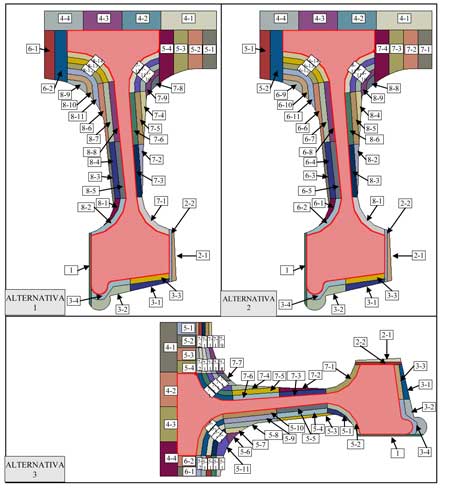
The discretisation of the alternatives 1 and 2 are identical to the discretisation 2 realizar in the previous point. In the alternative 1 changes the order of the basic operations described previously and in the alternative 2 changes the order of mechanised of the faces of the cube and of the disk with regard to the alternative 1. Finally, in the alternative 3 changes a bit the discretisation and also the order of the operations of mechanised in the cube and the disk.
To the equal that in the previous point, the comparison of the three alternatives has realizar in base to the axial deformation of the checkpoint. This comparison can see in the graphic 2. Also it has graficado the deformation of the current sequence to have like reference. As it appreciates , the effect of the sequence is remarkable in the distortion that suffers the checkpoint at the end of the process. By means of the alternative 1 achieves diminish the deformed final a bit but with the alternatives 2 and 3 the decrease is more accused (1 mm). This has to especially because the mechanised of the inner face of the disk does before that the one of the external face and also because both operations do from out to inside, that is to say, from the side of the zone of rolling to the axis of the wheel. Therefore, can say that these two operations are the most critical for the final distortions.
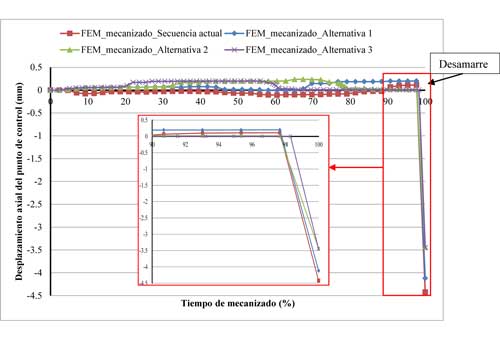
The difference of the deformed of the different alternatives can see in the figure 11.
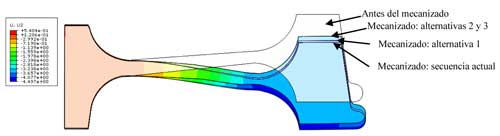
Apart from the final distortions, another appearance to consider is the state of residual tensions final that there is after the mechanised. As it observes in the figure 12, in the alternatives 2 and 3 in addition to achieving that the final distortions are lower, achieves also that the residual tensions are lower.
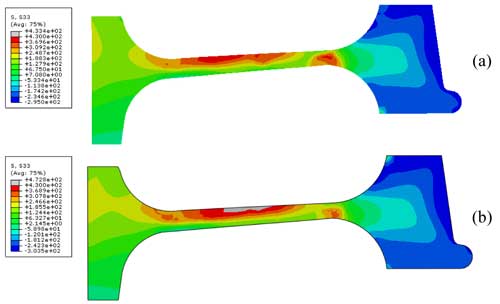
2. Conclusions
By means of this work has verified that it is feasible to realizar the simulation of the final distortions of a chain of processes of manufacture of a relatively simplified way.
Mainly has analysed the process of mechanised splitting of a tensional state induced practically by the process of temper. Of this way, has studied the effect that has the mechanised in the final distortions and also has showed that it can diminish this adverse effect playing with the sequences of mechanised. Besides, they have identified the most critical operations that have greater impact in the final distortion. Specifically, it has seen that it is recommended to mechanise before the inner face of the disk that the external face and in both cases the elimination of the material would owe to do from the zone of rolling to the axis of the wheel.
With all this, has verified that the methodology simplified used to simulate the process of mechanised is valid for the purpose of this study, not being necessary to use perfectionist models and computationally costly.
3. References
[1] J. K. Rai And P. Xirouchakis, ‘Finite element method based machining simulation environingingment for analyzing part errors induced during milling of thin-walled components', International Journal Of Machine Tools & Manufacture, 48, 629-643, 2007.
[2] T. Berruti And G. Ubertalli, ‘Influence of Cutting Parameters on Residual Stresses Induced by Milling in Pressesure Die-Cast Aluminum Alloy Components', J. Manu. Sci. Eng., vol. 123(4), pp. 547-551, 2001.
[3] P. Chevrier, B. Bolle, To. Tildu, P. Cezard And J. Tinnes, ‘Investigation of Surface Integrity in Highspeed End Milling of to Low Alloyed Steel', vol. 43, number 11, p. 113, 2003.
[4] M. Saint Sebastian, P. Alvarez and To. Echeverría, ‘New methodology applied to modelling machining distortion caused by stress relief', CIRP Conference 2009, 2009.
[5] DEFORM, ‘Computer simulationof the Machinig Process', 2002.
[6] D. Systemes, Abaqus Analysis User's Manual 6.12, 2012.
[7] T. D. Marusich, S. Usui, S. Lankalapalli And N. Saini, ‘Residual Stress Prediction for Part Distortion Modeling', 2006.
[8] V. Dattoma, M. Of Giorgi and R. Nobile, ‘On the evolution of welding residual stress after milling and cutting machining', 2006.
[9] K. Jacobus, R. DeVor And S. Kapoor, ‘Experimenting on the residual stresses generated by endmilling', Journal of Menufacturing Science and Engineering, vol. 123, number 4, pp. 748-753, 2001.