Sensores inteligentes en la industria alimentaria
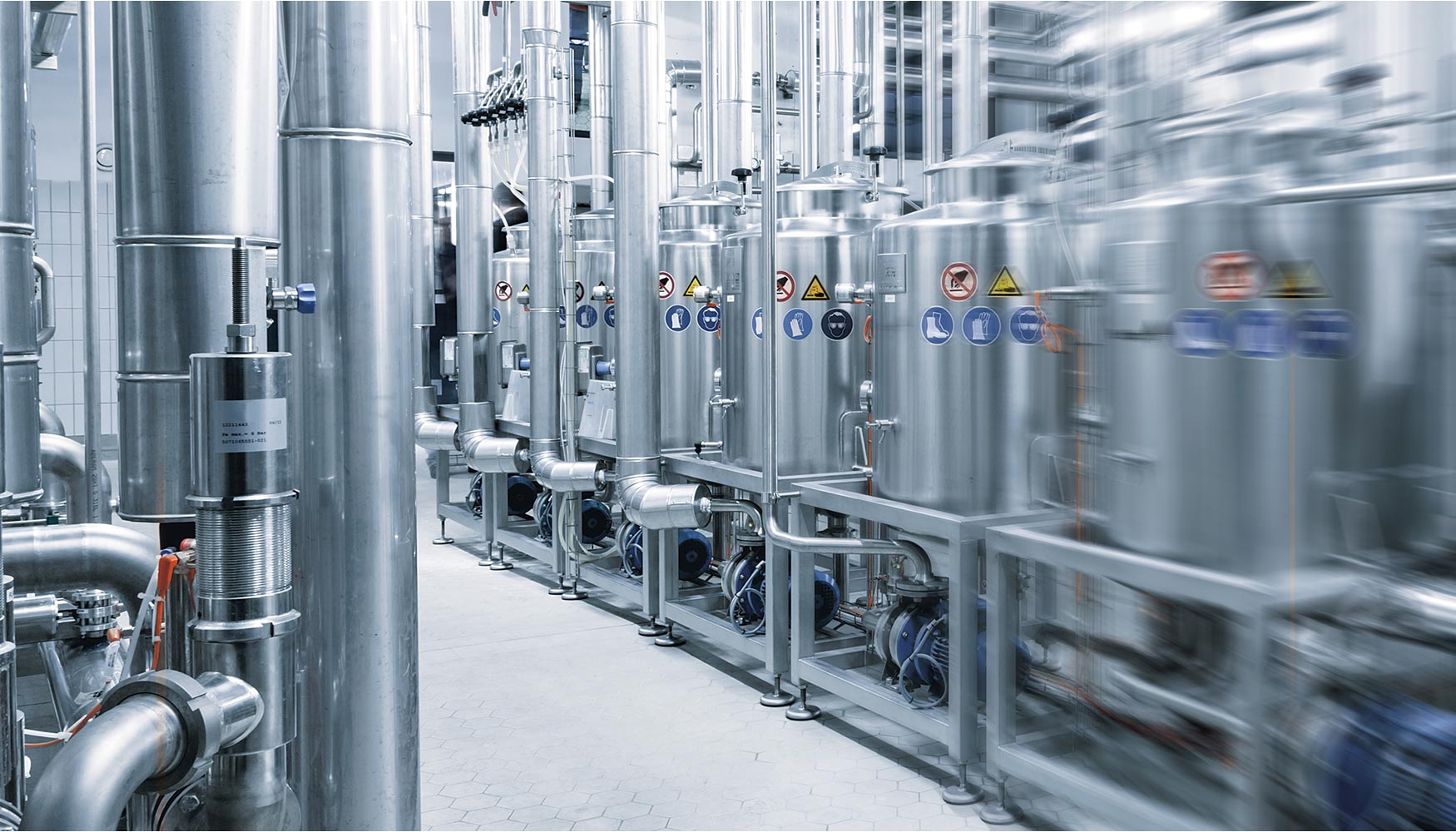
La automatización de procesos en la industria alimentaria requiere una gran cantidad de sensores. Los parámetros más importantes que se deben registrar son la presión, la temperatura, el caudal y el nivel. Las exigencias planteadas a estos sensores son muy parecidas a las requeridas en la industria general de procesos. El diseño aséptico es, sin embargo, en muchos casos imprescindible. Muchas aplicaciones también requieren la posibilidad de utilización en zonas potencialmente explosivas.
