RTM en el sector de la automoción
La sustitución de piezas fabricadas con materiales convencionales por piezas fabricadas con materiales compuestos contribuye a la reducción del peso del vehículo, a una mayor eficiencia en el consumo del combustible y a una mejora en la relación entre potencia y peso del vehículo lo que se traduce en un mayor rendimiento del mismo. Históricamente, el uso de materiales compuestos en el sector de la automoción se ha visto limitado debido, fundamentalmente, a los tiempos de ciclo (capacidades de producción). Sin embargo, las nuevas normativas que afectan directamente a las emisiones de CO2 están impulsando el uso de materiales compuestos en este sector.
En la Unión Europea (EU), el transporte por carretera aporta aproximadamente una quinta parte de las emisiones totales de dióxido de carbono (CO2), principal causante del efecto invernadero. El transporte es el único sector importante en la UE, donde las emisiones de gases de efecto invernadero siguen aumentando; casi un 23% entre 1990 y 2010. La Comisión Europea ha puesto en marcha, siguiendo la estrategia que adoptó en 2007, un marco jurídico global para reducir las emisiones de CO2 de los nuevos vehículos ligeros como parte de los esfuerzos para garantizar que cumple con sus objetivos de reducción de emisiones de gases de efecto invernadero bajo el Protocolo de Kioto y más allá. La legislación establece objetivos vinculantes de emisiones para los coches y furgonetas. Para los coches, los fabricantes están obligados a garantizar que su parque de vehículos nuevos no emite más de un promedio de 130 gramos de CO2 por kilómetro (g CO2/km) en 2015 y esta cifra debe disminuir a 95 g CO2/km en 2020. Para furgonetas el objetivo obligatorio es de 175 g de CO2/km para 2017 y 147 g de CO2/km para el año 2020 1.
Una de las estrategias más efectivas cuando los fabricantes de vehículos se enfrentan al reto de reducir las emisiones de CO2 es la reducción del peso del vehículo donde los materiales compuestos juegan un papel fundamental. El moldeo por trasferencia de resina (RTM) es un proceso para la fabricación de composites que ha logrado una importancia relevante dentro de este sector ya que permite la obtención de piezas con un acabado ‘clase A’. En este proceso, el refuerzo de fibras se coloca en el interior de un molde. A continuación, el molde se cierra y se inyecta la resina. Después del curado, la pieza se desmoldea y se prepara para las siguientes fases de pintado. Este sistema de producción también permite la aplicación de un gel coat que constituirá la superficie cara vista de la pieza eliminando las fases posteriores de pintado. Los moldes empleados en este proceso pueden ser de distintos tipos, desde moldes de aluminio, acero o níquel de mayor coste hasta moldes de resina más económicos.
Nota:
1 ‘European Comission’ Climate. European Comission, Web. 12 Dec 2013. http://ec.europa.eu/clima/policies/transport/vehicles/index_en.htm
El proceso de RTM ha ido evolucionando a lo largo de los años con el objetivo de mejorar la calidad de las piezas y los tiempos de ciclo convencionales (entre 15-85 minutos 2). El equilibrio entre el tipo de resina de inyección, el diseño del molde y el proceso ha sido, y sigue siendo, fundamental para lograr este objetivo. En 1997, JHM Technologies, Inc. y Plastech en el Reino Unido desarrollaron lo que se conoce como Molde de RTM de ‘pieles’ intercambiables (MIT). Este método incorpora, en un mismo molde, múltiples caras idénticas (pieles) de bajo coste. Mientras que en la piel situada en el molde, se inyecta y se polimeriza la resina, otra piel puede ser utilizada en la fase de aplicación de gel coat y, a continuación, en la colocación del refuerzo de fibra. De este modo, los sistemas de pieles intercambiables contribuyen a la disminución en el tiempo de producción de una pieza.
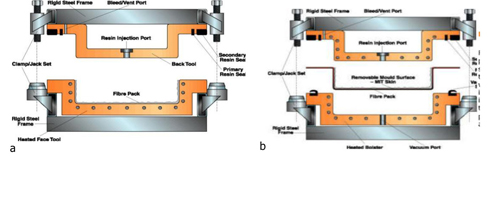
Actualmente, los principales agentes implicados en el proceso de producción mediante RTM (productores de materias primas, equipos, fabricantes de vehículo…) están trabajando en distintos sistemas con el fin de conseguir una disminución total de los tiempos de ciclo. Un ejemplo lo encontramos en el desarrollo que están llevando a cabo Momentive Specialty Chemicals’ (Columbus, Ohio) junto con Cannon (Boromeo, Italia) y KraussMaffei (Munich/Eppigen, Alemania) para BMW. En este, se han obtenido sistemas de resinas epoxi de cinco minutos de curado (se está trabajando en la obtención de ciclos de curado de dos minutos), que combinados con equipos de alta presión de inyección (hasta 200 bars de presión con ratios de inyección de 200 g/s) han logrado una disminución de los tiempos de ciclo. Por otra parte, Huntsman Polyurethanes (Everberg, Belgium) junto con Frimo (Lotte, Alemania), empresa especialista en la producción de piezas de RTM, ha desarrollado resinas de poliuretano de curado rápido que utilizadas con refuerzos de fibra constituyen una alternativa en el mercado de los materiales compuestos. Otra división de Huntsman, Huntsman Advance Materials, trabaja en lo que han denominado como Fast RTM, con presiones de inyección mayores de 15 bars. En este último caso, se han conseguido tiempos de ciclo entre 5,5 y 13 minutos, incluyendo los tiempos de colocación de la preforma en el molde, inyección, curado y desmoldeo. También se están realizando esfuerzos por parte de fabricantes de fibras que están desarrollando prepegs de curado rápido y fabricantes de equipos (prensas, equipos de inyección, robots) que mejoran sus equipos para lograr el objetivo común de reducción de los tiempos de ciclo 3.
