Para ello, la firma une sus conocimientos de big data con los mundos virtual y físico de MindSphere, su sistema operativo IoT basado en la nube
Siemens convertirá las plantas industriales en fábricas de datos con su gemelo digital
Gracias a los avances en algoritmos y tecnologías de simulación, Siemens es capaz de crear la mayoría de los productos en el mundo virtual gracias a los llamados ‘gemelos digitales’. Pero a medida que este proceso evoluciona, no sólo se pueden desarrollar las características geométricas de un objeto, sino también sus características funcionales, como los coeficientes de expansión y contracción o la resistencia al calor. Además, de su optimización de seguridad, que ya se está probando actualmente en el mundo virtual. Es más, según las estimaciones de Siemens, procesos de fabricación enteros están en camino de ser desarrollados, probados y optimizados de esta manera.
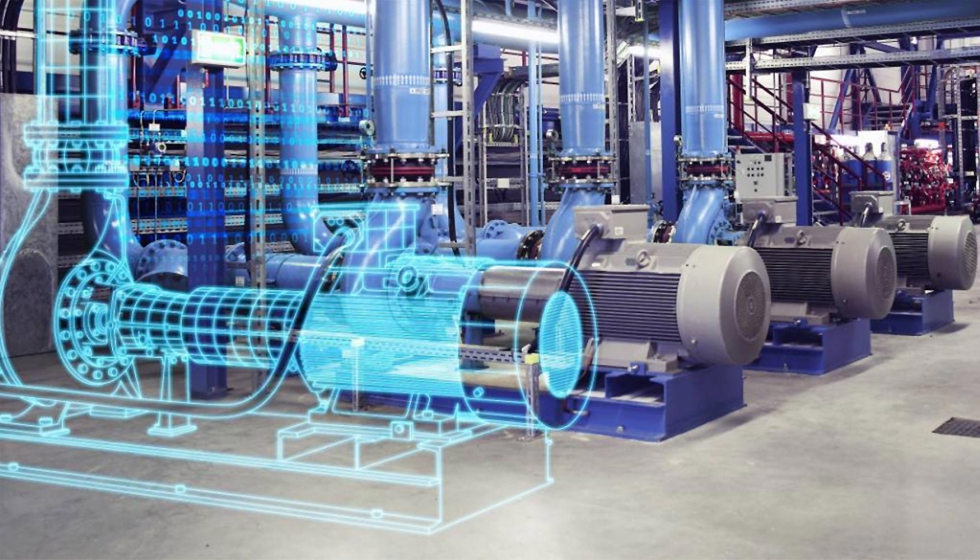
Los datos en el gemelo digital
Pero esto no termina aquí. Una vez que un objeto —desde una turbina de gas hasta una instalación de producción completa— se ha optimizado en el mundo virtual y su modelo físico ha sido construido, probado y operado en el mundo real, se abre una nueva dimensión en el mundo virtual: los datos del mundo físico pueden fluir hasta refinar y aumentar la precisión del gemelo digital original a través del ciclo de vida del producto. “El concepto de gemelo digital completa el ciclo del conocimiento desde el diseño y la prueba hasta la producción y operación, y de la adquisición y análisis de datos a un servicio mejorado, y vuelta a empezar”, explica el Dr. Norbert Gaus, jefe de Investigación en Digitalización y Automatización de Tecnología Corporativa de Siemens.
Esto permite que, por ejemplo en un futuro cercano, una vez que se haya creado un producto en el mundo virtual, sus datos serán transferidos sin interrupciones a instalaciones de producción donde los seres humanos, asistidos por robots semiautónomos, usarán métodos de fabricación substractivos aditivos y tradicionales para, automáticamente, traducir esos datos en objetos físicos. Además, a medida que se dan estos pasos de producción, se simularán en tiempo real, permitiendo así comparar modelos de comportamiento con el rendimiento real y poder así mejorar continuamente la calidad y el mantenimiento predictivo.
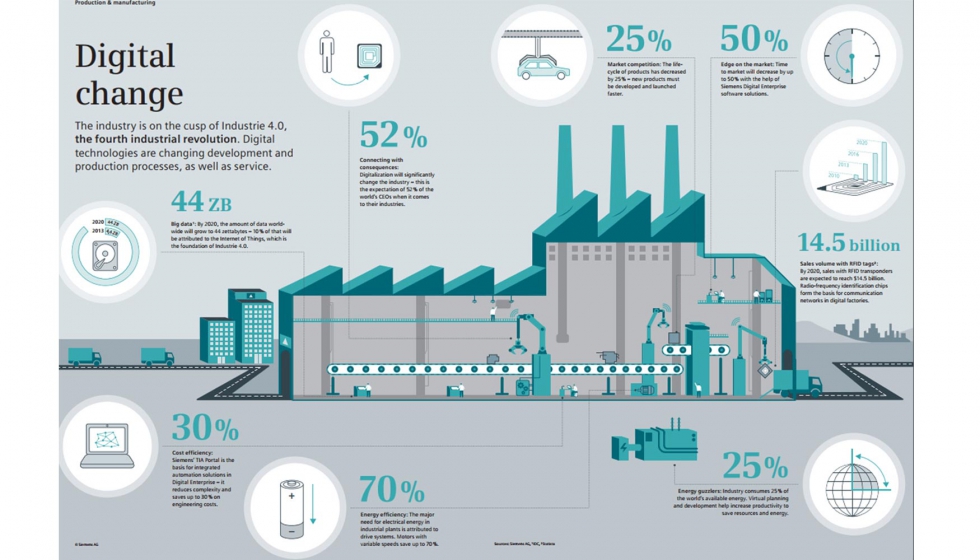
Flexibilidad automatizada
Dichas plantas de producción serán ciber-físicas, lo que significa que todos sus robots, máquinas y procesos funcionarán como un Internet de las Cosas auto-organizado y basado en la inteligencia artificial, que optimizará constantemente los flujos de materiales y energía dentro y entre las instalaciones de producción.
