La exactitud de los encóderes angulares
Las distintas aplicaciones demandan diferentes combinaciones de características y rendimiento para optimizar su función, algunas requieren precisión, otras repetibilidad, alta resolución o errores cíclicos reducidos para el control del bucle de velocidad. Generalmente, se selecciona el encóder que ofrece un equilibrio entre sus especificaciones y la función a la que va destinado; y hay una increíble variedad para elegir. Sin embargo, sólo unos pocos cumplen todos los requisitos.
El control del movimiento de precisión no puede depender sólo de la exactitud. La respuesta dinámica del sistema es igualmente importante. Es importante medir la posición con exactitud, pero el sistema no sirve para nada si no tiene la capacidad de posicionarse con exactitud. Los motores rotativos de transmisión directa (o motores de par) desarrollan un par elevado y activan el servocontrol de precisión para ángulos muy pequeños. Su respuesta dinámica es excelente porque la carga se acopla directamente a la transmisión, eliminando la necesidad de elementos de transmisión que introducirían holgura, histéresis, errores en los dientes de los engranajes o estiramiento de las correas. Los motores de par, sin bastidor y de gran diámetro interno no pueden acoplarse fácilmente al eje de un encóder. Los encóderes de anillo proporcionan una solución adecuada. Además, al igual que la carga, el encóder de anillo también se acopla rígidamente a la transmisión, eliminando cualquier holgura no deseada en el sistema. En cualquier sistema de medición o control, es preferible que el encóder esté tan cerca de la transmisión como sea posible. Esto ayuda a minimizar posibles resonancias que puedan influir en el rendimiento del servo, especialmente cuando aumente el ancho de banda.
Sea cual sea la aplicación, la retroalimentación directa y fiable de la posición es la clave...
Cuando se selecciona un encóder rotativo o angular, no es aconsejable optar por el de mayor exactitud, sin considerar la tasa de transferencia de datos, el tamaño del sistema, la complejidad y el coste. Hay disponibles encóderes con exactitud y resolución de decenas de nanómetros. Análogamente, los encóderes angulares pueden proporcionar un rendimiento por debajo del arcosegundo (un arcosegundo representa 1 micra en un radio de 206,25 mm).
A la hora de determinar la exactitud necesaria, es conveniente separar la precisión, la resolución y la repetibilidad:
- Para aplicaciones que requieran una elevada repetibilidad, (por ejemplo, un posicionador) la exactitud del ángulo de cada estación es secundaria en relación a la capacidad del sistema para detenerse siempre en la misma señal del encóder después de un tiempo.
- Para un movimiento continuo y suave, la resolución y precisión seleccionadas no deben permitir “fluctuaciones” del ancho de banda del servocontrol.
- Para un dispositivo de movimiento lento, como un telescopio astronómico, la medición angular precisa es más importante que la tasa máxima de transferencia de datos.
- Para el montaje de una cámara en un helicóptero, que requiera un posicionamiento manual preciso, la resolución es más importante que la repetibilidad o la exactitud absoluta; aunque esto último llegue a ser más importante si el mismo sensor proporciona los datos del objetivo para un sistema de armamento.
- En sistemas de alta velocidad, pueden surgir conflictos entre la velocidad y el intercambio de datos sobre la precisión del posicionamiento. Los sistemas de paso mayor (menos recuentos de línea) admiten una mayor tasa de transferencia de datos. Los sistemas de paso más fino (más recuentos de línea), sin embargo, proporcionan unos errores de interpolación menores.
Una vez que se han entendido los requisitos de precisión, la selección del encóder apropiado resulta mucho más fácil. A pesar de las afirmaciones de algunos fabricantes, la precisión en la medición rotativa raramente es una característica “plug & play”. Entender el error total es la clave para optimizar el rendimiento.
Determinación del error total
- Cada parte del sistema debe rotar en sus rodamientos sin desplazamiento radial (es decir, sin que haya movimiento lateral) de sus ejes de rotación.
- El sistema de eje que conecta el componente en cuestión al encóder debe ser rígido para impedir la torsión.
- El acoplamiento debe diseñarse de tal manera que el movimiento del encóder que rota en su rodamiento sea el mismo que el del componente en cuestión rotando sobre su propio sistema de rodamiento; es decir, se necesita una junta precisa de velocidad constante.
- Las distancias entre las líneas alrededor del borde de la escala del encóder deben ser uniformes, y la cabeza lectora debe interpolar entre ellas linealmente.
- La escala del encóder debe ser totalmente circular con el eje de rotación, y éste debe pasar perpendicularmente por su centro.