Sensores con valor añadido
Ifm, especialista en sensores, ofrece los equipos adecuados para muchas aplicaciones. Una gran parte de la gama de productos también está disponible en versión aséptica para la industria alimentaria. En todos sus proyectos de desarrollo, esta mediana empresa apuesta por los productos innovadores, para poder así ofrecer un valor añadido a sus clientes. Un ejemplo actual de este tipo de innovación es el sensor de nivel LR, equipo que funciona con la tecnología de ondas radar guiadas. El sensor se monta en vertical en el extremo superior del depósito y envía la señal de ondas hacia abajo a lo largo de la sonda. Cuando la onda alcanza la superficie del fluido, se refleja y es enviada de vuelta al sensor. A partir del tiempo de recorrido de la señal, el sensor determina la distancia con respecto a la superficie y, con ello, el nivel en el depósito. Este principio de medición evita al mismo tiempo dos de los problemas que pueden producirse durante la medición de nivel con otro tipo de sensores. Por una parte, el sensor no se ve afectado por residuos adheridos a la pared del depósito o a la sonda. Incluso con fluidos viscosos, la onda radar se propaga sin problemas a lo largo de la sonda aunque haya adherencias. La medición de nivel con fluidos que forman espuma en su superficie también plantea unos requisitos especiales. En estas aplicaciones, el sensor de nivel LR también detecta el nivel sin fallos. La señal de nivel afectada por la espuma es evaluada de forma segura por el sensor y la distancia con respecto a la superficie del fluido es detectada con fiabilidad.
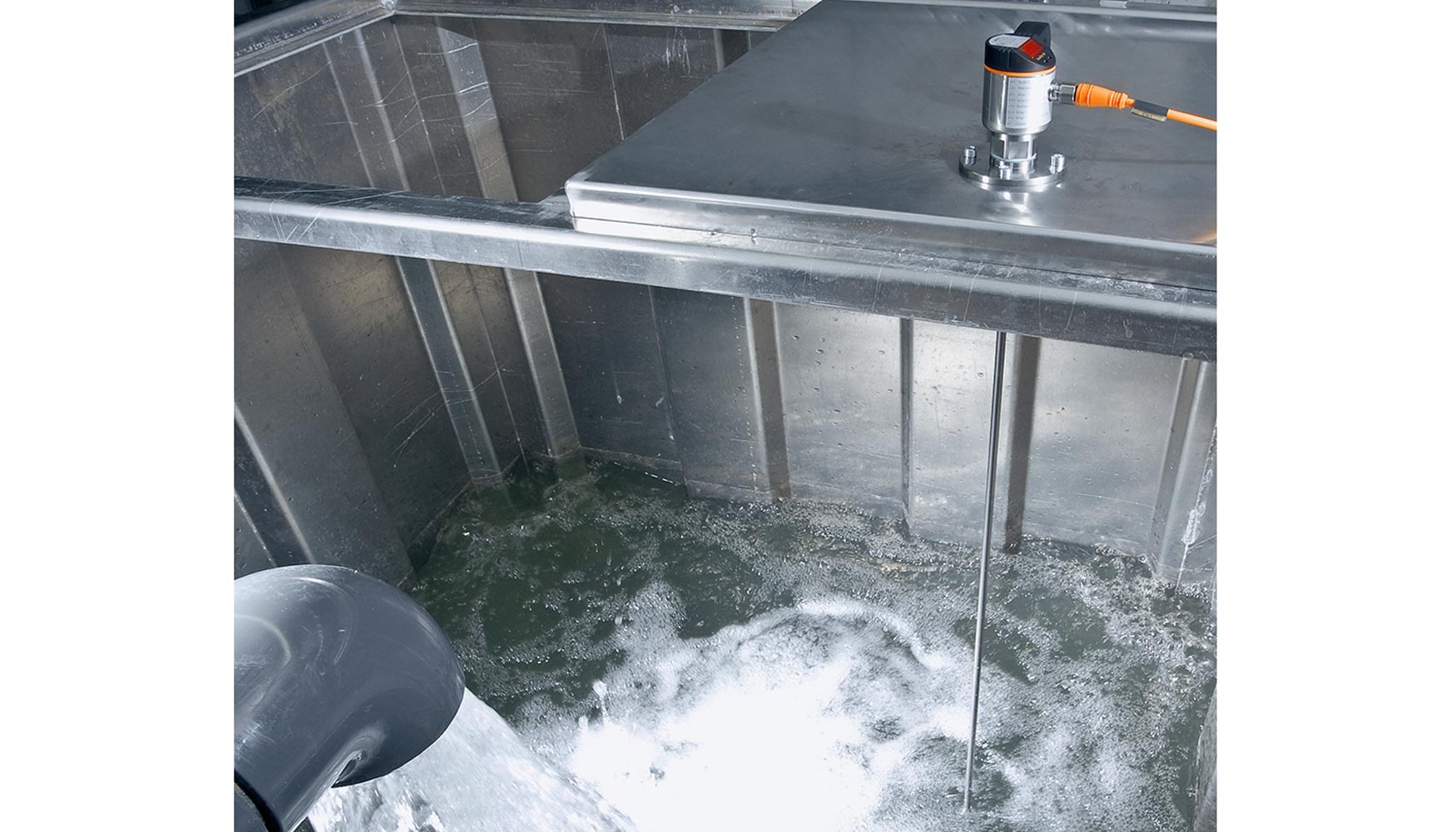
Los sensores de nivel LR de Ifm electronic funcionan con ondas radas guiadas, evitando así mediciones erróneas causadas por residuos adheridos o formación de espuma.
