MSP y Empire Cycles colaboran con Renishaw
Publirreportaje: Renishaw y MSP facilitan el mecanizado de piezas de 5 ejes
En MSP son especialistas en ingeniería avanzada. Han proporcionado ahorros de costes de producción valorados en millones de euros a fabricantes del sector aeroespacial de todo el mundo en los principales proyectos internacionales.
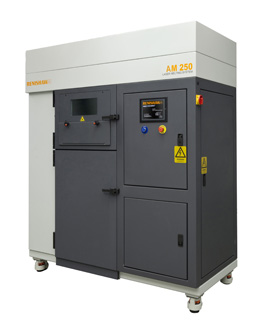
MSP ha desarrollado dos productos para facilitar la fabricación de piezas en 5 ejes. NC-Checker y NC-PerfectPart simplifican la tarea de trabajar con máquinas de 5 ejes y el centraje de piezas en 5 ejes. Empresas que desean incrementar su productividad y reducir los costes de los procesos de fabricación de piezas complejas tienen ahora una respuesta a algunas de las dificultades que generan este tipo de piezas. Además de trabajar con fabricantes Prime y Tier 1 del sector aeroespacial de todo el mundo, nuestra experiencia en procesos de mecanizado ha permitido extendernos rápidamente a otros sectores, especialmente a la industria de los composites, donde los sistemas de MSP están ampliamente extendidos, y a la fabricación a medida de piezas de Fórmula 1.
MSP ha trabajado con el fabricante de sistemas de defensa, BAE Systems, al que ha aportado un ahorro de 21 millones de libras* solamente en la fabricación una pieza del más avanzado caza militar que existe actualmente, el F35 II Lightening. (*durante la vida de la pieza).
El equipo de proyecto de BAE Systems se percató de que para solucionar los problemas de fabricación de la puerta del compartimento de tobera necesitaban ayuda especializada para una pieza tan compleja. MSP fue invitado a revisar el proyecto para buscar una salida satisfactoria. Se identificaron tres áreas de mejora 1) utillaje de amarre, 2) alineación de pieza y 3) mantener la calidad de la geometría de la máquina en un alto nivel.
El equipo de producción de BAE Systems diseñó un revolucionario utillaje para la pieza. Por su parte MSP implementó su sistema NC-PerfectPart para primeramente chequear la capacidad de la máquina antes de verificar que la alineación de la pieza estaba dentro de tolerancia. Todo simplemente con un toque de botón del operario.
La velocidad y precisión que conllevó este esfuerzo conjunto en la fabricación de la puerta del compartimento de tobera permitió ganar a los equipos de proyecto de BAE Systems y MSP el prestigioso premio BAE Systems Chairman’s GOLD Award de 2013, seleccionado entre otros 1.000 proyectos e innovaciones.
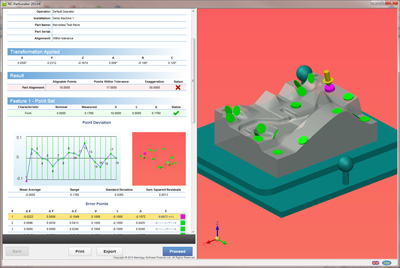
El primer cuadro metálico de bicicleta impreso en 3D fabricado por Renishaw para Empire Cycles
Renishaw, en colaboración con el fabricante de bicicletas Empire Cycles, ha creado el primer cuadro de bicicleta metálico impreso en 3D del mundo. El trabajo en equipo de Renishaw y Empire Cycles ha optimizado el diseño de las bicicletas para la fabricación por aportación de material, y ha conseguido crear un cuadro de titanio resistente y ligero mediante optimización topológica - el nuevo cuadro es un 33% más ligero que el original. El cuadro se ha fabricado por aportación de material con aleación de titanio por secciones posteriormente unidas. Este método aporta una serie de ventajas:
Libertad de diseño
- Rápidas iteraciones; flexibilidad para realizar mejoras de diseño inmediatamente antes de pasar a producción
- Posibilidad de crear formas mediante optimización topológica (véase a continuación)
- Fabricación exclusiva a medida: realización de tiradas limitadas con la misma facilidad que la fabricación en cadena
Construcción
- Formas complejas con refuerzos internos
- Estructuras huecas
- Características integradas, como el nombre del ciclista
Rendimiento, aleación de titanio
- El tubo vertical es un 44% más ligero que en la versión de aluminio
- Máxima resistencia: conforme a la norma EN 14766
- Resistente a la corrosión y larga duración