- La cabeza lectora debe leer la escala sin cometer error de paralaje u otro error geométrico, y debe estar rígidamente montada a un marco de referencia que no rote.
Si no se cumple alguno de los puntos citados más arriba, habrá discrepancias entre la posición angular del componente en cuestión y lo que indica el sistema de encóder. Investigando las posibles fuentes de error, pueden determinarse sus contribuciones individuales y el error total del sistema.
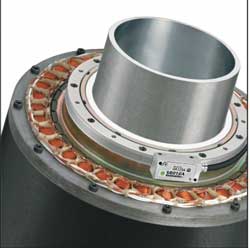
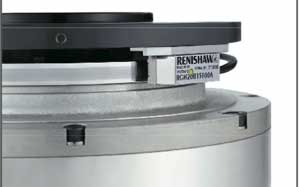
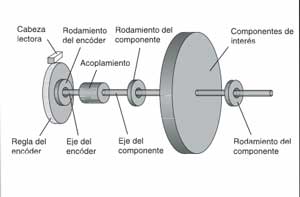
Fuentes de error
“Deslizamiento de rodamientos”
Errores de acoplamiento
El diseño del acoplamiento en sí puede tener una influencia significativa en la precisión del sistema, debido a las deficiencias causadas por ciertos factores como la holgura, la rigidez a la torsión y el error angular.
Efecto de la torsión del eje
Excentricidad de la regla y distorsión
Vaivén de la escala
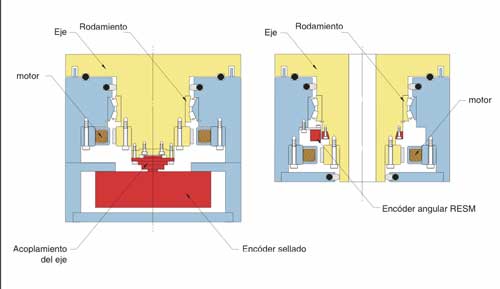
Errores provocados por la cabeza lectora
Error de subdivisión
Paralaje: Si la distancia entre la regla y la cabeza lectora cambia (debido a la excentricidad del anillo, a cambios de temperatura, etc.), se producirán errores, a menos que la cabeza lectora esté correctamente alineada con respecto a la línea central de la regla rotatoria. Si se ajusta la cabeza lectora, los cambios en la altura durante el desplazamiento producirán errores proporcionales al seno del ángulo de ajuste.
Estabilidad del montaje:
El sistema debe diseñarse de tal manera que la cabeza lectora no se mueva con respecto al eje de la regla de rotación, debido a los cambios de posición, carga, temperatura, vibración, etc.
Exactitud de la graduación de la regla
Si el encóder angular se extrajera y se volviera a montar sobre el mismo o diferente husillo, y se comprobara de nuevo la precisión con una cabeza lectora, el error registrado sería diferente. La diferencia correspondería al error provocado por el cambio en la excentricidad y ovalización de la regla del encóder angular, entre su instalación inicial para la graduación y su reinstalación para la utilización. El error total medido en este caso se denomina "Error instalado" y es la definición del error que más fielmente refleja el rendimiento conseguido por el usuario.
Por tanto, en resumen:
- Error de graduación = Error en el espaciado de las graduaciones durante la fabricación,
- Error del sistema = Error de graduación + SDE
- Error instalado = Error del sistema + Efectos de las diferencias en la instalación
Técnicas de compensación de errores
En la medida que lo primero exceda lo segundo, debe optarse entre elegir un sistema de encóder diferente con especificaciones mejores, si puede encontrarse alguno que cumpla con las dimensiones necesarias, el plazo de entrega y el presupuesto, y las técnicas de compensación de errores aplicables para satisfacer las deficiencias encontradas. Las dos técnicas de compensación más potentes hacen uso de múltiples cabezas lectoras y mapas de error.
Múltiples cabezas lectoras: Colocando dos cabezas lectoras diametralmente opuestas se eliminan los efectos de excentricidad, y los armónicos impares más altos del error repetitivo. Esto también elimina los efectos del deslizamiento de rodamientos de la medición angular, pero normalmente es necesario emplear un rodamiento con mejores especificaciones o cuatro cabezas lectoras para combatir el deslizamiento de rodamientos para obtener un posicionamiento angular más preciso. Incrementar el número de cabezas lectoras reducirá el futuro error repetitivo, pero normalmente se considera que las ventajas que pueden obtenerse se ven sobrepasadas por la complejidad y el coste que supone colocar más de 4 cabezas. Lo bueno de esta técnica es que no es necesario realizar una calibración para que sea eficaz; una gran ventaja en lo referente al tiempo y diseño del sistema de prueba.