En la versión para la industria alimentaria, la sonda está compuesta por acero inoxidable. Todas las demás piezas del sensor tienen un diseño aséptico y cumplen los requisitos según EHEDG. El usuario puede cambiar fácilmente la sonda para adaptar el rango de medición. Ifm ofrece varillas en diferentes longitudes desde 150 mm hasta 2.000 mm. En caso necesario, el usuario también tiene la posibilidad de cortar la sonda según la longitud requerida. Este concepto modular ofrece mayor flexibilidad a los usuarios y disminuye los costes. Como todos los nuevos sensores de Ifm, el sensor de nivel LR también está disponible con interfaz IO-Link.
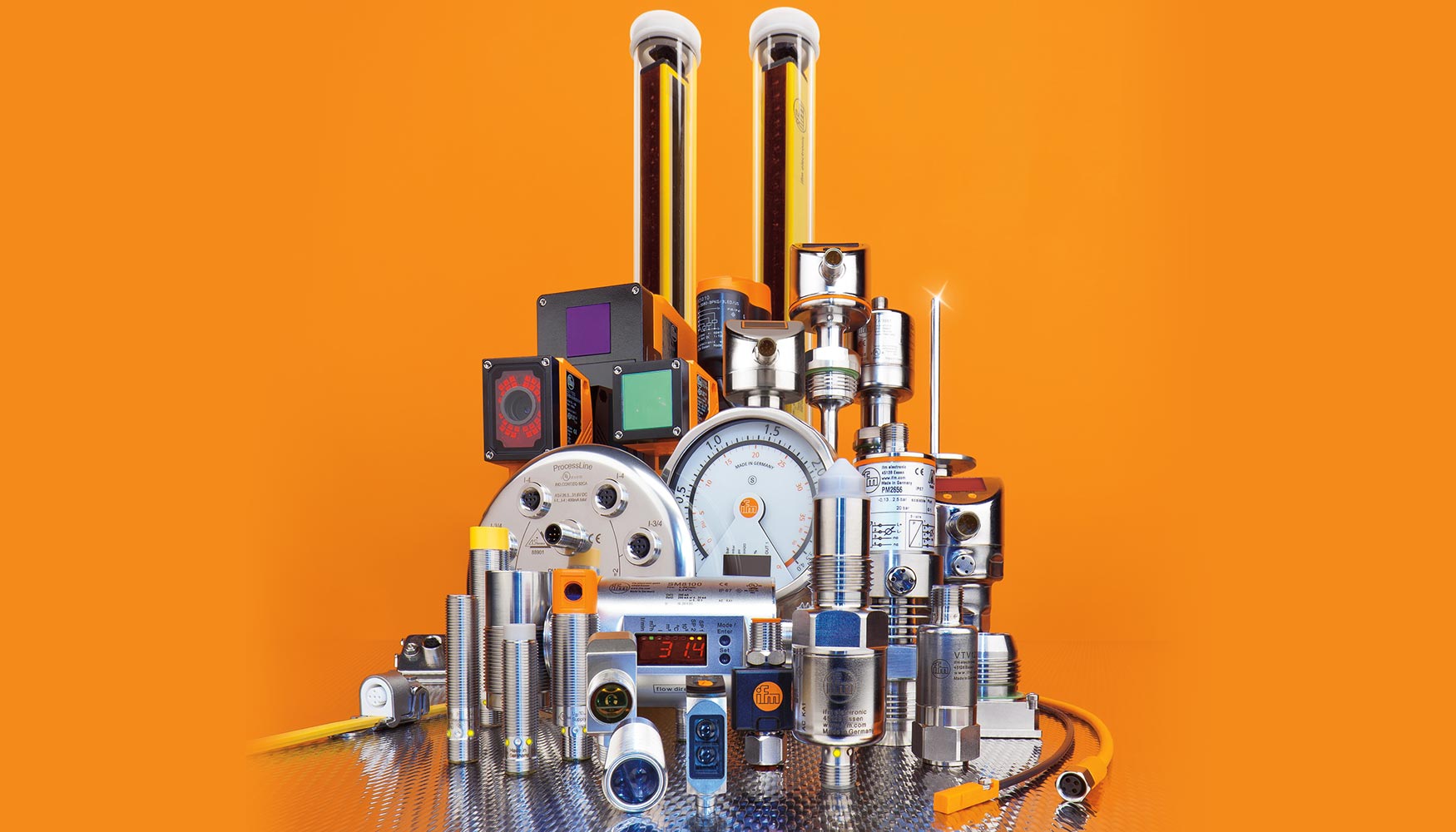
Numerosos sensores de Ifm son aptos para las aplicaciones de la industria alimentaria y cumplen los requisitos correspondientes para un diseño aséptico.
