Arburg GmbH & Co. KG y Balluff GmbH fabrican aditivamente sensores industriales con formas individualizadas
Sensores impresos en 3D
La impresión 3D es cada vez más importante en la fabricación industrial. No solo hace posible producir formas muy complejas que de otro modo serían virtualmente imposibles de generar usando procesos convencionales, sino que también permite producir pequeños lotes de forma rentable. Sin embargo, hasta ahora, la integración de componentes electrónicos y, en consecuencia, la producción de sensores personalizados ha presentado un desafío. Ahora, junto con las empresas Arburg y Balluff con sede en Baden-Württemberg, Fraunhofer IPA ha logrado un gran avance.
Los sensores con forma individualizada son interesantes para tareas en la tecnología de automatización, ya que se pueden usar de manera flexible para una variedad de aplicaciones. Los sensores de proximidad inductivos están disponibles en carcasas de metal cilíndricas en las que se instalan una bobina, una placa de circuito y un enchufe en una configuración fija, un componente estándar con una geometría fija. En la tecnología de automatización, los sensores de proximidad inductivos se utilizan en gran número para la detección sin contacto de objetos metálicos. En aplicaciones industriales no solo pueden registrar la proximidad de un componente, sino también a qué distancia se encuentra. Sin embargo, debido a la forma de las carcasas, hasta ahora no se habían desarrollado sensores de proximidad inductivos para su integración en entornos específicos (por ejemplo, dedos de agarre de brazo robótico).
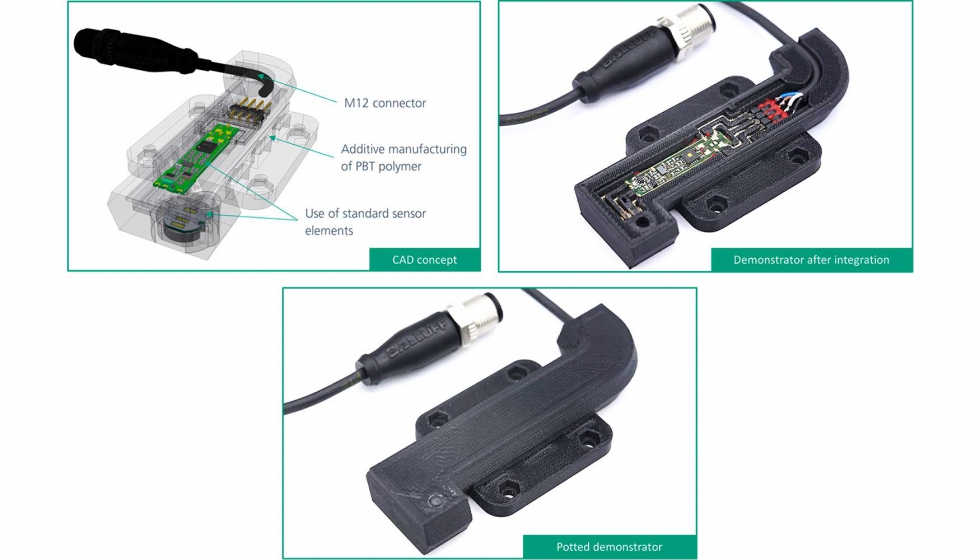
Modelo de demostración de sensor personalizado en diferentes etapas de producción: concepto CAD (arriba a la izquierda), después de la integración de los componentes electrónicos (arriba a la derecha) y como modelo de demostración terminado (abajo). Fuente: Fraunhofer IPA.
Una carcasa de cualquier forma
Entonces surgió la pregunta: ¿Por qué no imprimir la carcasa del sensor en plástico para que se pueda fabricar en cualquier forma? Esto es exactamente lo que ha logrado un equipo de investigación del Centro de Producción Aditiva del Instituto Fraunhofer de Ingeniería de Fabricación y Automatización IPA. El equipo contó con el apoyo de colegas del fabricante de máquinas de procesamiento de plásticos Arburg GmbH & Co. KG y del especialista en sensores y automatización Balluff GmbH. Se requería un plástico con alta rigidez dieléctrica y propiedades ignífugas para la carcasa del sensor. Los expertos optaron por el tereftalato de polibutileno (PBT) de plástico semicristalino, que se utiliza como material de moldeo por inyección estándar para la producción de carcasas electrónicas. Sin embargo, este tipo de material aún no se había utilizado para la impresión 3D, lo que requería un trabajo pionero
Pistas de conductor en impresión 3D
El plástico se introdujo en forma de granulado en un ‘freeformer’, el sistema de fabricación aditiva industrial de Arburg, que utiliza una unidad de preparación de material con un tornillo de plastificación especial. Después de fundir el granulado estándar, el proceso de formación libre, que no utiliza moldes, seguido: un cierre de boquilla de alta frecuencia descargó pequeñas gotas de plástico, que podrían colocarse con precisión con la ayuda de un portador de piezas móviles.
De esta manera, el freeformer creó componentes tridimensionales con cavidades capa por capa, en las que se podrían insertar componentes durante el proceso de impresión. Para hacer esto posible, el freeformer interrumpió automáticamente el proceso en cada capa respectiva, de modo que la bobina, la placa de circuito y el enchufe pudieran integrarse con mucha precisión. En un proceso separado, se utilizó un dispensador para producir las pistas conductoras de plata dentro de la carcasa. Para completar el proceso, todo lo que se necesitaba era sobreimprimir las cavidades y luego envolverlas en poliuretano.
El proyecto de investigación ‘Integración de funciones electrónicas en componentes fabricados aditivamente’ se llevó a cabo durante dieciocho meses. Stefan Pfeffer, que dirigió el proyecto en Fraunhofer IPA, está trabajando actualmente con Arburg en la investigación de cómo los plásticos conductores también se pueden utilizar en el futuro para aprovechar áreas de aplicación adicionales.