Mapas de error: Si el sistema de control está así configurado, puede emplearse un mapa de error, bien con o en lugar de múltiples cabezas lectoras, para reducir los errores repetitivos.
Para que esta técnica sea eficaz, el fabricante del equipo original debe calibrar el sistema del encóder rotativo empleando un interferómetro, u otra referencia reconocida, después del montaje final del dispositivo.
No se puede confiar en ningún certificado de calibración proporcionado por el fabricante del encóder, porque se ignorarían los errores introducidos durante el proceso de instalación, haciendo que el mapa de error carezca de utilidad.
Merece la pena optimizar el número de puntos del mapa de error. Para un ciclo de error variable sinusoidalmente, tomar siete puntos por ciclo eliminan aproximadamente el 90 por ciento del error a esa frecuencia. Un mapa de error de cien puntos compensa, por tanto, la mayoría de los errores en los primeros catorce armónicos, pero debe tenerse en cuenta que puede incrementar potencialmente los errores provocados por los armónicos más altos restantes. Es evidente que esta técnica no tiene influencia sobre los efectos del deslizamiento de rodamientos, la torsión del eje u otras fuentes de error dependientes del tiempo.
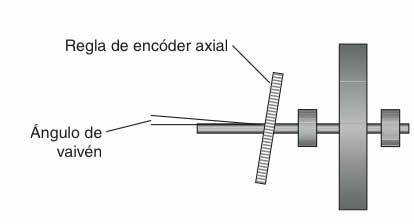
Funciones atractivas en los encóderes inteligentes Signum
Mediante un rendimiento a alta velocidad sin contacto combinado con funciones avanzadas como la marca de referencia óptica de fase automática In-Trac, la gama Signum redefine el rendimiento de los encóderes. El encóder angular óptico Resm se compone del anillo Resm, la cabeza lectora SR y la interfaz Si. El Resm es un anillo de acero inoxidable de una pieza, con una escala de 20 µm grabada directamente en la periferia. Dispone de una marca de referencia óptica In-Trac con repetición en ambas direcciones y velocidades de funcionamiento superiores 3.600 rpm (Ø52 mm) y hasta 85° C.
Los ejes giratorios de precisión de las máquinas herramienta requieren encóderes fiables y precisos para la retroalimentación de posición angular. El encóder de respuesta dinámica Resm proporciona una repetitividad del sistema que ningún otro encóder sellado puede alcanzar. Con una precisión a ±0,5 arcosegundos y una repetitividad a 0,02 arcosegundos, es perfecto para las aplicaciones de precisión más exigentes. Además, al formar parte de la gama Signum, el sistema de encóder Resm proporciona una calidad de señal excepcional, con un nivel de error de subdivisión más bajo que ningún otro encóder de su clase.
El Resm no sólo proporciona una precisión inigualable, sino que es, además, sumamente compacto y fácil de instalar. El anillo de bajo perfil se distribuye en una amplia gama de tamaños (Ø52 mm a Ø413 mm) y recuentos de línea, todos con un amplio diámetro interno que simplifica su integración. Este amplio diámetro interno facilita el paso de los cables y las conducciones neumáticas por la máquina, mientras que el montaje en cono patentado de Renishaw permite un ajuste activo que reduce los errores de instalación y facilita la integración. El encóder modular sin contacto Resm se ajusta firmemente al rotor de la máquina para evitar acoplamientos incorrectos, oscilaciones, torsión del eje y otros errores de histéresis que invaden los encóderes sellados. Además, las interfaces pueden colocarse a distancia y conectarse a la máquina mediante un pequeño conector en el cable de la cabeza lectora en los sistemas con acceso limitado.
Con un rendimiento a alta velocidad y elevada temperatura (hasta 85 ºC y más de 3.600 rpm), la cabeza lectora SR, sellada a la sonda IP64, permite una recuperación rápida en caso de salpicaduras de refrigerante o inmersiones cortas. Como todos los encóderes Renishaw, cuenta con una óptica de de filtrado exclusiva, que proporciona una inmunidad excepcional a la suciedad, agua, aceite, polvo y grasa. El Resm utiliza también el procesamiento de señales inteligente Signum, lo que garantiza una fiabilidad excelente y un error cíclico muy reducido (<±40 nm), asimismo, el completo software Signum permite realizar un reglaje óptimo y diagnósticos del sistema en tiempo real a través del puerto USB del PC.