Comunicación a través de IO-Link
La comunicación cobra cada vez más importancia en la era de la Industria 4.0. La interacción con los sensores es el primer paso para garantizar la comunicación integral hasta el nivel de gestión empresarial. Ifm apuesta por IO-Link como interfaz en el nivel del sensor. Con este protocolo digital se completan las interfaces analógicas convencionales, como por ejemplo 4...20 mA, en todos los nuevos sensores del fabricante. En comparación con la transmisión analógica, los valores de medición no se ven alterados por fallos en el cable. Asimismo también es posible transmitir simultáneamente diversas magnitudes de medición de un único sensor (véase cuadro), ofreciendo así al usuario otro valor añadido.
En lo que respecta a las operaciones de mantenimiento y reparación, el usuario también se beneficia de los sensores con interfaz IO-Link. En caso de sustitución de un equipo, la configuración de los sensores a través de IO-Link permite la transmisión directa de los parámetros al nuevo sensor. No es necesario realizar una compleja configuración del sensor en la aplicación. De esta forma, la producción se interrumpe durante un periodo muy breve. IO-Link también permite al usuario acceder a los datos de autodiagnóstico de los sensores, pudiendo encontrar rápidamente un sensor defectuoso. Así también se consigue aumentar la productividad de la instalación.

Transmisión de datos a un sistema ERP
Otro aspecto importante de la comunicación digital de los sensores es la posibilidad de utilizar los datos de los sensores adicionalmente para sistemas ERP del nivel superior de gestión empresarial. Para este tipo de tareas Ifm utiliza el denominado Linerecorder. El Linerecorder Agent Connectivity Port es, por ejemplo, una pasarela de software que permite la comunicación bidireccional entre una gran cantidad de diferentes interfaces. De esta manera se posibilita la comunicación entre, por un lado, los sistemas ERP y, por otro, los datos de los equipos del nivel de campo, de control y del nivel superior. El software Linerecorder Sensor permite la detección y transmisión de todos los datos específicos para sensores IO-Link. Los datos se pueden transmitir directamente al sistema ERP sin que el PLC de la solución de automatización se vea sobrecargado adicionalmente. Este recorrido directo de los datos de los sensores eludiendo el nivel de control es denominado en Ifm comunicación en Y, ya que los datos, emulando la grafía de dicha letra, llegan por un lado al PLC y por otro, alcanzan directamente al nivel superior de gestión. Esta solución ofrece posibilidades que son prácticamente inviables con sensores convencionales con interfaces analógicas. El registro de datos, el mantenimiento preventivo condicional y el aumento de la eficiencia energética son solo algunos ejemplos de ello.
Los sensores inteligentes son el futuro
Los sensores inteligentes ofrecen grandes ventajas en muchas aplicaciones de la industria alimentaria y contribuyen a la reducción de costes. Aunque actualmente todavía se siguen utilizando señales analógicas para muchas soluciones de automatización, cada vez se está extendiendo más el uso de sensores con interfaz IO-Link. El valor añadido que ofrecen estos sensores en diversos niveles convence a cada vez más clientes del cambio a la comunicación digital.