Dentro de este marco, Aimplas trabaja, junto con otros 12 socios europeos, en el proyecto europeo Ecogel Cronos. El principal objetivo de este proyecto es el desarrollo de un sistema ecológico de RTM de alta productividad. Para ello, se va a trabajar fundamentalmente en dos aspectos;
- la formulación y fabricación de un gel coat en polvo de curado rápido que disminuirá la emisión de compuestos orgánicos volátiles en la planta de producción y
- el diseño y la construcción de moldes con sistemas intercambiables de ‘pieles’ reforzados con fibras de carbono y calefactados eléctricamente.
Notas:
2 Klaus, Ritter. ‘RTM advances facilitate mass production in the automotive market’. Reinforced Plastics. 30 Jul 201230 Jul 2012: n. page. Web. 12 Dec. 2013.
3 Sloan, Jeff. ‘Auto composites quest: One-minute cycle time?’. Composites World. 01 08 201201 08 201201 08 2012: n. page. Web. 12 Dec. 2013. http://www.compositesworld.com/articles/auto-composites-quest-one-minute-cycle-time.
La utilización de un gel coat permite la obtención de piezas totalmente acabadas sin necesidad de la aplicación de fases posteriores de pintado. La utilización de un gel coat en polvo presenta ventajas adicionales respecto a la utilización de los, empleados actualmente, gel coat líquidos. Entre estas ventajas cabe destacar la importante reducción de tiempos de ciclo (entre un 70 y un 88%), la posibilidad de reutilización del exceso de gel coat en polvo aplicado utilizando sistemas de aspiración de polvos, un mayor rendimiento efectivo en gramos por superficie de material aplicado (1:4), una mayor calidad de las piezas ya que se mejora la interfase gel coat – resina y una reducción de las emisiones de compuestos orgánicos volátiles en las plantas de producción.
El diseño y fabricación de un molde con ‘pieles’ intercambiables con una estructura de fibra de carbono que actúa como soporte pero también como elemento calefactor es otro de los retos del proyecto. La utilización de estos moldes asegura un calentamiento homogéneo de toda la pieza a la temperatura necesaria para la formación de la película de gel coat y con la calidad superficial requerida en el sector de la automoción ‘superficie Clase A’. Además, se prevé la utilización de preformas para mejorar drásticamente la velocidad de producción actual.
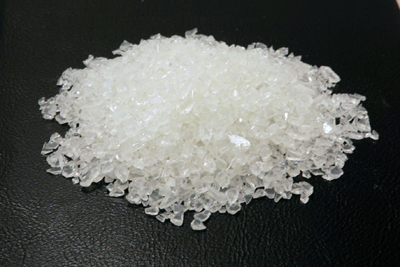
Finalmente, se emplearán dos casos de estudio para demostrar las ventajas del las nuevas tecnologías desarrolladas en el proyecto; una pieza para el sector del transporte de mercancía pesada y una pieza para vehículos ligeros. En el primer caso, la pieza se obtendrá con el recubrimiento del gel coat en polvo del color del acabado final, sin necesidad de posteriores tratamientos. La pieza a realizar para vehículos ligeros, se obtendrá con un recubrimiento de gel coat en polvo con propiedades de conductividad eléctrica preparada para su pintado en un baño de pintura cataforética tal y como es habitual en el pintado de piezas metálicas.
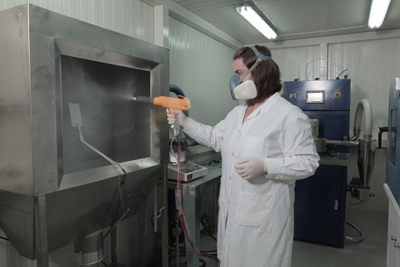
El consorcio del proyecto está constituido por 13 organizaciones europeas que incluyen, Aimplas, Ecoinnova y Cidetec en España, Composite Integration, Axon y NetComposites de Reino Unido, Clerium de Holanda, Indupol International N.V. de Bélgica, e-Xstream engineering de Luxemburgo, ‘Dortmund University of Applied Sciences and Arts’ en Alemania, Ketek en Finlandia, Megara de Grecia y Steel Belt Systems Powder Coating Division (SBS) de Italia.
La investigación que conducirá a estos resultados ha recibido subvención del 7º Programa Marco de la Unión Europea (FP7/2007-2013), bajo el acuerdo de subvención no. 609203. Para más información puede visitarse la web del proyecto en www.ecogelcronos.eu.