Recuperación de RAEE en España: el reto tecnológico
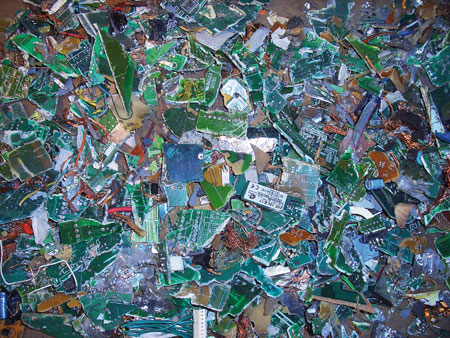
A un año de la fecha límite (14 febrero de 2014) para la transposición al ordenamiento jurídico español de la Directiva 2012/19/UE sobre residuos de aparatos eléctricos y electrónicos (RAEE), sigue en el aire el interrogante de si se podrán alcanzar los ambiciosos objetivos marcados por la misma.
La norma fija nuevas cuotas de reciclado más exigentes, así como mayores regulaciones para la recogida de los distintos grupos de RAEE; en concreto, establece que a finales de 2019, el 85% de los RAEE generados deberán ser recogidos de forma separada y tratados en instalaciones autorizadas
Esta es una transposición considerada “crucial” por todos los agentes del sector. Supone una oportunidad para dinamizar la actividad, ralentizada los últimos años por diferentes motivos, el principal de ellos el descenso del consumo, que se ha traducido en una menor generación de residuos eléctricos y electrónicos.
“En estos momentos de crisis es necesario valorizar al máximo los residuos. La nueva Directiva ayudará a canalizar mejor los flujos de residuos generados, por lo que se espera un aumento a medio plazo de las entradas en planta de reciclaje. El reto para las plantas es adaptarse a la Directiva y en ese cambio conseguir mejorar la eficiencia de sus procesos, junto con un incremento de los ingresos por venta de subproductos”, afirma Judit Jansana, jefe técnico comercial para Iberia y Latinoamérica de Titech.
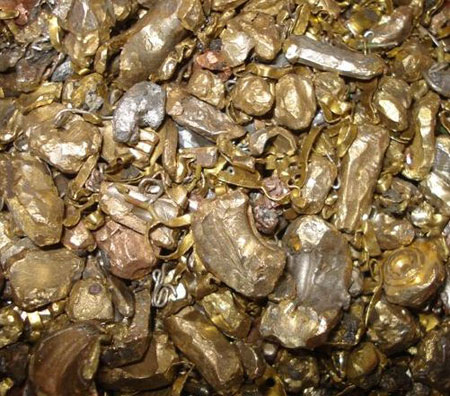
Qué puede hacer la tecnología para incrementar las cuotas de reciclado
Si se cumplirán o no los objetivos de la Directiva es motivo de debate, pero en lo que sí existe acuerdo es en que estas cuotas sólo serán alcanzables con la tecnología apropiada.
La propia norma indica en su articulado que los Estados Miembros deben asegurar que todos los RAEE se recogen separadamente y son procesados adecuadamente, utilizando en todo momento las mejores técnicas disponibles. Por ello, uno de los factores determinantes para que los gestores de residuos, tanto españoles como europeos, alcancen esos objetivos es el grado de tecnificación de las instalaciones y plantas recicladoras.
En ese sentido, Jansana ha explicado que “la única forma de incrementar las cuotas de reciclado es revisar el concepto tradicional de planta, en el que muchos procesos se realizan de forma mecánica o manual, y sustituirlo por la tecnología actual de clasificación por sensores, que permite la optimización en la recuperación de metales y la obtención de valiosos subproductos metálicos. Además de hacer posible la recuperación de fracciones poliméricas y el adecuado tratamiento de la fracción de finos”.
“El uso de tecnología de vanguardia ayudará a las empresas españolas a cumplir con las cuotas fijadas, además de reducir sus costes operativos, en tanto que la automatización de los procesos consigue aumentar la productividad, mientras que se incrementan los ingresos por la venta de subproductos de mayor calidad y con mayor eficiencia” afirma.
Las ventajas son claras. Como dato, con el método tradicional de separación el contenido de metales en el material de rechazo es de aproximadamente entre un 10% hasta incluso un 30%, mientras en un proceso automatizado basado en tecnología de sensores el rechazo total está libre de metales en menos de un 1%.
Así, en una planta de recuperación de RAEE diseñada con una combinación específica de maquinaria de clasificación por sensores (electromagnéticos (EM3), sensores NIR o cercano Infrarrojo y cámara de color (CCD)) se consigue maximizar la recuperación de todos los metales, especialmente los NO Férricos todavía existentes en los flujos de rechazo, como acero inoxidable, cables eléctricos, placas de circuito impreso, cobre, latón, etc. También permite la recuperación de nuevos subproductos para su venta, como los finos; así como la separación de polímeros en sus distintas familias y la separación de fracciones metálicas entre sí, como cables eléctricos, cobre, latón y placas de circuito eléctrico, sin necesidad de granular ni de mesas densimétricas Y para aquellos que hayan optado por granular también se separa el cobre y el latón del resto de metales mediante cámara de color de alta resolución.