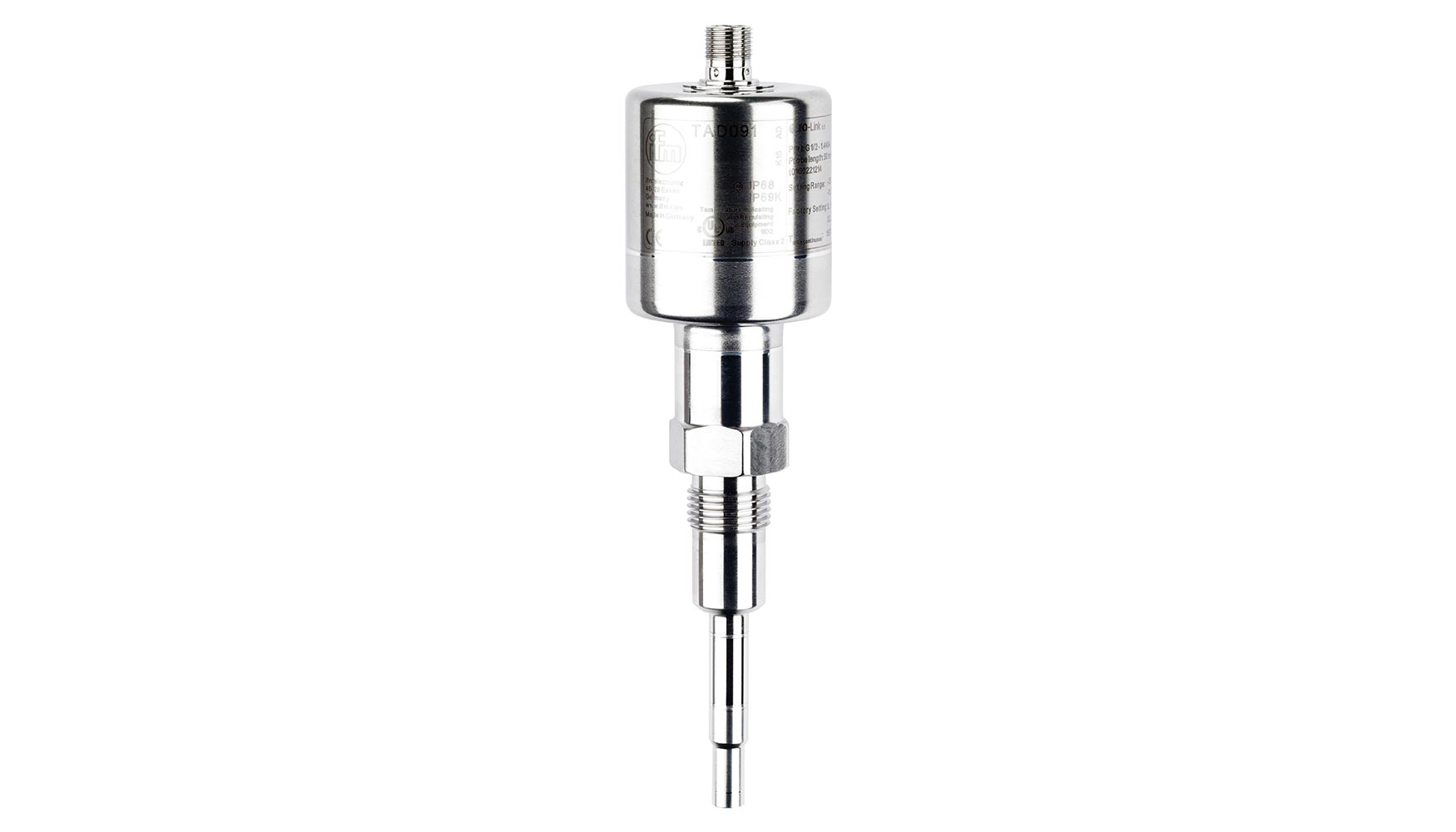
Medición de temperatura con valor añadido
Un ejemplo típico de sensor que ofrece un valor añadido al usuario es el sensor de temperatura TAD. Este equipo está provisto de dos elementos sensores distintos que funcionan independientemente el uno del otro. Ambos elementos sensores (un sensor Pt1000 y un termistor NTC) tienen parámetros de temperatura contrapuestos. Un microprocesador integrado en el sensor de temperatura evalúa las señales de ambos sensores y comprueba la plausibilidad del valor de temperatura medido. El resultado de la supervisión interna de derivas es transmitido por el TAD a una salida de diagnóstico por separado. Ambos valores de temperatura, el valor diferencial y el de diagnóstico también pueden ser transmitidos a través de IO-Link. Con este sensor ya no es necesario realizar la calibración periódica que suele estar establecida para los sensores de temperatura. Precisamente en la industria alimentaria, donde en algunos procesos es esencial el mantenimiento exacto de una determinada temperatura, se pueden ahorrar de esta manera los costes de una calibración externa.