Un ejemplo del grado en el que la inteligencia artificial (AI) y las redes neuronales pueden optimizar un sistema complejo es su aplicación a una turbina de gas de Siemens. “Nuestro sistema de AI ha sido capaz de reducir las emisiones entre un 10% y un 15% adicional”, dice Gaus. “Este nuevo mundo de la fabricación abrirá la puerta a la producción de piezas asequibles y producidas individualmente, adaptadas a las demandas y requerimientos específicos de los clientes, así como al uso de materiales diseñados para aumentar la relación entre rendimiento y peso de piezas”, añade.
Por eso Siemens, a través de sus laboratorios de todo el mundo, continúa investigando y ya está generando prototipos de esta tecnología como soluciones de fabricación. Para ello, la compañía está fusionando sus conocimientos de big data con los mundos virtual y físico de MindSphere, su sistema operativo Internet of Things basado en la nube, con el objetivo de abrir el camino hacia los métodos de planificación digital (realidad virtual), de fabricación de aditivos, de software para sistemas robóticos o de nuevas tecnologías para los entornos de Industria 4.0.
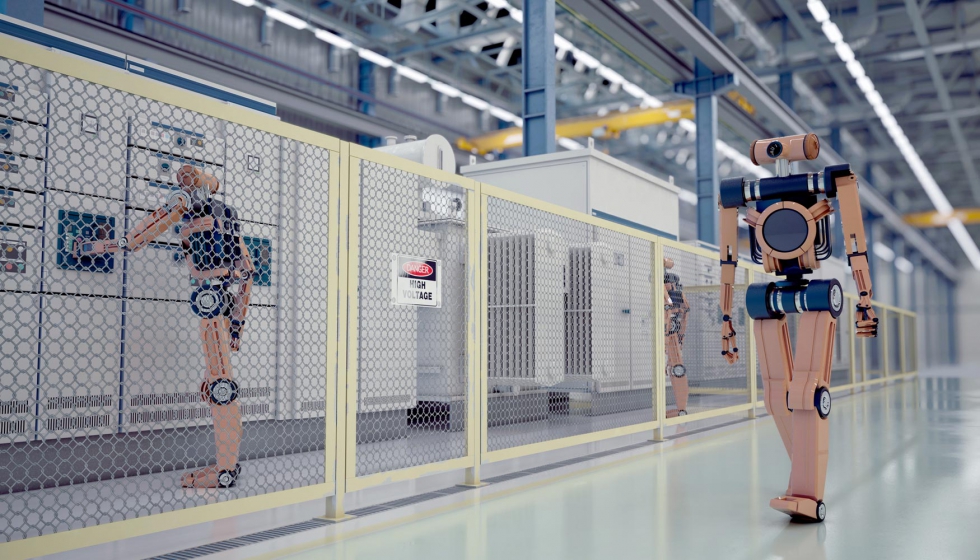
¿Qué es un gemelo digital?
Resumidamente, es un modelo virtual de un proceso, producto o servicio a través de la información obtenida de sensores o automatismos. Esta unión del mundo físico con el virtual permite el análisis inteligente de datos y la monitorización de sistemas para:
- Evitar problemas antes de que se produzcan
- Prevenir tiempos de inactividad
- Desarrollar nuevas oportunidades de negocio
- Planificar el futuro mediante simulaciones
- Personalizar la producción a los requerimientos del cliente
Este tipo de tecnología digital hace que empresas de todos los tamaños puedan cubrir sus demandas y conseguir reducir el time-to-market casi un 50%, mejorar la flexibilidad e incrementar la productividad en hasta un 20%, lo que determina la competitividad de las compañías.
¿Cómo funciona un gemelo digital?
Para poder entender cómo se genera un gemelo digital hay que incidir en la importancia de la información del mundo físico. Sin datos reales, no hay digital twin.
En primer lugar, los sensores recopilan datos sobre el estado del proceso, producto o servicio en tiempo real. Los componentes están conectados a un sistema basado en La Nube que recibe y procesa toda la información obtenida. Esta entrada analiza y compara todo lo obtenido junto con otros parámetros contextuales.
Una vez se obtiene el análisis del proceso, se puede generar de manera virtual el proceso, producto o servicio y dotarlo de todas aquellos cambios antes de ponerlo en fabricación. Solamente cuando virtualmente se consigue satisfacer los requisitos de un proyecto, se produce físicamente.
Aplicaciones y ventajas del gemelo digital
La prevención de fallos de las máquinas es una de las ventajas más obvias y, potencialmente, transformadoras que el gemelo digital podría tener en la industria. Pero, sus aplicaciones pueden ser aprovechadas por otros sectores como el energético.
Gracias al análisis y simulación virtual, las empresas podrían ahorrar un 70% de energía lo que repercutiría en una reducción de costes tanto para el productor como para el consumidor final.