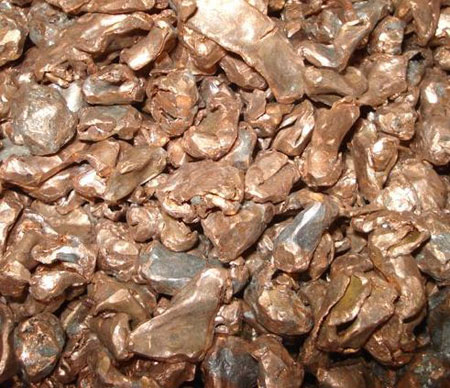
Sensores para separar los componentes peligrosos de los RAEE
Dentro de las políticas para la salud y el cuidado del medioambiente, la Directiva establece la obligatoriedad de dar un tratamiento selectivo a los RAEE, a fin de evitar la dispersión de contaminantes en el material reciclado o en el flujo de residuos.
La norma incluye una relación de sustancias y componentes considerados nocivos, que deben ser separados. Uno de los aspectos en los que incide es en la identificación y separación de plásticos que contengan materiales pirorretardantes bromados (BFR), que y forman parte de circuitos impresos, carcasas de plástico o conectores y cables. Como ha señalado Judit Jansana: “Todos los plásticos de RAEE deben ser previamente tratados para la separación de los retardantes a la llama de Bromo del resto de plásticos, un proceso que requiere de nuevas tecnologías, pues muy difícilmente se podrá lograr esta distinción manualmente”.
Por ello, la tecnología de sensores mediante rayos X está cada vez más extendida para llevar a cabo esta operación, ya que garantiza los mejores resultados, al distinguir los materiales por su densidad atómica. En una instalación diseñada para esta aplicación, combinando un equipo de sensores NIR y otro de sensores con rayos X, es posible recuperar para su eliminación hasta el 97% de los plásticos con BFR, separando primero por tipos de plásticos con el sensor de infrarrojos, para luego separar dentro de cada familia los que tienen Bromo (BFR) de los que no.
Las pequeñas plantas de reciclaje pueden beneficiarse de esta tecnología
La tecnología de clasificación basada en sensores para el tratamiento de RAEE ofrece beneficios tanto operativos, como ambientales y económicos para todo tipo de plantas, incluso las de menor capacidad de procesado. Esto es debido a que son equipos polivalentes, ocupan relativamente poco espacio, tienen un menor consumo eléctrico y bajos costes de mantenimiento. Aun contando con la necesaria inversión inicial, esta tecnología resulta rentable para las empresas, pues permite recuperar más fracciones y de mejor calidad, reducir costes de operación y maximizar ingresos; y con una rápida amortización.
“Uno de los grandes retos del sector es hacer frente la proliferación de un gran número de pequeñas plantas de reciclaje y conseguir optimizar su gestión y su rentabilidad a través de las nuevas tecnologías definiendo nuevos procesos más eficaces”, explica Jansana. Titech se adapta a las necesidades de las pequeñas plantas de clasificación de RAEE con equipos multitarea disponibles en varios tamaños, desde 600 milímetros de ancho de banda hasta 3 metros de ancho.
“Titech ofrece para los empresarios de este mercado del reciclado equipos altamente flexibles, capaces de trabajar con distintos materiales y programas gracias a la posibilidad de combinar distintos sensores en un mismo equipo de separación. Por ejemplo, la familia de separadores Titech finder se puede combinar con la familia Titech autosort para separar por un lado todos los metales con el sensor electromagnético. Por otro lado, con el sensor de Infrarrojos se puede realizar la separación de una sola familia de plásticos como el ABS o el PS, o bien combinando dos sensores se pueden separar placas de circuito impreso; o también sólo cables eléctricos con aislamiento plástico”, concluye Judit Jansana.
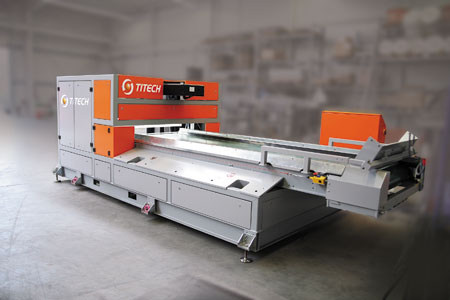
Acerca de Titech
Titech forma parte de Tomra Sorting Solutions y ya ha suministrado más de 3.000 máquinas de clasificación basadas sensores a la industria del reciclado de residuos y del metal en más de 40 mercados. Tomra Sorting Solutions ofrece más de 25 soluciones de clasificación para diversas aplicaciones de reciclaje y es un proveedor líder para los sectores del reciclaje, la minería y el procesado de alimentos.